DINEN锌及锌合金涂层
ISO1461-1999德国镀锌标准

附录NA引用标准(未包括在规范化引用和参考文献中)DINEN10204 金属产品的检验文件(包括修改件A1:1995)DINENISO1460 黑色金属材料表面热浸镀锌涂层-单位面积重量测定法(ISO1460:1992)DINENISO2064 金属和其他无机涂层-厚度测量相关定义和换算(ISO2064:1980)DINENISO2178 磁性基体表面上非磁性涂层-磁性法涂层厚度测量(ISO2178:1982)ICS?25.220.40描述字:金属涂层、钢制品、热浸镀锌、要求、试验 中文版钢铁制品表面热浸镀锌涂层 技术规格和试验方法(ISO1461:1999)本欧洲标准于1998年11月8日由CEN 批准。
CEN 成员有义务遵守CEN /CENELEC 内部规范,这些规范规定了本欧洲标准不作任何修改而作为国家标准的条件。
有关这些国家标准的最新通知单和文献参考可向管理中心秘书处或任何CEN 成员申请来获得。
本欧洲标准有三种官方版本(英语、法语、德语)。
通报了中央秘书处且由CEN 成员国负责翻译成本国语言的其他版本具有与官方版本相同的效力。
CEN 成员包括以下国家的标准机构:奥地利、比利时、捷克共和国、丹麦、芬兰、法国、德国、希腊、冰岛、爱尔兰、意大利、卢森堡、荷兰、挪威、波兰、葡萄牙、西班牙、瑞典、瑞士和英国。
欧洲标准化委员会管理中心:rue?de?Stassart?36,布鲁塞尔B 区1050号 1999 CEN :全球范围内任何形式和任何方式的宣传权利归CEN 成员国家所有 参考号:EN?ISO?1461:1999?EEN?ISO?1461 1999年2月欧洲标准前言国际标准ISO1461:1999 钢铁制品表面热浸镀锌涂层—技术规格和试验方法,由国际标准化组织(ISO)的ISO/TC107“金属和其他无机涂层技术委员会”制定。
经CEN/TC262“金属和其他无机涂层技术委员会”(其秘书处由BSI领导)批准而作为欧洲标准。
EN_ISO-12944-4(1998) 中文版 色漆和清漆 防护漆体系对钢结构的腐蚀防护 第4部分 表面和表面预处理类型
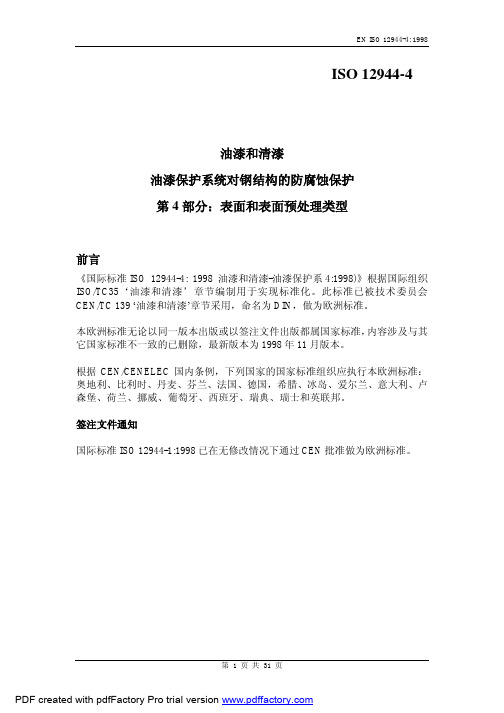
PDF created with pdfFactory Pro trial version
EN ISO 12944-4: 1998
ISO 4628-3:1982, 油漆和清漆-油漆涂层等级下降的评估-缺陷强度、数量、普 通类型尺寸的认定-第 3 部分:生锈程度认定。 ISO 4628-4:1982, 油漆和清漆-油漆涂层等级下降的评估-缺陷强度、数量、普 通类型尺寸的认定-第 4 部分:裂化程度认定。 ISO 4628-5:1982, 油漆和清漆-油漆涂层等级下降的评估-缺陷强度、数量、普 通类型尺寸的认定-第 5 部分:剥落程度认定。 ISO 4628-6:1982, 油漆和清漆-油漆涂层等级下降的评估-缺陷强度、数量、普 通类型尺寸的认定-第 6 部分:通过胶布粘贴测量规定的粉化程度。 ISO 8501-1:1988, 油漆和相关产品应用前钢结构底层的预处理-表面清洁度视 觉评估-第 1 部分:未涂层钢结构底层和整个去除上层涂层后钢结构底层的生锈 等级和预处理等级;
EN ISO 12944-4: 1998
ISO 12944-4
油漆和清漆 油漆保护系统对钢结构的防腐蚀保护 第 4 部分:表面和表面预处理类型
前言
《国际标准 ISO 12944-4: 1998 油漆和清漆-油漆保护系 4:1998)》根据国际组织 ISO/TC35‘油漆和清漆’章节编制用于实现标准化。此标准已被技术委员会 CEN/TC 139 ‘油漆和清漆’章节采用,命名为 DIN,做为欧洲标准。 本欧洲标准无论以同一版本出版或以签注文件出版都属国家标准,内容涉及与其 它国家标准不一致的已删除,最新版本为 1998 年 11 月版本。 根据 CEN/CENELEC 国内条例,下列国家的国家标准组织应执行本欧洲标准: 奥地利、比利时、丹麦、芬兰、法国、德国,希腊、冰岛、爱尔兰、意大利、卢 森堡、荷兰、挪威、葡萄牙、西班牙、瑞典、瑞士和英联邦。 签注文件通知 国际标准 ISO 12944-1:1998 已在无修改情况下通过 CEN 批准做为欧洲标准。
DIN 55928

替代`77.01版本1991年5月与国际标准机构(ISO)制定的标准ISO8501—1:1988 之间的相互关系请看说明。
“金属材料构件通过涂层和衬里来防腐”DIN55928包括以下部分:DIN55928第1部分一般介绍,概念,腐蚀强度。
DIN55928第2部分有利于防腐的结构。
DIN55928第3部分防腐工作计划。
DIN55928第4部分表面的预处理和检查。
DIN55928第4部分的附录1 比较样板图片DIN55928第4部分的附录1 A1 DIN55928第4部分的附录1的更改。
DIN55928第4部分的附录2 对部分钢表面进行打磨预处理的样板图片(标准—清洁度Pma)DIN55928第4部分的附录2 A1 DIN55928第4部分的附录2的更改。
DIN55928第5部分防腐系统和涂层材料。
DIN55928第6部分防腐工作的执行和监督。
DIN55928第7部分检查表面的技术条例。
DIN55928第8部分(草案)薄壁结构的防腐。
DIN55928第9部分涂层材料,粘和剂和涂料的配方。
德国DIN标准化研究所喷涂材料和类似涂层材料标准化协会(FA)建筑工程标准化协会(NABau)喷砂材料标准化协会(Astra)目录1.目的和使用范围2.一般介绍3.预处理表面的原始状态3.1 未涂层表面3.2 涂层表面4.表面清洁度,表面预处理方法4.1 清洁程度要求和清洁度4.2 外来涂层/附着物的清除4.3 本身涂层和附着物的清除4.3.1 去氧化皮4.3.2 除锈4.3.3清除镀锌层腐蚀物质4.4 机械化表面预处理方法4.4.1 喷砂4.4.1.1 喷砂系统4.4.1.1.1 干式喷砂4.4.1.1.2 潮湿喷砂4.4.1.1.3 湿式喷砂4.4.1.2 喷砂材料4.4.1.3 特殊情况下喷砂的使用4.4.1.3.1 薄钢板的喷砂4.4.1.3.2 清扫式喷砂4.4.1.3..3 点式喷砂4.4.2 使用手工工具进行机械式表面预处理4.4.3 使用电动工具进行机械表面预处理4.5 高温表面预处理方法(火花除锈)4.6 化学表面预处理方法(酸洗)4.7 锈蚀转化剂,锈蚀稳定剂,和渗透剂4.8 环境条件对表面预处理和表面清洁度的影响4.9 预处理过程中周围环境的保护4.10 预处理表面的质量检查4.10.1 肉眼可见污渍的检查4.10.2 肉眼不可见污渍的检查5.表面粗糙度5.1 一般介绍5.2 经过喷砂处理后的粗糙度检查6.预处理表面处理完毕后,涂层加工之前的过渡性保护7.经过过渡性保护或部分经过过渡性保护的表面要继续涂层前的处理7.1焊接,铆接,螺钉和其它连接部位的预处理7.2 涂层表面还需做进一步涂层时的预处理7.3 需涂层的热度锌表面预处理7.3.1镀锌层缺陷部位和因安装、运输造成损伤的部位的处理7.3.2未经风蚀的热镀锌表面预处理7.3.3经过风蚀的热镀锌表面预处理涉及的标准和其它资料其它有关标准更改说明1.目的和使用范围:[1](1)钢结构件[1]的防腐保护涂层和衬里的效果和使用寿命(下面简称涂层和衬里)在很大程度上取决于需要防腐的表面的预处理质量。
DIN EN ISO 2808

DIN EN ISO 2808涂料和清漆漆膜厚度的测定前言译文略简介a)b)c)d)1 范围本国际标准描述了一些测量基材上涂层厚度的方法。
方法确定了对以下内容的描述:湿膜厚度,干膜厚度,未固化喷塑涂层厚度。
参考现有的单个标准。
否则将细节描述方法。
本方法的综述参见附录A,适用领域现有的标准和精度被列入单个方法。
此国际标准也定义了关于膜厚的术语。
国际标准也定义了关于膜厚确定的术语。
2 术语参考文件以下参考文件时此文件应用时必不可少的。
作为参考,仅有那些引用版本适用。
对于更新的参考,那么将参考文件的最新版本(包括任何修正过的申请)。
ISO463,几何学产品技术规范(GPS)—尺寸测量设备—机械度盘式指示器的设计和度量衡学特点。
ISO 3611, 外部测量的千分卡尺ISO 4618:2006, 色漆和清漆—术语和定义ISO 8503-1, 在喷涂油漆和相关产品之前对钢铁底材的准备-喷砂清洁钢铁底材的表面粗糙性特点—部分1:ISO表面型材比较仪(对研磨喷砂清洁表面的评估)的规范和定义3 术语和定义鉴于本文件的目的,ISO4618和以下给出的术语和定义适用。
底材将要喷涂涂层的表面[ISO 4618 :2006]涂层施加在底材上的单层货多层的连续的涂层材料层[ISO 4618:2006]膜厚底材表面和涂层膜表面之间的距离。
湿膜厚度刚刚喷涂上的湿膜材料的厚度,在喷涂后立刻测量。
干膜厚度当涂层硬化后,表面的涂层的厚度未固化喷塑涂层的厚度刚喷涂的塑粉的厚度,喷塑后从喷塑烤房出来前测量的塑粉材料的厚度。
相关表面区域1)覆盖的或即将被涂层覆盖的部件的一部分,即涂层的适用性和/或外观很重要的那部分。
试验区域1)相关表面区域的代表部分,将在此部分进行协议次数的单次测量。
测量区域1)进行单次测量的区域最小局部膜厚1)在特定试验样品的相关表面上的局部膜厚的最低值最大局部膜厚1)在特定试验样品的相关表面上的局部膜厚的最高值平均膜厚1)试验区域的所有单次干膜厚度的算数平均值,或膜厚重量分析的测定值。
DINEN1559-3:1997铸件附加供货条件
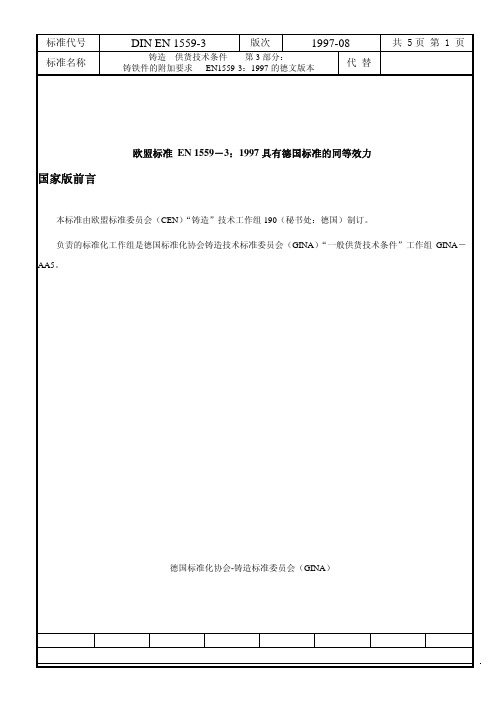
欧盟标准 EN 1559-3:1997具有德国标准的同等效力国家版前言本标准由欧盟标准委员会(CEN)“铸造”技术工作组190(秘书处:德国)制订。
负责的标准化工作组是德国标准化协会铸造技术标准委员会(GINA)“一般供货技术条件”工作组GINA-AA5。
德国标准化协会-铸造标准委员会(GINA)欧盟标准 EN 1559-31997年6月关键词:铸造技术,铸铁,铸件,概念,中间用户和生产厂的关系,标注,生产制造,要求,检验,管理,包装,标记德语版铸造供货技术条件第三部分:对铸件的附加技术要求本欧盟标准于1997年5月2日通过了欧盟标准化委员会(CEN)的审批。
