成型各工序工艺要求
流延成型的工艺要求
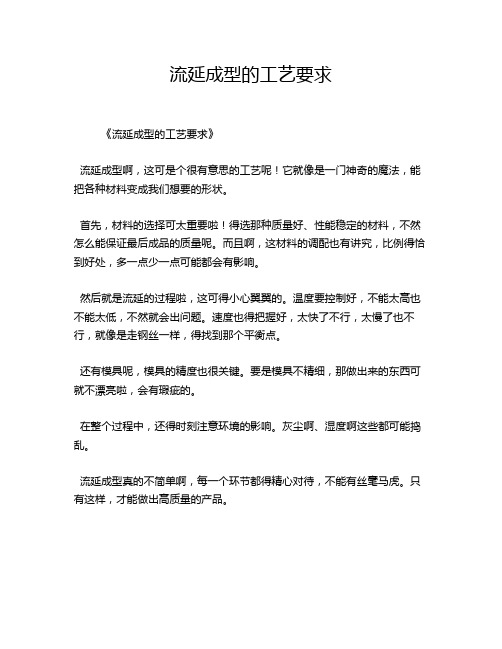
流延成型的工艺要求
《流延成型的工艺要求》
流延成型啊,这可是个很有意思的工艺呢!它就像是一门神奇的魔法,能把各种材料变成我们想要的形状。
首先,材料的选择可太重要啦!得选那种质量好、性能稳定的材料,不然怎么能保证最后成品的质量呢。
而且啊,这材料的调配也有讲究,比例得恰到好处,多一点少一点可能都会有影响。
然后就是流延的过程啦,这可得小心翼翼的。
温度要控制好,不能太高也不能太低,不然就会出问题。
速度也得把握好,太快了不行,太慢了也不行,就像是走钢丝一样,得找到那个平衡点。
还有模具呢,模具的精度也很关键。
要是模具不精细,那做出来的东西可就不漂亮啦,会有瑕疵的。
在整个过程中,还得时刻注意环境的影响。
灰尘啊、湿度啊这些都可能捣乱。
流延成型真的不简单啊,每一个环节都得精心对待,不能有丝毫马虎。
只有这样,才能做出高质量的产品。
橡胶模压成型工艺要求

橡胶模压成型工艺要求
在制造橡胶制品的过程中,橡胶模压成型是一种常用的工艺方法。
橡胶模压成型工艺要求严格,需要注意多个方面以确保产品质量和生产效率。
首先,选择合适的橡胶材料至关重要。
橡胶材料应该符合产品设计的要求,如耐磨、耐油、耐高温等性能。
同时,橡胶材料的硬度、粘度、流动性等参数也需要考虑到模压成型的实际情况。
其次,模具设计是影响产品质量的重要因素之一。
模具应该具有良好的设计,使得产品可以顺利脱模,避免气泡和瑕疵的产生。
模具的材质和表面处理也需要考虑到橡胶材料的特性,以确保成型后产品的表面光滑度和尺寸精度。
在橡胶模压成型的过程中,温度、压力和时间是关键的参数。
温度过高或过低都会影响橡胶材料的流动性和硬度,导致产品质量不稳定。
压力的控制要均匀,以确保橡胶材料能够填充模具的所有细节,避免出现空洞和变形。
成型时间的控制也需要精准,过长或过短都会对产品的性能产生影响。
另外,模具的维护和保养也是至关重要的。
定期清洁模具,检查有无损坏和磨损,确保模具表面平整度和精度。
及时更换老化的模具以避免对产品质量造成影响。
最后,对成型后的产品进行质量检验也是必不可少的环节。
检查产品的尺寸、外观和性能,确保符合设计要求。
如果发现产品有质量问题,需要及时调整模具和工艺参数,避免批量生产出现质量问题。
总的来说,橡胶模压成型工艺是一个需要综合考虑材料、模具设计、工艺参数、维护保养等多个方面因素的复杂过程。
只有严格按照要求操作,才能生产出高质量的橡胶制品。
1。
模压成型工艺条件要求有哪些
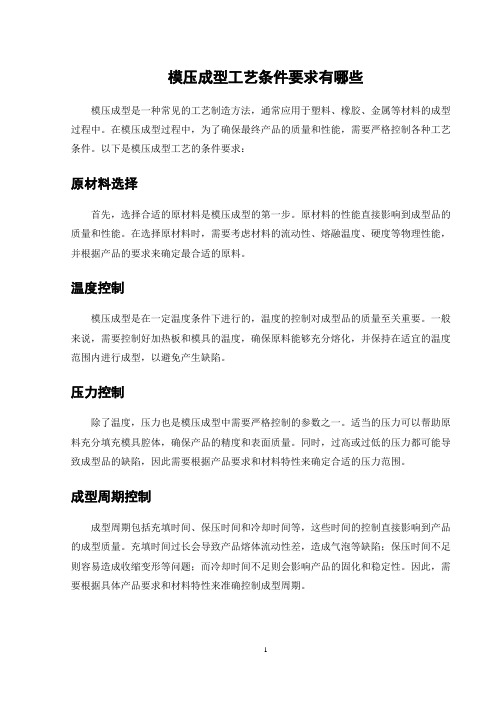
模压成型工艺条件要求有哪些模压成型是一种常见的工艺制造方法,通常应用于塑料、橡胶、金属等材料的成型过程中。
在模压成型过程中,为了确保最终产品的质量和性能,需要严格控制各种工艺条件。
