加工中心不执行换刀故障诊断
加工中心机械手故障分析及诊断

( h njj lg r pc ds i r e inleho g 。 hnjj ua 470 。hn Z ag aec l eo a o ae n u rs o s oa cnl y Z agii H n n 2 00 C i ii oe f es i te p f s t o ae a)
( )故 障诊 断 : 障发 生后 , 3 故 除机 械手 不能 动作 外 。 床 其 机 它 部 分 都 工作 正 常 。用 手 工 换 刀后 , 机床 也 能 正 常 工 作 。因 此
认为是主轴定 向信号 ( 主轴定 向完 成后 , 送到 刀库 电机 的一个
信号 , 信号 电压为 2 V) 4 未送 到 P C, 使 P C没有换刀指 令。 L 致 L 查机床连接图 , C I 座 2 、3号上 测到 主轴定 向完成 信 在 N 插 22
加 工 中心 的 换 刀 可 分 为 有 机 械 手 换 刀 方 式 和 无 机 械 手 换 刀 方式 两 类 。大 多 数加 工 中 心 都 采 用 有 机 械 手 换 刀 方 式 。 这 种方 式下 , 械手 是 自动 换 刀 装 置 的 重 要 组 成 部 分 , 的 功 能 机 它 是 将 用过 的刀 具 送 回刀 库 , 从 刀库 上 取 出新 的刀 具 安 装 到 主 并
朱树红 , 罗生 夏
( 家界 航 空 工业 职 业技 术 学 院 , 南 张 家 界 4 70 ) 张 湖 2 00 摘 要 : 两 例 加工 中心 机 械 手故 障 , 析 诊 断 其故 障 的方 法 及 过程 , 介绍 分 总结 出排 除故 障 的 措施 。
关键词 : 中心; 加工 机械 手 ;L 故 障诊 断 P C;
刀 动 作 , 无 报警 。 且
加工中心不执行换刀故障诊断

加工中心不执行换刀故障诊断□杜江华在通常情况下,数控加工中心自动换刀功能出现故障的原因主要有:某个输入或输出信号不对,出现短路、断路,位置检测不到位,刀库乱刀,数刀计数器出错,继电器损坏;由于与之有联系的液压、气压系统,机械卡死、松脱等的影响。
但是有那么一些故障很少遇见,特别在资料不祥无提示,故障点隐蔽,报警信息少,甚至无报警情况下,需要仔细认真的去观察分析。
以下介绍几例供参考。
1、输入数据不规范造成停机机床配置:北京机电研究院制造的VMC1000C立式加工中心,数控系统为FANUC 0i-MA,带一刀套编码选刀方式的自动刀库。
故障现象:机床开始加工出现报警“OVERTRAVL -Y”,即Y轴负向超程启动循环加工后,未换刀便执行起刀点的语句,未按照正常路径走刀,Y轴负向已经硬限位。
分析处理:(1)查看系统参数号1320和1321(存储式行程检测)是正确的,说明软限位未改变。
有关行程的参数也无异常。
(2)有乱走刀、不换刀现象,怀疑位置环有问题。
执行另一段G56与故障段G58基本相同的加工程序(即工件坐标系不同),发现机床加工一切正常。
位置环损坏、机床参数发生改变或丢失的可能性排除。
(3)怀疑机床数据处理中断或时序控制错误等,按下急停按钮,关断机床电源,重新启动机床,运行有问题的程序,情况依旧。
(4)对照G56和G58的X、Y、A坐标值完全相同,唯有Z坐标有不同。
是否G58不能够使用了呢?决定将该程序段中的G58改成G54,在G54上设定G58的坐标值,再执行修改的程序,机床运行正常。
(5)由此判定,或是G58功能支持软件的宏程序发生错误,或是G58确认的坐标值没有被系统所认可(即NC给机床‘MT’的执行数据不同于设置的数据),而是记忆成为另外的数据,因为一旦运行程序其走刀的方向和位置都不对,显然后者是可能性较大。
