浅谈变换催化剂和变换炉的选择
变换催化剂的使用效果评价
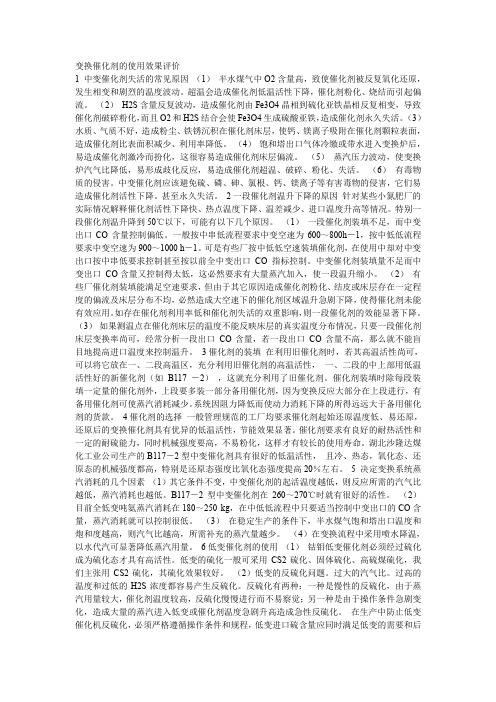
变换催化剂的使用效果评价1 中变催化剂失活的常见原因(1)半水煤气中O2含量高,致使催化剂被反复氧化还原,发生相变和剧烈的温度波动。
超温会造成催化剂低温活性下降,催化剂粉化、烧结而引起偏流。
(2)H2S含量反复波动,造成催化剂由Fe3O4晶相到硫化亚铁晶相反复相变,导致催化剂破碎粉化,而且O2和H2S结合会使Fe3O4生成硫酸亚铁,造成催化剂永久失活。
(3)水质、气质不好,造成粉尘、铁锈沉积在催化剂床层,使钙、镁离子吸附在催化剂颗粒表面,造成催化剂比表面积减少、利用率降低。
(4)饱和塔出口气体冷缴或带水进入变换炉后,易造成催化剂激冷而扮化,这很容易造成催化剂床层偏流。
(5)蒸汽压力波动,使变换炉汽气比降低,易形成歧化反应,易造成催化剂超温、破碎、粉化、失活。
(6)有毒物质的侵害。
中变催化剂应该避免硫、磷、砷、氯根、钙、镁离子等有害毒物的侵害,它们易造成催化剂活性下降。
甚至永久失活。
2一段催化剂温升下降的原因针对某些小氮肥厂的实际情况解释催化剂活性下降快、热点温度下降、温差减少、进口温度升高等情况。
特别一段催化剂温升降到50℃以下,可能有以下几个原因。
(1)一段催化剂装填不足,而中变出口CO含量控制偏低。
一般按中串低流程要求中变空速为600~800h-1,按中低低流程要求中变空速为900~1000 h-1。
可是有些厂按中低低空速装填催化剂,在使用中却对中变出口按中串低要求控制甚至按以前全中变出口CO指标控制。
中变催化剂装填量不足而中变出口CO含量又控制得太低,这必然要求有大量蒸汽加入,使一段温升缩小。
(2)有些厂催化剂装填能满足空速要求,但由于其它原因造成催化剂粉化、结皮或床层存在一定程度的偏流及床层分布不均,必然造成大空速下的催化剂区域温升急剧下降,使得催化剂未能有效应用。
如存在催化剂利用率低和催化剂失活的双重影响,则一段催化剂的效能显著下降。
(3)如果测温点在催化剂床层的温度不能反映床层的真实温度分布情况,只要一段催化剂床层变换率尚可,经常分析一段出口CO含量,若一段出口CO含量不高,那么就不能盲目地提高进口温度来控制温升。
CO变换催化剂的选择与使用寿命分析

煤化工与甲醇化 工 设 计 通 讯Coal Cemical MethanolChemical Engineering Design Communications·15·第45卷第8期2019年8月一氧化碳的选择与使用对工业的生产具有直接的影响,正确地选择与使用一氧化碳不仅可以提升企业的工作效率,并且还能够对企业的产品在质量上有所提高,还能够增加企业的经济与社会效益,为企业的发展奠定坚实的基础。
在进行变换催化剂的使用过程之中,错误的使用并且操作催化剂就会导致催化剂的使用寿命大大降低。
因此,对催化剂的选择与正确的使用进行研究与论述是十分有必要的。
1 co 变换催化剂的选择摘 要:一氧化碳变换催化剂技术随着工业化的脚步而快速的发展,一氧化碳变换技术主要是依靠催化剂的性能而得以发展的。
变换催化剂的性能以及本身的功能对制作工艺具有决定性作用。
主要针对催化剂的性能进行介绍,以方便在净化工艺工作之中工作人员的选择,并对催化剂的使命寿命,以及如何延长催化剂的使用寿命进行分析。
