控制连铸板坯星状裂纹的对策
连铸坯表面裂纹形成及防止分析

浸入式水口对中,防止偏流 合理的浸入式水口设计(合适的出口直径,倾角) 合适的水口插入深度 合适的频率和振幅
(3) 结晶器振动
2 铸坯表面纵裂纹
(4) 出结晶器铸坯运行 二次冷却均匀性 (5) 调整钢水成分 钢中碳含量避开包晶区,C向下线或上线控制 钢中S<0.015% 残余元素Cu、As、Zn控制<0.1%
图2-4 拉速对纵裂纹的影响
2 铸坯表面纵裂纹
(3) 保护渣 液渣层厚度<10mm,纵裂纹增加(图2-5)。
图2-5 液渣层厚度对纵裂纹的影响
2 铸坯表面纵裂纹
(4) 结晶器液面波动 液面波动<±5mm,纵裂纹最少(图2-6);
图2-6 结晶器液面波动对纵裂纹的影响
2W (T1 T2 ) W
连铸坯表面裂纹 形成及防止
宋晔
内容
1 2 3 4 5 前言 铸坯表面纵裂纹 铸坯表面横裂纹 铸坯表面星形裂纹 结论
1.前言
连铸坯质量概念: ◆ 铸坯洁净度(夹杂物数量、类型、尺寸、 分布) ◆ 铸坯表面质量(表面裂纹、夹渣、气孔) ◆ 铸坯内部质量(内部裂纹、夹杂物,中 心疏松、缩孔、偏析) ◆ 铸坯形状缺陷(鼓肚、脱方)
2 铸坯表面纵裂纹
2.3 影响表面纵裂纹产生的因素
(1) 钢水成分
◆ [S]>0.015%,纵裂纹增加(图2-2);
◆ [C]=0.12~0.15%,纵裂纹产生严重(图2-3)
图2-2 钢中[S]与裂纹指数的关系
2 铸坯表面纵裂纹
பைடு நூலகம்
图2-3 含碳量对板坯宽面纵裂纹的影响
2 铸坯表面纵裂纹
(2) 拉速 拉速增加,纵裂纹指数增加(图2-4);
板坯中心裂纹的成因与对策
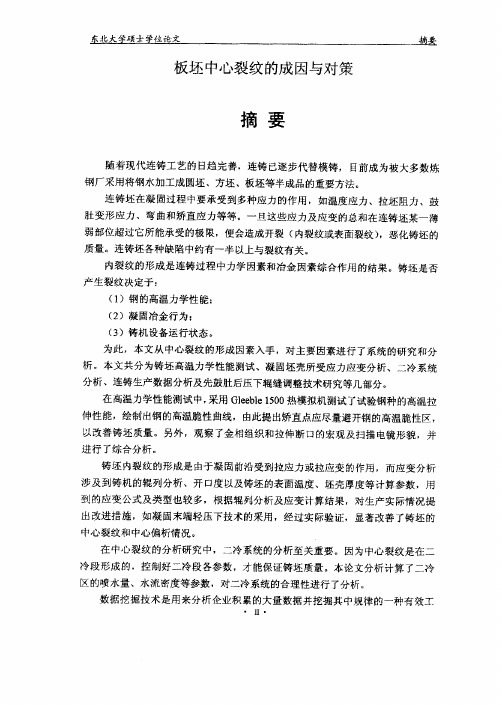
在中心裂纹的分析研究中,二冷系统的分析至关重要。因为中心裂纹是在二 冷段形成的,控制好二冷段各参数,才能保证铸坯质量。本论文分析计算了二冷 区的喷水量、水流密度等参数,对二冷系统的合理性进行了分析。 数据挖掘技术是用来分析企业积累的大量数据并挖掘其中规律的一种有效工
I ・ I
I . V
t pru ad lh kesA crn tt rls l iad cli ru s e e t e s l ns co i o oe aa s n cl ao e l m a r n h tc . d g h lr n y s a u t n t e i e s o se , r i m as pt a ad i t b p cc. r m l sf f s ip v g n a uf wr n vla d r te o ea p , t sm on e r r e o d ad e y i F x e o r a t r utn nl y be aot tip v t st o cuao ad t n e co t ho g hs n p d m r e tu f si n sli d i e o a e d e o o h a s a tn o o c e u
() a o f d i i ; i o sl ict n 2 B hv r oi f ao e
( R ni stoeu m n g e qi et 3 un t f p . ) n a T e fr i t s ie as o o ao i o bn t nl e cn r , h atl cue f m t n cm i d aa z te t hr oe n rc , e i f i s r e o y h e e
ic ssii a tn a pro sb c cs lap rs qato sb t ua n ea w k t l s r k w u pe , ul f s a tn cri e a f , n a a o d a o i y l a
连铸坯内部裂纹产生的主要原因及解决措施
