(工艺技术)缠绕成型工艺
缠绕成型工艺实验
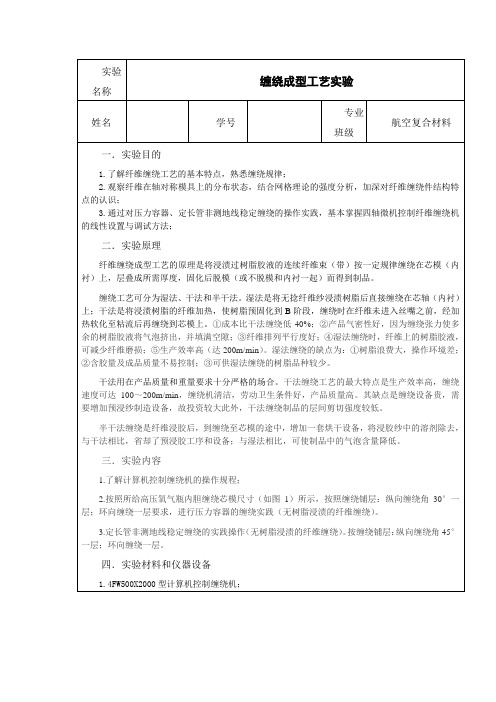
2.高压氧气瓶铝内胆缠绕芯模;3.圆轴钢模;4.600Tex缠绕纱五.实验步骤1.在老师的指导下,熟悉计算机控制缠绕机的操作程序,开启缠绕机,在“机器调整”的窗口下使小车、伸臂、丝嘴分别以较慢的速度正反向动作一次,并回到原点。
2.根据轴对称压力容器缠绕模具的基本尺寸(如图1、图2)和缠绕线性要求设定缠绕机的材料参数、工艺参数并保存好缠绕文件;材料参数纱团数树脂含量纤维密度(3/g cm)纱片宽度(mm)纤维Tex(g/km)树脂密度(3/g cm)是否采用计算机设定张力张力采样间隔(s)2 30% 2.54 4 1200 1.25 0 103.按纱团数要求,安装纱团、排好纱线、安装模具;4.挂上纤维束,开始试验模型缠绕;5.换上圆轴钢模,按上述2—4步骤做定长管非测地线稳定缠绕的实践操作。
五.思考与讨论1.纤维缠绕成型工艺的技术特点是什么?纤维缠绕成型的优点①能够按产品的受力状况设计缠绕规律,使能充分发挥纤维的强度;②比强度高:一般来讲,纤维缠绕压力容器与同体积、同压力的钢质容器相比,重量可减轻40~60%;③可靠性高:纤维缠绕制品易实现机械化和自动化生产,工艺条件确定后,缠出来的产品质量稳定,精确;④生产效率高:采用机械化或自动化生产,需要操作工人少,缠绕速度快(240m/min),故劳动生产率高;⑤成本低:在同一产品上,可合理配选若干种材料(包括树脂、纤维和内衬),使其再复合,达到最佳的技术经济效果。
缠绕成型的缺点①缠绕成型适应性小,不能缠任意结构形式的制品,特别是表面有凹的制品,因为缠绕时,纤维不能紧贴芯模表面而架空;②缠绕成型需要有缠绕机,芯模,固化加热炉,脱模机及熟练的技术工人,需要的投资大,技术要求高,因此,只有大批量生产时才能降低成本,才能获得较的的技术经济效益。
2.纤维缠绕时纤维张力大小有何影响?(1)张力对制品机械性能有影响。
张力过小,则制品强度偏低。
(2)张力对制品密实程度有影响。
第6章 缠绕成型工艺 (1)

第六章 缠绕成型工艺
③ 纤维都必须进行表面处理,以改善与树脂基 体的浸润性和粘附性。 玻璃纤维亦采用优良的增强型浸润剂。碳纤维则 应采用气液相氧化法、表面清洁法、电沉积与电 聚合法等进行表面处理,以改善表面结构,提高 表面活性; 6.1.2
纤 维 缠 绕 制 品 的 ④ 与树脂浸渍件性好,浸透速度快; 优 ⑤ 各股纤维张力均匀; 点 ⑥成带性好,不起毛,不断头。
第六章 缠绕成型工艺
6.1.3 原材料 主要有纤维增强材料与树脂两大类。 选择原则
纤 维 缠 绕 制 品 的 优 点
6.1.2
产品的各项设计性能指标
缠绕制品的使 用性能要求
工艺性要求
经济性要求
第六章 缠绕成型工艺
6.1.3 原材料 (1)增强材料 主要是中碱、无碱粗纱。另外有玻璃布带、碳纤维 等。应根据不同产品对性能的要求进行选用。
第六章 缠绕成型工艺
6.2.3 芯模设计 芯模设计的内容 根据制品批量、尺寸、固化温度、生产周期、工作载荷、 树脂收缩等因素进行:
芯 模 设 计
6.2.3