关键词:CO 变换催化剂;催化剂的选择;使用寿命中图分类号:TQ426 文献标志码:A 文章编号:1003–6490(2019)08–0015–02Selection and Service Life Analysis of CO Shift CatalystZhang TaoAbstract :The carbon monoxide shift catalyst technology has developed rapidly with the pace of industrialization.The carbon monoxide shift technology has been developed mainly by relying on the performance of the catalyst.The performance of the shift catalyst and its own function are decisive for the manufacturing process.This article is mainly to introduce the performance of the catalyst to facilitate the selection of workers in the puri fication process ,as well as to introduce the mission life of the catalyst and how to extend the life of the catalyst for analysis.Key words :CO shift catalyst ;catalyst selection ;catalyst life CO变换催化剂的选择与使用寿命分析张 涛(伊犁新天煤化工有限责任公司,新疆伊犁 835000)收稿日期:2019–05–29作者简介: 张涛(1987—),男,山东高密人,助理工程师,主要从事变换催化剂相关工作。
变换催化剂与变换工艺

1.1 Fe-Cr系催化剂的费-托副反应问题
Fe3O4的表面是变换活性表面,Cr2O3与Fe3O4形成 固溶起着结构性辅助催化作用,Cr2O3不改变 Fe3O4表面的比活性,但可大幅度提高Fe3O4的耐 热稳定性。 不同型号的催化剂含有不同的助剂,如K2O、Mg、 Ca、Sr、Ba等氧化物和碳酸盐。
Co的位置类似于MoS2晶体中边Mo原子的位置
上,如上图中的d位。实验证明Co-Mo-S相中Co原子的多少与其H源自S活性的高低有很好的线性关系。
Eltznel等在实验的基础上,利用Co-Mo-S模型,系 统地计算了第一周期各过渡金属元素与MoS2形 成的Co-Mo-S分子簇的能级图,与实验结果相关 联,从电子转移角度更深刻地阐述了助剂作用。
当气体的含硫量较低此时可能会发生上层还原的 铁作“脱硫剂”,下层“暂时无硫”此时会产 生上节所述的“无硫气体工况”,但弗托副反 应的程度较轻,通常的表现是变换后甲烷含量 的提高,严重时也会生存乙炔,导致铜洗带液。 同时在中低低流程中“暂时无硫”现象有时会 使低变催化剂特别是第一低变发生“反硫化”, 这种异常工况已时有发生要引起注意。
1.2 H2S的问题
1.2.1 H2S与费-托副反应 当气体中无硫(如天然气造气)过度还原生成的铁 还发生下列反应: 3Fe+2CO→Fe3C+CO2 5Fe+4CO→Fe5C2+2CO2 也就是Fe3C、Fe5C2首先是由Fe3O4还原成Fe再与CO 反应而生成的。此时会可能有以下二种副反应生成: 析碳反应:CO→CO2 + C 费-托反应:CO+H2→CH4、C2H2、C2H6、C3H8… 上述反应是体积缩小反应,变换压力愈高,反应也 愈容易进行,这就是无硫变换气容易产生弗托反应 的原因,显然,压力愈高,弗托副反应也愈明显。
