催化裂化过程反应化学的进展
我国催化裂化工艺技术进展_许友好
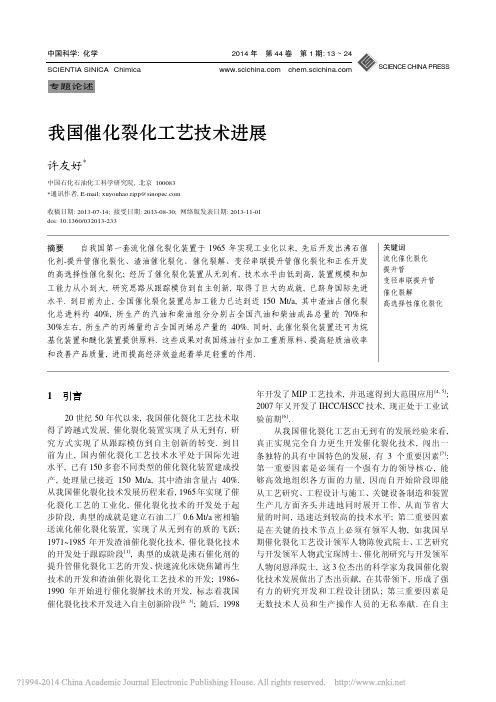
《中国科学》杂志社
SCIENCE CHINA PRESS
我国催化裂化工艺技术进展
许友好*
中国石化石油化工科学研究院, 北京 100083 *通讯作者, E-mail: xuyouhao.ripp@ 收稿日期: 2013-07-14; 接受日期: 2013-08-30; 网络版发表日期: 2013-11-01 doi: 10.1360/032013-233
年开发了 MIP 工艺技术, 并迅速得到大范围应用[4, 5]; 2007 年又开发了 IHCC/HSCC 技术, 现正处于工业试 验前期[6]. 从我国催化裂化工艺由无到有的发展经验来看 , 真正实现完全自力更生开发催化裂化技术 , 闯出一 条独特的具有中国特色的发展 , 有 3 个重要因素 [7]: 第一重要因素是必须有一个强有力的领导核心 , 能 够高效地组织各方面的力量 , 因而自开始阶段即能 从工艺研究、工程设计与施工、关键设备制造和装置 生产几方面齐头并进地同时展开工作 , 从而节省大 量的时间, 迅速达到较高的技术水平; 第二重要因素 是在关键的技术节点上必须有领军人物 , 如我国早 期催化裂化工艺设计领军人物陈俊武院士、 工艺研究 与开发领军人物武宝琛博士、 催化剂研究与开发领军 人物闵恩泽院士, 这 3 位杰出的科学家为我国催化裂 化技术发展做出了杰出贡献, 在其带领下, 形成了强 有力的研究开发和工程设计团队 ; 第三重要因素是 无数技术人员和生产操作人员的无私奉献 . 在自主
产率分布 (%)
汽油性质
烯烃 芳烃 MON
a) 抚顺二厂第一套装置的标定数据; b) 高桥分公司渣油催化裂化装置标定数据
入大气中. 再生器烧焦所用的空气由主风机供给, 大 部分空气分成两路进辅助燃烧室 , 以较高的线速通 过分布板小孔, 进入再生器密相床层, 与催化剂接触 进行烧焦; 少量的空气经增压机增压, 增压后送到密 相提升管, 作提升空气用. 密相流化催化裂化装置加 工大庆蜡油时典型的产物分布和汽油产品性质列于 表 1[7]. 兰州炼油厂于 1965 年 12 月建成了我国第一套 3 kt/a 的微球催化剂生产装置, 生产出合格的微球催 化剂. 随后, 微球催化剂应用于我国第一套催化裂化 装置, 并取得满意的工业应用结果. 随着催化裂化装 置的增多以及加工能力的增加, 1970、1976 和 1978 年 相继在长岭炼油厂、 齐鲁石化公司催化剂厂和石油六 厂建成投产年产分别为 6、4.5 和 2 kt 的微球催化剂 生产装置, 从而形成了我国 4 个裂化催化剂制备基地[9].