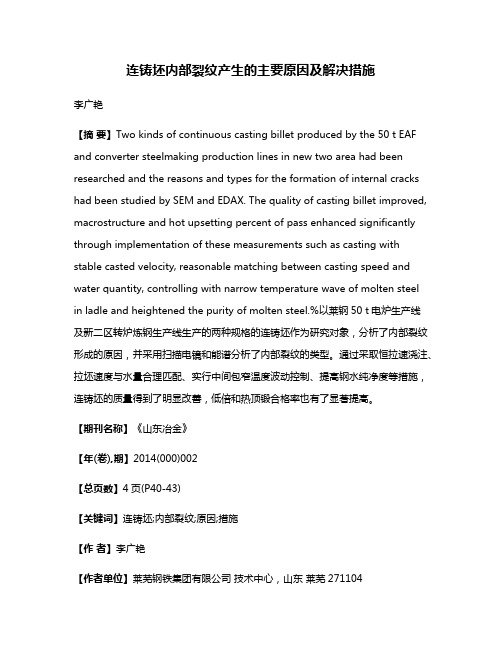
连铸坯内部裂纹产生的主要原因及解决措施李广艳【摘要】Two kinds of continuous casting billet produced by the 50 t EAF and converter steelmaking production lines in new two area had been researched and the reasons and types for the formation of internal cracks had been studied by SEM and EDAX. The quality of casting billet improved, macrostructure and hot upsetting percent of pass enhanced significantly through implementation of these measurements such as casting with stable casted velocity, reasonable matching between casting speed and water quantity, controlling with narrow temperature wave of molten steelin ladle and heightened the purity of molten steel.%以莱钢50 t电炉生产线及新二区转炉炼钢生产线生产的两种规格的连铸坯作为研究对象,分析了内部裂纹形成的原因,并采用扫描电镜和能谱分析了内部裂纹的类型。
通过采取恒拉速浇注、拉坯速度与水量合理匹配、实行中间包窄温度波动控制、提高钢水纯净度等措施,连铸坯的质量得到了明显改善,低倍和热顶锻合格率也有了显著提高。
【期刊名称】《山东冶金》【年(卷),期】2014(000)002【总页数】4页(P40-43)【关键词】连铸坯;内部裂纹;原因;措施【作者】李广艳【作者单位】莱芜钢铁集团有限公司技术中心,山东莱芜271104【正文语种】中文【中图分类】TG115.21 前言铸坯裂纹的形成是一个非常复杂的过程,是传热、传质和应力相互作用的结果。
连铸板坯表面星状裂纹的形成与控制

浇注断面: 1 m ( 0 1 0 m ; 20 x 5一 3 ) m 6 5 m 结晶 器长度: 5 m 8m ; 0 中间包容量: 0; 4t 铸机半径: 00m ; 1 0m 5 冶金长度: 96. m ; 288 6 m 3
振动参数:振幅 t 5 m,频率 5 一 5smn 37m . 0 1 / i,负滑脱率 3 .% 6 95 o
Cr c o Co t u u Ca t a a k f n i o s s S b n l Dn Zin i hog g l
g n i k - l e t S ( P noM ia In SeC. l t a6n ad l ) a f s r n t o o e
A s}t s o t p cc oC p dco aMin, h ppr aa s t b a B e n r te C utn eag Te eh nle h h c a d h ai f r i t e o g a a s y d e c s o lgui l k n i a t c n ne u sae, i p dco a e f id a c c f a n h o t n s e t n drg u i u s o t n r o t n e e a r k n a n o d u un r tn o
钢 种
C CO a 4. 0 20 . 20 .
主要成分 ( 及物化指标 %)
S2 i O
3. 00 2. 95
3. 00
从仇
4. 0 40 . 42 .
F 60 . 80 . 85 .
