七大浪费经典介绍(中英文版)英语学习外语学习教育专区
7大浪费经典介绍(中英文)
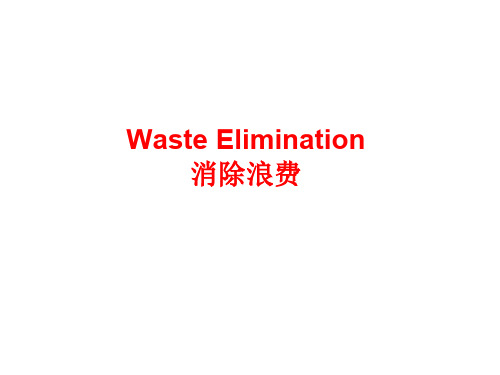
Equipment
Downtime 设备停机时间
Poor layout 糟糕的厂区布局
Supplier Quality 供应商的质量
Low Down Inventory To Expose Problem
通过降库存暴露问题
库存水平
维修问题 效率问题 质量问题
交货问题
23
Waste of Motion
磨削工序
Heat Treatment
热处理
Moving Material
搬运
15
Value Added – Examples
增值案例
Is it Value Added (VA) or Non-Value Added (NVA)?
请判断是否增值?
VA增值 NVA不增值 Cutting operation
为什么?
28
Overproduction Waste
生产过剩
Overproduction spins off all other types of waste 生产过剩 超过了 其他所有的 浪费形式
29
• Overproduction
• Need more boxes • Need many pallets • Need fork lift • Need fork lift drivers • Need additional floor space • Need warehouse • Need warehouse operators • Many parts get rusty • Need sorting operator • Need rework • Make scrap
7
Value Added – Examples
七大浪费经典

① 作业内容与工艺检讨不足
② 冲床作业上重复的试模,不必要的 动作
② 模夹治具不良
③ 成型后去毛头,加工的浪费 ④ 钻孔后的倒角浪费 ⑤ 最终工序的修正动作
③标准化不彻底 ④ 材料未检讨
精品课件
CTP制造中心
2. 浪费的种类(7大“最”状)
① 工程设计适正化 ② 作业内容的修正 ③ 治具改善及自働化 ④ 标准作业的贯彻
② 使先进先出的作业困难
③ 损失利息及管理费用
④ 物品之使用价值会减低,变成呆滞品
⑤ 占用厂房、造成多余的工作场所、仓库 建设投资的浪费
⑥ 造成无形的浪费
精品课件
CTP制造中心
2. 浪费的种类(7大“最”状)
没有管理的紧张感 设备能力及人员需求误判 对场地需求的误判 产品品质变差的可能性 容易出现呆滞物料
① 材料・部品被提前吞吃 ② 电、空气等能源的浪費
⑥ 使先进先出的工作产生困难 ⑦ 会造成库存空间的浪费
③ 货架与箱子的增加 ④ 搬运者,运输的增加
⑧ LEADTIME变长(在庫增加)
⑤ 会把等待的浪费隐藏起来,掩盖稼动率不足的问题
到销售为止的时间变长(转换为钱的速度减慢
精品课件
现金流减缓)
CTP制造中心
··· ···
・有效动作(创造价值的动作)只占到所有动作的
1/9
精品课件
CTP制造中心
2. 浪费的种类(7大“最”状)
① 作业流程配置不当
① 一个流生产方式的编成 ② 生产线U型配置
① 补助动作的消除
② 无教育训练
③ 标准作业之落实
②作业标准
③ 设定的作业标准不合理
④ 动作经济原则的贯彻 ⑤ 加强教育培训与动作训练
工厂管理之七大浪费
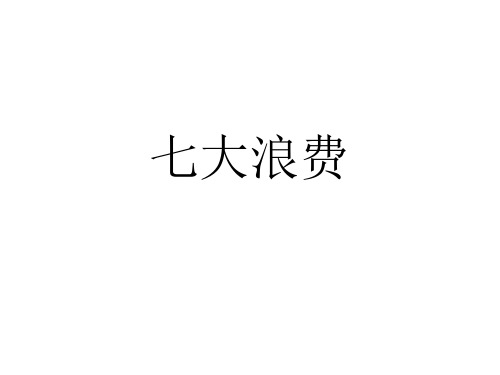
课程目标
了解和能够向他人解释浪费的七种型态(徵候、 原因、影响)
找出每一种浪费的范例和消除浪费的解决方式
我们要如何定义「浪费」?
