汽车动力传动系统参数优化匹配方法
汽车传动系参数的优化匹配

功率极限发挥率 . 反映了发动机输 出的最 大功率 丌 雠在驱动轮上 速器 传 动 比 的乘 积 。 得到发挥的极 限程度 , 其定义如式所示。优化时取 . 的最大值。 42 目标 函 数 的建 立 .
421汽 车动力系统 匹配程度评价指标 优 化的 目标 函数 采用 -. 驱动功率极 限发挥率 . m ,它反映了发动机输 出的最大功率 在
式 中 : n —— 发动机 转速 1 ( mi) 广 多项 式 中系数 ; O r, n; c 多项 式中阶数。 用最小二乘法拟合获得发动机外特性拟合 曲线。 33传动系效率的数学模型 发动机的净功率输出 , . 主要用于克服 离合器起步过程、 动力传递 的能量损失和行驶阻力, 均匀行驶时各种损 失, 因此在大多情况下 , 以采用经验公式进行估算:7 吼叼 可 = 式 中: im — 分 别 为 圆 柱齿 轮 、 ,, — 圆锥 齿 轮和 万 向 节 数量 : , , 一 分别为圆柱齿轮、 叼 圆锥齿轮和万 向节的传 动效率。
驱 动 轮 上 得 到 发 挥 的极 限程 度 。 422 约 束 条 件 .. 4221 变速 器 速 比 约 束 条件 ...
转 矩 尬 可 以 看 成 是 发 动 机 转 速 的 函 数 ,用 以 下 多 项 式 表 示 :
= ,
(= , , , , i0 1 2 … k)
i O =
的 传 动 比 可 以 无 级 变 化 ,则 阴 影部 分 可 以完 全 消 除。 但 对 于 机 械 变 34 汽 车 行驶 方程 式 . 速 器 而 言 , 变 速 器 只 有 汽 车 的行 驶 方 程式 为 : + = + 几 个 挡 位 , 以 , 影 区 所 阴 图 1 驱动特性曲线 4汽车动力传动系参数优化 匹配 不可能完全消 除, 但可 以通过选 择适 当的传动比 , 使阴影部 分的面积 41设计 变量 的确定 传动 系主要设计参数就是各挡传 动比, . 对 最 小 , 就 是 动 力传 动 系 的优 化 问题 。 这 传动 系而言 , 在其他条件相同的情况下 , 最终影响汽车动 力性及燃油 图 2反映不同速度下发动机传到汽车驱动轮上的极限功率。 驱动 经济性 的参数是传 动系的总传动 比,即变速器各挡的传动 比与主减
燃料电池汽车溷合动力系统参数匹配与优化
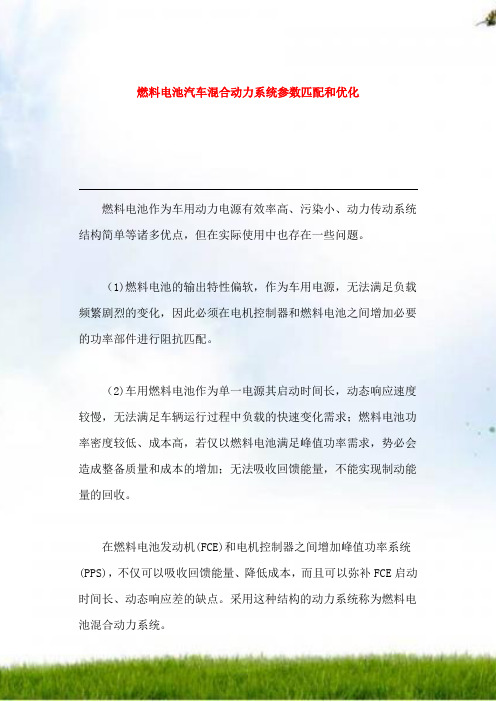
燃料电池汽车混合动力系统参数匹配和优化燃料电池作为车用动力电源有效率高、污染小、动力传动系统结构简单等诸多优点,但在实际使用中也存在一些问题。
(1)燃料电池的输出特性偏软,作为车用电源,无法满足负载频繁剧烈的变化,因此必须在电机控制器和燃料电池之间增加必要的功率部件进行阻抗匹配。
(2)车用燃料电池作为单一电源其启动时间长,动态响应速度较慢,无法满足车辆运行过程中负载的快速变化需求;燃料电池功率密度较低、成本高,若仅以燃料电池满足峰值功率需求,势必会造成整备质量和成本的增加;无法吸收回馈能量,不能实现制动能量的回收。
在燃料电池发动机(FCE)和电机控制器之间增加峰值功率系统(PPS),不仅可以吸收回馈能量、降低成本,而且可以弥补FCE启动时间长、动态响应差的缺点。
采用这种结构的动力系统称为燃料电池混合动力系统。
“燃料电池+动力蓄电池”是目前研发的燃料电池混合动力系统主要构型,主要有如图1所示4种结构。
结构(a)、(b)和(c)中,燃料电池和驱动系统都是间接连接,可以在一些特定条件下的场地车上使用,但受目前燃料电池技术水平的限制,这3种动力系统结构难以在功率需求和功率波动都比较大的车型上实现。
