钴钼系耐硫变换催化剂装填及使用过程注意事项
硫化过程中注意要点

硫化过程中注意要点钴钼系耐硫低变催化剂硫化过程的控制要注意以下几点:①控制好升温硫化温度。
既要控制升温速度,又要保证床层能达到硫化最终温度。
②CS2加入量和加入时间的控制。
初期加入量小,逐步增加。
升温至20 0℃左右加入CS2。
③稳定操作。
空速、电加热功率、CS2加入量是硫化操作的三个主要调节手段。
在实际操作中应稳定CS2的加入量,以调气量为主、调电加热器的功率为辅。
④硫化要完全。
从硫化时间、床层温度、炉出口H2S浓度判断硫化终点,保证催化剂达到最佳活性。
在硫化操作中,应注意:1. 用半水煤气硫化,应控制半水煤气中氧含量≤0.5%,严防氧含量超标,并作预见性调节。
用变换气硫化时应防止床层带水。
2. CS2的加入时间不能过早,也不能过晚,一般在催化剂升温至200℃左右加入。
3. 严防油污带入床层。
油污易在高温下炭化,沉积于催化剂颗粒之中,影响催化剂的活性。
油污主要来源,一是半水煤气中带油,特别是回收压缩二段余热后,半水煤气带油更多,因此要经常排放油水分离器、焦炭过滤器倒淋。
二是通过CS2带入。
CS2是有机溶剂,CS2贮罐阀门等所带油污会溶于CS2而带入床层,因此要预先把硫化系统的油清洗干净。
4. 硫化过程中要加强H2S的分析,开始每小时一次,后期半小时一次,分析结果力求准确。
5. CS2是易燃危险品,硫化时要注意安全,加强管理,谨慎操作。
用固体硫化剂代替CS2硫化比较完全。
6. 用高硫煤制得,半水煤气中H2S含量大于2g/m3(标),硫化时可以不加CS2,利用未脱硫的半水煤气自然硫化。
但硫化时间长,催化剂的活性一般不如采用CS2硫化效果好。
因此,自然硫化较少采用。
耐硫变换催化剂装填方案

耐硫变换催化剂装填方案(此方案由山东齐鲁石化院科力公司提供)一、装填催化剂前应具备的条件及确认事项1、确认出口收集器的金属网完好,2、热电偶保护管完好,3、催化剂卸出管盲板法兰已复位,4、炉内清理干净,同时变换炉前系统应确保彻底吹扫干净,5、装填催化剂的临时工棚以搭好,6、对使用的瓷球、触媒、拉西环提前检查数量,规格及型号,核对变换炉格栅、金属丝网,碎片收集器的规格、数量材质确认无误,7、大调斗、吊车到现场及叉车。
二、充填时注意事项1、充填开始前要预先确认充填高度,并在炉内作上标记,2、绝对不可使催化剂、瓷球从0.6m以上高度倒下来,3、设备内部作业前一定要进行气体分析,确认安全后戴上面罩进行作业。
4、操作人员在炉内工作时,不能直接踩在触媒上,要在触媒上铺上木板,防止破损,在作业完成后,必须把使用过的木板拿出炉外。
5、充填作业时中,如果下雨、雪立即停止作业,保护催化剂不被淋湿。
6、在热电偶套管周围充填时,注意不要造成架空。
7、作业时,不要将异物带入炉内(铁销、纸、烟头、泥土等)。
8、应做好装填记录,包括物料的规格、型号和材质,装填的数量,高度,装填的时间等。
9、在装填之前,通常没有必要对催化剂进行过筛,但是在运输及装卸过程中,由于不正确地作业可能是催化剂损坏,若发现磨损或破碎则应过筛。
