2500td预分解窑操作体会
预分解窑操作体会

预分解窑操作体会•相关推荐预分解窑操作体会在水泥厂中,烧成车间相对而言要比其他车间复杂得多。
这主要是孰料烧成有严格的热工制度,要求风、煤、料、窑速进行合理匹配,出现异常情况要及时调整。
否则,短时间内影响一点产量事小,如果处理不当还会出现红窑或预分解系统堵塞等问题。
通过生产实践体会到,当一个好的操作员,既要解决在中控窑操作自如,判断正确、果断,又要解决好现场出现的实际问题,实属不易。
下面就预分解窑的操作谈一些体会,供大家参考。
1、看火操作的具体要求1)作为一名回转窑操作员,首先要学会看火。
要看火焰形状、黑火头长短、火焰温度及是否顺畅有力,要看熟料结粒、带料高度和翻滚情况以及后面来料的多少,要看烧成带窑皮的平整度和厚度等。
2)操作预分解窑窑坚持前后兼顾,要把预分解系统情况与窑头烧成带情况结合起来考虑,要提高窑的快转率。
在操作上,要严防大起大落、顶火逼烧,要严禁跑生料或停窑烧。
3)监视窑和预分解系统的温度和压力变化、废气中O2和CO含量变化和全系统热工制度的变化。
要确保燃料的完全燃烧,减少黄心料。
尽量使熟料结粒细小均齐。
4)严格控制熟料F-CaO含量小于1.5℅,立升重波动±50g/L以内。
5)在确保孰料产量的前提下,保持适当的废气温度,缩小波动范围,降低燃料消耗。
6)确保烧成带窑皮平整,厚薄均匀,坚固。
操作中要努力保护好窑衬,延长安全运转周期。
2、预热器系统的调整2.1撒料板的调节撒料板一般都置于旋风筒下料的底部。
经验告诉我们,通过排灰阀的物料都是成团的,一股一股的。
这种团状或股状物料,气流不能带起而直接入旋风筒中造成短路。
撒料板的作用就是将团状或股状物料撒开,是物料均匀分散地进入下一级旋风筒进口管道的气流中。
在预热器系统中,气流与均匀分散物料间的传热主要在管道内进行的。
尽管预热器系统的结构形式有较大的`差别,但下面一组数据基本相同。
一般情况下,旋风筒进出口气体温度之差在20℃左右,出旋风筒的物料温度比出口气体温度低10℃左右。
窑外分解窑熟料产量和质量的提高与稳定

2500/d窑外分解窑熟料产量和质量的提高与稳定某水泥有限公司2500t/h熟料生产线是由天津水泥工业设计研究院设计的。
分解炉为DD炉,预热器为双系列的;回转窑规格为Ф4×60m;生料磨为Ф4.6×10+3.5m中卸烘干磨;煤磨为Ф2.8×5+3m风扫磨;煤粉计量采用德国PFISTER公司生产的DRW4.10转子秤;篦冷机为天津院开发的带有充气篦板的冷却机;控制系统为天津院开发的集散型控制系统。
该生产线于2006年1月份点火,试生产期间熟料质量不稳定,日产熟料2500t左右。
经过1年多来的实践和探索,使窑的熟料质量和日产能力得以提高与稳定, 2006年连续12个月生产合格熟料729045t;2007年1月至4月共生产熟料259802t;从2006年10月份开始到目前一直稳定运转在较高的产质量水平上(见表1)。
以下为我们稳定提高熟料产质量的具体做法。
表1 2006年-2007年4月窑运转情况1 积极采取措施稳定生料质量1)严把原材料关。
我公司有自己的石灰石矿山,地质勘探结果表明,CaO含量平均为52.4%,含有夹石层,我们做法是,对矿山进行分片取样检验,根据检验结果,再进行高品位石灰石与低品位石灰石进行搭配开采(即使每片石灰石CaO含量都在控制范围内,也要多点搭配开采),要求矿山车间遵照执行,下山石灰石每两小时检验一次CaO含量,发现有低于49%时,及时通知矿山车间更改搭配比例,确保下山石灰石CaO含量在50%-53%之间,另外严格控制石灰石破碎粒度要<25mm。
我公司砂岩附近采购,化验室人员定期到砂岩矿取样检验,进行指导开采,要求进厂砂岩SiO2含量在72-73%之间,一旦检验结果超出此范围,及时通知砂岩矿调整搭配比例,确保砂岩成分被动严格控制在较小的范围内,砂岩粒度控制在<25mm。
我公司主要从两家采购,严格控制进厂水分和品位。
2)充分发挥均化设施作用。