结构(d)的优点是:蓄电池可回收再生制动的能量和吸收燃料电池富裕的能量;蓄电池组作为燃料电池发动机的输出功率平衡器,调节燃料电池发动机的效率和动态特性,改善整车燃料经济性,提高动态响应速度。
图1 燃料电池混合动力系统结构对于本文所研究的燃料电池汽车,其车型的整车参数及动力性指标如表1所示。
表1 整车参数和设计性能要求2 燃料电池混合动力系统参数匹配2.1 电机参数设计目前,可用作车用驱动电机的有直流电机、交流感应电机、永磁同步电机、直流无刷电机、开关磁阻电机等。
交流异步电机由于结构简单、坚固且控制性能好,被欧美国家广泛采用。
永磁同步电机和直流无刷电机能量密度和效率较高,在日本得到广泛使用。
开关磁阻电机使用较少。
矿用汽车动力传动系统参数匹配建模优化

矿用汽车动力传动系统参数匹配建模优化张鹏;马海英;侯晓晓【摘要】在对公路汽车动力性与燃油经济性评价指标进行分析基础上,以Matlab/GUI为开发工具,开发矿用汽车动力传动系统计算仿真及参数优化平台.该平台以原地起步加速时间和等速百公里油耗线性加权为目标函数,采用线性加权法把他转化成单一目标函数;建立矿用汽车发动机和传动系统匹配方案优化数学模型.对矿用汽车动力性和燃油经济性进行计算,对传动系统匹配方案和传动系参数进行优化分析.以改进前后某车各项性能指标进行仿真,验证改进方案可行性,对改进后传动系参数进行优化,验证优化平台实用性.通过遗传算法优化模型分析,最后对具有可控性总速比和传动效率进行灵敏度分析,为新车设计和旧车改型提供参考.【期刊名称】《机械设计与制造》【年(卷),期】2019(000)006【总页数】5页(P60-64)【关键词】矿用汽车;动力性;燃油经济性;参数优化平台;动力系统【作者】张鹏;马海英;侯晓晓【作者单位】黄河交通学院汽车工程学院,河南焦作 454950;黄河交通学院汽车工程学院,河南焦作 454950;黄河交通学院汽车工程学院,河南焦作 454950【正文语种】中文【中图分类】TH16;U463.2121 引言矿用汽车动力传动系统匹配合理程度,在很大程度上决定该车动力性、燃油经济性。
为改善矿用汽车动力性和燃油经济性,对动力传动系统进行合理匹配是一个重要途径[1]。
搭建合理高效参数优化平台,即可实现对矿用汽车动力性和燃油经济性进行仿真计算,还可实现对系统匹配方案和参数进行优化,可便捷高效实现对系统参数优化。
文献[2]搭建动力传递数学模型,对功率和燃油最优时运行状况进行分析;文献[3]搭建动力传递系统模型,研究参数影响;文献[4]根据发动机最佳经济性工作区间与常用工作区间之间相对位置,对最佳工作位置进行优化;文献[5]基于实际档位与动力系统油门控制之间关系进行优化。
以Matlab/GUI为开发工具,开发矿用汽车动力传动系统计算仿真及参数优化平台。
NJ1042轻型货车发动机与传动系参数优化匹配

l 1
≥ … ≥ 止
l
(- 2 9)
为 了防止轻型货车加速过程 中出现动力传递中断 ,应保证当前梢 发动机的最高转速 n 对应的最大车速 U 一 i 一高于换人下一 档时发动机 最大转矩 点转速 I 对应 的车速 U 即: 1 T ,
一
≤ 唑 d l , ‘ — ) =,・, 1 2 ‘n
nT
( — 0 2 1)
1目 十1
23N 14 . J0 2基本参数及优化结果 汽车总质量 m= 4 0 g 4 5 k ,轮胎滚动半径 R = . 6 03 m,空气阻力系数 5 Cm . 汽车 迎 风 面积 A 34m 传 动 阻力 系 数 f002, 油 密 度 f06 4, = .4 , = .1 燃 p 07 2 g ( = .2  ̄/ 汽油 )变速器各挡速 比: c ,
1 ——预期最高车速 1 满足最大爬坡度要求 , 则有:
i ≥j
i
…
— —
( —5) 2
预期最 大爬坡度
(— 2 6)
满足加速时 间要求 , 则有:
t ≤t
t 预期加速 时间 对 于轻型货车 , 直接 挡最大动力 因数一 般为 00—0O , .5 .8 因此满足 直接挡最 大动力 因数要求 , 则有:
和燃 油经济性 。 本文以 N 14 轻型货车为研 究对象, 用数学模型和优化方法 , J0 实例验证 了在 动力性 下降很 小的条件下 , 通过 匹配优 化轻型货车的动 力系统可 以改善轻型货车的燃油经济性 。 [ 关键词 ] 传动 系 优化 发动机 动力性
1 引言 .
满足最高车速要求 , 则有:
U ≥u (— ) 2 4
在对轻 型货 车的动力系统进行 匹配优 化设计 过程中 ,当发动机和 传 动系参数确定后 , 需要对整车 的使用性 能进行 评价 , 以判断发动机与 传动系统匹配是 否合理 ; 为优化 动力系统以获得更好的综合性能提 也 供依据 , 价的合 理与否直接影 响到优 化决策。汽车的动力性 、 评 燃油经 济性 和排放性是 汽车整 车性能评价 中最重要 、 最基本的组成部分 。 根据发动机原理和汽车理论 ,汽车动力性 和燃 料经济性指标是相 互 矛盾 的, 因为动力性好 , 别是加速性和爬坡 性好 , 特 一般要求 汽车稳 定 行驶 的后备功率大 ; 但对 于燃料经济性来说 , 必然 降低发动机的负荷 率 , 而使燃料经济性变差 。从汽车使用要求来看 , 从 既不可脱离动力性 来 孤立地追求燃料经济性 , 也不能脱离经济性来 孤立 地追求动力性 , 最 佳的设计方案是 汽车 的动力性与燃料经济性之间取得最佳折衷 。 汽车动力性燃料经济性 的综合评价指标 , 该能定 量的反映汽车 应 动 力传动 系统 的匹配程度 ,能够反 映出发 动机动 力性与燃料经济性的 发挥程度 以及汽 车实 际行驶工况所对应 的发动机 工况与其理想工况的 差异。为此 , 本文 以能量效率作为汽车动力性和燃 油经济性综合评价指 标。 2N 14 . J 0 2轻 型 货 车 传 动 系 的 优 化 匹 配 21目标 函数 的建立 . 目 函数是使设计得 以优化 的函数 ,可以用来评价设计方案 的好 标 坏, 建立 目标 函数是整个优化设计过程中的重要 问题。 轻 型货车动力系统 匹配优化 的 目的是使 轻型货 车在保证动力性的 前 提下 , 常用行驶工况下燃 油经济性最佳 , 能满足排放性 的要 求 , 在 并 因此 , 这是一个多 目标优化 问题 。轻型货 车的动力 性 、 油经济性和排 燃 放性指标 既相互联系又相互矛盾 , 建立 目 函数 时 , 标 不能单独考虑动力 性 指标 、 燃油经济性指标或排放性指标 , 实际优 化过程中也很难达到 在 各 单 目 的最优解 。 标 一般通过构造评价函数 , 将这样 的多 目 标优化 问题 转化 为单 目标优化问题 ,然后利用单 目标优化 问题 的求 解方法求m最 优解 , 并把这种最优解 当作多 目标优化问题的最优解l 1 l 。 本文 以轻 型货车 的燃油经济作 为 目 函数 ,采用加权组合法构造 标 评 价函数 , 通过在燃油经济性评价指标 和排 放性评 价指标 中引入加权 因子 , 考虑这 两个分 目 标在综合评价指标 中相对重要程 度方 面的差 异。 由此建立轻型货车动力系统匹配优化设 计的 目标 函数 为:
关于纯电动汽车动力传动系统匹配与整体优化

关于纯电动汽车动力传动系统匹配与整体优化摘要:发展新能源汽车成为未来汽车行业的主要趋势,纯电动汽车已经成为社会关注的重点问题。
