精磨工艺知识
镜面研磨工艺
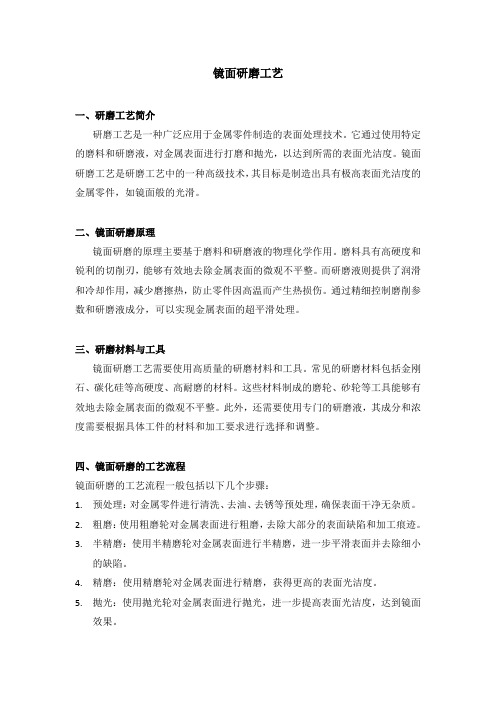
镜面研磨工艺一、研磨工艺简介研磨工艺是一种广泛应用于金属零件制造的表面处理技术。
它通过使用特定的磨料和研磨液,对金属表面进行打磨和抛光,以达到所需的表面光洁度。
镜面研磨工艺是研磨工艺中的一种高级技术,其目标是制造出具有极高表面光洁度的金属零件,如镜面般的光滑。
二、镜面研磨原理镜面研磨的原理主要基于磨料和研磨液的物理化学作用。
磨料具有高硬度和锐利的切削刃,能够有效地去除金属表面的微观不平整。
而研磨液则提供了润滑和冷却作用,减少磨擦热,防止零件因高温而产生热损伤。
通过精细控制磨削参数和研磨液成分,可以实现金属表面的超平滑处理。
三、研磨材料与工具镜面研磨工艺需要使用高质量的研磨材料和工具。
常见的研磨材料包括金刚石、碳化硅等高硬度、高耐磨的材料。
这些材料制成的磨轮、砂轮等工具能够有效地去除金属表面的微观不平整。
此外,还需要使用专门的研磨液,其成分和浓度需要根据具体工件的材料和加工要求进行选择和调整。
四、镜面研磨的工艺流程镜面研磨的工艺流程一般包括以下几个步骤:1.预处理:对金属零件进行清洗、去油、去锈等预处理,确保表面干净无杂质。
2.粗磨:使用粗磨轮对金属表面进行粗磨,去除大部分的表面缺陷和加工痕迹。
3.半精磨:使用半精磨轮对金属表面进行半精磨,进一步平滑表面并去除细小的缺陷。
4.精磨:使用精磨轮对金属表面进行精磨,获得更高的表面光洁度。
5.抛光:使用抛光轮对金属表面进行抛光,进一步提高表面光洁度,达到镜面效果。
五、镜面研磨的质量控制在镜面研磨过程中,质量控制是关键。
需要严格控制研磨参数,如压力、转速、温度等。
同时,需要定期检查和更换研磨材料和工具,确保其性能和质量。
此外,还需要对研磨后的零件进行严格的检测,如表面粗糙度、尺寸精度等,以确保达到设计要求。
六、研磨液的选择与使用研磨液的选择和使用对于镜面研磨工艺至关重要。
需要根据具体工件的材料和加工要求选择合适的研磨液成分和浓度。
同时,在使用过程中,需要严格控制研磨液的用量和温度,以防止零件过热或过度腐蚀。
晶圆减薄研磨工艺
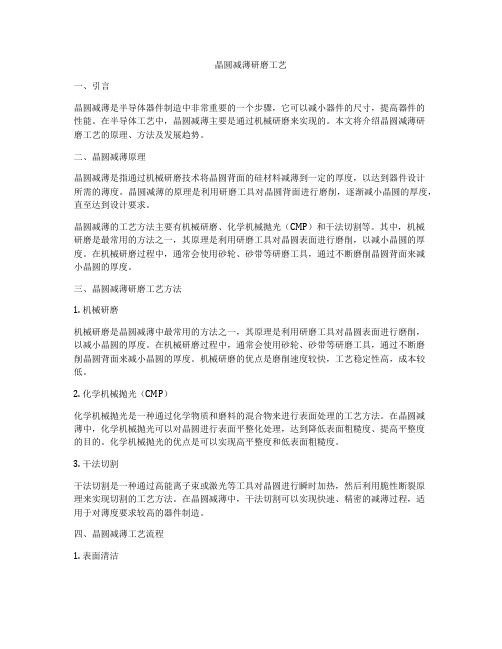
晶圆减薄研磨工艺一、引言晶圆减薄是半导体器件制造中非常重要的一个步骤,它可以减小器件的尺寸,提高器件的性能。
在半导体工艺中,晶圆减薄主要是通过机械研磨来实现的。
本文将介绍晶圆减薄研磨工艺的原理、方法及发展趋势。
二、晶圆减薄原理晶圆减薄是指通过机械研磨技术将晶圆背面的硅材料减薄到一定的厚度,以达到器件设计所需的薄度。
晶圆减薄的原理是利用研磨工具对晶圆背面进行磨削,逐渐减小晶圆的厚度,直至达到设计要求。
晶圆减薄的工艺方法主要有机械研磨、化学机械抛光(CMP)和干法切割等。
其中,机械研磨是最常用的方法之一,其原理是利用研磨工具对晶圆表面进行磨削,以减小晶圆的厚度。
在机械研磨过程中,通常会使用砂轮、砂带等研磨工具,通过不断磨削晶圆背面来减小晶圆的厚度。
三、晶圆减薄研磨工艺方法1. 机械研磨机械研磨是晶圆减薄中最常用的方法之一,其原理是利用研磨工具对晶圆表面进行磨削,以减小晶圆的厚度。
在机械研磨过程中,通常会使用砂轮、砂带等研磨工具,通过不断磨削晶圆背面来减小晶圆的厚度。
机械研磨的优点是磨削速度较快,工艺稳定性高,成本较低。
2. 化学机械抛光(CMP)化学机械抛光是一种通过化学物质和磨料的混合物来进行表面处理的工艺方法。
在晶圆减薄中,化学机械抛光可以对晶圆进行表面平整化处理,达到降低表面粗糙度、提高平整度的目的。
