冲压工艺卡细化检查表
冲压工厂焊接备件产品质量检验卡

总成名称:
零件号:
ห้องสมุดไป่ตู้台次
1 2 3 4 5 6 7 8 9 10 15 20 25 30 35 40 45 50 60 70 80 90 100 120 140 160 180 200
检查人
检查时间 (日/时/分)
外观
主操及生产日期:
检查项目 焊点数量 焊点位置 焊点质量
检查员首检 检查员中检 检查员末检
主操抽检
督导抽检
备注说明:
1、检查合格(“√”);检查不合格(“×”);未检查(“/”)。 2、操作工根据当日生产量对照台次检查,10台及以下须全检。 3、检查员每批次至少检查3件,生产3件以下不计。 4、主操和督导每批次至少抽查2件,生产2件以下不计。
质量检验卡
主操及生产日期:
尺寸 (错孔、错边)
不合格原因简要描述
一次合格率: 班长: 日期:
冲压巡检记录表

重大不良现象 材料用错、实物与图纸不符、冲压反向、离型面贴反. 巡检时间 图纸尺寸
测量 工具
C卡尺、S钢尺、OC投影仪、2D二次元 综合 检查担当 判定
实测值 ① ② ③ ④ ⑤
尺寸 外观 特性
备 注ILeabharlann QC: 日期:确认: 日期:
承认: 日期:
冲压巡检记录表
客户
1 2 3 4
品名
工单确认 加工要求
品番
材质 料厚
颜色
工序
WO单/图面/模具/标准样板一致性确认. 冲压面对刀口、 非冲压面对刀口). 全冲压、 半冲压、 底纸分层).
6 5
材料放置方向 方向性确认( 加工状态确认(
尺寸不良、破损、缺料、皱折、异 常见不良现象 色、脏污、爆边、溢胶、缺胶、材料用 错、氧化、全冲压 、未冲断
冲压生产过程工艺操作安全检查表
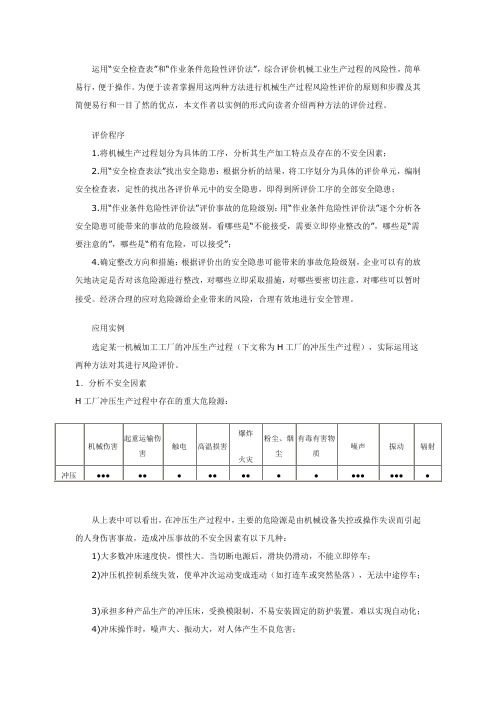
运用“安全检查表”和“作业条件危险性评价法”,综合评价机械工业生产过程的风险性,简单易行,便于操作。
为便于读者掌握用这两种方法进行机械生产过程风险性评价的原则和步骤及其简便易行和一目了然的优点,本文作者以实例的形式向读者介绍两种方法的评价过程。
评价程序1.将机械生产过程划分为具体的工序,分析其生产加工特点及存在的不安全因素;2.用“安全检查表法”找出安全隐患:根据分析的结果,将工序划分为具体的评价单元,编制安全检查表,定性的找出各评价单元中的安全隐患,即得到所评价工序的全部安全隐患;3.用“作业条件危险性评价法”评价事故的危险级别:用“作业条件危险性评价法”逐个分析各安全隐患可能带来的事故的危险级别,看哪些是“不能接受,需要立即停业整改的”,哪些是“需要注意的”,哪些是“稍有危险,可以接受”;4.确定整改方向和措施:根据评价出的安全隐患可能带来的事故危险级别,企业可以有的放矢地决定是否对该危险源进行整改,对哪些立即采取措施,对哪些要密切注意,对哪些可以暂时接受。
经济合理的应对危险源给企业带来的风险,合理有效地进行安全管理。
应用实例选定某一机械加工工厂的冲压生产过程(下文称为H工厂的冲压生产过程),实际运用这两种方法对其进行风险评价。
1.分析不安全因素H工厂冲压生产过程中存在的重大危险源:从上表中可以看出,在冲压生产过程中,主要的危险源是由机械设备失控或操作失误而引起的人身伤害事故,造成冲压事故的不安全因素有以下几种:1)大多数冲床速度快,惯性大。
