常见注塑缺陷和对策
注塑常见缺陷的解决方法

注塑常见缺陷的解决方法注塑是一种常见的制造工艺,可以用于生产各种塑料制品。
然而,在注塑过程中常常会出现一些缺陷,如翘曲、气泡、短射等。
这些缺陷会降低产品的质量,影响使用效果。
因此,解决这些缺陷是注塑加工中重要的一环。
下面是一些常见缺陷的解决方法:1.翘曲:翘曲是指注塑制品的形状变形,不符合设计要求。
翘曲的原因可能是注塑温度过高、材料流动不均匀等。
解决方法包括:优化注塑工艺参数,例如调整注塑温度、压力、速度等;增加型腔冷却方式,以提高产品的冷却效果;使用合适的塑料料种,如改变注塑材料的配方,选择更具平衡性能的材料。
2.气泡:气泡是指注塑制品中出现的气体孔洞,影响了产品的外观和性能。
气泡的形成可能是由于注塑材料中的挥发性成分未完全排除、注塑机排气不良等原因。
解决方法包括:增加注塑所需的压力和温度,以促使挥发性成分完全排出;改善注塑机的排气系统,有效排除气泡。
3.短射:短射是指注塑过程中,塑料流动未能充满整个模具的情况。
短射的原因可能是注塑料温度过低、注塑机压力不足、型腔阻力过大等。
解决方法包括:提高注塑温度和压力,以增加塑料的流动性;改善模具的设计,减少型腔的阻力;检查注塑机的喷嘴和螺杆是否损坏,及时更换。
4.热流线:热流线是指注塑制品表面出现的不均匀纹路,影响产品的外观。
热流线的形成可能是由于塑料流动速度过快、模具温度不均匀等原因。
解决方法包括:调整注塑机的喷嘴和螺杆速度,控制塑料的流动速度;优化模具的冷却系统,使模具温度均匀分布。
5.尺寸偏差:尺寸偏差是指注塑制品的尺寸与设计要求不符,可能是由于模具磨损、注塑工艺参数不恰当等原因。
解决方法包括:定期检查和修复模具,以保证模具的精度;优化注塑工艺参数,例如调整注射时间、压力和温度,以控制产品的尺寸。
总的来说,解决注塑常见缺陷需要综合考虑材料、工艺和设备等方面的因素。
通过不断优化参数和改进工艺,可以改善产品的质量,提高注塑加工的效率。
此外,定期维护和保养注塑设备和模具也是预防和解决缺陷的重要措施。
注塑缺陷描述及解决方案

注塑缺陷描述及解决方案一、缺陷描述注塑是一种常见的塑料加工方法,广泛应用于各个行业。
然而,在注塑过程中,常常会出现一些缺陷,影响产品的质量和性能。
下面将描述一些常见的注塑缺陷。
1. 气泡缺陷:气泡是注塑过程中常见的缺陷之一。
它们通常出现在塑料制品的表面或内部,给产品的外观和强度带来不利影响。
气泡的形成可能是由于塑料材料中含有挥发性成分,或者注塑过程中存在过高的温度或压力。
2. 热流痕缺陷:热流痕是由于注塑过程中塑料材料的流动受到阻碍而形成的。
它们通常呈线状或条状,并且会降低产品的外观质量。
热流痕的形成可能是由于模具设计不合理、注塑温度过高或注塑速度过快等原因。
3. 毛刺缺陷:毛刺是指产品表面出现的细小突起,给产品的触感和外观带来不良影响。
毛刺的形成可能是由于模具表面粗糙、注塑温度过高或注塑压力过大等原因。
4. 缩孔缺陷:缩孔是指塑料制品内部出现的空洞或凹陷,降低了产品的强度和密封性能。
缩孔的形成可能是由于注塑过程中塑料材料的收缩不均匀或注塑温度不合适。