三、充填的顺序和方法1、瓷球的充填(1)划出瓷球充填的高度,用粉笔作上记号。
(2)把帆布袋接在装催化剂漏斗下面,炉内作业人员拉住布袋出口,避免瓷球直接落到下面摔坏。
(3)将瓷球铺平,确认达到所规定的高度。
(4)催化剂卸出管也要装上瓷球。
(5)将预制好的金属丝正确地铺在瓷球上,留出催化剂卸管口。
2、催化剂的装填a、二段催化剂装填(1)将催化剂装入吊斗(2)把催化剂用起重机调到装填口,由炉口工作人员将催化剂倒入事先安装在炉口的漏斗中,经溜槽进入帆布袋进炉内。
(3)装填一定催化剂后,应停止装填,把表面推平,装填时要移动帆布袋,使催化剂铺平。
耐硫变换催化剂循环硫化方案
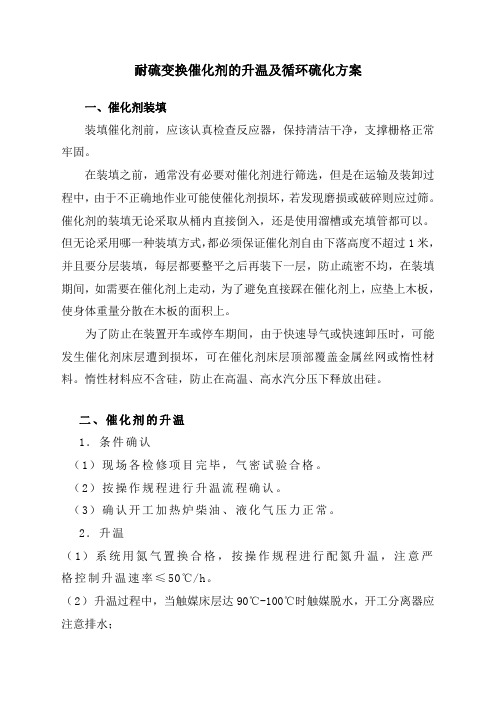
升 0.5 常温~120
30
3
0.5
120
6
温
0.5
120~220
30
3
0.5
220
6
备注 氮气量 20000Nm3/h 恒温释放吸附水
恒温拉平床层温差
三、催化剂的硫化 1、当催化剂床层温度达到 200℃~220℃时,把氢气加到氮气中,控
制反应器入口温度在 200℃~220℃,分析变换炉入口氢气含量 10%(干基) 左右。
耐硫变换催化剂的升温及循环硫化方案
一、催化剂装填 装填催化剂前,应该认真检查反应器,保持清洁干净,支撑栅格正常 牢固。 在装填之前,通常没有必要对催化剂进行筛选,但是在运输及装卸过 程中,由于不正确地作业可能使催化剂损坏,若发现磨损或破碎则应过筛。 催化剂的装填无论采取从桶内直接倒入,还是使用溜槽或充填管都可以。 但无论采用哪一种装填方式,都必须保证催化剂自由下落高度不超过 1 米, 并且要分层装填,每层都要整平之后再装下一层,防止疏密不均,在装填 期间,如需要在催化剂上走动,为了避免直接踩在催化剂上,应垫上木板, 使身体重量分散在木板的面积上。 为了防止在装置开车或停车期间,由于快速导气或快速卸压时,可能 发生催化剂床层遭到损坏,可在催化剂床层顶部覆盖金属丝网或惰性材 料。惰性材料应不含硅,防止在高温、高水汽分压下释放出硅。
H2S 分析 1 次/ 半小时
四、硫化过程中不正常情况的处理 1、床层温升缓慢 配氢量或氮气量过高,入口温度控制较低,可通过增加开工加热器的
蒸汽量,提高变换炉入口温度来控制。 2、床层温度急剧上升 二硫化碳加入过快或入口温度调节过高都可能导致温度急剧上升。可
采取的措施为:降低变换炉入口温度;减少直到停止加入二硫化碳。
变换催化剂升温硫化注意事项
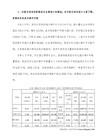
置 换 4~6 200-300 180-200 直 至出 口 硫 化 氢 含 量
≤1g/m3 ,并入系统。
以防电加热器超压。
(3) 在煤气升温结束前,硫化罐应按要求装填好CS2,检查制氮机所送管线是否通畅,升压至
0.1~0.2MPa备用。
3.3. 硫化期
(1) 待低变炉进口温度达210℃,即可用N2将CS2压入系统,用硫化罐出口流量计控制CS2加入量,保证入炉CS2浓度为5~10g/m3,开始硫化。
