丁辛醇的合成
丁辛醇生产技术及其发展趋势
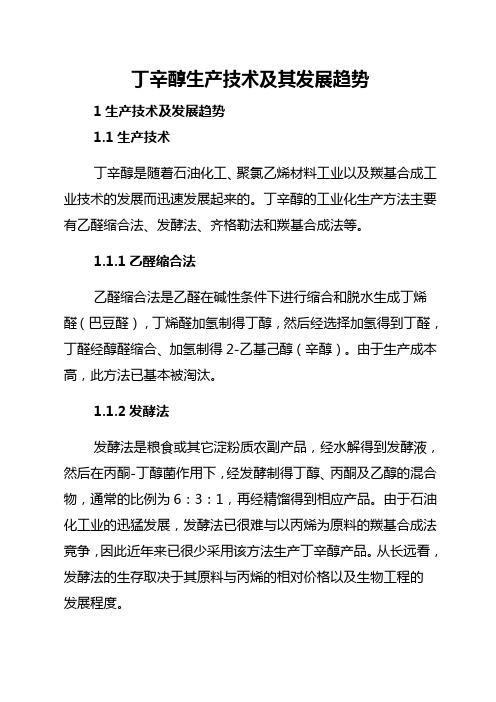
丁辛醇生产技术及其发展趋势1生产技术及发展趋势1.1生产技术丁辛醇是随着石油化工、聚氯乙烯材料工业以及羰基合成工业技术的发展而迅速发展起来的。
丁辛醇的工业化生产方法主要有乙醛缩合法、发酵法、齐格勒法和羰基合成法等。
1.1.1乙醛缩合法乙醛缩合法是乙醛在碱性条件下进行缩合和脱水生成丁烯醛(巴豆醛),丁烯醛加氢制得丁醇,然后经选择加氢得到丁醛,丁醛经醇醛缩合、加氢制得2-乙基己醇(辛醇)。
由于生产成本高,此方法已基本被淘汰。
1.1.2发酵法发酵法是粮食或其它淀粉质农副产品,经水解得到发酵液,然后在丙酮-丁醇菌作用下,经发酵制得丁醇、丙酮及乙醇的混合物,通常的比例为6:3:1,再经精馏得到相应产品。
由于石油化工业的迅猛发展,发酵法已很难与以丙烯为原料的羰基合成法竞争,因此近年来已很少采用该方法生产丁辛醇产品。
从长远看,发酵法的生存取决于其原料与丙烯的相对价格以及生物工程的发展程度。
1.1.3齐格勒法齐格勒丁辛醇生产方法是以乙烯为原料,采用齐格勒法生产高级脂肪醇,同时副产丁醇的方法。
1.1.4羰基合成法羰基合成法是当今最主要的丁辛醇生产技术。
丙烯羰基合成生产丁辛醇工艺过程:丙烯氢甲酰化反应,粗醛精制得到正丁醛和异丁醛,正丁醛和异丁醛加氢得到产品正丁醇和异丁醇;正丁醛经缩合、加氢得到产品辛醇。
丙烯羰基合成法又分为高压法、中压法和低压法。
丙烯羰基合成法的主流技术专利商如下:高压法:鲁尔 (Ruhr)技术、巴斯夫(BASF)技术、三菱(MCC)技术、壳牌(Shell)技术。
中压法:壳牌(Shell)技术、鲁尔-化学(Ruhr-chemic)技术、三菱(MCC)铑法技术。
低压法:雷普法(Reppe)技术、伊士曼(Eastman)技术、戴维(Davy UCC Johnson Matthey)技术、三菱化成(MCC)技术。
高压的羰基合成技术由于选择性较差、副产品(丙烷和高沸物)多,已被以铑为催化剂的低压羰基合成技术所取代。
低压羰基合成丁辛醇工艺技术

低压羰基合成丁辛醇工艺技术摘要:低压羰基合成法是目前生产丁辛醇的主要方法。
世界上羰基合成丁醛装置中,低压羰基合成工艺技术占55%。
丁辛醇装置以丙烯、合成气为原料,采用Davy/DOW低压羰基合成工艺技术生产2-乙基己醇和正丁醇,同时副产异丁醇,设计年运行时间为8000小时,操作弹性为60%~110%。
关键词:低压羰基;丁辛醇;工艺技术;分析引言:丁辛醇装置采用世界较为先进的LP OxoSM SELECTORSM 10液体循环技术,生产2-乙基己醇(俗称辛醇)和正丁醇,它以丙烯和合成气为原料,在铑、三苯基膦催化剂的作用下,发生羰基合成反应生成混合丁醛,丁醛经过丁醛异构物分离得到高纯度正丁醛,在0.2×10-2mol的NaOH溶液作用下,发生缩合反应生成辛烯醛,辛烯醛在铜催化剂作用下与H2发生加氢反应生成粗辛醇,再经过精制后得到产品辛醇;混合丁醛加氢后得到粗混合丁醇,经过预精馏和精馏系统进入丁醇异构物塔。
丁醇异构物塔顶分离出的混合丁醛也可直接进行异构物分离得到正丁醛和异丁醛,异丁醛直接外送至界外,正丁醛经加氢、精制后,得到产品正丁醇。