我公司有Ф80m石灰石预均化库,公司要求堆料层数达到500层以上,并进行往复式布料,整个预均化库储存量不低于15000t;对砂岩的做法是,在矿点附近设不低于6000t储存量露天堆场,再输送到我公司砂岩堆棚,进行二次倒堆,在公司堆棚内储存量也低于6000t,再通过皮带输送砂岩预均化库再次均化;对铁粉的做法是,每批铁粉到公司露天堆场后,进行拢堆,再通过皮带输送铁粉预均化库。
[精选]【工作总结】水泥厂预分解窑岗位工作经验总结范本(WORD档)P13--资料1
![[精选]【工作总结】水泥厂预分解窑岗位工作经验总结范本(WORD档)P13--资料1](https://img.taocdn.com/s3/m/186dce1958fafab069dc02ef.png)
[精选]【工作总结】水泥厂预分解窑岗位工作经验总结范本(WORD档)P13--资料1水泥厂预分解窑岗位工作经验总结在水泥厂中,烧成车间相对而言要比其它车间复杂得多。
这主要是熟料烧成有严格的热工制度,要求风、煤、料和窑速进行合理匹配,出现异常情况要及时调整。
否则,短时间内影响一点产质量事小,如果处理不当还会出现红窑或预分解系统堵塞等问题。
通过生产实践体会到,当一个好的窑操作员,既要在中控室操作自如,判断正确、果断,又要解决好烧成现场出现的实际问题,实属不易。
下面就预分解窑的操作谈一些体会。
1、作为一名回转窑操作员,首先要学会看火。
要看火焰形状、黑火头长短、火焰亮度及是否顺畅有力,要看熟料结粒、带料高度和翻滚情况以及后面来料的多少,要看烧成带窑皮的平整度和窑皮的厚度等。
2、操作预见性要好、要坚持前后兼顾,炉窑协调,确保预分解窑系统的热工制度的合理与稳定。
要把预分解系统情况与窑头烧成带情况结合起来考虑,要提高快转率。
在操作上,要严防大起大落、顶火逼烧,要严禁跑生料或停窑烧。
3、监视窑和预分解系统的温度和压力变化、废气中O2和CO含量变化和全系统热工制度的变化。
要确保燃料的完全燃烧,减少黄心料。
尽量使熟料结粒细小均齐。
4、严格控制熟料fCaO含量低于1.5%,立升重波动范围在±50g/L以内。
5、在确保熟料产质量的前提下,保持适当的废气温度,缩小波动范围,降低燃料消耗。
6、确保烧成带窑皮完整坚固,厚薄均匀,坚固。
操作中要努力保护好窑衬,延长安全运转周期。
7、预分解窑的发热能力来源于两个热源,即窑头和分解炉,对物料的预烧主要由分解炉完成,熟料的烧结主要由回转窑来决定。
因此在操作中必须做到以炉为基础,前后兼顾,炉窑协调,确保预分解窑系统的热工制度的合理与稳定。
调节分解炉的喂煤量,控制分解炉出口温度在870~900度,确保炉内料气的温度范围,保证入窑生料的分解率。
影响煤粉充分燃烧的因素有几个方面:一是炉内的气体温度;二是炉内氧气量;三是煤粉细度。
预分解窑窑系统的操作体会
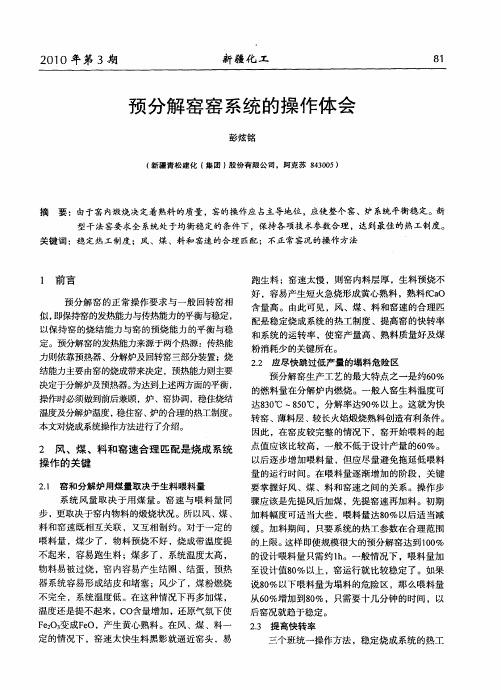
前结 圈不 高 时 ,一般 对窑 操作 影 响不 大 ,不
( )生料成 分 的均 匀性差 1
致使煤灰在窑尾大量沉降并产生还原气氛,就是由 于拉大排风使 窑内气流断面风速增加 , 火焰拉长 , 液相提前 出现 ,这都容易形成熟料圈 。
3 异 常 窑 况 的 分析 及 处 理
31 结 圈的处 理方法 .
31 前结圈的处理方法 .. 1
原料 的预均化 、配料 电子皮带秤 、出磨 生料X
关键词 :稳 定 热工制度 ;风 、煤 、料 和窑速 的合理 匹配 ;不正 常窑 况的操 作 方法
l 前 言
预分解窑的正 常操作要求与一般回转窑相 似, 即保持窑的发热能力与传热能力的平衡与稳定 , 以保持窑的烧结能力与窑的预烧能力的平衡与稳
定 。预分解 窑的发热能力来 源于两个热源 :传热 能 力则依靠 预热器 、分解炉及 回转窑三部分装置 ;烧 结能力 主要 由窑的烧成带来决定 ,预热能力则主要 决定 于分解炉及预热器 。 达到上述 两方 面的平衡 , 为 操作时必须 做到前后兼顾 ,炉 、窑协调 ,稳住烧结 温度及分解炉温度 , 稳住 窑、 的合理 的热工制度 。 炉 本文对烧成系统操作方法进行 了介绍 。
至设计值8%以上 ,窑运行就比较稳定了。如果 0
说8 %以下喂料量为塌料 的危险区,那么喂料量 0 从 6 %增加 到 8% ,只需 要 十几 分钟 的时 间 ,以 0 0
后 窑况就 趋于稳 定 。
23 提 高快 转率 .
