凝固过程数值模拟隐式算法时间步长优化模型研究
热顶半连铸6061铝合金棒凝固过程数值模拟

热顶半连铸6061铝合金棒凝固过程数值模拟热顶半连铸6061铝合金棒凝固过程数值模拟随着科技的不断进步和制造业的发展,铝合金在工业界的应用越来越广泛。
其中,6061铝合金因其优良的机械性能、可焊性和耐腐蚀性而备受关注。
热顶半连铸是一种常用的生产6061铝合金棒的工艺,能够实现高效连铸和精细凝固控制。
为了更好地理解和优化该工艺,数值模拟成为研究该过程的重要手段。
热顶半连铸6061铝合金棒的凝固过程可粗略地分为液相凝固和固相凝固两个阶段。
液相凝固阶段是指铝合金在高温下的结晶过程,而固相凝固阶段则是指铝合金液相经过较低温度下的再结晶过程。
凝固过程中的温度场、相变场、结晶场以及流动场等因素互相影响,并且与合金材料的成分、含气含杂质等参数也密切相关。
数值模拟是通过借助计算机对工程问题进行数学分析和仿真模拟的一种方法,其基本原理是通过求解数学模型来获取工程问题的解决方案。
针对热顶半连铸6061铝合金棒的凝固过程,数值模拟可以帮助我们研究该过程中的各种物理现象和过程,并提供准确的数值结果。
首先,数值模拟可以模拟凝固过程中的温度场变化。
通过对铝合金棒进行热传导和热对流分析,可以得到在不同时间和位置上的温度分布。
这对于控制凝固过程中的温度梯度和温度均匀性非常重要,以确保铝合金棒的横截面质量均匀。
其次,数值模拟可以模拟凝固过程中的相变过程。
熔融态的铝合金在凝固过程中会发生相变,例如液态铝合金凝固为固态铝合金。
通过建立相变模型和相变规律,可以模拟铝合金凝固过程中相变的时间和位置,并对凝固速度和晶粒尺寸的影响进行研究。
此外,数值模拟还可以模拟凝固过程中的流动场。
液态铝合金在凝固过程中会发生流动,这对于凝固速度和组织结构的形成具有重要影响。
通过建立流动模型和流动规律,可以模拟液态铝合金在凝固过程中的流动情况,并对凝固速度和晶粒尺寸的分布进行分析。
最后,数值模拟可以分析凝固过程中的力学性能。
凝固后的铝合金棒的力学性能会受到凝固过程中温度场、相变场和晶体生长过程的影响。
钢铁冶炼过程中的数值模拟与优化研究

钢铁冶炼过程中的数值模拟与优化研究第一章引言钢铁行业作为国民经济的重要组成部分,一直是各国竞相发展的重点产业之一。
不过在现代化的发展进程中,科技的支持和推动必不可少。
而数值模拟与优化技术的出现和应用,为钢铁冶炼提供了新的途径和手段。
本章将从现状、背景、目的等多个角度来介绍本文关注的钢铁冶炼过程中的数值模拟与优化研究。
第二章钢铁冶炼过程中的数值模拟技术2.1 热力学模拟技术热力学模拟技术是指通过建立数学模型,对钢铁冶炼过程中的热力学现象进行计算。
这种技术可以帮助钢铁冶炼工程师更加准确地预测热力学现象的变化趋势,为钢铁冶炼过程中的操作决策提供依据。
目前,一些著名的热力学模拟软件如Thermocalc、FactSage等已被广泛应用于钢铁冶炼生产中。
2.2 流体力学模拟技术流体力学模拟技术是指通过建立数学模型,对钢铁冶炼过程中的流体现象进行计算。
这种技术可以帮助钢铁冶炼工程师更加准确地模拟炉内的流体流动、混合等过程。
一些著名的流体力学模拟软件如Fluent、Star-CCM+等已被广泛应用于钢铁冶炼生产中。
第三章钢铁冶炼过程中的数值优化技术3.1 工艺参数优化工艺参数优化是指通过对钢铁冶炼过程中的各个参数进行调整、优化,以提高钢铁冶炼过程的效率和质量。
目前,一些数值优化软件如Optimus、Design-Expert等已被广泛应用于钢铁冶炼生产中。
3.2 设备参数优化设备参数优化是指通过对钢铁冶炼过程中的各个设备参数进行调整、优化,以提高钢铁冶炼过程的效率和质量。
目前,一些数值优化软件如ANSYS、Simulink等已被广泛应用于钢铁冶炼生产中。
