机床精度(学生实验报告)解析
机床精度(学生实验报告)

三 、实验原理
机床几何精度测量
按 JB2314—78 普通机床规定,机床精度检 验包括机床导轨直线度、垂直度、平行度、 端面的平面度,机床部件之间直线度、垂直 度、平行度、同轴度,机床部件的运动精度, 主轴回转精度等18项。
四、 实验步骤与方法
►
框式水平仪的工作原理: 框式水平仪主要部分是一个弧形玻璃管,它的内壁磨成100米左右的 曲率半径。刻有刻度的玻璃管内充以少量乙醚液体,中间留一个气泡。 如图1所示。不论水平仪放在什么位置,玻璃管中的页面总是处于水 平,气泡总是向高处移动,读出气泡两端边缘,移动的格数,即可求 出相应的高度差。水平仪的刻度值为0.02/1000,它表示将该水平仪 放在1米长的平尺表面上,在平尺右端垫起0.02mm的高度,平尺便倾 斜一个a角,此时,水平仪正好移动一个刻度值。
△H △H L1 L
图1 水平仪测量升落差的原理图
►
如果我们在实验中,框式水平仪不是放在1米的平尺上, 而是放在200mm的平板上,那么△H为多少呢Tga=△H △H=200*Tga=0.004mm 水平仪读数的符号,习惯上规定:气泡移动方向和水平 移动方向相同时读数为正值,相反时为负值。
►
1. 溜板在垂直水平面的不直度
反向间隙误差可能起因
► 用于弥补原有反向间隙而对机床进行的反向间补
偿的数值过大,导致原来具有正值反向间隙问题 的机床出现负值反向间隙。 ► 机器可能受到编码器滞后现象的影响 ► 在机床的导轨中可能存在间隙,导致当机床在被 驱动换向时出现在运动中跳跃。
反向间隙对加工带来的影响
在机器上负值反向间隙的影响为圆弧插 补的刀具轨迹将出现一向内凹的跳跃。
主轴锥孔中心线的径向跳动
测量位置 a b 1 2 允差 是否合格
机床的实验报告

机床的实验报告机床的实验报告一、引言机床是现代制造业中不可或缺的重要设备,它对于产品的加工和制造起着至关重要的作用。
为了更好地了解机床的工作原理和性能特点,本次实验旨在通过对机床进行测试和分析,探讨其工作效率和精度等方面的问题。
二、实验目的1.了解机床的基本结构和工作原理;2.测试机床在不同工况下的工作效率;3.测量机床的加工精度,并分析其影响因素。
三、实验装置和方法本次实验使用的机床为数控车床,其主要组成部分包括床身、主轴、进给系统等。
实验过程中,我们将通过调整主轴转速和进给速度来模拟不同的工况。
同时,使用测量工具如卡尺、百分表等来测量加工件的尺寸和表面粗糙度。
四、实验结果与分析1.工作效率测试通过改变主轴转速和进给速度,我们测试了机床在不同工况下的工作效率。
结果显示,随着主轴转速和进给速度的增加,机床的加工速度也相应增加。
然而,当速度达到一定程度后,加工效率的提升并不明显,甚至可能导致加工质量下降。
因此,在实际生产中,需要根据具体情况选择适当的工作参数,以达到最佳的加工效果。
2.加工精度测试为了评估机床的加工精度,我们测量了加工件的尺寸和表面粗糙度。
实验结果表明,机床的加工精度受到多个因素的影响,如机床本身的结构和刀具的质量等。
此外,材料的性质和切削液的使用也会对加工精度产生一定的影响。
因此,在实际生产中,需要综合考虑这些因素,采取相应的措施来提高加工精度。
五、实验结论通过本次实验,我们了解了机床的基本结构和工作原理。
同时,我们还测试了机床在不同工况下的工作效率和加工精度,并分析了影响机床性能的因素。