浅析变换工艺催化剂的使用及常见问题的处理

浅析变换工艺催化剂的使用及常见问题的处理作者:永学健张涛来源:《中国化工贸易·下旬刊》2019年第07期摘要:本篇文章中所讲的变换催化剂主要指的是钴、钼系催化剂,这种催化剂使用时间较长,使用面积覆盖也较为广泛,为钴、钼系催化剂的积累了丰富的使用经验。
但是在钴、钼系催化剂这么多年的使用过程之中,也出现了诸多的问题影响了催化剂的正常使用。
因此,笔者针对现如今关于钴、钼系催化剂在使用当中的问题提出自己的论述观点,并且总结出原因分析以及提出此昂对应的解决办法,希望可以对钴、钼系催化剂的使用有一定的借鉴意义。
关键词:变换工艺催化剂;钴、钼系催化剂;催化剂的使用钴、钼系催化剂主要适用于以煤或者是重油为主要原料的合成氨厂,这种催化剂有着超高的耐硫功能,但是在没有或者有很少的硫化氢的环境之中,钴、钼系催化剂的活性就会比较弱。
由于最近几年,人们越发的关注环境保护问题,化肥行业也随之开展了节约能源,降低能源消耗的工作,因此,钴、钼系催化剂由于它的耐硫功能就得到了诸多厂家的青睐,但是在使用的过程之中由于存在着问题没有得到解决,也就造成了催化剂在工作之中出现结焦、失活等现象的发生。
1 钴、钼系催化剂的正确使用在上个世纪50年代的时候,钴、钼系催化剂就是在当时研发的最新型的催化剂,它对一氧化碳的变换工艺有着很好的变幻效果。
最有典型的主要是有K8-11等等。
钴、钼系催化剂主要是通过氧化铝为主要的載体,利用氧化铝改善低温活性性能,钴、钼系催化剂的助催化剂在一般情况之下都是选择碱金属钾。
在进行催化剂的选用的时候,一定要注意不仅是要关注它的活性性能,还要考虑它的强度。
通常情况下来说的话,催化剂的活性与强度是成反比例的,催化剂的活性性能越好,反之,催化剂的强度就会变得非常的差[1]。
催化剂生产商在进行制造催化剂的过程之中要充分的考虑到强度与活性性能二者之间的关系,并且还要找到一个可以达到这两者之间的平衡点。
钴、钼系催化剂的最大的特点就是很高的宽温耐硫性,这种催化剂通常情况之下都具有良好的活性性能、较高的机械强度以及选择性,尤其是在低温变换活性和低硫变换活性这两个方面,在世界上也是处于领先地位的,同时钴、钼系催化剂对高空速、高水气的环境适应能力很强,具有良好的稳定,还具有较大的操作弹性。
变换催化剂知识

变换催化剂知识钴钼催化剂在使用一段时间后,由于重烃聚合而会产生结碳。
这不仅降低催化剂活性,而且会使催化剂床层阻力增加,产生压差,此时就应将催化剂烧碳以获得再生。
在粗煤气被切断,并加上了相应的盲板之后,把与触媒重量比为0.1-0.3:1的中压蒸汽与正常变换过程的相反流向,由反应器底部通入,自顶部排出,这样可将粉尘杂质吹出。
蒸汽以84℃/h的速度给催化剂床层升温,直到催化剂床层温度为350-450℃时为止(若超过500℃将会损害催化剂)然后继续通蒸汽,直到气流的冷凝液在取样中大致没有杂质为止。
之后通入工作空气,使蒸汽中含氧量为0.2-0.4%(即空气0.5%~2%),进行烧碳;观察床层温度,可以从床温的变化来观察床层含碳物质的燃烧情况,蒸汽中的空气决不能超过5%,通入的空气量可适量调节,以将床温控制在501℃以下。
压力对烧碳无大影响,但从气体分布均匀考虑,气体压力以1到3个大气压为宜。
在烧碳过程中也会将催化剂中的硫烧去,而使催化剂变成氧化态。
烧碳过程中应当密切观测床层温度,调节空气或氧的浓度来控制床层温度,当床层中不出现明显温升、燃烧前缘已经通过反应器,出口温度下降,气体中O2上升,就意味着烧碳结束。
适当提高氧浓度进一步烧碳。
若温度不出现明显上升,可连续提高氧浓度,最后用空气冷却到50℃以下。