但是当前纯电动汽车在关键技术等方面还是存在不足,主要集中在续航和充电等两个方面,而如何处理好纯电动汽车动力传动系统匹配,做好系统参数的设置,使汽车在规定电量当中最大限度地提升动力性,保障有效的续航里程成为主要目标。
解决纯电动汽车动力传动系统参数匹配与整体优化具有现实意义。
关键词:纯电动汽车;动力传动系统匹配;整体优化我国汽车尾气排放严重,能源消耗不断地加快,导致传统汽车节能环保问题突出。
而纯电动汽车在结构上更为简单,能源选择多样,与传统汽车相比不会产生加大的噪声,能够更好地控制尾气的排放,逐渐的受到了不同汽车企业的关注,加大了对纯电动汽车的研发力度。
1纯电动汽车结构原理动力系统、电气设备等共同构建成为纯电动汽车的基本结构,并且与内燃机在结构上进行比较,两者最大的差异主要集中在动力系统上,特别是纯动力汽车主要有电力驱动系统、电源管理系统以及辅助系统。
在电力驱动系统运行当中将电池化学能之间的转换为汽车动能,同时还能够在汽车减速等状态下降动能转换为电能直接的存储到电池当中。
功率转换器、机械传动系统、电子控制器等共同构建成为电力驱动系统,对于纯电动汽车整体动力与经济状况等有着直接的影响。
电源系统能够为汽车的行驶提供驱动能源,主要有能量管理系统、充电装置、蓄电池等。
并且能够检测电池的运行状态,开展及时的充电管理。
纯电动汽车辅助功能主要有照明系统、空调系统等。
同时还具有辅助动力源,能够为空调系统等提供及时的电源。
2纯电动汽车动力系统参数匹配设计2.1电机参数设计对于驱动电机纯电动汽车有着较高的要求,与传统电机相比在技术规范上更为严格,这是由于驱动电机关系到汽车的频繁起动和停车的过程有效性,将会承受较大的制动力,特别是纯电动汽车在电机使用上要凸显出瞬时功率、过载能力等特点,需要拥有较为突出的加速性能,要保障其使用寿命较长。
纯电动客车动力传动系参数匹配及整车性能研究
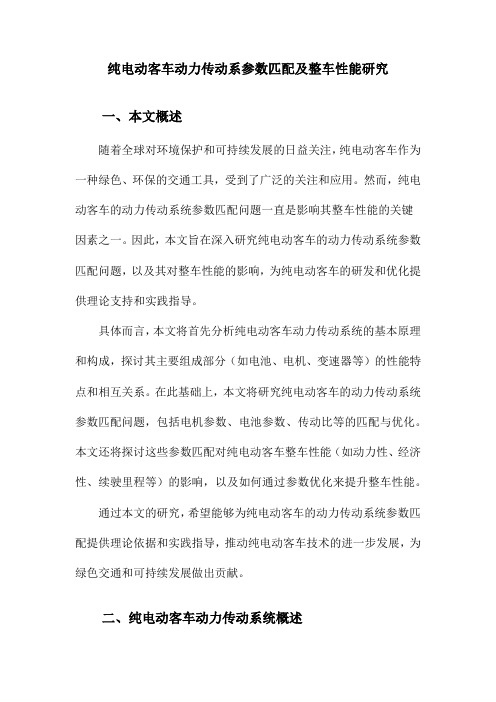
纯电动客车动力传动系参数匹配及整车性能研究一、本文概述随着全球对环境保护和可持续发展的日益关注,纯电动客车作为一种绿色、环保的交通工具,受到了广泛的关注和应用。
然而,纯电动客车的动力传动系统参数匹配问题一直是影响其整车性能的关键因素之一。
因此,本文旨在深入研究纯电动客车的动力传动系统参数匹配问题,以及其对整车性能的影响,为纯电动客车的研发和优化提供理论支持和实践指导。
具体而言,本文将首先分析纯电动客车动力传动系统的基本原理和构成,探讨其主要组成部分(如电池、电机、变速器等)的性能特点和相互关系。
在此基础上,本文将研究纯电动客车的动力传动系统参数匹配问题,包括电机参数、电池参数、传动比等的匹配与优化。
本文还将探讨这些参数匹配对纯电动客车整车性能(如动力性、经济性、续驶里程等)的影响,以及如何通过参数优化来提升整车性能。
通过本文的研究,希望能够为纯电动客车的动力传动系统参数匹配提供理论依据和实践指导,推动纯电动客车技术的进一步发展,为绿色交通和可持续发展做出贡献。
二、纯电动客车动力传动系统概述纯电动客车作为新能源汽车的重要组成部分,其动力传动系统的设计与优化对于提升整车性能具有至关重要的作用。
纯电动客车的动力传动系统主要由电池组、电机、控制器以及传动机构等核心部件构成。
这些部件的协同工作,使得纯电动客车能够实现高效、环保的行驶。
电池组是纯电动客车的“心脏”,它为整车提供所需的电能。
电池组的性能直接影响到车辆的续航里程、加速性能以及能量利用率等关键指标。
因此,在动力传动系统参数匹配过程中,需要充分考虑电池组的能量密度、充放电速率以及循环寿命等特性。
电机作为动力输出装置,负责将电能转化为机械能,驱动车辆行驶。
电机的选择需要考虑其功率、扭矩以及效率等因素,以确保纯电动客车在不同工况下都能够提供足够的动力。