欧盟标准化委员会(CEN)成员国承诺,遵守欧洲标准化委员会和欧洲电工标准化委员会(CEN/CENELEC)工作条例中规定的一切条件,对本欧盟标准不进行任何修改的作为国家版标准予以采用。
这些国家标准最新状态的清单及其目录可以从中央秘书处或每个CEN成员那里索取。
本欧盟标准有三种官方版本(德文版、英文版、法文版)。
由欧盟成员国自行负责将欧盟标准翻译成本国语言并通知欧盟标准化委员会中心秘书处,这些版本的标准与欧盟官方公布的标准具有同等的效力。
欧盟标准化委员会成员国是指以下国家的国家标准化委员会:比利时、丹麦、德国、芬兰、法国、希腊、爱尔兰、冰岛、意大利、卢森堡、荷兰、挪威、奥地利、葡萄牙、瑞典、瑞士、西班牙、捷克和英国。
CEN欧盟标准化委员会前言 3 引言 4 1 适用范围 42 标准的引用说明 43 概念4 4由用户提供的信息 44.1 有约束力的信息 4 4.2 自由选择的信息 4 4.3 图纸、模型和模具 4 4.4 有关质量(重量)的信息 4 4.5预制的样件 4 4.6首批样件 4 5标记 4 6制造 5 6.1制造方式 5 6.2焊接 5 7 要求 57.1 概述 5 7.2 材料 5 7.3 铸件 5 8材料检验特征的确定及证书 5 8.1概述 5 8.2检验 5 8.3检测批次的取样 5 8.4试件 5 8.5检验方法 5 8.6无效检验 5 8.7复验 5 8.8分类和返修 5 9标记 5 10包装和表面防护处理 5 11质量投诉 5附录A(参考性) 参考文献 5前言本标准由欧盟标准委员会“铸造”技术协会(CEN/TC190)制订,秘书处是德国。
大众标准TL 244中文2010年12月版

大众汽车集团标准TL2442010年12月版分类号:50223关键字:锌,镍,钝化处理,密封,无Cr(VI),防腐蚀,表面保护锌/镍-合金涂覆层表面保护要求Cr (在1000Mpa和1200Mpa之间的钢制件时,必须按DINENISO4042作热处理。
这些当作坚固防腐层(稳定等级为6)的涂覆层,亦特别适用于除了腐蚀负荷增加和温度负荷增加至150°C (例如:发动机室和刹车系统)之外的部件以及螺栓拧紧系统。
银色涂覆层(例如:Ofl-r642,Ofl-r643,Ofl-r645和Ofl-r647)特别适用于导线连接(接地线连接)。
这些涂覆层特别适用于内部传动的紧固元件,以避免附加的施力作用。
另外,鉴于其电化相容性,这些涂覆层尤其适用于与铝材料的连接(但不适用于与镁材料直接连接)。
Ofl-r647和Ofl-r648特别适用于表面处理后会发生塑性变形的从动元件。
(如管道系统、拉钉、拉帽、打孔螺栓)2标记方法参见VW13750,第2章节。
3技术要求3.1表面防护类型表面保护类型见表1:进行一次完整的试验需要10个成品件。
注1:采用封闭剂的表面保护类型,可能影响涂胶的附着性能。
由于其微裂性,这些涂覆层也不适合于诸如空调装置的供气系统的密封元件。
采用这种涂覆方法的部件,必须避免后来的塑性变形(卷边、挤压、弯曲),这是因为这种情况会导致损害防腐性能,从而降低防腐耐抗性。
Ofl-r647或Ofl-r648将优先运用于会发生塑性变形的零件。
Ofl-r647将优先应用于流体运载系统。
除非元件在图纸上特意标出不须涂覆,否则元件的全部表面必须依照所需的保护类型并表明其性质,涂覆层应牢牢的附着在基体材质上。
表面形态的一般注意事项:锌镍涂层零件表面粗糙度,除其他因素外,取决于锌镍电解液特性和组件的表面光洁度。
有涂层与无涂层之间的表面粗糙度相差必须≦Rz5um。
锌/镍涂覆的表面:由严重开裂引起的结瘤(如图1)会对品质产生负面影响(如剥落,防腐能力不足,元件在组装过程中无意识擦伤),所以必须要避免。
【精品】DIN-50965电镀层--钢铁和铜及铜合金上的锡镀层(中文版)

D I N-50965电镀层--钢铁和铜及铜合金上的锡镀层(中文版)德国标准 2000年5月电镀层——钢铁和铜及铜合金产品的锡镀层ICS 25.220.40 替代了1982年2月版本前言本标准由DIN材料试验标准委员会制定,采用了DIN EN 1430 中的技术规范。
内容增补本标准与1982年2月版本标准相比,主要变化如下:1.补充了订货技术条件的内容;2.不再对使用条件的数目进行规定;3.对本标准的编辑进行了修改。
先前版本发布情况:DIN 50965: 1962-10/ 、1982-02。
由DIN-Sprachendienst 将德文翻译成英文。
假若出现分歧争议,应以德文原版标准为准(权威版本)1 应用范围本标准制定了钢铁和铜基材料上锡镀层的技术规范,标准中规定了锡镀层的最小厚度以及提供了基体金属表面光洁度和热处理方面的技术条件内容。
本标准不涉及半成品和紧固件(参考DIN EN ISO 4042), 螺纹件必须依据供需双方进行涂覆(电镀)。
注意:使用该标准时,必须遵守相关安全规定,如,TRGA和TRGS 以及《德国危险物质及材料规定》。
2 引用标准及规范性文件本标准包含有标注日期和没有标注日期的标准以及其他出版物规定条款。
这些规范性文件在本标准文本适当场合进行了引用,标准编号和标题如下所列。
对于标注日期的引用文件,其随后所有的修改单或修订版不适用于本标准;对于没有标注日期的引用文件,其最新版本适用于本标准。
引用标准:DIN 32506-3 软钎焊的可焊性检验——镀锡工件试样垂直浸渍试验DIN 50902 金属材料防腐涂层——术语、工艺方法、表面预处理DIN EN 1403 金属材料防腐涂层—电镀层—一般性要求规定的工艺方法DIN EN ISO 2064金属镀层和其他无机涂层—有关涂层厚度测量的定义和规定(ISO 2064:1996)DIN EN ISO 4042 紧固件——电镀层(ISO 4042:1999)引用文件:Technische Regeln für gefährliche Arbeitsstoffe und GefahrstoffeMAK-Liste: Maximale Arbeitsplatzkonzentrationen und biologische Arbeitsstofftoleranzwerte (List of thresholdvalues for dangerous substances at workplaces and compatibility values), 1989 TRK-Liste (List of guideline values for concentrations of hazardous substance at workplaces)Verordnung zum Schutz vor gefährlichen Stoffen, as of 15 November 1999, BGB l. (German Federal Law Gazette) I,No. 52, p. 2233 ff.3术语及定义3.1电镀层电解液中通过阴极沉积产生的金属覆盖层(镀层)(参照DIN 50902)3.2主要表面(有效面积)除非有其他协议,主要表面是指可以接触放入直径20mm球的产品区域译者备注:在DIN EN ISO 2064 中“主要表面”定义为“工件上某些已涂覆或待涂覆镀层的表面,在该表面上镀层对其使用性能和(或)外观至关重要”。
DIN_50979_中文版
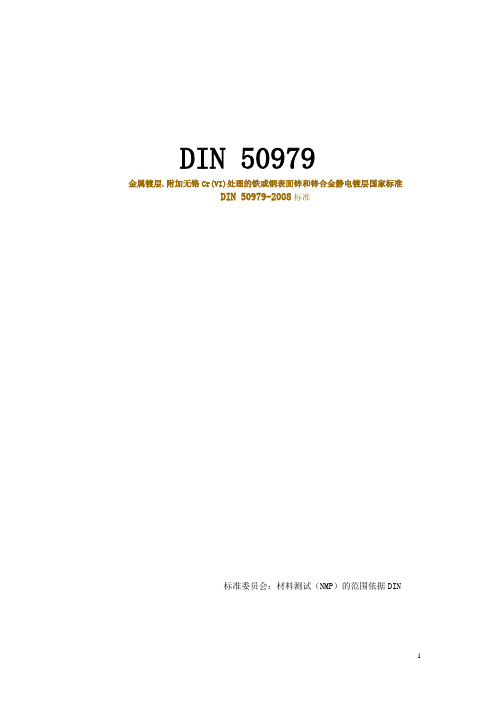
DIN 50979金属镀层.附加无铬Cr(VI)处理的铁或钢表面锌和锌合金静电镀层国家标准DIN 50979-2008标准标准委员会:材料测试(NMP)的范围依据DIN目录内容页码前言 (3)1.应用领域 (3)2.引用的规范文件 (3)3.标准内容 (4)3.1. 电镀层 (4)3.2. 钝化膜的形成 (4)3.3. 封闭后处理 (4)3.4. 特殊情况(功能性要求表面) (5)3.5. 具体的实例 (5)4.需求数据 (5)5.具体材料 (6)6.涂层方法/涂覆工艺 (6)6.1. 锌或锌合金的预处理和表面电镀 (6)6.2. 后处理 (6)6.2.1. 钝化效果 (6)6.2.2. 封闭 (7)6.3. 滚镀/挂镀(零件处理) (7)6.3.1. 零件滚镀处理 (7)6.3.2. 零件挂镀处理 (7)6.4. 氢脆 (7)6.4.1. 基本原理 (7)6.4.2. 方法 (8)6.4.2.1. 材料强度<1000N/mm² (8)6.4.2.2. 材料强度≥1000N/mm² (8)7.材料要求和试验方法 (9)7.1. 涂层厚度 (9)7.2. 涂层吸附性 (9)7.3. 无六价铬要求 (10)7.4. 抗腐蚀盐务测试 (10)7.4.1. 基本要求 (10)7.4.2. 锌或锌合金钝化涂层最小抗腐蚀能力 (10)8. 实验报告 (12)8.1. 一般资料 (12)8.2. 抗拉伸强度≥1000 N/mm²的材料表面涂层的特殊要求 (12)8.3. 检验结果 (12)参考资料 (13)前言本文件被DIN NA 062-01-76 AA“电镀层”的标准委员会制定,主要用于盐务测试(NMP-Normenausschuss Materialprüfung)标准。
1.应用领域本标准适用于在铁的材料表面电镀和无六价铬的锌电镀以及锌合金涂层,其中锌合金的涂层包含镍或铁(锌/镍,锌/铁)以及其他合金成分。
- 1、下载文档前请自行甄别文档内容的完整性,平台不提供额外的编辑、内容补充、找答案等附加服务。
- 2、"仅部分预览"的文档,不可在线预览部分如存在完整性等问题,可反馈申请退款(可完整预览的文档不适用该条件!)。
- 3、如文档侵犯您的权益,请联系客服反馈,我们会尽快为您处理(人工客服工作时间:9:00-18:30)。