3.4. 强化期
催化剂层各点为400~450℃,保持~4小时出口H2S含量≥10g/NM3,强化硫化结束。
3.5. 降温置换阶段
(1) 硫化至各段均进入降温置换阶段,控制电炉出口温度200℃,待床层温度降至≤300℃,然后
停止加 CS2置换。
(2) 联系检修拆、加盲板后,即可导气制合格变换气开车。
(3) 变换常压放空运行两小时后至变换气成分合格后方可向后工序送气。
(4) 注意事项:
(1) 升温硫化严格按要求进行,升温期间,单点温度不得超过500℃,升温速率严格按30∽50℃/h
进行。
(2) 硫化过程中,严格控制进口煤气中O2%,严防O2含量跑高造成炉温急骤上升,烧毁触媒, CS
(2) 控制电炉出口温度200~250℃。催化剂床层温度200~300℃,时间约为8~10小时,待于出
口硫化氢≥ 3g/NM3,可认为硫化初期结束。
(3) 硫化时密切注意床层温度,用电加热器组数、CS2加入量及煤气量等调节床层温度。
(4) 硫化时炉进口H2含量应保证≥25%,便于CS2氢解。
反应生成H2S,与CoO、MoO3反应生成CoS、MoS2。
浅析变换工艺催化剂的使用及常见问题的处理

浅析变换工艺催化剂的使用及常见问题的处理作者:永学健张涛来源:《中国化工贸易·下旬刊》2019年第07期摘要:本篇文章中所讲的变换催化剂主要指的是钴、钼系催化剂,这种催化剂使用时间较长,使用面积覆盖也较为广泛,为钴、钼系催化剂的积累了丰富的使用经验。
但是在钴、钼系催化剂这么多年的使用过程之中,也出现了诸多的问题影响了催化剂的正常使用。
因此,笔者针对现如今关于钴、钼系催化剂在使用当中的问题提出自己的论述观点,并且总结出原因分析以及提出此昂对应的解决办法,希望可以对钴、钼系催化剂的使用有一定的借鉴意义。
关键词:变换工艺催化剂;钴、钼系催化剂;催化剂的使用钴、钼系催化剂主要适用于以煤或者是重油为主要原料的合成氨厂,这种催化剂有着超高的耐硫功能,但是在没有或者有很少的硫化氢的环境之中,钴、钼系催化剂的活性就会比较弱。
由于最近几年,人们越发的关注环境保护问题,化肥行业也随之开展了节约能源,降低能源消耗的工作,因此,钴、钼系催化剂由于它的耐硫功能就得到了诸多厂家的青睐,但是在使用的过程之中由于存在着问题没有得到解决,也就造成了催化剂在工作之中出现结焦、失活等现象的发生。
1 钴、钼系催化剂的正确使用在上个世纪50年代的时候,钴、钼系催化剂就是在当时研发的最新型的催化剂,它对一氧化碳的变换工艺有着很好的变幻效果。
最有典型的主要是有K8-11等等。
钴、钼系催化剂主要是通过氧化铝为主要的載体,利用氧化铝改善低温活性性能,钴、钼系催化剂的助催化剂在一般情况之下都是选择碱金属钾。
在进行催化剂的选用的时候,一定要注意不仅是要关注它的活性性能,还要考虑它的强度。
通常情况下来说的话,催化剂的活性与强度是成反比例的,催化剂的活性性能越好,反之,催化剂的强度就会变得非常的差[1]。
催化剂生产商在进行制造催化剂的过程之中要充分的考虑到强度与活性性能二者之间的关系,并且还要找到一个可以达到这两者之间的平衡点。