5. 热胀冷缩缺陷:热胀冷缩是指注塑制品在冷却过程中由于温度变化而引起的尺寸变化。
如果注塑制品的尺寸与设计要求不符,就会影响产品的装配和使用。
热胀冷缩的控制需要合理设计模具和控制注塑工艺参数。
二、解决方案针对上述注塑缺陷,以下是一些常见的解决方案,以帮助改善产品质量和性能。
1. 气泡缺陷解决方案:- 选择低挥发性的塑料材料,减少挥发性成分的含量。
- 调整注塑过程中的温度和压力,避免过高的温度或压力导致气泡的形成。
- 使用真空抽气装置,帮助排除塑料材料中的气泡。
2. 热流痕缺陷解决方案:- 优化模具设计,确保塑料材料的流动畅通无阻。
- 降低注塑温度,避免过高的温度导致热流痕的形成。
- 控制注塑速度,避免过快的注塑速度导致热流痕的产生。
3. 毛刺缺陷解决方案:- 改善模具表面的光洁度,减少毛刺的形成。
- 调整注塑温度和压力,避免过高的温度或压力导致毛刺的产生。
注塑工艺与产品缺陷解决方案100例

注塑工艺与产品缺陷解决方案注塑工艺是一种常见的制造方法,用于生产各种塑料制品。
然而,在注塑过程中可能会出现一些产品缺陷。
以下是一些常见的注塑产品缺陷及其解决方案:1. 短射(Short Shot):指塑料注射不完整,导致产品部分或全部空洞。
解决方案包括:- 检查模具温度和压力,确保足够的塑料流动。
- 检查塑料熔融温度和压力,确保充分熔融。
- 检查模具设计,确保填充均匀。
2. 气泡(Air Traps):在产品内部形成气泡,影响外观和强度。
解决方案包括:- 调整注射速度和压力,以减少气体陷阱的形成。
- 优化模具通道和冷却系统,确保塑料充分流动并迅速冷却。
3. 热胀冷缩(Warping):产品在冷却后变形或扭曲。
解决方案包括:- 优化模具温度和冷却系统,确保均匀冷却。
- 调整注射速度和压力,避免内部应力积累。
- 使用合适的塑料材料,具有较低的热胀冷缩性能。
4. 流痕(Flow Marks):产品表面出现纹理或痕迹。
解决方案包括:- 调整注射速度和压力,确保塑料流动顺畅。
- 优化模具设计,减少填充阻力。
- 提高模具温度,增加塑料流动性。
5. 毛刺(Flash):产品边缘出现额外的塑料。
解决方案包括:- 检查模具关闭力,确保模具严密闭合。
- 检查模具设计,减少模具间隙。
- 控制注射速度和压力,避免过多的塑料溢出。
6. 熔接线(Weld Lines):由于塑料流动不畅导致的界面线。
解决方案包括:- 调整注射速度和压力,以减少熔接线形成。
- 优化模具设计,减少填充阻力。
- 提高模具温度,增加塑料流动性。
以上只是一些常见的注塑产品缺陷及其解决方案,具体解决方案还需要根据具体情况进行调整和优化。
为了确保产品质量,注塑过程中的工艺参数、模具设计以及塑料材料的选择都非常重要。
注塑缺陷原因分析与解决方案
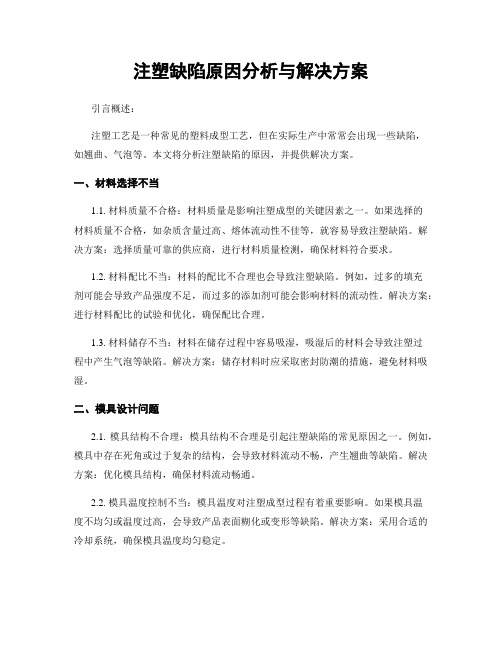
注塑缺陷原因分析与解决方案引言概述:注塑工艺是一种常见的塑料成型工艺,但在实际生产中常常会出现一些缺陷,如翘曲、气泡等。
本文将分析注塑缺陷的原因,并提供解决方案。
一、材料选择不当1.1. 材料质量不合格:材料质量是影响注塑成型的关键因素之一。