同时,电机的控制策略也是动力传动系统中的重要环节,它直接影响到车辆的驾驶性能和能量消耗。
控制器是纯电动客车的“大脑”,它负责协调电池组、电机以及传动机构等部件的工作。
汽车传动系参数的优化匹配研究(精)

汽车传动系参数的优化匹配研究课题分析:汽车的动力性、燃油经济性和排放特性是汽车的重要性能。
如何在保证汽车具有良好动力性的同时尽量降低汽车的油耗并获得良好的排放特性,是汽车界需要解决的重大问题。
传动系参数的优化匹配设计是解决该问题的主要措施之一。
汽车传动系参数的优化匹配设计是在汽车总质量、质量的轴荷分配、空阻及滚阻等量已确定的情况下,合理地设计和选择传动系参数,从而大幅提高匹配后汽车的动力性、燃油经济性和排放特性。
以往传动系统参数设计依靠大量的实验和反复测试完成,耗时长,费用高,计算机的广泛应用和新的计算方法的出现,使得以计算机模拟计算为基础的传动系设计可在新车的设计阶段就较准确地预测汽车的动力性、经济性和排放特性,经济且迅速。
目前国内围绕汽车传动系参数的设计和优化,主要在以下几个方面展开工作:①汽车传动系参数优化匹配设计评价指标的研究;②汽车传动系各部分数学模型的研究,特别是传动系各部分在非稳定工况下模型的研究;③按给定工况模式的模拟研究;④按实际路况随机模拟的研究;⑤传动系参数优化模型的研究;⑥模拟程序的开发和研究。
检索结果:所属学科:车辆工程中文关键字:汽车传动系参数匹配优化英文关键字:Power train;Optimization;Transmission system; Parameter matching;使用数据库:维普;中国期刊网;万方;Engineering village;ASME Digital Library文摘:维普:检索条件: ((题名或关键词=汽车传动系)*(题名或关键词=参数))*(题名或关键词=优化)*全部期刊*年=1989-2008汽车传动系统参数优化设计1/1【题名】汽车传动系统参数优化设计【作者】赵卫兵王俊昌【机构】安阳工学院,安阳455000【刊名】机械设计与制造.2007(6).-11-13【文摘】主要研究将优化理论引入到汽车传动系参数设计中,以实现汽车的发动机与传动系的最佳匹配,达到充分发挥汽车整体性能的目的。
纯电动汽车传动系统参数匹配及优化

4、跨领域合作:加强汽车、电子、电力等多个领域的合作与交流,共同推动 纯电动汽车传动系统参数匹配及优化的技术创新和发展。通过跨领域合作,可 以充分利用各领域的优势资源和技术成果,实现传动系统性能的全面提升。
参考内容二
随着环保意识的不断提高和电动汽车技术的不断发展,纯电动汽车成为了现代 交通工具的重要选择。而传动系统作为纯电动汽车的关键部分,其性能和效率 直接影响到整个车辆的性能和续航里程。因此,对纯电动汽车传动系统参数进 行优化,可以提高车辆的动力学性能和能源利用效率。本次演示将开展纯电动 汽车传动系统参数优化的仿真研究。
总之,本次演示通过对纯电动汽车传动系统参数优化的仿真研究,找出了最优 的参数组合并分析了其对车辆性能的影响。这一研究对于提高纯电动汽车的动 力学性能和能源利用效率具有重要意义,并为未来纯电动汽车的发展提供了有 益参考。
参考内容三
随着全球对环保和可持续发展的日益,电动汽车(EV)作为一种零排放、低噪 音、高效率的交通工具,在近年来得到了快速发展。其中,纯电动汽车(BEV) 由于其完全依赖电力驱动,具有更高的能源利用效率和环保性能。然而,要实 现纯电动汽车的广泛应用,仍需解决诸多技术难题,其中包括动力传动系统的 匹配与整体优化。本次演示将就这一主题进行深入探讨。