浪费 是: - 耗费了时间、资源或空
间但对客户手中的产品或 服务却不能增加价值。
丰田着名的追寻浪费
• Muda- (浪费):浪费的七种型态, 及其范畴。
• Muri- (超载):操作员或机器的过 量运作或压力。
定义
做得比客户需求还多,或者是赶在客户需求之 前生产。
影响: 时间的滥用、 额外的搬运、额外的空 间、努力、金钱 及潜在的品质问题。过量生 产还会导致其它各种形式的浪费。
原因(举例): 不稳定的工作环境(停机时 间、品质问题、“JIC"等。)
举例………?
范例
过量生产的浪费
越多的存货 =越多的金钱
JIT仓库 进料5500件 出货1500件
范例
多余制程的浪费
裁斷
裁斷點料
檢驗
包裝
JIT倉庫點料
針車點料 針車
• 所有步骤对客户来说都能增加产品的价值吗?
多余制程的浪费
范例
垫上鞋舌防护片
多余制程的浪费
移除鞋舌护片
• 难道所有的步骤对客户来说都能增加产品的价值吗?
动作的浪费
定义 人或机器造成人体操作上的压力或额外的动 作,却不能增加产品价值。 影响: 时间浪费或虚耗、人体工学的问题、 非因生产所耗费的劳务、人员的伤害或金钱 的浪费。 原因: 模组式现场配置、机器设定、设置不 良。 举例………?
拿取最下面的盒子以遵循先进先出原则
浪费
(站立,弯腰,拿取盒子,放下盒 子…)
转身,然后从物架上拿取物料
库存的浪费
7大浪费经典介绍中英文版
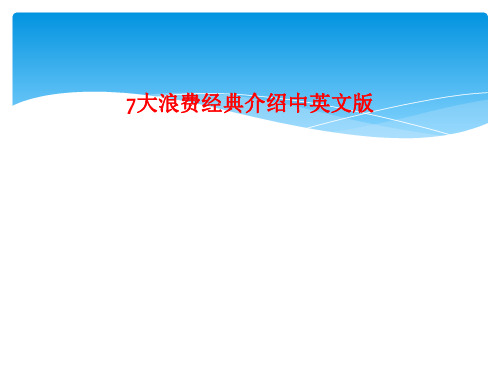
Is it Value Added (VA) or Non-Value Added (NVA)?
请判断是否增值?
VA增值NVA不增值 Cutting operation
切削工序
Grinding operation
磨削工序
Heat Treatment
热处理
Moving Material
搬运
Inspection
请判断是否增值?
VA增值NVA不增值 Cutting operation
切削工序
Grinding operation
磨削工序
Heat Treatment
热处理
11 2020/11/30
11
Value Added – Examples
增值案例
Is it Value Added (VA) or Non-Value Added (NVA)?
生产过剩
Overproduction is considered the worst waste! 生产过剩被认为是最严重的浪费!
Why?
为什么?
27 2020/11/30
27
Overproduction Waste
生产过剩
Overproduction spins off all other types of waste 生产过剩 超过了 其他所有的 浪费形式
检查
16 2020/11/30
16
Non-Value Added 非增值
95%
of all
manufacturing
time is non-value
added!