1.低压羰基合成丁辛醇技术七十年代中期,美国UCC公司、英国DAVY公司和J.M公司合作开发了铑膦催化体系─低压羰基合成工艺。
压力1.6-1.8MPa,正异比高达10:1~12:1,基建投资和生产成本均低于高、中压羰基合成技术。
1.1气相法将催化剂加入并联的两台反应器中,丙烯、合成气按一定比例分别从反应器和分馏塔底部进入。
产品由循环气带出,经冷凝、分离后,由分馏塔底部采出,过量气体循环进入反应系统,催化剂留在反应器内直至失效取出再生。
因该羰基合成反应为气相反应,故称气相法。
1.2液相法液相法是以丙烯、合成气为原料,以铑为催化剂生产丁辛醇的低压羰基合成法,是低压羰基合成的进一步改进。
其优点是:一是反应器容积小,产率高;二是原料单耗降低;三是成本及能耗降低;四是催化剂使用形式为活性循环型;五是反应温度低,可用于生产高碳醇。
丁辛醇合成工艺评价及选择

丁辛醇合成工艺评价及选择摘要:本文介绍了合成丁辛醇技术,对丁辛醇装置主要专利技术的特点做了评价,并举例炼油化工一体化企业中建设丁辛醇装置技术选择及总体平衡。
关键词:羰基法丁辛醇工艺技术炼化一体化一、概述丁辛醇是重要的基本有机原料,包括正丁醇、异丁醇和辛醇(或称2-乙基己醇)三个重要品种。
正丁醇可作溶剂、生产邻苯二甲酸二丁脂、醋酸丁脂、磷酸脂类增塑剂、丁醛、丁酸、丁胺和和乳酸丁酯等化工产品。
异丁醇可以用于生产石油添加剂、抗氧剂、醋酸异丁酯等有机产品;辛醇主要用于制造邻苯二甲酸二辛酯(dop)和对苯二甲酸二辛酯,还用于柴油添加剂、合成润滑剂、抗氧剂、溶剂、消泡剂等。
二、丁辛醇生产工艺情况丁辛醇的工业化生产方法主要有乙醛缩合法、发酵法、齐格勒法和羰基合成法等。
1.乙醛缩合法二战期间,德国开发了乙醛缩合法(aldol)法。
利用乙醛在碱性条件下进行缩合和脱水,生产丁烯醛(巴豆醛),丁烯醛加氢制得丁醇,丁醇经选择性加氢得到丁醛,丁醛经醇醛缩合、加氢制得辛醇。
由于此方法工艺流程长、收率低、生产成本高,现已基本被淘汰。
2.发酵法利用粮食或其它淀粉农副产品,经水解得到发酵醇,然后在丙酮-丁醇菌作用下,经发酵制得丁醇、丙酮及乙醇的混合物,再经精馏得到相应的产品。
由于近几十年石油化工的高速发展,发酵法已经难于以丙烯为原料的羰基合成法竞争,因此近年来很少采用该方法生产丁辛醇产品。
3.齐格勒法该方法以乙烯为原料,利用齐格勒法(ziegler)生产高级脂肪醇,同时副产丁醇的方法。
4.羰基合成法羰基合成法主要以丙烯与合成气(一氧化碳和氢气)为原料生产丁辛醇,其主要工艺过程为①丙烯氢甲酰化反应,粗醛精制得到正丁醛和异丁醛;②正丁醛和异丁醛加氢得到产品正丁醇和异丁醇;③正丁醛经缩合,加氢得到产品辛醇。
④进行反应生成丁醛,加氢得到丁醇。
丙烯羰基合成法又分为高压法、中压法和低压法。
4.1高压法高压法羰基合成技术是四十年代开发成功的,六十年代建了大量装置,主要技术专利商有鲁尔(ruhr)技术、巴斯夫(basf)技术、三菱(mcc)技术、壳牌(shell)技术。
丁辛醇生产工艺
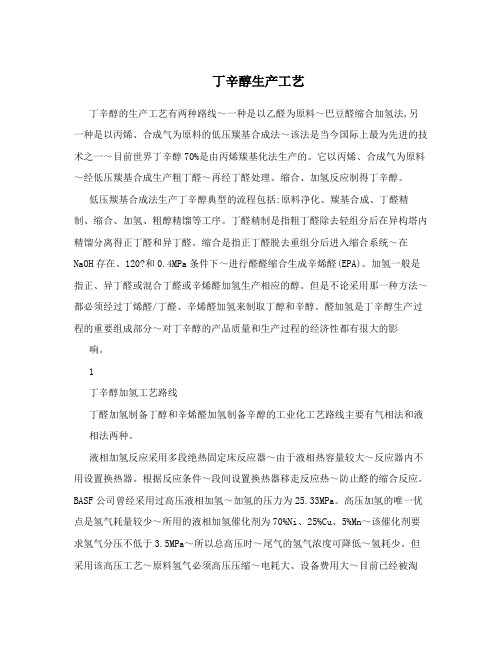
丁辛醇生产工艺丁辛醇的生产工艺有两种路线~一种是以乙醛为原料~巴豆醛缩合加氢法,另一种是以丙烯、合成气为原料的低压羰基合成法~该法是当今国际上最为先进的技术之一~目前世界丁辛醇70%是由丙烯羰基化法生产的。