烧碳之后的催化剂需重新硫化方能使用。
若需将催化剂卸出,由于使用过的催化剂在70℃以上有自燃性,因此应先在反应器内冷却至大气温度。
卸时准备水龙头喷水降温熄火。
除了一个卸出孔外,不要再特意开孔,以免因“烟囱效应”导致催化剂床层温度飞升。
正常生产中工艺气中一般含有0.3-0.6%的氧气,由于氧气的纯在,对催化剂有较大的危害,不仅会使钴钼催化剂硫酸盐化,而且还会与催化剂中的Cos和Mos2发生反应,生成SO2和无活性的单质Co、Mo使催化剂永久失活。
所以现在都在研究使用保护剂(也就是脱氧剂)。
处于硫化状态的钻钼系耐硫变换催化剂非常活泼.遇空气易于氧化.并放出大量的热,引起催化剂床层温度暴涨,反应方程式如下:(1)2MoS2+ 702—2Mo03+ 4SO2(2)2CoS+ 302—2Co0+ 2SO2使用Co-Mo耐硫变换催化剂的氮肥厂家,经常因催化剂床层出现问题(如偏流、结块及部分出现粉化等),需要重新装填处理;有些厂家需更换部分催化剂或需要卸出催化剂复活。
煤制甲醇原料气工艺及耐硫变换催化剂的选择

煤制甲醇原料气工艺及耐硫变换催化剂的选择纵秋云1,刘捷2(1.青岛科技大学,山东青岛266042;2.青岛联信化学有限公司,青岛胶州266300)0前言根据煤气化方法的不同,以煤为原料制取甲醇原料气的生产方法可分为德士古水煤浆加压气化,鲁奇粉煤加压连续气化,常压固定床间歇气化以及近期应用的Shell粉煤加压气化等4种。
根据变换压力的不同,又可分为高压(>6.0MPa)、中压(3.0~4.0MPa)和低压(<2.0MPa)等变换流程。
气化方法不同,制取的原料气中的CO含量不同,采用的耐硫变换工艺也大不相同。
同一种气化工艺,由于变换压力、原料气中的H2S含量、水/气以及后续工段微量CO及H2S脱除方法的不同,采用的耐硫变换工艺也不同。
特别是近期,随着Shell粉煤加压气化在合成氨和甲醇生产中的应用,对耐硫变换催化剂提出了更多和更加苛刻的要求。
本文在文献调研和分析的基础上,介绍了几种典型的煤制甲醇耐硫变换工艺及其所用催化剂,对Shell粉煤加压气化流程中第一反应器催化剂使用的问题进行了分析和讨论,对节能型Shell粉煤加压气化低水/气变换新流程进行了简单介绍。
1 水煤浆加压气化工艺流程水煤浆加压气化又称德士古(Texaco)水煤浆加压气化,于20世纪50年代初期,由美国德士古公司在重油部份氧化气化的基础上开发成功,随后又在日本、瑞典和意大利等国工业应用。
我国的陕西渭河化肥厂、上海焦化厂、山东鲁南化肥厂、山东德州恒升化工集团(产品甲醇)及兖矿国泰化工有限公司等企业均采用这种工艺。
因水煤浆气化具有单台气化炉生产能力大、吨氨能耗低和煤种适应范围广等优点,因此是当前合成甲醇生产中较为先进的造气方法。
在水煤浆气化制甲醇的流程中,又分为是全气量耐硫变换和部分气量耐硫变换流程。
全气量通过流程:顾名思义,就是将全部的工艺气体都通过变换催化剂床层,通过调节气/汽等手段,来控制出口气CO 浓度,达到希望的气体组成。
为了控制变换出口的CO含量,通常要在较低的水/气下操作,因此需要催化剂有低温活性和耐低水/气的能力。
变换

第四章 甲醇原料气中一氧化碳的变换以重油与煤为原料所制得的粗甲醇原料气均需经过一氧化碳变换工序。
一氧化碳变换工序的主要有两个作用:一是调整甲醇原料气氢碳比例。
合成甲醇所用的气体组成应保持一定的氢碳比例。
在甲醇合成反应中,应使15.210.222-=+-=CO CO CO H f 或05.20.222-=+=CO CO H M当以重油或煤、焦为原料生产甲醇时,气体组成偏离上述比例,CO 过量而H 2不足,需通过变换工序使过量的一氧化碳变换成氢气,以调整氢碳比。