于是,将G58的X、Y、Z和A的坐标值重新设置为“0”,按“REST”复位,再重新输入原来的坐标值,机床恢复了正常。
加工中心机械手换刀故障的处理

加工中心机械手换刀故障的处理一:故障现象我们公司使用的是韩国大宇生产的数控加工中心,发那科操作系统,工人在加工产品的过程中,由于装夹产品的错误,导致撞机,机械原点下移,机械手不能正常换刀。
二:处理方法:1.首先使用M39令,使机床处于维修状态,让机床后面机械手处理方式开关变成手动方式,让机械手回到原点状态。
2.如果机床不能做回原点操作,修改K12号参数。
3.回原点后经观察,机械原点不在机械手换刀位置,我们知道,主轴过低,机械手在换刀时会因为换刀位置过低而碰伤机床,完不成换刀工作;过高,机械手虽然能完成换刀工作,但机械手送到主轴后,因没有到达位置而卡刀不紧,造成掉刀现象。
4.我们知道,大宇数控加工中心执行换刀命令时,首先会执行零号程序,而零号程序中有G28 Z0指令,也就是说,Z轴不管停在任何位置,如果程序中有换刀指令,主轴先回机械原点,再执行换刀命令,就与台中精机生产的数控加工中心类似,一旦执行换刀指令,就会执行G30 Z0一样,机床先回第二机械原点,再执行换刀指令,从而完成换刀工作。
如果台中精机生产的数控加工中心主轴换刀位置无意中被破坏,可以通过调整1241号参数进行Z轴的上下定位,通过4031号参数的调整可以进行主轴定位角度的定位,因此,我们试图进行1240参数的调整,没有达到理想目的。
5.我们想办法调整机械原点限位块,使机械原点向上或向下移动,以便使机床停在最佳机械手换刀位置,但没有成功,我们不管怎么调整机械原点,机床都在一定的数值内变化着,就是没达到换刀位置,最后,我们采用调整伺服电机编码器的方法,让编码器旋转一个角度,通过这样的方法,我们才把主轴定位在最佳机械手换刀位置,伺服编码器旋转的角度可以对照显示屏调整。
三:可能原因由于误操作,伺服电机在快速行走的状况下,突然碰到强大阻力,在系统报警之前,机床虽然停止行走,但伺服编码器可能还会旋转一定的角度,当关机再开机后,机床的机械原点位置偏移就可以解释了,这就是撞机后机械手不能正常工作的原因。
加工中心换刀故障分析与维修

加工中心的常见故障中,换刀故障约占1/3,因此对其分析与处理很重要,本文通过具体实例分析其原因,并给出维修方法,供大家参考使用。
一、加工中心换刀过程或原理南昌高级技工学校实习车间所用加工中心型号为M CV/610,数控系统采用F ANUC0-MC。
正常换刀过程如下:Z轴回零,主轴定向。
刀库门开,(或机械手)前移抓刀,主轴松刀。
主轴上移(或机械手后移)刀具被拔出主轴孔。
刀库转至所需刀位,同时主轴自动吹净其刀具孔。
主轴下移(或机械手前移),刀具插入主轴孔并被夹紧。
刀库门关,刀库(机械手)后退,换刀完成。
二、主要故障实例1.刀库向前抓刀后停止,主轴不松刀分析处理:由现象知换刀在第(2)步停止,刀库前移动作已完成,压下相应限位开关就发信号通知NC系统动作完成,该信号未发出以致主轴不松刀,打开机床数控柜,检查限位输入信号未发现,推测限位开关问题,但用万用表检查开关却有信号,外接一线至NC系统,故障消失,原因是断线引起故障。
2自动换刀至第5步停止,主轴不装刀分析与处理:在M DI状态下,依次M19→M81→M82→M83→M84,动作均正常,排除电气部分故障,手动检查气缸亦有动作推测为气流不畅,检查气缸进气管,发现接头处漏气,重新安装后故障消失。
3.自动换刀至第2步,主轴松刀延时过久分析处理:换刀能完成说明NC系统正常,查阅有关延时的诊断DGN300~400,均正常值,但气缸动作时有时无,推断电磁阀问题,拆开电磁阀,阀芯磨损,更换新的后故障消失。
