第4章 加工精度
精密加工第4章 电化学加工

3)电极极化
平衡电极电位是没有电流通过电极时的情况, 当有电流通过时,电极的平衡状态遭到破坏,使阳极 的电极电位向正移(代数值增大),阴极的电极电位 向负移(代数值减小),这种电极电位偏离了无电流 通过电极的电极电位情况称为电极极化. 极化后的电极电位与平衡电位的差值称为超电位 (过电位). i
1 2 电极极化曲线 -V 电位 +V i-电流密度;1-阴极;2-阳极
据电化学加工原理,可将电化学加工分为三类:
利用阳极溶解
电解:通过电化学反应从工件表面去除金属. 电解抛光:通过电化学反应从工件表面去除金属毛刺.
利用阴极上的沉积作用
电镀:在工件表面沉积金属:材料表面装饰保护.
电铸:在阴极上沉积实现附着加工. 电刷镀:
复合电镀:
复合加工
Fe+2 + 2e
Fe (沉积,还原反应)
随着金属表面负电荷的增多,溶液中Fe+2 返回金 属表面的速度逐渐增加。最后,这两种相反的过 程达到动态平衡。
对于化学性能比较活泼的金属(如铁),其表面 带负电,溶液带正电,形成一层极薄的“双电 层”,金属越活泼,这种倾向越大。
活泼金属的双电层
不活泼金属的双电层
电解磨削:
各种电化学方法的比较
工艺名称 电解加工 电解磨削 电铸加工 电镀与 电刷度
电化学 电化学 电化学 电化学 去除加工 去除加工 附着加工 附着加工 加工原理 机械磨削 阴极沉积 阴极沉积 作用 阳极溶解 剥取沉积 附着在表 电解作用 层 面
电化学方法与传统加工方法相比所具有的特点:
① 可对任何硬度、强度、韧性的金属材料进行加工,加工 难加工材料时,其优点更为突出。 ② 加工过程中不存在机械切削力和切削热作用,故加工后 表面无残余应力和冷硬层,也无毛刺 、棱边,表面质量 好。 ③ 大面积上可同时进行加工,也无需粗精分开,故一般具 有较高的生产率。 ④ 加工过程监测与自动控制、工具的准确设计、加工精度 的提高,以及电化学作用的产物(气体或废液)的处理 等都是亟待解决的问题。
加工精度
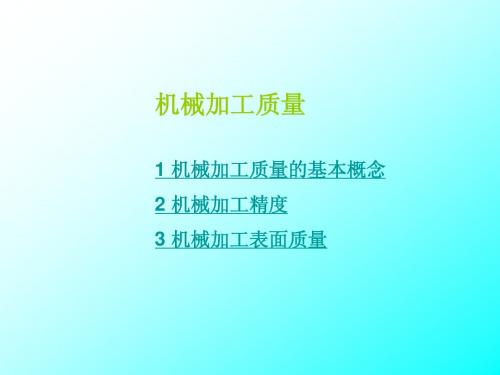
返回本章目录
工件回转(车削)的情况: ①工件回转在1处: R1 = R - A ②工件回转在2处: R2 = R ③工件回转在3处: R3 = R + A ④工件回转在4处: R4 = R D1-3= R1+R2=2R D2-4= 2R = D1-3
返回本章目录
工件孔轴心线
α
主轴回转轴心线
主要影响工件的形状精度
垂直误差
两者比较
R y 400Rz
结论:普通机床导轨水平误差比垂直误差对加 工误差影响大得多。(此例两者相差400倍)
返回本章目录
误差敏感方向— 对加工误差影响大的加工表面的法线方向。 平面磨床误差敏感方向为
导轨垂直误差。
返回本章目录
2)主轴误差
主轴回转误差
—主轴实际回转中心的瞬时位置 与理想位置的最大偏差。 一般把主轴误差分解为三种独立运动形式: ①纯轴向窜动△x ②纯径向移动△r ③纯角度摆动△α
机械加工质量
1 机械加工质量的基本概念 2 机械加工精度 3 机械加工表面质量
机械加工质量
1 机械加工质量的基本概念
机器零件的加工质量决定了机器的: 1.性能 2.质量 3.寿命 机器产品加工质量的内容: 1.加工精度 2.加工表面质量
返回本章目录
机器产品加工质量要求越来越高(近30年) 加工精度 (普通)从0.01mm →0.005mm (精密)从1μm → 0.02μm (超精密)从0.1μm →0.001μm 加工表面质量粗糙度方面已获得小于 0.0005μ m的粗糙度。 加工质量与设备、工艺方法、工艺措施有关。
返回本章目录
(4)工艺系统受力变形 工艺系统在加工过程中受: ①切削力; ②惯性力; ③重力; ④夹紧力 力作用→产生工艺系统变形→加工误差
第4章 4.3 加工误差的统计分析

x 有无常值系统误差——工件尺寸算术平均值 是否 与公差带中心重合; 有无废品?是尺寸过大废品,还是尺寸过小废品?是
可以修复的废品,还是不可修复的废品?
