呋喃树脂砂硬化控制的现场实践
呋喃树脂砂在铸造生产中的应用及质量控制

呋喃树脂砂在铸造生产中的应用及质量控制摘要呋喃树脂砂是近20年来发展最快的铸造工艺之一,用呋喃树脂砂生产的铸件,尺寸精确、表面光洁、棱角清晰、废品率低,并能节约造型工时、提高生产效率、改善劳动条件和成产环境。
2007年,山东安信机械制造有限公司对铸造车间进行技术改造,建立了一条树脂砂生产线,再该条生产线正式投产前,通过对员工进行系统的技术培训,制定相关的规章制度和操作规范,顺利实现了由水玻璃砂生产工艺向树脂砂生产工艺的转变。
本文对铸造生产各工序的过程控制作一简单阐述。
关键词呋喃树脂砂;铸造;生产;质量控制1 铸造工艺的控制呋喃树脂砂的特点是瞬间发气量大,高温溃散性好,易产加成气孔、夹渣和冲砂缺陷,在设计浇注系统时,应坚持快速、平稳、分散的浇注原则,浇注系统的截面积要比粘土砂工艺稍大一些,内浇道要分散放置。
树脂砂强度高、刚性好,铸件不容易产生缩孔缺陷,故应采用相对较高的浇注温度,以避免出现气孔和夹渣缺陷,厚大铸铁件的浇注温度也不应低于1 320℃。
2 砂型质量的控制2.1 原材料的选择及要求2.1.1 原砂树脂砂工艺对原砂的要求很高,原砂的粒度应根据主要产品的壁厚来确定,由于我公司主要以生产薄壁铸件为主,且未配备原砂烘干设备,故选用了粒度为50/100目的烘干擦洗砂。
2.1.2 树脂、固化剂国内成产树脂、固化剂的厂家很多,但具有自主研发能力、具备完善的检测设备和严密可靠的质量保证体系的厂家屈指可数。
经检验、对比,我们选用了济南圣泉集团股份有限公司生产的环保型呋喃树脂和磺酸固化剂,树脂加入量一般为原砂重量的1.0%~1.2%。
3 型砂工艺参数的控制3.1 可使用时间在生产过程中,我们将型砂表面开始固化的时间作为型砂的可使用时间,一般情况下,型砂的可使用时间应控制在6~10min,对于大型铸型或砂芯,可使用时间可延长15min,通过调整固化剂的加入量来控制型砂的可使用时间。
3.2 型砂强度初强度:是指型砂在1h的抗拉强度,型砂的初强度应控制在0.1~0.4MPa。
呋喃树脂自硬砂控制技术

呋喃树脂自硬砂控制技术程利军零正技罗勇广西柳工机械股份有限公司广西柳州545007)摘要本文主要从硅砂的性能要求、造型过程的控制和再生砂的回用等对呋喃树脂自硬砂技术进行了探讨,供广大铸造同行参考。
关键词呋喃树脂自硬砂硅砂造型再生砂在线检测随着中国制造业近几年的长足发展,中国的铸造业也迎来了历史上最好的发展机遇。
目前,我国铸件的产量已连续多年位居世界之首。
呋喃树脂自硬砂工艺由于其生产周期短、铸件表面精度高、铸件质量容易控制、柔性化制造能力高等特点,已经被广泛的应用到机床铸件、耐磨铸件、工程机械铸件等产品中。
而铸造企业能否发挥呋喃树脂自硬砂的特点,有效的提高铸件的质量,这与型砂的控制技术有着密切的关系。
砂型铸造行业公认型砂控制技术、熔炼控制技术和管理水平三者决定了一个铸造厂在市场上的竞争能力,由此可见型砂的控制技术在铸造业中的重要性。
本文就呋喃树脂砂的一些控制技术提出一些个人的观点,希望同行提出批评指正。
1硅砂的技术要求1.1 硅砂的粒度组成硅砂的粒度反映了硅砂的颗粒大小和分布状态。
由于自硬砂强度的获得是依靠呋喃树脂“包覆”硅砂表面形成的高分子链,所以硅砂的粒度越细,从理论上说获得同样强度的树脂消耗量就越大,型砂的成本也就越高,所以在保证铸件不发生粘砂缺陷的前提下,尽可能提高硅砂的粒度。