对于未来展望,本次演示认为,纯电动汽车传动系统参数优化的仿真研究仍有 很多工作需要做。首先,需要进一步深入研究不同参数组合下的传动系统性能 表现,以找到更为优秀的参数组合。其次,需要新型材料和制造工艺在纯电动 汽车传动系统中的应用,探讨其对于提高传动系统性能和效率的影响。此外, 还需要考虑不同驾驶工况和路况下的传动系统性能表现,以进一步提高仿真研 究的现实意义。
- 1、下载文档前请自行甄别文档内容的完整性,平台不提供额外的编辑、内容补充、找答案等附加服务。
- 2、"仅部分预览"的文档,不可在线预览部分如存在完整性等问题,可反馈申请退款(可完整预览的文档不适用该条件!)。
- 3、如文档侵犯您的权益,请联系客服反馈,我们会尽快为您处理(人工客服工作时间:9:00-18:30)。
1机械传动汽车动力传动系统参数的优化通常包括发动机性能指标的优选,机械变速器传动比的优化和驱动桥速比的优化,以下分别阐述。
7.1汽车发动机性能指标的优选方法 在汽车设计中,发动机的初选通常有两种方法:一种是从保持预期的最高车速初步选择发动机应有功率来选择的,发动机功率应大体上等于且不小于以最高车速行驶时行驶阻力功率之和;一种是根据现有的汽车统计数据初步估计汽车比功率来确定发动机应有的功率。
在初步选定发动机功率之后,还需要进一步分析计算汽车动力性和燃料经济性,最终确定发动机性能指标(如发动机最大转矩,最大转矩点转速等)。
通常在给定汽车底盘参数、整车性能要求(如最大爬坡度max i ,最高车速m ax V ,正常行驶车速下百公里油耗Q ,原地起步加速时间t 等),以及车辆经常运行工况条件下,就可以选择发动机的最大转矩T emax ,及其转矩n M ,最大功率max e P 及其转速P n ,发动机最低油耗率min e g 和发动机排量h V 。
在优选发动机时常常遇到两种情况:一种情况是有几个类型的发动机可供选择,在整车底盘参数和车辆经常行驶工况条件确定时,这属于车辆动力传动系合理匹配问题,可用汽车动力传动系统最优匹配评价指标来处理。
第二种情况是根据整车性能要求和汽车经常行驶工况条件来对发动机性能提出要求,作为发动机选型或设计的依据,而这时发动机性能是未知的。
对于计划研制或未知性能特性指标的发动机性能可看作为发动机设计参数和运行参数的函数,此时,外特性和单位小时燃油消耗率可利用表示发动机的简化模型。
优选汽车发动机参数的方法: (1) 目标函数F (x )目标函数为汽车行驶的能量效率最高。
(2) 设计变量X],,,,[max h M p e em V n n P T X(3) 约束条件1) 发动机性能指标的要求 发动机转矩适应性要求:3.1/1.1≤≤P em T T转矩适应性系数也可参考同级发动机试验值选取。
发动机转速适应性要求:0.2/4.1≤≤M p n n如果M n 取值过高,使4.1/<M p n n ,则可能使直接档稳定车速偏高,汽车低速行驶稳定性变差,换档次数增多。
2) 汽车动力性要求 最大爬坡度要求:tg k eM i i f Gr T ηαα01max max )sin cos (+⋅≥最高车速要求:1.1~0.1/max =p a V V ,即 1.1377.00.10max ≤≤kp a r n i i V 高档直接档动力性要求:max 2015.21o a D k t em D G AV C G r i T ≥-η 汽车加速性能的要求:原地起步连续换档加速时间不得大于要求值0t0t t ≤3) 汽车燃料经济性要求:直接档在常用车速下行驶的百公里油耗不得超过其限制值0Q0Q Q s ≤发动机排量的要求:h h e P V P P ≤</max 13式中,h P 、1P ——分别为发动机升功率的统计上、下限值,kW/L 。
根据上述建立的优化模型,即可优选出最优发动机参数,并选择发动机型号。