二是使粗煤气中的有机硫(COS 、CS 2等)水解转化为无机硫(H 2S ),便于脱除。
甲醇合成原料气必须将气体中总含硫量脱至0.1ppm 以下。
以煤制的粗水煤气中硫的主要存在形式有两种无机硫H 2S (90%)和有机硫COS (10%)。
除非采用甲醇洗,通常的湿法脱硫难以在变换前脱除有机硫。
设置了变换工序后,有机硫化物均可在变换催化剂上转化为H 2S ,便于后工序脱除。
COS + H 2O ═ CO 2 + H 2S (4-1)工业生产中,一氧化碳变换反应均在催化剂存在的条件下进行。
根据反应温度不同,变换过程分为中温变换和低温变换。
中温变换催化剂以三氧化二铁为主,反应温度为350~550℃,反应后气体中仍含有3%左右的一氧化碳。
低温变换以铜(或硫化钴-硫化钼)为催化剂主体,操作温度为180~280℃,反应后气体中残余一氧化碳可降到0.3%左右。
近年来,随着高活性耐硫变换催化剂开发和使用,变换工艺发生了很大变化,由过去单纯的中温变换、中低温变换,发展到目前的中变串低变、全低低、中低低变换等多种新工艺。
第一节 一氧化碳变换原理一、变换反应的特点 变换反应可用下式表示:CO + H 2O(g) ═ CO 2 + H 2 +Q (4-2)变换反应的特点是可逆、放热、反应前后体积不变,并且反应速率比较慢,只有在催化剂的作用下才具有较快的反应速率。
变换反应是放热反应,反应热随温度升高而有所减少,其关系式为[]mol cal T T T Q /109703.010845.2219.010*******⨯⨯+⨯⨯-+=-- (4-3)式中 T —温度,K 。
一氧化碳变换催化剂的特性与选用(上)

Page 2
LOGO
一氧化碳变换催化剂的性能与特点
工业上使用较为广泛的Fe3o4为主相的铁系催化剂、cu为主相的铜系催化剂和 MoS2为主相的钼系催化剂一氧化碳变换催化剂.通常为了改善催化剂的某些缺 陷或强化某项特点,而引入一些助催化剂使得即使是同一类催化剂亦各具特色。 2.1 铁系催化剂 以Fe 3o 4为主相的铁系催化剂因为单纯的Fe 3o 4在操作温度(温度区间300~470℃, 常称为中温或高温)下, 由于结晶颗粒的长大而很快失活, 因此在催化主相中加 入一定的(结构性)助催化剂。工业上较为成功的助催化剂主要有CrO3 , 因此铁系 催化剂也称为铁铬中(高)变催化剂。
Page 5LOGO Nhomakorabea一氧化碳变换催化剂的性能与特点
2 l 5 低水汽比铁铬中变催化剂 为了改善铁铬中变催化荆对水汽比的适应-肚,特别是节能型烃娄蒸汽转化流程 (水碳比小于2.75) 通过添加锢促进剂.改善了铁铬中变催化剂对低水汽比条件 的适应性, 主要型号有:B113-2等。 2.1.6 本体低硫铁铬中变催化剂 催化剂本体硫含量的高低.直接影响催化剂使用前的放硫时间,本体岔硫量低的 催化剂有利于保护后续的对硫非常敏感的催化剂.如铜锌低变催化剂等 主要型 号有:B110-2、B113等。
Page 3
LOGO
一氧化碳变换催化剂的性能与特点
2.1.1 铁铬中变催化剂 传统的铁铬中变催化剂的结构性助催化剂CrO3 的含量一般为7%~12%,
此外为了改善催化剂的催化活性还添加调变性助催化剂如K+ 等。 2.1.2 低铬型铁铬中变催化剂 由于CrO 3对于人体和环境具有毒害作用. 为了减少CrO 3对于人体和
Page 8
LOGO
一氧化碳变换催化剂的性能与特点
- 1、下载文档前请自行甄别文档内容的完整性,平台不提供额外的编辑、内容补充、找答案等附加服务。