化学机械抛光的优点是可以实现高平整度和低表面粗糙度。
3. 干法切割干法切割是一种通过高能离子束或激光等工具对晶圆进行瞬时加热,然后利用脆性断裂原理来实现切割的工艺方法。
在晶圆减薄中,干法切割可以实现快速、精密的减薄过程,适用于对薄度要求较高的器件制造。
四、晶圆减薄工艺流程1. 表面清洁在进行晶圆减薄之前,首先需要对晶圆表面进行清洁处理,以确保研磨过程中不受到杂质的干扰。
2. 粗磨经过表面清洁处理后,将晶圆放入研磨设备中进行粗磨。
在粗磨过程中,通常会选择适当的研磨工具和磨料,以尽快减小晶圆的厚度。
3. 精磨粗磨完成后,再将晶圆放入研磨设备中进行精磨。
磨工(技师、高级技师)第一章
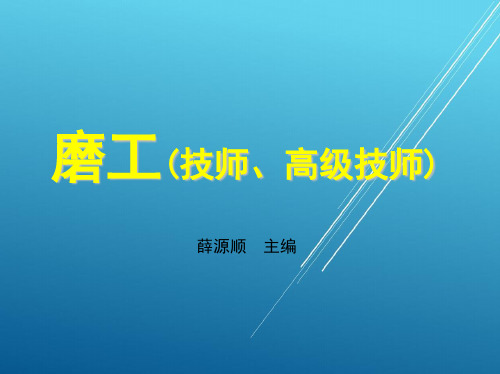
第一节 高精度轴类、套类零
削作用外,主要是对工件表面强烈的摩擦、抛光作用。 (4)低应力磨削 微刃与工件表面间维持着一定的磨削压力,低表面 粗糙度磨削是低应力磨削。
3.镜面磨削加工实例
第一节 高精度轴类、套类零
图1-8 精密轧辊
1)为了保证轧辊面的加工精度,
第一节 高精度轴类、套类零
轧辊面应分精磨、超精磨和镜面磨削。 2)在MG1432B型高精度万能外圆磨床上超精磨ϕ120mm外圆。 选择砂轮特性:WAF230K。 3)在MG1432B型高精度万能外圆磨床上镜面磨ϕ120mm外圆。 选择砂轮特性:WA/GC(白刚玉、绿色碳化硅混合磨料加石墨)F600K, 用树脂结合剂砂轮。
(2)机械传动系统主要部件的结构
第一节 高精度轴类、套类零
图1-2 头架 1、2—带轮 3—手柄 4—壳体 5—底座 6、7—离合器 8—拨盘 9、13—轴承 10—弹簧 11—主轴 12—螺母 14—滚柱推力支承
15、16—十字垫圈 17—螺套 18—刻度盘 19—圆盘
第一节 高精度轴类、套类零
7.砂轮架快速引进故障
砂轮架快速引进故障是重复定位精度超差,原因是:
第一节 高精度轴类、套类零
1)定位螺钉松动。 2)砂轮架快速引进位置调整不当。 3)砂轮架快速进退液压缸中单向阀密封不良。 检修方法是: 1)调整砂轮架快速引进位置,松开砂轮架垫板前端的方头定位螺钉, 调整方头螺钉时使砂轮架后退0.02~0.04mm,并锁紧螺母,检测10次, 使引进千分表读数误差小于0.002mm。 2)拆卸液压缸端盖,敲击单向阀中钢球与端盖孔中锥形座,使其紧密 接触,使单向阀恢复密封性。
第一节 高精度轴类、套类零
四、低表面粗糙度磨削工艺
高精度磨削加工中,使工件表面粗糙度值低于Ra0.2μm的磨削称为 低表面粗糙度磨削。
精密研磨陶瓷材料工艺流程
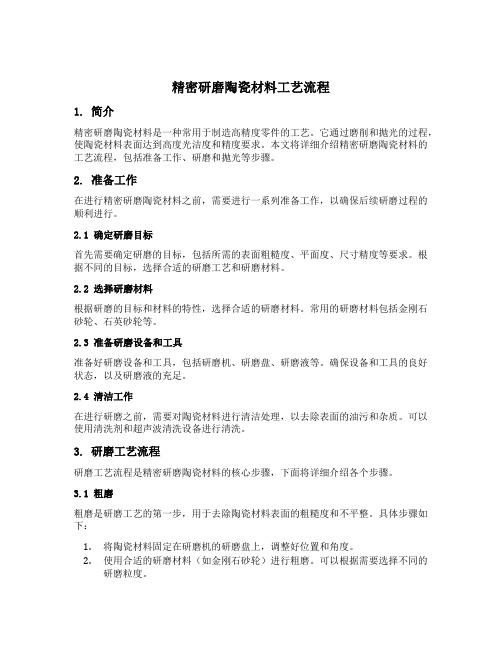
精密研磨陶瓷材料工艺流程1. 简介精密研磨陶瓷材料是一种常用于制造高精度零件的工艺。
它通过磨削和抛光的过程,使陶瓷材料表面达到高度光洁度和精度要求。
本文将详细介绍精密研磨陶瓷材料的工艺流程,包括准备工作、研磨和抛光等步骤。
2. 准备工作在进行精密研磨陶瓷材料之前,需要进行一系列准备工作,以确保后续研磨过程的顺利进行。
2.1 确定研磨目标首先需要确定研磨的目标,包括所需的表面粗糙度、平面度、尺寸精度等要求。
根据不同的目标,选择合适的研磨工艺和研磨材料。
2.2 选择研磨材料根据研磨的目标和材料的特性,选择合适的研磨材料。
常用的研磨材料包括金刚石砂轮、石英砂轮等。
2.3 准备研磨设备和工具准备好研磨设备和工具,包括研磨机、研磨盘、研磨液等。
确保设备和工具的良好状态,以及研磨液的充足。