GERMAN STANDARD July 2008 p t i o n - K N O R R -B R E M S E S y s t e m e f ür S c h i e n e n f a h r z e u g e G m b H - C u s t . n o . 4987428 - S u b s . n o . 00849501/002/001 - 2008-06-24 10:34:55Metallic coatings –Electroplated coatings of zinc and zinc alloys on iron or steel with supplementary Cr(VI)-free treatmentDocument comsists of 13 pagesStandards Committee on Material Testing (NMP) within DINDIN 50979:2008-07c r i p t i o n - K N O R R -B R E M S E S y s t e m e f ür S c h i e n e n f a h r z e u g e G m b H - C u s t . n o . 4987428 - S u b s . n o . 00849501/002/001 - 2008-06-24 10:34:55ContentsPageForeword................................................................................................................................................3 1. Field of application.................................................................................................................3 2. Normative references.............................................................................................................3 3. Designation:............................................................................................................................4 3.1. Electroplated coatings...........................................................................................................4 3.2. Passivating .............................................................................................................................4 3.3. Sealing.....................................................................................................................................4 3.4. Essential areas (functional area)..........................................................................................5 3.5. Examples of designations.....................................................................................................5 4. Order data................................................................................................................................5 5. Base materials.........................................................................................................................6 6. Coating methods / Process technology...............................................................................6 6.1. Pretreatment and deposition of the zinc or zinc alloy coating..........................................6 6.2. Post-treatments......................................................................................................................6 6.2.1. Passivations ...........................................................................................................................6 6.2.2. Seals........................................................................................................................................7 6.3. Drum/Trestle (parts handling)...............................................................................................7 6.3.1. Drum parts..............................................................................................................................7 6.3.2. Trestle parts............................................................................................................................7 6.4. Hydrogen embrittlement........................................................................................................7 6.4.1. Basics......................................................................................................................................7 6.4.2. Method selection....................................................................................................................8 6.4.2.1. Materials with strengths < 1 000 N/mm 2...............................................................................8 6.4.2.2. Materials with strengths ≥ 1 000 N/mm 2.............................................................................8 7. Requirements for the coatings and test methods...............................................................9 7.1. Coat thickness........................................................................................................................9 7.2. Layer adhesion.......................................................................................................................9 7.3. Cr(VI) absence......................................................................................................................10 7.4. Resistance in short-term corrosion tests..........................................................................10 