芯模设计需满足的基本要求 芯模设计的内容 芯模强度、刚度计算
第六章 缠绕成型工艺
6.2.3 芯模设计
芯模设计需满足的基本要求
能够承受缠绕过程的工作载荷、自重及加工过程的机械
芯 模 设 计
6.2.3
载荷;
具有一定刚度,在使用期间保持合乎要求的尺寸;
能经受固化温度的作用; 易于脱模。
6.1 概述
概 述
6.1
第六章 缠绕成型工艺 6. 缠绕成型工艺
6.1 概述
概 述
6.1
第六章 缠绕成型工艺 6. 缠绕成型工艺
纤维缠绕成型工艺流程
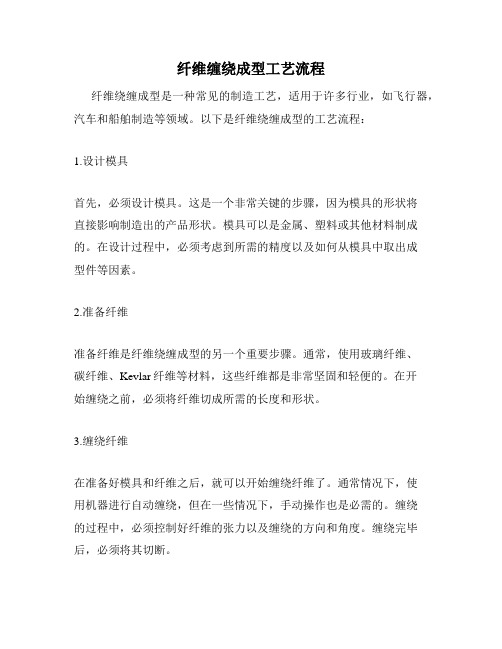
纤维缠绕成型工艺流程纤维绕缠成型是一种常见的制造工艺,适用于许多行业,如飞行器,汽车和船舶制造等领域。
以下是纤维绕缠成型的工艺流程:1.设计模具首先,必须设计模具。
这是一个非常关键的步骤,因为模具的形状将直接影响制造出的产品形状。
模具可以是金属、塑料或其他材料制成的。
在设计过程中,必须考虑到所需的精度以及如何从模具中取出成型件等因素。
2.准备纤维准备纤维是纤维绕缠成型的另一个重要步骤。
通常,使用玻璃纤维、碳纤维、Kevlar纤维等材料,这些纤维都是非常坚固和轻便的。
在开始缠绕之前,必须将纤维切成所需的长度和形状。
3.缠绕纤维在准备好模具和纤维之后,就可以开始缠绕纤维了。
通常情况下,使用机器进行自动缠绕,但在一些情况下,手动操作也是必需的。
缠绕的过程中,必须控制好纤维的张力以及缠绕的方向和角度。
缠绕完毕后,必须将其切断。
4.喷涂粘合剂切断的纤维件需要进行粘合。
为此,必须使用喷涂粘合剂。
这些粘合剂通常是环氧树脂或其他类似材料,可以粘合纤维并使其成型。
5.加热和硬化完成喷涂粘合剂后,需要将成型件进行加热和硬化。
加热的时间和温度取决于粘合剂使用的类型和成型件的大小和形状。
通过加热和硬化,可以使纤维件硬化、固化并成型,以达到所需的形状和性能。
6.处理表面最后,在完成纤维绕缠成型的过程中,需要处理表面。
这可以包括研磨、切割和涂覆表面处理剂等步骤,以使成型件达到所需的表面光滑度和外观。
纤维绕缠成型的过程可能因产品类型、制造设备和制造商的不同而有所不同。
以上步骤只是纤维绕缠成型过程的一个常见流程。
缠绕成型工艺的优缺点分析

缠绕成型工艺的优缺点分析
缠绕成型工艺是一种常用的复合材料加工技术,将预先融化的材料通过机械设备缠绕在模具上进行成型。
以下是缠绕成型工艺的优缺点分析:
优点:
1. 设计灵活性较高:缠绕成型工艺可以生产各种不同形状和尺寸的产品,可以满足不同需求。
2. 成本较低:相对于其他复合材料加工工艺,缠绕成型工艺的生产成本较低,适用于大批量生产。
3. 强度高:通过缠绕成型工艺制造的产品具有较高强度,适用于各种高强度应用场景。
4. 耐腐蚀性好:由于采用了复合材料,缠绕成型产品具有较好的耐腐蚀性能,适用于一些特殊环境。
缺点:
1. 设备投资较高:缠绕成型过程需要专用的设备和模具进行操作,设备的投资成本较高。
2. 制造工艺复杂:缠绕成型过程需要严格控制工艺参数和工艺流程,操作技术要求较高。
3. 耗时较长:相比于其他加工方法,缠绕成型工艺的生产周期较长,不适合需求紧迫的场合。