催化裂化催化剂的发展历程及研究进展
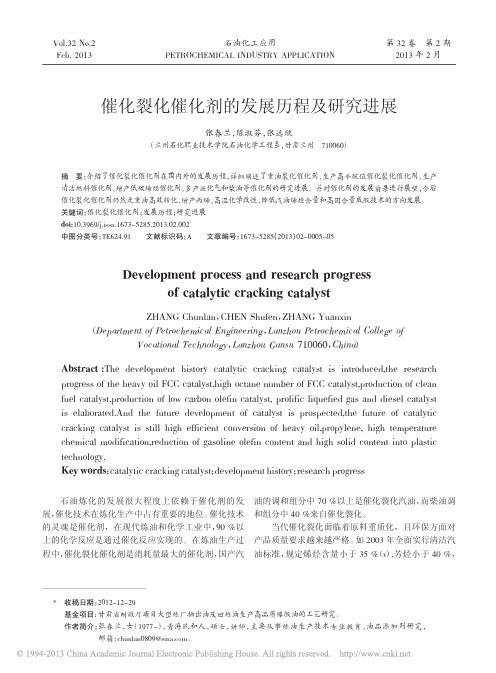
催化裂化催化剂的发展历程及研究进展张春兰,陈淑芬,张远欣(兰州石化职业技术学院石油化学工程系,甘肃兰州710060)摘要:介绍了催化裂化催化剂在国内外的发展历程,详细阐述了重油裂化催化剂、生产高辛烷值催化裂化催化剂、生产清洁燃料催化剂、增产低碳烯烃催化剂、多产液化气和柴油等催化剂的研究进展。
并对催化剂的发展前景进行展望,今后催化裂化催化剂仍然是重油高效转化、增产丙烯、高温化学改性、降低汽油烯烃含量和高固含量成胶技术的方向发展。
关键词:催化裂化催化剂;发展历程;研究进展doi:10.3969/j.issn.1673-5285.2013.02.002中图分类号:TE624.91文献标识码:A文章编号:1673-5285(2013)02-0005-05Development process and research progress of catalytic cracking catalystZHANG Chunlan ,CHEN Shufen ,ZHANG Yuanxin(Department of Petrochemical Engineering ,Lanzhou Petrochemical College ofVocational Technology ,Lanzhou Gansu 710060,China )Abstract :The development history catalytic cracking catalyst is introduced,the researchprogress of the heavy oil FCC catalyst,high octane number of FCC catalyst,production of clean fuel catalyst,production of low carbon olefin catalyst,prolific liquefied gas and diesel catalyst is elaborated.And the future development of catalyst is prospected,the future of catalytic cracking catalyst is still high efficient conversion of heavy oil,propylene,high temperature chemical modification,reduction of gasoline olefin content and high solid content into plastic technology.Key words :catalytic cracking catalyst ;development history ;research progress*收稿日期:2012-12-29基金项目:甘肃省财政厅项目大型炼厂抽出油及回炼油生产高品质橡胶油的工艺研究。
催化裂化催化剂的发展历程及研究进展

催化裂化催化剂的发展历程及研究进展催化裂化是一种重要的石油加工技术,通过将石油分子在催化剂的作用下进行裂解,得到高附加值的产品,如汽油和石脂油。
催化裂化催化剂的发展历程可以追溯到20世纪初,经过了多个阶段的演进和改进。
本文将详细介绍催化裂化催化剂的发展历程及研究进展。
20世纪初,催化裂化催化剂主要采用天然矿物催化剂,如石英、蛭石等。
这些催化剂具有一定的催化活性,但缺乏稳定性和选择性,难以应对复杂的原料和严苛的工业操作条件。
20世纪30年代,随着石油需求的增加和技术的进步,人们开始研发新型催化剂。
那时,主要采用的是氧化物催化剂,如铝、硅等。
这些催化剂的活性和稳定性有了一定的提升,但仍然存在一些问题,如选择性不高、催化剂寿命短等。
20世纪50年代,人们开始尝试使用酸性功能组分的催化剂,如酸化铁、硫酸等。
这些催化剂具有较高的催化活性和选择性,但具有腐蚀性,容易造成催化剂失效和设备损坏。