如果选择的材料质量不合格,如杂质含量过高、熔体流动性不佳等,就容易导致注塑缺陷。
解决方案:选择质量可靠的供应商,进行材料质量检测,确保材料符合要求。
1.2. 材料配比不当:材料的配比不合理也会导致注塑缺陷。
例如,过多的填充剂可能会导致产品强度不足,而过多的添加剂可能会影响材料的流动性。
解决方案:进行材料配比的试验和优化,确保配比合理。
1.3. 材料储存不当:材料在储存过程中容易吸湿,吸湿后的材料会导致注塑过程中产生气泡等缺陷。
解决方案:储存材料时应采取密封防潮的措施,避免材料吸湿。
二、模具设计问题2.1. 模具结构不合理:模具结构不合理是引起注塑缺陷的常见原因之一。
例如,模具中存在死角或过于复杂的结构,会导致材料流动不畅,产生翘曲等缺陷。
解决方案:优化模具结构,确保材料流动畅通。
2.2. 模具温度控制不当:模具温度对注塑成型过程有着重要影响。
如果模具温度不均匀或温度过高,会导致产品表面糊化或变形等缺陷。
解决方案:采用合适的冷却系统,确保模具温度均匀稳定。
2.3. 模具磨损严重:模具长时间使用后会出现磨损,磨损严重的模具会导致产品尺寸不准确或表面粗糙等缺陷。
解决方案:定期检查和维护模具,及时更换磨损严重的模具部件。
三、注塑工艺参数设置不当3.1. 注射压力过高或过低:注射压力是影响注塑成型的关键参数之一。
如果注射压力过高,会导致产品变形或开裂,而注射压力过低则会导致产品表面光洁度不高。
解决方案:根据产品要求和材料特性,合理设置注射压力。
3.2. 注射速度不合理:注射速度对产品的充填和冷却过程有着重要影响。
如果注射速度过快,会导致产品内部产生气泡或短射,而注射速度过慢则会导致产品表面瑕疵。
注塑成型缺陷及解决方法

注塑成型缺陷及解决方法注塑成型是一种常用的塑料制品生产工艺,但在实际操作过程中,难免会出现一些缺陷。
下面将介绍几种常见的注塑成型缺陷及其解决方法。
1.短射:短射指的是塑料在模腔中注入不完全,导致制品形状不完整或缺少一部分。
短射可能由于注射速度过快或进气不畅引起。
解决方法是调整注塑机的注射速度和压力,确保塑料充分进入模腔,并检查进气口是否畅通。
2.气泡:气泡是指制品表面或内部出现空洞。
气泡的形成可能由于塑料中含有水分、模具开放不当等原因。
解决方法是在注塑前将塑料干燥处理,确保塑料中不含水分,并检查模具密封性以防止气体进入模腔。
3.缩短:缩短是指制品尺寸比设计要小,可能由于塑料收缩不均匀或模具温度不稳定引起。
解决方法是通过调整模具温度和冷却系统,使塑料在注塑过程中均匀收缩,并确保模具温度稳定。
4.色差:色差是指制品表面颜色不均匀,可能由于塑料熔融不充分、颜料添加不均匀等原因。
解决方法是加长塑料的熔化时间,确保塑料充分熔融,并确保颜料充分混合均匀。
5.枝晶:枝晶是指制品表面出现树枝状的纹理,可能由于注塑温度过高或冷却时间不足引起。
解决方法是降低注塑温度,延长冷却时间,确保塑料在注塑过程中充分凝固。
6.毛刺:毛刺是指制品表面出现刺状的尖突物,可能由于模具间隙过大或模具磨损引起。
解决方法是调整模具间隙,确保模具紧密结合,并定期检查模具磨损情况。