以下是模压成型工艺的条件要求:原材料选择首先,选择合适的原材料是模压成型的第一步。
原材料的性能直接影响到成型品的质量和性能。
在选择原材料时,需要考虑材料的流动性、熔融温度、硬度等物理性能,并根据产品的要求来确定最合适的原料。
温度控制模压成型是在一定温度条件下进行的,温度的控制对成型品的质量至关重要。
一般来说,需要控制好加热板和模具的温度,确保原料能够充分熔化,并保持在适宜的温度范围内进行成型,以避免产生缺陷。
压力控制除了温度,压力也是模压成型中需要严格控制的参数之一。
适当的压力可以帮助原料充分填充模具腔体,确保产品的精度和表面质量。
同时,过高或过低的压力都可能导致成型品的缺陷,因此需要根据产品要求和材料特性来确定合适的压力范围。
成型周期控制成型周期包括充填时间、保压时间和冷却时间等,这些时间的控制直接影响到产品的成型质量。
充填时间过长会导致产品熔体流动性差,造成气泡等缺陷;保压时间不足则容易造成收缩变形等问题;而冷却时间不足则会影响产品的固化和稳定性。
因此,需要根据具体产品要求和材料特性来准确控制成型周期。
模具设计模具设计是模压成型中至关重要的一环。
合理的模具结构可以有效地避免产品缺陷的产生,保证产品的精度和表面质量。
在模具设计中,需要考虑成型品的结构、收缩率、流道设计等因素,确保原料能够充分填充模具,并在成型过程中保持稳定的形状。
综上所述,模压成型工艺条件的要求包括原材料选择、温度控制、压力控制、成型周期控制和模具设计等多个方面。
只有在严格控制这些条件的前提下,才能生产出质量优良的模压成型产品,满足客户的需求并提升企业的竞争力。
密封条成型工艺及生产工序简介

密封条成型工艺及生产工序简介密封条成型工艺及生产工序是指将原材料制成密封条产品的一系列工艺和过程。
下面是该过程的简介。
1. 原材料准备:选择适合的密封材料,如橡胶、硅胶或塑料,并进行初步加工,如切割成条状或片状。
2. 配方调制:根据产品要求,调配出合适的原材料配方,包括添加剂和填充材料,以提高密封条的性能和使用寿命。
3. 混炼:将原材料和配方中的添加剂混合,通过搅拌和热处理等方法,使原料充分混合,确保配方均匀。
4. 挤出成型:将混合好的原材料导入挤出机,通过挤压和模具形成带有密封条形状的连续胶条。
在挤出过程中可以加入压纹、纹理和标记等特殊要求。
5. 切割成型:将挤出的连续胶条切割成固定长度的密封条,可以采用刀切割或拉伸断裂等方法。
6. 成品检验:对切割好的密封条进行外观质量、尺寸精度和物理性能等方面的检验,确保产品符合要求。
7. 包装和存储:将合格的密封条进行包装,并标明产品信息、生产日期和储存条件等,以便运输和存储。
以上是密封条成型工艺及生产工序的简介。
在实际生产中,还需要根据不同产品要求和工艺可行性,进行材料采购、模具制造和设备调试等前期准备工作,以确保产品的质量和效率。
密封条成型工艺及生产工序是密封条生产过程中极为关键的环节,直接关系到产品的质量和性能。
