800mm电子铝箔轧机板形自动控制系统
阿亨巴赫铝箔轧机板形自动控制系统
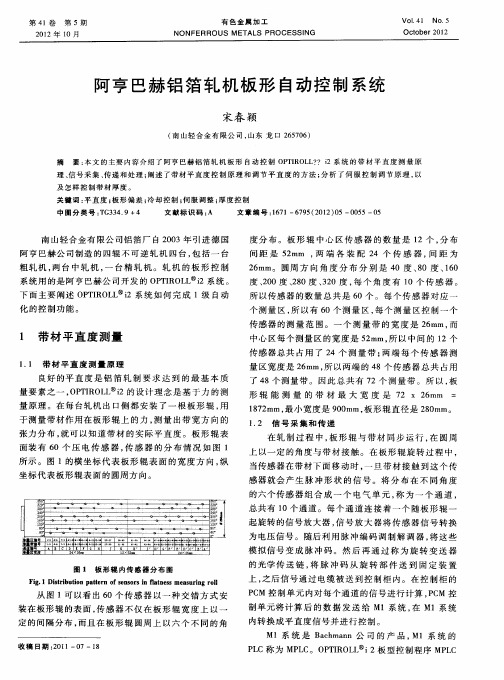
南 山轻 合金 有 限公 司铝箔 厂 自 2003年引 进德 国 阿 亨 巴赫 公 司 制 造 的 四 辊 不 可 逆 轧 机 四 台 ,包 括 一 台 粗轧 机 ,两 台 中轧 机 ,一 台精 轧 机 。 轧 机 的 板 形 控 制 系 统 用 的 是 阿 亨 巴 赫 公 司 开 发 的 OPTIROLL@i2系 统 。 下面 主要 阐述 OPTIROLL@i2系 统 如何 完成 1级 自动 化 的控 制 功能 。
收 稿 日期 :2011—07—18
度 分 布 。板 形 辊 中心 区传 感 器 的 数 量是 12个 ,分 布 间距 是 52r am ,两 端 各 装 配 24个 传 感 器 ,间 距 为 26mm。圆周 方 向 角 度 分 布 分 别 是 40度 、8O度 、160 度 、200度 、280度 、320度 ,每 个 角 度 有 10个 传 感 器 。 所 以传 感器 的数 量 总共 是 60个 。每个 传 感器 对 应 一 个 测量 区 ,所 以有 60个测 量 区 ,每个 测量 区控制 一 个 传感 器 的测 量 范 围。一 个 测 量 带 的宽 度 是 26r am,而 中心 区每个测 量 区 的宽 度是 52mm,所 以 中间 的 12个 传感 器 总共 占用 了 24个 测 量 带 ;两端 每个 传 感 器 测 量 区宽度 是 26r am,所 以两 端 的 48个 传 感 器 总共 占用 了 48个 测 量 带 。 因 此 总 共 有 72个 测 量 带 。所 以 ,板 形 辊 能 测 量 的 带 材 最 大 宽 度 是 72 X 26mm = 1872mm,最小 宽度是 900mm,板形 辊 直径是 280r am。 1.2 信 号 采 集 和 传 递
在轧 制 过 程 中 ,板 形 辊 与 带 材 同步 运 行 ,在 圆周 上 以一定 的角 度与 带材 接 触 。在 板 形辊 旋 转过 程 中 , 当传感 器在 带材 下 面移 动 时 ,一 旦 带 材接 触 到 这个 传 感 器 就会 产 生 脉 冲形 状 的信 号 。将 分 布 在 不 同角 度 的六个 传感 器 组 合 成 一 个 电气 单 元 ,称 为 一 个 通 道 , 总共有 10个 通道 。每 个 通 道连 接 着 一个 随板 形 辊 一 起 旋转 的信 号放 大器 ,信 号放 大 器 将传 感 器信 号转 换 为 电压 信号 。 随后 利 用 脉 冲编码 调 制 解 调器 ,将 这 些 模 拟信 号变 成 脉 冲码 。然 后 再 通 过称 为旋 转 变 送 器 的光 学 传 送 链 ,将 脉 冲 码 从 旋 转 部 件 送 到 固定 装 置 上 ,之后 信号 通过 电缆 被 送 到控 制 柜 内 。在控 制 柜 的 PCM 控制 单元 内对 每个通 道 的信号 进行计 算 ,PCM控 制单 元将 计算 后 的数 据 发 送 给 M1系 统 ,在 M1系统 内转 换成 平直 度信 号并进 行控 制 。
铝板带箔轧机板形控制系统动态过程控制异常处理方法探讨

铝板带箔轧机板形控制系统动态过程控制异常处理方法探讨作者:王修亮来源:《科学与财富》2015年第19期摘要:随着我国铝加工行业的转型升级,更加关注于铝加工产品的厚度控制精度和板形控制能力,在铝板带箔轧机控制领域引进了SIEMENS、ABB板形控制系统。
本文针对SIEMENS板形控制系统在动态过程控制中出现的一此问题进行了较为深入的研究和总结,希望对我们以后在使用和调试铝板带箔轧机板形控制系统时有所帮忙。