它以丙烯、合成气为原料~经低压羰基合成生产粗丁醛~再经丁醛处理、缩合、加氢反应制得丁辛醇。
低压羰基合成法生产丁辛醇典型的流程包括:原料净化、羰基合成、丁醛精制、缩合、加氢、粗醇精馏等工序。
丁醛精制是指粗丁醛除去轻组分后在异构塔内精馏分离得正丁醛和异丁醛。
缩合是指正丁醛脱去重组分后进入缩合系统~在NaOH存在、120?和0.4MPa条件下~进行醛醛缩合生成辛烯醛(EPA)。
加氢一般是指正、异丁醛或混合丁醛或辛烯醛加氢生产相应的醇。
但是不论采用那一种方法~都必须经过丁烯醛/丁醛、辛烯醛加氢来制取丁醇和辛醇。
醛加氢是丁辛醇生产过程的重要组成部分~对丁辛醇的产品质量和生产过程的经济性都有很大的影响。
1丁辛醇加氢工艺路线丁醛加氢制备丁醇和辛烯醛加氢制备辛醇的工业化工艺路线主要有气相法和液相法两种。
液相加氢反应采用多段绝热固定床反应器~由于液相热容量较大~反应器内不用设置换热器。
根据反应条件~段间设置换热器移走反应热~防止醛的缩合反应。
BASF公司曾经采用过高压液相加氢~加氢的压力为25.33MPa。
高压加氢的唯一优点是氢气耗量较少~所用的液相加氢催化剂为70%Ni、25%Cu、5%Mn~该催化剂要求氢气分压不低于3.5MPa~所以总高压时~尾气的氢气浓度可降低~氢耗少。
但采用该高压工艺~原料氢气必须高压压缩~电耗大、设备费用大~目前已经被淘汰。
BASF公司和三菱化成工艺中醛的加氢采用中压液相加氢工艺~加氢压力为4.0-5.0MPa~加氢反应器形式采用填充床~反应温度为60-190?。
气相加氢法由于操作压力相对较低~工艺设备简单而被广泛应用。
目前~工业上丁辛醇装置上大多采用铜系催化剂气相加氢工艺。
如U.D.J联合工艺中采用低压气相加氢~压力为0.59-0.69MPa。
丁辛醇的生产工艺与技术路线的选择

丁/辛醇的生产工艺与技术路线的选择2.1 丁辛醇生产方法丁辛醇是随着石油化工、聚氯乙烯材料工业以及羰基合成工业技术的发展而迅速发展起来的。
丁辛醇的工业化生产方法主要有乙醛缩合法、发酵法、齐格勒法和羰基合成法等。
2.1.1乙醛缩合法二战期间,德国开发了乙醛缩合法(Aldo1)法。
……2.1.2发酵法发酵法是粮食或其它淀粉质农副产品,经水解得到发酵液,然后在丙酮-丁醇菌作用下,经发酵制得丁醇、丙酮及乙醇的混合物,通常的比例为……2.1.3齐格勒法齐格勒丁辛醇生产方法是以乙烯为原料,采用齐格勒法生产高级脂肪醇,同时副产丁醇的方法。
2.1.4羰基合成法……2.2 丁辛醇生产工艺技术比较及选择2.2.1 国外丁辛醇生产工艺对比……丁辛醇主要生产工艺的比较见表2.1。
表2.1 丁辛醇主要生产工艺的比较关于丁辛醇生产的几种主要工艺技术方法列表如下。
表2.2 丁辛醇工艺技术方案对比表2.2.2 国外丁辛醇生产工艺选择……2.3 丁辛醇合成工艺技术进展及发展趋势2.3.1 国外丁辛醇合成工艺技术进展丁醇和辛醇是用途广泛的重要精细化工原料,随着生产规模的不断扩大,丁辛醇技术发展重点集中在合成工艺和催化剂的研究和开发上,国外生产商改进丁辛醇合成工艺形成了各具特色的专有技术,引起了业内人士的极大关注。