95%
的生产时间是
不能增值的
17 2020/11/30
Waste Elimination 消除浪费
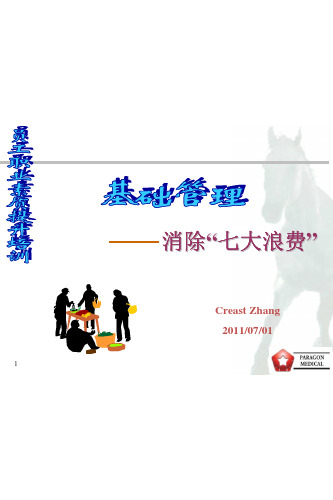
表现形式:
•不良品存在库房内待修 •设备能力不足所造成的安全库存 •换线时间太长造成次大批量生产的浪费 •采购过多的物料变库存
库库存存是是万万恶恶的的根根源源,,有有时时也也称称之之为为库库存存黑黑洞洞
26
3.6 库存的浪费
过多的库存会造成的浪费:
表现形式:
•自动机器操作中,人员的“闲视”等待 •作业充实度不够的等待 •设备故障、材料不良的等待 •生产安排不当的人员等待 •上下工程间未衔接好造成的工程间的等待
18
3.3 等待的浪费
原因:
•生产线布置不当,物流混乱 •设备配置、保养不当 •生产计划安排不当 •工序生产能力不平衡 •材料未及时到位 •管理控制点数过多 •品质不良
•一个流的生产方式 •品保制度的确立及运行 •定期的设备、模治具保养 •持续开展“5S活动”
注意:
•能回收重做的不良
•能修理的不良
13
•误判的不良
3.2 制造过多的浪费 (Over Production)
无法保证可卖出的产品做了太多
是浪费的源头
表现形式:
•物流阻塞 •库存、在制品增加 •产品积压造成不良发生 •资金周转率低 •材料、零件过早取得 •影响计划弹性及生产系统的适应能力
29
3.7 动作的浪费
原因:
•作业流程配置不当 •无教育训练 •设定的作业标准不合理
注意:
•补助动作的消除 •作业标准
对策:
•一个流生产方式的编成 •生产线U型配置 •标准作业之落实 •动作经济原则的贯彻 •加强教育培训与动作训练
30
3.8 新概念的浪费: (1) 时间的浪费 (Time)
精益生产中的七大浪费

精益生产中的七大浪费消除七大浪费是精益生产的核心理念之一,七大浪费可用“TIM WOOD”表示(分别取7种浪费之英文首字母:运输、库存、动作、等待、过量生产、多余的工序、缺陷),以下对七大浪费作简要介绍。
一、七大浪费介绍第一种:运输的浪费主要表现为:车间布置采用批量生产,依工作站为区别的集中的水平式布置所致,无流线生产的观念。
第二种:库存的浪费主要表现为:管理者为了自身的工作方便或本区域生产量化控制一次性批量下单生产,而不结合主生产计划需求流线生产所导致局部大批量库存。
库存的损害表现有:(1):产生不必要的搬运、堆积、放置、防护处理、找寻等浪费。
(2):使先进先出的作业困难。
(3):损失利息及管理费用。
(4):物品的价值会减低,变成呆滞品。
(5):占用厂房空间,造成多余的工场、仓库建设投资的浪费。
(6):没有管理的紧张感,阻碍改进。
(7):设备能力及人员需求的误判。
第三种:动作的浪费主要因素表现为:生产场地不规划,生产模式设计不周全,生产动作不规范统一。
第四种:等待的浪费主要因素表现为:作业不平衡,安排作业不当、待料等。
第五种:过量生产的浪费主要因素表现为:管理者认为制造过多与过早能够提高效率或减少产能的损失和平衡车间生产力。
制造过多(早)的损害表现有:(1):提早用掉费用(材料费、人工费),不能创造利润。
(2):把“等待的浪费”隐藏起来,使管理人员漠视等待的发生和存在。
(3):自然而然地积压在制品,其结果不但会使制程的时间变长(无形的),而且会使现场工作的空间变大,机器间距离因此加大,逐渐地吞蚀利润。
(4):产生搬运,堆积的浪费,使得先进先出的作业产生困难。
第六种:多余的工序的浪费主要因素表现为:制造过程中作业加工程序动作不优化,可省略、替代、重组或合并的未及时检查。
