快速成型技术的发展历史
快速成型技术在制造业中的应用
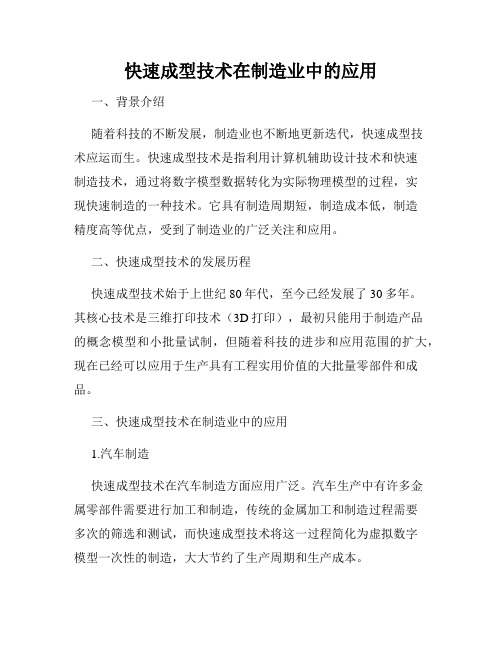
快速成型技术在制造业中的应用一、背景介绍随着科技的不断发展,制造业也不断地更新迭代,快速成型技术应运而生。
快速成型技术是指利用计算机辅助设计技术和快速制造技术,通过将数字模型数据转化为实际物理模型的过程,实现快速制造的一种技术。
它具有制造周期短,制造成本低,制造精度高等优点,受到了制造业的广泛关注和应用。
二、快速成型技术的发展历程快速成型技术始于上世纪80年代,至今已经发展了30多年。
其核心技术是三维打印技术(3D打印),最初只能用于制造产品的概念模型和小批量试制,但随着科技的进步和应用范围的扩大,现在已经可以应用于生产具有工程实用价值的大批量零部件和成品。
三、快速成型技术在制造业中的应用1.汽车制造快速成型技术在汽车制造方面应用广泛。
汽车生产中有许多金属零部件需要进行加工和制造,传统的金属加工和制造过程需要多次的筛选和测试,而快速成型技术将这一过程简化为虚拟数字模型一次性的制造,大大节约了生产周期和生产成本。
2.航空航天制造在航空航天制造领域,不仅要求制造零件的构造合理,而且要求制造零件具有足够的强度,耐热性,抗腐蚀等性能。
快速成型技术可以制造设计复杂的零件,如涡轮叶片,喷嘴等高难度零件,此外,快速成型技术还可以用于制造航空用材料,如金属陶瓷等。
3.医疗设备制造在医疗设备制造方面,快速成型技术可用于生产高精度,高品质的假肢,矫形器和外科手术器械等医疗器械,这些器械具有良好的适应性和合理性,对手术质量和病人康复起到了重要作用。
四、快速成型技术的优势1.设计复杂零件快速成型技术可以通过复杂的数字模拟模型,将复杂的结构转化成实际的三维模型,可以简化设计,控制生产周期。
2.制造周期短传统加工制造技术需要大量的时间完成整个加工制造过程,快速成型技术可以大大缩短加工周期,在保证加工精度的同时,提高生产效率。
3.制造成本低传统的加工制造技术需要大量的安装和制造机械设备,而快速成型技术为基于数字模拟的生产模式,减少了机械设备的制造和安装成本。
机械制造快速成型技术
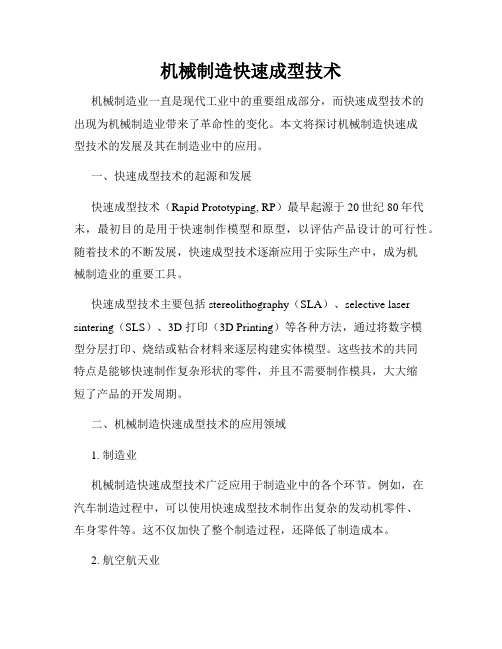
机械制造快速成型技术机械制造业一直是现代工业中的重要组成部分,而快速成型技术的出现为机械制造业带来了革命性的变化。
本文将探讨机械制造快速成型技术的发展及其在制造业中的应用。
一、快速成型技术的起源和发展快速成型技术(Rapid Prototyping, RP)最早起源于20世纪80年代末,最初目的是用于快速制作模型和原型,以评估产品设计的可行性。
随着技术的不断发展,快速成型技术逐渐应用于实际生产中,成为机械制造业的重要工具。
快速成型技术主要包括 stereolithography(SLA)、selective laser sintering(SLS)、3D 打印(3D Printing)等各种方法,通过将数字模型分层打印、烧结或粘合材料来逐层构建实体模型。
这些技术的共同特点是能够快速制作复杂形状的零件,并且不需要制作模具,大大缩短了产品的开发周期。
二、机械制造快速成型技术的应用领域1. 制造业机械制造快速成型技术广泛应用于制造业中的各个环节。
例如,在汽车制造过程中,可以使用快速成型技术制作出复杂的发动机零件、车身零件等。
这不仅加快了整个制造过程,还降低了制造成本。