……2.3.2 国内丁辛醇合成工艺技术进展……2.3.3 国内丁辛醇合成工艺技术发展趋势随着世界经济全球化及规模生产经济最大化,丁辛醇工业发展的重点将集中在催化剂的研究和开发上。
其技术发展趋势是:……2.4 丁辛醇质量指标2.4.1 丁醇质量指标工业正丁醇:执行标准:GB/T 6027/1998,该标准适用于合成法与发酵法生产的工业正丁醇。
要求:外观:透明液体,无可见杂质。
表2.3 正丁醇质量指标项目指标分析方法优等品一等品合格品色度,Hazen单位(铂-钴色号)≤10 15 GB/T3143密度(20℃)g/cm30.809~0.811 0.808~0.812 GB/T4472 沸程(0℃,101.325Kpa)包括(117.7℃),℃≤ 1.0 2.0 3.0 GB/T7534 正丁醇含量,% ≥99.5 99.0 98.0 色谱法硫酸显色试验(铂-钴色号)≤20 40 比色法酸度(以乙酸计),% ≤0.003 0.005 0.01 容量法水分,% ≤0.1 0.2 GB/T6283 蒸发残渣,% ≤0.003 0.005 0.01 重量法2.4.2 辛醇质量指标辛醇:执行标准:GB/T 6818/1993,本标准适用于由丙烯羰基合成法及乙醛缩合法制得的工业辛醇。
丁辛醇的成分
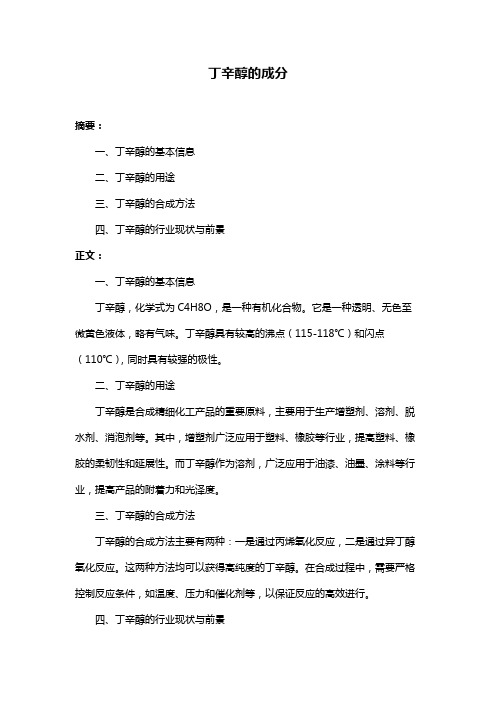
丁辛醇的成分
摘要:
一、丁辛醇的基本信息
二、丁辛醇的用途
三、丁辛醇的合成方法
四、丁辛醇的行业现状与前景
正文:
一、丁辛醇的基本信息
丁辛醇,化学式为C4H8O,是一种有机化合物。
它是一种透明、无色至微黄色液体,略有气味。
丁辛醇具有较高的沸点(115-118℃)和闪点(110℃),同时具有较强的极性。
二、丁辛醇的用途
丁辛醇是合成精细化工产品的重要原料,主要用于生产增塑剂、溶剂、脱水剂、消泡剂等。
其中,增塑剂广泛应用于塑料、橡胶等行业,提高塑料、橡胶的柔韧性和延展性。
而丁辛醇作为溶剂,广泛应用于油漆、油墨、涂料等行业,提高产品的附着力和光泽度。
三、丁辛醇的合成方法
丁辛醇的合成方法主要有两种:一是通过丙烯氧化反应,二是通过异丁醇氧化反应。
这两种方法均可以获得高纯度的丁辛醇。
在合成过程中,需要严格控制反应条件,如温度、压力和催化剂等,以保证反应的高效进行。
四、丁辛醇的行业现状与前景
随着我国经济的快速发展,对塑料、橡胶、涂料等行业的需求不断增加,丁辛醇的市场需求也随之增长。
近年来,我国丁辛醇产业呈现出规模扩大、产能提高、产品多样化的趋势。
同时,行业竞争也日益激烈,企业需要不断提高生产技术、降低成本,以应对市场竞争。
展望未来,随着环保法规的日益严格,绿色、环保型丁辛醇产品将受到更多关注。
此外,随着科研技术的进步,丁辛醇在新领域的应用也将不断拓展,为行业发展提供新的机遇。
丁辛醇产业将继续朝着高效、环保、多元化的方向发展。
总之,丁辛醇作为一种重要的精细化工原料,在塑料、橡胶、涂料等行业具有广泛应用。
丁辛醇生产工艺

丁辛醇生产工艺
丁辛醇的生产工艺有两种路线:
一种是以乙醛为原料,巴豆醛缩合加氢法;
另一种是以丙烯、合成气为原料的低压羰基合成法。
该法是当今国际上最为先进的技术之一,目前世界丁辛醇70%是由丙烯羰基化法生产的。
它以丙烯、合成气为原料,经低压羰基合成生产粗丁醛,再经丁醛处理、缩合、加氢反应制得丁辛醇。