下面将更详细地介绍密封条成型工艺及生产工序的相关内容,以及一些常见的技术要点和注意事项。
1. 原材料准备:在密封条的生产过程中,常用的材料有橡胶、硅胶和塑料。
橡胶密封条具有耐磨损、耐油、耐高温等特点,常用于汽车、机械设备等领域。
硅胶密封条具有耐高温、耐酸碱、耐腐蚀等特点,适用于电子、医疗器械等领域。
塑料密封条具有耐腐蚀、阻燃性好等特点,适用于建筑、家居等领域。
在制备原材料时,首先需要选择合适的材料类型,并根据产品要求进行初步加工。
例如,对于橡胶密封条,可以进行胶片切割或拉伸成条状,以供后续工序使用。
2. 配方调制:密封条在使用过程中需要具备优异的性能,如抗拉伸性、耐热性、耐腐蚀性等。
成型作业指导书

成型作业指导书
1.目的:为规范成型操作,确保本工序产品符合要求。
2.范围:适应本公司裁断,成型工序。
3.职责:在生产技术厂长领导下,成型车间负责本过程的控制,操
作工人按操作规程严格工艺操作。
4.裁断:质量标准
裁断公差宽度为5mm,角度为0.5度。
帘布必须摆放平整,无折子、无杂质、无劈缝,无胶豆等质量问题。
操作工必须按照施工标准严格操作角度宽度要符合施工标准。
5.成型:
(1)工艺条件:风压0.4-0.8Mpa
(2)质量标准:成型筒宽度,项点周长务必正确,内面胶贴附不得折皱,对正中心,帘子线贴符对齐标线,确保帘线无折子,
无漏白,无杂物,无断线,无胶豆等问题,各层方向相反,
接头无脱开,接头压线为5-7根,钢丝圈放上下左右必须对
正并压实,帘线接头一定要错开。
胎面胶贴符对正中心线。
胎面接头要接平不要过大或过小并压实,把成好的胎胚挂在
架车上不得落地。
热压成型工艺流程

热压成型工艺流程热压成型是一种常用的塑料加工工艺,其工艺流程主要包括原材料准备、预热、热压、冷却和后处理等步骤。
下面将详细介绍各个步骤的具体内容。
首先是原材料准备。
热压成型通常使用的原材料是塑料颗粒或者塑料片材。
在进行热压成型之前,需要根据产品的要求选择合适的原材料,并按照一定的比例将其混合均匀,以确保产品的性能和质量。
接下来是预热。
预热是为了提高塑料的流动性和降低成型时间。
在预热的过程中,需要将混合好的塑料原料加热至一定的温度,通常为塑料的熔化温度。
预热温度的确立需要根据不同的塑料材料来确定。
第三步是热压。
在热压过程中,将预热好的塑料原料放置于加热板之间,然后施加一定的压力。
同时,加热板会继续为塑料原料提供热量,使其保持在熔化状态。
塑料原料在热压的过程中会流动,填满热压模具的腔体,形成所需的产品形状。
第四步是冷却。
冷却是为了使热压成型后的塑料产品固化并保持其形状。
冷却的方法主要有自然冷却和水冷却两种。
在自然冷却的情况下,塑料产品会通过自身散热而进行冷却。
而在水冷却的情况下,可以将塑料产品放置于水中进行快速冷却,以提高生产效率。
最后是后处理。