7.4.1. General..................................................................................................................................10 7.4.2. Minimum resistance of passivated zinc or zinc alloy coatings.......................................10 8. Test report .............................................................................................................................12 8.1. General information.............................................................................................................12 8.2. Special data for coating high-strength materials withtensile strength ≥ 1 000 N/mm ².........................................................................................12 8.3. Test results (12)References (13)DIN 50979:2008-07b sc r i p t i o n - K N O R R -B R E M S E S y s t e m e f ür S c h i e n e n f a h r z e u g e G m b H - C u s t . n o . 4987428 - S u b s . n o . 00849501/002/001 - 2008-06-24 10:34:55ForewordThis document has been formulated by the working committee NA 062-01-76 AA “Electroplated coatings” of the Standards Committee for Material Testing (NMP).1. Field of applicationThis standard applies for electrodeposited and Cr(VI)-free passivated zinc coatings and zinc alloy coatings on iron materials. The zinc alloy coatings contain nickel or iron (zinc/nickel, zinc/iron) as alloy components.The main purpose in the application of the coatings or coating systems is to protect components made from ferrous materials against corrosion.This standard defines the designations for the coating systems indicated above and specifies minimum corrosion activities in the described test methods as well as the minimum layer thickness necessary for this.2. Normative referencesThe documents cited below are necessary for the application of this document. In the case of dated references, only the edition referred to applies. In the case of undated references, the last edition of the document (including all amendments) referred to applies.E DIN 50969-1:2008-02, Prevention of hydrogen-induced brittle fractures caused during production in high-strength steel components – Part 1: Preventative measures 1)DIN EN 1403, Corrosion protection of metals – Electrodeposited coatings – Method of specifying general requirements DIN EN 15205, Determination of hexavalent chromium in corrosion protection layers – Qualitative analysisDIN EN ISO 3497, Metallic coatings – Measurement of coating thickness – X-ray spectrometric methods DIN EN ISO 9227, Corrosion tests in artificial atmospheres – Salt spray testsDIN 50979:2008-07c r i p t i o n - K N O R R -B R E M S E S y s t e m e f ür S c h i e n e n f a h r z e u g e G m b H - C u s t . n o . 4987428 - S u b s . n o . 00849501/002/001 - 2008-06-24 10:34:553. Designation:3.1. Electroplated coatingsThe electroplated coatings consists of zinc or zinc alloys corresponding to Table 1.Table 1 – Designation of the electroplated coatingsCode Definition Zn Zinc coating without added alloy partnerZnFe Zinc alloy coating with a percent by weight of 0.3 % to 1.0 % iron ZnNiZinc alloy coating with a percent by weight of 12 % to 16 % nickel3.2. PassivatingPassivating designates the production of conversion layers by treatment with suitable Cr(VI)-free solutions in order to improve the corrosion resistance of the coatings. Colourations are possible.As chromium (VI)-free passivations are new systems, a new nomenclature according to Table 2 has been adopted.Table 2 – Passivations3.3. SealingSeals increase the corrosion resistance and usually have a layer thickness up to 2 µm. Seals consist of Cr(VI)-free organic and/or inorganic compounds.Products that can be removed with cold cleaner (e.g. based on oil, grease, wax) are not considered as a seal within the scope of this standard.The effect of seals on the functional properties of the component, e.g. transition resistance, weldability, compatibility with working substance, bonded joints, are to be evaluated on a component-specific basis.DIN 50979:2008-07b sc r i p t i o n - K N O R R -B R E M S E S y s t e m e f ür S c h i e n e n f a h r z e u g e G m b H - C u s t . n o . 4987428 - S u b s . n o . 