低压羰基合成法生产丁辛醇典型的流程包括:原料净化、羰基合成、丁醛精制、缩合、加氢、粗醇精馏等工序。
丁醛精制是指粗丁醛除去轻组分后在异构塔内精馏分离得正丁醛和异丁醛。
缩合是指正丁醛脱去重组分后进入缩合系统,在NaOH存在、120?和0.4MPa条件下,进行醛醛缩合生成辛烯醛(EPA)。
加氢一般是指正、异丁醛或混合丁醛或辛烯醛加氢生产相应的醇。
但是不论采用那一种方法,都必须经过丁烯醛/丁醛、辛烯醛加氢来制取丁醇和辛醇。
醛加氢是丁辛醇生产过程的重要组成部分,对丁辛醇的产品质量和生产过程的经济性都有很大的影响。
丁辛醇生产工艺
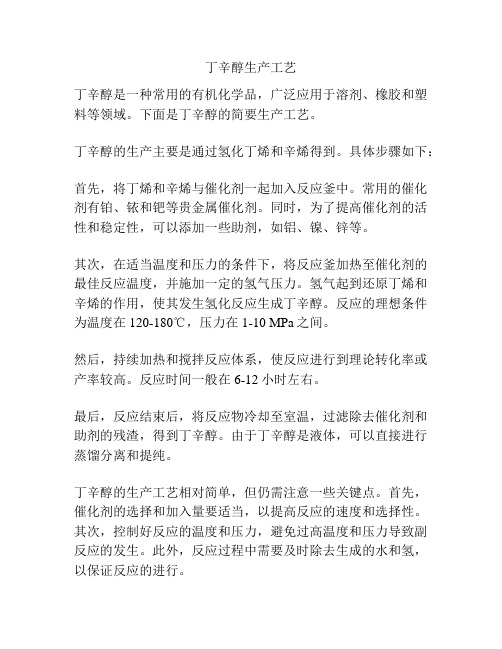
丁辛醇生产工艺
丁辛醇是一种常用的有机化学品,广泛应用于溶剂、橡胶和塑料等领域。
下面是丁辛醇的简要生产工艺。
丁辛醇的生产主要是通过氢化丁烯和辛烯得到。
具体步骤如下:
首先,将丁烯和辛烯与催化剂一起加入反应釜中。
常用的催化剂有铂、铱和钯等贵金属催化剂。
同时,为了提高催化剂的活性和稳定性,可以添加一些助剂,如铝、镍、锌等。
其次,在适当温度和压力的条件下,将反应釜加热至催化剂的最佳反应温度,并施加一定的氢气压力。
氢气起到还原丁烯和辛烯的作用,使其发生氢化反应生成丁辛醇。
反应的理想条件为温度在120-180℃,压力在1-10 MPa之间。
然后,持续加热和搅拌反应体系,使反应进行到理论转化率或产率较高。
反应时间一般在6-12小时左右。
最后,反应结束后,将反应物冷却至室温,过滤除去催化剂和助剂的残渣,得到丁辛醇。
由于丁辛醇是液体,可以直接进行蒸馏分离和提纯。
丁辛醇的生产工艺相对简单,但仍需注意一些关键点。
首先,催化剂的选择和加入量要适当,以提高反应的速度和选择性。
其次,控制好反应的温度和压力,避免过高温度和压力导致副反应的发生。
此外,反应过程中需要及时除去生成的水和氢,以保证反应的进行。
总结起来,丁辛醇的生产主要是通过氢化丁烯和辛烯得到,条件是适当温度和压力下,在催化剂的作用下进行反应。
这种生产工艺简单可行,但仍需要注意控制好关键条件,以提高产率和纯度。
- 1、下载文档前请自行甄别文档内容的完整性,平台不提供额外的编辑、内容补充、找答案等附加服务。
- 2、"仅部分预览"的文档,不可在线预览部分如存在完整性等问题,可反馈申请退款(可完整预览的文档不适用该条件!)。
- 3、如文档侵犯您的权益,请联系客服反馈,我们会尽快为您处理(人工客服工作时间:9:00-18:30)。
二、(丁)辛醇的合成丁醇和辛醇(2-乙基己醇)是有机合成中间体,丁醇用作树脂、油漆和粘接剂的溶剂和制造增塑剂、消泡剂、洗涤剂、脱水剂和合成香料的原料;辛醇主要用于制造邻-二甲酸二辛酯、癸二酸二辛酯、磷酸三辛酯等增塑剂,还用作油漆颜料的分散剂、润滑油的添加剂、杀虫剂和印染等工业的消泡剂。
丁辛醇可用乙炔、乙烯或丙烯和粮食为原料进行生产。
各种生产方法的简单过程如表5-5-01所示。
以乙烯为原料的乙醛缩合法步骤多,生产成本高,且有严重的汞污染。
现在只有少数国家采用;以丙烯为原料的氢甲酰化法原料价格便宜,合成路线短,是目前生产丁醇和辛醇的主要方法。