钴、钼系催化剂的最大的特点就是很高的宽温耐硫性,这种催化剂通常情况之下都具有良好的活性性能、较高的机械强度以及选择性,尤其是在低温变换活性和低硫变换活性这两个方面,在世界上也是处于领先地位的,同时钴、钼系催化剂对高空速、高水气的环境适应能力很强,具有良好的稳定,还具有较大的操作弹性。
耐硫变换催化剂及其使用技术
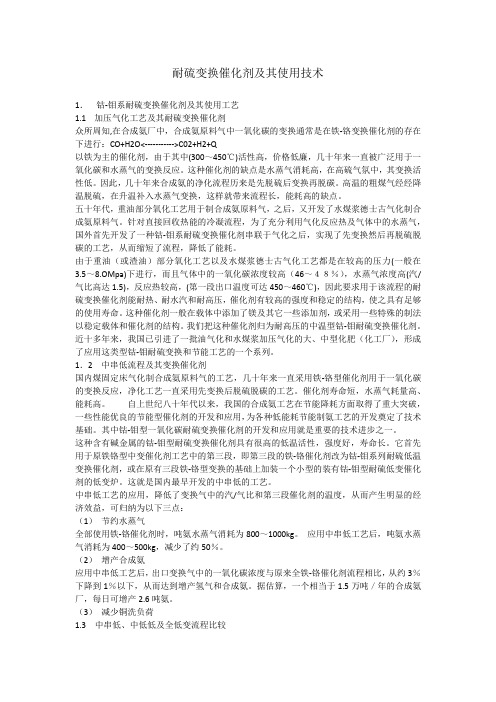
耐硫变换催化剂及其使用技术1.钴-钼系耐硫变换催化剂及其使用工艺1.1加压气化工艺及其耐硫变换催化剂众所周知,在合成氨厂中,合成氨原料气中一氧化碳的变换通常是在铁-铬变换催化剂的存在下进行:CO+H2O<----------->C02+H2+Q以铁为主的催化剂,由于其中(300~450℃)活性高,价格低廉,几十年来一直被广泛用于一氧化碳和水蒸气的变换反应。
这种催化剂的缺点是水蒸气消耗高,在高硫气氛中,其变换活性低。
因此,几十年来合成氨的净化流程历来是先脱硫后变换再脱碳。
高温的粗煤气经经降温脱硫,在升温补入水蒸气变换,这样就带来流程长,能耗高的缺点。
五十年代,重油部分氧化工艺用于制合成氨原料气,之后,又开发了水煤浆德士古气化制合成氨原料气。
针对直接回收热能的冷凝流程,为了充分利用气化反应热及气体中的水蒸气,国外首先开发了一种钴-钼系耐硫变换催化剂串联于气化之后,实现了先变换然后再脱硫脱碳的工艺,从而缩短了流程,降低了能耗。
由于重油(或渣油)部分氧化工艺以及水煤浆德士古气化工艺都是在较高的压力(一般在3.5~8.OMpa)下进行,而且气体中的一氧化碳浓度较高(46~48%),水蒸气浓度高(汽/气比高达1.5),反应热较高,(第一段出口温度可达450~460℃),因此要求用于该流程的耐硫变换催化剂能耐热、耐水汽和耐高压,催化剂有较高的强度和稳定的结构,使之具有足够的使用寿命。
这种催化剂一般在载体中添加了镁及其它一些添加剂,或采用一些特殊的制法以稳定载体和催化剂的结构。
我们把这种催化剂归为耐高压的中温型钴-钼耐硫变换催化剂。
近十多年来,我国已引进了一批油气化和水煤浆加压气化的大、中型化肥(化工厂),形成了应用这类型钴-钼耐硫变换和节能工艺的一个系列。
1.2中串低流程及其变换催化剂国内煤固定床气化制合成氨原料气的工艺,几十年来一直采用铁-铬型催化剂用于一氧化碳的变换反应,净化工艺一直采用先变换后脱硫脱碳的工艺。
耐硫变换催化剂硫化过程

31一、硫化剂的种类合理选用硫化剂是预硫化技术应用的关键,目前常见的硫化机主要划分为以下几种:1.有机硫化剂。
有机硫化剂主要包括有机过氧化物、含硫促进剂和多硫聚合物等,与元素硫一样,有机硫化剂在硫化反应时同样存在反应剧烈、放热集中等问题,而且有机硫化剂预硫化催化剂存在释放硫现象,不利于运输和装填。
2.无机硫化剂。
目前常用的无机硫化剂有元素硫、硫化氢、二硫化碳和硫代硫酸铵等,元素硫作为硫化剂的最明显优势是硫化效率高,与其他硫化剂相比,单位质量硫化剂中硫的含量最高,1mol元素硫可以生成8mol的硫化氢。