4. 不适合大型异型产品:由于缠绕成型需要在模具上进行成型,对于大型异型
产品来说,模具制造和操作相对困难。
综上所述,缠绕成型工艺具有一定的优点和缺点,应根据具体需求和产品特性来选择是否采用该工艺。
缠绕
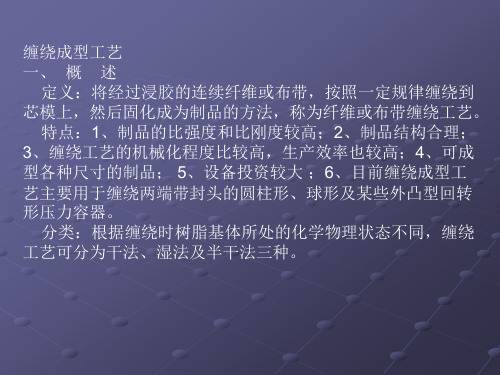
四、纤维缠绕规律 缠绕成型工艺要求连续纤维按照芯模和馈送纤维的丝嘴两个 系统相对运动的变化,在芯模上绕制成各种花纹。 要制成可用的制品,则必须要求把纤维按一定规律均匀地布满 在整个心模表面上。这种规律,就被称之为缠绕规律。 缠绕规律由芯模与丝嘴之间相对运动关系所决定。 缠绕规律可归结为环内缠绕、纵向平面缠绕和螺旋缠绕三种 类型。
缠绕成型工艺 一、 概 述 定义:将经过浸胶的连续纤维或布带,按照一定规律缠绕到 芯模上,然后固化成为制品的方法,称为纤维或布带缠绕工艺。 特点:1、制品的比强度和比刚度较高;2、制品结构合理; 3、缠绕工艺的机械化程度比较高,生产效率也较高;4、可成 型各种尺寸的制品; 5、设备投资较大 ;6、目前缠绕成型工 艺主要用于缠绕两端带封头的圆柱形、球形及某些外凸型回转 形压力容器。 分类:根据缠绕时树脂基体所处的化学物理状态不同,缠绕 工艺可分为干法、湿法及半干法三种。
缠绕过程中芯模与丝嘴的相对关系 1、单切点缠绕
丝嘴在芯模的纵向上经历了一个往复,同时围绕芯模旋转了 θ1,θ1角称为缠绕中心角。其值为:θ1=360+∆θ
∆θ与纱片宽度有关,设纱片宽为b,则:
式中D为圆筒段直径,α为圆筒段的缠绕角
(b)是单切点线型的另一种情况,称为“8”字形单切点缠绕线型, 其标准线在芯模的圆筒段上发生一次相交。丝嘴沿芯模纵向经历一 个往复,同时围绕芯模旋转角度为:
1 环向缠绕规律 线型:缠绕时,芯模绕本身轴线作匀速转动,丝嘴沿芯模筒 体段轴线方向均匀移动。芯模每转一周,丝嘴移动一个纱片宽度, 如此循环下去直至纱片均匀地布满芯模筒体段表面为止。 特点:1、 环向缠绕的纤维只提供环向强度;2、纤维的缠绕 角(即纤维缠绕在芯模上时,纤维方向与芯模轴线之间的夹角)通 常在85~90度之间。 方法:实现环向缠绕的缠绕机运动速比可以定义为:在单位 时间里芯模的转数Zm与丝嘴移动距离T的比值,即
缠绕成型工艺文件

缠绕成型工艺文件缠绕成型工艺是一种常用的制造工艺,广泛应用于航空航天、船舶、汽车、建筑等领域。
本文将从工艺流程、材料选择、设备要求等方面介绍缠绕成型工艺文件的相关内容。
一、工艺流程缠绕成型工艺的流程一般包括以下几个步骤:1. 准备工作:包括确定产品设计要求、选择合适的材料、准备模具等。
2. 简化模型制作:根据产品的几何形状,制作简化模型,用于计算纤维预浸料的用量和布放方式。
3. 纤维预浸料制备:将纤维和树脂进行预浸润处理,以提高纤维和树脂的结合力。
4. 缠绕工艺参数确定:根据产品的要求和纤维预浸料的性能,确定缠绕工艺参数,如缠绕角度、缠绕速度等。
5. 缠绕成型:根据缠绕工艺参数,在模具上进行纤维的缠绕成型。
6. 固化处理:对缠绕成型后的产品进行固化处理,使其达到设计要求的性能。
7. 后续处理:包括修整、表面处理等,以提高产品的外观和性能。