1.2硅砂的角形系数硅砂的角形系数S=Sw/St图l试样抗拉强度与型砂粒度关系注:实验型砂组成的余量为0.212目以下Sw一硅砂的实际比表面积(cm2/g)St一硅砂的理论比表面积(cm2/g)硅砂的角形系数越小,表面就越园整,同样体积的硅砂表面积越小,硅砂和呋喃树脂的物理和化学结合力就越强,获得同样的抗拉强度需要的树脂消耗量就越低。
作为自硬砂用的硅砂角性系数要求≤1.30,最好≤1.15。
1.3硅砂的加工处理由于天然硅砂有大量直径小于0.02的泥分和一些污染物和一些有碱性的物资,泥分的存在极大的降低了硅砂的粒度组成,提高了树脂的消耗量,同时有碱性的物资在树脂砂硬化过程中消耗了大量的催化剂——对甲苯磺酸等物资,造成砂型硬化很慢甚至不硬化,所以硅砂必须经过擦洗和粒度分选处理。
浅谈呋喃树脂砂的生产与质量控制

向性 ;如果砂 型或砂芯强 度过低 ,往往会 造成粘砂 、夹砂等铸造 缺陷 。因 制 ,完全 可以保证产 品质量 。但在 呋喃树脂砂生产 过程 中,还有很多 问题
水玻璃砂 相 比需要延长打箱 时间 ,减小热应 力来降低铸 件产生裂 纹 的倾 微粉 含量 越高 ,型砂 的透气性 越差,同时消耗的树脂和 固化 剂也越高 。因
向性 。
此需要严 密监控除尘设 备的工作状态 ,及 时清理灰尘 。同时要 对型砂进
浇注系统对呋 喃树 脂砂生产 的铸钢件质量 影响较大 ,如果 浇注 系统 行 定期检查和监控 ,否则将 对产品质量和生产造 成极大 的不利影 响 。
水 玻璃砂的大一些 。针对 呋喃树脂砂发气量 大和高温易溃散 的特点,在铸 法 保证砂型质量 ,同时也使生产无法 正常进行 。特别是在 夏季这种 情况
件结构和生产条件 允许的条件下 ,尽量采用 底注方式 。
更为突 出。因此需要采取 冷却系统对砂温进行 降温处理 以保证正 常生产
对于大型铸钢 件 ,为了避免产生气孔 等缺陷 。在浇 注前需要采 用热 的进行 。而在冬 季 由于环境温度偏 低 ,造成 呋喃树脂砂 固化速度 过慢或
显比在粘土砂中的凝 固速度缓慢。特别是在铸件的热节处或转角部位由
5型砂质量 的控制
于凝 固缓慢 ,极易在 这些部位产生裂 纹等缺 陷。另外 由于呋喃树 脂砂高
影 响砂 型质量的 因素 ,其 中型砂 中微粉含量对树脂 和固化剂 的使用
温退让性 差 ,铸件 产生热 裂纹 的倾 向性 明显增 大 。根据 呋喃树脂 砂的这 量影 响很 大 ,而 目直接影响铸 件质量。对于新砂应妥善保 管 ,防aD'b来杂
些特点 ’并结合 铸件的结构特 在铸件 易产生裂纹 的部位应设 置拉筋 ,在 质污染 ,同时要特别防止碳酸盐等碱性物质混入。对于再生砂需要严格
呋喃树脂砂.doc

浅谈铸铁件呋喃树脂自硬砂生产技术及应用作者:赵占良我国加入世贸组织以后,铸铁件的出口量增长迅猛,与此同时国际市场对铸件的要求也越来越高。
因砂型铸造中呋喃树脂粘结剂的应用,明显的提高了铸件的质量,给国内铸造aa 行业带来了较为显著的经济效益,得到了铸造界的一致认同。
但在生产过程中,也存在着一些问题,如果不加以重视和解决,势必会带来不必要的经济损失。
因此,我们在树脂砂生产技术方面,作了一些工作与探索,为我公司进一步加大国外来图加工业务,拓宽出口范围,作出了努力。
1.呋喃树脂砂的优缺点1.1优点1) 铸件的尺寸精度高、外部轮廓清晰;铸件表面光洁,外观质量好;组织致密,铸件综合品质高。
由于树脂砂具有较好的流动性、易紧实、脱模时间可调节、硬化后强度高、在其后的搬运及合箱过程中不变形;因树脂砂的刚度高,在浇注和凝固过程基本上无形壁位移现象,所以铸件的尺寸精度高,它比粘土砂及油砂生产的铸件可提高1-2个级别。