2. 航空航天业航空航天是对零件质量和性能要求十分严苛的行业,而机械制造快速成型技术正好能够满足这些需求。
通过快速成型技术,可以制造出轻量化、高强度的航空零件,提高飞行器的性能。
3. 医疗器械快速成型技术在医疗器械领域也有着广泛的应用。
例如,可以通过快速成型技术制作假肢、人工关节等医疗器械,以满足不同患者的需求。
这种定制化的生产方式大大提高了治疗的效果和患者的生活质量。
三、机械制造快速成型技术的优势1. 加速产品开发周期传统的制造过程中,需要制作模具,而制作模具往往非常耗时。
而快速成型技术通过直接构建实体模型,省去了制作模具的过程,大大缩短了产品的开发周期。
2. 降低制造成本传统的制造过程中,制作模具需要大量的材料和人力资源。
而快速成型技术不需要制作模具,只需要输入数字模型即可进行生产,有效节约了成本。
“快速成型”之浅析

“快速成型”之浅析一、快速成型发展历史:快速原型制造技术,又叫快速成形技术,简称RP技术。
快速成型技术是九十年代发展起来的一项先进制造技术,是为制造业企业新产品开发服务的一项关键共性技术, 对促进企业产品创新、缩短新产品开发周期、提高产品竞争力有积极的推动作用。
自该技术问世以来,已经在发达国家的制造业中得到了广泛应用,并由此产生一个新兴的技术领域。
二、快速成型技术的原理运用:RP技术是在现代CAD/CAM技术、激光技术、计算机数控技术、精密伺服驱动技术以及新材料技术的基础上集成发展起来的。
不同种类的快速成型系统因所用成形材料不同,成形原理和系统特点也各有不同。
但是其基本原理都是一样的,那就是“分层制造,逐层叠加”,类似于数学上的积分过程。
形象地讲,快速成形系统就像是一台"立体打印机"。
三、快速成型技术的优越性:它可以在无需准备任何模具、刀具和工装卡具的情况下,直接接受产品设计数据,快速制造出新产品的样件、模具或模型。
因此,RP技术的推广应用可以大大缩短新产品开发周期、降低开发成本、提高开发质量。
由传统的“去除法”到今天的“增长法”,由有模制造到无模制造,这就是RP技术对制造业产生的革命性意义。
四、快速成型技术特点:快速成型技术将一个实体的复杂的三维加工离散成一系列层片的加工,大大降低了加工难度,具有如下特点:(1)成型全过程的快速性,适合现代激烈的产品市场;(2)可以制造任意复杂形状的三维实体;(3)用CAD模型直接驱动,实现设计与制造高度一体化,其直观性和易改性为产品的完美设计提供了优良的设计环境;(4)成型过程无需专用夹具、模具、刀具,既节省了费用,又缩短了制作周期。
(5)技术的高度集成性,既是现代科学技术发展的必然产物,也是对它们的综合应用,带有鲜明的高新技术特征。
快速成型华曙高科小编总结:快速成型技术特点决定了RP技术主要适合于新产品开发,快速单件及小批量零件制造,复杂形状零件的制造,模具与模型设计与制造,也适合于难加工材料的制造,外形设计检查,装配检验和快速反求工程等。
快速成形技术发展状况与趋势

快速成形技术发展状况与趋势快速成形技术,又称为三维打印、增材制造等,是近年来新兴的一种制造技术,它可以将数字化的设计文件转化为实体物体,而且速度快、成本低,能够满足个性化定制的需求。
该技术的发展已经引起海内外制造业的广泛关注和研究,下面介绍快速成形技术的发展状况和趋势。
快速成形技术最早出现在20世纪80年代,最初被用于快速制作模型,其发展始于CAD 设计技术、计算机组成技术以及材料工程技术的发展。