第四章数值模拟与优化在钢铁冶炼中的应用实例4.1 数值模拟在连铸过程中的应用在连铸过程中,数值模拟技术可以帮助工程师更加准确地模拟流体流动、凝固过程等现象,从而预测浇注过程中可能出现的问题,优化浇注过程中的工艺参数。
4.2 数值模拟在高炉炉缸内炉渣流动中的应用在高炉炉缸内炉渣流动中,数值模拟技术可以帮助工程师更加准确地模拟炉缸内的炉渣流动、混合等过程,从而优化高炉炉渣的排放、降低污染物排放。
铝合金铸件凝固过程的宏观及微观模拟仿真研究进展
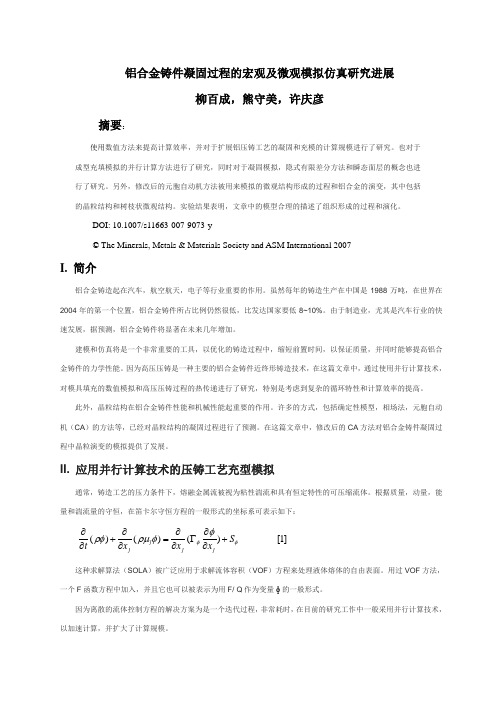
铝合金铸件凝固过程的宏观及微观模拟仿真研究进展柳百成,熊守美,许庆彦摘要:使用数值方法来提高计算效率,并对于扩展铝压铸工艺的凝固和充模的计算规模进行了研究。
也对于成型充填模拟的并行计算方法进行了研究,同时对于凝固模拟,隐式有限差分方法和瞬态面层的概念也进行了研究。
另外,修改后的元胞自动机方法被用来模拟的微观结构形成的过程和铝合金的演变,其中包括的晶粒结构和树枝状微观结构。
实验结果表明,文章中的模型合理的描述了组织形成的过程和演化。
DOI: 10.1007/s11663-007-9073-y© The Minerals, Metals & Materials Society and ASM International 2007I. 简介铝合金铸造起在汽车,航空航天,电子等行业重要的作用。
虽然每年的铸造生产在中国是1988万吨,在世界在2004年的第一个位置,铝合金铸件所占比例仍然很低,比发达国家要低8~10%。
由于制造业,尤其是汽车行业的快速发展,据预测,铝合金铸件将显著在未来几年增加。
建模和仿真将是一个非常重要的工具,以优化的铸造过程中,缩短前置时间,以保证质量,并同时能够提高铝合金铸件的力学性能。
因为高压压铸是一种主要的铝合金铸件近终形铸造技术,在这篇文章中,通过使用并行计算技术,对模具填充的数值模拟和高压压铸过程的热传递进行了研究,特别是考虑到复杂的循环特性和计算效率的提高。
此外,晶粒结构在铝合金铸件性能和机械性能起重要的作用。
许多的方式,包括确定性模型,相场法,元胞自动机(CA )的方法等,已经对晶粒结构的凝固过程进行了预测。
在这篇文章中,修改后的CA 方法对铝合金铸件凝固过程中晶粒演变的模拟提供了发展。
II. 应用并行计算技术的压铸工艺充型模拟通常,铸造工艺的压力条件下,熔融金属流被视为粘性湍流和具有恒定特性的可压缩流体。
根据质量,动量,能量和湍流量的守恒,在笛卡尔守恒方程的一般形式的坐标系可表示如下:()()()[1]j j j jS t x x x φφφρφρμφ∂∂∂∂+=Γ+∂∂∂∂这种求解算法(SOLA )被广泛应用于求解流体容积(VOF )方程来处理液体熔体的自由表面。
基于ANSYS的铸件充型凝固过程数值模拟的开题报告

基于ANSYS的铸件充型凝固过程数值模拟的开题报告1. 研究背景铸造是一种重要的制造工艺,广泛应用于工业生产中。
铸造的过程中,充型凝固是其中最基本的环节之一,其质量直接影响着铸件的成型和性能。
传统的充型凝固过程试验需要大量人力、物力和财力投入,成本较高,同时也难以控制实验条件,因此利用数值模拟方法对铸造过程进行分析与预测就显得格外重要。
ANSYS是一种应用广泛的数值分析软件,它可以应用于多个领域的工程仿真,包括铸造领域。
基于ANSYS的铸造充型凝固过程数值模拟可以较为精确地模拟铸造工艺,对铸件质量控制有着重要的作用。
因此,本文拟研究基于ANSYS的铸造充型凝固过程数值模拟方法。
2. 研究内容本文主要研究基于ANSYS的铸造充型凝固过程数值模拟方法。
研究的具体内容包括:(1)建立充型凝固数值模型:通过ANSYS建立铸造模型,并在模型中考虑充型、凝固和冷却等因素,确定模型的边界条件。
