PCB制程管控及审核重点
PCB供应商制程审核要点

PCB供应商制程审核要点内层1、针对预清洁线是否有建立预先点检表单?是否已经执行(已经填写)?2、刷磨/预清洁化学药水是否有证据证明其有按照理化室文件规定的频率进行分析?3、是否有证据证明预清洗倾槽与更槽计划有符合文件要求?4、是否有证据证明所有的化学品与文件上管控的物质有监督并管控?5、槽液测试是否每班测试一次以确保预清洁品质良好?6、无尘室的预清洁线入口到无尘室是否有良好的压力?7、无尘室的温度,湿度与尘埃粒子是否按照10K(万级)最高要求管控,并且有管控实效通知系统?8、无尘室的压膜与曝光区是否用的是黄灯并且所有的外部窗户使用的是UV膜?9、是否有证据可以证明干膜或是湿膜储存在温度与湿度管控的环境内?并且,到期管控有先进先出目录?10、在压膜前是否有粘尘滚轮清洁机器?11、针对干膜压膜,是否检查了压膜滚轮的温度并使用红外线表进行确认?12、是否有文件规定的干膜检验标准指导书以判定接受或判退?13、所有的制程工具与材料是否有相应的定义并管控在制定区域?包括老化敏感材料有效期过期?14、是否有文件规定干膜剥膜/重工程序有定义最大的重工次数?15、对干膜压膜,是否有对压膜滚轮温度进行检验并对红外线表进行确认?16、是否对工作菲林的最新版本进行管控?17、是否有证据表明管控了曝光的最大次数并对工作菲林曝光次数进行监控?18、在确定曝光次数后,是否使用粘尘滚轮对底片进行清洁?审核粘尘滚轮的状况?19、在底片设计阶段,是否确认了前后对准度的工具/制程最大公差?是否被定义为关键SPC参数?20、在这些制程是否对上下对准度进行确认?21、可允许的最大曝光次数是否有文件规定并有相应的系统对其跟踪?22、是否能证明菲林的曝光次数有进行监控并且底片没有超出文件规定的使用期限?23、曝光和显影之间是否按文件规定最大的静置时间并有按照此要求执行?24、DES 线是否有预启动点检表?是否已经进行(有完整地填写)?25、是否能证明所有的化学品有进行监控并有管控清单?26、DES线是否有文件规定不良品与返工计划,并且有客观证据说明有按照其要求执行?27、在批量蚀刻前是否先进行首件确认,以保证蚀刻机设备与线径?28、是否至少定期稽核一次蚀刻站并有相应的维护记录作为品质文件?29、蚀刻机运作速度是否有规定并且有文件规定铜重量/厚度?30、过滤系统是否完善?清洁频率与更换频率是多少?31、是否有文件规定最大水洗污染水准,水洗流动率与对传导性进行确认?32、是否有专门的对DES线清洁,烘干与无沾污进行检验?33、剥膜机是否有过滤系统以去除干膜膜屑?34、是否有作业员单独操作每个重要项目(控制,电源,地面)以防止刮伤?35、是否规定作业员的清洁计划?36、现场是否有系统规定主要测试哪条线径?37、是否有文件规定线径测试的频率?外层AOI1、所有层数是否100%进行AOI检测?2、所有的工具是否有相应的规定并放置在指定的区域?3、是否对电源/接地层进行检验并按照抽样计划定期统计?4、是否根据客户资料制定AOI程序,并且由工程建立所需的AOI关键参数设备与程序?5、AOI程序是否有相应的参数,其涉及到最小线径,最小间距,等?6、是否有不良标准板用于确认每台AOI机是否能够在开始每批测试前测出所有的不良?7、现场是否系统要求干膜首件发现重复不良时作出相应的通知?8、若一批内出现了各种不良,此信息是否立即反馈给DES作业员并审核其作业动作?例如:残铜,线路缺口,短路,断路?9、AOI不良确认是否有独立的确认站并且有收集不良资料并进行有意义的报告?10、修补后的板子是否有重新过AOI确认找出的不良已经全部修补OK?11、AOI站的产率是否每日进行跟踪并及时反馈给I/L制程建立相应的改善小组?