以丙烯为原料经氢甲酰化生产丁醇和辛醇,主要包括下列3个反应过程:a.在金属羰基络合物催化剂作用下,丙烯氢甲酰化合成丁醛:CH3CH=CH2+CO+H2→CH3CH2CHOb.丁醛在碱催化剂作用下缩合为辛烯醛:表5-5-01 丁辛醇的生产路线c.辛烯醛加氢合成2-乙基己醇在反应(a)中,丙烯氢甲酰化有高压和低压二种方法,低压法有一系列优点,为世界各国看好。
1.正丁醛的制备(1)化学反应主反应:CH2=CHCH3+CO+H2→CH3CH2CH2CHO平行副反应:这两个反应是衡量催化剂选择性的重要指标。
连串副反应:当丁醛过量时,在反应条件下,缩丁醇醛又能与丁醛缩合,生成环状缩醛和链状三聚物:缩丁醇醛很容易脱水生成另一种副产物烯醛:根据热力学研究,上述诸反应都为放热反应,平衡常数都很大,其中丙烯加氢生成丙烷和丙烯氢甲酰化生成异丁醛的两个副反应,平衡常数比主反应还大。
因此,选择催化剂和控制合适的反应条件相当重要。
(2)催化剂和催化机理工业上采用的有羰基钴和羰基铑催化剂2种。
①羰基钴和膦羰基钴催化剂制作羰基钴的原料有金属钴、环烷酸钴、油酸钴、硬脂酸钴和醋酸钴等,采用上述钴盐的好处是它们易溶于原料烯烃和溶剂中,可使反应在均相系统内进行。
研究表明,氢甲酰化的催化活性物种是HCo(CO)4,但它不稳定,容易分解,故用上述原料先制成Co2(CO)8,再让它转化为HCo(CO)4。
例如在3~4MPa,135~150℃下反应液中的钴粉可发生以下反应生成Co2(CO)8:2Co+8CO====Co2(CO8)△H0=-462 kJ/mol然后再进一步与氢作用转化为HCo(CO)4Co2(CO)8+H2=====2HCo(CO)4若以钴盐为原料,在反应液中,Co2+先由H2还原为零价钴,然后按上述反应过程转化为活性物种HCo(CO)4。
反应系统中Co2(CO)8和HCo(CO)4的比例由反应温度和氢分压决定:平衡常数K与温度的关系为:K=1.365-1900/ T在工业上采用的反应条件下,两者之间的比例大致相等。
Co2(CO)8虽比HCo(CO)2稳定,但在低CO分压下,也会发生分解:Co2(CO)8--à2Co↓+8CO因此,保持一定的CO分压,不仅对氢甲酰化反应是必需的,对稳定催化体系同样也是必需的。
为使Co2(CO)8不分解,在操作条件下(140~180℃),CO的分压因达到8MPa才行。
原料丙烯中有二氧化碳、水、氧等杂质会使金属钴钝化,为此要求氧含量<1%;某些硫化物如氧硫化碳(COS)、硫化氢、不饱和硫醚、硫醇、二硫化碳和元素硫等,会使催化剂中毒,为此要求原料中硫含量小于10 ppm。
羰基钴参与氢甲酰化的机理可描述如下:HCo(CO)4====H〖AKC·〗o(CO)3+CO上列活性基团与烯烃配位生成π-络合物.生成的π-络合物转变为配位不饱和烷基三羰基钴,后者与CO结合生成烷基羰基钴:然后烷基羰基钴中的1个CO基转移到烷基上形成C-Co 键,得到酰基三羰基钴配位不饱和化合物:后者按下列反应之一生成酰基羰基钴酰基羰基钴按如下反应之一生成醛:可发生异构化,并转化为正丁醛:因此,降低CO分压和增加H2分压对生成正构醛有利,但CO分压不能降得很低,否则催化剂会分解析出金属钴。
在高压下CO可使Co2(CO)7转化为Co2(CO)8:Co2(CO)7+CO=====Co2(CO)8从而完成1个催化循环。