- 2、"仅部分预览"的文档,不可在线预览部分如存在完整性等问题,可反馈申请退款(可完整预览的文档不适用该条件!)。
- 3、如文档侵犯您的权益,请联系客服反馈,我们会尽快为您处理(人工客服工作时间:9:00-18:30)。
浅谈变换催化剂和变换炉的选择
摘要:变换工艺根据所选用的催化剂是否耐硫,将变换工艺分为耐硫变换
和非耐硫变换工艺。
变换反应的顺利进行主要取决于两方面的因素,催化剂和变
换炉。
本文通过介绍不同类型变换催化剂和变换炉的发展、应用及优缺点,为广
大化工同行在变换催化剂和变换炉的选择上提供帮助。
关键词:变换工艺;变换催化剂;变换炉
1变换催化剂的选择
通常使用的催化剂有高温变换催化剂、低温变换催化剂和宽温耐硫变换催化剂。
1.1高温变换催化剂
高温变换催化剂其活性相是由Fe2O3部分还原得到的Fe3O4。
在实际应用过程中,高温烧结导致Fe3O4表面积下降,引起活性的急剧下降,造成纯Fe3O4的活性
温区很窄,耐热性很差。
因此常加入结构助剂提高其耐热性,防止烧结引起的活
性下降。
由于铁铬系高温变换催化剂中铬是剧毒物质,造成在生产、使用和处理
过程中对人员和环境的污染及毒害,但工业化与应用业绩较少。
高温变换催化剂
的粉化是它的一个主要问题。
催化剂的更换往往不是由于活性丧失,而是由于粉
化造成过大的压差。
部分催化剂的粉化,引起气流不均匀,也将导致转化率下降。
蒸汽消耗较高,有最低水气比要求,要求变换入口水气比在1.4以上,变换后的
水气比应大于0.8,导致过剩蒸汽冷凝量过多、能耗增加,不宜选用。
1.2低温变换催化剂
低变催化剂的最大特点就是活性温度低,在200~260℃的范围内,变换反应
就能迅速进行。
低变催化剂对硫化物极为敏感,由于生成铜盐而永久性中毒。
氯
或氯离子也引起永久性中毒,这是由于催化剂发生结晶而引起的。
另外,原料气中的不饱和烃可能在催化剂表面析炭或结焦。
1.3宽温耐硫变换催化剂
钴钼系耐硫宽温变换催化剂具有很高的低温活性,它比铁系高温变换催化剂起活温度低100~150℃,甚至在160℃就显示出优异的活性,与铜系低温变换催化剂相当,且其耐热性能与铁铬系高温变换催化剂相当,因此具有很宽的活性温区,几乎覆盖了铁系高温变换催化剂和铜系低温变换催化剂整个活性温区。
其最突出的优点是其耐硫和抗毒性能很强,另外还具有强度高、使用寿命长等优点。
但其致命的缺点是使用前需要繁琐的硫化过程,使用中工艺气体需要保证一定的硫含量和较高的汽气比,以防止催化剂反硫化的发生,特别是在高温操作时更为严重,随着温度的升高,最低的硫含量和汽气比也随之提高,当原料含硫波动较大时,造成操作过程控制复杂化。
1.4三种系列催化剂的性能比较表
经上综合比较,煤间接液化制油、煤制甲醇、煤制乙二醇等项目变换工艺推荐选用Co-Mo系宽温耐硫催化剂。
2反应器(变换炉)型式的选择
变换炉是变换系统的核心,是CO转化为H2的关键设备,变换炉的设计,要
求做到催化剂利用率高,CO的变换率高低可调,温度操作控制手段简单有效、流
程结构简单、系统阻力小、自热利用合理,热损失少。
变换炉内CO反应热的移
出方式,决定于变换炉的结构形式。
从这个角度来看变换炉分为绝热型变换炉和
等温型变换炉两类。
2.1绝热型变换炉
绝热型变换炉是国内氮肥行业普遍使用的炉型。
这种变换炉为全轴向型塔或
轴径向塔,所装催化剂一般分为一~三段,煤气经过催化剂床层升高到一定温度后,出段间间接换热或直接冷激,将气体温度降低。
而后进入下一段催化剂床层
继续反应。
一般第一段催化剂反应温度较高,目的在于加快反应速度,提高催化
剂的利用率。
第二段反应温度较第一段低,最后一段反应温度最低,主要考虑化