7.烧焦:烧焦是指塑料在注塑过程中受热过度,产生发黑或炭化的现象。
烧焦可能由于注塑温度过高或注射速度过快引起。
解决方法是降低注塑温度,调整注射速度,确保塑料受热均匀。
总结起来,解决注塑成型缺陷的关键是调整注塑机参数、保证模具质量和稳定性,以及进行适当的后处理工艺。
此外,及时发现和修复模具的损坏也是避免缺陷的重要措施。
注塑成型常见的缺陷和解决方案

注塑成型常见的缺陷和解决方案
与设计有关的原因与改良措施 1、模温不稳定:提供冷却/加热均衡的模具
-
THANKS
欢迎领导来夸我
70%~80%。如在料头附近 发现注射不满,可以解 释为:流体前锋在这
物理原因:熔料的注射 压力和/或注射速度太低, 熔料在射向流长最末
候。实际上,当需要高 注射压力时,保压也应 按比例提高:正常时, 保
些点被阻挡,较厚的地 方先被充满。如此,在 模腔几乎被充满之后, 在
注塑成型常见的缺陷和解决方案
缩水。这是因为内部 仍有热量,它会穿过 外层并对外层产生加 热作用
模壁的地方先冻结, 在制品中心形成内应 力。如果应力太高, 就会导致
到模件内,在模壁和 已凝固的制品外层之 间就会形成沉降。这 些沉降通
制品内产生的拉伸应 力会使热的外层向里 沉降,在此过程中形 成收缩
注塑成型常见的缺陷和解决方案
与加工参数有关的原因与改良措施 1、保压太低:增加保压 2、保压时间太短:延长保压时间 3、模壁温度太高:降低模壁温度 4、熔料温度太高:降低熔料温度,降低料筒温度 与设计有关的原因与改良措施 1、料头横截面太小:增加料头横截面 2、料头太长:缩短料头 3、喷嘴孔太小:增加喷嘴孔径
注塑缺陷描述及解决方案

注塑缺陷描述及解决方案注塑是一种常用的塑料加工方法,通过将熔化的塑料材料注入模具中,经过冷却固化后得到所需的塑料制品。
然而,在注塑过程中,可能会出现一些缺陷,影响产品的质量和性能。
本文将详细描述常见的注塑缺陷,并提供相应的解决方案。
一、缺陷描述1. 短射(Short Shot):指注塑过程中塑料未充满模具腔体,导致制品缺少某些部分或整体不完整。
解决方案:可能的原因包括模具温度过低、注塑速度过快、塑料材料不足等。
解决方法包括增加模具温度、调整注塑速度、增加塑料材料供给量等。
2. 翘曲(Warping):指注塑制品在冷却后产生变形,失去原本的平整形状。
解决方案:可能的原因包括模具温度不均匀、冷却时间不足、注塑压力过大等。
解决方法包括优化模具设计、增加冷却时间、减小注塑压力等。
3. 气泡(Air Traps):指注塑制品中出现气泡或空洞。
解决方案:可能的原因包括塑料材料中含有水分、注塑压力不稳定、模具排气不畅等。
解决方法包括使用干燥的塑料材料、调整注塑压力、改善模具排气系统等。
4. 热缩(Shrinkage):指注塑制品在冷却后出现尺寸缩小的现象。
解决方案:可能的原因包括模具温度过高、冷却时间不足、塑料材料收缩率不合理等。
解决方法包括降低模具温度、增加冷却时间、选择合适的塑料材料等。
5. 热裂纹(Hot Cracks):指注塑制品在冷却过程中出现裂纹。
解决方案:可能的原因包括注塑温度过高、冷却速度过快、塑料材料选择不当等。