由以上叙述可知,羰基钴催化剂的主要缺点是热稳定性差,为不使催化剂分解需在高的CO分压下操作,而且产品中正/异丁醛比例较低。
为提高催化剂的稳定性和选择性,在研究羰基钴催化剂的基础上发展了膦羰基钴催化剂。
膦羰基钴催化剂是将施主配位基,如膦(PR3)、亚磷酸酯(P(OR)3)、胂(AsR3)、月弟(SbR3)(R可以是烷基、芳基、环烷基或杂环基)等取代HCo(CO)4中的CO基,例如HCo(CO)3[P(nC4H9)3]等。
它一方面可增强催化剂的热稳定性,另一方面又可提高对直链正构醛的选择性。
此外还具有加氢活性高、生成的副产物少等优点,但对不同原料烯烃氢甲酰化的适应性差。
②膦羰基铑催化剂用铑取代钴,再加上膦基的功能,使膦羰基铑的活性高出羰基钴102~104倍,正/异醛的比例也高达9~16∶1,早期使用Rh4(CO)12催化剂,正/异醛比例仅为1∶1,后用有机膦配位基取代部分羰基,活性和选择性都达到一个高水平,催化剂稳定,能在较低CO压力下操作,并能忍受150℃高温和1.87 kPa真空蒸馏,能反复使用。
此催化剂母本商品名ROPA,结构式为:在反应条件下ROPA与过量的三苯基膦和CO,H2反应生成一组呈平衡的络合物:其中的HRh(CO)2(pph3)2和HRh(CO)(pph3)3被认为是催化剂的活性物种,三苯基膦(pph3)浓度大,对活性组分生成有利。
膦羰基钴催化机理与羰基钴基本相同,可用图5-5-01表示。
催化剂分子中的L为pph3或PBu3(Ph-苯基,Bu-丁基)。
上述3种催化剂的性能比较见表5-5-02。
表5-5-02 三种氢甲酰化催化剂性能比较催化剂HCo(CO)4HCo(CO)3P(nC4H9)3HRh(CO)(pph3)3温度,℃压力,Mpa催化剂浓度,%生成烷烃量产物正/异比140-18020-300.1-1.0低醛/醇3~4∶1160-2005-100.6明显醇/醛8~9∶190-1101- 20.01-0.1低醛12~15∶1由表5-5-02可以看到,膦羰基铑催化剂的性能是十分优越的。
(3)工艺条件的讨论①反应温度图5-5-03 丙烯氢甲酰化副产物生成量与温度的关系催化剂 HCo(CO)4图5-5-02 温度对丙烯氢甲酰化产物中正/异醛比的影响催化剂HCo(CO)4图5-5-04 温度与丙烯转化率和正/异醛比的关系催化剂\ Rh(pph32CoCl反应温度对反应速度,产物醛的正/异比率和副产物的生成量都有影响,温度升高,反应速度加快,但正/异醛比率随之降低,重组分和醇的生成量随之增加。
图5-5-02,图5-5-03和图5-5-04示出了温度对丙烯氢甲酰化的影响。
图5-5-02是对正/异醛比率的影响;图5-5-03是对副产物生成量的影响;图5-5-04是对丙烯转化率和正/异醛比率的影响。
因此,反应温度不宜过高,使用羰基钴催化剂时,一般控制在140~180℃,使用膦羰基铑催化剂时一般控制在100~110℃,并且要求反应器有良好的传热条件以防止局部反应区域的反应温度过高②CO分压,H2分压和总压丙烯氢甲酰化动力学方程为:在羰基钴催化剂上得到的动力学方程与此类似。
由上列动力学方程知,CO分压低,对反应速度有利。