2020/6/2
.
24
可修复废品与不可修复废品
轴:不可修复废品
Q 过小
Δ0
xL
Tm
T min
T
镗孔:不可修复废品
Q 过大
xU T max
(如刀具磨损)以及其
0
它因素的影响,至少应使 T6。从上图分析可
知,保证加工系统不出废品的充分、必要条件是:
T2 (3 0)6 2 0
动画演示 7.28
无常值误差时的情形
当 0 XTM 0 时,过大废品、过小废品相等(如图
所示)。
Q合格 2F(z)2
1
2
z z2
e 2dz
0
式中: zxx T/2
2
( x , 0 )
式中,x —— 零件尺寸;
x —— 零件尺寸的算术平均值;
1 n
x n i1 xi ,它表示加工尺寸的分布中心;
y ——零件尺寸为 x 的概率密度;
—— 一批零件的均方根差,表示这批零件加工尺
寸的分布范围。
n
xi
x2 / n
i1
式中,n —— 一批零件的数量。
当 xx3 时,面积A 0 . 9 9 7 3 9 9 . 7 3 % 仅有
0.27%的计算误差。故可近似认为:在 3(或 6 )的
工件尺寸实际分散范围内,代表了100% 全部的零件。
6σ原则
6σ表示这批零件的随机误差的大小和工序精度的高低。 即:若能计算出一批零件的均方根误差σ,则该批零件的随 机误差就是6σ。
机加工第四章孔加工

六、拉削(P73)
拉削是一种高生产率的加工方法。加工精度可达IT7, Ra值可达0.8~0.4mm。 拉刀是一种多齿刀具。拉削时,由于后一个刀齿直径 大于前一个刀齿直径,从而能够一层层从工件上切出 金属。拉削过程如P74图4-19所示。 拉削视频 外拉削视频
圆孔拉刀的组成部分及作用(P73)
头部L1:用来将拉刀夹持在机床上并传递动力; 颈部L2:直径最小,拉力过大时在此部位发生断裂; 过渡锥L3:使拉刀容易进入工件的孔中; 前导部分L4:起引导作用,使工件轴线和拉孔轴线重 合; 切削部分L5:承担主要的切削任务; 校准部分L6:没有齿升量,起刮光孔壁和校正孔径作 用; 后导部分L7:保证拉刀最后一齿与工件间的正确位置。 拉孔刀视频
确定孔的加工方案的原则:首选满足技术要求,同时 考虑经济性和生产率等方面的因素。 拟定孔的加工方案比外圆表面复杂,这是因为: 1)孔的类型很多,功用不同,孔径和孔径比及技术要 求相关甚远; 2)孔的加工方法很多,且每一种加工都有一定的局限 性; 3)带孔零件的结构和尺寸多种多样。
一、机床的选用(P77)
铰削加工视频
2、铰削的特点(P70)
1)较高的精度和较低的Ra值:主要是刀具、加余量及切 削条件所致。 2)铰孔纠正位置误差的能力很差; 3)适应小孔和深孔的加工,Φ80mm以上的孔径不宜铰削 加工; 4)铰削的适应性较差:不能加工阶梯孔、短孔,且是定 径刀具。 5)可加工钢、铸铁和有色金属件,但不宜加工淬火件和 硬度较高的材料 。
二、孔的分类(P65)
根据孔的结构和用途,可分为以下几种类型:(如 P65图4-1和图4-2所示) 1、紧固孔和辅助孔:IT12~IT11;Ra值12.5~6.3um。 2、回转体零件的轴心孔:一般是与轴类零件相配合的表 面或是其它表面的基准面。对精度要求很高。 3、箱体支架类零件的轴承孔:孔本身尺寸精度及Ra值均 要求很高;孔与孔、孔与基准面之间也有很高的位置 精度要求。
第三版机械制造工艺学第四章习题解答