通过这些实验结果,我们可以得出以下结论:1.机床的工作效率受到主轴转速和进给速度的影响,需要根据具体情况选择适当的工作参数;2.机床的加工精度受到多个因素的影响,包括机床本身的结构、刀具的质量以及材料的性质等;3.在实际生产中,需要综合考虑这些因素,采取相应的措施来提高机床的工作效率和加工精度。
机床检测实习报告
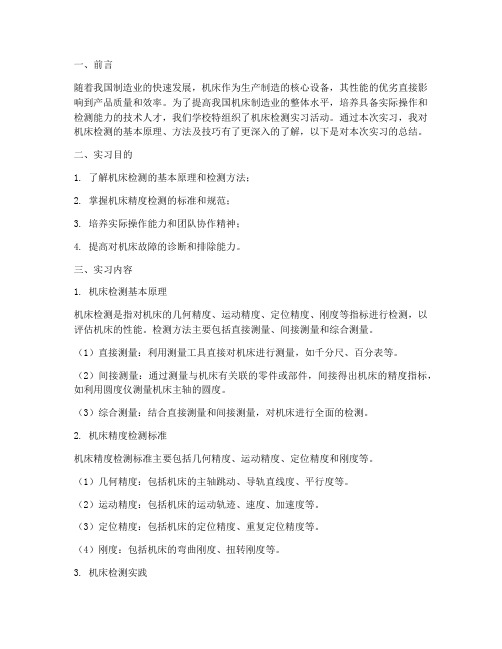
一、前言随着我国制造业的快速发展,机床作为生产制造的核心设备,其性能的优劣直接影响到产品质量和效率。
为了提高我国机床制造业的整体水平,培养具备实际操作和检测能力的技术人才,我们学校特组织了机床检测实习活动。
通过本次实习,我对机床检测的基本原理、方法及技巧有了更深入的了解,以下是对本次实习的总结。
二、实习目的1. 了解机床检测的基本原理和检测方法;2. 掌握机床精度检测的标准和规范;3. 培养实际操作能力和团队协作精神;4. 提高对机床故障的诊断和排除能力。
三、实习内容1. 机床检测基本原理机床检测是指对机床的几何精度、运动精度、定位精度、刚度等指标进行检测,以评估机床的性能。
检测方法主要包括直接测量、间接测量和综合测量。
(1)直接测量:利用测量工具直接对机床进行测量,如千分尺、百分表等。
(2)间接测量:通过测量与机床有关联的零件或部件,间接得出机床的精度指标,如利用圆度仪测量机床主轴的圆度。
(3)综合测量:结合直接测量和间接测量,对机床进行全面的检测。
2. 机床精度检测标准机床精度检测标准主要包括几何精度、运动精度、定位精度和刚度等。
(1)几何精度:包括机床的主轴跳动、导轨直线度、平行度等。
(2)运动精度:包括机床的运动轨迹、速度、加速度等。
(3)定位精度:包括机床的定位精度、重复定位精度等。
(4)刚度:包括机床的弯曲刚度、扭转刚度等。
3. 机床检测实践在实习过程中,我们先后对车床、铣床、磨床等不同类型的机床进行了检测。
具体操作如下:(1)检测机床的主轴跳动:使用百分表测量主轴在不同位置的高度差,以评估主轴的跳动情况。
(2)检测导轨直线度:使用水平仪和千分尺测量导轨的直线度,以评估导轨的精度。
(3)检测机床的定位精度:使用专用测量工具对机床进行定位精度检测,如测量工件在机床上的重复定位误差。
(4)检测机床的刚度:使用压杆法或扭杆法检测机床的弯曲刚度和扭转刚度。
四、实习体会1. 通过本次实习,我对机床检测的基本原理、方法及技巧有了更深入的了解,提高了自己的实际操作能力。
最新机床实验报告
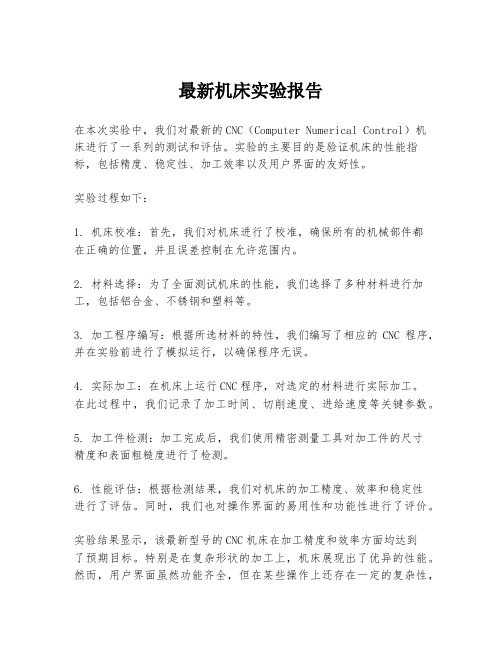
最新机床实验报告
在本次实验中,我们对最新的CNC(Computer Numerical Control)机床进行了一系列的测试和评估。
实验的主要目的是验证机床的性能指标,包括精度、稳定性、加工效率以及用户界面的友好性。
实验过程如下:
1. 机床校准:首先,我们对机床进行了校准,确保所有的机械部件都
在正确的位置,并且误差控制在允许范围内。
2. 材料选择:为了全面测试机床的性能,我们选择了多种材料进行加工,包括铝合金、不锈钢和塑料等。
3. 加工程序编写:根据所选材料的特性,我们编写了相应的CNC程序,并在实验前进行了模拟运行,以确保程序无误。
4. 实际加工:在机床上运行CNC程序,对选定的材料进行实际加工。
在此过程中,我们记录了加工时间、切削速度、进给速度等关键参数。
5. 加工件检测:加工完成后,我们使用精密测量工具对加工件的尺寸
精度和表面粗糙度进行了检测。