当切断电源后,滑块仍滑动,不能立即停车;2)冲压机控制系统失效,使单冲次运动变成连动(如打连车或突然坠落),无法中途停车;3)承担多种产品生产的冲压床,受换模限制,不易安装固定的防护装置,难以实现自动化;4)冲床操作时,噪声大、振动大,对人体产生不良危害;5)操作工作单调重复,往复操作次数大,工人易疏忽或疲劳,发生事故。
2.用“安全检查表法”找出安全隐患将H工厂冲压生产过程作为安全检查对象,结合H工厂冲压生产过程的具体情况,编制了作业环境、冲压机械和工艺操作三个检查表,具体的安全检查表内容及检查结果如下:表1:H厂冲压生产过程作业环境安全检查表表2:H厂冲压生产过程冲压机械安全检查表表3:H厂冲压生产过程工艺操作安全检查表3.冲压生产过程中可发生的事故的危险等级:通过使用安全检查表的是非判断方式,我们共检查出H厂的冲压生产过程中有如下的几项安全隐患:使用作业条件危险性评价法,逐个分析各安全隐患可能带来的事故的危险程度:1)冲压车间的保温措施不够:事故发生的可能性(L):冬天,车间内的温度过低,会对操作者的生理和心理造成不好的影响,但导致事故的可能性极小,属“可能性小,完全意外”,取L=1暴露于危险环境的频繁程度(E):操作人员只有在每年冬季的三四个月里,才会在每天的工作时间里呆在车间,故我们大体取值E=3发生事故的后果(C):取C=1危险分值D=L*E*C=3<20,危险程度属“稍有危险,可以接受”2)噪声干扰,控制措施不得力:事故发生的可能性(L):车间内超标的噪声,会对操作者的生理和心理造成不好的影响,除直接导致职业病外,还可能影响工作时工人的注意力,导致事故,属“相当可能”,取L=6暴露于危险环境的频繁程度(E):操作人员每天的工作时间里呆在噪声超标的车间里,故我们取值E=6发生事故的后果(C):取C=3危险分值D=L*E*C=48,在20—70之间,危险程度属“一般危险,需要注意”3)不能做到设备定期检修,不能做到及时避免设备突发性故障:事故发生的可能性(L):如果设备不能保证定其检修,就不能保证其可靠性和灵敏性,发生突发性故障导致事故的可能性很大,属“完全可以预料到”,取L=10暴露于危险环境的频繁程度(E):我们大体取值E=3发生事故的后果(C):取C=3危险分值D=L*E*C=90,在70—160之间,危险程度属“显著危险,需要整改”4)对于某些设备(如:剪板机等),为了生产操作的方便,一般都在生产加工时,将防护罩卸下:事故发生的可能性(L):如果设备在加工时没有防护设施,则操作人员稍不注意,就很容易造成事故属“相当可能”,取L=6暴露于危险环境的频繁程度(E):操作人员每天的工作时间里呆在没有防护设施的机械旁,故我们取值E=6发生事故的后果(C):取C=3危险分值D=L*E*C=108,在70—160之间,危险程度属“显著危险,需要整改”应该注意,危险等级的划分是凭经验判断的,难免带有局限性和人的主观性,在具体应用其来评价某一作业环境时,需要根据实际情况予以修正。
冲压检查表

6
保险盖
1、使用是否完好;2、强度和尺寸是否符合(含备用的)
2、参照说 明书。
2、备用的三个月
7
安全用电
是否有电线破皮、老化以及私拉乱扯现象
1、目测
1个月
8
地脚螺丝
是否有缺失、松动(40T以上的冲床)
1、目测 2、试验
1个月
9
支撑螺丝
是否有缺失、松动(开式可倾冲床)
1、目测 2、试验
1个月
10
电机的固定及支撑螺丝 是否有缺失、松动