机械制造工艺学部分习题解答4第四章:机械加工精度及其控制(第3版P226-228)4-1车床床身导轨在垂直平面内及水平面内的直线度对车削圆轴类零件的加工误差有何影响?影响程度各有何不同?答:导轨在垂直平面内的直线度引起的加工误差发生在被加工表面的切线方向上,是非敏感误差方向,对零件的加工精度影响小;导轨在水平面内的直线度引起的加工误差发生在加工表面的法线上是误差敏感方向,对加工精度影响大。
4-2试分析滚动轴承的外环内滚道及内环外滚道的形状误差(如图4-87题4-2图)所引起的主轴回转轴线的运动误差,对被加工零件精度有什么影响?答:轴承内外圈滚道的圆度误差和波度对回转精度影响,对工件回转类机床,滚动轴承内圈滚道圆度对回转精度的影响较大,主轴每回转一周,径向圆跳动两次。
对刀具回转类机床,外圈滚道对主轴影响较大,主轴每回转一周,径向圆跳动一次。
4-3试分析在车床上加工时,产生下述误差的原因:1)在车床上镗孔,引起被加工孔圆度误差和圆柱度误差;2)在车床三爪自定心卡盘上镗孔,引起内孔与外圆同轴度误差;端面与外圆的垂直度误差。
答:1)在车床上镗孔,引起加工孔的圆度误差是主轴圆跳动、刀杆刚度不足,圆柱度误差是车床导轨在水平面和垂直面的直线度误差。
2)在车床三爪卡盘上镗孔,工件同轴度误差原因可能是工件装夹误差、主轴圆跳动;端面垂直度误差原因是主轴轴向圆跳动(轴向窜动)。
4-4在车床两顶尖装夹工件车削细长轴时,出现4-88a,b,c,所示误差原因是什么?可以用什么方法来减少或消除?答:a)是属于工件在切削力的做用下发生变形(工件刚度不足),可以通过改变刀具的角度来减少径向切削分力、或者加装中心架或者跟刀架来减少变形。
b)是机床受力变形所致(机床主轴和尾座的刚度不足),可以通过提高机床各部件的刚度来改变。
c)由刀具磨损引起,可以采用耐磨刀具来切削,或较少单次切削深度来提高刀具耐磨性。
4-5试分析在转塔车床上将车刀垂直安装加工外圆(图4-89)时,影响直径误差的因素中,导轨在垂直面内和水平面内的弯曲,哪个影响大?与卧式车床比较有什么不同?为什么?答:如图4-89所示转塔车床的刀具安装在垂直面内,由于垂直面为误差敏感方向,所以导轨垂直面内的弯曲对工件直径误差影响较大。
第四章第3节-定位误差分析
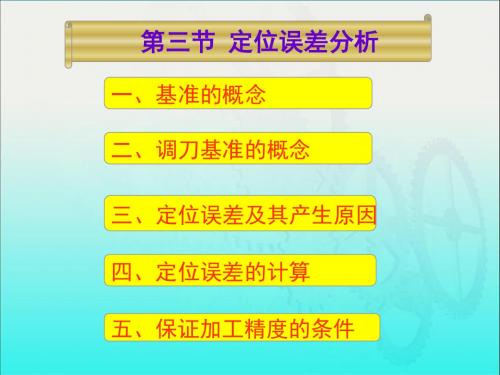
通过以上计算,可得出如下结论: ⑴即定位误差随工件误差的增大而增大; ⑵与V形块夹角 ą有关,随ą增大而减小,但 定位稳定性变差,故一般取ą =90゜;
⑶∆dw与工序尺寸标注方式有关,本例中∆dw1
> ∆dw3 > ∆dw2 。
三.保证加工精度的条件
采用夹具加工时的误差计算不等式:
分析: 1)对轴线尺寸l,定位基准和设计 基准为左端面,调刀基准为心轴 台阶端面,三者重合, △dw1=0
2)对槽深尺寸H,设计基准为外圆 的下母线,定位基准为内孔轴线, 定位基准和设计基准不重合,其联系尺寸为外圆半径和外圆轴线与内孔轴线的同 轴度误差T(e),与H的方向相同, △jb2=0.016/2+0.015=0.023mm 又工件内孔为定位基准,定位心轴轴线为调刀基准,内孔与心轴为间隙配合,因 调整螺母时心轴和内孔在任意边接触,此时: △jw2=△D+△d+△=0.021+0.013+0.007=0.041mm 因此,△dw2=△jb2+△jw2=0.064mm>0.10/3,定位不合理
(1)要求保证上 母线到加工面
的尺寸,即设
计基准为B:
尺寸H1的定位误差为:
d 1 dw1 1 2 sin 2
d1