三个班统一操作方法 ,稳定烧成系统 的热工
8 2
新疆 化 工
达80 一80 3℃ 5 ℃,分解率达9 %以上。这就为快 0 转 窑 、薄料 层 、较 长火焰煅 烧 熟料创 造有 利条 件 。
提高2500td新型干法窑熟料产量的措施
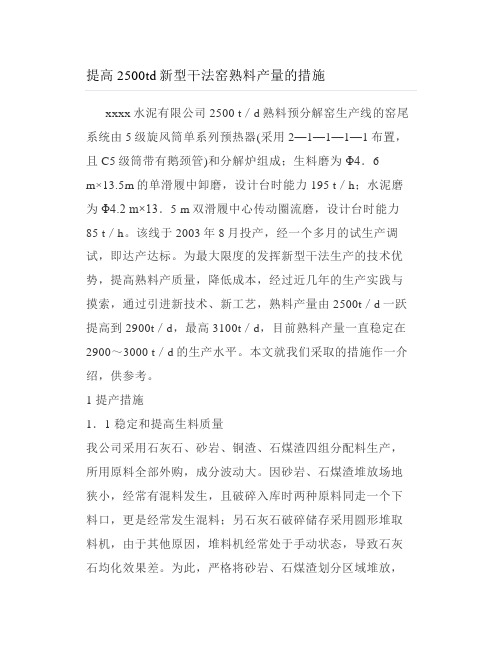
提高2500td新型干法窑熟料产量的措施xxxx水泥有限公司2500 t/d熟料预分解窑生产线的窑尾系统由5级旋风筒单系列预热器(采用2—1—1—1—1布置,且C5级筒带有鹅颈管)和分解炉组成;生料磨为Φ4.6m×13.5m的单滑履中卸磨,设计台时能力195 t/h;水泥磨为Φ4.2 m×13.5 m双滑履中心传动圈流磨,设计台时能力85 t/h。
该线于2003年8月投产,经一个多月的试生产调试,即达产达标。
为最大限度的发挥新型干法生产的技术优势,提高熟料产质量,降低成本,经过近几年的生产实践与摸索,通过引进新技术、新工艺,熟料产量由2500t/d一跃提高到2900t/d,最高3100t/d,目前熟料产量一直稳定在2900~3000 t/d的生产水平。
本文就我们采取的措施作一介绍,供参考。
1 提产措施1.1 稳定和提高生料质量我公司采用石灰石、砂岩、铜渣、石煤渣四组分配料生产,所用原料全部外购,成分波动大。
因砂岩、石煤渣堆放场地狭小,经常有混料发生,且破碎入库时两种原料同走一个下料口,更是经常发生混料;另石灰石破碎储存采用圆形堆取料机,由于其他原因,堆料机经常处于手动状态,导致石灰石均化效果差。
为此,严格将砂岩、石煤渣划分区域堆放,且控制堆放量并及时破碎后入各自的储存库,以最大程度避免了混料现象发生;同时,行车抓料堆放时采用抛撒堆料,堆取料机以自动状态堆料。
使石灰石均化效果更佳。
这样使原料质量得到控制,从而能稳定和提高入窑生料成分的波动。
1.2 控制原燃料中有害成分的含量原料、原煤中的有害成分,对预热器的结皮影响较大,尤其这些有害成分在回转窑—预热器的循环大量富集,形成硫钾钙石、灰硅钙石和硫硅钙石等低熔点易结皮的矿物质,加速窑尾上升烟道、分解炉及C4,C5级筒结皮过厚,影响系统通风,产量降低。
我公司曾经出现几次原煤中SO3含量过高[w(SO3)最高达到1.8%],造成预热分解系统结皮严重而堵塞。
2500td预分解窑熟料产质量的提高与稳定
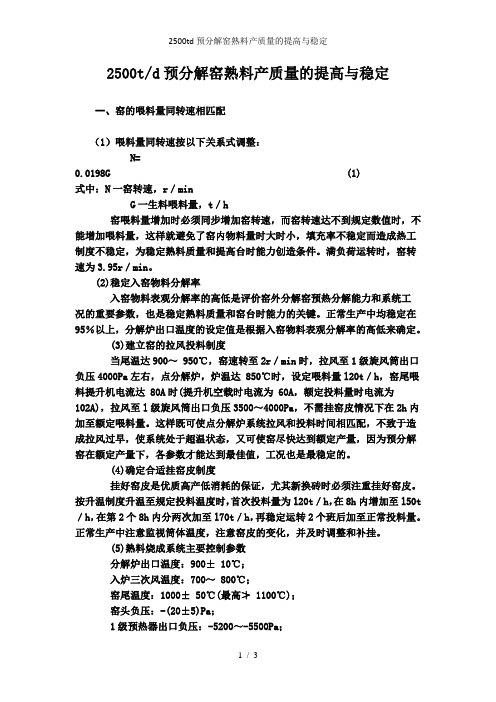
2500t/d预分解窑熟料产质量的提高与稳定一、窑的喂料量同转速相匹配(1)喂料量同转速按以下关系式调整:N=0.0198G (1)式中:N一窑转速,r/minG一生料喂料量,t/h窑喂料量增加时必须同步增加窑转速,而窑转速达不到规定数值时,不能增加喂料量,这样就避免了窑内物料量时大时小,填充率不稳定而造成热工制度不稳定,为稳定熟料质量和提高台时能力创造条件。
满负荷运转时,窑转速为3.95r/min。
(2)稳定入窑物料分解率入窑物料表观分解率的高低是评价窑外分解窑预热分解能力和系统工况的重要参数,也是稳定熟料质量和窑台时能力的关键。
正常生产中均稳定在95%以上,分解炉出口温度的设定值是根据入窑物料表观分解率的高低来确定。
(3)建立窑的拉风投料制度当尾温达900~ 950℃,窑速转至2r/min时,拉风至1级旋风筒出口负压4000Pa左右,点分解炉,炉温达 850℃时,设定喂料量l20t/h,窑尾喂料提升机电流达 80A时(提升机空载时电流为 60A,额定投料量时电流为102A),拉风至l级旋风筒出口负压3500~4000Pa,不需挂窑皮情况下在2h内加至额定喂料量。
这样既可使点分解炉系统拉风和投料时间相匹配,不致于造成拉风过早,使系统处于超温状态,又可使窑尽快达到额定产量,因为预分解窑在额定产量下,各参数才能达到最佳值,工况也是最稳定的。
(4)确定合适挂窑皮制度挂好窑皮是优质高产低消耗的保证,尤其新换砖时必须注重挂好窑皮。
按升温制度升温至规定投料温度时,首次投料量为l20t/h,在8h内增加至l50t /h,在第2个8h内分两次加至l70t/h,再稳定运转2个班后加至正常投料量。
正常生产中注意监视筒体温度,注意窑皮的变化,并及时调整和补挂。