而且元素硫常温下化学稳定性较好,不易与空气发生作用,存储、运输和装填较为便利。
但元素硫与催化剂作用较弱,同时硫化反应剧烈,很容易使催化剂烧结。
3.混合硫化剂。
单一使用有机和无机硫化剂在实际应用中都存在一定缺陷,为此,诸多学者将研究重点放在混合硫化剂上。
像将元素硫与石蜡混合作为混合硫化剂或是溶于含有硫醇、脂肪酸的有机聚硫化合物溶液中。
目前常见集中硫化剂的物化性质如下表1所示: 表1 硫化剂物化性质二、预硫化反应机理1.硫化剂分解硫化剂分解是指硫化剂在催化剂作用下通过硫化工艺发生化学反应生成硫化氢的过程。
结合上文给出的几种常见硫化剂写出硫化剂分解过程中发生的化学反应表达式如下:(1)二硫化碳 4H 2+CS 2=CH 4+2H 2S(2)二甲基二硫化物 3H 2+CH 3SSCH 3=2CH 4+2H 2S (3)二甲基硫化物 2H 2+CH 3SCH 3+2H 2=CH 4+H 2S (4)乙硫醇 H 2+CH 3CH 2SH=CH 3CH 3+H 2S(5)正丁硫醇H 2+CH 3CH 2CH 2CH 2SH=CH 3CH 2CH 2CH 3+H 2S 2.催化剂活性组分的相态转化耐硫变换催化剂硫化过程的主要目的有两点,第一,使催化剂中的活性组分处于最佳活性价态。
第二,将催化剂中的金属活性组分转化为硫化物。
钴钼系变换催化剂的硫化步骤和方法

硫化步骤:触媒升温硫化曲线表:阶段执行时间(hr) 空速(h-1 ) 床层各点温度(℃) 入炉H2S含量(g/Nm3 ) 备注1.升温12~14 200~300 常温~210 用煤气将系统置换合格后推电炉升温2.硫化期20~24 100~200 210~300 10~15 待出口气的H2S含量≥3g/Nm3 ,床层穿透3.强化期109 100~200 300~350350~450 15~20 变换炉出口H2S含量≥10g/Nm34.降温置换~8 200~300 180~200 0.05 出口H2S含量≤0.5g/Nm3 ,并入系统生产1、煤气升温阶段(1) 常温~120℃(6~8h),120℃恒温2 h,120~200℃(4h)。
(2) 按升温硫化流程调节好有关阀门,压缩机1台三出送气压力<0.2MPa,最大循环气量15000Nm3/h。
(3) 待电加热器、变换炉各处煤气置换O2<0.5%,电加热器通气正常后,启3组电炉丝开始煤气升温。
(4) 打开循环气体出口阀,关低变炉出口DN150放空阀,将循环气体导入压机一入煤气总管,开始循环升温。
(5) 电加热器升温时,采取必要措施严格按升温曲线进行。
升温期间视各段温升情况及时增减电炉丝组数,调节各段进气阀开度、气量或煤气换热器进出口煤气副线阀等。
当两变换炉床层温差较大时,可用进两炉的升温煤气阀调节不同入炉点的气量。
(6) 升温期间,严格控制煤气中O2<0.5%,防止电加热器起火**,严格控制煤气系统压力不得超过0.3MPa。
(7) 恒温前应先降低热煤气温度。
(8) 在煤气升温结束前3h,两硫化罐应按要求灌装好CS2,并连接好N2瓶,升压至0.45~0.5MPa、并排水后备用。