_____ _____ _____ _____ B1 B2 AB2 AB1 AO2 O2 B2 AO1 O1 B1 d d d d d d 1 2 2 1 1 2 1 1 2 2sin 2 2sin 2 sin 2 2 2
由上面的分析可知: 设计基准和定位基 准都体现在工件上, 而调刀基准却是由 夹具定位元件的定 位工作面来体现。
机械制造技术基础_重点
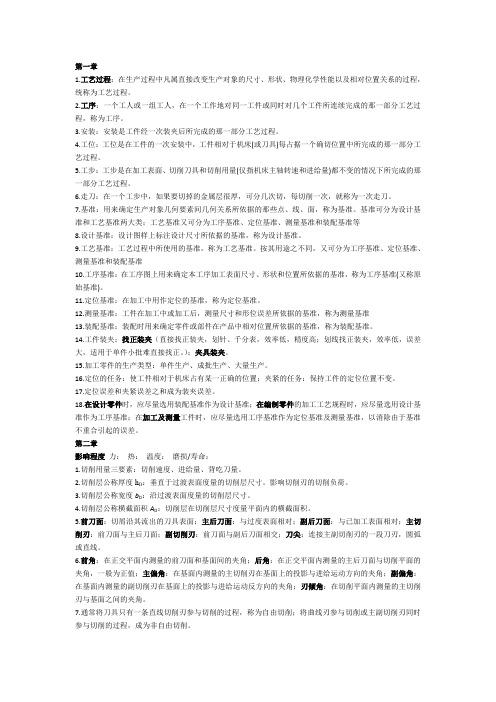
第一章1.工艺过程:在生产过程中凡属直接改变生产对象的尺寸、形状、物理化学性能以及相对位置关系的过程,统称为工艺过程。
2.工序:一个工人或一组工人,在一个工作地对同一工件或同时对几个工件所连续完成的那一部分工艺过程,称为工序。
3.安装:安装是工件经一次装夹后所完成的那一部分工艺过程。
4.工位:工位是在工件的一次安装中,工件相对于机床(或刀具)每占据一个确切位置中所完成的那一部分工艺过程。
5.工步:工步是在加工表面、切削刀具和切削用量(仅指机床主轴转速和进给量)都不变的情况下所完成的那一部分工艺过程。
6.走刀:在一个工步中,如果要切掉的金属层很厚,可分几次切,每切削一次,就称为一次走刀。
7.基准:用来确定生产对象几何要素间几何关系所依据的那些点、线、面,称为基准。
基准可分为设计基准和工艺基准两大类;工艺基准又可分为工序基准、定位基准、测量基准和装配基准等8.设计基准:设计图样上标注设计尺寸所依据的基准,称为设计基准。
9.工艺基准:工艺过程中所使用的基准,称为工艺基准。
按其用途之不同,又可分为工序基准、定位基准、测量基准和装配基准10.工序基准:在工序图上用来确定本工序加工表面尺寸、形状和位置所依据的基准,称为工序基准(又称原始基准)。
11.定位基准:在加工中用作定位的基准,称为定位基准。
12.测量基准:工件在加工中或加工后,测量尺寸和形位误差所依据的基准,称为测量基准13.装配基准:装配时用来确定零件或部件在产品中相对位置所依据的基准,称为装配基准。
14.工件装夹:找正装夹(直接找正装夹,划针、千分表,效率低,精度高;划线找正装夹,效率低,误差大,适用于单件小批难直接找正。
);夹具装夹。
15.加工零件的生产类型:单件生产、成批生产、大量生产。
16.定位的任务:使工件相对于机床占有某一正确的位置;夹紧的任务:保持工件的定位位置不变。
17.定位误差和夹紧误差之和成为装夹误差。
18.在设计零件时,应尽量选用装配基准作为设计基准;在编制零件的加工工艺规程时,应尽量选用设计基准作为工序基准;在加工及测量工件时,应尽量选用工序基准作为定位基准及测量基准,以消除由于基准不重合引起的误差。
04精密加工和特种加工

抛光特点:
①方法简便、经济,不用特殊设备;
②容易对曲面进行加工;
③只能提高粗糙度,不能改变零件的尺寸精度、形状精度或位置精度;
④劳动条件差。
抛光应用: 抛光主要用于零件表面的装饰加工,或者利用抛光方法去除前道工序的加工
痕迹,提高零件的疲劳强度。
抛光零件表面的形状可以是平面、外圆、孔、以及各种成形表面等。 五、各种精密加工方法的比较:
用装有细磨粒、低硬度的油石磨头,在一定压力下 对工件表面进行光整加工的方法称为超级光磨 。
• 加工时工件旋转,油石以恒力轻压于工件表面, 在作轴向进给的同时作轴向微小振动,从而达到 对工件微观不平的表面进行光磨的效果。
超级光磨的特点 : ①加工余量极少,一般为3 ~ 10μm; ②生产率较高,一般加工时间只需30~60秒; ③表面质量好,Ra<0.012μm; ④设备简单,操作方便。 但是,超级光磨只能提高表面质量,不能提高尺寸精度和形位精度。