熔点/ T
12 10 18 00 19 00
熔速 ( 5%) , X ( 0C /a 10 / 3 度 1 0 ) " 3 Ps
浅谈连铸板坯表面夹杂与裂纹的分析及预防措施

板坯连铸表面夹杂与表面裂纹的分析及预防措施摘 要:针对马钢板坯连铸生产过程中出现的表面夹杂与裂纹进行分析研究,提出了改进措施.关键词:连铸坯;表面夹杂;表面裂纹前 言连铸板坯表面出现夹杂与裂纹是影响铸坯质量的重要缺陷.夹杂与裂纹的出现,轻者要进行表面精整,重者会导致大宗废品的出现,既影响了铸机的生产,又影响了铸坯的质量,增加了企业的成本.本文就马钢第一炼钢厂板坯(220mmx1 300mm)生产中出现的表面夹杂和表面裂纹问题,从多角度分析研究其产生的原因,并提出减少夹杂与裂纹的措施,为板坯连铸生产提高参考.㈠ 表面夹杂缺陷1.1 夹杂来源和形成机理分析马钢第一炼钢厂板坯夹杂主要有两种类型:Ⅰ类为块状分布呈黄或白色;Ⅱ类为连续分布呈青色.通过电镜扫描分析发现:Ⅰ类夹杂是因耐火材料成块脱落而造成的,这种夹杂的结晶与上水口砖及某种耐火泥的结晶基本相同.因此,可以推断Ⅰ类夹杂的来源主要是结晶器上口与其护板之间抹的耐火泥和石英下水口成块脱落.这是因为在成分,颜色,岩相结构3方面与夹杂基本相同.在Ⅱ类夹杂的基体中有大小不等的结晶相α—A120,颗粒.而α—A12O 3有来源于脱氧产物的特征.夹杂中还有SiO 2,SiO 2为石英下水口的熔融状态.因此,可以推断Ⅱ类型夹杂的来源是石英下水口吸附A12O 3后的产物.形成机理是,A12O 3容易在石英质水口壁上附集.由于水口砖质的不均匀性及钢流冲刷的作用,A12O 3被吸附的结果会演变成凸起状颗粒.随其与基体结合面的减小,钢流冲刷及颗粒的增大,最后脱离石英水口而进入结晶器内.以A12O 3,和SiQ 2为主要组成的夹杂物因其熔点高,在保护渣中不易被熔融吸附.当它存在于结晶器四壁的钢液弯月面处时,若操作稍有不慎,这种颗粒状夹杂物就很容易被卷入铸坯表面形成表面夹杂.1.2 减少夹杂的解决办法连铸提高钢的质量控制夹杂物的办法有两类:第一类是防止夹杂物的生成和带入,第二类是去除钢液中已存在的夹杂物。
连铸板坯表面裂纹的成因

图1 中间罐温度与拉 速的对应图
图1 中间罐温度与拉 速的对应图
2)浸入式水口对中 2)浸入式水口对中
浸入式水口与结晶器不对中极易产生偏 流冲刷坯壳,还能引起结晶器液面翻腾, 保护渣不能形成均匀渣膜,导致传热不 良,坯壳厚薄不均而引起裂纹的发生。 投产初期采用人工下装式浸人式水口, 水口不易准确对中,尤其热换水口时, 更难保证对中,这些都可能导致裂纹的 发生。
5)保护渣的行为 5)保护渣的行为
现场所用保护渣的流动性不好。研 究表明,保护渣熔融不充分,粘度 过大,使流人坯壳和结晶器间隙的 渣膜不均匀,会导致摩擦力的变化 及坯壳冷却不均匀,造成坯壳厚薄 不均,引起裂纹的发生。
4 采取的措施