20世纪90年代以后,该技术经过不断的改良和完善,应用范围逐渐扩大,主要涉及到汽车、航空、医疗、建筑等领域。
目前,全球主要的快速成形技术公司有美国Stratasys、德国EOS、瑞典Arcam和中国沃特玛等。
近年来,随着材料科技、智能制造和数字工厂的发展,快速成形技术呈现出以下几个趋势:1. 多材料、多工艺:不同快速成形技术采用不同材料和工艺,未来发展方向是多材料、多工艺的结合。
例如,增材制造可以利用多种材料打印出复杂的组件,立体光绘可以通过多重叠加实现更高的可塑性和更精细的表面质量。
2. 智能化、网络化:快速成形技术已经与计算机、互联网和智能化制造相结合,实现了数字化和智能化的设计与制造,未来将趋向于更加智能化和网络化,实现生产和流程的自动化。
例如,智能打印机具有自我诊断和自动修复的功能,可以自主管理并调节打印参数,提高设备利用率和打印效率。
3. 个性化、定制化:快速成形技术具有快速、便捷、低成本的特点,可以实现个性化和定制化的生产,未来将趋向于更加个性化和高效化。
例如,医疗领域可以利用该技术制作个性化的医疗器械、假体和植入物,满足患者的特殊需求;商品领域可以利用该技术实现全球化生产和本地化供应,提高响应速度和市场竞争力。
4. 生态可持续、绿色制造:快速成形技术采用增材制造和材料回收等技术,可以实现生态可持续和绿色制造,未来将趋向于更加环保和节能。
例如,采用生物降解材料可以实现零污染和资源循环利用,采用能源节约技术可以减少能源消耗和碳排放。
快速成型技术概述

和其他几种快速成型方法相比,该方一法也存在着许多缺点。主要有:
三、光固化成型工艺
四、叠层实体制造工艺
叠层实体制造工艺的基本原理
四、叠层实体制造工艺
2.叠层实体制造技术的特点 其主要特点如下: ( 1 )原型精度高。 ( 2 )制件能承受高达200℃ 的温度,有较高的硬度和较好的力学性能,可进行各种切削加工。 ( 3 )无须后固化处理。 ( 4 )无须设计和制作支撑结构。 ( 5 )废料易剥离。 ( 6 )可制作尺寸大的制件。 ( 7 )原材料价格便宜,原型制作成本低。
( 1 )能承受一定高温。 ( 2 )与成型材料不浸润,便于后处理。 ( 3 )具有水溶性或者酸溶性。 ( 4 )具有较低的熔融温度。 ( 5 )流动性要好。
五、熔融沉积快速成型工艺
选择性激光烧结工艺的基本原理
当一层截面烧结完后,工作台下降一个层的厚度,铺料辊又在上面铺上一层均匀密实的粉末,进行新一层截面的烧结,直至完成整个模型。
01
1940年,Perera提出相似的方法,即沿轮廓线切割硬纸板,然后堆叠,使这些纸板形成三维地貌图。
02
1964年,Zang进一步细化了该方法,建议用透明的纸板,每一块均带有详细的地貌形态标记。
03
1972年,Matsubara使用光固化材料,光线有选择地投射或扫射到这个板层,将规定的部分硬化,没有扫描或没有一硬化的部分被某种溶剂溶化。
04
五、熔融沉积快速成型工艺
五、熔融沉积快速成型工艺
2.熔融沉积工艺的特点 熔融沉积快速成型工艺之所以被广泛应用,是因为它具有其他成型方法所不具有的许多优点。具体如下: ( 1 )由于采用了热融挤压头的专利技术,使整个系统构造原理和操作简单,维护成本低,系统运行安全。 ( 2)成型速度快。 ( 3 )用蜡成型的零件原型,可以直接用于熔模铸造。 ( 4 )可以成型任意复杂程度的零件。 ( 5 )原材料在成型过程中无化学变化,制件的翘曲变形小。 ( 6 )原材料利用率高,且材料寿命长。 ( 7 )支撑去除简单,无需化学清洗,分离容易。