后处理一般包括产品的修整、清洁和质量检查等步骤。
修整是为了将产品表面的毛刺和余料去除。
清洁是为了将产品表面的杂质和污染物清除。
质量检查是为了确保产品的尺寸和质量满足要求。
根据产品的要求,可能还需要对产品进行表面处理和组装等工序。
热压成型工艺流程的每个步骤都非常重要,任何一个环节的问题都可能导致产品的质量下降。
因此,在实际操作中需要严格控制每个步骤的工艺参数,并进行充分的工艺试验和质量检查,以确保产品能够满足客户的要求。
同时,还需要对每个步骤进行维护和保养,以确保设备的正常运行,提高生产效率和产品质量。
成型车间制作流程
工序:刷中底、帮脚白胶无钉夹包,要求楦头部、中底头部、刷少量白胶,宽度不得超过15mm,若过多会影响脱楦;中底板刷胶一圈宽度15-18mm,不可遗漏或堆胶;鞋帮包脚刷胶宽度10-12mm均匀到位,若里布未修到位,需退上道工序重修,不得流入下道工序,分清左右脚、码号,成双作业。
工序:抹里布、粘中底、前帮手前帮手要求检查每只鞋帮需符合上述要求,同楦号、码号一致再操作,操作过程中参照生产确认样,注意头帮高低、机心圆顺、前后中心点同楦对齐;前撑两侧鞋帮搭地,左右平行,内侧允许向前1-3mm,脚背贴楦,包头平整,包脚内外侧基本一致,头部支口平整,不可有花角。
工艺操作说明工序:拉中帮首先检查上道工序是否符合第八点的要求才可操作,否则退回上道工序一律不予操作;操作过程中,内里、支跟、拉贴楦同帮面平顺;必须先拉内腰,再拉外腰,后支跟、内外边脚长短是否一致,内腰允长2-3mm,后帮严格按照鞋楦定位点及后帮包脚大小;注意脚背、腰档必须贴楦;后跟小割线平顺、接缝不可歪斜,后上口、内外基本平行,一般允许内脚高1-2mm;特别注意,内外包脚大小基本一致,腰档搭地,装饰物内外基本平行;支口平整,后帮处内外拉中帮时,稍往头部带一些,便利后帮操作,成双作业。
工艺操作说明工序:后帮机、锤鞋后帮手根据不同楦型,首先调节好角度,符合操作基本要求,后帮高度严格按照定位线要求作业,保证后帮支口平整,不可有花角;成双配对作业流到下道工序。
锤鞋为半成品验收:其职责主要是检查以上工序(第五—十条)操作要求。
帮面贴楦、高低一致、支口平整、机心圆顺,前、中、后三点一线,不可歪斜,成双作业。
工序:画线、打磨根据底型,由组长做好相应的垫片,注意同双高底一致,不要歪斜,前后包脚拉磨打平,面料支口不可磨断,轮机上打磨,会发生安全事故。
工艺操作说明工序:底处理、面处理底、面处理按组长指导,根据不同材料用相对应的处理剂;帮面要先清理灰尘,再刷处理剂;按底型画线位,不可外溢到帮面上;TPR材料鞋底刷处理剂时,务必均匀到位不可漏刷,更不可有处理剂堆在上面,外侧底边若刷到处理剂应及时处理掉,处理不掉的应作废品处理,绝对不可流到下道工序。
鞋厂成型各工序工艺要求