1、目测 2、试验
1个月
备注:上表中的各项由安全办全体在冲压部日常巡查或维修工作中安全检查的基本内容。电工负责用电安全及光电保护、双手操作和电机及电箱、操作箱的紧固螺丝
检查; 机修工负责冲床使用(含保险盖)、安全挡板、防护网、地脚螺丝、支撑螺丝的检查。检查出的问题必须有记录、有结果,作为绩效考核的重要依据。
补充说明:
冲压部安全控点检查表
检查日期:
安全控点
检查内容
1
冲床使用
1、是否超负荷;2、螺杆调节是否超出范围
模具安全挡板 1、有否;2、有效性
检查方法
1、检查保 险; 2、目测
1、目测
检查人:
检查周期
现场随时
现场随时
检查结果
2
四要素
防护网 光电保护 双手操作
1、有否;2、有效性 1、有否;2、有效性(含高度调节) 1、有否;2、有效性(16T以上的冲床)
1、目测
1、目测 2、试验 1、目测 2、试验
现场随时 现场随时 现场随时
3
劳保用品
耳塞、眼镜、手套、防护帽、代手工具等是否正确使用
1、目测
冲压模具细部设计检查表

6 每一下料工程站是否会容易跳屑?
7 安装沖子入块与冲子固定板框口是否有方向性设计?
8 脫料入块与脱料板框口是否有方性设计?
9 下模入块与下模板框口是否有方向性设计?
10 折弯成型冲子与下模折弯成型入块是否有方向性设计?
11 是否需要增加调整偏摆之工程站?
12 是否需要增加調整高低針之工程站?
13 是否需要增加调整扇形之工程站?
actionitems编号工作內容ecdacd冲压模具设计检查表模具编号依据当时之实际状况叙述
冲压模具细部设计检查表
模具编号 :
日期 :
项目
检查內容
1 每一個工程站之排配是否适当
2 下料刀口与冲子加工是否可行?
3 下料刀口与冲子承受强度是否可行?
4 滑块机构设计是否可行
5 每一弯曲工程站成形是否稳定?
14 浮升梢高度设定与排配是否适当?
15 是否需要预留工程站?
Action Items :编号Fra bibliotek工作內容是
否
□
□
□
□
□
□
□
□
□
□
□
□
□
□
□
□
□
□
□
□
□
□
□
□
□
□
□
□
□
□
BY ECD
备注 ACD
※ 依据当时之实际状况叙述:
检查者 :
确认者 :
. SD-011A
JN.LY W-GY-04-JL01 冲压制造部工艺纪律检查表

一项次不合格扣2分。
2.操作者应掌握本岗位工艺参数、工艺要求
一项次不合格扣1分。
3. 按生产工艺要求程序进行操作。未按生产工艺要求程序进行操作
一项次不合格扣2分。
4. 未严格按照工艺规定的检验频次进行检验并记录的
一次扣2分。
5. 钣件按要求定位准确,
一次1分。
一处不合格扣1分。
8.当日冲压件有无首验、巡检、末检检验,并按照工艺规定的检验频次进行检验且记录做出检验数据报告。首末件是否按规定检查存放
一项不合格扣2分。
9.装架作业协同检验有无执行
发现一次扣2分。
10.有无卡废料、检知异常现象发生。协同检验有无执行(特别是装架作业)
发现一处扣2分。
四、操作者必须按工艺标准进行操作
路径(部门级):各制造部→各制造部(归档保存) 记录保存期限:3年
一处不合格扣2分。
六、安全
1.自动线门关闭后生产线内是否有人,人员进入模腔时有无放置安全栓,天车吊物下是否有人。
发现一处扣5分。
2.操作工需穿戴劳保用品上岗。
发现一处扣5分。