但催化剂在低CO分压下会分解,因此,对羰基钴催化剂而言,温度为150~160℃,催化剂浓度为0.9%(w)左右时,CO分压要求达到10MPa,对膦羰基铑催化剂在110~120℃时,需1.0MPa;CO分压对正/异醛比率也有影响,随着CO分压增加,正/异醛比率下降;氢分压增高,反应速度加快,烯烃转化率提高,正/异醛比率上升。
但氢分压增高,也促进副反应,使副产物增多,结果反使醛的收率下降。
图5-5-05示出了H2/CO对产物分布的影响,图5-5-06示出氢分压对正/异醛比率的影响,由两图可以得出,H2分压要适宜。
工业上一般采用H2/CO=1∶1(摩尔比)。
由动力学方程知道,当H2/CO=1∶1时,反应速度与总压无关,但总压对正/异醛的比率仍有影响,对膦羰基铑催化剂而言,总压升高,正/异醛比率开始下降较快,但当压力达到4.5MPa后,下降极其缓慢,对羰基钴催化剂而言,总压升高,正/异醛比率则是上升的,但高沸物也随着增多。
图5-5-05 n(H2)/n(CO)比对丙烯氢甲酰化产物中醛/醇分布的影响曲线催化剂 HCo(CO)4,总压不变1-醛;2-醇图5-5-06 氢分压对丙烯氢甲酰化产物中正/异醛比率的影响●温度 110℃ Pco 10MPa○温度90℃ Pco 6.8MPa催化剂Rh(pph3)2CoCl③溶剂氢甲酰化常要用溶剂。
溶剂的作用有:a.溶解催化剂;b.当原料是气态烃时,使用溶剂能使反应在液相中进行,对气-液间传质有利;c.用作稀释剂可以带走反应热以利反应温度的控制。
常用的溶剂有脂肪烃、环烷烃、芳烃,各种醚类、酯、酮和脂肪醇等。
工业生产中为方便起见常用产品本身或其高沸点副产物作溶剂或稀释剂。
溶剂对氢甲酰化的影响示于表5-5-03。
由表5-5-03可见,采用非极性溶剂能提高正丁醛的产量。
表5-5-03 丙烯在各种溶剂中氢甲酰化结果溶剂 2.2.4-苯甲苯乙醚乙醇丙酮三甲基戊烷正/4.6 4.5 4.4 4.4 3.8 3.6 异醛比图5-5-07 借Oxo合成法由丙烯制正丁醇的工艺流程示意图1.羰基化合成塔;2.催化剂分离槽;3.脱气塔;4.重馏分分离塔;5.丁醛分离塔;6.氢化塔;7.粗丁醇分离塔;8.丁醇精馏塔(4)生产过程和工艺流程①高压法生产正丁醛和正丁醇这是采用羰基钴催化剂经氢甲酰化生产正丁醛和正丁醇的工艺。
工艺流程示于图5-5-07。
现扼要阐述如下。
羰基合成塔中充入含3%~5%羰基钴催化剂的催化液、循环气和新鲜原料丙烯,一氧化碳及氢气按一定比例从合成塔底部通入,在140~180℃及15~30MPa 的条件下进行羰基化反应。
合成塔内装有搅拌或挡板借以提高气、液接触效率,还设有冷却盘管以除去多余的反应热。
生成的反应产物随尾气一同从塔顶出来,尾气中也常夹带一定量的催化液,经设在反应器上部的分离器回收返回反应器;反应混合物在分离槽中分离,催化液返回合成塔,其余的进入脱气塔,脱除未反应的气体;尾气从塔顶放出,利用其热量产生蒸气。
因放出的尾气中丙烯已很少,一氧化碳和氢气也基本用尽,而且杂质较多,可引出系统另作处理。
脱气塔塔釜流出的反应液,含有催化剂,需加以回收,工业上称为脱钴工序。
这是因为:a.钴是比较贵的金属,长年流失,累加的量不少,给工厂带来沉重的经济负担;b.含钴的反应液在蒸馏过程中会发生缩聚反应,生成高沸物,使醛收率下降;c.在由丁醛加氢制丁醇中,钴会使加氢催化剂中毒。