2) 不用烘干,缩短了生产周期,节省了能源。
3) 省去了烘干工序,型砂易紧实,溃散性好易清理等,大幅度降低了工人的劳动强度,为实现机械化生产创造了条件。
1.2不足之处1) 对原砂质量要求高;2) 造型和浇注现场,在生产过程中有刺激性气味。
3) 采用树脂砂生产,成本较高,应综合考虑。
由上所述可以看出,树脂砂的优点较为突出,因此在国内得到了推广应用。
2.呋喃树脂砂的生产工艺技术2.1原材料的选用1) 铸造用砂的要求原砂对呋喃树脂砂的性能粘结剂用量以及铸件表面质量的影响很大,要求原砂中的SiO2含量要高,含泥量和酸耗值要低。
粒度:大件42或30组别,中件21组别,小件15或10组别。
2) 呋喃树脂含糠醇的树脂称为呋喃树脂,其糠醇含量较高,树脂的存放性能得以改善,热强度高但增加了成本。
树脂中的游离甲醛是生产中产生刺激性气体的来源,也是恶化环境的因素之一,应加控制。
铸铁件生产应选用低氮或无氮树脂,实际应用根据铸件的技术要求和结构来选择。
浅谈呋喃树脂自硬砂的生产及应用
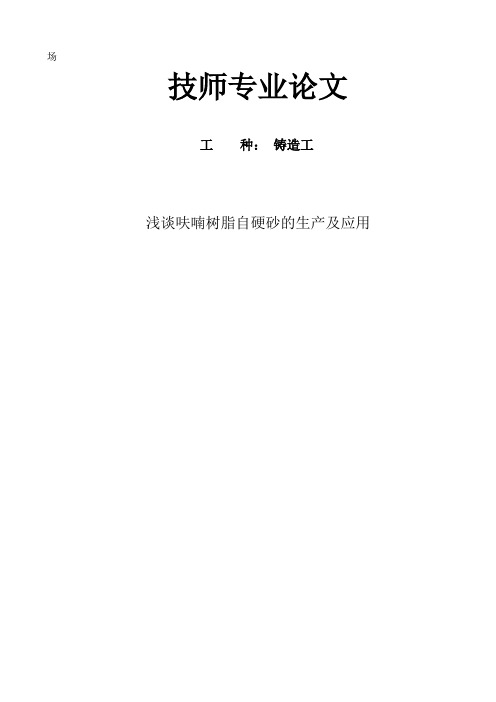
场技师专业论文工种:铸造工浅谈呋喃树脂自硬砂的生产及应用摘要 (2)引言 (2)1.呋喃树脂砂性能的优缺点 (2)2.呋喃树脂自硬砂的生产工艺技术 (3)3.工艺及现场控制 (6)4.呋喃自硬树脂砂铸件的缺陷分析及防止措施 (8)5.结论 (9)参考文献 (10)本论文针对呋喃树脂自硬砂的坭芯生产,阐述了呋喃树脂自硬砂的原材料配比、混制及硬化工艺。
结合作者多年在实际生产工作中的经验,就生产中出现的实际问题进行分析和讨论,通过采取文中提出的控制、解决措施,有效地解决了铸件出现的气孔、粘砂、热裂、冲/夹砂、脉纹等铸造缺陷。
关键词:呋喃树脂自硬砂、铸造缺陷、夹砂、热裂、脉纹引言呋喃树脂自硬砂工艺是指在呋喃树脂砂中加入一定量的酸性固化剂,使之在芯盒或砂箱内经历一定时间后,在常温条件下通过自行硬化成型(不需烘烤或吹入硬化气体)的一种造型制芯工艺。
呋喃树脂自硬砂硬化反应机理可简单描述为:涂敷在砂粒表面的树脂在酸性固化剂的催化作用下,呋喃树脂分子上的活性氢、羟甲基与羟甲基之间发生缩聚反应和呋喃环上的双键打开发生加成聚合反应,形成三维网状结构固体树脂,使型(芯)砂硬化成型。
1.呋喃树脂砂性能的优缺点1.1优点1)铸件的尺寸精度高、外部轮廓清晰、铸件表面光洁,外观质量好、组织致密、铸件综合品质高。
2)呋喃树脂自硬砂具有较好的流动性,容易紧实,脱模时间可调节,硬化后强度高,在其后的搬运及合箱过程中不变形,因树脂砂的强度高,在浇注和凝固过程中基本上不会出现位移现象,所以铸件的尺寸精度高。
3)不用烘干,缩短了生产周期、节省了能源、芯砂易紧实、溃散性好、容易清理、大幅度降低了劳动强度,为实现机械化生产创造了条件。
1.2 呋喃树脂自硬砂的不足之处1)对原砂质量要求高2)在生产过程中有刺激性气味3)采用树脂砂生产,成本较高2.呋喃树脂自硬砂的生产工艺技术2.1 原材料的选用1)铸造用砂的要求:原砂对呋喃树脂砂的性能、粘结剂用量、以及对铸件表面质量的影响很大,要求原砂中的SiO2含量要高、含泥量和酸耗值要低。
呋喃树脂砂生产铸铁件过程控制

明、 生 产注 意事项 、 浇 注温 度及 时 间控制 等 。
2 造 型 控 制
( 1 ) 混砂
树 脂砂 铸造 用砂 分 为 原砂 和再 生 砂 。原 砂选