(2)数值模拟求解:利用ANSYS的求解功能,对模型进行数值模拟,获得充型凝固过程的温度和流动场分布等参数。
(3)结果分析:对数值模拟结果进行分析,评估充型凝固过程的质量,提出改进方案并进行优化。
3. 预期成果本研究的预期成果主要包括:(1)建立基于ANSYS的铸造充型凝固数值模型,实现对铸造过程的数值模拟。
(2)通过数值模拟获得铸造过程中的温度和流动场分布等参数,并对其进行分析。
(3)评估充型凝固过程的质量,提出改进方案并进行优化。
4. 研究意义本研究的意义主要体现在以下几个方面:(1)通过数值模拟方法获得铸造过程中的温度和流动场等参数,可以更准确地评估充型凝固过程的质量。
(2)实现基于ANSYS的铸造充型凝固数值模拟,可以在一定程度上避免传统充型凝固实验的高成本和实验条件不易控制的问题。
(3)本研究的方法可以为铸造行业提供参考,为铸造过程的质量控制提供技术支持。
5. 研究进程安排本研究的进程安排如下:(1)前期准备阶段:熟悉铸造充型凝固过程数值模拟理论,了解ANSYS软件的使用方法,确定研究方向。
二元合金定向凝固过程的相场模拟的开题报告
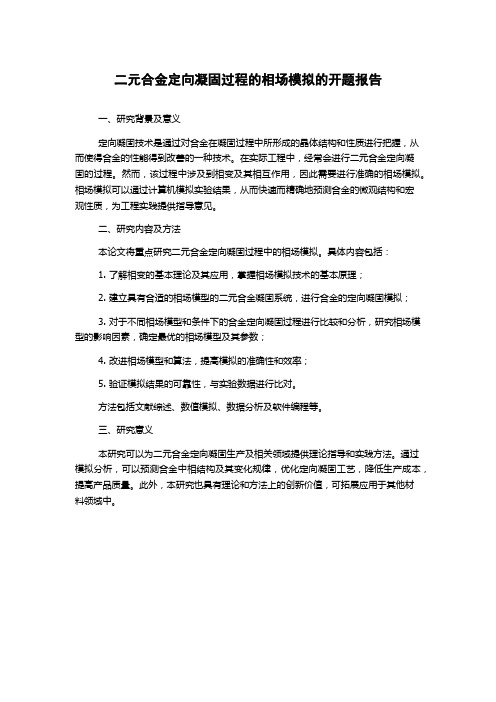
二元合金定向凝固过程的相场模拟的开题报告
一、研究背景及意义
定向凝固技术是通过对合金在凝固过程中所形成的晶体结构和性质进行把握,从而使得合金的性能得到改善的一种技术。
在实际工程中,经常会进行二元合金定向凝
固的过程。
然而,该过程中涉及到相变及其相互作用,因此需要进行准确的相场模拟。
相场模拟可以通过计算机模拟实验结果,从而快速而精确地预测合金的微观结构和宏
观性质,为工程实践提供指导意见。
二、研究内容及方法
本论文将重点研究二元合金定向凝固过程中的相场模拟。
具体内容包括:
1. 了解相变的基本理论及其应用,掌握相场模拟技术的基本原理;
2. 建立具有合适的相场模型的二元合金凝固系统,进行合金的定向凝固模拟;
3. 对于不同相场模型和条件下的合金定向凝固过程进行比较和分析,研究相场模型的影响因素,确定最优的相场模型及其参数;
4. 改进相场模型和算法,提高模拟的准确性和效率;
5. 验证模拟结果的可靠性,与实验数据进行比对。
方法包括文献综述、数值模拟、数据分析及软件编程等。
三、研究意义
本研究可以为二元合金定向凝固生产及相关领域提供理论指导和实践方法。
通过模拟分析,可以预测合金中相结构及其变化规律,优化定向凝固工艺,降低生产成本,提高产品质量。
此外,本研究也具有理论和方法上的创新价值,可拓展应用于其他材
料领域中。
金属铸造凝固过程的界面传热系数的研究与应用的开题报告

金属铸造凝固过程的界面传热系数的研究与应用的开题报告一、选题背景金属铸造是制造高强度、高质量零部件的重要方法之一。
金属在铸造过程中从液态状态逐渐凝固固化,凝固过程的传热速度和方式会对铸件的晶粒组织、漏斗流、固化收缩等性能产生重要影响。
因此,研究凝固过程中的界面传热系数对于优化铸造工艺、提高产品质量和性能具有重要意义。
二、选题意义当前,我国金属铸造行业的发展具有独特的优势和良好的发展前景。
但铸造行业缺乏高效、精确、可靠的传热模型,铸造工艺优化和质量提高的效果难以达到最优化。
因此,深入研究铸造凝固过程中的界面传热系数,对实现金属铸造工艺的优化与可靠化具有重要意义。
三、研究目标本次研究旨在:1.系统研究铸造凝固过程中的界面传热系数,建立凝固过程的传热模型;2.开展铸造凝固过程中的温度场和凝固组织演化的数值模拟,验证传热模型的可靠性和精度;3.利用传热模型和数值模拟结果优化铸造工艺,提高产品质量和性能。
四、研究内容1.理论基础与方法:系统介绍凝固过程的传热过程及相关物理学理论。