4.自动换刀主轴不定向,且CRT上出现警示1010、409分析处理:维修手册无警示1010、409之说明。
从其工作原理分析,自动换刀时,CNC系统发出主轴定向信号M19,经控制电路启动定向时间检测电路,磁传感器发出信号,经电路处理产生一系列慢转信号,当位置误差小于0.1,电路发出到达信号,通知CPU,发出主轴停止信号,同时切断定向时间检测电路,定向完成。
由现象知NC系统已发出定向指令M19,可能由于定向电路设定不合理引起,调整设定,故障不消失,检查主控板是否故障、调换依然,说明控制电路无问题,推断故障在伺服部分,用万用表检查晶体管模块有关端子间的电阻值。
加工中心刀库(斗笠、圆盘)常见故障诊断及解决对策

一. 斗笠刀库故障
原因:
1.刀盘电机、进刀电机、退刀电机相序相反
2.进刀到位、退刀到位的信号检测线路有问题
3.主轴松到、紧刀到位信号检测线路有问题或推刀距离有偏差
4.主轴定位角度有偏差
5.主轴第二参考点有偏差
6.刀库乱刀号
7.刀盘计数开关损坏或刀盘旋转不停止
解决对策:
1.调整电机接线相序
2.调节进刀、退刀感应开关位置,如损坏更换
3.调节松、紧刀位置开关和打刀缸推刀距离
4.调节主轴参数3207(三菱)参数4077(发那科)至合适角度
5.调节轴参数2038(三菱)参数1241(发那科)到合适坐标值及调节栅格量 6.做刀库刀号归零操作PLC开关16号(三菱),PMC开关K2.0(发那科) 7. 调节计数开关位置,如损坏则需更换
二. 圆盘刀库故障
原因:
1.刀盘电机、手臂电机相序相反
2.刀盘电机、手臂电机刹车松紧不当
3.刀套上及下位置有偏差或刀套气缸到位感应开关位置不合适 4.手臂扣刀位置有偏差,扣不紧,有异响
5.手臂未归零位,换刀动作不能继续
6.刀套号错乱。
加工中心机械故障诊断方法及常见故障维修
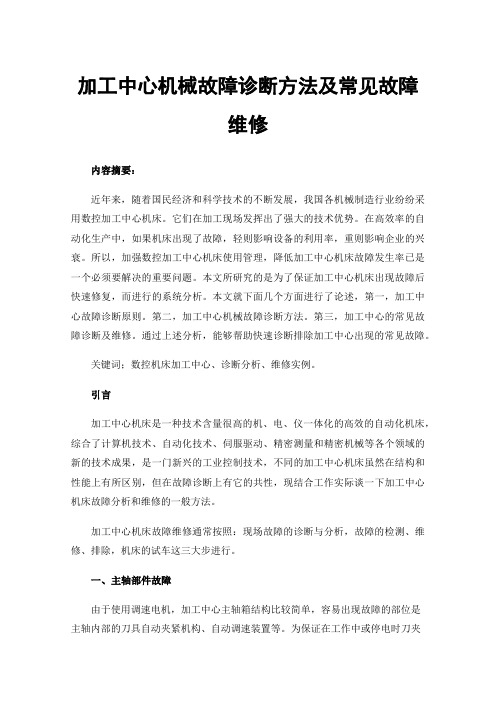
加工中心机械故障诊断方法及常见故障维修内容摘要:近年来,随着国民经济和科学技术的不断发展,我国各机械制造行业纷纷采用数控加工中心机床。
它们在加工现场发挥出了强大的技术优势。
在高效率的自动化生产中,如果机床出现了故障,轻则影响设备的利用率,重则影响企业的兴衰。
所以,加强数控加工中心机床使用管理,降低加工中心机床故障发生率已是一个必须要解决的重要问题。
本文所研究的是为了保证加工中心机床出现故障后快速修复,而进行的系统分析。
本文就下面几个方面进行了论述,第一,加工中心故障诊断原则。
第二,加工中心机械故障诊断方法。
第三,加工中心的常见故障诊断及维修。
通过上述分析,能够帮助快速诊断排除加工中心出现的常见故障。
关键词;数控机床加工中心、诊断分析、维修实例。
引言加工中心机床是一种技术含量很高的机、电、仪一体化的高效的自动化机床,综合了计算机技术、自动化技术、伺服驱动、精密测量和精密机械等各个领域的新的技术成果,是一门新兴的工业控制技术,不同的加工中心机床虽然在结构和性能上有所区别,但在故障诊断上有它的共性,现结合工作实际谈一下加工中心机床故障分析和维修的一般方法。
加工中心机床故障维修通常按照:现场故障的诊断与分析,故障的检测、维修、排除,机床的试车这三大步进行。
一、主轴部件故障由于使用调速电机,加工中心主轴箱结构比较简单,容易出现故障的部位是主轴内部的刀具自动夹紧机构、自动调速装置等。
为保证在工作中或停电时刀夹不会自行松脱,刀具自动夹紧机构采用弹簧夹紧,并配行程开关发出夹紧或放松信号。
若刀具夹紧后不能松开,则考虑调整松刀液压缸压力和行程开关装置或调整碟形弹簧上的螺母,减小弹簧压合量。