1)提高出钢温度的命中率,确保过热度为15℃±5t,重 新制定中间罐温度与拉速的对应表,见表1。 2)拉速升降时必须按每分钟≤0.15m/min的幅度操作,以 保证结晶器液面波动较小。 3)引进浸入式水口快速更换装置,换水口过程仅需3s, 更换水口迅速、准确、平稳及对中良好。 4)改进保护渣,要求保护渣粘度合适,熔化均匀及形成 的渣膜厚度适中。为此,保护渣的熔点由1145℃调为 1 0 7 0 ℃ , 粘 度 由 0 . 2 3 8 Pa·s(1300℃) 调 为 0 . 1 4 2 Pa·s(1300℃)。 5)对Q235等裂纹敏感性强的钢种,结晶器宽面水量由 200m3/h调为185m3/h。
连铸板坯表面裂纹的成因 及防止措施
1 2 3 4 5 前言 铸机状况 铸坯表面裂纹的影响因素 采取的措施 效果
1 前言
连铸板坯裂纹是影响连铸机产量 和铸坯质量的重要缺陷,轻者要 进行精整,重者会导致拉漏或废 品,影响铸机生产率和铸坯质量。 本文就生产中出现的铸坯表面裂 纹进行分析,并提出减少裂纹的 措施。
连铸板坯三角区裂纹的成因及对策

连铸板坯三角区裂纹的成因及对策
连铸板坯三角区裂纹是钢铁生产中的一种常见缺陷,其成因主要包括以下几个方面:一是板坯冷却不均匀,导致板坯中心温度过高,而三角区温度过低,形成应力集中区;二是连铸机结晶器进口位置不当,导致流场不稳定,形成钢液湍流,进一步加剧应力集中;三是原料成分不均匀,特别是硫、磷等元素含量超标,会加剧板坯中的应力,从而导致三角区裂纹的产生。
为了预防和控制连铸板坯三角区裂纹,可以采取如下措施:一是加强板坯冷却措施,确保板坯温度均匀;二是优化连铸机结晶器的进口位置、流道设计等,确保流场稳定;三是控制原料成分,特别是硫、磷等元素含量,保证板坯中应力的合理分布。
- 1 -。
连铸方坯中心裂纹成因分析及控制方法
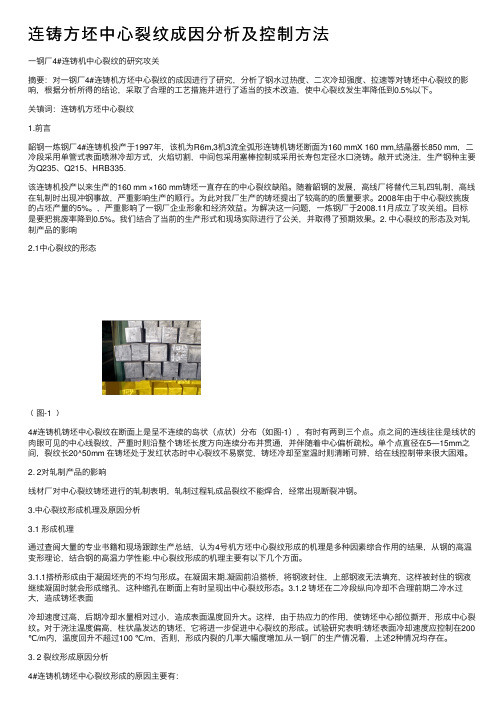
连铸⽅坯中⼼裂纹成因分析及控制⽅法⼀钢⼚4#连铸机中⼼裂纹的研究攻关摘要:对⼀钢⼚4#连铸机⽅坯中⼼裂纹的成因进⾏了研究,分析了钢⽔过热度、⼆次冷却强度、拉速等对铸坯中⼼裂纹的影响,根据分析所得的结论,采取了合理的⼯艺措施并进⾏了适当的技术改造,使中⼼裂纹发⽣率降低到0.5%以下。
关镇词:连铸机⽅坯中⼼裂纹1.前⾔韶钢⼀炼钢⼚4#连铸机投产于1997年,该机为R6m,3机3流全弧形连铸机铸坯断⾯为160 mmX 160 mm,结晶器长850 mm,⼆冷段采⽤单管式表⾯喷淋冷却⽅式,⽕焰切割,中间包采⽤塞棒控制或采⽤长寿包定径⽔⼝浇铸。
敞开式浇注,⽣产钢种主要为Q235、Q215、HRB335.该连铸机投产以来⽣产的160 mm ×160 mm铸坯⼀直存在的中⼼裂纹缺陷。
随着韶钢的发展,⾼线⼚将替代三轧四轧制,⾼线在轧制时出现冲钢事故,严重影响⽣产的顺⾏。
为此对我⼚⽣产的铸坯提出了较⾼的的质量要求。
2008年由于中⼼裂纹挑废的占坯产量的5%。
,严重影响了⼀钢⼚企业形象和经济效益。
为解决这⼀问题,⼀炼钢⼚于2008.11⽉成⽴了攻关组。
⽬标是要把挑废率降到0.5%。
我们结合了当前的⽣产形式和现场实际进⾏了公关,并取得了预期效果。
2. 中⼼裂纹的形态及对轧制产品的影响2.1中⼼裂纹的形态﹙图-1 ﹚4#连铸机铸坯中⼼裂纹在断⾯上是呈不连续的岛状(点状)分布(如图-1),有时有两到三个点。