00849501/002/001 - 2008-06-24 10:34:55If there are special requirements for the surface functionality, the use of the seal as well as the type of sealing agent must be agreed, as the range of potential surface modifications through sealing is large. REMARK The interference colours formed through passivation are usually also remedied through sealing.Table 3 – SealsCode Description T0 Without seal T2 With seal3.4. Essential areas (functional area)In the case of components with complex shapes, in particular components with hollow spaces, it ispossible that the requirements for the resistance in the short-term corrosion tests and for the minimum thickness cannot be complied with in all areas of the electroplated surface. In these cases, the areas essential for the surface protection must be marked with a dot-dash line on the drawing.If no essential area is specified by the customer, the definition according to DIN EN 1403 applies.3.5. Examples of designationsDesignation for a zinc/nickel alloy coating on a component made from steel (Fe), a smallest local layer thickness of 8 µm (8) and iridescent passivated (Cn):Eletroplated coating DIN 50979 – Fe//ZnNi8//Cn//T0Designation for a zinc/iron alloy coating on a component made from steel (Fe), a smallest local layer thickness of 8 µm (8) and black passivated (Fn) and sealed:Eletroplated coating DIN 50979 – Fe//ZnFe8//Fn//T2For further information on the designation, see DIN EN 1403.4. Order dataThe customer must provide at least the following information to the coating company: a) Component strengths (with consideration of 6.4);b) Data on the component: Basic material, component manufacturing process, heat treatments; c) Data on the essential areas in conjunction with 3.4; d) Designation of the coating to be applied (see 3.5).If required, more detailed requirements for the coating properties and testing (e.g. appearance, sliding properties, media resistance) can be specified.If necessary, additional information on requirements or restrictions for the coating process can be given.DIN 50979:2008-07c r i p t i o n - K N O R R -B R E M S E S y s t e m e f ür S c h i e n e n f a h r z e u g e G m b H - C u s t . n o . 4987428 - S u b s . n o . 00849501/002/001 - 2008-06-24 10:34:555. Base materialsThe coating of components from low-alloy steels with coatings according to this standard is state-of-the-art. If other iron-based materials are present (e.g. cast or sintered materials, materials with distinct components of passivation-friendly alloy elements or also materials with special strength properties), it may be necessary to specially adapt the treatment processes (pretreatment, coating, post-treatment) and, if need be, implement additional measures in order to comply with the requirements of this standard. The coating company therefore needs to have detailed information on the composition, properties and production process of the components to be coated.When coating high-strength steel parts with a tensile strength ≥ 1 000 N/mm², the preproduction (e.g. material selection, hardening, joining) has to be carried out in such way that damage due to delayed hydrogen-induced brittle fractures is eliminated with a high degree of certainty.The components to be coated must not exhibit any material, processing or surface faults which can affect the corrosion protection and/or the appearance of the coatings in an adverse or unexpected manner.The impurities (corrosion products or scale, oil, grease, dirt etc.) occurring on the surfaces of the parts to be treated must be able to be removed in the cleaning and pretreatment processes normally utilised. An agreement concerning the surface quality might be necessary, if applicable.6. Coating methods / Process technology6.1. Pretreatment and deposition of the zinc or zinc alloy coatingIn order to ensure a reliable process sequence, the complete pretreatment and coating process, physical data (treatment times, temperatures) as well as all process chemicals must be recorded, documented and optimised if need be. The individual process intervention limits as well as the frequency of the monitoring and analysis processes must be defined. The resultant measures must be described and archived by the coating company.A typical process sequence is shown below: a) Alkaline degreasing (coordinated in line with the existing oil/grease-based surface films); b) Pickling (usually HCl, inhibited); c) Alkaline electrolytic degreasing (preferably anodic); d) Metal deposition; e) Post-treatment through passivation and, if necessary, sealing; f) Drying.6.2. Post-treatments6.2.1. PassivationsPassivations are conversion coatings and are created by immersing or spraying the components with passivation solutions. At the same time, the deposited coating reacts with the passivation solution to form a thin film protecting the metallic coating. Part of the coating is usually dissolved by the reaction.DIN 50979:2008-07b sc r i p t i o n - K N O R R -B R E M S E S y s t e m e f ür S c h i e n e n f a h r z e u g e G m b H - C u s t . n o . 