是否对直通率与最终生产率目标进行定义?12、若产量低于目标,是否采取相应的改善措施?13、是否针对最高不良项目有要求使用柏拉图进行分析?是否采取持续有效的改善方法以减少最高不良?"14、返工指导书是否符合IPC规范?15、是否有明确的说明若返工时超过3条线路断路,则报废?16、是否针对已经焊接的线路进行胶带测试,以确保修补板的可靠性?棕化1、是否能证明棕化药水供应商在3个月前有对棕化线进行稽核?若没有这样做,是否采取了相应的措施?2、是否有进行DOE确保最好的棕化厚度以保证在热压测试制程发生分层?3、是否对微蚀率进行监控?其是否有SPC图管控并有正在进行的措施?4、氧化粘合强度测试是否针对所有材料类型的每条线每周进行一次测试?5、棕化药水是否有定量给料系统?6、是否使用DI水进行水洗?7、机器是否干燥并无污染?8、是否能证明黑化厚度有很好的管控?9、氧化板是否颜色统一,外表无刮伤/或操作导致损坏?10、离子污染测试是否按照要求每次换班执行一次?11、氧化线是否返工?若有返工,是否有文件规定最大返工次数?压合1、叠合线无尘室是否有相应的温度与湿度管控?2、是否规定氧化线-叠合作业的静置时间?3、现场是否有文件以确保每对预叠有按照凡谷承认的要求执行?4、是否定期检查以确保实际降温率不超过5度/分?温度升温与降温速率是多少?5、每批钢板是否定期清洁并打磨?钢板的厚度是否定期检查其厚度?6、是否能证明压合平台是否平整/平行并至少1-6个月检查一次?7、压合后的板厚是否进行抽樣检验, 对每PNL至少检验的5个点?8、X-RAY冲床是否管控对准度的设计补偿精确度?9、是否有品质检验程序文件对压合板数脂沾污进行定义?10、所有用于凡谷型号的板材,是否每周对压合产品检测一次TG与△TG?11、是否有文件规定X-RAY钻孔对准度的接受/判退标准?12、是否有文件定义对X-RAY钻孔系统进行尺寸测量确认?钻孔1、钻孔机是否有破损钻咀与不良钻咀尺寸鉴定能力?2、钻孔机是否能够清楚地定义钻孔参数,包括堆叠厚度?3、是否在开始生产前,对钻孔程序进行检验?4、是否能证明钻轴偏移管控良好?5、堆叠高度,每钻咀的最大钻次,进刀速度是否对板材类型,板厚,曾数,与孔尺寸进行管控?6、是否通过切片或X-RAY对钻咀对准度进行检验?频率是多少?7、是否对钻咀破损有调查改善计划并减少了不良次数?是否有客观证据证明已经有管控此项?8、是否有文件规定钻孔重工/修补程序并有相关品质点检表?9、所有PCB漏钻孔位于钻孔机台面上已经钻过的位置?10、再次研磨的钻咀是否在使用前进行检验与确认?11、是否有文件规定并对最大研磨次数进行管控?12、在使用之前是否对铝板进行检验,以确保无凹陷与刮伤?13、每轴底部的板子是否检验其孔尺寸,孔位,孔对准度与孔数量等?14、对钻孔精确度,孔径,孔数量,孔位与铜箔表面确认,是否有相应的检验程序?15、钻孔机孔位对准度能力数据是否对每台机器/每轴进行跟踪?16、钻孔机偏移度是否追踪到每台机器/每轴?17、在钻孔后是否通过良品测试机器或X-RAY检验其对准度?18、钻孔制程是否使用SPC?19、所有的PASS/REJECT板是否贴有相应的标签以避免混料或遗失?20、是否有SPC管控并有最近更新关键参数管控?21、所有超出管控的项目是否有相应的改善对策?化学沉铜1、去毛刺线是否有启动前点检表?是否已经运行(完整填写)?2、去毛刺机器是否有风刀,流动性&超声波?3、在去冲孔孔内毛刺后,是否检验孔?若有,是否有持续改善的资料?4、去毛刺后,板面与孔是否完全干燥?5、去毛刺线是否有开机点检表?目前是否运行?6、生产线上的温度,抽水机,槽液条件等是否管控在制程规范内?7、是否能证明化学药水分析有定期完成?8、化学沉铜线是否有开机点检表?目前是否运行(完整填写)?9、是否检查化学沉铜的孔两面的背光?10、化学沉铜在开始生产前是否有进行是试镀?11、化学沉铜线生产是否有规定的品质确认程序的判定接受/判退标准。