2.界面传热系数的测定方法:从实验和理论两个角度讨论界面传热系数的测定方法。
对比不同方法的优缺点,选择最合适的测量方法。
3.凝固过程传热模型的建立与验证:建立凝固过程的传热模型,探求凝固过程传热规律。
将模型与实验数据和数值模拟结果进行对比,验证模型的精度和可靠性。
4.研究铸造凝固过程中的温度场和凝固组织演化:根据模型所得出的界面传热系数计算铸造凝固过程的温度场和凝固组织演化规律。
通过数值模拟计算,验证模型的有效性和合理性。
5.铸造工艺优化:将界面传热系数模型和数值模拟结果应用于工业生产实践,探讨优化铸造工艺,提高产品质量和性能。
五、预期目标1.系统研究凝固过程的传热过程及相关物理学理论,了解界面传热系数的影响因素和测量方法。
2.建立凝固过程的传热模型,探求凝固过程传热规律。
3.验证传热模型的精度和可靠性。
4.基于数值模拟结果和传热模型,探讨优化铸造工艺,提高产品质量和性能。
铸件凝固模拟过程中的几种时间步长计算方法探讨_龚文邦

(4)
式中 T L ———液相线温度 ; T S ———固相线温度 。
将式(4)代入式(3), 整理得 :
ρcp
+ TL
L -
TS
ΔT
=
λ6(TΔix
-T Δx
0)Δτ
(5)
令 ce =cp +L /(T L - TS ), 为等效比热容(无相变时 , ce =c), 则有 :
ΔT
=ρ6cλe
Ti - T 0 Δx Δx
cp ———比热容 , J / kg K ; T ———温度 , K ; t ———时间 , s ; λ———导热系数 , W /m K ;
Q′———内热源 , Q′=рL f s/ T ; L ———熔化潜热 , J / kg ; f s ———固相率 。
按差分格式将方 程(1)离散 , 并 假定 Δx =Δy =
为了在满足稳定求解的前提下 , 尽量加快计算速 度 , 本文根据不同情况经理论推导 , 得到了几种时间步 长的计算方法 。 1 满足 Fo urier 方程收敛条件的时间步长计算
金属液充型后 , 金属与铸型内部传热主要以不稳 定导热方式进行 。其控制方程为 :
收稿日期 :2005-05-28 ; 修订日期 :2006-01-17 基金项目 :国家自然科学基金资助项目(10176009);国家航天支撑技 术
图 1 单元(i , j , k)与相邻 单元的热交换
Fig . 1 Heat ex change between units(i, j , k)and adjoining units
在 Δτ时间内 , 单元(i , j , k)的总热量变化 Q 为 :
Q
=ρC p Δx 0 Δy 0 Δz 0
中国古代青铜器凝固过程的数值模拟及其相关工艺问题

青铜器铸造过程中的缺陷预防与控制
防止金属氧化
在熔炼和注入过程中,防 止金属氧化,以减少铸造 缺陷。
控制注入压力
在注入过程中,控制压力 ,以防止模具填充不均或 产生气孔等缺陷。
及时处理异常情况
在铸造过程中,及时处理 异常情况,如模具破裂、 金属溢出等,以减少铸造 缺陷的产生。
06
结论与展望
研究结论与贡献
VS
温度场分布的影响
温度场分布的不均匀性会导致青铜器内部 产生热应力,进而影响其力学性能和显微 组织结构。在某些情况下,不均匀的温度 场分布还可能导致青铜器产生裂纹或变形 等缺陷。因此,为了提高青铜器的质量和 性能,需要对其凝固过程中的温度场分布 进行精确控制。
青铜器凝固过程中的热力学参数变化
热力学参数的测量
感谢您的观看
THANKS
结论
通过对中国古代青铜器凝固过程的数值模 拟,研究得出了青铜器在凝固过程中的温 度场、应力场、微观组织演化等规律,揭 示了青铜器铸造过程中的关键工艺参数对 凝固组织的影响机制。
贡献