20世纪60年代,人们将焦油催化裂化硅铝酸催化剂推向了催化裂化工业化生产的舞台。
这种催化剂具有良好的热稳定性和选择性,能够实现高效的催化裂化反应。
焦油催化裂化硅铝酸催化剂的应用推动了石油工业的发展,成为当时催化裂化的主流技术。
近年来,催化裂化催化剂的研究进展主要集中在以下几个方面:1.催化剂结构设计:通过调控催化剂的孔径分布、酸中心密度和酸强度等结构参数,以提高其活性、选择性和稳定性。
常见的结构设计方法包括合金化、钾的添加、微介孔化等。
2.催化剂负载材料研究:将催化剂负载在合适的载体上,可以提高催化剂的分散性和稳定性。
常用的载体材料包括Al2O3、SiO2、TiO2等。
3.催化剂表面改性:通过表面改性的方法,如纳米粒子修饰、溶胶-凝胶法制备等,可以改变催化剂的活性中心和表面酸性,以提高其催化效果。
4.新型催化剂开发:人们正在探索使用新型催化剂,如纳米材料、金属有机骨架材料(MOFs)等,以提高催化裂化过程的效率和选择性。
浅谈催化裂化技术进展

广
州
化
工
V0 1 . 4l No . 8 Apr il .2 01 3
G u a n g z h o u C h e mi c a l I n d u s t r y
浅 谈 催 化 裂 化 技 术 进 展
张 宇 ,杨 进华
发展具有 以下特点 :技术相对成熟 ;能大量生产高辛烷值 汽油组 分 ;转化深度大 ,轻质油品和液化气收率高 ;装置压力低 ,操作 条件相对缓和,投资省 ;丙烯 、丁烯等利用价值高。 催 化 裂 化 近 几 年 面 临着 原 料 重 质 化 、高 硫 化 及 环 保 法 规 1 3 益 严 格 等 重 大 问 题 。化 解 这 些 问 题 需 要 开 发 新 的工 艺 和 技 术 , 这就需要总结前人的研究成果 ,对传 统的催化裂 化工艺过 程反 应化学 的认识进行分析和总结 ,以便更 深刻地认识 催化裂 化过 程反应化学规律 ,并 进行创新 。现从工 艺及 反应 器两方 面进展
管 反应 器 、双 提 升 管 反 应 器 、下 行 式催 化 裂化 反 应 器 几 个 方 面 阐述 了 催 化 裂 化 反 应 器 的 进 展 。最 后 展 望 了未 来 催 化 裂 化 工 艺 和 反
应 器 的 发展 趋 势 。
关键 词 :催化裂化;工艺;反应器; 趋势
中图分 类 号ቤተ መጻሕፍቲ ባይዱ:T E 6 2 4
艺 根 据组 分选 择性 裂化 的原 理 ,将 提 升 管 反 应 器 从 底 部 到 顶 部
依次设计 为汽油反应 区 、重质油 反应 区、轻质 油反应 区和总反 应深度控 制区。在不 同的反应 区域对 裂化性能不 同的组分 进行 选 择性 裂化 ,达 到 同时 多产 液 化 气 和 柴 油 的 目的 。在 催 化 剂 方
催化裂解制烯烃工艺及催化剂研究进展

催化裂解制烯烃工艺及催化剂研究进展摘要:低碳烯烃(乙烯、丙烯、丁烯和丁二烯等)是非常重要的基本有机化工原料,特别是乙烯的生产能力常被视为一个国家和地区石油化工发展水平的标志。
由于储能电池技术井喷式发展和环保要求进一步严格,电动汽车凭借行驶过程近零污染、节能、低使用成本的优势,替代燃油汽车成为不可逆转的发展趋势,随之而来将是交通用油消费量急剧下降。
因此,石油加工企业应提前布局实现由“燃油型”向“化工型”转型升级。
关键词:催化裂解制;烯烃工艺;催化剂引言低碳奥氏体是生产聚合物(聚乙烯和聚丙烯)的主要化学材料之一,也是石化工业的主要产品之一。
目前国内乙烯和丙烯供应不足,乙烯自给率约为64%,丙烯自给率约为77%,仍需大量进口。
此外,丙烯/乙烯需求比率上升,而产量比率下降。
随着化学工业的发展,对低碳奥氏体的需求迅速增长,其产量已成为经济发展的重要指标。
低碳奥氏体主要是通过热裂解或催化裂解获得的,其中热裂解技术是制造低碳奥氏体的主要技术,但热裂解反应温度高,二氧化碳排放量大;催化裂化反应温度低、目标产物收率高已成为近年来该技术的发展和应用前景。
用于生产低碳烯丙烯的原料可以是乙烷,丙烷,丁烷,也可以是轻/重型油脂,汽油,减压柴油等。