快速成型技术的发展历史
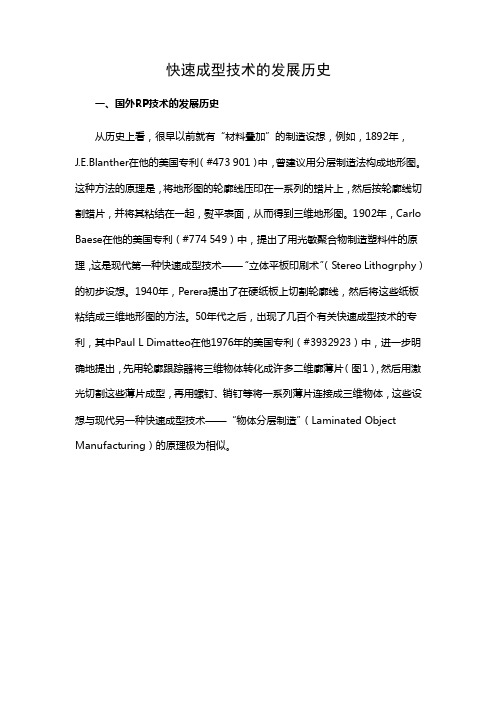
快速成型技术的发展历史一、国外RP技术的发展历史从历史上看,很早以前就有“材料叠加”的制造设想,例如,1892年,J.E.Blanther在他的美国专利(#473 901)中,曾建议用分层制造法构成地形图。
这种方法的原理是,将地形图的轮廓线压印在一系列的蜡片上,然后按轮廓线切割蜡片,并将其粘结在一起,熨平表面,从而得到三维地形图。
1902年,Carlo Baese在他的美国专利(#774 549)中,提出了用光敏聚合物制造塑料件的原理,这是现代第一种快速成型技术——“立体平板印刷术”(Stereo Lithogrphy)的初步设想。
1940年,Perera提出了在硬纸板上切割轮廓线,然后将这些纸板粘结成三维地形图的方法。
50年代之后,出现了几百个有关快速成型技术的专利,其中Paul L Dimatteo在他1976年的美国专利(#3932923)中,进一步明确地提出,先用轮廓跟踪器将三维物体转化成许多二维廓薄片(图1),然后用激光切割这些薄片成型,再用螺钉、销钉等将一系列薄片连接成三维物体,这些设想与现代另一种快速成型技术——“物体分层制造”(Laminated Object Manufacturing)的原理极为相似。
图1 Paul的分层成型法上述早期的专利虽然提出了一些快速成型的原理,但还很不完整,更没有实现快速成型机械及其使用原材料的商品化。
80年代末之后,快速成型技术有了根本性的发展,出现的专利更多,仅在1986~1998年期间注册的美国专利就有24个。
这首先是Charles W Hull在他1986年的美国专利(#4 575 330)中,提出了一个用激光束照射液态光敏树脂,从而分层制作三维物体的现代快速成型机的方案。
随后,美国的3D Systems公司据此专利,于1988年生产出了第一台现代快速成型机SLA-250(液态光敏树脂选择性固化成型机),开创了快速成型技术发展的新纪元。
在伺候的10年中,涌现了10多种不同形式的快速成型技术和相应的快速成型机,如薄形材料选择性切割(LOM)、丝状材料选择性熔覆(FDM)和粉末材料选择性烧结(SLS)等,并且在工业、医疗及其他领域得到了广泛到的应用。
快速成型技术介绍

1、新产品研制开发阶段的试验验证 2、新产品投放市场前的调研和宣传 3、基于快速成型技术的快速制模(RT)技术 由于RP方法对使用材料的限制,并不能够完全替代 最终的产品。在新产品功能检验、投放市场试运行和准确 获得用户使用后的反馈信息等方面,仍需要由实际材料制 造的产品。因此, 需要利用RP原型作母模来翻制模具, 这便产生了基于RP的快速模具制造技术(RT)。 RP+RT技术提供了一条从模具的CAD模型直接制造 模具的新概念和方法。它将模具的概念设计和加工工艺集 成在一个CAD/CAM系统内,并行工程的应用,为信息 流的畅通流动创造了良好的条件。
图12、FDM快出成型支撑结构图
三、快速成型技术的应用