4987428 - S u b s . n o . 00849501/002/001 - 2008-06-24 10:34:556.2.2. SealsAdditional organic and/or inorganic substances are applied onto or embedded in the passivation during the sealing.Layer accumulations can result, depending on the component geometry and process. These must be minimised, if possible, through suitable measures (e.g. blowing-off for trestle parts, movement of drum parts).6.3. Drum/Trestle (parts handling)6.3.1. Drum partsTypical drum parts are bolts, nuts and other small components. The components are introduced into the coating drums as bulk material then pretreated and provided with the coating while the drum is rotating. The drum rotation ensures that all components are coated comparably. However, surface damage can result due to the movement of the parts. It is possible to minimise the damage e.g. through reduced drum rotation or lower drop heights when emptying the drum. Nevertheless, drum coatings usually yield a lower corrosion resistance than is the case with trestle coatings. 6.3.2. Trestle parts This involves parts which have to be coated on the trestle owing to their size, design or, possibly, special requirements. During this, the parts are coated while positioned on trestles. Depending on the position of the components on the trestle, different layer properties (mainly layer thickness of the metallic coating) can result Optimisation is possible, for example, by using component-specific trestles.6.4. Hydrogen embrittlement6.4.1. BasicsThe steel parts to be coated can absorb hydrogen during the electroplating treatment for creating coatings according to this standard, e.g. during pickling, electrolytic cleaning and during the electroplating metal deposition. Active hydrogen diffused in the metal lattice preferably at energetically favourable areas (lattice structural faults, areas of high stress concentration).Hydrogen-induced, delayed brittle fractures can arise from this, while the critical interaction of: – material and material state (strength, hardness); – hydrogen absorption during the pretreatment and coating process; – mechanical parts stress, also locally depending on the design of the parts. have to be taken into account in particular.DIN 50979:2008-07 c r i p t i o n - K N O R R -B R E M S E S y s t e m e f ür S c h i e n e n f a h r z e u g e G m b H - C u s t . n o . 4987428 - S u b s . n o . 00849501/002/001 - 2008-06-24 10:34:55Figure 1 – Interaction of material, mechanical stress and hydrogen absorptionThe critical parameters for the material are the tensile strength and toughness. The hazard due to hydrogen increases as the strength increases.All steel parts with a tensile strength of R m ≥ 1 000 N/mm 2 (also locally restricted, e.g. for case-hardened or cold-formed joints or in weld seam areas) are deemed to be high-strength and are classified as critical.6.4.2. Method selection6.4.2.1. Materials with strengths < 1 000 N/mm 2The choice of treatment method is free insofar as the requirements comply with this standard and no damage to the usage properties occurs. 6.4.2.2. Materials with strengths ≥ 1 000 N/mm 2 Protection against delayed brittle fracture (hydrogen embrittlement) is paramount for the coating.The surface treatment method must be realised so that damage due to delayed hydrogen-induced brittle fractures is eliminated with a high degree of certainty. The procedure for dealing with potential defective coatings (peeling-off of coatings and new coatings) must be examined and consequences resulting from this described.The measures for minimising the risk of delayed hydrogen-induced brittle fractures and the processes necessary for this must be agreed between the customer/manufacturer and the coating company.The required process inspection and process testing accompanying production can typically be carried via stress tests on a sufficient number of suitable hydrogen-sensitive samples. The information given in E DIN 50969-1 must be observed.MaterialMechanical stress (also internal or localstress)Hydrogen in thematerialFracture, at critical interactionDIN 50979:2008-07b sc r i p t i o n - K N O R R -B R E M S E S y s t e m e f ür S c h i e n e n f a h r z e u g e G m b H - C u s t . n o . 