由于催化剂是影响催化裂解过程的重要因素,因此本文综述了轻质(轻油)作为低碳奥氏体催化剂生产率原料的研究进展。
1.催化性能影响因素制备方法对催化性能的影响,制备方法影响着金属颗粒在载体上的分散程度、载体与金属的相互作用力以及金属颗粒大小,从而影响催化剂的性能。
甲烷催化裂解反应中常用的制备方法有浸渍法、熔融法和共沉淀法等。
Guo等使用浸渍法和共沉淀法制备了一种由混合金属氧化物和氧化铝负载的Ni基催化剂。
研究发现与共沉淀法相比,浸渍法制备的催化剂中Ni颗粒发生了团聚。
这主要是因为在共沉淀法制备的催化剂中,Ni与载体之间的强相互作用力抑制了Ni颗粒的团聚。
Lazaro等比较了浸渍法和熔融法制备的Ni/TiO2催化剂的活性,研究发现浸渍法制备的催化剂初始活性较高,氢气产率为80%,但在反应200分钟后氢气产率迅速下降至40%。
催化裂化轻汽油醚化工艺的技术进展

催化裂化轻汽油醚化工艺的技术进展随着环境保护要求的日益严格与技术发展的需求,我国于2003年7月开始在全国实行新配方汽油(亦称清洁汽油)标准,要求车用汽油中烯烃的体积分数不大于35%。
总的来看,清洁汽油发展的趋势是低硫、低芳烃、低烯烃、低蒸气压和较高的辛烷值。
在我国,催化裂化(FCC)汽油占成品汽油的80%以上,其特点是烯烃含量高。
因此生产清洁汽油必须降低烯烃含量,而合理利用FCC汽油中的轻烯烃既可降低烯烃含量又可提高汽油辛烷值。
FCC轻汽油醚化生产混合醚工艺可将FCC轻汽油中的活性烯烃(能够进行醚化反应的烯烃)转化为叔烷基醚,不但降低了汽油中的烯烃含量,还可提高汽油的辛烷值和氧含量,并可降低汽油的蒸气压。
因此,FCC轻汽油醚化技术是生产环境友好清洁汽油的理想技术之一。
由于我国汽油辛烷值较低,烯烃含量高,在我国加快推广和应用FCC轻汽油醚化技术尤为重要。
FCC汽油中有大量的C4~11活性烯烃,随碳数的增加,活性烯烃的含量显著增加,同时醚化反应的转化率下降,醚化产物的辛烷值降低。
因此,一般选择初馏点约为75℃的FCC汽油馏分或C5~7馏分,即FCC轻汽油作为醚化反应的原料。
FCC轻汽油中的叔戊烯、叔己烯和叔庚烯在催化剂的存在下与甲醇进行醚化反应生成相应的甲基叔戊基醚(TAME)、甲基叔己基醚(THxME)、甲基叔庚基醚(THpME),从而得到辛烷值高而蒸气压低的醚化汽油。
本文介绍了国内外典型的FCC轻汽油的醚化工艺。
1 国外的FCC轻汽油醚化工艺1.1 Neste公司的NExTAME工艺芬兰Neste工程公司开发的FCC轻汽油中C5~7烯烃醚化工艺,即NExTAME工艺于1995年5月在芬兰实现工业化,工艺流程见图1。
该工艺主要由选择性加氢反应器、预反应器、精馏塔和侧线反应器组成,特点是采用精馏塔和侧线反应器来提高原料中活性烯烃的转化率。
预反应器和侧线反应器都使用强酸性阳离子交换树脂为催化剂。
图1 NExTAME工艺流程FCC轻汽油原料经选择性加氢把二烯烃转化为单烯烃后进入预反应器进行反应,然后送入精馏塔分馏。
催化裂化后反应系统快分的研究进展
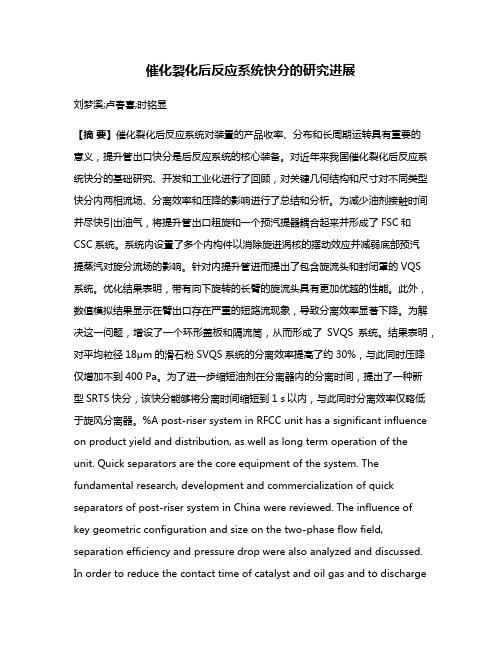
催化裂化后反应系统快分的研究进展刘梦溪;卢春喜;时铭显【摘要】催化裂化后反应系统对装置的产品收率、分布和长周期运转具有重要的意义,提升管出口快分是后反应系统的核心装备。
对近年来我国催化裂化后反应系统快分的基础研究、开发和工业化进行了回顾,对关键几何结构和尺寸对不同类型快分内两相流场、分离效率和压降的影响进行了总结和分析。
为减少油剂接触时间并尽快引出油气,将提升管出口粗旋和一个预汽提器耦合起来并形成了FSC和CSC系统。
系统内设置了多个内构件以消除旋进涡核的摆动效应并减弱底部预汽提蒸汽对旋分流场的影响。
针对内提升管进而提出了包含旋流头和封闭罩的VQS系统。
优化结果表明,带有向下旋转的长臂的旋流头具有更加优越的性能。
此外,数值模拟结果显示在臂出口存在严重的短路流现象,导致分离效率显著下降。
为解决这一问题,增设了一个环形盖板和隔流筒,从而形成了SVQS系统。
结果表明,对平均粒径18μm的滑石粉SVQS系统的分离效率提高了约30%,与此同时压降仅增加不到400 Pa。