6. 性能评估:根据检测结果,我们对机床的加工精度、效率和稳定性
进行了评估。
同时,我们也对操作界面的易用性和功能性进行了评价。
实验结果显示,该最新型号的CNC机床在加工精度和效率方面均达到
了预期目标。
特别是在复杂形状的加工上,机床展现出了优异的性能。
然而,用户界面虽然功能齐全,但在某些操作上还存在一定的复杂性,
建议制造商进一步优化。
总体而言,该机床是一款性能可靠、加工能力强的设备,适合用于精密加工领域。
未来的工作将集中在进一步优化操作流程和提高自动化程度上,以满足更广泛的工业应用需求。
机床实验报告

机床实验报告一、实验目的本次机床实验的主要目的是深入了解机床的工作原理、性能特点以及操作方法,并通过实际操作和数据测量,评估机床在不同加工条件下的精度、效率和稳定性,为后续的生产加工提供可靠的参考依据。
二、实验设备本次实验所使用的机床为_____型数控机床,该机床具有高精度、高速度和高自动化程度等特点。
其主要技术参数如下:1、行程:X 轴_____mm,Y 轴_____mm,Z 轴_____mm。
2、主轴转速:最高_____r/min,最低_____r/min。
3、进给速度:X 轴_____mm/min,Y 轴_____mm/min,Z 轴_____mm/min。
4、定位精度:X 轴_____mm,Y 轴_____mm,Z 轴_____mm。
此外,实验还配备了各种刀具、量具、夹具以及计算机辅助设计与制造(CAD/CAM)软件等。
三、实验材料实验所用的材料为_____材质的圆柱形毛坯,其直径为_____mm,长度为_____mm。
四、实验内容与步骤1、机床的开机与回零操作打开机床总电源,启动数控系统。
依次按下“回零”按钮,使机床的 X、Y、Z 轴回到机床坐标系的原点。
2、刀具的安装与对刀操作根据加工工艺要求,选择合适的刀具,并将其安装在机床的刀库中。
采用手动方式移动机床坐标轴,使刀具靠近工件,并通过试切法对刀,确定刀具在机床坐标系中的位置。
3、程序的编制与输入使用 CAD/CAM 软件生成加工程序,或者手动编写加工程序。
通过数控系统的操作界面,将程序输入到机床的控制器中。
4、机床的调试与加工对输入的程序进行语法检查和模拟运行,确保程序的正确性。
调整机床的加工参数,如主轴转速、进给速度、切削深度等。
启动机床,进行实际加工,并在加工过程中密切观察机床的运行状态,及时处理出现的问题。
5、加工质量的检测与分析加工完成后,使用量具对工件的尺寸、形状和表面粗糙度等进行检测。
将检测结果与设计要求进行对比,分析加工误差产生的原因,并提出改进措施。
加工机床精度测试报告
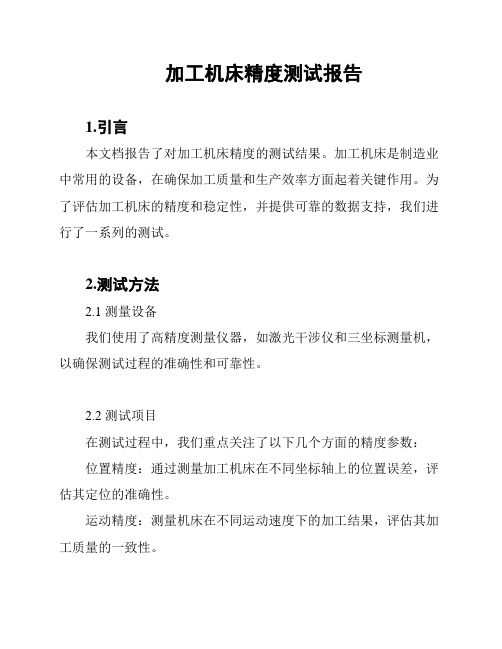
加工机床精度测试报告1.引言本文档报告了对加工机床精度的测试结果。
加工机床是制造业中常用的设备,在确保加工质量和生产效率方面起着关键作用。
为了评估加工机床的精度和稳定性,并提供可靠的数据支持,我们进行了一系列的测试。
2.测试方法2.1 测量设备我们使用了高精度测量仪器,如激光干涉仪和三坐标测量机,以确保测试过程的准确性和可靠性。
2.2 测试项目在测试过程中,我们重点关注了以下几个方面的精度参数:位置精度:通过测量加工机床在不同坐标轴上的位置误差,评估其定位的准确性。
运动精度:测量机床在不同运动速度下的加工结果,评估其加工质量的一致性。
重复定位精度:通过多次定位同一位置,测量其位置误差的稳定性和可重复性。