点之间的连线往往是线状的⾁眼可见的中⼼线裂纹,严重时则沿整个铸坯长度⽅向连续分布并贯通,并伴随着中⼼偏析疏松。
单个点直径在5—15mm之间,裂纹长20^50mm 在铸坯处于发红状态时中⼼裂纹不易察觉,铸坯冷却⾄室温时则清晰可辨,给在线控制带来很⼤困难。
2. 2对轧制产品的影响线材⼚对中⼼裂纹铸坯进⾏的轧制表明,轧制过程轧成品裂纹不能焊合,经常出现断裂冲钢。
3.中⼼裂纹形成机理及原因分析3.1 形成机理通过查阅⼤量的专业书籍和现场跟踪⽣产总结,认为4号机⽅坯中⼼裂纹形成的机理是多种因素综合作⽤的结果,从钢的⾼温变形理论,结合钢的⾼温⼒学性能.中⼼裂纹形成的机理主要有以下⼏个⽅⾯。
- 1、下载文档前请自行甄别文档内容的完整性,平台不提供额外的编辑、内容补充、找答案等附加服务。
- 2、"仅部分预览"的文档,不可在线预览部分如存在完整性等问题,可反馈申请退款(可完整预览的文档不适用该条件!)。
- 3、如文档侵犯您的权益,请联系客服反馈,我们会尽快为您处理(人工客服工作时间:9:00-18:30)。
32
因,认为是轧钢的原因造成(加热或冷却)。1996 年1月、2月生产的此类钢坯,也在轧制钢板时又 少量出现一些有龟裂缺陷的钢板,因原因不明炼 钢厂仍未采取任何措施.但此后较长时期又未出 现,直至1997年1月、2月、3月期问又零星出现 有龟裂缺陷的钢板,而且仍是发生在16Mn低合 金系列钢种。因均是在冬季发生,有人就提出“钢 板产生龟裂缺陷与冬季结晶器给水温度低,结晶 器冷却强度大有关,还与五厂冬季控制铜板冷却 速度有关”的观点.随后1997年11月至1998年 3月冬季期问又继续地出现这类缺陷,似乎又再 次验证了前面的说法,的确此后的1998年4至9 月较长时期又未出现钢板龟裂缺陷.而当时最严 重的缺陷是切割断面“三角区”裂纹,此也是当时 连铸板坯质量攻关的重点。但从10月份就又开始 出现钢板龟裂缺陷并一直延续至今,并且在一段 时期内成为导致钢板报废率最高的质量问题。
1999年3月下旬至4月期间宝鸡宽板厂轧 16Mn桥梁板,用了近1000t板坯轧制合格率不 到lo%,其余均有龟裂缺陷,其中少部分可修磨 交货。而1998年5月~8月期间,宽板分厂轧了 2000多吨桥梁板也未曾出现过龟裂缺陷,当时轧 板厚度为<lOmm、而今年轧板厚度均为>一22mm 以上的中厚板.因此,进一步验证了龟裂缺陷发生 率与轧制钢板厚度相关.
(at型机械科技}2001年第1、2期(合刊)
控制连铸板坯星状裂纹的对策
董荣华 (重庆钢铁股份有限公司,重庆400081)
摘要 回顾重锕七厂连铬板坯星状裂纹导致轧制钢板表面产生龟裂缺陷、以及对钢坯产生星裂的机理 的认识过程,借助国外在这方面的研究成果进行对比分析。认为控制板坯里裂的最重要技术措施是采用“结晶 器软冷却”工艺、以及控制锕的扶紊律势和铜当量.
(1)/E I区,柱状晶间裂纹因偏析导致在晶间 形成富积S、P,有时也有B的液膜而加剧}
(2)在I区,晶粒闯界产生的裂纹量,是由于 细小的硫化物和硫氧化物的沉淀析出以及铁皮下 富积的Cu、Sn、Sb等元素造成的.