第二节 特种加工
特种加工是相对于传统的切削加工而言,传统的切削加工是用刀具靠机械 能去除工件表面的多余材料。当工件材料的强度、硬度、脆性、韧性过高, 或零件的结构过于复杂,或尺寸太小,或零件的刚度较差时,传统的切削加 工方法就难于实现。特种加工就是为解决这些难题而发展起来的一种新的加 工方法.
特种加工是直接利用电能、光能、声能、热能、化学能或多种能量复合形 式进行加工的方法。常用的特种加工有电火花加工、电解加工、超声波加工、 激光加工、电子束加工和离子束加工等。
精度为3~O.3 μm,粗糙度为O.3~O·03μm的叫精密加工;
精度为0.3~0.03 μm,粗糙度为0.03~0.005 μm的叫超精密加工,或亚微米 加工;
精度为0.03 μm(30纳米),粗糙度优于0.005 μm以上的则称为纳米(nm)加工。
- 1、下载文档前请自行甄别文档内容的完整性,平台不提供额外的编辑、内容补充、找答案等附加服务。
- 2、"仅部分预览"的文档,不可在线预览部分如存在完整性等问题,可反馈申请退款(可完整预览的文档不适用该条件!)。
- 3、如文档侵犯您的权益,请联系客服反馈,我们会尽快为您处理(人工客服工作时间:9:00-18:30)。
φ10 F7 k6
Z
φ6F7
g6
Y
图4-19 钻径向孔的夹具
21
4.2.4 调整误差
试切法(图4-20 a) )
测量误差。 测量误差。 试切时与正式切削时切削厚度 不同造成的误差。 不同造成的误差。 机床进给机构的位移误差。 机床进给机构的位移误差。
a)
调整法(图4-20 b) )
a)径向圆跳动 )
b)端面圆跳动 )
c)倾角摆动 )
图4-5 主轴回转误差基本形式
8
4.2.2 机床误差
◆ 主轴回转误差对加工精度的影响 ★ 主轴径向圆跳动对加工精度的影响(镗孔) 主轴径向圆跳动对加工精度的影响(镗孔) 考虑最简单的情况,主轴回转中心在X方向上作简谐 考虑最简单的情况,主轴回转中心在 方向上作简谐 直线运动,其频率与主轴转速相同,幅值为2e。 直线运动,其频率与主轴转速相同,幅值为 。则刀 尖的坐标值为: 尖的坐标值为:
机械制造工艺学
第4章 机械加工精度
4.1 概述
1
4.1.1 机械加工精度的基本概念
加工精度是指零件加工后的实际几何参数与理想 加工精度 是指零件加工后的实际几何参数与理想 几何参数的接近程度。 几何参数的接近程度。 加工误差是指加工后零件的实际几何参数对理想 加工误差是指加工后零件的实际几何参数对理想 几何参数的偏离程度。 几何参数的偏离程度。
3
原理误差 定位误差 调整误差 刀具误差 夹具误差
工件相对于刀具静止状态下 的误差
图4-2 原始误差构成
4.1.3 误差敏感方向
误差敏感方向
工艺系统原始误差方向不同,对 工艺系统原始误差方向不同, 加工精度的影响程度也不同。 加工精度的影响程度也不同。对 加工精度影响最大的方向, 加工精度影响最大的方向,称为 误差敏感方向。 误差敏感方向。 误差敏感方向一般为已加工表面 过切削点的法线方向。 过切削点的法线方向。
∆≈0 ∆
a) )
b) )
图4-12 止推轴承端面误差对主轴 轴向窜动的影响
13
4.2.2 机床误差
◆ 主轴回转误差的测量 传统测量方法存在问题: ★ 传统测量方法存在问题: 包含心轴、锥孔误差在内 包含心轴、 非运动状态。 非运动状态。 ★ 准确测量方法
图4-13 传统测量方法