成型各工序工艺要求一:成型前段流水工序1.穿鞋带:松紧要适度.2.套楦:套楦要求鞋面的标志点部位与鞋楦的相应点对正,尤其是后帮中缝与鞋楦的后弧中心线对正,鞋面的前端中心点与鞋楦的同一部位对点对正,鞋面口门中心与鞋楦背中心线对正,鞋面套在鞋楦上时,不得歪斜,扭转,各个部位的松紧程度均与一致。
(针对全套和半套鞋)3.车网脚线:车缝是时尽量靠边,车缝距离1—3毫米,针距2。
5—3针/厘米,沿皮料边高出0。
3厘米车缝。
前后车缝需拉顺、平整,不可起皱、要车缝住里布,车缝一圈。
如果里布长度不足,须加接长,在车缝网脚。
(针对敲帮鞋)4.刷港宝药水:要均匀到位,不能刷太多外溢,或没有刷到位。
及刷过药水的要及时生产,不能堆放太久,以免港宝药水挥发。
(针对使用港宝后衬的鞋面)5.刷白乳胶:刷中底上的白乳胶宽度为2—3厘米,鞋面上网脚的宽度为1。
2-1。
5厘米,不能刷得太宽,或污染到鞋面.且中底和鞋面号码一定要配套,不能错码,(如果中底不是用订上去的要在鞋楦和中底两头刷少许白乳胶)6.过加热烤箱7.绷前帮:根据鞋楦的大小型号,调整好爪子形状,撑台高度(撑台上升高度超过扫刀1—2毫米),压头压着时间为3-4秒,二次压力为200—400千牛。
绷帮前将鞋面套在鞋楦上,鞋面可能较紧,这时将鞋面后跟抬高,先用第一抓对准中心点将鞋面固定,绷第二、三抓时,将鞋面里布拉顺往下拉,用力要适中,保证鞋面贴楦。
为第三抓留下余地.要保证鞋头不可歪斜、高低.8.拉中帮:拉帮顺序为,先内腰、后外腰,外腰由左至右,内腰由右至左。
要到贴楦,内外腰高低一致.9.绷后帮:后帮机压着时间为3秒,压着力为350-400千牛,后跟高低要一致,里布不能有起皱现象。
10.定点:用圆规等工具在鞋头或后跟上规定的高度标记画线,确保同一双鞋的高度统一。
11.画线:根据每款鞋的型体配置各种鞋底画线模,左右两台画线机的压力要一致,鞋面上的画线要清晰,要与大底弧度一致,同双鞋鞋头后跟高度要一致。
鞋厂成型各工序工艺要求
成型各工序工艺要求一:成型前段流水工序1.穿鞋带:松紧要适度.2.套楦:套楦要求鞋面的标志点部位与鞋楦的相应点对正,尤其是后帮中缝与鞋楦的后弧中心线对正,鞋面的前端中心点与鞋楦的同一部位对点对正,鞋面口门中心与鞋楦背中心线对正,鞋面套在鞋楦上时,不得歪斜,扭转,各个部位的松紧程度均与一致。
(针对全套和半套鞋)3.车网脚线:车缝是时尽量靠边,车缝距离1-3毫米,针距2.5-3针/厘米,沿皮料边高出0.3厘米车缝。
前后车缝需拉顺、平整,不可起皱、要车缝住里布,车缝一圈。
如果里布长度不足,须加接长,在车缝网脚。
(针对敲帮鞋)4.刷港宝药水:要均匀到位,不能刷太多外溢,或没有刷到位。
及刷过药水的要及时生产,不能堆放太久,以免港宝药水挥发。
(针对使用港宝后衬的鞋面)5.刷白乳胶:刷中底上的白乳胶宽度为2-3厘米,鞋面上网脚的宽度为1.2-1.5厘米,不能刷得太宽,或污染到鞋面。