3.测试结果3.1 位置精度测试结果经过多次测试和数据分析,我们得出如下结论:加工机床在X轴和Y轴上的位置精度分别为±0.02mm和±0.03mm,满足我们的要求。
在Z轴上的位置精度为±0.05mm,略低于我们的期望值,需要进一步调整和优化。
3.2 运动精度测试结果我们测试了机床在不同运动速度下的加工结果,发现加工质量的一致性较好,并没有明显的速度依赖性。
各轴的位置误差在设定范围内,达到了我们的要求。
3.3 重复定位精度测试结果通过多次定位同一位置进行测试,我们发现加工机床的重复定位精度非常稳定,位置误差小于±0.02mm,满足了我们的要求。
4.结论在本次加工机床精度测试中,我们得出以下结论:加工机床的位置精度满足要求,但Z轴的位置精度仍可进一步优化。
加工机床的运动精度和重复定位精度表现良好,满足我们对加工质量和稳定性的要求。
5.建议和改进措施针对Z轴位置精度不达标的问题,我们建议采取以下改进措施:对机床进行更详细的调整和校准,以提高Z轴的位置精度。
定期对加工机床进行维护和保养,确保其保持良好的工作状态。
不定期进行精度测试,并根据测试结果进行相应的调整和优化。
机床几何精度检验实验报告
河北师范大学机床几何精度检验实验指导书专业__________班级________实验小组成员_______________________________________一、实验目的1、熟悉机床几何精度检验的内容原理和方法和步骤。
2、掌握仪器的使用以及实验数据的处理,误差曲线的绘制等。
3、通过实验了解被实验机床几何精度情况及与加工精度的关系,掌握机床几何精度检验方法。
4、深刻理解加工精度的概念,认识机床精度的重要性。
二、实验设备和仪器设备:CA6140车床1台,C620-1车床两台仪器:框式水平仪1个,验棒2个,千分表3个,磁力表座3个。
三、实验内容四、实验方法及步骤(一)床身导轨的直线度和导轨在同一平面在内1、床身导轨在垂直平面内的直线度将水平仪纵向放置在溜板上靠近和床身结合点前导轨处,从刀架处于主轴箱一端的极限位置开始,自左向右一次移动溜板,每次移动的距离应等于或接近于检验局部误差的长度。
记录溜板在每一位置时水平仪的读数。
2、床身导轨在同一平面内检验方法同上,但水平仪横向放置在两导轨间的流板上。
(二)溜板移动在水平面内的直线度在前后顶尖顶紧一根检验棒,刀架上装一千分表,使其测头转在检验棒的側母线上。
调整尾座,使千分表在检验棒的两端相等。
然后移动溜板检验,千分表在溜板全部行程上的读数的最大代数值差,就是溜板移动在水平面内直线度误差。
(三)主轴定心轴颈的跳动将千分表安装在机床固定部件上,使千分表测头垂直于主轴定心轴颈并触及主轴定心轴颈;旋转主轴,千分表读数最大差值即为主轴定心轴颈的径向跳动误差。
(四)主轴锥孔中心线的径向跳动将检验棒插在主轴锥孔内,把千分表安装在机床固定部件上,使千分表测头垂直触及被测表面,旋转主轴,记录千分表的最大读数差值,在a、b 处分别测量。
标记检棒与主轴的圆周方向的相对位置,取下检棒,同向分别旋转检棒90 度、180 度、270 度后重新插入主轴锥孔,在每个位置分别检测。
车 床 几 何 精 度 检 验 实 验 报 告
车床几何精度检验实验报告(二)一. 目的 :1.了解车床精度标准、检验项目、检验方法及检具。
2.掌握车床各项精度对其加工精度的影响及原因。
3.掌握检测数据的处理方法及误差曲线绘制。
二. 要求:1.了解机床精度标准、熟悉检验方法及检具.2. 分析精度的影响因素。
3. 理解机床导轨直线度误差曲线绘制方法及误差计算。