(3)在■区,晶粒间界裂纹是由于在以低的变 形速度变形的过程中氮化物和氮化碳的动态析出 而产生的,有时沿奥氏体晶粒间界有先共析铁素 体而加剧裂纹的产生}晶粒问界裂纹(“B”型和 “C”型)与析出物的富积有关,为此,初生奥氏体
4国外对板坯星形裂纹帆理认识和控制星形裂 纹的对策
4.1连铸中裂纹的形成及控制裂纹的对策 4.1.1 连铸中裂纹的产生主要与三个特殊温度 区域有关。对连铸来讲典型的变形速度是属于低 于0.001/s的低变形速度。零塑性的高温区位于 平衡和非平衡固相线温度之间,它导致柱状晶间 裂纹}而在700~900'C之间的低塑性低温区会产 生晶粒间裂纹(沿臭氏体晶粒边界),在900~ 1200.1C之间的中间区域保持短时间也会出现品粒 间界裂纹. 4.1.2这种裂纹还与结构组成有关,如图1、2所 示。
关键调连讳授坯曼状裂纹对策
The Strategy of Controling The Star Crack of Continuous Casting Slab
Dong Ronghua
Ahtract The paper 100ks back the crack defect arisen On rolled steel plate surface resulted from star
1)集中发生在16Mn类低合金钢系列钢种 (其他钢种偶尔有步量)。
2)龟裂缺艏的产生与板坯厚度和轧制铜板厚 度有关。厚度240mm的板坯多在轧厚度≥22mm 的钢板出现龟裂缺陷,尤以轧≥25ram厚度钢板 龟裂缺陷发生率几乎与轧制钢板厚度成正比{而 厚度为210mm的板坯则多在轧制厚度≥18ram 的钢板中产生龟裂缺陷f厚度为l?Omm的钢坯 多为轧厚度12ram以下的钢板,一般不出现有钢 板龟裂缺陷.
其后在重钢七厂随机抽样取16Mn类低合金 钢系列钢种的板坯试件、刨削检验的结果也证实 了星裂普遍存在于这类钢坯表皮或皮下至一定深 度。基于前述认识,腋即叉引出了新的问题。若钢 板星裂是结晶器Cu渗入坯壳并在晶粒间界析出 所致,那么结晶器铜板的磨损速率一定非常大(亦 即结晶器寿命非常短)。但是实践证明:即使浇钢 约500炉后正常返修的结晶器,其内外弧及两侧 铜壁磨损量相当小,其磨损值几乎可忽略不计。导 致结晶器返修的主要原因是:(1)下口磨损使倒锥 度小或无倒锥度(主要是安装对弧原因或振动精 度超标所致)I(2)铜壁上有严重的划痕(主要是送 引锭操作不当或尾坯浇注操作不当,以及处理漏 钢时拉伤铜壁表面).若不是结晶器Cu渗入所 致,晶粒间界析出的Cu又从何而来?为什么使用 镀层结晶器后钢坯星裂明显减少?
Co-Ltd,and crack Ori continuous casting slab in factory No.7 of Chongqing Iron and steel
the process of recog·
nizing the mechanism of arising the star crack on continuous casting slab.Through contrasting and analyzing with the aid of research achievements in this area in foreign country,the author believes that the most impor—
3国内控制星裂的方法与经验
国内连铸界对钢坯星裂产生的机理至今尚无 全面认识,究其原因主要是钢坯星裂过去在各板 坯连铸车间发生率极低,因此未能引起连铸技术 界的广泛重视。但最近两三年来国内多数钢铁厂 都在积极调整品种结构,低合金钢比太大上升,且 轧制厚规格钢板比例也有上升.因此很多板坯连 铸车间钢坯星裂发生率也大幅上升,星裂问题开 始引起连铸技术界的广泛重视.国内宝钢、武钢、 首钢、济钢、鞍钢等厂从事连铸技术的领导和专家
万方数据
《重型机械科技)2001年第1、2期(合刊)
和局部冷却强度就会生成高强度弯月面凝壳进行 正常收缩,并与结晶器脱离.