且中底和鞋面号码一定要配套,不能错码,(如果中底不是用订上去的要在鞋楦和中底两头刷少许白乳胶)6.过加热烤箱7.绷前帮:根据鞋楦的大小型号,调整好爪子形状,撑台高度(撑台上升高度超过扫刀1-2毫米),压头压着时间为3-4秒,二次压力为200-400千牛。
绷帮前将鞋面套在鞋楦上,鞋面可能较紧,这时将鞋面后跟抬高,先用第一抓对准中心点将鞋面固定,绷第二、三抓时,将鞋面里布拉顺往下拉,用力要适中,保证鞋面贴楦。
为第三抓留下余地。
要保证鞋头不可歪斜、高低。
8.拉中帮:拉帮顺序为,先内腰、后外腰,外腰由左至右,内腰由右至左。
要到贴楦,内外腰高低一致。
9.绷后帮:后帮机压着时间为3秒,压着力为350-400千牛,后跟高低要一致,里布不能有起皱现象。
10.定点:用圆规等工具在鞋头或后跟上规定的高度标记画线,确保同一双鞋的高度统一。
11.画线:根据每款鞋的型体配置各种鞋底画线模,左右两台画线机的压力要一致,鞋面上的画线要清晰,要与大底弧度一致,同双鞋鞋头后跟高度要一致。
塑料压铸成型的工艺和流程
三、塑料制品成型阶段
在进行塑料制品成型之前,需要准备好塑料原料和成型设备。
通过上述的流程,就可以完成塑料压铸成型的制造过程。塑料压铸成型具有成本低、生产效率高、制品精度高等优点,在各个行业中得到了广泛应用。
塑料压铸成型的工艺和流程
下载温馨提示:该文档是我店铺精心编制而成,希望大家下载以后,能够帮助大家解决实际的问题。文档下载后可定制随意修改,请根据实际需要进行相应的调整和使用,谢谢!
并且,本店铺为大家提供各种各样类型的实用资料,如教育随笔、日记赏析、句子摘抄、古诗大全、经典美文、话题作文、工作总结、词语解析、文案摘录、其他资料等等,如想了解不同资料格式和写法,敬请关注!
Download tips: This document is carefully compiled by theeditor. I hope that after you download them,they can help yousolve practical problems. The document can be customized andmodified after downloading,please adjust and use it according toactual needs,thank you!
四、后处理阶段
在塑料制品成型完成后,还需要进行一些后处理工作,以保证产品质量和外观。
1.去除余料:成型完成后,需要将塑料制品从模具中取出,并去除余料和毛刺等不良部位。
- 1、下载文档前请自行甄别文档内容的完整性,平台不提供额外的编辑、内容补充、找答案等附加服务。
- 2、"仅部分预览"的文档,不可在线预览部分如存在完整性等问题,可反馈申请退款(可完整预览的文档不适用该条件!)。
- 3、如文档侵犯您的权益,请联系客服反馈,我们会尽快为您处理(人工客服工作时间:9:00-18:30)。
成型各工序工艺要求
一:成型前段流水工序
1. 穿鞋带:松紧要适度.