三. 内容:1.机床导轨直线度误差曲线绘制方法及误差计算1)测量方法:床身导轨在垂直平面内的直线度:将框式水平仪纵向放置在溜板上靠近前导轨处a,从刀架靠近主轴箱右端位置开始,自左向右每隔200 mm测量一次,并记录读数,选择适当的比例,以导轨长度为横坐标,以水平读数刻度为纵坐标,作出导轨在垂直平面内的直线度曲线。
然后根据曲线计算出全长上的直线度误差和200mm 长度上的局部误差。
测量结果:2)导轨全长直线度误差:以曲线二端点OE的连接直线为基准,取曲线到基准直线纵坐标中最大的正值 (DF段)与最大的负值 (GA段)的绝对值之和,作为导轨全长的直线度误差,即直线度误差=DF×0.02/1000×200+GA×0.02/1000×200 =(DF+GA)×0.02/1000×200=[(8-7×4/5)+7×1/5]×0.02/1000 ×200=0.019mm图示导轨在垂直平面内的直线度曲线(横坐标导轨长度,纵坐标水平仪格数)3)局部直线度误差:取曲线上任意两点相对于基准直线OF的纵坐标值差的最大值为导轨的局部直线误差,即局部直线误差=(DF一CM)×0.02/1000×250=[(8—7×4/5)一(6—7×3/5)]×(0.02/1000)×250=0.6×(0.02/1000)×250=0.003 mm2.用图示表示其中三项精度检测方法及检测工具序号检验项目公差mm 测量结果mm 检测方法及检测工具(仪器)1 床身导轨在垂直平面内的直线度0.02(中凸) 0.019全长0.003/200mm工具:框式水平仪,百分表,塞尺2溜板移动在水平面内的直线度0.02工具:百分表、500毫米检验棒1根3 主轴与尾座两顶尖的等高度0.04(只许尾座高)工具:百分表、500毫米检验棒1根四分析影响上述三项精度的因素1.影响机床导轨导向误差的因素:1.床身导轨在垂直平面内的直线度:1)机床的制造误差2)机床的安装误差3)导轨磨损。
机床主轴回转精度实验报告
实验报告
实验名称:机床主轴的回转精度实验
班级:
姓名:
学号:
成绩:
湖南工业职业技术学院机械系数控中心
实验三:机床主轴的回转精度实验
一、实验目的:
1、掌握机床回转误差运动状态及对工件加工精度的影响;
2、了解车床主轴回转误差的测量方法。
二、实验器材:
1、C620车床一台,
2、圆柱心棒一根,
3、千分表三个。
实验方法:
4、按图示把心轴安装到车床主轴上;
2、按图示安装上千分表;分别离主轴前端50mm,100mm,200mm,400mm,600mm处测量各一次;
3、低速(150r/min)开动机床,记录跳动值和窜动值;
4、高速(630r/min)开动机床,记录跳动值和窜动值;
5、依下列方式计算出角向摆动:
tgα=(600mm处的跳动值-100mm处的跳动值)/(600-100),多算几处,取平均值。
数控铣床精度验证报告
数控铣床精度验证报告1. 引言本报告旨在对数控铣床的精度进行验证,并评估其与标准要求的符合程度。
精度验证对于确保数控铣床的正常运行和产品质量至关重要。
2. 实验目的本实验的目的是通过对数控铣床进行精度验证,评估其在尺寸、线形和位置方面的精度,以确定其与标准要求的符合程度。
通过验证结果,可以判断数控铣床是否满足生产需求,或者是否需要进行调整和校准。
3. 实验方法3.1 确定测量标准:根据相关标准和要求,选择合适的测量标准和仪器,并进行校准。
3.2 测量尺寸精度:选取多个代表性零件,在不同位置和角度上测量其尺寸,并与标准尺寸进行比较。