2.4 清洁工作在进行研磨之前,需要对陶瓷材料进行清洁处理,以去除表面的油污和杂质。
可以使用清洗剂和超声波清洗设备进行清洗。
3. 研磨工艺流程研磨工艺流程是精密研磨陶瓷材料的核心步骤,下面将详细介绍各个步骤。
3.1 粗磨粗磨是研磨工艺的第一步,用于去除陶瓷材料表面的粗糙度和不平整。
具体步骤如下:1.将陶瓷材料固定在研磨机的研磨盘上,调整好位置和角度。
2.使用合适的研磨材料(如金刚石砂轮)进行粗磨。
可以根据需要选择不同的研磨粒度。
3.开始研磨,保持适当的研磨压力和速度,确保研磨均匀。
4.定期检查研磨效果,调整研磨条件和参数,直到达到要求的粗糙度和平面度。
3.2 中磨中磨是在粗磨之后进行的一道工序,用于进一步提高陶瓷材料的平面度和精度。
具体步骤如下:1.使用较细的研磨材料(如石英砂轮)进行中磨。
选择合适的研磨粒度,通常比粗磨要细。
2.调整研磨机的参数,如研磨压力、速度等,以获得更好的研磨效果。
3.进行中磨,保持适当的研磨压力和速度,确保研磨均匀。
4.定期检查研磨效果,调整研磨条件和参数,直到达到要求的平面度和精度。
3.3 精磨精磨是研磨工艺的最后一道工序,用于进一步提高陶瓷材料的光洁度和精度。
齿轮精磨后的工艺流程

齿轮精磨后的工艺流程英文回答:Gear grinding is a precision machining process used to improve the surface finish and dimensional accuracy of gears. It involves removing material from the gear teeth using a grinding wheel. The process is typically performed after the gears have been heat-treated and hardened to achieve the desired hardness and strength.The gear grinding process can be divided into several steps:1. Set-up: The first step is to set up the gear grinding machine. This involves mounting the gear on the machine's work spindle and aligning it properly. The machine's settings, such as the grinding wheel speed and feed rate, are also adjusted.2. Pre-grinding: Before the actual grinding process, apre-grinding operation is often performed. This involves removing any burrs or sharp edges from the gear teeth to ensure a smooth and even grinding process.3. Grinding: The grinding operation begins with the grinding wheel coming into contact with the gear teeth. The grinding wheel is typically made of abrasive