(5)熟料烧成系统主要控制参数分解炉出口温度:900± 10℃;入炉三次风温度:700~ 800℃;窑尾温度:1000± 50℃(最高≯ 1100℃);窑头负压:-(20±5)Pa;1级预热器出口负压:-5200~-5500Pa;入窑物料分解率:>95%。
预分解窑操作体会

预分解窑操作体会1、看火操作的具体要求1)作为一名回转窑操作员首先要学会看火要看火焰形状、黑火头长短、火焰温度及是否顺畅有力要看熟料结粒、带料高度和翻滚情况以及后面来料的多少要看烧成带窑皮的平整度和厚度等2)操作预分解窑窑坚持前后兼顾要把预分解系统情况与窑头烧成带情况结合起来考虑要提高窑的快转率在操作上要严防大起大落、顶火逼烧要严禁跑生料或停窑烧3)监视窑和预分解系统的温度和压力变化、废气中O2和CO含量变化和全系统热工制度的变化要确保燃料的完全燃烧减少黄心料尽量使熟料结粒细小均齐4)严格控制熟料FCaO含量小于1.5℅立升重波动±50g/L以内5)在确保孰料产量的前提下保持适当的废气温度缩小波动范围降低燃料消耗6)确保烧成带窑皮平整厚薄均匀坚固操作中要努力保护好窑衬延长安全运转周期2、预热器系统的调整2.1撒料板的调节撒料板一般都置于旋风筒下料的底部经验告诉我们通过排灰阀的物料都是成团的一股一股的这种团状或股状物料气流不能带起而直接入旋风筒中造成短路撒料板的作用就是将团状或股状物料撒开是物料均匀分散地进入下一级旋风筒进口管道的气流中在预热器系统中气流与均匀分散物料间的传热主要在管道内进行的尽管预热器系统的结构形式有较大的差别但下面一组数据基本相同一般情况下旋风筒进出口气体温度之差在20℃左右出旋风筒的物料温度比出口气体温度低10℃左右这说明在旋风筒中的物料与气体的热交换是微乎其微的因此撒料板将物料散开程度的好坏决定了生料的受热面积的大小直接影响热交换效率撒料板的角度太小物料分散不好不好;反之板易被烧坏而且大股物料下塌时由于管路截面较小容易产生堵塞与此同时注意观察各级旋风筒进出口温度差直至调到最佳位置2.2排灰阀平衡杆角度及其配重的调整预热器系统中每级旋风筒的下料管都设有排灰阀一般情况下排灰阀摆动的频率越高进入下一级旋风筒进气管道中的物料越均匀气流短路的可能性就越小排灰阀摆动的灵活成都主要取决于排灰阀平衡杆的角度及其配重根据经验排灰平衡杆应在水平线一下并与水平线之间的夹角小于30度有人做过计算最好能调到15度左右因为这时平衡杆和配重的重心唯一变化很小而且翻版阀开度增大上述重心和阀板传动间距同时增大力矩增大阀板复位所需的时间缩短排灰阀摆动的灵活程度可以提高至于配重应在冷态时初期调到用手指轻轻一抬平衡杆就起来一松手就复位热态时只需随个别排灰阀作微量调整即可2.3压缩空气防堵吹扫装置吹扫时间的调整预热器系统中每级旋风筒根据其位置、内部温度和物料性能不同在锥体一般设有1~3圈压缩空气防堵吹扫装置空气压力一般控制在0.6~08MPA系统正常运行时由计算机定时进行自动吹扫吹扫时间可以根据需要人为设定一般为每隔20分钟左右整个系统自动轮流吹扫一遍每级旋风筒吹扫3~5秒当预热器系统压力波动较大或频繁塌料等异常情况时随时可以调整吹扫时间间隔甚至可以定在某一级旋风筒上进行较长时间的连续吹扫当然无异常时不应该采取这种吹扫方式因为吹入大量的冷空气将会破坏系统的正常的热工制度降低热效率增加热耗3、新窑第一次点火及挂窑皮期间的操作方法新窑耐火衬料烘干结束后一般可以继续升温进行投料运行但如果耐火衬料烘干过程中温度控制忽高忽低波动大升温速率太高则最好将火熄灭待冷却后进行系统内部检查如果发现耐火衬料大面积剥落则必须进行修补甚至更换3.1窑头点火升温3.1.1窑头点火现代化的预分解窑窑头都采用三通道或四通道燃烧器喷嘴中心都设有点火装置新窑第一次挂窑皮最好采用轻柴油点火因为这样点火有煤混合燃烧用煤量少煤粉燃尽率高如果用木材点火火焰温度低初期喷出的煤粉只有挥发分和部分固定碳燃烧煤粉中大部分固定碳未燃尽就在窑内沉降而且木材燃烧后留下大量木灰这些煤灰和木灰在高温作用下被烧熔粘挂耐火砖表面不利于粘挂永久、坚固、结实和稳定的窑皮窑头点火一般用油的面纱包邦在点火棒上点燃后置于喷嘴的下方随后喷油待窑内温度稍高一些后开始喷少量的煤粉待火焰稳定、棉纱包快燃尽时抽出点火棒以后