择3 0— 7 0目的擦 洗砂 ; 再生砂工艺要求为 : 灼 烧
减 量 ≤3 %, 微 尘 ≤0 . 8 % 。在 生 产 过 程 中 , 可 定 期、 定量 加入 原砂 , 以保证 型砂 质量 的稳定 性 。 型 砂黏 结 剂 为 呋 喃 树 脂 和 磺 酸 固化 剂 , 其 中
Abs t r ac t: Al t h o u g h f u r a n r e s i n s a n d c a s t i n g i s a ma t u r e t e c hn o l o g y,b u t t h e pr o d u c t i o n o f c a s t i n g d e -
Ch e n Mi n g,Xu Xi n gl i ,W e n Xi n gl e i
( N i n g x i a S h i n r i C a s t i n g C o .L t d , N i n g x i a Y i n c h u a n 7 5 0 0 0 0 C h i n a )
c o n t r o l , a n d s u p p l i e s t h e i ns t r uc t i o n t o c a s t i n g d e f e c t c o n t r o 1 . Ke yW o r ds: f u r a n r e s i n s a nd;c a s t i r o n;c a s t i n g;p r o c e s s c o n t r o l
呋喃树脂自硬砂控制技术

呋喃树脂自硬砂控制技术程利军零正技罗勇广西柳工机械股份有限公司广西柳州545007)摘要本文主要从硅砂的性能要求、造型过程的控制和再生砂的回用等对呋喃树脂自硬砂技术进行了探讨,供广大铸造同行参考。
关键词呋喃树脂自硬砂硅砂造型再生砂在线检测随着中国制造业近几年的长足发展,中国的铸造业也迎来了历史上最好的发展机遇。
目前,我国铸件的产量已连续多年位居世界之首。
呋喃树脂自硬砂工艺由于其生产周期短、铸件表面精度高、铸件质量容易控制、柔性化制造能力高等特点,已经被广泛的应用到机床铸件、耐磨铸件、工程机械铸件等产品中。
而铸造企业能否发挥呋喃树脂自硬砂的特点,有效的提高铸件的质量,这与型砂的控制技术有着密切的关系。
砂型铸造行业公认型砂控制技术、熔炼控制技术和管理水平三者决定了一个铸造厂在市场上的竞争能力,由此可见型砂的控制技术在铸造业中的重要性。
本文就呋喃树脂砂的一些控制技术提出一些个人的观点,希望同行提出批评指正。
1硅砂的技术要求1.1 硅砂的粒度组成硅砂的粒度反映了硅砂的颗粒大小和分布状态。
由于自硬砂强度的获得是依靠呋喃树脂“包覆”硅砂表面形成的高分子链,所以硅砂的粒度越细,从理论上说获得同样强度的树脂消耗量就越大,型砂的成本也就越高,所以在保证铸件不发生粘砂缺陷的前提下,尽可能提高硅砂的粒度。
1.2硅砂的角形系数硅砂的角形系数S=Sw/St图l试样抗拉强度与型砂粒度关系注:实验型砂组成的余量为0.212目以下Sw一硅砂的实际比表面积(cm2/g)St一硅砂的理论比表面积(cm2/g)硅砂的角形系数越小,表面就越园整,同样体积的硅砂表面积越小,硅砂和呋喃树脂的物理和化学结合力就越强,获得同样的抗拉强度需要的树脂消耗量就越低。
作为自硬砂用的硅砂角性系数要求≤1.30,最好≤1.15。