学平衡。
这样由于温度不断的变换、各处的反应速度不均衡,催化剂的利用率较低,气体通过床层的阻力也较大。
当变换一氧化碳含量超过50%,变换反应因浓度差大,推动力也较大,因此,变换反应床层易超温,催化剂易被还原或烧毁;对合成甲醇来讲,变换的深度浅,且第一段催化剂反应温度较高,可副产中压过热蒸汽。
2.2等温型变换炉
等温型变换炉为全径向塔,在变换炉内催化剂床层中设置换热管,CO反应热
不断通过管内冷介质移走,使催化剂床层从上到下温度变化不大。
这种变换炉由
耐压的外壳和装有催化剂的内件与热交换器所组成。
正常操作时,气体由底部三
通中心管外侧进入,通过外壳与内件之间的环隙,以保持外壁为相对低温,气体
由径向框均匀分布进入催化剂床层,进行CO的变换反应,反应所放出的热量与
埋在催化剂中的换热管内过饱和热水进行热交换。
这样,变换过程在催化剂床中
边反应边换热,反应热由汽包不断的向外释放中压蒸汽而移走,反应后的变换气
离开催化剂床层,径向均匀地进入中心集气管,从中心管导向,在炉底三通排出。
进入蒸汽过热器与汽包来的变换反应热所产生的饱和蒸汽换热,自产的蒸汽再与
煤气混合进入变换炉,这样就形成了变换反应的自热循环利用的目的。
同时通过
汽包蒸汽压力的调节,达到直接控制催化剂床层温度的目的。
2.3绝热型和等温型变换炉的对比
(1)绝热型变换炉
①适应性差:半水煤气CO:30%以下适用,CO高于30%,催化剂床层容易飞温,难于操控;
②绝热温升大,反应段数多,或反应炉多,中间需间接降温或喷水降温;
③操作较复杂,控制床层温度难度大,但实际控制效果迟缓且难于稳定;
④流程长,床层温度高,催化剂容易粉化板结.变换炉及系统阻力大
⑤变换反应热没有合理利用,补充蒸汽量大,运行不经济;
⑥在汽气比低、温度高(>400℃)时,易发生甲烷化强放热反应,生成无用
的CH4,增加后续工艺的处理麻烦,同时会使催化剂床层温度猛升,烧坏催化剂。
(2)等温型变换:
①适应性强:CO:30~90%原料气均适用,特别是高CO更优,变换气CO:
1.5~0.4%或更低可调;
②恒温、等温、低温、不超温(≤280℃),催化剂床层无温差;壳体可用
15CrMoR,塔壁薄,设备轻;
③操作简单,控制汽包蒸汽出口压力调压阀,即可操作床层温度;
④变换压力2.0~6.0MPa;根据用户需要确定;
⑤低阻力:反应器阻力~0.01MPa,系统阻力~0.08MPa;
⑥等温变换自产2.5~4.0MPa蒸汽,与管网极少量蒸汽结合,可使变换反应
达到自热循环,热能自用;蒸汽自给,并为其它锅炉提供80℃以上的软水。
经过对比等温变换技术具有流程简单,系统阻力降小,占地少,催化剂装填
量少、使用寿命长等优点,适合处理高一氧化碳浓度的粗煤气或其他工业气体[1]。
结语
变换反应的顺利进行主要取决于两方面的因素,催化剂和变换炉,催化剂是
实现先进工艺的关键因素之一,而反应器的选型对发挥催化剂的活性和寿命有很
大的关系,只有将二者有机结合,才能节能降耗和实现最佳工艺指标。
同时特定
项目变换工艺方案的选择还应综合考虑如下因素:气化方式、下游产品氢碳比要求、系统压降、副产蒸汽规格与全厂蒸汽动力平衡的匹配性及设备运行和维护等[2]。
参考文献
[1]王照成,刘庆亮,李繁荣,丁玲,肖敦峰,胡四斌.等温变换技术及其工
业化应用进展[J].煤化工,2020,48(06):12-15.
[2]黄金库,樊义龙,王永锋.绝热与等温变换工艺方案比选探析[J].化工设计,2019,29(06):3-7.
[3]张新堂,孙淼元,郝元国.KC -103S 型预硫化耐硫变换催化剂的性能及工
业应用[J].工业催化.2016,(1)。