随着用煤量的增加火焰的稳定程度提高逐渐减少轻柴油的喷入量直至全部取消在此期间窑尾温度应遵循升温曲线要求缓慢上升在RSP型分解炉上为使RSP型分解炉涡流分解室有足够的温度加速煤粉的燃烧窑头点火前应将2个C4旋风筒排灰阀杆吊起这样窑尾部分高温废气可以进入涡流分解室经排灰阀、下料管入C4旋风筒对涡流分解室起到预热升温的作用3.1.2升温曲线和转窑制度图1曲线表示系统从冷态点火升温到开始挂窑皮期间窑尾废气温度、C5出口温度以及不同温度段的转窑制度3.2投料挂窑皮当预热器丛分预热窑尾温度达950度左右这时分解炉涡流分解室可达650~700度窑头火砖开始发亮发白时早先喂入的几吨生料也即将进入烧成带这时窑头留火待料保持烧成带有足够的温度并将吊起的2个C4排灰阀复原三次风管阀门开至10℅左右打开涡流燃烧室和分解室阀门开始向涡流室喷轻柴油和少量的煤粉当C1出口温度达400~450度时打开置于C1出口至高温风机废气管道的冷风阀门掺入冷风调节废气温度保护高温风机待C5出口温度达900度时适当开达三次风管阀门即可下料喂料量为设计能力的30~40℅喂料后逐渐关闭冷风阀适当加大喂煤量和系统排风量窑以较低的转速(如0.3~06R/MIN)连续运转并开始挂窑皮当系统比较正常分解炉稳定后就可以撒除点火喷油嘴如果烧无烟煤则应适当延长点火喷嘴的使用时间但优良可以减少一对无烟煤起助燃作用挂好窑皮时延长烧成带火砖寿命提高回转窑运转率的重要环节其关键是掌握火候待生料到达烧成带及时调整燃料量和窑速确保稳定的烧成带温度窑速与喂料量相适应十粘挂的窑皮厚薄一致、平整、均匀、坚固挂窑皮期间严防烧成带稳定巨变温度太高挂上的窑皮易被烧垮生料易烧流在窑内推车会严重磨蚀耐火砖;温度降低会跑生料形成疏松夹心窑皮极易塌落影响窑皮质量挂窑皮时间一般为3~4个班窑皮挂到一定程度以后生料量可以3~5T/H的速度增加直至100℅的设计能力窑速和系统排风也随燃料和生料喂料量的增加而逐渐加大3.3冷却机的操作1)挂窑皮初期窑产量很低待熟料开始入冷却机时再启动蓖床但蓖速一定要慢使熟料在蓖床上均匀散开并保持一定的料层厚度2)以设定冷却风量为依据使蓖下压力接近设定职注意避免冷却机阀门开度太大否则吹穿料层造成短路3)运行中注意观察拉链机张紧情况并检查有无空气泄漏和串风现象漏风严重时可以暂时停拉链机使吉内积攒一定的细料以提高料封效果4)操作中如发现蓖板翘起或脱落要及时处理严防蓖板掉入熟料熟料破碎机造成严重的事故3.4三次风管阀门的调节1)分解炉点火时三次风温度很低因此打开电动高温蝶阀时宜小且缓慢以避免分解室温度骤降给点火带来困难2)投料后适当地调整涡流分解室顶部3个阀门的开度以满足他们所在位置管道阻力的差异当生料喂料量达到设计产量的80%左右时使总阀门开度达70~100%3.5系统的温度的控制从投料挂要皮到窑产量达设计能力之前烧成系统热耗一般都比较高因此系统温度可比正常值偏高控制:1)窑尾温度:1000~1050度;2)分解炉混合室出口温度:900度;3)c1出口废气温度:350~400度;3.6废气处理系统的操作1)系统投料之前一般增湿塔不喷水但出口废气温度≦250度以免损坏电收尘器的极板和壳体2)增湿塔投入运行后注意塔底窑灰水分严防湿底3)待烧成系统热工制度基本稳定后电除尘器才能投入运行并控制电除尘器入口废气CO含量在允许范围内4、窑皮的影响因素4.1生料化学成分所谓挂窑皮就是液相凝固到耐火砖表面的过程因此熟料烧成液相量的多少、液相量粘度的高低直接影响窑皮的形成而生料化学成分直接影响液相量及其粘度以前湿法窑人们主张挂窑皮期间的生料N值是当地偏低一些而KH饱和适当偏高一些但对于预分解窑目前窑头使用三风道或四风道燃烧器回转窑正常时一次风量少二次风温度有很高因此煤粉燃烧速度、火焰温度远高于湿法窑如果降低N值液相量相应增加物料容易烧流挂上的窑皮不吃火容易脱落所以都主张挂窑皮的生料应与正常生料成分相同为好4.2烧成温度和火焰的控制挂好烧成带窑皮的主要因素除有一定的液相量和液相粘度以外还要有适当的温度气流、物料和耐火砖之间要有一定的温差一般控制在正常生产时的烧成温度掌握熟料结粒细小均齐不烧大块更不能烧流严禁跑生料升重控制在正常生产指标内要保持烧成带温度稳定、窑速稳定、火焰形状完整、顺畅这样挂出的窑皮厚薄一致、平整、均匀、坚固4.3喂料量和窑速为了使窑皮挂的坚固、均匀、平整温度窑内热工制度是先决条件挂窑皮期间稳定的喂料量和稳定的窑速是至关重要的喂料量过多或窑速过快窑内温度就不容易。