解决方法包括降低注塑温度、控制冷却速度、选择合适的塑料材料等。
二、解决方案1. 优化模具设计:合理设计模具结构,确保充模充型均匀,避免短射、翘曲等缺陷的发生。
2. 控制注塑工艺参数:包括模具温度、注塑速度、注塑压力等。
通过调整这些参数,可以解决短射、翘曲、气泡等缺陷。
3. 选择合适的塑料材料:不同的塑料材料具有不同的性能和特点,选择合适的材料可以避免热缩、热裂纹等缺陷的发生。
4. 增加冷却时间:适当延长注塑制品的冷却时间,有助于避免翘曲、热缩等缺陷的产生。
注塑缺陷及其解决方法
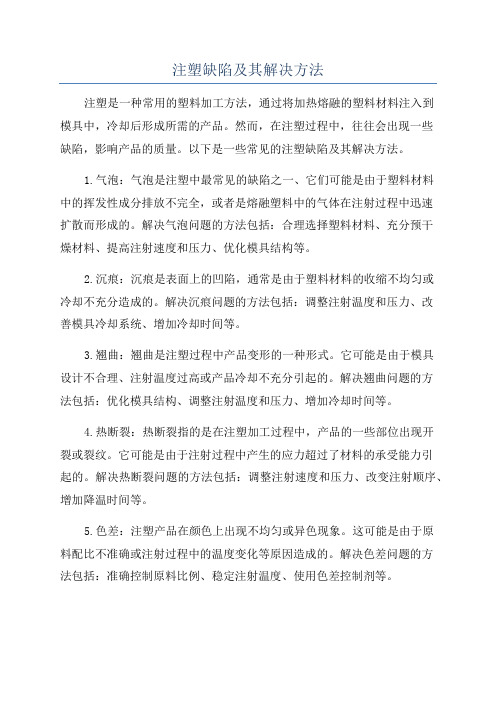
注塑缺陷及其解决方法注塑是一种常用的塑料加工方法,通过将加热熔融的塑料材料注入到模具中,冷却后形成所需的产品。
然而,在注塑过程中,往往会出现一些缺陷,影响产品的质量。
以下是一些常见的注塑缺陷及其解决方法。
1.气泡:气泡是注塑中最常见的缺陷之一、它们可能是由于塑料材料中的挥发性成分排放不完全,或者是熔融塑料中的气体在注射过程中迅速扩散而形成的。
解决气泡问题的方法包括:合理选择塑料材料、充分预干燥材料、提高注射速度和压力、优化模具结构等。
2.沉痕:沉痕是表面上的凹陷,通常是由于塑料材料的收缩不均匀或冷却不充分造成的。
解决沉痕问题的方法包括:调整注射温度和压力、改善模具冷却系统、增加冷却时间等。
3.翘曲:翘曲是注塑过程中产品变形的一种形式。
它可能是由于模具设计不合理、注射温度过高或产品冷却不充分引起的。
解决翘曲问题的方法包括:优化模具结构、调整注射温度和压力、增加冷却时间等。
4.热断裂:热断裂指的是在注塑加工过程中,产品的一些部位出现开裂或裂纹。
它可能是由于注射过程中产生的应力超过了材料的承受能力引起的。
解决热断裂问题的方法包括:调整注射速度和压力、改变注射顺序、增加降温时间等。
5.色差:注塑产品在颜色上出现不均匀或异色现象。
这可能是由于原料配比不准确或注射过程中的温度变化等原因造成的。
解决色差问题的方法包括:准确控制原料比例、稳定注射温度、使用色差控制剂等。
6.熔接线:熔接线是由于注塑模具的设计和操作问题导致两个或多个熔融塑料部分相互连接而形成的。
解决熔接线问题的方法包括:调整模具结构,避免部件交汇点过多,调整注射速度和压力等。
总之,注塑缺陷的解决方法主要包括调整材料配比、优化模具结构、控制注射温度和压力、增加冷却时间等。
同时,及时调整机器参数、进行模具维护和清洁,以保证注塑过程的稳定性和可靠性。
通过以上的措施,可以有效减少注塑缺陷,提高产品质量。
- 1、下载文档前请自行甄别文档内容的完整性,平台不提供额外的编辑、内容补充、找答案等附加服务。
- 2、"仅部分预览"的文档,不可在线预览部分如存在完整性等问题,可反馈申请退款(可完整预览的文档不适用该条件!)。
- 3、如文档侵犯您的权益,请联系客服反馈,我们会尽快为您处理(人工客服工作时间:9:00-18:30)。
2、若合流痕无论如何消除不掉,同时又担心成型品的性能,则可变更注 入口的位置,或是变换注射速度,将形成合流痕的部位移至与强度无关的地方。