维修实例1、故障现象:HTM4228G龙门式加工中心加工过程中出现镗孔精度下降,圆度超差,故障分析:首先检查主轴定心锥孔位置和镗刀杆结合部,发现主轴定心锥孔表面有轻微研伤,用千分表检查主轴锥孔直线度超差0.08mm,根部圆跳动0.06mm,远端圆跳动0.10mm。
斗笠式刀库更换过程中的常见故障

数控机床刀库的故障率相对较高。
根据以往的工作经验,对斗笠式刀库换刀常见故障过程总结了以下原因:示例1故障现象:CNC系统发出换刀命令,刀库不运行。
原因分析:1检查机器的运行模式是否正确?机器是否锁定?指令是否正确?虽然这些原因很简单,但初学者也很容易犯错误。
2检查CNC机床的压缩空气,检查气压是否在要求的范围内。
通常,数控机床中常用的压缩空气压力在0.5MP至0.6MP之间。
如果压缩空气压力低于此范围,则在换刀过程中由于压力不足,刀库将无法运行。
3检查刀库的初始值。
状态正常吗?检查传感器A和E的状态是否良好?发送到CNC系统PLC的入口信号是否正确?可以通过CNC系统提供的PLC地址诊断功能进行检查。
示例2症状:刀库移动到主轴的中心,但不执行下一个动作。
原因分析:1检查刀库到主轴侧的确认信号传感器B和E是否良好?发送到CNC系统PLC的信号状态是否正常?这种故障现象主要是由传感器不良引起的;2如果传感器状态和信号正常,请检查主轴工具是否拧紧?3检查主轴定位是否完成?4确认第一个参考点返回是否完成?示例3故障现象:刀库从主轴上取刀并且不会旋转到目标刀具位置。
原因分析:一般刀库的旋转电机由三相异步电机驱动。
如果发生上述故障,应进行以下检查:1参考机床电气图,用万用表和其他测试工具检查电机启动电路是否正常。
2检查刀库的功率是否正常?交流接触器和开关是否正常?一般情况下,刀库主回路部分的电源为三相交流380V电压,交流接触器线圈控制部分的电源为交流110V或直流24V。
检查该部分电路,确保电路正常;3如果上述部件正常,在这种情况下,是否检查了刀库驱动电机的正常操作?4如果消除了上述故障,请考虑刀库机械部件是否有干涉?旋转驱动电机和刀库之间的连接是否断开?示例3故障现象:主轴抓住刀具后,刀库不会移回初始位置。
原因分析:1检查气源压力是否在要求的范围内?2检查刀具驱动电机控制电路是否正常?刀库可以正向和反向控制电机,实现刀库的左右平移。
加工中心换刀故障处理

故 障现象 , 多询问操作者 , 弄清故障的种类 、 频繁程度及 重复性 , 机床 运转情况 。 还要利用机床报警信息 和 自诊断功能判断故障。
W1 3. 09 -41
造成动作不到位 , 检测 开关检测不到信号 ; ②检测开关 失灵。使 用一薄铁片感应接近开关 , 确认开关 良好 。 接着检查换刀系统机 械手的两个开关 ,发现机械臂停在中间位置 ( 没有靠 近两个开
指令 , 执行 中主轴实际转速高于输入转速 。按下急停按钮 , 用手
盘动主轴卡盘 , 与其他正常机床比较 , 屏幕上反 映出的转速没有
L T C一 5 0 B A N 车床 故 障处理 一例
秦
1 . 故障现象
L T C 一 5 0 B / W 车床采用 F A N U C 0 i — T C 系统 , 主 轴 驱 动 器 型
伟
许油污 ,日积月 累,油污等顺着线路流人到下端 的编码器插头 内。 油污 内夹杂有皂化液及加工 中出现 的金属粉末等异物 , 进入
插孔 内可造成某些插脚之间 出现非正常导通 。经主轴外置编码 器反馈 电缆一 主轴驱动器 J Y A 3 插 孔- * J Y 7 B,接至机床数控系
号A 0 6 B 一 6 1 1 1 - H 0 4 5 # H 5 5 0 。机 床加工过程 中无报警 , 操作 人员 反映加工 出的产 品有较 明显颤纹 , 且单件产 品加工 时间变短 , 但
使得 P L C被迫中断执行程序 而引起换刀故障 。 据此判断故障原