4987428 - S u b s . n o . 00849501/002/001 - 2008-06-24 10:34:55Heat treatments are necessary to avoid brittle fractures. These must be carried out after the electroplating for the hydrogen effusion and, if necessary, also before the electroplating to relieve component internal stresses. For this, see also E DIN 50969-1:2008-02, 3.4 and 4.4.It is particularly important to ensure that the applied metallic coating as a diffusion barrier does not prevent the success of the heat treatment for the hydrogen effusion. The properties of the parts must not be altered detrimentally. REMARK Reference values for a heat treatment for the hydrogen effusion are given in Table 4:Table 4 – Reference values for heat treatment for hydrogen effusion after an electroplatingtreatment corresponding to this standard Tensile strengthR m N/mm 2 Heat treatment conditions in the air circulation furnace minimum retentiontime at parts temperature (215 ± 15) °Ch1,000 to 1,250 6 1,251 to 1,450 12 1,451 to 1,600 20 1,601 to 2,00024In conjunction with the coating of components at potential risk from hydrogen, tests as per E DIN 50969-2 must be carried out in addition to the above measures.7. Requirements for the coatings and test methods7.1. Coat thicknessThe methods according to Table 5 give minimum material thicknesses (d min ) and apply for the essential areas.The thicknesses of the zinc and zinc alloy coatings should preferably be determined with the X-ray spectrometric method as per DIN EN ISO 3497.Other applicable layer thickness measuring methods are e.g.: – Microscopic measurement as per DIN EN ISO 1463; – Coulometric method as per DIN EN ISO 2177; – Magnetic method as per DIN EN ISO 2178The layer thickness of passivations and seals is not included in the consideration.7.2. Layer adhesionThe test parts are stored for 30 minutes at (220 ± 10) °C and then immediately quenched in water with a temperature of 15 °C to 25 °C. Flaking and blister formation must not occur in the coating (thermal shock test as per DIN EN ISO 2819). REMARK A bending or surface grinding of the components, if feasible, is recommended as a further test for theadhesive strength.DIN 50979:2008-07c r i p t i o n - K N O R R -B R E M S E S y s t e m e f ür S c h i e n e n f a h r z e u g e G m b H - C u s t . n o . 4987428 - S u b s . n o . 00849501/002/001 - 2008-06-24 10:34:557.3. Cr(VI) absenceThe applied layer must be chromium-(VI)-free in agreement with DIN EN 15205.7.4. Resistance in short-term corrosion tests7.4.1. GeneralSalt spray tests as per DIN EN ISO 9227-NSS must be carried out. REMARK The corrosion performance of the coated components in use cannot be concluded from the results of theshort-term corrosion tests without more information. When using the components, very different load profiles(temperature, moisture, flow …) can occur, while only the specified, limited test climates occur in the short-term corrosion tests.7.4.2. Minimum resistance of passivated zinc or zinc alloy coatingsDepending on the coating system and test, minimum test times are specified concerning the test duration by which no corrosion products of the coating (white rust) or basic material (red rust) may occur. The essential areas of the tested component are to be evaluated.The requirements for the minimum resistance apply in the “coated state” as well as after a heat storage at 120 °C/24 h before the corrosion test. The heat storage is not necessary for the coating system Zn//An//T0.Non-agreed treatments (e.g. waxing, greasing) which can improve the resistance in the corrosion tests are not permissible.Influences (e.g. through sorting processes, transport, assembly or aggressive media), which can damage the corrosion protection properties of the coatings must be avoided before the corrosion test. An evaluation or limitation of the extent of the damage is not an object of this standard.The attainable corrosion resistance of coatings can also depend greatly on the components to be coated (material, geometry) in addition to the coating system and coating quality. In the case of components where an optimum coating quality cannot be achieved without further measures (e.g. due to material defects or complex component geometry), an agreement concerning lower corrosion resistance might be necessary.DIN 50979:2008-07b sc r i p t i o n - K N O R R -B R E M S E S y s t e m e f ür S c h i e n e n f a h r z e u g e G m b H - C u s t . n o . 