3.自动线及模修设备区安全防护装置(如围栏等)损坏后未做出安全警示标志,未及时上报维修。
不上报维修扣2分,不做安全警示标志扣5分
一项次不合格扣2分。
五、设施设备保养及物料存放
1. 要求检具、模具定期保养,检具型面清洁、无破损,模具油漆无脱落,金属裸露部分无生锈。按工艺规程和计划对模具进行定期维护保养清洗,维护实施情况符合工艺要求,记录完全。
发现一处扣2分
2.模具安装前未按规定对模具上、下模板及工作台面进行清理或者清理不干净;压件前及压件过程中未按规程对模具进行检查清理和润滑;压件后模具清理不彻底。
冲、剪、压机械安全检查表
防护罩是否设计合理,操作方便;
是否有足够的强度,无棱角毛边;
是否与开关有机的连接,以便于开关的检修。
脚踏开关的自由行程是否≥15mm
开关内弹簧是否是确保复位的压簧。
脚踏开关与防护罩均是否PE可靠,动作灵敏可靠,且防高温触及,无水浸泡。
6
机床PE可靠,电气控制有效
投光器与受光器组成的光轴数为两个以上时,其光轴间距是否不大于50㎜。
对于由若干光轴所组成的垂直平面被安设在距工作危险区的距离超过500mm时,其光轴间距是否不大于70mm;.
投光器、受光器的安装是否稳固,并便于调节;
安全保护装置的电子控制部分是否不安装在受阳光曝晒和具有40℃以上的热源处,
是否避开对电子器件存在干扰的强磁场。
冲剪压机械的金属结构件、电动机壳体、变压器壳体、穿线金属管等,是否均PE可靠。
PE连接的通用要求,是否符合第三章第43节“金属切削机床”的有关要求。
冲剪压机械可移动的开关电源线是否采用三芯橡胶电缆线
外套蛇皮管,如有物件压砸可能时,是否用槽钢或钢管(盖)防护。
电气控制的通用要求,是否符合第三章第43节“金属切削机床”的有关要求
制动器和离合器是否相互协调与联锁,开机时制动器先松闸,离合器稍滞后再结合。
联锁或连接是否均准确、紧固,工作时稳定、协调。
行程限位装置、控制装置是否正确,动作完好有效。
3
紧急停止按钮灵敏、醒目,在规定位置安装有效
大型冲压机前、后面是否均按装紧停按钮
紧停按钮是否设置在控制点、给料点附近,人手可迅速触及且不会产生误动作之处。
线路是否没有接头、破损、老化或过载。
随机配备的电器箱柜安全要求,是否符合第三章第43节“金属切削机床”的有关要求
冲压热处理安全检查表-水压机安全检查表
冲压热处理安全检查表-水压机安全检查表一、设备安全检查:1. 检查水压机的设备外观是否完好,如屏幕、按钮、开关等是否损坏或松动。
2. 检查水压机的传动部件是否有明显的异响或松动。
3. 检查水压机的润滑系统是否正常运行,是否有漏油现象。
4. 检查水压机的电气系统是否正常运行,如电线、电缆、接线端子是否有松动或破损。
5. 检查水压机的冷却系统是否正常运行,如水箱、水管、水泵是否有漏水现象。
6. 检查水压机的气路系统是否正常运行,如压缩空气管路、气缸、气阀是否有漏气现象。
7. 检查水压机的安全装置是否完善,如安全门、安全光幕、急停开关等是否正常使用。
二、工作环境安全检查:1. 检查水压机的工作区域是否整洁有序,如有杂物、油污等是否及时清理。
2. 检查水压机的周边区域是否存在危险物品、易燃易爆物品等。
3. 检查水压机的工作区域是否通风良好,如有排风设备是否正常运行。
4. 检查水压机的工作区域是否有明火,如焊接、切割等作业是否按规定进行。