日产2500td熟料生产线增产到3000td操作体会
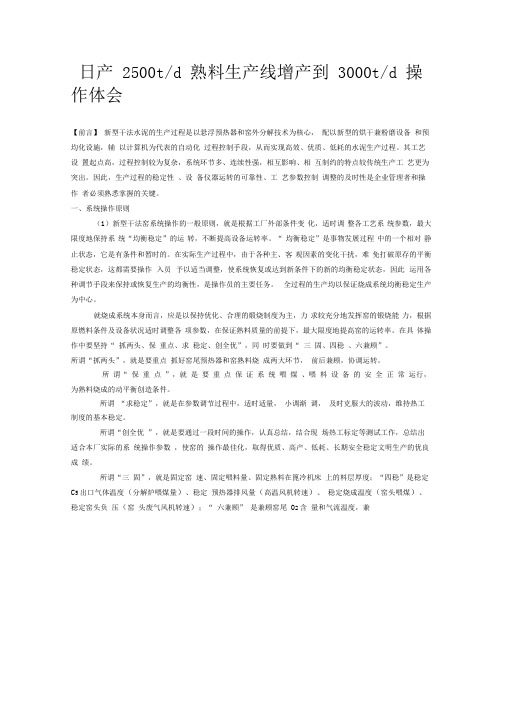
日产2500t/d 熟料生产线增产到3000t/d 操作体会【前言】新型干法水泥的生产过程是以悬浮预热器和窑外分解技术为核心,配以新型的烘干兼粉磨设备和预均化设施,辅以计算机为代表的自动化过程控制手段,从而实现高效、优质、低耗的水泥生产过程。
其工艺设置起点高,过程控制较为复杂,系统环节多、连续性强,相互影响、相互制约的特点较传统生产工艺更为突出。
因此,生产过程的稳定性、设备仪器运转的可靠性、工艺参数控制调整的及时性是企业管理者和操作者必须熟悉掌握的关键。
一、系统操作原则(1)新型干法窑系统操作的一般原则,就是根据工厂外部条件变化,适时调整各工艺系统参数,最大限度地保持系统“均衡稳定”的运转,不断提高设备运转率。
“ 均衡稳定”是事物发展过程中的一个相对静止状态,它是有条件和暂时的。
在实际生产过程中,由于各种主、客观因素的变化干扰,难免打破原存的平衡稳定状态,这都需要操作入员予以适当调整,使系统恢复或达到新条件下的新的均衡稳定状态,因此运用各种调节手段来保持或恢复生产的均衡性,是操作员的主要任务。
全过程的生产均以保证烧成系统均衡稳定生产为中心。
就烧成系统本身而言,应是以保持优化、合理的煅烧制度为主,力求较充分地发挥窑的锻烧能力,根据原燃料条件及设备状况适时调整各项参数,在保证熟料质量的前提下,最大限度地提高窑的运转率。
在具体操作中要坚持“ 抓两头、保重点、求稳定、创全优”,同时要做到“ 三固、四稳、六兼顾”。
所谓“抓两头”,就是要重点抓好窑尾预热器和窑熟料烧成两大环节,前后兼顾,协调运转。
所谓“ 保重点”,就是要重点保证系统喂煤、喂料设备的安全正常运行,为熟料烧成的动平衡创造条件。
所谓“求稳定”,就是在参数调节过程中,适时适量,小调渐调,及时克服大的波动,维持热工制度的基本稳定。
所谓“创全优”,就是要通过一段时间的操作,认真总结,结合现场热工标定等测试工作,总结出适合本厂实际的系统操作参数,使窑的操作最佳化,取得优质、高产、低耗、长期安全稳定文明生产的优良成绩。
- 1、下载文档前请自行甄别文档内容的完整性,平台不提供额外的编辑、内容补充、找答案等附加服务。
- 2、"仅部分预览"的文档,不可在线预览部分如存在完整性等问题,可反馈申请退款(可完整预览的文档不适用该条件!)。
- 3、如文档侵犯您的权益,请联系客服反馈,我们会尽快为您处理(人工客服工作时间:9:00-18:30)。
2500t/d预分解窑操作体会2009-4-7 作者:1薄料快烧薄料快烧能够充分利用刚分解生成的新生态CaO具有的高活化能,而且能改善水泥熟料中硅酸盐矿物的结晶形态,提高熟料矿物的水化活性和熟料强度。
窑速越快,物料被扬起越高,窑内物料与热气流接触越好,传热效率越高;窑速越快,料与料、料与窑衬温差小,这样料与料的粘结也会少,不容易结圈、结球、挂长窑皮的现象;窑速越快,托轮与轮带间形成的油膜越均匀,润滑效果越好,延长托轮和轮带寿命。
另一方面,因为薄料快烧使得窑内热气流动快,热耗偏高,要提高窑头火焰的热力强度,保证烧成带有足够的烧成温度。
但是,并不是窑速越快越好,否则吨熟料煤耗将大大增加。
2满负荷生产作为预分解技术核心设备的分解炉,其主要功能是完成炉内煤粉燃烧及生料分解率达到85%-95%。
满负荷生产风、煤、料达到最佳匹配,有利于分解炉燃烧反应及分解反应的稳定进行,提高效益,降低吨熟料煤耗、电耗。
在操作上,较大的喂料量,较大的总风量,可以提高窑内氧含量,提高二次风温,使火焰强劲有力,有利于煤粉完全燃烧,避免煤粉在窑尾烟室燃烧的现象,防止液相提前出现,减少过渡带结圈、窑内结球,保证窑的正常煅烧。
满负合生产有利于提高流体的固气比。
固气比提高后,由于离心力的作用,物料间凝聚力增加,因而旋风筒的分离效率亦会提高,有利于热量的吸收。
3确保火焰合适的行状和热力强度烧成控制的重点是掌握好火焰的行状和热力强度。