PCB制程管控及审核重点

作用 去除不規則之板邊 去除板邊銳利錂角 清除殘屑
ቤተ መጻሕፍቲ ባይዱ
制程管控 銑刀規格 參數設定
稽核重點
棕化
壓合
預疊
壓合
整理课件
銅箔 膠片 基板 膠片 銅箔
鉆靶 清洗
半撈
去毛邊
12
流程 鑽孔
作用 通孔製作
制程管控
A.鑽針管控 B.機臺參數設定 C.孔數,孔偏,孔壁粗糙
稽核重點
報廢管制及研磨記錄 斷針檢查及處理程序 首件檢查記錄
預烤
曝光
清洗
顯影
22
流程 作用
曝 光 防焊區域 影像轉移
制程管控
稽核重點
A.無塵室管理 B.曝光能量及真空度 C.底片進出及報廢管制 D.底片版序及曝光次數管控
溫濕度,落塵量,傳遞門,人員著裝 管制記錄,重工管制 管控方式,報廢記錄 管控方式,監控記錄
前處理
防焊
塞孔
塗佈 整後理烘课烤件
預烤
底片 綠漆 銅箔 膠片 基板 膠片 銅箔 綠漆
制程管控
A.顯影液濃度及溫度 B.顯影/水洗噴淋壓力 C.顯影點及輸送速度 D.添加量及添加頻率 E.顯影不潔,曝偏
稽核重點
酸性/鹼性/危險品管控 參數是否在管制範圍 置放時間是否管制
前處理
外層
覆膜
曝光 AOI
整理课件
乾膜 銅箔 膠片 基板 膠片 銅箔 乾膜
顯影
蝕刻
清洗
去膜
18
流程 蝕刻
作用
外層線路 形成
PCB 制程管控及稽核重點
整理课件
1
內層
壓合
鑽孔
包裝出貨
多層板 一般製作流程
外觀檢驗
PCB制程管控及审核重点

加强制造过程的监控,确保工艺参 数正确;采用高可靠性的材料和工 艺;定期检查PCB线路,发现断路 及时修复。
常见问题三:阻抗不匹配
总结词
阻抗不匹配是指PCB上的线路阻抗与预期值不符,导致信号传输质 量下降的现象。
详细描述
阻抗不匹配可能由线路宽度、长度、介质常数等参数变化引起。阻 抗不匹配可能导致信号反射、失真或延迟。
流程监控
对制程中的关键环节进行 实时监控,确保流程的稳 定性和一致性。
管控工具与技术
工具选择
根据制程需求,选择合适 的生产设备和检测工具。
技术更新
关注行业新技术发展,及 时引进和应用先进的制程 技术。
工具维护
定期对生产设备和检测工 具进行维护和保养,确保 其正常运行和准确性。
管控标准与规范
标准制定
PCB制程管控及审核重点
目 录
• PCB制程概述 • PCB制程管控要点 • PCB制程审核重点 • PCB制程常见问题及解决方案 • PCB制程发展趋势与展望
01 PCB制程概述
PCB制程简介
PCB制程是将电子零件与电路以导电铜箔印刷的方式,安装在基板(PCB)上,以 实现电子电路的连接与组装的一种工艺。
THANKS FOR WATCHING
感谢您的观看
柔性PCB技术
总结词
柔性PCB技术具有柔性和可弯曲的特性,适用于各种不规则表面和空间受限的应 用场景。
详细描述
柔性PCB技术利用柔性基材和特殊的加工工艺,实现了PCB的可弯曲和可折叠特 性。这种技术广泛应用于穿戴设备、折叠屏手机等领域,为现代电子产品带来了 更灵活的设计和更轻薄的外观。
绿色环保PCB技术
02
良好的PCB制程可以简化生产流程,提高生产效率,降低生产
PCBA-关键制程点管控

三、轨道角度管控
综合各种因素来看,轨道角度对波峰焊接的影响不是非 常显著,故此参数一般情况下可不用调整,保持在5-7度之 间即可。建议调整到6.5-6.8度之间较好。