materials such as aluminum oxide or cubic boron nitride. As the wheel rotates, it removes material from the gear teeth, gradually shaping them into the desired profile. The grinding process is carefully controlled to achieve the required surface finish and dimensional accuracy.4. Inspection: After the grinding process, the gears are inspected to ensure that they meet the specified requirements. This may involve using various measurement tools, such as micrometers and gear testers, to check the gear's dimensions, tooth profile, and surface finish.5. Finishing operations: Depending on the application and requirements, additional finishing operations may be performed after the grinding process. These operations caninclude deburring, polishing, and coating to further improve the gear's performance and durability.6. Final inspection: Once all the finishing operations are completed, a final inspection is conducted to verify that the gears meet all the specified criteria. This ensures that the gears are ready for assembly and use in various mechanical systems.In summary, the process of gear grinding involves setting up the machine, pre-grinding the gear teeth, performing the grinding operation, inspecting the gears, conducting finishing operations if necessary, and conducting a final inspection. This process ensures that the gears have the desired surface finish, dimensional accuracy, and performance characteristics.中文回答:齿轮精磨是一种用于改善齿轮表面光洁度和尺寸精度的精密加工工艺。
精磨工艺

精磨工艺.txt喜欢我这是革命需要,知道不?!你不会叠衣服一边呆着去!以后我来叠!我一定要给你幸福,谁也别想拦着。