本研究为深入理解中国古代青铜器制造工 艺提供了理论支持,同时为优化青铜器制 造过程、提高铸造质量提供了重要的指导 。
研究不足与展望
03
收敛性和稳定性分析
在进行数值模拟时,需要确保计算过 程的收敛性和稳定性。通过对计算过 程进行监控和分析,可以确保模拟结 果的准确性和可靠性。
04
中国古代青铜器凝固过程 的数值模拟结果
青铜器凝固过程的温度场分布
温度场分布特征
通过对青铜器凝固过程的数值模拟,可以 得出其温度场分布。在凝固开始时,青铜 器表面和内部的温度分布较为均匀。随着 凝固的进行,温度场分布逐渐变得不均匀 ,表面温度逐渐降低,而内部温度则逐渐 升高。这种温度场分布的变化与青铜器的 形状、大小以及所处的环境条件有关。
- 1、下载文档前请自行甄别文档内容的完整性,平台不提供额外的编辑、内容补充、找答案等附加服务。
- 2、"仅部分预览"的文档,不可在线预览部分如存在完整性等问题,可反馈申请退款(可完整预览的文档不适用该条件!)。
- 3、如文档侵犯您的权益,请联系客服反馈,我们会尽快为您处理(人工客服工作时间:9:00-18:30)。
Study on Time Step Optimization Model for Solidification Simulation with Component Wise Splitting Method
铸造
Vol 53 No 9
7 24
FOUNDRY
Sep. 2004
计算机应用
凝固过程数值模拟隐式算法
时间步长优化模型研究
董怀宇, 熊守美, 程万里
( 清华大学机械工 程系, 北 京 100084)
摘要: 在铸造过程计算机模拟中, 温度场计 算采用显式方 法由于稳 定性的 要求, 时 间步长受 限, 计算 效率低。采 用
图 4 No 2 方案预测的缩松 Fig 4 Simulation results of shrinkage prediction of the No 2 scheme
表 3 轧钢机架模拟计算的结果 Table 3 Si mulati on result of the mill housing
轧钢机架
铸件 总单元数
( 铸钢 20)
单元数
自动优化时间步长 489694 10018050
时间 步长/ s
-
预计凝固 计算 时间/ s 时间/ s 151901 11088
3 结论
( 1) 在分数 步长法计算凝固过程温 度场的基础 上, 提出了单元跨越固液相线时间的概念, 以单元跨 越固液相线时间来衡量凝固过程; 在此基础上, 开发 了自动优化时间步长模型。在凝固计算过程中, 自动 调整时间步长, 实现在保证计算精度的情况确定的问题。
in sand casting pr ocess
测试单元
No 1 方案 点
No 2 方案 1 相对误差 ( % )
No 1 方案 点
No 2 方案 3 相对误差 ( % )
73 6 s 1318 4 1321 3
0 09 1186 5 1187 6
0 09
温度 / C 310 6 s 499 4 s 761 7 s 1053 2s 1198 5 1187 4 1173 4 1142 7 1198 3 1186 9 1172 5 1141 6
1081
245
( 均匀时间步长)
No 2 方案
12721 360000 -
1082
140
( 变化时间步长)
在铸件对称剖切面上取 5 个凝固速度不同的铸件 单元, 位置如图 3 所示, 输出铸件凝固过程温度场的
图 2 两种方案计算时间步长比较 Fig 2 Comparison of time step of t wo schemes
铸造
董怀宇等: 凝固过程数值模拟隐式算法时间步长优化模型研究
7 25
时间 t s 的基础上, 计算时间步长的公式为:
t n+ 1 =
t sn m
式中 t n+ 1
第 n + 1 时间步的时间步长, s
t sn
第 n 时间步铸件单元跨越固液相线
时间, s
m
确定时间步长划分精度常数
图 1 低于固、液相线的铸件单元百分数随时间变化曲线 Fig 1 Time dependent profiles of percent ages of cast ing cells below
2 模拟验证及分析
为了验证自动优化时间步长模型的正确性和可行 性, 作者对不同复杂程度的铸件进行了温度场的数值 模拟 计 算。 计 算机 硬 件 配 置 为 Win2000, PIII 1G, 1 5G 内存。 2 1 砂型铸造实验件温度场计算实例
选用砂型铸造实验件进行模拟验证, 铸件材料为 球铁 250。采用两种方案进行温度场计算比较, 在分 数步长法 的基础上, No 1 方案采用 均匀时间 步长; No 2 方案采用自动优化时间步长。计算情况如表 1 所示, 两方案预计的凝固时间非常一致, 所花费的计 算时间却几乎相差 1 倍。No 2 方案中自动优化时间 步长变化曲线如图 2 所示, 可以看出时间步长开始时 比 1 75s 小, 随着凝固的进行, 时间步长逐步增大, 然后在一定的范围里波动。
作者通过点模数 5 预测获得铸件完全凝固时间, 从而确定出初始计算时间步长。在单元跨越固液相线
基金项目: 国家重点基础研究规划项目 ( G2000067208- 3) 。收稿日期: 2004-04-05 收到初稿, 2004- 04-16 收到修订稿。 作者简介: 董怀宇 ( 1979- ) , 男, 白族, 云南大理人, 硕士研究生, 从事铸造数值模拟研究。
图 3 记录温度数据的单元位置 Fig 3 Cells posit ions recording simulation temperature data
2 2 某厂轧钢机架件温度场计算实例 选用某厂砂型铸造轧钢机架件进行模拟验证。铸
件材质为铸钢 20。计算情况如表 3 所示, 时间步长
726 Sep. 2004
( 2) 用均匀时间步长方案和自动优化时间步长模 型方案对铸件进行了温度场的模拟计算, 对计算结果 进行了比较, 验证了模型的可靠性。并与实际情况比 较了缺陷的位置与大小, 验证了模型的正确性。
参考文献: 1 林首位, 徐宏, 侯华, 龚荣良. 铸件三维温度场数值模拟隐式
图 6 轧钢机架的缩孔缩松预测结果 Fig 6 Shrinkage prediction of the mill housing 差分法研究 J . 铸造 2002, ( 6) : 358~ 361 2 刘伟涛, 曾大新, 苏俊义. 用 交替方向隐 式迭代法 计算铸件 凝 固过程的温度场 J . 西安交通大学学报. 2000, ( 7) : 68~ 72 3 吴亮, 熊守美, 柳百成. 应用 分数步长法 进行压铸 过程温度 场 数值模拟研究 J . 铸造. 1998, ( 11) : 15~ 19 4 Xiong Shoumei, Li Yongqiang, Peng Jingsong. Zone partit ioning computation t echnique during solidification simulation of sand casting process J . Int J Cast Metal Res. , 2002, 15, ( 4) : 385 ~ 388 5 Upadhya G, Paul A J. Comprehensive casting analysis model using a geometry- based technique followed by fully coupled, 3-D fluid flow, heat t ransfer and solidification kinetics calculations J . AFS Transact ions, 1992, 100: 25~ 33