4987428 - S u b s . n o . 00849501/002/001 - 2008-06-24 10:34:55Table 5 – Minimum layer thicknesses and test duration for passivated (transparent, iridescent)zinc and zinc alloy coatings for testing as per DIN EN ISO 9227-NSSMinimum test durationhType of surface protection layerVersion type Methodwithout coating corrosionwithout basic materialcorrosion(depending on the Zn or Zn alloy layer thickness)5 µm 8 µm 12 µm Drum 8 48 72 96 Electroplated zinc coating,transparent passivatedZn//An//T0Trestle 16 72 96 120 Drum 72 144 216 288 Electroplated zinc coating,iridescent passivatedZn//Cn//T0Trestle 120 192 264 336 Drum 120 192 264 360 Electroplated zinc coating,iridescent passivated and sealedZn//Cn//T2 Trestle 168 264 360 480 Drum 96 168 240 312 Electroplated zinc-iron alloy coating, iridescent passivatedZnFe//Cn//T0Trestle 168 240 312 384 Drum144 216 288 384 Electroplated zinc-iron alloy coating, iridescent passivated and sealed ZnFe//Cn//T2Trestle 216 312 408 528 Drum 120 480 720 720a Electroplated zinc-nickel alloy coating, iridescent passivatedZnNi//Cn//T0Trestle 192 600 720 720a Drum168 600 720 720a Electroplated zinc-nickel alloy coating, iridescent passivated and sealedZnNi//Cn//T2Trestle360720720a720aaTo limit the expense of the tests, the requirements are restricted to 720 h.DIN 50979:2008-07c r i p t i o n - K N O R R -B R E M S E S y s t e m e f ür S c h i e n e n f a h r z e u g e G m b H - C u s t . n o . 4987428 - S u b s . n o . 00849501/002/001 - 2008-06-24 10:34:55Table 6 – Minimum layer thicknesses and test duration for passivated (black) zinc and zinc alloycoatings for testing as per DIN EN ISO 9227-NSSMinimum test durationhType of surface protection layerVersion type Methodwithout coating corrosionwithout basic materialcorrosion(depending on the Zn or Zn alloy layer thickness)5 µm 8 µm 12 µm Drum 120 192 264 360 Electroplated zinc-iron alloy coating, black passivated and sealed ZnFe//Fn//T2Trestle168 264 360 480 Drum 168 480 720 720a Electroplated zinc-nickel alloy coating, black passivated and sealed ZnNi//Fn//T2Trestle240 600 720 720a Drum 48 480 720 720a Electroplated zinc-nickel alloy coating, black passivatedZnNi//Fn//T0Trestle72600720720aaTo limit the expense of the tests, the requirements are restricted to 720 h.The occurrence of mild visual changes (grey fog) without voluminous character is permissible and does not represent any impairment to the corrosion protection.There are still no universally recognised values for the corrosion resistance at present for electroplated zinc coatings, black passivated and sealed (Zn//Fn//T2).8. Test report8.1. General informationThe following must be tested by the coating company: a) Reference to this standard (i.e. DIN 50979);b) Conformity of the coatings with the requirements of this standard; c) Coating company for the surface protection;d) Applied technology (e.g. trestle or drum coating and applied coating system).8.2. Special data for coating high-strength materials with tensile strength ≥ 1 000N/mm²Designation and confirmation of the measures implemented for minimising the risk of delayed hydrogen-induced brittle fractures.8.3. Test resultsResults of the technological tests according to this standard (see section 7). The tests as per 7.2, 7.3, 7.4 must be carried out accompanying the process. The test bodies (supplier and/or subcontractor and/or independent test institute) are to be appointed.DIN 50979:2008-07b sc r i p t i o n - K N O R R -B R E M S E S y s t e m e f ür S c h i e n e n f a h r z e u g e G m b H - C u s t . n o . 4987428 - S u b s . n o . 00849501/002/001 - 2008-06-24 10:34:55ReferencesDIN EN ISO 1463, Metallic and oxide coatings – Measurement of coating thickness – Microscopical methodDIN EN ISO 2177, Metallic coatings – Measurement of coating thickness – Coulometric method by anodic dissolutionDIN EN ISO 2178, Non-magnetic coatings on magnetic substrates – Measurement of coating thickness – Magnetic methodDIN EN ISO 2819, Metallic coatings on metallic substrates – Electrodeposited and chemically deposited coatings – Review of methods available for testing adhesion。