1.3硅砂的加工处理由于天然硅砂有大量直径小于0.02的泥分和一些污染物和一些有碱性的物资,泥分的存在极大的降低了硅砂的粒度组成,提高了树脂的消耗量,同时有碱性的物资在树脂砂硬化过程中消耗了大量的催化剂——对甲苯磺酸等物资,造成砂型硬化很慢甚至不硬化,所以硅砂必须经过擦洗和粒度分选处理。
呋喃树脂砂的使用方法

呋喃树脂砂的使用方法由于树脂自硬砂具有尺寸精度高、生产周期短、铸件质量高等特点,该工艺越来越多地用在机床、阀门、铸管、模具等众多领域,成为改善铸件质量、提高工艺水平的一种重要工艺方法。
本公司以其先进的技术和可靠的质量控制体系生产多种型号的自硬树脂,以适应铸钢、铸铁、有色金属及特殊要求的场合,其产品被越来越多的铸造企业采用。
呋喃树脂自硬砂工艺的一个特点就是固化速度、脱模时间受温度、湿度影响很大,最佳的温度范围是20℃~30℃,湿度则是越低越好,这时无论是固化剂用量、树脂砂强度还是固化速度都较理想。
随着冬季的到来,固化速度明显降低,每降低8℃,固化速度就降低一半。
许多客户尤其是新客户常发现2-3小时也不能脱箱,影响生产速度,所以用户必须掌握树脂砂工艺的特性,采取必要措施来解决这个问题。
常用的方法有:⒈更换固化剂公司有针对不同季节使用的固化剂,当冬季到来之前,注意及时更换使用G09固化剂或酸值更大的固化剂。
⒉ 增加固化剂的用量增加固化剂用量可以显著提高固化速度,这是生产中常用的方法,但加入量不宜过高,一方面增加成本,另一方面对终强度有害,且增加发气量,易产生气孔等缺陷。
⒊ 提高砂温通过增加砂温调节装置来提高砂温。
⒋ 增加环境温度很多铸造车间冬季无取暖设备,温度只有0℃左右,严重影响了固化速度,为此可以在造型现场设置几个取暖炉适当提高环境温度。
⒌ 提高模具、砂箱温度,保持干燥对金属模型、芯盒、砂箱可以适当加热以提高固化速度,对木模、木砂箱一定要保持其干燥。
另外,温度对树脂、固化剂粘度影响较大,因而波及定量泵流量,为保证加入量准确,每天生产前需校验树脂、固化剂量。
树脂砂的可使用时间随着树脂种类的不同有很大变化,它是供用户选择生产方法、工装、设备的重要依据,因此有必要介绍一下可使用时间的概念及其检测方法,以便于用户更好地控制生产。
⒈定义:树脂砂的可使用时间是指从混砂完毕至放置到不能制作出合格型芯的这段时间。
- 1、下载文档前请自行甄别文档内容的完整性,平台不提供额外的编辑、内容补充、找答案等附加服务。
- 2、"仅部分预览"的文档,不可在线预览部分如存在完整性等问题,可反馈申请退款(可完整预览的文档不适用该条件!)。
- 3、如文档侵犯您的权益,请联系客服反馈,我们会尽快为您处理(人工客服工作时间:9:00-18:30)。
参考资料 1 原著 加比莱.格兰特, 翻译 于震宗 ,缪良.自硬砂之理论与应用(一、二卷) 2 胡彭生主编.型砂(第二版) 3 唐玉林主编.圣泉铸工手册
10
面硬度 (℃*湿度)
脱模难
93
18*70
脱模难
90
20*70
脱模难
85
23*77
脱模亦可
80
20*70
脱模亦可
75
25*76
脱模亦可
70
25*76
脱模亦可
65
19*ቤተ መጻሕፍቲ ባይዱ7
脱模亦可
60
22*70
脱模易
55
25*76
脱模易
47
24*65
脱模情况
好 好 好 好 好 好 好 基本完整 不光洁 粘模
备注
脱模难 脱模难 脱模难 脱模亦可 脱模亦可 脱模亦可 脱模亦可 脱模亦可 脱模易 脱模易
1.2 金属模加热时的脱模
表2
砂型表 现场情况
面硬度 (℃*湿度)
93
18*70
90
20*70
85
23*77