3.3 测量线形精度:使用光学仪器对刀具轨迹进行测量,比较其与理想轨迹的差异。
3.4 测量位置精度:通过测量加工后的零件相对于工装的位置,评估数控铣床的位置精度。
4. 实验结果4.1 尺寸精度验证结果:根据测量数据计算得出的尺寸偏差小于标准要求的允许误差范围。
4.2 线形精度验证结果:测量结果显示刀具轨迹与理想轨迹之间的差异小于标准要求的允许误差范围。
4.3 位置精度验证结果:测量结果显示加工后的零件相对于工装的位置偏差小于标准要求的允许误差范围。
5. 分析和讨论根据实验结果,数控铣床在尺寸、线形和位置方面的精度都满足标准要求。
因此,我们可以确认该数控铣床适用于当前的生产需求,无需进行调整和校准。
6. 结论本次数控铣床精度验证实验结果表明,该数控铣床在尺寸、线形和位置方面的精度均符合标准要求。
验证结果为生产提供了有效的保障,确保产品质量稳定。
7. 建议为了确保数控铣床始终保持良好的精度,建议定期进行精度验证和校准。
同时,操作人员应接受培训,熟悉数控铣床的操作规程,避免误操作对精度造成影响。
8. 参考文献[1] 相关标准和要求文献引用以上为数控铣床精度验证报告的内容和结论,供参考和记录使用。
- 1、下载文档前请自行甄别文档内容的完整性,平台不提供额外的编辑、内容补充、找答案等附加服务。
- 2、"仅部分预览"的文档,不可在线预览部分如存在完整性等问题,可反馈申请退款(可完整预览的文档不适用该条件!)。
- 3、如文档侵犯您的权益,请联系客服反馈,我们会尽快为您处理(人工客服工作时间:9:00-18:30)。
测量位置 0-200mm 200-400mm 400-600mm 600-800mm 800-
1000mm
水平读数
2. 主轴锥孔中心线的径向跳动
检验方法:此项检验是在 CA6140 型 车 床 上 进 行 , 将 300mm锥度检验棒插入主轴孔 中,用千分表分别在a,b处检验, 检验棒对主轴a处时点,允许 误 差 0.01mm,b 处 是 远 端 误 差 0.02mm.
反向间隙误差可能起因
► 用于弥补原有反向间隙而对机床进行的反向间补 偿的数值过大,导致原来具有正值反向间隙问题 的机床出现负值反向间隙。
► 机器可能受到编码器滞后现象的影响 ► 在机床的导轨中可能存在间隙,导致当机床在被
驱动换向时出现在运动中跳跃。
反向间隙对加工带来的影响
在机器上负值反向间隙的影响为圆弧插 补的刀具轨迹将出现一向内凹的跳跃。
△H △H L1
L
图1 水平仪测量升落差的原理图
► 如果我们在实验中,框式水平仪不是放在1米的平尺上, 而是放在200mm的平板上,那么△H为多少呢Tga=△H △H=200*Tga=0.004mm
► 水平仪读数的符号,习惯上规定:气泡移动方向和水平 移动方向相同时读数为正值,相反时为负值。
1. 溜板在垂直水平面的不直度
测量位置 a b
主轴锥孔中心线的径向跳动
1
2
允差
是否合格
6 主轴轴肩支撑面的跳动
检验方法:千分表吸持在导轨上,将表垂直打在主轴轴肩 端面靠外侧处,平动旋转主轴两周以上,千分表读数的最 大值为端面跳动误差。
最大跳动
表8 主轴轴肩支撑面的跳动
允差
0.02
是否合格
7 主轴定心轴颈的径向跳动
检验方法:千分表座吸 持在导轨上,将表头打 在主轴空心轴颈上,平 动旋转主轴两周以上, 千分表读数的最大差值 为径向跳动误差。
一、实验目的
► 熟悉机床运动精度检验的内容、原理、方 法和步骤
► 掌握仪器的使用,以及实验数据的处理, 误差曲线的分析。