第四章精磨精磨又称细磨。
它是介于粗磨与抛光两大工序之间的重要工序。
精磨的目的是保证工件达到抛光前所需要的面形精度、尺寸精度和表面粗糙度。
因此,精磨的质量对抛光的影响是非常重要的。
精磨的方法分为散粒磨料精磨和金刚石精磨。
前者称为古典法精磨,又称自由研磨;后者称为高速精磨。
§4—1精磨的技术要求与技术分类一、精磨的技术要求。
1、表面粗糙度要求粗磨完工的光学玻璃表面粗糙度比较大,即表面凹凸程度很严重。
散粒磨料加工常以金刚砂研磨后留下来的表面,其玻璃表面破坏层约30微米,表面粗糙度RZ小于6微米;固着磨料加工常以金刚石砂轮加工的表面,其表面破坏层约50微米,表面粗糙度RZ约在0.9微米以下。
精磨的目的之一,就是要使光学玻璃表面凹凸程度变小,以达到能被抛光抛去的程度。
目前情况下认为:用散粒磨料以金刚砂加工后破坏层在12微米以下,粗糙度在0.4微米以下;固着磨料加工时,以W10金刚石丸片加工后的破坏层在8微米以下,表面粗糙度Rz在0.35微米以下。
2、几何面形精度要求光学完工的几何面形要求—般很高,往往是在微米级精度,要达到这样高的精度,只能通过精磨这道工序逐级提高,从而为最后的抛光工序作好准备。
在古典法抛光中,精磨后的表面几何形状要比抛光完工零件差4~8个牛顿干涉圈,大约2微米左右;在现代高速抛光中只能相差2个牛顿干涉圈,约0.5微米左右。
这里要注意,在实际生产中,精磨后的面形应该是低光圈,这时对凸透镜来说是曲率半径应大一些,而对凹透镜则相反,曲率半径要小一些。
二、精磨方法的分类精磨一般可以分为散粒磨料研磨法和固着磨料法。
后者又分为:成型面形工具和范成法之分。
散粒磨料精磨也称古典法,就是以金属成型模具(通常用黄铜),中间加上金刚砂对玻璃逐步研磨。
每更换一次磨料粒度就得更换一个曲率半径的球摸。
光学零件工艺第9章透镜的精磨

第一节 光学零件的上盘
一、球面零件上盘 1. 弹性上盘
制作火漆团
加热工件
放火漆团
放工件于贴置模
放粘结模
冷却
特点:
以被加工面为基准,粘结模简单,通用性大, 缺点是不能承受高速高压工艺条件,工房间温 度梯度不能太大。
注意事项:粘结模温度不宜过高;粘结模要放正; 可用专用装置的粘结模以确保精度。
好
表面粗糙度 1.6-0.4 0.4-0.1 0.05-0.025
加工余量 0.04-0.06 0.01-0.02 0.005-0.01
差
表面粗糙度 3.2-0.8 0.8-0.2 0.1-0.025
加工余量 0.06-0.08 0.015-
0.01-0.02
0.03
三、常见疵病及产生原因
名称
产生原因
2. 刚性上盘
加热粘结模
贴粘结纸
粘贴工件
冷却
特点:过程简单、粗磨可以成盘加工, 能承受较高速度和压力;以粘结面为 基准面。粘结模专用性强,加工模具 成本高。
注意事项:工件在承座上要放正;工 件间胶层厚度要均匀一致。
3、弹性上盘镜盘设计
主要设计粘结模上零件可以放多少圈?每圈可以放多少个? 盖比/% 100~55 60~40
超精磨覆盖比/% 100~60 65~45
Z—精磨片的总数目 AP—精磨片的表面积 Hjm—精磨模的矢高 hjm—精磨片的矢高
30~50 45~35 50~40
50~120 40~20 45~25
>120 <25 <30
余弦磨损
球面精磨模在使用过程中其加工面的曲率半径 始终不变,而且被加工面的光圈稳定,这就是所谓 的余弦磨损。
精磨工艺知识

仪条纹﹐在白光照射下﹐可见到彩色光环﹐这种彩色光环称为光圈﹐物理学中称为牛顿环 。
•
2.面本数 红色光圈有几圈﹐面本数就有几本.