三、操作安全检查:1. 检查操作人员是否具备相关岗位培训和操作证书。
2. 检查操作人员是否佩戴个人防护用品,如安全帽、护目镜、防护手套等。
3. 检查操作人员是否按照操作规程进行工作,是否存在违规操作行为。
4. 检查操作人员是否注意观察设备运行状态,如异常情况是否及时报修。
5. 检查操作人员是否正确地使用紧急停机按钮或急停开关。
四、维护安全检查:1. 检查设备维护人员是否具备相关技术培训和维护资质。
2. 检查设备维护人员是否按照维护计划进行定期检修和保养。
3. 检查设备维护人员是否按照操作手册进行设备调试和维修。
4. 检查设备维护人员是否按照操作规程进行设备维护,如使用维护工具是否合规。
五、紧急救援安全检查:1. 检查紧急救援设备是否齐全,如急救箱、灭火器、安全绳等是否处于正常状态。
2. 检查紧急救援通道是否畅通,如安全出口、逃生通道等是否易于使用。
3. 检查操作人员是否熟悉应急预案,如火灾、事故等应急情况的处理方法。
冲压件检查基准书细化检查表
孔径Φ 11 孔径Φ 11 孔径Φ 11 孔径Φ 12 孔径Φ 12 孔径Φ 9 孔径Φ 9 中地板左右后加强板外观 毛刺 孔数检查 基准孔孔径Φ 12 孔径Φ 9 孔径Φ 9 孔径Φ 9 孔径Φ 9 孔边距38 孔边距36.7 子口边20.5 子口边11.5 中地板 外观 毛刺 孔数检查 检具定位孔孔径Φ 16 检具定位孔孔位Φ 16 检具定位孔孔径Φ 16 检具定位孔孔位Φ 16 孔径Φ 14 孔径Φ 14孔位 孔径Φ 14 孔径Φ 14孔位 孔径Φ 14 孔径Φ 14孔位 孔径Φ 14 孔径Φ 14孔位 孔径Φ 14 孔径Φ 14孔位 孔径Φ 14 孔径Φ 14孔位 孔径Φ 14 孔径Φ 14孔位 孔径Φ 14 孔径Φ 14孔位 间隙 修边线 后地板左边板 外观 毛刺 孔数检查 基准孔孔径Φ 8 基准孔孔径Φ 8 孔间距162.5 孔边距12 翻遍高度4.5 翻边宽度13 后地板右边板 外观
K1检查基准书细化检查表
零部件号 前防撞梁外板 检查项目 目测 目测 游标卡尺0.02/150 目测 游标卡尺0.02/150 游标卡尺0.02/150 钢卷尺2m 钢直尺150mm 游标卡尺0.02/150 目测 游标卡尺0.02/150 目测 游标卡尺0.02/150 游标卡尺0.02/150 游标卡尺0.02/150 游标卡尺0.02/150 游标卡尺0.02/150 钢直尺150mm 钢卷尺2m 目测 游标卡尺0.02/150 目测 游标卡尺0.02/150 游标卡尺0.02/150 游标卡尺0.02/150 游标卡尺0.02/150 游标卡尺0.02/150 游标卡尺0.02/150 游标卡尺0.02/150 目测 游标卡尺0.02/150 游标卡尺0.02/150 游标卡尺0.02/150 游标卡尺0.02/150 游标卡尺0.02/150 游标卡尺0.02/150 游标卡尺0.02/150 游标卡尺0.02/150 游标卡尺0.02/150 目测 游标卡尺0.02/150 目测 游标卡尺0.02/150 游标卡尺0.02/150 游标卡尺0.02/150 游标卡尺0.02/150 游标卡尺0.02/150 游标卡尺0.02/150 目测 游标卡尺0.02/150 判定标准 无开裂、无隐裂、无褶皱 外观 毛刺 孔数检查 孔径①Φ 10 孔径①Φ 10 孔间距877 尺寸100.5 