二、材料选择在缠绕成型工艺中,常用的纤维材料包括碳纤维、玻璃纤维、芳纶纤维等。
选择合适的纤维材料需要考虑产品的使用环境、强度要求、重量限制等因素。
同时,还需要选择合适的树脂,常见的树脂有环氧树脂、酚醛树脂等。
三、设备要求缠绕成型工艺需要使用一些专用设备,包括缠绕机、模具、树脂喷涂设备等。
缠绕机是实现纤维缠绕的主要设备,其性能和控制系统的稳定性对产品的成型质量有着重要影响。
模具的设计和制作需要根据产品的几何形状和尺寸进行,模具的表面光洁度和耐磨性也是关键因素。
树脂喷涂设备用于将树脂均匀地喷涂到纤维上,以提高纤维和树脂的结合力。
四、缠绕成型工艺文件的编制缠绕成型工艺文件是指对缠绕成型工艺进行规范和记录的文件。
它包括产品的设计要求、工艺参数、材料选择、设备要求、操作规程等内容。
编制缠绕成型工艺文件的目的是为了保证产品的质量和一致性,提高生产效率。
工艺文件的编制应根据实际情况进行,包括以下几个方面:1. 产品设计要求:包括产品的几何形状、尺寸、强度要求等。
2. 工艺参数:根据产品的要求和材料的性能,确定缠绕角度、缠绕速度、固化温度等参数。
缠绕成型工艺
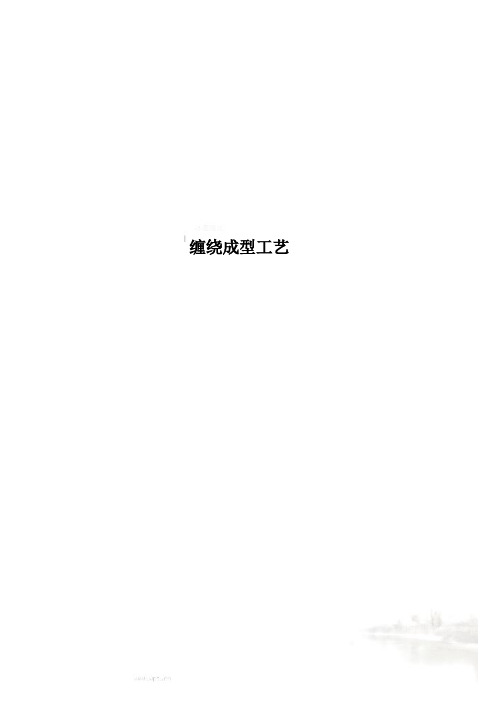
缠绕成型工艺缠绕成型工艺1.1纤维缠绕工艺的分类:缠绕工艺:将浸过树脂胶液的连续纤维或布带,按照一定规律缠绕到芯模上,然后固化脱模成为复合材料制品的工艺过程。
决定产品形状的模具基本纤维缠绕机1.1.1 干法缠绕将预浸纱带(或预浸布),在缠绕机上经加热软化至粘流状态并缠绕到芯模上的成型工艺过程。
干法缠绕特点:制品质量稳定(预浸纱由专用预浸设备制造,能较严格地控制纱带的含胶量和尺寸);缠绕速度快(100~200m/min); 缠绕设备清洁,劳动卫生条件好;预浸设备投资大。
干法缠绕制品质量较稳定,并可大大提高缠绕速度,可达到100m /min ~200m /min 。
缠绕设备清洁.劳动卫生条件较好。
玻璃钢.高压储气罐/碳纤维球1.1.2 湿法缠绕将无捻粗纱(或布带)经浸胶后直接缠绕到芯模上的成型工艺过程。
此法无须另行配置浸渍设备。
对材料要求不严,便于选材,故比较经济纱片质量及缠绕过程中张力不易控制。
特点:不需要预浸渍设备,设备投资少;对材料要求不严,便于选材;纱片质量不易控制和检验;张力不易控制;胶液中存在大量溶剂,固化时易产生气泡;浸胶辊、张力辊等要经常维护刷洗。
湿法缠绕工艺流程:原 材 料缠绕 设 备打磨喷漆胶液配制纱团集束固化 浸胶脱模 张力控制 纵、环 芯模制造制品 浸 胶 缠 绕增强材料:应用最广、量最大的是玻璃纤维。
此外有碳纤维,Kevlar 纤维等。
卧式缠绕机缠绕设备立式缠绕机卧式缠绕机立式缠绕机缠 绕 机 构纱架浸胶槽1.1.3 半干法缠绕将无捻粗纱(或布带)浸胶后,随即预烘干,然后缠绕到芯模上的成型工艺方法 与湿法相比,增加了烘干工序,除去了溶剂。
与干法相比,无需整套的预浸设备,缩短了烘干时间,使缠绕过程可在室温下进行。
提高了制品质量。
1.2 纤维缠绕制品的优点(1) 比强度高 FWRP 的比强度3倍于钛,4倍于钢i) 材料表面缺陷是影响其强度的重要因素。