2. 套楦:套楦要求鞋面的标志点部位与鞋楦的相应点对正,尤其是后帮中缝与鞋楦的后弧中心线对正,鞋面的前端中心点与鞋楦的同一部位对点对正,鞋面口门中心与鞋楦背中心线对正,鞋面套在鞋楦上时,不得歪斜,扭转,各个部位的松紧程度均与一致。
(针对全套和半套鞋)
3. 车网脚线:车缝是时尽量靠边,车缝距离1-3毫米,针距2.5-3针/厘米,沿皮料边高出0.3厘米车缝。
前后车缝需拉顺、平整,不可起皱、要车缝住里布,车缝一圈。
如果里布长度不足,须加接长,在车缝网脚。
(针对敲帮鞋)
4. 刷港宝药水:要均匀到位,不能刷太多外溢,或没有刷到位。
及刷过药水的要及时生产,不能堆放太久,以免港宝药水挥发。
(针对使用港宝后衬的鞋面)
5. 刷白乳胶:刷中底上的白乳胶宽度为2-3厘米,鞋面上网脚的宽度为1.2-1.5厘米,不能刷得太宽,或污染到鞋面。
且中底和鞋面号码一定要配套,不能错码,(如果中底不是用订上去的要在鞋楦和中底两头刷少许白乳胶)
6. 过加热烤箱
7. 绷前帮:根据鞋楦的大小型号,调整好爪子形状,撑台高度(撑台上升高度超过扫刀1-2毫米),压头压着时间为3-4秒,二次压力为200-400千牛。
绷帮前将鞋面套在鞋楦上,鞋面可能较紧,这时将鞋面后跟抬高,先用第一抓对准中心点将鞋面固定,绷第二、三抓时,将鞋面里布拉顺往下拉,用力要适中,保证鞋面贴楦。
为第三抓留下余地。
要保证鞋头不可歪斜、高低。
8. 拉中帮:拉帮顺序为,先内腰、后外腰,外腰由左至右,内腰由右至左。
要划伤、车线爆开一律返工。
6. 鞋面任何部位花角、发角、折皱不平顺,一律返工。
7. 鞋头高低误差1.5㎜以上者一律返工。
8. 后跟歪斜误差2㎜以上者一律返工。
9. 鞋头绷帮大小需符合工艺说明要求,左右脚大小统一,高低误差1.5㎜内配双。
10. 针车脱线、跳针、浮线以及裁断皮革缺陷或者装饰配件松动脱落等不良现象应返修。
11. 中底不可超出鞋楦边缘1.5㎜,中底走位,卷折一律返工。
二:成型中段流水工艺要求
1. 配双:同双的半成品,左右脚号码一致、配色必须一致。
检查鞋头大小;后跟高度是否一致,如有问题必须及时调整更改,并向管理人员反映。
2. 配底:检查鞋底品质,如有不良应剔除。
同一双鞋底左右脚号码必须一致,且鞋底号码必须与鞋面号码配对。
检查鞋面号码与鞋楦号码是否一致,有无同边,单脚,将同号码的楦、底配双成对放入流水线。
3. 刷鞋面和鞋底处理剂:鞋面/大底处理按不同材质正确使用处理剂,刷鞋面时必须按画线来刷,不能超过画线标记。
刷完边侧,底部也需回刷。
刷鞋底时不能把处理剂漏到大底边或凝结在大底上,且各个部位药水都要全部刷到位。
4. 刷鞋面和鞋底胶:1. 刷鞋面胶按照定位线从鞋后跟外侧刷起,经鞋头绕鞋一圈,不能出现积胶、欠胶、溢胶、接缝处回胶现象。
胶水要刷均匀且薄,不要使刷胶部位的胶水粘到不该刷得地方。
不要使胶水凝结在皮料的连接处。
周围刷胶不可超出画线及没有刷到画线处。
二次刷胶和第一次刷法一样,就是不能未刷到或超过一次胶。
2. 刷大底胶第一遍要稀一些,使胶水能够充分侵润被粘物的表面,有利于胶水被粘物内部的扩散和渗透。
刷胶方法是往复推刷,因为单向刷胶时,被粘物表面上被磨起的绒毛会向一侧倾倒,产出绒毛上部有胶、下部无胶的结果。
而双向往复刷胶则可使胶水充分侵润被粘物的表面。
第二遍刷胶的浓度要高于头遍胶,二遍胶对提高剥离强度起着决定性的作用。
头遍胶对黏合强度的提高几乎不起作用,但由于头遍胶的作用是侵润被粘物的表面,并扩散、渗透到被粘去的内部,以便形成胶粘过度层,为二遍胶发挥作用打好基础。
刷胶方法是单向推刷,这样可以避免胶水产生堆积,胶膜的厚薄也比较均匀,刷胶时应用力适中,每次刷胶完后都必须干。