四、链条速度管控
链速对波峰焊接也有较大影响,同时链速还会影响到产能。 因此对链速的调整应该慎重,尽可能优化之后将其固定,不要 轻易更改。链速主要会影响焊点的浸锡时间和最后的拖锡状态。 链速快,焊接时间短,但相对的脱锡效果会好;链速慢,焊接 时间长,脱锡效果差。链速的调整范围比较大,一般情况下可 调整在1.2 – 1.5 米/分钟。
四、 炉温曲线管控
d. 炉温曲线温度-时间关系图:
温度
217℃ 峰值温度:235 -250℃
回流区:>217℃ 时间:45 – 90 秒
升温斜率: 1- 3℃/秒
150℃
降温斜率: 1- 4℃/秒
预热区:150-217℃ 时间:60 – 120 秒
时间
五、 炉温测试板管控
炉温测试板是测试炉温曲线的基础,只有制作了合格的炉温测 试板,才能确保所测试出来的炉温曲线能够正确反映板在炉中的 温度和时间关系,才能帮助我们分析和判断所发生的问题,否则 极容易对相关工程技术人员产生误导。炉温测试板管控要点有: a. 测温点选取:回流炉测温板测温点选取遵循以下原则: i)有BGA 元件时,优先选取BGA元件,且BGA上要有2个测温点,一个位 于BGA中心,一个位于BGA边缘; ii)无BGA元件时,可按以下 顺序来选取元件:QFP, PLCC, SOP, DIODE, CHIP; iii)元件选 取时应注意在零件分布密度高的位置及低的位置要均匀;iv)如无 特殊要求零件,应尽可能选择一个热容最大及一个热容最小的零 件;v)每个测温板选点应不少于4个; b. 热电偶埋点方法:i)普通元件热电偶的感应头应贴紧在元件焊点 上;ii)BGA元件热电偶的感应头应贴紧在锡球上。热电偶的感应 头可用高温锡线或红胶来进行固定。要确保热电偶的感应头与 元件脚或焊盘有紧密接触且完全被锡或红胶包住,没有裸露在空 气中。
PCBA制程介绍及管制重点
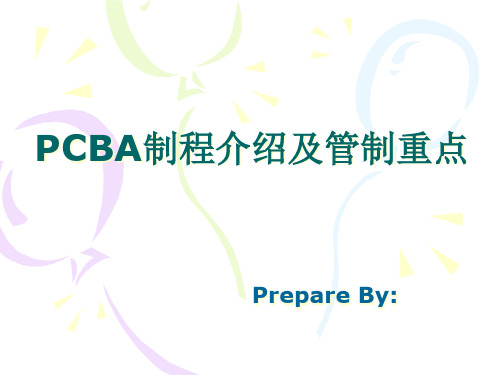
PCBA制程介绍及管制重点
Prepare By:
一.基本术语
EMS (Electronics Manufacturing Serving): 电子制造服务
SMT (Surface Mount Technology) 表面贴装技术
Solder Paste :锡膏 Stencil:钢网 Printing:印刷 Placement:贴片 Placement Equipment:贴片机 Nozzle:吸嘴
熔点(度) 183 189
Lead-Free
214~219
影响焊膏特性的重要参数主要有:
1.粘度:粘度与温度之间的关系是反比. 2.锡膏成分,配比及焊剂含量 3.锡膏粉末颗粒形状,粒度和分布 4.熔点 5.工作寿命和储存期限
六.回流焊品质控制
回流焊原理:
PCB进入升温区时,焊膏中的熔剂,气体挥发掉,同时,焊膏中的 助焊剂润湿焊盘,器件件端头和引脚,锡膏软化塌落,覆盖焊盘, 元器件引脚与氧气隔离;进入保温区后,PCB和元器件得到充分 的预热,以防PCB和元件损伤.PCB进入焊接区后,温度迅速上 升使锡膏熔化,液态焊锡对焊盘,远期件端头和引脚润湿,扩散 和回流混合形成焊锡接点.PCB进入冷却区后,使焊点凝固, 此时完成回流焊. 量测Reflow Profile至少需要量测3个点
(4). Pick and place (Fuji-IP3)
放置大型零件
SMD
(5). Reflow (Conceptronics) 热熔
SMD Big SMD
SMD
SMD
Basic PCBA assembly Process:
(6).Glue dispensing (Bottom side)- Fuji GL5 上膠