第七种:缺陷的浪费主要因素表现为:工序生产无标准确认或有标准确认未对照标准作业,管理不严密、松懈所导致。
二、以制造业为例,消除浪费之优先顺序优先级#1 过量生产这是7种浪费中最严重的一种,因为:a)它衍生出了另外的6种浪费b)它掩盖了真正的生产能力,从而导致你做出诸如转包工作或是在不必要的方面投资这样错误的决定。
识别消除生产中的七大浪费(经典)

等待的浪费
生产过程中设备、人员等资源的闲置和等待,导致 效率低下和成本增加。
搬运的浪费
不必要或不合理的物料、半成品、成品在生产过程 中的搬运,增加了运输成本和时间。
浪费的分类
01
02
03
04
加工的浪费
过度或不必要的加工,导致资 源浪费和产品成本的增加。
库存的浪费
过多的库存导致资金占用、管 理成本增加,同时还可能引发 品质问题。
缺陷和重修
定义
缺陷和重修是指产品不符合质量标准或 客户要求,需要进行返工或报废。
影响
降低客户满意度、增加成本、影响企 业声誉。
原因
质量控制不严格、产品设计缺陷、生 产过程中的问题。
解决方法
加强质量管理体系建设,实施严格的 质量检测和把关,提高产品设计质量 和生产过程的稳定性。
未充分利用员工才能
定义
03
02
原因
设备故障、生产不平衡、计划安排 不当。
解决方法
加强设备维护保养,实施均衡化生 产,优化计划调度。
04
过程浪费
定义
原因
过程浪费是指在生产过程中出现的各种不 合理的操作和动作。
操作不当、工艺流程不合理、缺乏标准化 作业。
影响
增加成本、降低效率、影响产品质量。
解决方法
制定标准化作业指导书,优化工艺流程, 加强员工培训和操作规范。
某服务企业在服务过程中存在一些浪费现象,如服务流程繁琐、人力资源浪费、客户沟通不畅等。为 了消除这些浪费,该企业采取了相应的措施,如优化服务流程、引入智能客服、加强员工培训等。
通过这些措施,该企业提高了服务质量和效率,减少了浪费,增加了客户满意度,最终实现了业务增 长。
JIT精益生产—七大浪费PPT课件

15
七大浪费之 6:过度加工 OVER PROCESSING
超出必要范围 画蛇添足 不必要的检验 太多审批 太多花样
16
Over Processing 过度加工
如何拼写?
How do you spell that?
17
七大浪费之 7 :次品 DEFECTS
物品 设备 信息 服务 …… 凡是不符合客户要求的
37
发现浪费方法之 3
1. VSM 价值流 2. Gemba 去现场 3. 5S 整理整顿 4. Visual Control 可视化管理 5. Layout 布局 6. Standard Work 标准作业
38
5S
Sort-----------Seiri -------分类 Set in order--Seiton------定位 Shine---------Seiso -------擦亮 Standardize--Seiketsu--- 标准化 Sustain-------Shitsuke ---保持(素养)
便区分。
目的:排除寻找的浪费。 “三定”原则:
定位置:多思考易于“归位”的方法; 定数量:没有数量管制,位置将无法确定; 定标识:让任何人能一看就明白。
44
44
5S---SHINE 擦亮
每天清理作业区域 如有必要增加频率 边擦拭边检查物品是否有短少,破损,裂痕,
跑冒滴漏 想些办法防止物品变脏
45
3-S:清扫
有事时去现场
发生问题时应该先去现场,不要在办公室里听汇 报。
到现场后立即检查,只问事件过程,不急着下结 论。
采取临时措施处置。 用QAS方法检查流程控制点,更新流程。 一个月后回顾新流程的有效性。