(9) 升温期间,要注意及时排放油分离器和活性炭滤油器导淋,严防油水带入系统。
(10) 循环升温时,不必开放空,待硫化开始后,可在系统出口处打开放空置换一部分气体,以补充氢气含量。
- 1、下载文档前请自行甄别文档内容的完整性,平台不提供额外的编辑、内容补充、找答案等附加服务。
- 2、"仅部分预览"的文档,不可在线预览部分如存在完整性等问题,可反馈申请退款(可完整预览的文档不适用该条件!)。
- 3、如文档侵犯您的权益,请联系客服反馈,我们会尽快为您处理(人工客服工作时间:9:00-18:30)。
钴钼系耐硫变换催化剂装填及使用过程注意事项
钴钼系耐硫变换催化剂装填及使用过程注意事项
摘要:摘要:从钴钼系耐硫宽温变换催化剂的装填、硫化、接气、操作等方面简述了其生产中的使用要求,提出了操作过程中的注意事项。
关键词:钴钼系催化剂装填硫化活性
一、装填
催化剂的装填是一个十分重要的步骤,要分层装填,每层都要整平之后再装下层,装填后的床层必须平整均匀,严防疏密不均形成沟流,影响催化剂的使用。
1.装填注意事项
1.1当汽气比、CO变换负荷选定后,可简单地由操作压力确定空速。
空速以半水煤气为准,如果原料气中CO含量体积分数约为45%,则选定的空速适当降低。
1.2为防止气体偏流,每段床层的高度不应小于1 m,床层高径比以0.5~1.0为宜。
1.3催化剂装填时,其上下均要铺设铁丝网下面2层,上面1层,在上层铁丝网上放置高度为50~100 mm的耐火球或铝球,以防止冷凝水直接接触催化剂。
二、硫化
1.硫化过程注意事项
在钴钼催化剂中,Mo是主催化剂,Co是助催化剂,对钴钼催化剂的硫化主要是对Mo的硫化。
Mo在硫化时一般Mo+6、Mo+5、Mo+4 3种价态存在,Mo+5与变换反应中的变换活性有关,,由于Mo+6、Mo+4 同时存在,因此Mo不能完全被还原,为保证硫化完全彻底硫化时应注意以下几点。
1.1干态硫化
一般在硫化之前,首先应对催化剂升温,脱除吸附水。
1.2提高H2S浓度
高硫浓度可保证硫化反应的需要,并缩短反应时间,不过在硫化初期不要将H2S含量提得太高,应采取逐渐渗透的方式,避免反应过急,使催化剂温度波动过大。
1.3低温硫化
当床层温度达到180℃时,将气体入口温度降到170~180℃,然后加入CS2,使催化剂在H2S吸收区反应,可避免硫化初期温度超过200℃而引起的异常激烈反应。
主要硫化阶段为180~300℃为保证温度,应将炉温控制在250℃左右,并逐步加大CS2的量。
当分析显示变换炉出口H2S达到1 g/m3或进出口H2S含量相等时,保持运行2 h 即为合格。
1.4高温处理
一般而言,钴钼系催化剂在高于175℃时是H2S的吸收区,其后随温度升高有利于硫化但当温度达到450℃时,催化剂的硫化也达到了极大值,温度如若继续升高,催化剂活性则反而降低。
所以在催化剂基本硫化结束后将催化剂床层温度升到450℃,Mo、Co、S的结构形态将会变化,使催化剂在Mo—Co—S形态中的Co原子数增大到极大值,催化剂活性也达到极大值。