相对裂纹敏感性与铁紊体量F的关系,A和 “B/C”型裂纹各自的F在超低碳、低碳和高碳钢 的位置及坯壳生长状况,见图3。
o.005%C
o.IO,‘C
I.o蹦C
寰】铜掘厚度与Cu。的关系
万方数据
‘重型机械科技}2001年第1、2期(合刊)
2对钢板产生龟裂原因的认识过程
1999年2月份重钢钢研所在对有龟裂缺陷 的钢板作电子探针检测中发现缺陷部位晶粒间界 有Cu析出,进而对钢坯检验发现,钢坯刨掉氧化 皮后肉眼即可见表皮有零星的星状裂纹,严重者 则为较多的星状裂纹集中于锕坯表面某一区域. 重钢七厂和重钢钢研所为检验其裂纹深度都曾以 刨削加工检测,发现大部分缺陷都在刨深至1~ 2ram后即可消失,而最深者近5ram。因此,在 1999年2月28日重钢公司组织的一次攻关研讨 会上,关于“钢坯星状裂纹是导致钢板产生表面龟 裂的直接原因”这一认识得到认同,大多数的同志 认为是由于结晶器低熔点的cu渗入坯壳后又在 晶粒问界析出而导致星形裂纹,解决的措施是改 用镀层结晶器以隔绝cu渗入坯壳。但为什么同 一种铜种、同一种断面、同一结晶器浇出的钢坯有 的有星裂,有的却没有星裂呢?这是当时提出却不 能解答的问题。1999年3月根据重铜五厂和重锕 生产处提供的有关统计资料作分析,发现产生龟 裂缺陷的钢板有两大特点:
K钾Words Continuous Casting S1ab,Star Crack,Strategy
l前言
重钢七厂于1993年7月首先在24板坯连铸 机上开发成功了第一个品种钢16Mn低合金钢. 当时板坯的综合质量指标较好,板坯的主要缺陷 是表面纵裂和断面中心裂纹.控制表面裂纹当时 主要是采取改进保护渣和稳定操作,较短时间内 表面原始合格率达到30%~40%左右}控制中心 裂纹则是通过改进二冷配水工艺参数,解决扇型 段对弧精度和精确调整夹辊开口度,至1994年底 前已经初步掌握了控制中心裂纹产生的技术。在 此期间连铸板坯和重钢五厂轧制钢板中都未反映 出钢坯星状裂纹和钢板出现龟裂缺陷.
舸板厚度(ram)
7~12 13~16
16 7~12 13~16
16
Cu指标
<31 <16—30
<lS <Z6 <16—25
铜种
无A1 无AI 无A1 Al镇静 A1镇静 AI慎静
童 羔
5 ^4 f ~3
叩2 U 正1
0
图3
4.1.4 对晶粒问界裂纹来说,加Ti对减少“B” 型和“c”型裂纹有作用的,除了减少自由氮之外, 加Ti还有细化晶粒的效果:细化奥氏体晶粒尺寸 也可以减轻非氧化性元素(Cu、Sn、Sb)在铁皮下 富积的影响. 4.I.5 Cu等非氧化性元素的影响及其对策
1999年5月初重钢部分管生产、技术、质量 的同志赴宝鸡宽板分厂对桥梁板产生龟裂缺陷作 专题研究.在现场对轧棚钢板期间龟裂缺陷较多
的同一炉号余下的钢坯和轧制钢板期间无龟裂缺 陷的同~炉号的余下钢坯分别进行了人工火焰全 面积刨皮清理、人工火焰局部清理和人工砂轮机 打磨清理,其结果证明;即使认为轧制钢板中不产 生龟裂缺陷的钢坯,并且打掉氧化皮后肉眼也不 可见星状裂纹,但在砂轮磨深0.1NO.2mm后也 出现了星状裂纹,越往深磨有的裂纹消失,但又有 新的裂纹出现,在观察成品钢板的冷弯试件时也 发现在试件弯曲拉仲面有较多的徽裂.因此,在宽 板分厂的现场分析会上笔者认为“星状裂纹普遍 存在于连铸16Mn类低合金钢系列板坯表面至皮 下,其最深可至皮下5mmI而在表皮已显现,或距 皮下浅于钢坯在加热炉加热时产生的氧化皮厚度 的皮下裂纹,当轧制压缩比小于~定值时,则在钢 坯表面可能产生龟裂缺陷机械科技)2001年第1、2期(台刊)