PCB各工艺质量控制重点
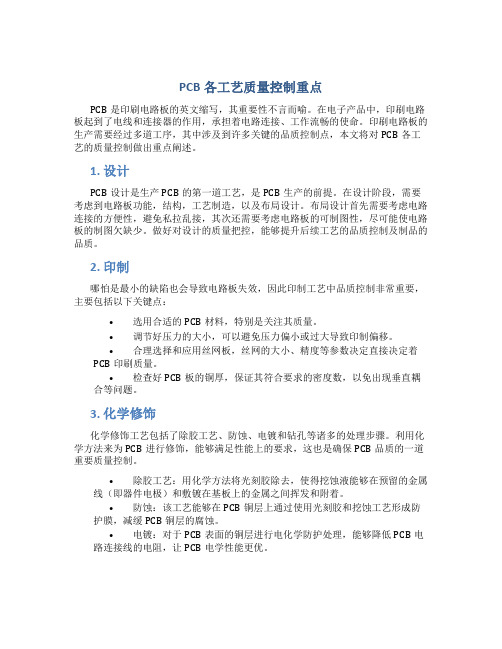
PCB各工艺质量控制重点PCB是印刷电路板的英文缩写,其重要性不言而喻。
在电子产品中,印刷电路板起到了电线和连接器的作用,承担着电路连接、工作流畅的使命。
印刷电路板的生产需要经过多道工序,其中涉及到许多关键的品质控制点,本文将对PCB各工艺的质量控制做出重点阐述。
1. 设计PCB设计是生产PCB的第一道工艺,是PCB生产的前提。
在设计阶段,需要考虑到电路板功能,结构,工艺制造,以及布局设计。
布局设计首先需要考虑电路连接的方便性,避免私拉乱接,其次还需要考虑电路板的可制图性,尽可能使电路板的制图欠缺少。
做好对设计的质量把控,能够提升后续工艺的品质控制及制品的品质。
2. 印制哪怕是最小的缺陷也会导致电路板失效,因此印制工艺中品质控制非常重要,主要包括以下关键点:•选用合适的PCB材料,特别是关注其质量。
•调节好压力的大小,可以避免压力偏小或过大导致印制偏移。
•合理选择和应用丝网板,丝网的大小、精度等参数决定直接决定着PCB印刷质量。
•检查好PCB板的铜厚,保证其符合要求的密度数,以免出现垂直耦合等问题。
3. 化学修饰化学修饰工艺包括了除胶工艺、防蚀、电镀和钻孔等诸多的处理步骤。
利用化学方法来为PCB进行修饰,能够满足性能上的要求,这也是确保PCB品质的一道重要质量控制。
•除胶工艺:用化学方法将光刻胶除去,使得挖蚀液能够在预留的金属线(即器件电极)和敷镀在基板上的金属之间挥发和附着。
•防蚀:该工艺能够在PCB铜层上通过使用光刻胶和挖蚀工艺形成防护膜,减缓PCB铜层的腐蚀。
•电镀:对于PCB表面的铜层进行电化学防护处理,能够降低PCB电路连接线的电阻,让PCB电学性能更优。
•钻孔:为了确保PCB板的通电性,钻孔的直径和深度需要合适,而且将钻孔拱口防护也是很关键的,若拱口防护不完善,则会导致铜连接不上或者没有电性能。
4. 组装在PCB生产的最后工阶段组装,同时也是PCB最为关键的一道工艺。
正确的组装工艺流程,是确保PCB电路运行正常的关键。
品保课制程管控及教育训练内容及PCB检验标准
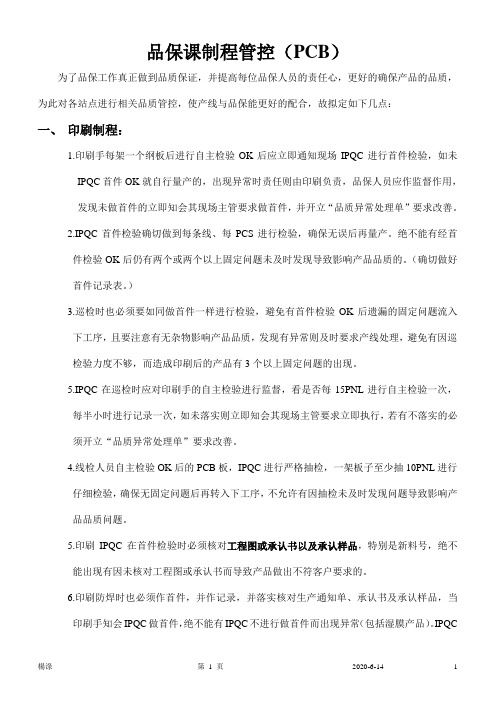
品保课制程管控(PCB)为了品保工作真正做到品质保证,并提高每位品保人员的责任心,更好的确保产品的品质,为此对各站点进行相关品质管控,使产线与品保能更好的配合,故拟定如下几点:一、印刷制程:1.印刷手每架一个纲板后进行自主检验OK后应立即通知现场IPQC进行首件检验,如未IPQC首件OK就自行量产的,出现异常时责任则由印刷负责,品保人员应作监督作用,发现未做首件的立即知会其现场主管要求做首件,并开立“品质异常处理单”要求改善。
2.IPQC首件检验确切做到每条线、每PCS进行检验,确保无误后再量产。
绝不能有经首件检验OK后仍有两个或两个以上固定问题未及时发现导致影响产品品质的。
(确切做好首件记录表。
)3.巡检时也必须要如同做首件一样进行检验,避免有首件检验OK后遗漏的固定问题流入下工序,且要注意有无杂物影响产品品质,发现有异常则及时要求产线处理,避免有因巡检验力度不够,而造成印刷后的产品有3个以上固定问题的出现。
5.IPQC在巡检时应对印刷手的自主检验进行监督,看是否每15PNL进行自主检验一次,每半小时进行记录一次,如未落实则立即知会其现场主管要求立即执行,若有不落实的必须开立“品质异常处理单”要求改善。
4.线检人员自主检验OK后的PCB板,IPQC进行严格抽检,一架板子至少抽10PNL进行仔细检验,确保无固定问题后再转入下工序,不允许有因抽检未及时发现问题导致影响产品品质问题。