表面积越大,缺陷率越高。
缠绕纤维直径很细,降低了微裂纹存在几率;所用纤维主要是无捻粗纱由于没有经过纺织工序,强度损失大大减少。
缠绕成型工艺及应用
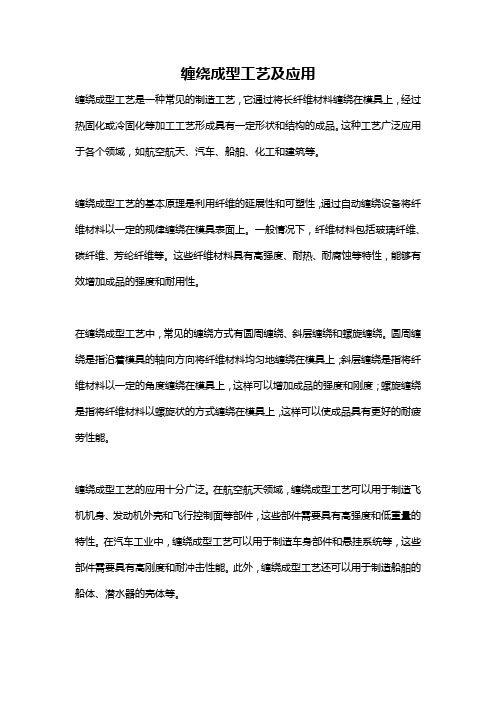
缠绕成型工艺及应用缠绕成型工艺是一种常见的制造工艺,它通过将长纤维材料缠绕在模具上,经过热固化或冷固化等加工工艺形成具有一定形状和结构的成品。
这种工艺广泛应用于各个领域,如航空航天、汽车、船舶、化工和建筑等。
缠绕成型工艺的基本原理是利用纤维的延展性和可塑性,通过自动缠绕设备将纤维材料以一定的规律缠绕在模具表面上。
一般情况下,纤维材料包括玻璃纤维、碳纤维、芳纶纤维等。
这些纤维材料具有高强度、耐热、耐腐蚀等特性,能够有效增加成品的强度和耐用性。
在缠绕成型工艺中,常见的缠绕方式有圆周缠绕、斜层缠绕和螺旋缠绕。
圆周缠绕是指沿着模具的轴向方向将纤维材料均匀地缠绕在模具上;斜层缠绕是指将纤维材料以一定的角度缠绕在模具上,这样可以增加成品的强度和刚度;螺旋缠绕是指将纤维材料以螺旋状的方式缠绕在模具上,这样可以使成品具有更好的耐疲劳性能。
缠绕成型工艺的应用十分广泛。
在航空航天领域,缠绕成型工艺可以用于制造飞机机身、发动机外壳和飞行控制面等部件,这些部件需要具有高强度和低重量的特性。
在汽车工业中,缠绕成型工艺可以用于制造车身部件和悬挂系统等,这些部件需要具有高刚度和耐冲击性能。
此外,缠绕成型工艺还可以用于制造船舶的船体、潜水器的壳体等。
在化工领域,缠绕成型工艺可以用于制造化工设备的容器、管道和阀门等。
这些设备需要具有耐腐蚀性和耐高温性能。
在建筑领域,缠绕成型工艺可以用于制造各种异型结构件,如碳纤维制品、玻璃纤维制品和混凝土增强材料等。
总的来说,缠绕成型工艺是一种重要的制造工艺,它可以制造出高性能、轻量化和耐用的成品。
随着纤维材料的发展和工艺的不断改进,缠绕成型工艺在各个领域的应用也将更加广泛。
- 1、下载文档前请自行甄别文档内容的完整性,平台不提供额外的编辑、内容补充、找答案等附加服务。
- 2、"仅部分预览"的文档,不可在线预览部分如存在完整性等问题,可反馈申请退款(可完整预览的文档不适用该条件!)。
- 3、如文档侵犯您的权益,请联系客服反馈,我们会尽快为您处理(人工客服工作时间:9:00-18:30)。
缠绕成型工艺1.1纤维缠绕工艺的分类:缠绕工艺:将浸过树脂胶液的连续纤维或布带,按照一定规律缠绕到芯模上,然后固化脱模成为复合材料制品的工艺过程。
决定产品形状的模具基本纤维缠绕机浸胶 胶纱纱锭 张力控制 固化 打模喷漆 脱模 芯模制造胶液配制纱团集束烘干 络纱 加热粘流纵、环向缠绕张力控制 纵、环向缠绕成品湿法缠绕干法缠绕玻璃钢.高压储气罐/碳纤维球1.1.1 干法缠绕将预浸纱带(或预浸布),在缠绕机上经加热软化至粘流状态并缠绕到芯模上的成型工艺过程。
干法缠绕特点:制品质量稳定(预浸纱由专用预浸设备制造,能较严格地控制纱带的含胶量和尺寸);缠绕速度快(100~200m/min); 缠绕设备清洁,劳动卫生条件好;预浸设备投资大。
干法缠绕制品质量较稳定,并可大大提高缠绕速度,可达到100m/min~200m/min。