a) 图4-14 主轴回转误差测量法
加工原理误差
加工原理误差是指采用了近似的成型运动或近似的刀刃轮 加工原理误差是指采用了近似的成型运动或近似的刀刃轮 廓进行加工而产生的误差。 廓进行加工而产生的误差。 例1:在数控铣床上采用球头刀铣削复杂形面零件 图4-4) :在数控铣床上采用球头刀铣削复杂形面零件(图
S = 8⋅ R ⋅ h
(4-3) )
e
3 1
结论: 结论 : 主轴径向跳动影响 加工表面的圆度误差。 加工表面的圆度误差。
图4-7 径向跳动对车外圆精度影响
10
4.2.2 机床误差
★ 主轴端面圆跳动对加工精度的影响 被加工端面不平,与圆柱面不垂直; 被加工端面不平,与圆柱面不垂直; 加工螺纹时,产生螺距周期性误差。 加工螺纹时,产生螺距周期性误差。 ★ 主轴倾角摆动对加工精度的影响 与主轴径向跳动影响类 不仅影响圆度误差, 似 , 不仅影响圆度误差 , 而且影响圆柱度误差。 而且影响圆柱度误差。
X = ( R + e) cos φ Y = R sin φ
式中 R —刀尖回转半径; 刀尖回转半径; 刀尖回转半径 φ—主轴转角。 主轴转角。 主轴转角 显然,上式为一椭圆。 显然,上式为一椭圆。
图4-6 径向跳动对镗孔精度影响
9
e
4.2.2 机床误差
★ 主轴径向圆跳动对加工精度的影响(车外圆) 主轴径向圆跳动对加工精度的影响(车外圆) 仍考虑最简单的情况,主轴回转中心在X方向上作简谐 仍考虑最简单的情况,主轴回转中心在 方向上作简谐 直线运动,其频率与主轴转速相同,幅值为2e。 直线运动,其频率与主轴转速相同,幅值为 。则刀尖 运动轨迹接近于正圆( 运动轨迹接近于正圆(图4-7)。 ) ◎ 思考 : 主轴回转中心在 思考: X方向上作简谐直线运动, 方向上作简谐直线运动, 方向上作简谐直线运动 其频率为主轴转速两倍, 其频率为主轴转速两倍 , 被车外圆形状如何? 被车外圆形状如何?
尺寸精度
加工精度 形状精度
位置精度
(通常形状误差限制在位置公差内,位 通常形状误差限制在位置公差内, 置公差限制在尺寸公差内) 置公差限制在尺寸公差内)
图4-1 加工质量包含的内容
2
4.1.2 影响加工精度的因素
原始误差—— 引起加工误差的根本原因是工艺系统存在
着误差,将工艺系统的误差称为原始误差。 着误差,将工艺系统的误差称为原始误差。
图4-11 轴承孔不圆引起镗床 主轴径向跳动
B A
图4-10 轴径不圆引起车床 主轴径向跳动
12
4.2.2 机床误差
◆ 影响主轴轴向精度的主要因素 ★ 推力轴承 滚道端面平面度误差及 与回转轴线的垂直度误 差(图4-12)。 ) ★ 其他因素 轴承孔、轴径圆度 误差; 误差 ;轴承孔同轴度误 轴肩、 差 ; 轴肩、 隔套端面平 面度误差及与回转轴线 的垂直度误差; 的垂直度误差; 装配质 量等。 量等。
原始误差分类
与工艺系统原始状 态有关的原始误差 (几何误差 几何误差) 几何误差
原始 误差
与工艺过程有关的 原始误差(动误差 动误差) 原始误差 动误差
主轴回转误差 工件相对于 机床误差 导轨导向误差 刀具运动状 态下的误差 传动误差 工艺系统受力变形(包括夹紧变形) 工艺系统受力变形(包括夹紧变形) 工艺系统受热变形 刀具磨损 测量误差 工件残余应力引起的变形
∆R = α ⋅ H =
D ∆R
X
α
Y
B
δ ⋅H
B
(4-5)
图4-15 导轨扭曲引起的加工误差 15
δ
4.2.2 机床误差