5.印刷IPQC在首件检验时必须核对工程图或承认书以及承认样品,特别是新料号,绝不能出现有因未核对工程图或承认书而导致产品做出不符客户要求的。
6.印刷防焊时也必须作首件,并作记录,并落实核对生产通知单、承认书及承认样品,当印刷手知会IPQC做首件,绝不能有IPQC不进行做首件而出现异常(包括湿膜产品)。
IPQC应对未做首件机种加大抽检力度。
NG的及时知会产线停产处理。
直至处理OK后再量产。
二、电镀制程:1.IPQC对电镀制程做到每小时巡检一次,针对一铜、二铜、镀镍、镀金、蚀刻等站点进行巡检,并做好相关记录,杜绝因巡检不及时与未及时发现异常而导致产品报废率增加。
PCB工程管制及送样评估介绍

PCB工程管制的重要性
提高产品质量
缩短产品上市时间
通过严格的工程管制,可以确保PCB 的设计和生产符合要求,减少缺陷和 错误,从而提高产品的整体质量。
通过优化设计、生产和测试流程,工 程管制有助于加快产品上市时间,满 足市场需求。
降低生产成本
有效的工程管制可以避免生产过程中 的浪费和重复劳动,降低生产成本, 提高生产效率。
样品制作流程
工程制图
根据客户要求,绘制PCB工程 图,并进行审查和修改。
材料采购
根据工程图,采购所需的电子 元件、线路板等材料。
样品制作
按照工程图进行PCB打样,并 进行初步测试和检查。
样品确认
将制作完成的样品交给客户确 认,确保满足客户需求。
样品评估标准
品质标准
根据行业标准和客户要 求,制定相应的品质评
根据客户要求,进行电路 原理图设计,确定各元件 的连接关系和信号走向。
元件选型
根据电路设计,选择合适 的电子元件,确保元件的 规格、性能参数符合设计 要求。
设计审查
电路正确性
检查电路原理图的设计是 否正确,各元件连接是否 合理,信号走向是否符合 要求。
元件选型合理性
评估所选择的元件是否符 合设计要求,性能参数是 否满足电路需求,是否符 合生产工艺要求。
制程优化
通过对制程参数的优化和改进,减少不良品率,提高 生产效率。
人员培训
加强操作人员的培训和管理,提高其技能水平和操作 规范性,从而提高制程效率。
04 送样评估介绍
送样需求确认
客户确认
与客户沟通,明确送样需求,包 括样品数量、规格、测试标准等 。
内部确认
根据客户要求,评估公司内部生 产能力和技术水平,确保能够满 足客户需求。
- 1、下载文档前请自行甄别文档内容的完整性,平台不提供额外的编辑、内容补充、找答案等附加服务。
- 2、"仅部分预览"的文档,不可在线预览部分如存在完整性等问题,可反馈申请退款(可完整预览的文档不适用该条件!)。
- 3、如文档侵犯您的权益,请联系客服反馈,我们会尽快为您处理(人工客服工作时间:9:00-18:30)。
底片 乾膜 基板 乾膜 底片
裁切
前處理 AOI
覆膜 清洗
曝光 去膜
顯影 蝕刻
內層
流程 顯影
作用 去除未被曝光 之乾膜
制程管控 A.顯影液濃度及溫度 B.顯影/水洗噴淋壓力 C.顯影點及輸送速度 D.添加量及添加頻率 E.顯影不潔,曝偏
稽核重點 酸性/鹼性/危險品管控 參數是否在管制範圍 置放時間是否管制
稽核重點
測試板區分/標示 人員認證,修補動作 檢測動作
包裝
依規定將電路板真空包裝
補充依賴度測試: 漂錫試驗 浸錫試驗 補線品質測試 離子污染度測試
綠漆 銅箔 膠片 基板 膠片 銅箔 綠漆
文字
噴錫
成型
電測
品檢 包裝
電測 品檢 包裝
Q&A
PCB 制程管控及稽核重點
04/12
內層
壓合
鑽孔
電鍍
包裝出貨
多層板 一般製作流程
外層
外觀檢驗
防焊
電測
成型
表面處理
文字
流 程 裁 切