80
20*70
75
25*76
70
25*76
65
19*77
60
22*70
55
25*76
47
24*65
脱模 情况 好 好 好 好 好 好 好 基本完整 不光洁 粘模
K2 侧架第一型脱模情况
备 注 砂型表 现场情况
之相适应。表三是呋喃树脂砂脱模时间与砂型质量情况的现场数据,从表三看出我公司铸工车间生产线
上呋喃树脂砂型的脱模时间控制在 12~25 分钟较好。
表3
上模脱模时间(分 钟)
呋喃树脂砂 K2 型侧架脱模时间与砂型质量情况
砂型质量情况
下模脱模时间(分
砂型质量情况
钟)
35
砂型易开裂
30
砂型易开裂
25
好
20
好
加热,第一型与第二型及以后的砂型脱模情况相当,脱模可控制表面硬在 70 左右。
2 金属模加热时的脱模时间控制
2.1 呋喃树脂砂脱模时间与砂型质量
在金属模加热情况下,可通过检测砂型的表面硬度确认是否可脱模,较长时间的单一产品亦可通过
经验判断进行脱模,但一定的脱模时间需要一定的固化速率,即一定的脱模时间需要特定的固化工艺与
8
注:1.以上数据使用再生砂,脱模时间控制在 15 分钟左右。 2.树脂用量 0.9%~1.0%(加偶联剂),固化剂 GS04 用量为树脂的 25~40%。 3.检测表面硬度计型号为 SYS 型砂型表面硬度计。
表 2 是 K2 侧架通过 45℃热风炉加热时脱模情况现场采集数据,从表二看出,由于对模具进行了
GS04
>15
正常
GC09
<15
固化不匀,强度不好
GS03
<12
固化不匀,强度不好 GC09
>20
正常
注: 1.以上数据使用再生砂或 80%的再生砂,砂温度小于 33℃。
2.树脂(FL-105)用量 0.91~1.00%(加偶联剂)。
3.因工艺需要,应尽量降低固化剂用量。
3.2 固化剂品种与气候温度
90 85 80 75 70 65 60 55
现场情况 (℃*湿度)
22*76 22*76 25*68 23*77 26*70 25*70 26*70 26*70
脱模情 况
好 好 好 基本完好 不光洁 局部粘模 局部粘模 明显粘模
备注
脱模难 脱模亦可
脱模易 脱模易 脱模易 脱模易 脱模易 脱模易
砂型表 面硬度
80 75 70 65 55 50 45 40
现场情况 (℃*湿度)
19*68 26*70 26*70 23*77 18*70 18*70 18*70 22*76
脱模情 况
好 好 好 好 基本完好 不光洁 局部粘模 明显粘模
备注
脱模难 脱模亦可
脱模易 脱模易 脱模易 脱模易 脱模易 脱模易
注:1.以上数据使用再生砂,脱模时间 15 分钟左右。 2.树脂用量 0.9%~1.0%(加偶联剂),固化剂 GS04 用量为树脂的 25~40%。 3.检测表面硬度计型号为 SYS 型砂型表面硬度计。
表 6 是固化剂品种与气候温度对照表,从表 6 看出 GS04 适应 18~30℃,GS03 适应 10~18℃,GC09
适应〈10℃。
表 6 固化剂品种选择与温度对照及用量推荐表
固化剂品种
温度(℃) 用 量(树脂量的%)
GS04
18~30
15~50
GS03
10~18℃
15~50
GC09
-5℃~10℃ 20~50
〈10
下工序跟不上,砂型易开裂等
转 K2 侧架
〉25
效率低,砂型易开裂
注: 1.以上数据使用再生砂或 80%的再生砂,砂温度小于 33℃。
2.树脂用量 0.91~1.00%(加偶联剂),固化剂 GS04、GS03、GC09.