快速成型技术的最初应用主要集中在产品开发中的设 计评价、 功能试验上。 设计人员根据快速成型得到的试 件原型对产品的设计方案进行试验分析、 性能评价 ,借此 缩短产品的开发周期、 降低设计费用。经过十几来的发 展 ,快速成型技术早已突破了其最初意义上的 “原型” 概 念 ,向着快速零件、 快速工具等方向发展。 目前RP技术已得到了工业界的普遍关注, 尤其在家用 电器、汽车、玩具、轻工业产品、建筑模型、医疗器械及 人造器官模型、航天器、军事装备、考古、工业制造、雕 刻、电影制作以及从事CAD 的部门都得到了良好的应用. 其用途主要体现在以下6个方面。
加热丝状材料喷头扫描并喷出半流动状材料材料固化图9fdm原理图喷头是实现fdm工艺的关键部件喷头结构设计和控制方法是否合理直接关系到成型过程能否顺利进行并影响成型的质量另一方面为了提高生产效率可以采用多喷头美国3d公司推出的actua2100其喷头数多达96个
快速成型技术
一、快速成型技术概述 二、快速成型技术加工方法和设备 三、快速成型技术的应用 四、快速成型技术中的问题 五、展望
快速成型技术及其发展综述

计算机集成制造技术与系统——读书报告题目名称:专业班级:学号:学生姓名:指导老师快速成型技术及其发展摘要:快速成型技术兴起于20世纪80年代,是现代工业发展不可或缺的一个重要环节。
本文介绍了快速成型技术的产生、技术原理、工艺特点、设备特点等方面,同时简述快速成型技术在国内的发展历程。
关键词:快速成型烧结固化叠加发展服务1 快速成形技术的产生快速原型(Rapid Prototyping,RP)技术,又称快速成形技术,是当今世界上飞速发展的制造技术之一。
快速成形技术最早产生于二十世纪70年代末到80年代初,美国3M公司的阿伦赫伯特于1978年、日本的小玉秀男于1980年、美国UVP公司的查尔斯胡尔1982年和日本的丸谷洋二1983年,在不同的地点各自独立地提出了RP的概念,即用分层制造产生三维实体的思想。
查尔斯胡尔在UVP的继续支持下,完成了一个能自动建造零件的称之为Stereolithography Apparatus (SLA)的完整系统SLA-1,1986年该系统获得专利,这是RP发展的一个里程碑。
同年,查尔斯胡尔和UVP的股东们一起建立了3D System公司。
与此同时,其它的成形原理及相应的成形系统也相继开发成功。
1984年米歇尔法伊杰提出了薄材叠层(Laminated Object Manufacturing,以下简称LOM)的方法,并于1985年组建Helisys 公司,1992年推出第一台商业成形系统LOM-1015。
1986年,美国Texas大学的研究生戴考德提出了选择性激光烧结(Selective Laser Sintering,简称SLS)的思想,稍后组建了DTM 公司,于1992年开发了基于SLS的商业成形系统Sinterstation。
斯科特科瑞普在1988年提出了熔融成形(Fused Deposition Modeling,简称FDM)的思想,1992年开发了第一台商业机型3D-Modeler。
- 1、下载文档前请自行甄别文档内容的完整性,平台不提供额外的编辑、内容补充、找答案等附加服务。
- 2、"仅部分预览"的文档,不可在线预览部分如存在完整性等问题,可反馈申请退款(可完整预览的文档不适用该条件!)。
- 3、如文档侵犯您的权益,请联系客服反馈,我们会尽快为您处理(人工客服工作时间:9:00-18:30)。
快速成型技术的发展历史一、国外RP技术的发展历史从历史上看,很早以前就有“材料叠加”的制造设想,例如,1892年,J.E.Blanther在他的美国专利(#473 901)中,曾建议用分层制造法构成地形图。