缠绕设备清洁.劳动卫生条件较好。
1.1.2 湿法缠绕将无捻粗纱(或布带)经浸胶后直接缠绕到芯模上的成型工艺过程。
此法无须另行配置浸渍设备。
对材料要求不严,便于选材,故比较经济纱片质量及缠绕过程中张力不易控制。
特点:不需要预浸渍设备,设备投资少;对材料要求不严,便于选材;纱片质量不易控制和检验;张力不易控制;胶液中存在大量溶剂,固化时易产生气泡;浸胶辊、张力辊等要经常维护刷洗。
湿法缠绕工艺流程:原 材 料缠 绕 设 备打磨喷漆胶液配制纱团集束固化浸胶脱模 张力控制纵、环芯模制造制品浸 胶 缠 绕增强材料:应用最广、量最大的是玻璃纤维。
此外有碳纤维,Kevlar 纤维等。
卧式缠绕机缠绕设备立式缠绕机卧式缠绕机立式缠绕机缠绕机构纱架浸胶槽张力控制器1.1.3 半干法缠绕将无捻粗纱(或布带)浸胶后,随即预烘干,然后缠绕到芯模上的成型工艺方法与湿法相比,增加了烘干工序,除去了溶剂。
与干法相比,无需整套的预浸设备,缩短了烘干时间,使缠绕过程可在室温下进行。
提高了制品质量。
1.2 纤维缠绕制品的优点(1) 比强度高FWRP的比强度3倍于钛,4倍于钢i) 材料表面缺陷是影响其强度的重要因素。
表面积越大,缺陷率越高。
缠绕纤维直径很细,降低了微裂纹存在几率;所用纤维主要是无捻粗纱由于没有经过纺织工序,强度损失大大减少。
(ii) 避免了布纹经纬交织点与短切纤维末端的应力集中(iii) 可以控制纤维的方向和数量,使产品实现等强度结构(ⅳ) 增强材料纤维含量高达80%(2) 可靠性高纤维缠绕复合材料制品基本解决了金属韧性随强度的提高而降低这一矛盾。
(3) 生产效率高,制品质量高而稳定,可实现机械化、自动化操作,生产效率高,便于大批量生产。
(4) 材料成本低,所用增强材料大多是无捻粗纱等连续纤维,减少了纺织和其它加工费用,材料成本低。
1.3 原材料主要有纤维增强材料与树脂基体两大类:(1)增强材料主要是中碱、无碱粗纱。
另外有玻璃布带、碳纤维、芳纶纤维等。
应根据不同产品对性能的要求进行选用。
(1) 航空和航天制品多选用性能优异价格昂贵的碳纤维和芳纶纤维,民用产品多选用连续玻璃纤维;(2) 满足制品的性能要求;(3) 纤维都必须进行表面处理;(4) 与树脂浸渍性好,浸透速度快;(5) 各股纤维张力均匀;(6) 成带性好,不起毛,不断头。
(2)树脂体系树脂及各种助剂、填料常用:不饱和聚酯树脂,环氧树脂(双酚A型)、酚醛-环氧树脂(环氧改性酚醛树脂)。
不饱和聚酯:含有非芳族的不饱和键,由不饱和二元羧酸或酸酐、饱和二元羧酸或酸酐与多元醇缩聚而成的具有酯键和不饱和双键的相对分子质量不高的线型高分子化合物。
不饱和聚酯树脂:在聚酯化缩聚反应结束后,趁热加入一定量的乙烯基单体,配成粘稠的液体,这样的聚合物溶液称之为不饱和聚酯树脂。
2 芯模外形同制品内腔形状尺寸一致,对芯模要求:1)足够的强度和刚度。
制造过程中要求芯模能够保证制品的结构尺寸及承受张力、固化热应力的载荷等。
(2)必须满足制品的精度要求。
(3)制作工艺简单、周期短,材料来源广,价格低。
(4)制品完成后,要求芯模能顺利清除干净,而不影响制品质量。