高温处理时, CS2的浓度不一定要非常高,正常时(以H2S计)保持在1~2 g/m3。
1.5硫含量与炉温的关系
钴钼系催化剂硫化时,硫含量与炉温的控制关系应执行“提硫不提温,提温不提硫”的原则。
钴钼系催化剂升温硫化的数据见下表。
催化剂升温硫化数据
1.6硫化坚持原则
“提硫不提温,提温不提硫”,防止触媒严重超温,严格控制触媒温度不超过450℃,如果触媒温度增长过快超过450℃,要立即停加CS2降低氮气入口温度并加大煤气的流量使床层快速降温。
1.7硫化结束后,将氮气系统彻底置换合格,不断补充氮气,各导淋取样分析H2S为零
三、接气
钴钼系催化剂升温硫化结束后,在接原料气时会伴随超温现象的发生,其不仅造成催化剂热衰老,还使催化剂部分有效成分升华,减
少钴钼系催化剂的使用寿命。
通过数年摸索,建议在钴钼系催化剂升温硫化或二次硫化后接气时应注意以下几点。
1.钴钼系催化剂在升温硫化结束之后,要将催化剂床层的温度降到300℃左右,不应太高。
2.钴钼系催化剂在升温硫化结束之后,在对催化剂进行降温时,要加大氮气的排放,加大新鲜氮气的补充,以带出变换炉内过剩的CS2。
3.变换炉在接原料气的同时,一般要立即加入足量的高压蒸汽,同时还要保证充足的H2含量,以防止发生反硫化现象。
4.一旦催化剂温度出现超温现象,严禁停煤气,更不能将煤气闷在变换炉内,可加大氮气补充量,减少煤气加入量,逐渐置换、降温。
四、操作
在日常生产操作时,由于钴钼系催化剂制作方法的限制,其最大的缺点之一是活性易降低,甚至丧失。
所以在操作中注意事项有以下几点。
1.反硫化现象影响
所一般来讲,较高床层温度、较高汽气比、较低的H2S含量是发生反硫化现象的3大原因,只有在这3种情况同时出现时才会发生反硫化现象。
2.冷凝水影响
冷凝水可致使催化剂粘连结块、偏流,甚至组分流失。
3.杂质影响
触媒粉尘、油污及硫等杂质进入炉内,会引起催化剂的物理包裹、粘连和偏流,因此在催化剂的装填或装置运行过程中,可采取增设过滤器等相关防范措施。
4.增压过程要缓慢,当压力增至1.0-1.5MPa时,最好运行3-4个小时后再逐步增压,增压速度≤0.4MPa/min,是催化剂在压力下继续深度硫化,从而发挥最好的催化剂活性。
五、小结
钴钼系催化剂在生产中有很多不利因素,大家要在平时工作中多观察、多分析,就会将不利因素避免,所以在应用钴钼催化剂过程中
要及时调整,及时沟通总结才能保证催化剂长周期稳定运行。
参考文献
[1]宋宪稳、吕洪浩钴钼催化剂超温运行原因分析化肥设计2006年第44卷第5期.
[2]汤太平、杨瑞化钴钼催化剂活性降低原因及对策中氮肥200年第4期.
[3]陈劲松、李小定一氧化碳低温变换工艺及其在中氮肥厂的应用.中氮肥1997年第2期
[4]向德辉、刘惠云化肥催化剂应用手册.化学工业出版社.
作者简介:王亮亮,男,汉族,1984年出生,黑龙江齐齐哈尔人,2008年毕业于齐齐哈尔大学,现任中煤龙化哈尔滨煤化工有限公司净化分厂助理工程师从事煤化工生产管理。
------------最新【精品】范文。