二、实验设备和仪器
►设备: VMC1165B立式加工中心 ►仪器: KGM,VM双坐标光栅
三 、实验原理
KGM,VM双坐标光栅介绍: 海德汉公司(HEIDENAIN拥有 一百多年光刻制造技术的德国公 司。以生产高精度的产品而著名 ) KGM,VM系列双坐标光栅。可进行 两维高动态测量。它的测量基准 是固定刻划的两维光栅栅线,这 使得在采用KGM进行测量时,测 量结果不会因环境因素如空气湿 度、环境温度或气压的波动而受 到影响。采用海德汉KGM双坐标 测量设备可以通过圆周测试、自 由曲线测试对机床控制环的动态 性能进行分析。
► 采用框式水平仪进行检测,用水平仪测量导轨在垂直面 内的不平度时,将床身导轨按溜板或过桥长200mm。
► 划分成若干段,将水平仪放在溜板上,记下气泡的位置, 然后原地转180度看气泡是否在原处,如果不在原处, 把水平仪纵向放置在溜板或过桥上,一般总是把水平仪 在 起端位置时的读数为零,然后依次移动溜板,记下每 一位置的读数及符号,填入表格。
表9 主轴定心轴颈的径向跳动
允差
是否合格
五、思考题
►导轨的实际形状是怎样的?它对哪种零件产 生较大的影响?
►主轴锥孔径向跳动和轴向的窜动对零件的加 工有什么影响?
实验二、机床运动精度的测试
对高速机床而言,动态测试的结果更能说明 机床运动精度的水平。通过对动态测试结果进行 分析,不仅可以了解机床当前的状态,还可以获 得由数控系统、驱动和位置测量元件所组成控制 环的参数设置信息。通过静态测试,例如直线轴 的定位误差测试,则可以反映出机床的几何精度。
出现反向间隙处理方法
► 检查数控系统反向间隙补偿参数设置是否 正确;
► 检查机器是否受到编码器滞后现象的影响; ► 去除机器导轨的间隙,可能需要更换已磨
损的机器部件。
检验棒 百分表 磁性表座
三 、实验原理
机床几何精度测量
按 JB2314—78 普通机床规定,机床精度检 验包括机床导轨直线度、垂直度、平行度、 端面的平面度,机床部件之间直线度、垂直 度、平行度、同轴度,机床部件的运动精度, 主轴回转精度等18项。
四、 实验步骤与方法
► 框式水平仪的工作原理: 框式水平仪主要部分是一个弧形玻璃管,它的内壁磨成100米左右的 曲率半径。刻有刻度的玻璃管内充以少量乙醚液体,中间留一个气泡。 如图1所示。不论水平仪放在什么位置,玻璃管中的页面总是处于水 平,气泡总是向高处移动,读出气泡两端边缘,移动的格数,即可求 出相应的高度差。水平仪的刻度值为0.02/1000,它表示将该水平仪 放在1米长的平尺表面上,在平尺右端垫起0.02mm的高度,平尺便倾 斜一个a角,此时,水平仪正好移动一个刻度值。
机床精度检测实验
主讲教师 曲征洪
实验一、机床几何精度的检测
一、实验目的
► 熟悉机床几何精度检验的内容、原理、方 法和步骤
► 掌握仪器的使用,以及实验数据的处理, 误差曲线的绘制
► 了解被测量机床的几何精度状况以及它和 加工精度的关系
二、实验设备和仪器
►设备: MAZAK车床 ►仪器: 式水平仪机床误差分析►KGM可以快速找出并分析机床的问题在,主 要可检查反向差、反向间隙、伺服益、垂直 度、直线度、周期误差等等性能。
误差举例
► 反向间隙(负值,见图)。 图形中有沿某轴线开
始向图形中心内凹的台阶, 负值反向间隙的大小通常 不受机床进给率的影响。 在本图中仅在Y 轴上显示 有负值反向间隙图中Y 轴 正负方向均存在相同大小, 为-14.2μm的负值反向间 隙或失动量。