在三通道燃烧器的操作过程中,应结合煤质、窑皮情况、窑负荷曲线(电流、功率曲线)、入窑生料三率值等因素的变化,合理调节燃烧器的内流风、外流风,以及燃烧器的斜度及其入窑的深度,确保火焰的合适行状和热力强度。
正常情况下火焰白亮、顺畅,熟料结粒均齐、合适,窑口无飞砂。
有时可看到飞砂料被强力抽进窑口的情形,说明火焰顺畅,通风良好,但烧成带温度较低,应适当增加窑头煤,降低一段篦速,增加料层厚度,提高二次风温。
同时应结合窑尾温度、窑负荷功率曲线等参数综合分析处理。
有时,过渡带结圈、烟室斜坡积料、分解炉下缩口及窑内掉大窑皮,出大球都可能导致窑内通风不良,火焰飘散无力,窑口飞砂严重,有黄心料等现象。
要针对不同的情况,采取相应的措施处理:1.3.1.过渡带结圈:通过减少内流风(内流风开到3~4即可)拉长火焰扫厚窑皮,间隔2~3h交替拉出、推进燃烧器(幅度300~500mm),通过冷热交替使厚窑皮烧掉。
烟室斜坡积料及分解炉下缩口结皮:通过提高窑速,减少窑头喂煤,关小三次风阀,增加窑内通风。
频繁出大球:通过提高窑速,减少窑头喂煤,使火焰偏离物料。
1.4以炉为基础,前后兼顾,炉窑协调,确保预分解窑系统的热工制度的合理与稳定。
预分解窑的发热能力来源于两个热源,即窑头和分解炉,对物料的预烧主要由分解炉完成,熟料的烧结主要由回转窑来决定。
因此在操作中必须做到以炉为基础,前后兼顾,炉窑协调,确保预分解窑系统的热工制度的合理与稳定。
调节分解炉的喂煤量,控制分解炉出口温度在850~900度,确保炉内料气的温度范围,保证入窑生料的分解率。
影响煤粉充分燃烧的因素有几个方面:一是炉内的气体温度;二是炉内氧气量;三是煤粉细度。
因此,一要提高燃烧的温度;二要保证炉内的风量;三要控制煤粉的细度。
在燃烧完全的条件下,通过分解炉加减煤的操作,控制分解炉出口气体温度。
如果加媒过量,分解炉内燃烧不完全,煤粉就会带入C5燃烧,形成局部高温,使物料发粘,积在锥部,到一定成都造成下料管堵塞。
相反,如果加煤过少,分解用热不够,导致分解炉此刻气温下降,分解率低,导致窑热负荷增加,熟料质量下降。
在具体操作中,要避免上述两种情况,要对不同的情况进行具体分析。
1.4.2.合理调节窑头的喂煤量:窑头喂煤量是否合理,可以通过观察窑头火焰情况和分解炉出口温度的稳定性。
如果窑头喂煤偏少,窑口发暗,火焰发红,分解炉出口温度不稳定,凤姐来喂煤量频繁加、减;如果窑头喂煤过多,窑口火焰白亮,分解炉出口温度不稳定,分解炉喂煤量不稳定,这种情况也不利于操作。
出现以上两种情况要及时对窑头用煤量进行调整,但不能大幅度调,要进行微调,达到火焰顺畅、窑口无飞砂、分解炉出口温度稳定易调整,操作上感到轻松自如。
1.5在操作过程中要做到:三固、四稳、六兼顾的原则。
三固:固定窑速,固定喂料量,固定一段篦床上的料层厚度。
四稳:稳定分解炉出口温度,稳定系统用风量,稳定烧成温度,稳定窑头负压。
六兼顾:兼顾C1出口气体温度负压,各级锥体负压变化,二、三次风温度,筒体表面温度,窑头收尘系统,废气处理系统。
点火升温、投料及止料操作中应做到:预分解窑的操作,点火升温、投料、止料在操作中使十分重要的过程。
合理的系统预热升温室成功投料的基础,投料的成功与否直接影响着熟料的质量和设备的运转率以及窑衬的使用寿命,因此,一名窑操作员不仅要有过硬的专业技术,同时要有高度的责任心。
2.1点火升温升温室投料的前期准备,保证投料时窑、炉、预热器的合理温度,为投料创造条件。
点火时,一次风量减到最少,点火烟囱帽开到10~20%,火点着后,逐渐加大一次风量,以不吹灭火焰为准,控制窑头保持微负压,使窑口在短时间内温度升起,待火焰稍亮后,启动喂煤风机,如果火焰不被吹灭,说明窑头可以用煤升温,一次风量加到正常风量,窑头喂煤量要大幅度的增加,尽快提高窑前的温度,逐渐减少回油压力,减少用油量,降低成本。
用煤升温后,烟囱帽开赌逐渐加大,控制烟室微负压,使火焰往后移,对窑后半部进行升温预热,此时起动高温风机(起动高温风机前废气处理系统已全部启动),液力偶合器给定0%,入口阀门开度给定0%,当烟室温度升到500℃后,逐渐打开高温风机入口阀门,逐渐关小烟囱帽,通过废气处理拉风,对分解炉、预热器进行升温。