3、模具阻力过大,树脂难于流动,先头的部分温度下降,形成合流痕。 遇到这种情况则须扩大模具流道或注入口。
另外,保压压力也有过高的时候,对于这些流动好的树脂,不要从一开始 就施加高保压压力。应边观察成形品的状况,边一点一点提高压力。
2、 最初锁模力不足时,当然会产生飞边,不了解所用模具所需锁模力究 竟有多大,就不可能作出断。先利用锁模力调整手柄 ,增加锁模力试试看。
上图为在模具接触面(分型面)形成的飞边。飞边主要是发生在分型面, 但其它如在小顶杆周围、抽芯周围有时也出现飞边。
1、最多的原因是螺杆料筒温度设定的过高,树脂在螺杆料筒内滞留时间 过长。
2、注射速度快,进料口过小,则树脂在进料口部分热分解,于是在成型 品上形成烧痕。遇到到这种情况,必须修改模具,或是降低注射速度。
3、螺杆旋转过快,会引起树脂过热。 4、偶尔成型品有点填充不足,该填充不足部分有时被烧黑,这是因模具 排气不足,把这种现象叫作黑条也不一定合适,但可以看作是类似现象。
5、模具温度过低也会造成和前一节相同的效果。 当必须施加高压向模腔填充时,有时会导致内部应力。刚成形之后,尽管看不 出有什么异常,但过儿天会发生裂纹,为防止这种不良现象发生,采用退火处 理十分有效。所谓退火系将这种具有内部应力的成型 品加热,消除其应力的 方法。
注塑成型不良现象及改善对策
表面 缺陷
成型材料
修正 注塑机及成型条件
方法 模具设计
制品设计
说明
1.成型物壁厚部分发生缩瘪时。
a、提高注射压力 a、加大浇口 a、把筋、突出
b、增大后期保压压 b、变短浇口 部分变细
力
c、改变浇口位 b、在筋、突出
c、降低缩瘪部分所 置
部分上加 R 角
A3
缩
改变收缩 率小的材
对应的注射速度 d、降低模具温度
什么东西相碰撞,在该处形成一块的办法来加以解决。 4、射出速度快,最初以高速度、呈长线状射入的树脂,立即被冷却,和
后进入的树脂之间产生温度差,于是不能充分熔合在一起,遇到这种情况,降 低射出速度,有时可以解决。
隐条纹
模腔
喷射树脂流
造成隐条纹的原因在模具填充的初期
九、夹水纹(熔接痕)
系指在成形品表面形成的细线状接缝,是不仔细看都发现不了的毛发状接 缝,发生在模腔内流动的熔融树脂的融合面上,因这种现象产生的线称之为合 流痕(或并料痕),与其它部分相比,其强度不足,从成型品的质量角度看, 应尽可能努力予以消除。
四、气泡
在成形品厚的部分易于形成气泡,产生气泡的道理和收缩一样,区别仅在 于表面不发生凹陷,仅在内部形成空洞。至于发生在表面或发生在内部,则与 模具冷却快慢有关。即对低温模具来说,将成形品表面急速冷却,则产生从内 部向表面的收缩,于是在中心附近形成因收缩引起的空洞。
因此,作为解决方法应注意模具温度,其它设施则和处理收缩的措施一样。
3、在模具接触面产生了伤痕、夹有脏东西或是模具平行度差,当然会产 生飞边,模具保管不善,则会使安装面打上伤痕,或是生锈,这样都会导致产 生飞边。所以应该养成习惯妥善保管模具。绝对不得将模具直接放置在地面上。
4、也应特别留意注塑机的模具安装面,安装模具之前应用抹布仔细擦拭。 5、计量过多,或是螺杆料筒的温度设定的过高,均会产生飞边,最初应 慢慢增加计量,温度设定因树脂而异,最好记住大致的标准温度。