为了进一步缩短油剂在分离器内的分离时间,提出了一种新型SRTS快分,该快分能够将分离时间缩短到1 s以内,与此同时分离效率仅略低于旋风分离器。
%A post-riser system in RFCC unit has a significant influence on product yield and distribution, as well as long term operation of the unit. Quick separators are the core equipment of the system. The fundamental research, development and commercialization of quick separators of post-riser system in China were reviewed. The influence of key geometric configuration and size on the two-phase flow field, separation efficiency and pressure drop were also analyzed and discussed. In order to reduce the contact time of catalyst and oil gas and to dischargeoil gas as soon as quickly, a rough cut cyclone was coupled with a pre-stripper. Internals were mounted in the system, which were also called FSC and CSC system, to diminish the fluctuating processing vortex core and to reduce the influence of pre-stripping steam. Then a post-riser system called VQS was proposed, which included a vortex quick separator and an isolated shell. The study was conducted to optimize the geometric configuration of the separator, and the one with long and downward spiral arms was found to have excellent performance. Furthermore, the simulation results showed that severe short cut flow occurred in the vicinity of the exit of arms, leading to significant drop of separation efficiency. Then, a new system called SVQS was proposed by adding an annular cover and a tube into the system. As a result, the separation efficiency considerably increased about 30%for 18μm talc, meanwhile the separation pressure drop raised only 400 Pa. In order to reduce the separation time, a quick separator was proposed and optimized. The separation time was reduced to less than 1 s, and separation efficiency was closed to 75% for 44μm talc, which was slightly lower than separation efficiency of cyclone.