这种方法的原理是,将地形图的轮廓线压印在一系列的蜡片上,然后按轮廓线切割蜡片,并将其粘结在一起,熨平表面,从而得到三维地形图。
1902年,Carlo Baese在他的美国专利(#774 549)中,提出了用光敏聚合物制造塑料件的原理,这是现代第一种快速成型技术——“立体平板印刷术”(Stereo Lithogrphy)的初步设想。
1940年,Perera提出了在硬纸板上切割轮廓线,然后将这些纸板粘结成三维地形图的方法。
50年代之后,出现了几百个有关快速成型技术的专利,其中Paul L Dimatteo在他1976年的美国专利(#3932923)中,进一步明确地提出,先用轮廓跟踪器将三维物体转化成许多二维廓薄片(图1),然后用激光切割这些薄片成型,再用螺钉、销钉等将一系列薄片连接成三维物体,这些设想与现代另一种快速成型技术——“物体分层制造”(Laminated Object Manufacturing)的原理极为相似。
图1 Paul的分层成型法上述早期的专利虽然提出了一些快速成型的原理,但还很不完整,更没有实现快速成型机械及其使用原材料的商品化。
80年代末之后,快速成型技术有了根本性的发展,出现的专利更多,仅在1986~1998年期间注册的美国专利就有24个。
这首先是Charles W Hull在他1986年的美国专利(#4 575 330)中,提出了一个用激光束照射液态光敏树脂,从而分层制作三维物体的现代快速成型机的方案。
随后,美国的3D Systems公司据此专利,于1988年生产出了第一台现代快速成型机SLA-250(液态光敏树脂选择性固化成型机),开创了快速成型技术发展的新纪元。
在伺候的10年中,涌现了10多种不同形式的快速成型技术和相应的快速成型机,如薄形材料选择性切割(LOM)、丝状材料选择性熔覆(FDM)和粉末材料选择性烧结(SLS)等,并且在工业、医疗及其他领域得到了广泛到的应用。
1998年止,全世界已拥有快速成型机4259台,快速成型机制造公司约27个,用快速成型机进行对外服务的机构331个。
SLA快速成型法是目前世界上公认的众多快速成型方法中最为广泛使用的一种方法,它经过10多年的发展历程,不断地趋向成熟和发展,图2形象地表示了其发展历程,美国3D Systems公司高级研究人员Bryal Bedal和Hopnquyer 预言,基于光敏树脂的激光固化成型可以达到亚微米级的分辨率。
由于该项技术是多学科的交叉和多项技术的高度集成,所以其整体性能的发展依赖于各种单元技术的发展,反之,单项技术的发展又不断地促进其整体技术的进步。
SLA技术可分为硬件、软件、材料以及成型工艺四大组成部分。
各部分的发展既相互促进,又相互制约。
软硬件的发展相互依赖又相互促进,而材料的发展很大程度上又决定着成型的工艺。
图2 SLA技术发展历程图多年来人们一直致力于以下几方面的研究:(1)硬件部分包括激光束精确光斑的获得、激光束光点扫描精度及定位精度的获得与控制;高可靠性、高效率的树脂再涂层系统;树脂液面位置的精确控制。
(2)材料的各种性能的研究,如聚合反应及固化的速度、聚合反应过程中的收缩、固化后零件的机械性能等;粘度也是一项重要的性能指标,因为它是影响涂层精度的关键因素,除此之外,还需要考虑特殊用途的需求,如用于融模铸造的树脂,要求发气量及残渣小;还有易储藏,无毒无味等要求。
(3)软件,主要是指树脂的预处理、整个成型过程的控制以及面向用户的易操作性。