在烟室温度500℃以前,窑按每30min 转1/4转,烟室温度在500~800℃,窑连续打辅转,此时,启动窑头、窑尾所有设备,篦冷机风机入口阀门开到50%,三次风阀开到30~50%,800℃时脱开辅传用主传转窑。
升温中,要合理控制升温速率,坚持“升温不回头”得原则,保证对窑、分解炉、预热器三部分的升温预热。
投料前,通知岗位人员检查预热器、活动翻板阀;确认各级下料管畅通,翻板阀活动灵活。
为成功投料打下坚实基础。
2.2投料操作当烟室温度升到950℃时。
窑头喂煤量给定到正常喂煤量,窑速要求大于1.5rpm,液力偶合器开度一次给定到75%,烟囱帽关到0%,开始喂料、窑尾喂煤。
由于刚投料,预热器、分解炉内各斜坡有积料积煤灰以及翻板阀的阻挡,如果初始投料量过小,第一股料的冲击力达不到预热器、分解炉内各斜坡的积煤及翻板阀的阻力,及易出现预热器堵料现象。
为保证预热器不出现堵塞又要保证质量不出现窜生料,因此,初始投料量应做到:一、初始投料量应超过设计初始投料量的20~30t/h,保证第一股料有足够的冲击力;二、当确认第一股料一但进入窑尾,立即减少投料量,减到设计的初始投料量。
在投料过程中,以“万变为不变”,任其参数的变化,但必须严格控制分解炉出口温度在850~900℃范围内。
当投料超过20min,窑功率曲线开始出现往上升趋势时,表明料已经进入烧成带。
如果窑功率超过50kw,说明投料顺利成功;如果窑功率低于50kw,且经过1—2min窑功率急速下滑,说明窑内马上要窜出生料,此时立即采取果断措施大幅度减窑速,适当增加窑头喂煤,防止窑内跑生料。
投料顺利成功后,要在最短时间内投料量达到最高产量,提高效益。
对于多次升温,因故不能投料的情况,窑操作员要及时通知现场注意烧成带的筒体温度,严防窑内局部高温,烧坏烧成带窑皮,影响烧成带窑衬得使用寿命。
投料正常后,在保证窑系统热工制度合理稳定的情况下,控制分解炉出口温度不高于900℃,稳定投料量、风量、窑速、篦速,逐步微调,优化操作,提高质量,降低吨熟料煤耗、电耗,实现效益。
2.3窑系统止料操作止料操作相对投料操作较简单,但对窑系统运转率也具有同样重要的意义。
止料操作过程中,也容易出现预热器堵塞现象或进高温风机气体稳定过高,对设备不利。
因此,止料操作必须做到:先止分解炉喂煤,待分解炉出口温度降到800℃时,止料、逐渐减少窑头喂煤、降低窑速,不要过早打开烟囱帽,保持高温风机拉风,待预热器料全部走完,最后一股料完全进窑后,降高温风机转速,减少拉风,打开烟囱帽。
逐步减少窑头喂煤量,降低窑速,待窑内物料适度倒空时,脱开主传连续辅转,止窑头煤。
3.化验室检测结果在操作上的指导作用操作中,化验室提供数据对操作起到重要作用。
操作员应及时了解检测结果,根据情况对系统有预见性,不穿总结操作经验。
3.1我厂由于矿山质量不稳、MgO含量高,对窑系统的操作增加科难度。
因此,操作员应及时了解矿山的情况,如果MgO含量高,分解炉出口温度控制应适当偏低,防止预热器堵塞。
因为MgCO3在400℃开始出现分解,而CaCO3在600℃开始出现分解,如果MgCO3含量高,五级旋风筒出现过多液相,极易造成堵塞,导致停窑。
3.2煤粉的变化在操作中应及时进行调整。
如果煤粉细度细、灰份低、发热量高煤质好,喷煤管内风适度关小,拉长火焰,熟料台时产量可以提高6~10t/h;相反,煤粉细度粗、灰份高、发热量煤质差,喷煤管内风适度开大,缩短火焰,进行短焰急烧,窑头喂煤适当加大。
3.3出磨、入窑生料三率值的变化对窑的操作具有预见性,生料三率值高,料耐烧性强,窑头用煤量要增加,分解炉出口温度适当控制偏高;反之,窑头用煤量要减少,分解炉出口温度适当控制偏低,防止预热器堵塞现象。
4.根据生料磨运行情况及均化库料位在操作中的指导作用在实际生产中,生料经常出现长时间停磨,导致均化库料位较低现象。
操作中,如果生料磨停车出现超过4h以上时,分解炉出口温度应控制比平时低5~10度,窑速控制比平时快0.1~0.3rpm。
因为均化库回灰量增多,生料灰份高,均化库均化效果差,防止预热器堵塞现象;生料灰份高,容易提前出现液相,窑内易结料球,通过提高窑速避免结料球,在出现结球前倒出窑外。