其次,有时也与保压压力和时间不足有关,有修改模具之前,最好大体上 检查一下。
收缩
棱
容 易 产 生 收 缩 的 部 位: A、 部件厚的部位,模具温度比较高时; B、 部件厚的部位和薄的部位的交叉点(棱的内侧等),部件薄的部分先
冷却,将厚的部分拉向内侧,造成表面凹陷。 C、 一般来说,厚度在 5mm 以上,则非应装止逆环的树脂未使用 止逆环等小失误也时有所见。
三、缩水
在成形品表面发生的不良现象属于最多的一类,因热收缩造成体积变化引 起的,多发生在部件厚的部分。可以看作是属于渐微的填充不足,所以前项填 充不足的对策亦可适用。
但收缩发生在填充结束之后,大多是因保压效果不充分引起的,因此,首 先应检查成型条件中的保压是否合适,也包括检查模具。
经常出现的情况是因浇口过小和模具温度过低,浇口首先固化,在保压阶 段不能对收缩部分进行补充。遇过这种情况当然应扩大浇口或是提高模具的温 度。
夹水纹
树脂流 夹水纹
十、表面模糊不清(阴云)
系指模具内表面差或使用脱模剂过多,则在表面形成模糊不清的部位。遇
到这种情况,应充分研磨模具,改善脱模就可以了。属于注塑机方面的可列举 以下几点:
1、因注射速度过快,设定温度过高等原因造成过热,引起树脂分解,导致 在表面形成模糊不清的现象。
2、模具温度过低也会产生这种现象。 3、树脂干燥不充分时,往往出现这种情况。
流痕
六、银条(料花)
系指在成形品表面产生沿树脂流动方向形成银白色条带的现象。 1、树脂过热分解,则产生这种现象,此时可降低料筒的设定温度。 2、 树脂干燥不足也会产生这种现象。 3、混入空气,有时也会产生这种现象,遇到这种情况,首先可以提高背
压。料筒后部温度设定得过高,有时也会妨碍空气排出。 4、注射速度过快,也会产生这种现象,其原因在于模具注入口过小,则
d、加宽流道 c、减少其壁厚 e、减少流动阻 d、在设计上考
料
e、降低注射温度 力
虑把筋等设
成形品的重量刚好相当于注塑机的最大射出量,有时也会出现填充不足的 现象,这是由于没有把保压残量行程(俗称容让)扣除的缘故。
3、为防止逆流,则需安装止逆环。聚乙烯、苯乙烯、聚丙烯及尼龙等低 粘度的树脂一定需要,不装的话,因逆流的关系,往往会导致填充不完全。
4、树脂温度过低,则粘度过高,流动性差,有时会造成模具填充不完全。 不管怎么说,树脂温度偏低一些好,过高则收缩加大,保证不了精度,或 是造成热分解而炭化,应始终记住按标准温度进行设定。
产生高剪切热,喷嘴孔径过小,亦呈现同样现象。降低注射速度,可防止这部 分烧痕,也可以扩大进料口及喷嘴的孔径。
5、其它方面,与模具有关的因素包括模具温度过低,排气不良,模腔表 面沾有水份或脏东西。均有可能导致形成银条(料花)。
银条(料花)
七、黑条
系指在成形品中形成的黑色条纹,起因于料筒不干净,或是因树脂材料热 分解形成的烧焦物,遇到这种情况,应尽量清扫螺杆料筒,不采用不良材料。 特别是当树脂热分解烧结到螺杆上之后,只要不进行分解清除,就怎么也不能 彻底弄干净。另外,塑料中若混有易分解的着色剂,则烧痕都位形成黑条,显 现在成形表面。有树脂形成烧痕的原因及解决方法如下:
所谓纵向飞边,几乎均起因于模具精度不够。象尼龙之类熔融粘度低的树 脂,特别容易产生飞边,如聚碳酸酯之类粘度高的树脂则难于产生飞边。
以最大锁模力锁模,仍然出现飞边时,则应考虑是否是机械能力不足。此
时的判断方法是,当模腔内的压力乘以模腔、流道的投影面积所得的数值未超 过机械是大锁模力的话,则不属于机械能力不足。
易于产生填充不足的部位,如上图所示,即针状 袋孔薄的部位和填充树脂时易于封住空气的部位
5、 模具引起的填充不足现象也多得出人意料。 模具内熔融树脂的通道-----浇口、注料口的通过面积小,则阻压力,妨 碍了塑料流入,应根据所用树脂的特性,设计相应的模具,同一模具用于多种 材料,难于得到同样的效果。 另外,对高粘度的树脂,追求成形品精度时,需提高模具温度,有助于树 脂流动,所以说与模具温度有很大关系。偶尔,因模腔的形状造成封入空气, 则该部分呈现填充不足现象。这样的模具则需要排除空气用的“排气槽”。 6、其它方面,如射出速度过慢,或是由于发生了纵向飞边,而不能提高 保压,则造成充填不足。
二、填充不足(缺胶)
所谓填充不足,是指模具填充不满的状态。在达到目的形状之前,冷却固 化则完全成为废品。
1、将射出量设定为最大,情况仍得不到改善,则表示射出压力不足,或 设定温度过低。
2、将计量设定为最大,温度压力根据常识判断亦无异常,出现填充不足 的现象时,多半需要检查注塑机的最大注射量。模腔容积超过最大射出量时, 绝对填充不完全。有成形品样品的话,这种检查很简单,成形之前当然需要检 查,首先测量样品、浇口及流道的重量,低于注塑机的最大注射量就不可以了。 利用注塑机所具有的最大容积乘以树脂的假比重,即可算出该树脂的最大射出 量。
3、料斗侧的设定温度过高,则在该部他树脂呈现流动化,变得不可能用 螺杆输送。
4、螺杆背压过高,则即使螺杆旋转亦不后退(加料),处理尼龙树脂时, 背压应偏低设定好。
5、半自动成形时,停止时间不稳定,对于尼龙场合也会造成进料不良。
十二、 龟裂、开裂
在成形品表面生成的细小裂纹称之为龟裂,生成的大裂纹叫作开裂。 产生这种现象的原因有两个,一是硬行顶出,二是成型品内部应力。 1、为了在顶出时不施加过份的力,应检查模具的起脱模斜度及光洁度, 同时设计小顶杆的个数及其直径等,应考虑与该成型品的形状相符合。 2、象潜伏式浇口那样,阻碍顶出时,应尽可能用粗大的顶杆插入注入口 的一端,这样可以将力平均地施加到成型品上。 3、注射压力过高,保压压力过高,保压时间过长都可能引起内部应力。 4、树脂温度过低,在模腔内处于勉强流动的状态,则应力残留并固化在 制件上。
但需正确估计模腔内压力,然而不能把产品目录所列出的射出压力看作是 模腔压力。射出压力充其量是料筒内的理论压力,树脂流入模具,即被冷却, 压力急剧下降。平均压力从低粘度部件 250kg/cm2到高粘度工业部件 800kg/cm2 左右,这种压力很难估计,虽然大体上有个基准,但要想保证估计精度,还需 要凭经验。
十一、下料不良
系指偶尔树脂材料不能从料斗进入螺杆,这是十分难办的情况,特别是 尼龙料更容易出现这种情况。