警( 刀库换刀位置错误 ) 。
2 . 故障排除
根据报警信息 , 判断故 障发生在换刀系统和刀库两部分 。 正 常换刀时机床机 械臂位置检测开关信号应 为 1 ,换刀 系统在机 械臂位置检测 开关 信号为 0 , 表示无 检测开关信 号送到 C N C单 元的输入接 口, 机床保 护功 能导致换刀被 中断 , 另外刀库换 刀位
- 1、下载文档前请自行甄别文档内容的完整性,平台不提供额外的编辑、内容补充、找答案等附加服务。
- 2、"仅部分预览"的文档,不可在线预览部分如存在完整性等问题,可反馈申请退款(可完整预览的文档不适用该条件!)。
- 3、如文档侵犯您的权益,请联系客服反馈,我们会尽快为您处理(人工客服工作时间:9:00-18:30)。
维护与修理
17 设全禄
摘要 着重讨论半波能耗制动元件的选择 ,在 Y/ △启动 、绕线电动机 、多速电动机中的应用 ,及其 Y/ △ 控制原理和接线方法 。
笔者“半波能耗制动的探讨与应用”一文在《设备管理与维 修》2000 年 10 期发表后 ,许多读者已将此技术应用于设备改造 之中 ,下面就改造中遇到的问题进行讨论 ,供同行参考 。
源 ,电动机定子通入直流电流 ,旋转磁场转速为零 ,由于转子带 着负荷继续转动 ,转子线圈切割磁力线 ,转子绕组便产生感应电 动势 ,这时电动机变成了发电机 ,若转子绕组形成闭合回路 ,转 子绕组中便有电流流过 ,根据右手定则电磁力 F 的方向与转子 的旋转方向相反 ,形成制动力矩 。所以 ,绕线式电动机使用半波 能耗制动时 ,控制方式和定子接线方法与鼠笼式相同 ,且转子的 三相绕组必须构成闭合回路 ,才能够获得制动力矩 。在制动电 压一定的情况下 ,调节转子回路的电阻值 ,便可以调节制动力矩 的大小 。
11 输入数据不规范造成停机 机床配置 :北京机电研究院制造的 VMC1000C 立式加工中 心 ,数控系统为 FANUC Oi - MA ,带一刀套编码选刀方式的自动 刀库 。 故障现象 :机床开始加工出现报警“OVERTRAVL - Y”,即 Y 轴负向超程启动循环加工后 ,未换刀便执行起刀点的语句 ,未按 照正常路径走刀 , Y 轴负向已经硬限位 。 分析处理 : (1) 查看系统参数号 1320 和 1321 (存储式行程检测) 是正确 的 ,说明软限位未改变 。有关行程的参数也无异常 。 (2) 有乱走刀 、不换刀现象 ,怀疑位置环有问题 。执行另一 段 G56 与故障段 G58 基本相同的加工程序 (即工件坐标系不 同) ,发现机床加工一切正常 。位置环损坏 、机床参数发生改变 或丢失的可能性排除 。 (3) 怀疑机床数据机处理中断或时序控制错误等 ,按下急停 按钮 ,关断机床电源 ,重新启动机床 ,运行有问题的程序 ,情况依 旧。 (4) 对照 G56 和 G58 的 X 、Y、A 坐标值完全相同 , 惟有 Z 坐 标有不同 。是否 G58 不能够使用了呢 ? 决定将该程序段中的 G58 改成 G54 ,在 G54 上设定 G58 的坐标值 ,再执行修改的程序 , 机床运行正常 。 (5) 由此判定 ,或是 G58 功能支持软件的宏程序发生错误 , 或是 G58 确认的坐标值没有被系统所认可 (即 NC 给机床‘MT’ 的执行数据不同于设置的数据) ,而是记忆成为另外的数据 ,因 为一旦运行程序其走刀的方向和位置都不对 ,显然后者是可能 性较大 。于是 ,将 G58 的 X 、Y 、Z 和 A 的坐标值重新设置为“0”, 按“REST”复位 ,再重新输入原来的坐标值 ,机床恢复了正常 。 由此看出 ,该故障是由于不规范的输入数据 ,使面板给 NC 的数据发生错误引起的 。采取消除数据 、重新输入的方法 ,故障 得以排除 。 21 系统参数受到干扰 机床配置 :宁江机床 (集团) 股份有限公司生产的 THM6350 卧式加工中心 。数控系统为 : FANUC Oi - MA ,配有随机选刀方 式的链式自动刀库 (32 把) 和机械手 。