作 用 將基板裁切至 適當工作尺寸
制程管控 A.調刀距離 B.磨邊及圓角清潔 C.經緯向一致 D.下製程前烘烤 A.水破試驗 B.刷痕測試
稽核重點 刀具保養及更換記錄 首件記錄/清潔記錄
前處理
覆膜
曝光 AOI
顯影 清洗
蝕刻 去膜
外層
流程
作用
制程管控 A.去膜液濃度/溫度及輸送速度 B.噴灑及水洗壓力 C.冷風車頻率及烘乾溫度 D. 添加頻率及添加量 E.斷/短路,刮傷 缺口,刮傷,凹陷等
稽核重點 藥水配槽記錄 參數是否在管制範圍 自動添加校驗記錄 重修管控 人員認證/首件記錄 良板/不良板區分
基板
棕化
預疊
壓合
鉆靶 清洗
半撈 去毛邊
壓合
流程 預疊
作用 依設計將內層板 與膠片堆疊
制程管控 A.堆疊次序 B.膠片數量 C.裁切刀距調整 D.貼膠/鉚合作業
稽核重點 PP儲存條件,FIFO及保存期限 首件檢查記錄
膠片 基板 膠片
棕化
預疊
壓合
鉆靶ቤተ መጻሕፍቲ ባይዱ清洗
半撈 去毛邊
壓合
流程 壓合
作用 將預疊好之內層板, 膠片與銅箔壓合
稽核重點 重修流程 測試記錄
銅箔 膠片 基板 膠片 銅箔
去毛頭
除膠渣
化學銅
電鍍銅
電鍍
流 程 前處理
作 用 清除表面異物
制程管控 A.水破試驗 B.刷痕測試 A.儲存條件,FIFO及保存期限 B.氣泡,皺折,髒點
稽核重點 測試記錄
覆
膜
將光阻劑(乾膜) 加諸於基板表面
管控方式 重修管控
乾膜 銅箔 膠片 基板 膠片 銅箔 乾膜
銑刀規格
參數設定
銅箔 膠片 基板 膠片 銅箔
棕化
預疊
壓合
鉆靶 清洗
半撈 去毛邊
壓合
流程
作用
制程管控
稽核重點
鑽孔
通孔製作
A.鑽針管控 B.機臺參數設定 C.孔數,孔偏,孔壁粗糙
報廢管制及研磨記錄 斷針檢查及處理程序 首件檢查記錄
銅箔 膠片 基板 膠片 銅箔
鑽孔
鑽孔
流 程
去毛頭
作用
去除鉆孔於板面產生 之多餘殘屑 去除孔內膠渣 以化學置換方式於孔 內壁形成銅導體
重修流程 是否X-Ray量測錫厚 膜厚管控, 重修流程 首件記錄 V-Cut 檢驗
加工電路板至 客戶指定形狀
綠漆 銅箔 膠片 基板 膠片 銅箔 綠漆
文字
噴錫
成型
電測
品檢 包裝
文字 噴錫 成型
流程
電測 補充 品檢
作用
測試電路板之電氣特性 阻抗測試 檢視電路板之外觀
制程管控
參數設定 A.人員訓練 B.驗孔機,板翹機 料號,數量及客戶要求
前處理 清潔並粗糙銅箔表面, 增強油墨與之附著力
測試方式/記錄
基板
裁切
前處理 AOI
覆膜 清洗
曝光 去膜
顯影 蝕刻
內層
流程 覆膜
作用 將光阻劑(乾膜) 加諸於基板表面 補充: 濕膜
制程管控 A.儲存條件,FIFO及保存期限 B.氣泡,皺折,髒點 A.儲存條件,FIFO及保存期限 B.油墨粘度及膜厚 C.塗佈轉速及IR溫度 D.油墨刮傷露銅
制程管控 A.升溫速率 B.升壓速率 C.板厚,凹陷,皺折,板翹 A.層間對準度 B.尺寸漲縮
稽核重點 是否有壓合防呆設計
銑靶
製作半撈,鉆孔用之 工具孔
人員認證
銅箔 膠片 基板 膠片 銅箔
棕化
預疊
壓合
鉆靶 清洗
半撈 去毛邊
壓合
流 程
作 用
制程管控
稽核重點
半 撈
去毛邊 清 洗
去除不規則之板邊
去除板邊銳利錂角 清除殘屑
稽核重點 管控方式 重修管控 管控方式 測試記錄
重修管控
乾膜 基板 乾膜
裁切
前處理 AOI
覆膜 清洗
曝光 去膜
顯影 蝕刻
內層
流程 曝光
作用 內層線路 影像轉移
制程管控 A.無塵室管理 B.曝光能量及真空度 C.底片進出及報廢管制 D.底片版序及曝光次數管控
稽核重點 溫濕度,落塵量,傳遞門,人員著裝 管制記錄,重工管制 管控方式,報廢記錄 管控方式,監控記錄