发动机简化模型发动机性能特性可看作是发动机性能指标和运行参数的函数,此时,外特性可表示为:22)()(e m m p p m m e n n n n T T T T -⋅---=式中,m T ——发动机最大有效转矩,N ·m ;p T ——发动机最大功率对应的转矩,N ·m ;m n ——发动机最大有效转矩对应的转速,r/minp n ——发动机最大功率对应的转速,r/min 。
发动机单位时间的油耗量可以表示为:h e o ox e t V T r G n G ⋅⋅+⋅=)(式中,t G ——发动机每分钟消耗的燃油量,g/min ;ox G ——发动机怠速时单位排量每转燃油消耗量,g/(r ·L);o r ——发动机单位排量单位转矩每转燃油消耗量提高系数g/( N ·m ·r ·L);h V ——发动机的排量,L 。
根据研究,汽油机和柴油机的的ox G 和o r 值范围如下表所示。
汽油机和柴油机的的ox G 和o r 值7.2汽车变速器速比的优化方法汽车传动系参数优化是以汽车动力性与燃料经济性模拟计算为基础,以汽车动力性要求为约束条件,多工况燃料经济性为目标函数进行优化。
汽车变速器速比优化最终目的是使汽车在满足动力性要求前提下,在常用行驶工况下燃料经济性最佳。
设计变量取变速器各档速比,表示为x (i ),i=1,k n (k n 为前进档位数)。
目标函数一般为汽车多工况循环模式的燃油消耗量Qs 。
约束条件主要包括:汽车的动力性要求和变速器各档速比间隔的要求。
在选择传动系参数时,应考虑汽车具有足够的动力性能,即应有足够的直接档动力因数D omax 和I 档最大动力因数D imax ,同时需校核I 档最大驱动力时附着条件。
式中, T em ——发动机最大有效转矩,N.m ηt ——传动系效率 r k ——车轮滚动半径,m C D ——汽车空气阻力系数 A ——汽车前迎风面积,m 2n em ——发动机最大转矩点所对应的转速,rpm; G ——汽车总重力,N 。
则直接档最大动力因数的约束条件应为D ol <D omax <=D oh式中,Dol,Doh ——分别为不同车型汽车直接档最大动力因数要求的上下限。
I 档最大动力因数反映了汽车最大爬坡能力,其计算式如下:Mg I I r n A C r I I T D kem D k t em ax⋅⎪⎪⎭⎫⎝⎛⋅⋅⋅⨯⋅-⋅⋅⋅=21010Im 377.015.21η同上,I 档最大动力因数的约束条件为h L D D D 1max 11<<GI r n A C r I T D k em D k t em 20max 0)377.0(15.21⋅⋅⨯⋅-⋅⋅=η5式中 D 1L ,D 1h ——分别为不同车型汽车I 档最大动力因数要求的上下限值。
在确定I 档动力因数后还应该按以下条件校核附着条件,即最大牵引力必须小于或等于汽车在地面上的附着力:ϕηϕ⋅≤⋅⋅⋅Z R I I T ktem 10式中 ϕ ——道路附着系数;ϕZ ——驱动轮上的法向反作用力,N 。
同样也可以汽车最大爬坡度要求代替动力因数作为约束条件。
变速器相邻档位的速比比值影响着变速器的使用性能,比值过大会造成换档困难。
根据统计,一般在1.4~1.8之间。
考虑到换档过程,外界道路阻力总是造成车速下降,换档时车速越高,换档过程的速度下降就越多,所以随着档位的提高,相邻两档的速比比值应逐渐降低。
据此对相邻档位的速比比值要求如下:h l I X i L X i I <+<)()( )1()()2()1(+<++i X i X i X i X式中,h l I I ,——分别为相邻速比间隔的下限和上限值。
此外,汽车最高车速,汽车原地起步连续换档加速时间限制也作为约束条件。