加工中心不执行换刀故障诊断
杜江华
在通常情况下 ,数控加工中心自动换刀功能出现故障的原 因主要有 :某个输入或输出信号不对 ,出现短路 、断路 ,位置检测 不到位 ,刀库乱刀 ,数刀计数器出错 ,继电器损坏 ;由于与之有联 系的液压 、气压系统 ,机械卡死 、松脱等的影响 。但是有那么一 些故障很少遇见 ,特别在资料不祥无提示 ,故障点隐蔽 ,报警信 息少 ,甚至无报警情况下 ,需要仔细认真的去观察分析 。以下介 绍几例供参考 。
竹市 618201
〔编辑 武思明〕
18
设备管理与维修 2004 №4
维护与修理
故障现象 :在自动加工方式下 ,每当执行换刀语句 (M06) 时 , 突然跳到下面的插补语句 ,未换刀而直接以原来的刀具加工 。同 时 ,后面刀库中刀具仍然在预选过程中 。无任何报警信息 。
分析处理 : (1) 怀疑到 NC 加工语句的正确性 ,仔细检查没有发现任何 问题 。 (2) 在通常情况下 ,不能换刀或者不能执行换刀语句的问题 是很常见的 ,此例中 ,后面的自动刀库中刀具仍然在预选过程 中 ,而且已经在利用原来的刀具加工 。为了确保人身和设备的 安全 ,必须即时停机 。为了进一步查找原因 ,在 MDI 方式下单 独执行换刀语句 (如 “: T2 ;M06 ;”) ,刀具能够交换 。由此确定不 是执行机构本身的问题 。 (3) 是否系统操作不规范 、电源电压波动大或其它外界干扰 因素 ,导致系统偶然出现紊乱 ? 重新启动运行 ,故障依旧 。 (4) 在 MDI 方式下 ,执行换刀和插补语句连贯时 (如 “: T2 ; M06 ; G01X20010Y15010 ;M30 ;”) 试运行的现象与自动方式下完全 一样 。决 定 进 一 步 查 看 PMCPRM 参 数 画 面 中 的 定 时 器 ( TI MER) 、计数器 (COUNTER) 、数据表 (DATA) 、保持继电器 ( KEEP2 RL) ,厂家没有完整的提供标准参数和具体对照含义 ,本工段有 一完全相同的该型加工中心 ,将两设备设置到相同的模式下 ,以 正常的参数作为参考标准一一排除 ,发现 KEEPRL 中 K03 # 1 = 1 ;而正常的 K03 # 1 = 0。该类数据通常作为定义或支持某个功 能的实现 。在确保即时停机的情况下 ,修改该位为“0”,试运行 。 机床恢复正常 。 系统中设置的各个参数在不规范操作 、车间电源电压不稳 和加工环境恶劣等影响下 ,很容易发生改变 ,甚至丢失 。本例中 问题出在参数发生了改变 。 31 元器件老化 ,造成感应不灵敏 机床配置 :由 STARRF∋SMASCHINEG AG 进口的 HX - 151 型立式加工中心 ,数控系统为 :Allen - Bradley series 10 NC。自动 刀库采用刀套编码方式选刀 。 故障现象 :刀库不能正常换刀 ,单独执行换刀也不行 ,一段 时间停机待查 。刀库换刀的主要动作是 :旋转选刀 、左运动 、上 运动 、下运动 、右运动 。报警信息为 “: 无法执行下去”。 分析处理 : (1) 报警信息提示不明确 。初步认为换刀过程中某条件未 得到满足 ,逐一查找刀库门开关 、刀库电机 、计数开关 、传动位置 准备 、按钮 、驱动等等 ,以及液压与气动部分 ,均无结果 。24V 电 源也正常 。 (2) 测试各个动作的逻辑顺序 ,均正常 ,但却总是执行到中 间某一个环节停顿下来 。仔细观察发现 ,每到了不能执行的那