制程管控
A.水破試驗 B.刷痕測試
稽核重點
參數於管制範圍
除膠渣 化學銅
A.藥液配槽校驗 B.背光級數/孔壁粗糙度
重修流程 切片檢查記錄
銅箔 膠片 基板 膠片 銅箔
去毛頭
除膠渣
化學銅
電鍍銅
電鍍
流 程 電鍍銅
作 用 以電鍍方式於孔內壁 形成銅導體,達到客戶 指定面/孔銅厚度
制程管控 A.面/孔銅厚度 B.手紋,刮傷,銅瘤 C.哈氏槽分析
乾膜 基板 乾膜
裁切
前處理 AOI
覆膜 清洗
曝光 去膜
顯影 蝕刻
內層
流程 蝕刻
作用 內層線路 形成
制程管控 A.蝕刻液酸度及比重 B.價銅含量 C.蝕刻/水洗噴淋壓力 D.蝕刻溫度及輸送速度 E.殘銅
稽核重點 酸性/鹼性/危險品管控 藥水配槽或自動添加校驗記錄 參數是否在管制範圍
乾膜 基板 乾膜
裁切
稽核重點 參數是否在管制範圍 油墨粘度濕重管制 網版管理
銅箔 膠片 基板 膠片 銅箔
前處理
塞孔
塗佈 後烘烤
預烤 清洗
曝光 顯影
防焊
流程 塗佈
作用 將油墨加諸於 板面外層線路
制程管控 A.離板/抬板間距 B.網版/治具對位
稽核重點 油墨粘度濕重管制 網版管理 人員取放板動作 首件檢查記錄 重修管控
預烤
去 膜 去除剩餘的乾膜 清 洗 去除板面殘餘藥液
AOI
內層線路檢查
基板
裁切
前處理 AOI
覆膜 清洗
曝光 去膜
顯影 蝕刻
內層
流程 棕化
作用 在銅面形成氧化層, 便於內層板與膠片 間之結合
制程管控 A.槽液分析 B.信賴性測試 *剝離力 *熱應力 *銅箔失重 C.刮傷,氧化,露銅
稽核重點 參數是否在管制範圍 測試記錄
前處理
覆膜
曝光 AOI
顯影 清洗
蝕刻 去膜
外層
流程 顯影
作用 去除未被曝光 之乾膜
制程管控 A.顯影液濃度及溫度 B.顯影/水洗噴淋壓力 C.顯影點及輸送速度 D.添加量及添加頻率 E.顯影不潔,曝偏
稽核重點 酸性/鹼性/危險品管控 參數是否在管制範圍 置放時間是否管制
乾膜 銅箔 膠片 基板 膠片 銅箔 乾膜
底片 綠漆 銅箔 膠片 基板 膠片 銅箔 綠漆 底片
前處理
塞孔
塗佈 後烘烤
預烤 清洗
曝光 顯影
防焊
流 程
顯 清 影 洗
作 用
防焊區域形成 去除板面殘餘藥液
制程管控
顯影不潔,曝偏
稽核重點
重修管控 參數是否在管制範圍
後烘烤
增加防焊綠漆之硬度
A.烤箱參數設定 B.依賴度測試 *硬度 *剝離力
重修管控 人員檢測動作
去 膜 去除剩餘的乾膜 清 洗 去除板面殘餘藥液
補充: 負片流程 黑孔 A O I 外層線路檢查
銅箔 膠片 基板 膠片 銅箔
前處理
覆膜
曝光 AOI
顯影 清洗
蝕刻 去膜
外層
流 程 前處理 塞 孔
作 用 清除表面異物 將指定通孔填 入油墨
制程管控 刷痕測試 A.離板/抬板間距 B.網版/治具對位 C.塞孔不良,漏塞
去除防焊綠漆 中之溶劑
烘箱參數設定
綠漆 銅箔 膠片 基板 膠片 銅箔 綠漆
前處理
塞孔
塗佈 後烘烤
預烤 清洗
曝光 顯影
防焊
流程 曝光
作用 防焊區域 影像轉移
制程管控 A.無塵室管理 B.曝光能量及真空度 C.底片進出及報廢管制 D.底片版序及曝光次數管控
稽核重點 溫濕度,落塵量,傳遞門,人員著裝 管制記錄,重工管制 管控方式,報廢記錄 管控方式,監控記錄
前處理 AOI
覆膜 清洗
曝光 去膜
顯影 蝕刻
內層
流程
作用
制程管控 A.去膜液濃度/溫度及輸送速度 B.噴灑及水洗壓力 C.冷風車頻率及烘乾溫度 D.添加頻率及添加量 E.斷/短路,刮傷 缺口,刮傷,凹陷等
稽核重點 藥水配槽記錄 參數是否在管制範圍 自動添加校驗記錄 重修管控 人員認證/首件記錄 良板/不良板區分
前處理