【期刊名称】《化工学报》【年(卷),期】2016(067)008【总页数】13页(P3133-3145)【关键词】流态化;多相流;分离;催化裂化;后反应系统【作者】刘梦溪;卢春喜;时铭显【作者单位】中国石油大学北京重质油国家重点实验室,北京 102249;中国石油大学北京重质油国家重点实验室,北京 102249;中国石油大学北京重质油国家重点实验室,北京 102249【正文语种】中文【中图分类】TQ052.5催化裂化是我国炼油工业最重要的二次加工工艺,生产了国内约75%的汽油、30%的柴油和40%以上的丙烯。
化学反应中的蒸汽裂解与催化裂化

蒸汽裂解和催化裂化是两种在化学反应中常见的裂化过程。
这两种裂化过程在石油化工、化学工程和材料科学等领域中具有重要的应用价值。
本文将介绍这两种裂化过程的基本原理和应用。
蒸汽裂解是一种通过加热和蒸汽作用下降低碳氢化合物分子量的反应过程。
在蒸汽裂解中,高分子碳氢化合物会经历碳-碳键和碳-氢键的断裂,生成低碳分子化合物,如烃类和芳香化合物。
蒸汽裂解反应是一种热力学驱动的过程,需要高温和高压条件下进行。
在蒸汽裂解过程中,蒸汽中的水和碳氢化合物在催化剂的存在下进行反应,从而产生低碳分子化合物。
蒸汽裂解在石化工业中具有广泛的应用。
例如,在裂解重油和煤焦油中,可以得到重要的烃类和芳香化合物,如乙烯、丙烯和苯。
这些化合物是石油化工生产中的重要原料,广泛应用于合成高分子材料、塑料和涂料等工业。
此外,蒸汽裂解还可以将废气和废料中的有机化合物转化为有用的化学品,从而实现资源的回收利用和环境保护。
催化裂化是一种通过催化剂的作用促使高分子化合物裂解为低分子化合物的反应过程。
在催化裂化中,催化剂可以降低反应的活化能,提高反应速率,并选择性地裂化高分子化合物。
催化裂化反应通常在相对较低的温度和压力条件下进行,因此能够节约能源并降低生产成本。
催化裂化在石油炼制过程中是一项重要的技术。
通过催化裂化,可以将高沸点的重质石油馏分转化为低沸点的石油产品,如汽油、柴油和润滑油。
这些石油产品是现代社会运输和工业生产的重要能源和原料。
催化裂化还可以使废油和垃圾转化为有价值的产品,实现废物的资源化。
值得注意的是,蒸汽裂解和催化裂化是两种不同的裂化过程,各自具有特定的应用领域和适用条件。
蒸汽裂解适用于较重的碳氢化合物,如煤焦油和重质油,需要高温和高压条件。
而催化裂化适用于较轻的碳氢化合物,如原油和废油,需要催化剂的存在和相对较低的温度。
综上所述,蒸汽裂解和催化裂化是两种重要的化学反应过程,具有广泛的应用。
蒸汽裂解是一种通过加热和蒸汽作用下降低碳氢化合物分子量的过程,主要应用于石油化工和化学工程。
- 1、下载文档前请自行甄别文档内容的完整性,平台不提供额外的编辑、内容补充、找答案等附加服务。
- 2、"仅部分预览"的文档,不可在线预览部分如存在完整性等问题,可反馈申请退款(可完整预览的文档不适用该条件!)。
- 3、如文档侵犯您的权益,请联系客服反馈,我们会尽快为您处理(人工客服工作时间:9:00-18:30)。
催化裂化过程反应化学的进展
0708010103 贺竹
1前言
自我国第一套流化催化裂化装置于1965年实现工业化以来,催化裂化工艺作为炼油的主要转化技术,发展极为迅速【1】。
到21世纪初,全国催化裂化装置总加工能力接近100Mt/a,其中渣油占催化裂化总进料约40%,成为我国加工渣油的主要手段之一。
我国催化裂化装置所生产的汽油和柴油组分分别占成品汽、柴油总量的75%和30%左右,所生产的丙烯量约占丙烯总产量的40%。
同时,催化裂化装置还可以为烷基化装置和醚化装置提供原料。
因此,催化裂化工艺对炼油行业提高轻质油收率和改善产品质量、提高经济效益起着举足轻重的作用【2】。
发展重油深度转化,增加轻质油品仍将是21世纪我国炼油行业的重大发展战略。