导轨与主轴回转轴线位置误差对加工精度的影响。 导轨与主轴回转轴线位置误差对加工精度的影响。
L D-∆d - Hy d Z X f a) ) ∆z f b) ) ∆z R0
∆ ∆x
k j ⋅∆φ
j
=
∑
n
j =1
1 k j ⋅ s in ω nt + α j kj
z1 = 64 z3 = z4 = 23 z2 = 16
(4-6) )
式中∆φΣ—传动链总的转角误差; 式中 传动链总的转角误差; ∆φj—第j个传动元件的转角误差; 个传动元件的转角误差; 个传动元件的转角误差 kj — 第j个传动元件的误差传递系 个传动元件的误差传递系 数,其数值等于该元件至末端元件的传 动比; 动比; ωn — 传动链末端元件角速度; 传动链末端元件角速度; αj— 第j个传动元件转角误差的初相 个传动元件转角误差的初相 角。
zn-1 = 1 zn = 96 d b ic
f
z5 = z6 = 23
c a
z7 = z8 = 16
e
图4-17 齿轮机床传动链
18
4.2.2 机床误差
◆ 提高传动精度措施 缩短传动链长度; 缩短传动链长度; 提高末端元件的制造精度与安装精度; 提高末端元件的制造精度与安装精度; 采用降速传动; 采用降速传动; 采用频谱分析方法,找出影响传动精度的误差环节; 采用频谱分析方法,找出影响传动精度的误差环节; 对传动误差进行补偿。 对传动误差进行补偿。
11
4.2.2 机床误差
◆ 影响主轴回转精度的主要因素 ★ 滑动轴承 车床(图4-10)— 轴径不圆 10) 车床( 引起车床主轴向跳动( 引起车床主轴向跳动(注意 其频率特性)。 其频率特性)。 镗床(图4-11)— 轴承孔不 镗床( 11) 圆引起镗床主轴径向跳动。 圆引起镗床主轴径向跳动。 静压轴承 — 对轴承孔或轴 径圆度误差起均化作用。 均化作用 径圆度误差起均化作用。 ★ 滚动轴承 内 外滚道 圆度误 内外 滚道圆 度误 差 、 滚 动体形状及尺寸误差。 动体形状及尺寸误差。
k= Fp ∆X
(4-7) )
工艺系统刚度; 式中 k—工艺系统刚度; 工艺系统刚度 Fp—吃刀抗力; 吃刀抗力; 吃刀抗力 ∆X —艺系统位移。 艺系统位移。 艺系统位移
α f
α
Z
c) )
图4-16 成形运动间位置误差对外圆和端面车削的影响
16
4.2.2 机床误差
◆ 影响导轨导向精度的主要因素 机床制造误差 机床安装误差 导轨磨损
17
4.2.2 机床误差
机床传动误差
◆ 机床传动误差对加工精度的影响 以齿轮机床传动链为例: 以齿轮机床传动链为例:
∆φΣ =
∑
n
j =1
∆φΣ A1 A2 Ai
φn ω1 a) ω2 b) ωi ω(频率) (频率)
图4-18 传动链误差的频谱分析
19
4.2.3 刀具与夹具误差
刀具误差
定尺寸刀具(钻头、 定尺寸刀具(钻头、 绞刀等) 绞刀等)尺寸误差影 响加工尺寸误差; 响加工尺寸误差; 成形刀具和展成刀具 形状误差影响加工形 状误差; 状误差; 刀具磨损影响加工尺 寸误差或形状误差。 寸误差或形状误差。
数学方法
◆统计分析方法:运用数理统计原理和方法,根据被测 统计分析方法:运用数理统计原理和方法, 质量指标的统计性质,对工艺过程进行分析和控制。 质量指标的统计性质,对工艺过程进行分析和控制。
5
机械制造工艺学
第4 章 机械加工精度
4.2 工艺系统的几何精度对加工 精度的影响
6
4.2.1 加工原理误差
∆Y 2 ∆RY = 2 R0 ∆RX = ∆X
(4-1) ) (4-2) )