以上构成了汽车变速器速比的一般优化模型。
7.3汽车主传动比优化方法汽车主传动比对汽车动力性燃料经济性影响很大。
主减速比增大,可以增加汽车的后备功率,提高汽车加速性能,但也会使汽车燃料经济性下降。
因此,主传动比的选择,应保证汽车的动力够用,又有最佳的燃料经济性。
对于某一特定的车辆,当汽车总重、重量分配和发动机等已确定后,如何合理的选择传动系参数,按传统的做法,需要进行大量的汽车动力性和燃料经济性计算和实验工作,而且由于各种条件限制,往往不能获得最理想的结果。
汽车主传动比的优化最终目的是使汽车在满足动力性要求下,在常用行驶工况燃料经济性最佳。
在选择传动系参数要求时,应考虑汽车具有足够的动力性能,即应有足够的直接档动力因数D 0max 。
直接档动力因数表示汽车在正常情况下行驶所具有的上坡和加速能力。
GI r n A C r i T D keM D kt o eM 20max 0)377.0(15.21⨯-=η 汽车最高设计车速,原地起步连续换档加速时间和最大爬坡度要求也作为约束条件。
7.4汽车传动系统参数的区间优化方法如前所述,传动系参数中齿轮齿数和模数为离散变量,而采用以上优化方法获得的速比值是一个确定的最优值,不一定满足生产厂家的实际生产需要,存在着变速器齿轮配齿的问题。
为此我们提出了汽车传动系参数的区间优化模型。
在这一模型里,不追求变量的确定优化值,只是在保证一定的优化效果的前提下,求设计变量的最大可行区间,这样就可以扩大传动系参数的选择范围,并可以解决变速器齿轮配齿问题。
用区间数表示需要共享的实际变量,则确定汽车传动系参数最大可行区间的问题可以表述为扩大设计变量区间数的宽度问题。
令Xi 为共享设计变量,则求最大共享区间问题的数学模型,即是求最大可行区间问题的数学模型,即是求最大可行区间宽度的优化问题。
在一定的约束条件下,其数学模型为:∑==li i i i X 1)(max ωαω满足约束条件c X X X F l ≤)(21,,,Λ'i i X X ⊆l i ,,,Λ21= 其中,)(ΛF 为约束区间函数,c 为约束区间函数的限制值,i α为权系数,l 为区间变量总数,)(i i X ω为第i 个区间数的区间宽度,'i X 可行区间变量i X 的约束区间数,],['''i i i X X X =。
上述模型描述的是区间扩张的逆问题,及规定函数的值域区间求定义域区间7的问题,在约束函数为凸函数时,有确定的解。
求解上述模型得到的可行区间宽度有时较窄,为了改善效果,引入“条件预优概念及方法”,也就是把影响实值函数),,,,,,(121n l l x x x x x F ΛΛ+的变量及参数分为两类,其中l x x x ,,,21Λ为一类,叫做关键变量,我们关心这些变量的可行变化区间],[i i X X ,而不关心它们取什么确定值;此外,我们把影响目标函数值的其他变量及参数在一定的范围内变动,这些扩大的变量称作为条件变量。
我们采用对条件变量优选的方法,即求n l l x x x ,,,21Λ++使),,,,,,(m in 121n l l x x x x x F ΛΛ+求解模型时,对应于每一组T l x x x z ],,,[21Λ=时,有一组对应的最优变量T n l l x x x y ],,,[*21*+*+*=Λ,我们把*y 称为预优条件变量,把这一类运算成为“条件预优运算”。
通过条件预优运算,能明显地提高与改善优化效果,即),,,,,,(),,,,,,(121**121n l l n l l x x x x x F x x x x x F ΛΛΛΛ++≤若我们把上述预优概念引入模型 ,那末就可以扩大关键变量允许选取的范围,改善最大可行区间的求解效果。