3.脱模时间从放砂开始计时。
9
3 固化剂的控制
3.1 固化剂用量与砂型质量
表 5 是固化剂用量与砂型质量对照表,从表五看出 GS04 的用量应不低于 10%,GS03 的用量应不低
于 12%,GC09 的用量应不低于 15%。
表5
固化剂用量与砂型质量对照表
固化剂品种 用量(%)
砂型质量
固化剂品种
用量 (树脂量%)
砂型质量
GS04
<12
固化不匀,强度不好 GS03
>15
正常
15
好
14
好
12
好
10
砂型上表面易掉砂
8
砂型易开裂,砂型表面粘模
7
砂型易裂断,砂型表面粘模
35
砂型易开裂
30
砂型易开裂
25
好
20
好
15
好
14
好
12
好
10
砂型上表面易掉砂
8
砂型易开裂,砂型表面粘模
7
砂型易裂断,砂型表面粘模
注: 1.以上数据使用再生砂或 80%的再生砂,砂温度小于 33℃。 2.树脂 FL105 用量 0.9%~1.0%(加偶联剂),固化剂 GS04、GS03、GC09 用量为树脂的 25~40%。 3.脱模时间从放砂开始计时。
呋喃树脂砂硬化控制的现场实践
南方汇通股份有限公司 张明富 摘 要:为了最大程度提高呋喃树脂砂生产的效率,本文根据南方汇通股份有限公司铸工车间呋喃树脂 砂无箱造型工艺的现场应用情况,简述了呋喃树脂砂硬化控制的现场应用实践。 关键词: 呋喃树脂砂 硬化现场控制 脱模 砂型质量 生产效率
1 一般情况下的脱模控制
1.1 金属模不加热时的脱模 表 1 是在 18℃~30℃及湿度在 70%左右时铁路货车大部件(转 K2 型侧架)脱模情况现场采集的
典型数据,从表一看出,侧架第一型因模型为冷模具,脱模应控制表面硬度在 85 左右;从第二型起脱 模即可控制表面硬度在 70 左右。
表1
转 K2 侧架第一型脱模情况
砂型表 面硬度
2.2 呋喃树脂砂脱模时间与生产节拍
生产线上固化剂品种及加入量一旦设定,就确定了呋喃树脂砂固化速率,也就确定了脱模时间范
围,表四是车间主要上线产品侧架的呋喃树脂砂工艺脱模时间与生产节拍对照表。
表4
呋喃树脂砂脱模时间与生产节拍对照表
砂型名称
脱模时间范围(分钟)
生产节拍情况
转 K2 侧架
10~25
正常
转 K2 侧架
注:1.以上数据使用再生砂或 80%的再生砂,砂温度度-5℃~35℃。 2.树脂用量 0.9~1.0%(加偶联剂)。
4 结论
为有效控制呋喃树脂砂的硬化而得到良好的砂型质量及最佳的生产节拍,并稳定较低的树脂、固
化剂加入量,可从下几方面开展进行控制:对传热快的模具(如金属模)开工前应进行预加热;根据气
温合理选用固化剂;控制好固化剂加入量及脱模时间。