人们期望着这种技术发展到只要简单地一按“按钮”,就能将CAD电子模型转变为三维实体模型。
(4)制作工艺是光固化成型过程的关键技术,零件的精度及成型效率主要决定于制作的工艺。
随着人们对光聚合机理、固化成型过程认识与研究的不断深入、零件精度也得到逐年提高(参见图3)。
但是,这项技术毕竟是一项新的成型技术,而“快速”成型的要求又使得所用的树脂材料有别于传统的聚合物,加之聚合反应过程的不可控性以及材料物性的时间依赖性,所以,目前的绝大部分研究在很大程度上依赖于所用的材料和试验条件,对成型工艺的研究还没有通用的分析与计算模型,并且,实际应用中,经验还起到相当重要的作用。
经过多年的研究及众多用户的使用经验,认为固化过程中树脂的收缩引起零件的变形是导致精度丧失的最主要原因,所以,人们一直在寻求最佳的制作工艺,以获得更高的零件精度。
图3 用户零件误差时间曲线二、RP技术在我国的发展概论RP技术自80年代末在我国开始研制以来,发展很快,可以概论如下:1、1个明确的指导思想,1个重要的保证开发创新与工程应用相结合的指导思想。
从市场发展规律来看,因为RPM 技术成本低、质量高,特别是快速响应能力明显优于传统制造技术,故有比较强的市场竞争力;从RPM技术自身发展规律来看,它具有双重性:一是先进性,二是实用性。
因此在我国从1991年RPM技术的研究开发启动时,就明确了开发创新和工程应用相结合的指导思想。
组织保证也是很重要的。
在近10年的发展中,组织建设也在逐渐完善;①在国家自然科学基金委员会及科技部的大力扶植下有些单位已经形成了比较明显的优势,是我国RPM技术研究的主导单位;②1997年中国机械工程学会电加工分会成立了RPM技术专业委员会,积极推进这一学科的建设与发展;③在国家科技部的支持下,建立了5个生产力促进中心(西北、湖北、深圳、天津、宁波),它们都在发挥着将RPM技术转化为生产力的推广作用。
2、2个技术依托,2个产品方向我国RPM技术的发展主要依托于2种技术:基于激光或其他光源成型的技术、挤压或喷射成型技术。
2个产品方向:一是服务于高精度及高性能零部件制造的大型系统;二是自动化的桌面小型系统,主要用于制造概念原型等,出现了不同RPM工艺并举、大小RPM设备齐上的百家争鸣、百花齐放的局面,有效促进了我国RPM技术的迅速发展。
3、3个积极作用,3个发展阶段3个积极作用是指启蒙作用、带头作用与推动作用:①1991年美国学者在中国的讲学,有效地起到了启蒙的作用;②随后,有些单位的科技工作者率先步入了这个行业,起到了很好的带头作用,如清华大学、华中理工大学、西安交通大学、北京隆源公司等;③科技部和国家自然科学基金委员会(简称“基金委”)的推动作用。
基金委在国内发展RPM技术之初,就积极地、及时地安排了一些项目,当这些项目基本完成并取得了良好的效果以后,即部分应用基础研究完成之后,开始步入产业化或商品化阶段时,科技部又给予了重点支持,所以才有了今天RPM技术在我国得以迅速发展的局面。
RPM技术在我国的发展经历了3个阶段:第一个阶段是起步跟踪阶段(1992~1994年)。
主要是消化、吸收国外的技术,特别是美国的先进技术。
通过消化吸收,一些单位明确了主攻方向,即清华大学以LOM、FDM为主,西安交通大学主要是SLA、华中理工大学主要是LOM,北京隆源公司主要是SLS,至今已初见成效。
第二个阶段是发展创新阶段(1995~1997年)。