流化催化裂化工艺仍将发挥不可取代的作用,这是因为流化催化裂化工艺经过几十年的发展,技术成熟,生产方案灵活,既可以最大量地生产高辛烷值汽油组分,又可以最大量地生产高辛烷值汽油组分和丙烯或最大量地生产轻质油组分,原料适应性广,从馏分油到重质原料油均可加工,装置压力等级低,操作条件相对缓和,投资省等特点。
由此可见,流化催化裂化装置仍将作为21世纪我国炼油行业的核心工艺装置【3】,主要在生产汽油、柴油、液化气和丙烯以及加工重质原料油等方面发挥着重要作用。
重油催化裂化工艺随着石油资源减少而面临着原料劣质化的巨大难题,同时节能降耗也是催化裂化技术所面临的重要问题【4】。
化解这些问题需要开发新的工艺和技术,这就需要总结前人的研究成果,对传统的催化裂化工艺过程反应化学的认识进行分析和总结,发现不足之处,进行有目的地设计烃类反应的探索试验,以便更深刻地认识催化裂化过程反应化学规律,并进行知识创新。
2催化裂化过程反应化学发展历程
催化裂化工艺发展史可追溯到19世纪90年代,至今已超过一百年。
在百年期间,催化裂化工艺经过几个阶段的快速发展:一是催化剂依次从无定型硅铝催化剂、X型分子筛、Y型分子筛、超稳分子筛到中孔分子筛的发展;二是反应器从固定床、移动床、密相流化床到提升管反应器的进步;三是其他各种新技术在反应再生系统中得到广泛应用,如两段再生、烧焦罐等催化剂再生技术,快速汽化、快速反应和快速分离的“三快”技术,以及催化剂预提升技术等【1】。
这些技术的发展促使催化裂化工艺达到一个崭新的水平。
2.1热裂化工艺
热裂化过程是一种单纯依靠加热使原料达到一定温度而发生较大分子裂化成较小分子, 重质馏分油部分转化为汽油和柴油的方法。
1913年釜式热裂化装置建成,随后管式加热炉和热油泵等新技术相继应用,热裂化装置从原始的间歇操作跃升为现代的连续操作模式。
在1920年至1940年间,随着汽车工业的发展,汽油需求量激增,此工艺得到了较大的发展。
热裂化工艺的技术特点是低温高压,其反应温度为470~480℃,反应压力为2.0~5.0MPa,所生产的汽油辛烷值较低(RON为60~70)且安定性差,难以满足发动机技术不断进步的要求。
至20世纪40年代,热裂化工艺逐渐被催化裂化工艺所取代【5】。
2.2催化裂化工艺
催化裂化反应与热裂化反应在反应历程上有着本质的差异。
石油烃类在酸性催化剂的作用下,裂化反应的活化能显著降低,在相同的反应温度下,其反应速度比热裂化反应高出若干个数量级,同时目的产物的选择性更高【6】。
催化裂化催化剂均为固体酸型催化剂。
最早使用的催化剂是天然白土,其主要成分是硅和铝,例如蒙脱石等。
它们经过酸处理和焙烧后即有一定的催化活性。
但天然白土催化剂的稳定性差,汽油质量产率只有20%~30%。
至20世纪40年代,人工合成的无定型硅酸铝催化剂取
代了天然白土。
由于合成硅酸铝催化剂的活性和稳定性均高于天然白土,且汽油质量产率可达35%左右。
因此,在工业装置上得到了广泛应用。
至20世纪60年代初, 又开发了以沸石分子筛为活性组分的裂化催化剂, 其性能比合成硅酸铝催化剂更优越【6】。
20世纪60年代后期,为适应高活性高选择性沸石催化剂而开发出提升管催化裂化工艺。
与流化床反应器相比,提升管反应器主要特点为:a.裂化反应具有更好的选择性,干气和焦炭产率明显地减少,更适合处理重质原料油;b.裂化反应效率更高,裂化反应可在很短时间内完成,并可以大幅度提高处理能力;c.裂化反应具有较好的灵活性,可以通过反应温度、催化剂性质等条件的变化,实现不同的生产方案。
提升管催化裂化工艺将流化催化裂化技术提高到一个新的水平【7】。
20世纪70年代以前,由于环境控制允许汽油加铅,所以当时追求的是高汽油产率,而辛烷值靠加铅来弥补。
20世纪年80代以来,汽油加铅量受到限制并逐步无铅化,造成汽油辛烷值难以满足车用汽油要求。
因而只追求高汽油收率而忽视辛烷值的提高已不能适应要求,两者兼顾或以提高汽油辛烷值为主成为催化裂化工艺技术发展不得不面临的选择。
为了应对汽油无铅化的目标,催化裂化工艺由最大量生产汽油向生产高辛烷值桶汽油或高辛烷值汽油方向发展。
由于汽油中烯烃的辛烷值较高,提高汽油中烯烃含量一直被作为催化裂化工艺技术发展的主要方向,主要表现在工艺参数和催化剂类型变化上。