在计算普通砂型铸造过程温度场时, 常采用有限 差分、有限元及边界元等数值计算方法。其中, 有限 差分法根据差分格式的不同, 又可分为显式差分法和 隐式差分法。显示差分法是比较成熟的方法, 易于理 解, 通用性强。目前, 国内外许多商品化软件, 如德 国的 MAGMA, 和清华大学的 FT-STAR 等, 都是用这 种方法实现铸件温度场的数值模拟及预测。但由于它
分数步长法- 隐式计算, 由于其求解方法绝对稳定, 因而对时间步长无限制。为了在保证计算精确度的 情况下尽可 能 地提高计算效率, 需要动态调节计算温度场的时间步长。本文中以凝固过程温度场的计算时间步长研 究为题, 提出 了 单元跨越固液相线时间的概念, 建立了自动优化计算时间步长的模型。对实际的不同大小, 不同形状复 杂程度的铸 件 进行模拟计算, 对均匀时间步长和自动调节时间步长的计算结果进行比较, 验证了自动调节时间步长的合理性 。
DONG Hua-i yu, XIONG Shou-mei, CHENG Wan-li ( Department of Mechanical Engineering, Tsinghua University, Beijing 100084, China)
Abstract: In order to improve the comput ing efficiency of solidification simulation of casting processes, the component wise splitt ing method was applied to calculate temperature field. A concept of t ime that casting cells across the liquidus and the solidus temperatures was proposed and a model for time step opt imization during solidification simulation was established according to the concept. The solidification processes of casting samples were modeled for the verification by both uniform time step method and dynamically optimized time step method. The simulated temperature fields and the predicted shrinkage defects are in agreement in both cases. Comparison of the simulation results showed that the model for time step optimization can properly adjust time step during solidification simulation and greatly improve the computational efficiency. Keywords: solidification simulation; implicit finite difference; time step; optimization