2.1芯模材料主要是钢材、木材、塑料、铝、石膏、水泥、低熔点金属、低熔点盐类等,国外较多用低熔点金属、低熔点盐,制造芯模时将其熔化浇铸成壳体,脱模时加入热水搅拌溶解或用蒸汽熔化。
2.1.1 芯模材料对制品的影响膨胀系数影响产品尺寸精度;弹性模量影响产品力学性能及尺寸精度;导热系数影响产品固化度;芯模中水份影响产品固化,甚至引起分层开裂。
采用易敲碎的材料;可溶或易熔盐类;将其熔化用铸造法浇铸成壳体,脱模时加入热水溶解低熔点金属;由可溶或易熔粘结剂粘起来的集合体。
分瓣式采用弓形铝合金片构成回转体,外表采用石膏隔板支撑金属细管,捆扎后用金属管捆扎成芯模,外表层刮石膏隔板式捆扎式框架装配式由芯轴、预制石膏板、铝管及石膏面层等部分构成高温固化,石膏脱水对制品质量有影响,不适于加压固成型工艺简单、成本低,适用于缺点:2.1.3 组合式芯模2.1.4 石膏隔板组合式芯模优点:2.2 圆筒芯模整体式芯模开缩式芯模开缩式芯模:芯模有中心轴,沿轴一定距离有一组可伸缩辐条式机构支撑轮状环。
用于支撑芯模外壳。
脱模时,通过液压的机械装置,使芯模收缩并从固化的制品中脱下来、然后再将芯模恢复到原始位置。
整体式芯模:1、具有经抛光的高精度表面2、具有锥度,不小于1/1000(便于脱模)2.3缠绕规律缠绕规律:描述纱片均匀、稳定、连续、排布在芯模表面,以及芯模与导丝头间运动关系的规律。
要求:(1) 纤维既不重叠又不离缝,均匀连续布满芯模表面。
(2) 纤维在芯模表面位置稳定,不打滑。
2.3.1 缠绕线型分类(1) 环向缠绕芯模绕自轴匀速转动,导丝头在筒身区间作平行于轴线方向运动。
芯模自转一周,导丝头近似移动一个纱片宽度的缠绕。
(只能缠绕直筒段)b(2) 螺旋缠绕:芯模绕自轴匀速转动,导丝头依特定速度沿芯模轴线方向往复运动。
可以缠绕圆筒段,也可缠绕端头(封头)。
纤维缠绕轨迹:由圆筒上的螺旋线和封头上与极孔相切的空间曲线组成。
(3)纵向缠绕(又称平面缠绕)导丝头在固定平面内做匀速圆周运动,芯模绕自轴慢速旋转,导丝头转一周,芯模转动微小角度,反映在芯模表面上近似一个纱片宽度。
纱片与芯模轴线间成0°~ 25°交角,纤维轨迹是一条单圆平面封闭曲线。
平面缠绕、缠绕角的正切值:2121e e c l l l r r tg +++=α平面缠绕参数关系图2.3.1螺旋缠绕线型连续纤维缠绕在芯模表面上的排布型式 (1)一个完整循环的概念螺旋缠绕时,由导丝头引入的纤维自芯模上某点开始(空间点),导丝头经过若干次往返运动后,又缠回到原来的起始点上(空间点)。
这样在芯模上所完成的一次(不重复)布线称为“标准线”。
完成一个标准线缠绕称为一个完整循环。
“标准线”是反映缠绕规律的基本线型。
纤维在芯模表面均匀布满的条件 (2)一个完整循环的切点数及分布规律 a 、切点位置“时序相邻”和“位置相邻”的概念在极孔圆周上按时间顺序相继出现的两个切点称为时序相邻的两切点。
时序相邻的切点的位置只能有两种情况:1) 两切点紧密排布,中间不能再加入其他切点, 称为两切点“位置相邻”。
平面缠绕的速比:单位时间内,芯模旋转周数与导丝头绕芯模旋转的圈数比或绕丝头转一圈时导丝头绕芯模旋转的圈数。