• 二、正光圈、负光圈的识别:
• 原器区分
•
负光圈: 当空气隙缩小时,条纹从边缘向中心移动。
•
正光圈: 当空气隙缩小时,条纹从中心向边缘移动。
颜色区分
负光圈 正光圈
•
正光圈:从中心到边缘的颜色顺序为黄、红、蓝。
• 2.测量时要每两小时用规零镜片规零一次。
• 3、检查项目要全面,不可漏检或不检
依据镜片形状选择测量方法:
• 双凸镜片
• 两面凹时
• 测量镜片为一面凹一 • :一面平一面凸时:
面凸时:
光圈
• 一﹑光圈概述
•
1.被检查镜片表面与标准曲率半径的原器面形有偏差时﹐它们之间形成对称的契形空气间隙﹐从面产生等干涉
子一般是硬质合金材料,我司也有铁端子 主要用于大镜盘。
• 3、夹具:固定镜片使镜片受力平衡,达到均
匀磨削的目的
• 4、合修砂:(分为600#、800# 、
1000#、1500# 、2000#)粗砂磨削快 修出的皿易垂边,细砂修复时较长,但修 出来的皿精度较好,所以我们要综合选 用合修砂。
• 5、测定环:测量曲率时的参照标准,一般情况
钻石型号
自锐性
适用性
特性
503V*1500
强+
快+
成本高,一般不使用
主要针对用49B易 打滑,磨耗度 150以下材料
49B*1500 18B*1500 18A*1500
强 稍差 强
快 稍差 稍差
通用
主要用于磨耗度180 以下材料
一般不使用
- 1、下载文档前请自行甄别文档内容的完整性,平台不提供额外的编辑、内容补充、找答案等附加服务。
- 2、"仅部分预览"的文档,不可在线预览部分如存在完整性等问题,可反馈申请退款(可完整预览的文档不适用该条件!)。
- 3、如文档侵犯您的权益,请联系客服反馈,我们会尽快为您处理(人工客服工作时间:9:00-18:30)。
二支无法磨削掉第一支所造成的伤痕,除非镜片材质硬用
三段加工时方考虑使用,其较适合做LAP皿
• 磨耗度:①65以下镜片外径ø3~φ30以内第一支用
SP49B1500#,第二支用SP33A#1800。
•
② 65以下镜片外径φ30以上第一支用a402 -
1500#,第二支用R10-1500#或SP27C1500#
•
∪Rx----表示总形钻石,一面为∪Rx,另一面为∞
•
Rx------表示颗粒钻石,两面曲率相等
•
X-------表示ห้องสมุดไป่ตู้石曲率
•
Φ-------表示钻石粒外径
•
#---------表示钻石粒度
•
T--------表示钻石粒高度
• 字母及数字组合则表示型号,如49B.R6…
• 假设一个总形钻石曲率为⊥R15,有效径为28Φ,高度为5T,粒度
•
③70~150,第一支用SP49B1500#,第二支用
SP33A1800#。
•
④160~200第一支用SP18B1500#,第二支用
SP27C2000#。
•
⑤ 200以上第一支用SP27C1000#第二支用
TR146A1300#。
砂挂S1钻石的设定主要考虑1.钻石自锐性﹒2.研削能力﹒3.S1完成品外观﹒4﹒研磨完成品外观﹒ 研削能力
挂第2支(精加工)→研磨(抛光)。
• 砂挂第1支特点:
•
金属基、切削力较强,一般切削8~12条厚度,
表面较光滑,呈雾状,弧度△h:0~-1条,确保镜
片厚度、弧度。
• 砂挂第2支特点:
• 树脂基,切削力弱,5~30秒切削1~2条厚度,
表面光滑透明,单检灯下略 带雾状,确保镜片光圈
外观。
三、 加工原理:
树脂型号
自锐性
研削能力
适用性
R6*1500
强
快
通用
R6*1800 27C*2000 RP334*1800
强
快
强 稍差(R6)
稍差 稍差(R6)
通用 通用 R6的替代品
特性
外观较粗糙,完品较蒙主要用于磨耗度 130以下的材料.也可做软材料(400)以上
的S1.