主要体现在如下5个方面:①比较成熟地掌握了这4种主要RPM技术和设备的研发能力。
②开发出具有我国特色的一些装备,由样机向商品机迈进。
值得指出的是,清华大学研发的水制冷成冰的快速成型系统和西安交通大学研制的紫外光快速成型系统,都是具有创意的。
③成型材料陆续国产化。
例如,清华大学开发了FDM用的蜡、ABS、尼龙等材料;西安交通大学开发了SLA用的国产光固化树脂;华中理工大学开发的LOM用纸、北京隆源公司开发的蜡粉以及尼龙粉等都已国产化。
④在技术原理及参数优化等方面的研究也取得了比较明显的进步。
如清华大学提出了关于制造维数的概念,西安交通大学提出了增材制造的理论以及华中理工大学和西安交通大学对反求工程的数据重构都进行了比较深入的研究。
⑤西安交通大学完成了RE/RP/RT集成的快速成型制造集成系统的开发;清华大学根据功能梯度原理研制出多功能RPM设备等。
这些成果不仅具有自己的知识产权,而且步入了国际先进行列。
第三个阶段是初级的产业化阶段(1998年到今)。
据不完全统计,国内现有RPM设备约100台,其中,国产设备50台左右。
可以说,进入了产业化的初级阶段。
1995年我们召开了第1届快速成型制造会议;1997年成立了专业委员会;1998年召开了国际研讨会;2000年召开了第2届快速成型制造会议。
在此期间,还多次参加了快速成型制造全球联盟组织会议;全球联盟主席在他的演讲中承认中国的RPM技术发展速度之快是惊人的,发展力量是不可忽视的,我们有理由认为,我们广大科技工作者的努力,至今已为我国RPM技术的发展奠定了扎实的思想基础、组织基础、技术基础和物质基础,并正充满信心地迎接着我国RPM 技术新的大发展时期的到来。
三、国内RP发展动向总体来说,近年来国内快速成型技术的水平有了质的提高,以清华大学为代表,国内各RP研发、设备生产和技术服务单位在RP技术、市场和应用服务都有很大进步。
1、技术方面国际上传统的所有RP工艺,如SLA、LOM、FDM、SLS等,在国内都有单位进行了成功的开发,多数关键部件都实现了国产化,比如FDM设备中的喷头,LOM设备中的激光器等:设备的稳定性、可靠性和造型精度、质量有了显著提高,成型材料性能也在不断进步。
除此之外,许多单位还创新低开展了RP新工艺新设备的研究,比如清华大学开发的低温冰型快速制造工艺和无模砂型制造工艺,拓宽了RP领域,在世界上处于领先地位。
2、市场方面几年来国内RP市场从起步已经逐步走向发展阶段。
企业界对于快速成型的认识已经有了比较全面的了解,快速成型已经逐步成为一种通用的设计方法和制造方法。
许多企业已有应用RP技术的设想或方案。
从地区分布(大陆)来讲,南方地区的市场已经基本成熟,其特点是企业认识程度高,技术、设备需求比较大;华东地区由于外企比较集中,市场潜力非常大,将是继华南之后的新的市场中心。
应用行业集中在首版制作领域,比如珠宝、家电、模具、玩具、汽车等新产品、工艺品开发、包装,以及外观要求较高的器件制作。
3、技术服务方面相对于两年前的RP行业,国内新增了许多RP技术服务型企业。
国内大部分企业购买RP设备的能力有限,但是单个小批量的RP原型件的需求又很大,在这种需求的刺激下,新增的RP技术服务公司购买国内外成熟的RP设备,从应用的角度,将三维结构数据获得、反求、快速成型技术、制造等服务,目前集中在首版制造领域。
这些企业在业务活动中,扩大了RP技术的宣传面,在RP应用的深度和宽度上都对市场有促进作用。