απcos D b i =纱片宽度缠绕角2) 两切点之间还可以加入其他切点,称两切点位置不相邻。
b、单切点与多切点的概念单切点缠绕:完成一个完整循环缠绕,极孔圆周上只有一个切点的情况。
多切点缠绕:完成一个完整循环缠绕,极孔圆周上有多个切点的情况完成一个完整的循环缠绕有两种情况:1) 时序相邻的两切点位置也相邻。
即在出现与初始切点位置相邻的切点以前,极孔上只有一个切点,这种缠绕线形称单切点线型。
2) 在出现与起始切点位置相邻的切点以前,极孔上已经出现了两个或两个以上切点,即时序相邻切点位置不相邻,这种缠绕线形称为多切点线型。
在极孔上的切点线型排布c 、一个完整循环的n 个切点必将等分极孔圆周由于芯模匀速转动,丝嘴每往返一次的时间又相同。
因此,一个完整循环的n 点切点必将等分极孔圆周。
3)纤维在芯模表面均匀布满的条件a 、一个完整循环的诸切点均布在极孔圆周上。
b 、位置相邻的两切点所对应的纱片在筒身段错开的距离等于一个纱片宽度。
2.3.2 纤维缠绕芯模转角(即缠绕中心角)与线型的关系设完成一个n 切点的完整循环缠绕,芯模转角为θ,导丝头每往返一次芯模转角为θn ,则:当从切点1绕到切点2或从切点2绕到切点3时,芯模转过中心角将是360°土Δθ,或者再加上360 °的整数倍。
θn 的推导:n=3 n=4n=55单切点: θ1=(1+N)360°±Δθ (N=0,1,2,······)其中Δθ是使位置相邻的两切点对应的纱片在筒身段错开一个纱片的距离。
两切点:一个完整循环导丝头往返2次才错过一个Δθ,导丝头往返一次时应错开Δθ/2。
θ2=[(1+N)360°±Δθ]/2=(1/2+N) 360°±Δθ/212 3三切点:θ3=[(1+N)360°±Δθ]/3 =(1/3+N) 360°±Δθ/3但是,n ≥3时各切点的排序与时间顺序不一定一致,例如θ3有2个值:θ3-1=(1/3+N )360°±Δθ/3θ3-2=(2/3+N )360°±Δθ/33124n=3θ5有4个值:θ5-1=(1/5+N)360°±Δθ/5θ5-2=(2/5+N)360°±Δθ/5θ5-3=(3/5+N)360°±Δθ/5θ5-4=(4/5+N)360°±Δθ/5则对于θn有θn=(K/n +N)360°±△θ/n K值需要使K/n为最简真分数。
在一个完整循环中,切点数不同,纤维缠绕的线型不同,导丝头往返一次芯模转角不同;如果在一个完整的循环中,切点数相同而切点排布顺序不同,则线型也不相同,导丝头往返一次的芯模转角也不同。
1n=3 n=4 n=512312312 3 4123412 3 4514 2 53 35 2415432“线型”以导丝头往返一次芯模旋转的转数来表示:S 0= θn /360° M=K + nNS 0-表示线型;M ——一个完整循环芯模转数; n ——切点数,也是一个完整循环导丝头往返次数。
不考虑芯模转角微调量θn =(K/n +N)360°±△θ/n S 0= K/n + N =M/n连续纤维缠绕在芯模表面上2.3.3 螺旋缠绕的转速比nM i =单位时间内,芯模转数与导丝头往返次数之比,完成一个完整循环,芯模转数与导丝头往返次数之比。