外观较粗糙,完品较蒙主要用于磨耗度 130~170的材料
砂挂基础知识讲座
讲解者:杨 会
目录
• 一、砂挂工程简介 • 二、砂挂工程定义 • 三、砂挂工程原理 • 四、砂挂辅材介绍 • 五、砂挂现用机台介绍 • 六、其它辅材介绍 • 七、弧度、厚度、光圈的测量方法 • 八、砂挂不良的原因及对策
一、简介
• 1、砂挂 -----------日文名,在大陆意义为精磨是
能看到面本数就不行)
• 2..S1砂挂完成品不能有发亮的砂目(白白的一块一
块的,一般分布在中心或边缘位置)
二、砂挂工程定义:
• 镜片加工流程:荒摺(NCG)→砂挂(精磨)→研磨
(抛光)
• 定义:是通过坚硬的钻石颗粒对玻璃表面进行微
小的切削作用,对于来料之CG完品,切除其裂层, 且达至规定之表面粗糙度(外观E)和表面形状误 差(光圈NR)、以及规定之中心厚度(T)。
t
各工程特点:
• CG(粗加工)→砂挂第1支(半精加工)→砂
• 底座马达带动砂挂皿转动:
1000~3000Nmin,摆动马达带动治具内镜 片左右摆动、(或前后)、治具+镜片因摩 擦力产生之自身转动,加以压力使镜片被 砂挂皿切削,从而三者运动之复合即为球 芯运动,加工出镜片表面(或球形之一部 份)。(如下图)
串棒 前后移动
镜片
主轴转动
切削液
治具 钻石粒
砂挂皿
为1500#,型号为49B,则表示为:
•
⊥R15×28Φ×5T×49B×1500#
• 1 、砂挂工程一般分两段加工,第
一段使用金属基钻石粒,第二段使 用树脂基钻石粒.
• 2、根据镜片外径的大小来选 • 3、根据镜片的材质(磨耗度)来选
砂挂辅材介绍
• F121000#其切削力太强,不适合用来直接加工镜片因第
外观较光滑,易有线伤痕.主要用于磨耗度 160~210的材料
与R6相似,但自锐性稍差.
8TS*2000/1500
稍差
稍差
通用
主要用于磨耗度300以上的材料
TSO1420*1800
强
稍差
一般不使用
自锐性和研削能力较8TS稍好主要用于 磨耗度300以上,用8TS易打滑的材料
选用原则
• 1..S1不能发亮,要保持一定粗造度(蒙的)(用原器
串棒 摆弧
镜片
主轴转动
切削液
治具 钻石粒
砂挂皿
LR型
MF2、LF、SSP-4型
切削液
治具回转
治具 镜片 前后摆动
主轴
钻石粒 皿台
春近型
四、砂挂辅材介绍
•
1、切削液
• 功用:增强切削力,冷却,将切削粉和热量带走。
•
常用种类:
•
绿色切削液
•
KF-6A
•
福邦
•
786-2D
• 切削液浓度对加工镜片的影响:
研磨前的重要工序,加工出研磨工序所需要的 表面精细度。
• (1)、第一道工序称S1,用1200#~1500#的钻石
粒磨削镜片:属金属结合剂
• (2)、第二道工序称S2,用1500#~2000#的树脂
基进行抛光加工。 2、加工出研磨工序所需要的球面精度. 3、满足镜片中心肉厚要求,在规定的尺寸公差之
内 4、研削的质量好坏对研磨质量有极大的影响
• 树脂基 :SP27C*1000#→R10*1500#→ZR7K*1500#→ZR3S*1800#→
SP33A*1800#→ SP27C*2000# → ZR7K*2000#→ TR146A*1300 # → 18A*1500 # 。
•
• 钻石粒相关知识认知
• 表示方法: ⊥Rx----表示总形钻石,一面为⊥Rx,另一面为∞
钻石型号
自锐性
适用性
特性
503V*1500
强+
快+
成本高,一般不使用
主要针对用49B易 打滑,磨耗度 150以下材料
49B*1500 18B*1500 18A*1500
强 稍差 强
快 稍差 稍差
通用
主要用于磨耗度180 以下材料
一般不使用
主要用于磨耗度 180~200的材 料
通用
主要用于软材料
砂挂S2树脂的设定主要考虑1. 树脂自锐性﹒2.研削能力﹒3.S2完成品外观﹒
• 砂挂切削液:① 浓度过于浓则加工出来的镜片外观易蒙
•
②浓度过于淡则加工出来的镜片亮,无切
削力,砂目.
砂挂辅材介绍
二 钻石粒的选用:
• 钻石粒: • 切削力由强到弱排例: • 金属基:
F12*1000#→SP49B1000#→SP49B*1200#→a402*1500#→SP49B*1500# →a733*1500#→N4R*1500#→ZM21S*1300#→N24*1500#。