一步 ,PLC 的动作输入信号灯迅速闪亮一下 。于是怀疑 PMC 块 的内部 PCB 板有故障 ,虚焊或者接触松动导致电流信号不稳 。 更换新的备件再试 ,故障依旧 。
(3) 经一段时间后 ,发现输入部分的主轴准停信号灯相当微 弱 ,有微小的闪动状态 ,亮度比周围的暗淡一些 ,偶尔甚至熄灭 。 联想到 ,通常换刀与主轴准停功能有联系 ,经查发现主轴准停接 近开关已经松动 ,感应也不灵敏 ,时好时坏 ,更换调整后机床换 刀功能恢复正常 。
一 、半波能耗制动元件的选择 选择电器元件 ,首先要计算出制动电流 IZ ,根据制动电流 来合理选择元件 。先测量出电动机任意两根进线之间的电阻 RO 值 ,再测量出电动机带着传动装置运转的轻载线电流 IQ ,将 测得的数据分别代入经验公式 ,便可以求出制动电流 IZ 和限流 电阻 R 值 : IZ = KIQ R = 220 ×0145/ IZ - RO 220V AC 的反向峰值电压为 314V ,所以 ,晶体二极管选用 400V ,额定电流大于 1125 IZ 即可 。由于通电时间小于 2s ,在不 频繁制动的情况下晶体二极管可以不用散热片 ,限流电阻功率 取 1/ 4W。系数 K 一般取 315~4 。由于磁饱和的原因 ,系数大 于 4 ,制动电流超过一定值 ,制动力矩不再增大 ,电动机发热量 增大 ,反而有害无益 。 例 1 一台 J02 - 32 - 4 型 3kW 电动机 ,Y接法 ,传动装置转速 高 ,惯量大 ,测得 RO 为 4138Ω ,轻载线电流 IQ 为 415A , K 取 4。 IZ = KIQ = 4 ×415 = 18A R = 220 ×0145/ IZ - RO = 99/ 18 - 4138 = 1112Ω 则 PR = IZ2 R/ 4 = 182 ×1112/ 4 = 90172W 所以 ,限流电阻选用 111Ω、100W 的法琅电阻 ,二极管选用 400V、2CZ30A 的硅整流二极管 。 例 2 一台 J02 - 52 - 4 型 10kW 电动机 , △接法 ,传动装置 转速较高 ,惯量不大 ,轻载线电流为 1015A ,在 Y 接法时测得 RO
三 、在 Y/ △启动控制线路中的应用 容量较小的电动机一般采用直接启动 。对于较大容量的电 动机 ,则需要采用降压启动 。电压 380V、绕组接法为 △或 △/ Y 的较大容量电动机 ,轻载启动时 ,多采用 Y/ △启动 。启动时绕 组为 Y连接 ,待转速升高到一定程度时 ,再将绕组换接为 △连 接 。停车断电后 ,三相绕组互相不连接 。这种启动控制线路 ,在 使用半波能耗制动时 ,可将绕组 Y 接 ,将其中两个绕组串联后 再接入半波直流 。其工作原理图如图 1 所示 。 当使用按钮操作时 ,按动 SB2 ,接触器 KM1 、KM3 吸合 ,电动 机绕组的 6 、4 、5 端由 KM3 主触点短接成为 Y 点 ,三相电源经 KM1 的主触点接入电动机三相绕组 ,电动机启动或运转 。KM1 自锁 , KM1 的辅助常闭点互锁住 KM4 。再按动 SB3 , KM3 释放 , Y 点断开 , KM2 吸合并自锁 ,电动机转入 △运转 。按下 SB1 ,接触 器 KM1 、KM2 释放切断三相电源 , KM1 的辅助常闭互锁点复位 接 通 KM4 。KM4吸合使 KM3也同时吸合 ,半波直流接到电动机
其实 ,本例故障的原因是一般的问题 ,因厂家资料上未提及 这一点而花费了大量时间 ;同时因主轴准停位置已到位 ,而电流 信号的微弱不易觉察 ,给诊断增加了难度 。因此 ,在诊断中要充 分利用发散思维 ,多观察 ,多分析 ,不要一味地依赖于厂家资料 。