虽然现有的催化裂化技术可以生成高辛烷值汽油,满足汽油无铅化的要求。
但无论是工艺条件的改变,还是新型分子筛催化剂的使用,都是以提高汽油组分中的烯烃含量来增加汽油辛烷值,其中烯烃质量分数大约为36%~60%。
20世纪70年代,由于能源危机改变了石油产品需求的结构,对重质燃料油或渣油的需要量稳步下降,而对汽油、柴油等轻馏分油则在增加。
重油催化裂化工艺是将重质原料油转化为轻馏分油的最有效方法之一,它作为一项炼油新工艺,已为很多国家所重视,而且得到了迅速发展【9】。
渣油催化裂化工艺目标是提高重油转化率和轻质油产率,降低焦炭产率,增强催化剂抗重金属能力和提高汽油的辛烷值桶。
渣油的馏程范围从初馏点小于300℃到终馏点大于750℃,分子体积大且范围较宽,在正常催化裂化条件下难以气化。
在重油中还含有较多的重金属和碱土金属元素,这些杂质会污染催化剂,使其活性下降或选择性变差。
此外,重油还含有杂环化合物、胶质和沥青质,硫和氮含量高,残炭高,氢碳比低等特点。
重油催化裂化装置的工艺参数设计和选用水热稳定性更好的超稳Y型分子筛的催化剂, 旨在强化裂化反应,抑制氢转移反应,从而造成重油催化裂化生产的汽油中烯烃含量高,汽油产率低,干气产率和液化气产率高。
但从氢利用角度来看,干气富含氢气,而焦炭贫氢,干气产率的增加,造成氢利用不够合理。
2.3催化裂解工艺
我国自1987年开始, 在世界上首先开发了以重油为原料, 以催化裂化工艺为基础的催化裂解工艺来生产低碳烯烃, 特别是丙烯【10】。
第一套工业示范装置于1990年开车成功【11】。
催化裂解工艺过程反应化学主要是在酸性催化剂上以正碳离子机理主要是五配位正碳离子进行的单分子裂化反应。
为了多产丙烯,需要强化单分子裂化反应,因此,在专用催化剂开发上,主要使用经过改性的、具有良好水热稳定性的五员环结构的中孔沸石。
该沸石酸强度高,但密度低,从而裂化反应活性高,氢转移反应活性低。
在工艺条件设计上,采用高出常规催化裂化30~80℃的反应温度,通过加大水蒸气注人量来降低油气分压,从而提高裂化反应活性,降低氢转移反应活性。
催化裂解工艺过程中烃类在酸性催化剂上的反应以单分子裂化反应为主,尽管多产丙烯, 但同时存在干气产率大幅度增加,汽油烯烃体积分数高达60%以上,原料仅限于质量较好的蜡油等问题【8,12】。
3.结论
回顾历史可以看出,满足市场需求和追求利润最大化是催化裂化工艺存在的基础和追求的目标。
在市场需求和追求利润最大化的驱动下,催化裂化工艺进行了许多重大的变革,催化裂化工艺每次重大的变革都是来自对催化裂化过程反应化学方面的知识创新。
参考文献
【1】陈俊武.催化裂化工艺与工程(第二版)[M].北京:中国石化出版社,2005,18~23 【2】侯芙生.21世纪我国催化裂化可持续发展战略[J].石油炼制与化工,2001,32(1):1~6 【3】陈俊武,卢捍卫.催化裂化在炼油厂中的地位和作用展望-催化裂化仍将发挥主要作用[J].石油学报(石油加工),2003,19(1):1~11
【4】瞿国华,黄大智,梁文杰.延迟焦化在我国石油加工中的地位和前景[J].石油学报(石油加工),2005,21(3):47~53
【5】程之光.重油加工技术[J].北京中国石化出版社,1994,360~378
【6】梁文杰.石油化学[M].山东:石油大学出版社,1995.219~299
【7】陈俊武.催化裂化工艺与工程(第二版〕[M]北京:中国石化出版社,2005.1153~1154 【8】许有好.催化裂化过程反应化学多维反应结构的研究[D]北京:石油化工科学研究院,2006
【9】陈俊武.催化裂化工艺与工程(第二版〕[M].北京:中国石化出版社,2005.17
【10】李再婷,蒋福康等.催化裂解制取气体烯烃[J].石油炼制[J],1989,20(7):31~33 【11】李再婷,蒋福康等.催化裂解工艺技术及其工业应用[J].当代石油化,2001,9(10):31~
35
【12】许友好,龚剑洪,叶宗君等.大庆蜡油在酸性催化剂上反应机理的研究.石油学报(石油加工),2006,22(2):34~38。