孔径Φ 14 前地板左右前加强板外观 毛刺 孔数检查 定位孔孔径Φ 6 定位孔孔径Φ 10 孔径Φ 6.5 定位孔孔径Φ 10 孔径Φ 6.5 子口孔数检查 基准孔孔径Φ 10 基准孔孔径Φ 10 孔径Φ 7 孔径Φ 7 孔径Φ 7 孔径Φ 7 孔边距6.5 手刹底座上板 外观 毛刺 基准孔孔径Φ 10 基准孔孔径Φ 9 孔径Φ 6.5 孔径Φ 6.5 孔径Φ 6.5 孔径Φ 6.5 孔径Φ 12 穿刺孔3.4 驾驶员座椅地脚加强梁 外观 毛刺 孔数检查 定位基准孔孔径Φ 10 定位基准孔孔径Φ 10 孔径Φ 7 孔径Φ 7 孔径Φ 7 孔径Φ 7 左右下边梁后内板 外观 毛刺
冲压工序卡-模板
模具编号
工序简图
检测工具
模具闭合高度(mm)
安全措施
顶杆规格
1、双手按钮,机床单发。
滑块压力(MPa)
气垫压力(MPa)
顶杆安装图
安装垫块规格
无
工位器具编号
辅助工具/辅料
备注
编制/日期
ห้องสมุดไป่ตู้标准化/日期
会签/日期
批准/日期
更改标记
处数
文件号
签字
日期
校对/日期
审核/日期
公司名称
冲压工序卡
标记
零件代号
编号:
零件名称
共页
第页
工序内容
操作注意事项
工序号
工序名称
1.定位准确;
2.制件100%自检:孔数、毛刺等有问题件隔离存放;
3.生产过程中,需经常清理模具工作表面的油泥、料渣等;
4.制件在生产和码放过程中不要磕碰、划伤。
设备型号
检验:首末件检验,巡检,形位尺寸由模具保证
检验标准:按冲压件检验通则。
- 1、下载文档前请自行甄别文档内容的完整性,平台不提供额外的编辑、内容补充、找答案等附加服务。
- 2、"仅部分预览"的文档,不可在线预览部分如存在完整性等问题,可反馈申请退款(可完整预览的文档不适用该条件!)。
- 3、如文档侵犯您的权益,请联系客服反馈,我们会尽快为您处理(人工客服工作时间:9:00-18:30)。
序号
制件名称工序闭合高度主缸压力液压垫压力液压垫上升距离1纵梁前段左内板落冲696.6
2成型55%
15T
282
3纵梁前段右内板落冲
696.6
470%
15T
275
5纵梁前段左外板
落冲701
6成型
85%
15T
83
7侧翻侧冲孔
848.48纵梁前段右内板落冲
701
9成型
85%
15T
86.7
10侧翻侧冲孔
844.511第四横梁左支架上板落料冲孔
43012一次成型400
13二次成型10MPa
3MPa
2521
14侧冲孔侧整
66015第四横梁右支架上板落料冲孔
43016一次成型400
17二次成型10MPa
3MPa
2521
18侧冲孔侧整
66019第四横梁支架下板落冲
485.5
20拉延12MPa
3MPa
1389
21冲孔37322翻遍切断
67523第一横梁上板落冲
521.3
24成型
10MPa 3MPa 137125第一横梁下板成型
10MPa
3MPa
2153
26修边冲孔
499.427第四横梁上板落料冲孔
604.7
28成型10MPa
3MPa
2247
29侧冲
55030第四横梁下板落料冲孔
597.6
31成型
12MPa
3MPa
1704
32纵梁中断内板修边冲孔
597.433成型、翻孔
558.934纵梁中断外板落冲
619.3
35成型
80%
30T
237.3
36
翻边侧冲孔
606.4
K2车架冲压工艺卡细化检查表。