关键词:铝板带箔轧机、动态过程、板形控制一、铝板带箔轧机箔材动态轧制过程板形控制异常状态现象描述:某铝加工厂铝板带箔轧机引进了SIEMENS板形检测控制系统,采用的SIEMENS板形辊共26个压力检测环,某规格产品箔材覆盖SIEMENS板形辊第4#-23#环,在箔材动态轧制过程SIEMENS板型辊第15个压力环检测值明显偏大(I.U值偏大),SIEMENS板型辊第24#-26#压力检测环在轧制过程中检测压力明显异常(注:由于板型辊第24#-26#环辊面上没有受到铝板带箔压力的作用,正常状态时RAW值应3300左右)。
如图1所示:二、铝板带箔轧机箔材动态轧制过程板形控制异常状态处理过程:1、验证L1级AFC控制系统的有效性,按照AFC控制系统控制原理,当SIEMENS板形辊压力环检测压力大于设定目标值时,AFC控制系统应控制减小对应板形辊环域的冷却喷射量以使工作辊相应的环域热膨胀,对应环域的铝板箔材会有微量变薄的趋势,从而使铝板箔材板形I_Unit接近于目标值。
但这次板型辊第15个环压力环检测值明显偏大,板形已严重超出控制目标 I_Unit值,冷却喷射量已调整到极限为零,不能再进行调控,这种现象说明AFC控制系统的控制是正确的,只是当冷却喷射量调控到极限值后还是不能改善铝板带箔处于板形辊第15环的板形。
如图2所示2、验证板形控制系统冷却喷射控制的有效性,通过强制手动控制第1-26组冷却喷射阀,一一验证了1-26组冷却喷射阀控制的有效性。
轧机钢板厚度自动控制的液压系统设计

内容提要本设计是冷连轧机上使用的钢板厚度自动控制系统。
主要作用是对连扎机的压下量进行精确微小的调整,用来消除轧件和工艺方面的因素影响轧制力而造成的厚度偏差。
对于轧制钢板的厚度精度进行控制调整,确保成品钢板的精度控制在规定的范围内。
液压AGC是厚度自动控制的简称,液压AGC采用了液压执行元件(压下缸)的AGC,国内成为液压压下系统。
AGC是现在板带轧机的关键系统,其功能是不管板带偏差的各种扰动因素如何变化,都能自动调节压下缸的位置,即轧机的工作辊间隙,从而是出口板厚恒定,保证产品的目标厚度、同板差、异板差达到性能指标要求。
本设计是从研究冷连扎机的执行部件入手,借鉴原系统图的设计方案,针对实际情况,综合理论知识和实践经验,绘制了连扎液压厚度自动控制部分原理图。
系统图完成后,本人对伺服系统进行了设计计算,选择元件和管路计算。
最后完成机架部分的阀台和油箱泵站的有关设计。
本文从研究当前液压系统的国内现状和发展趋势入手,以节能减排,创新,绿色,可持续发展为起点,提出解决方案。
相信AGC技术将向着高频化、高响应、高稳定性和高精度方向发展。
高性能的伺服阀,比例伺服阀和高精度测量装置也将出现,这将会给液压技术带来新一轮的革命。
目录内容提要 (I)1 绪论 (1)1.1 概述 (1)2 系统原理设计 (3)2.1 系统原理 (3)2.2 伺服控制系统的原理及其组成 (3)2.3 伺服系统的设计步骤 (4)3 液压系统的计算及元件的选择 (5)3.1 液压缸基本参数的确定与计算 (5)3.2 伺服阀的选择 (7)3.3 泵与电机的选择 (8)3.4 联轴器的选择 (10)3.5 液压阀的选择 (10)3.6 液压辅件的计算与选择 (13)4 阀的设计 (21)4.1 液压泵站主泵阀块设计 (21)4.2 机架阀块设计 (21)5 油箱与泵站的设计 (22)5.1 油箱的设计 (22)5.2 泵站的设计 (25)结论 (29)参考文献 (30)致谢 (31)1 绪论1.1 概述1.1.1 课题国内背景:钢板的冷轧机作为一种生产工艺经过了多种演变,它由单机架非可逆单张轧制,发展到成卷可逆轧制,冷轧机由单击架逐步发展成三机架、四机架、五机架乃至六机架的连扎机,最后出现了全连续轧机。
铝板带箔轧机高精度自动断带检测识别控制系统的设计应用
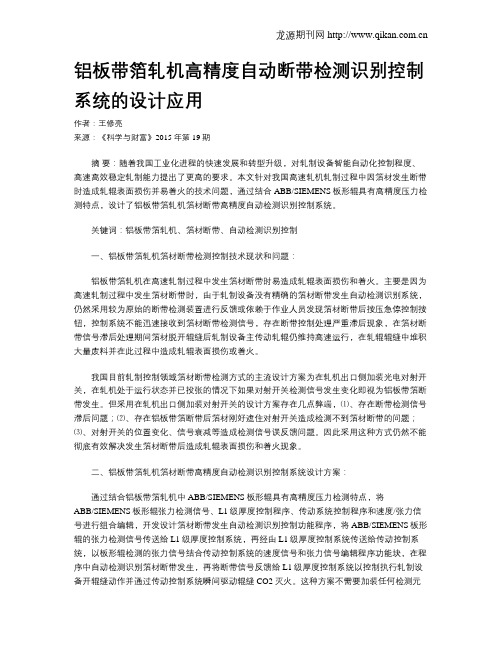
铝板带箔轧机高精度自动断带检测识别控制系统的设计应用作者:王修亮来源:《科学与财富》2015年第19期摘要:随着我国工业化进程的快速发展和转型升级,对轧制设备智能自动化控制程度、高速高效稳定轧制能力提出了更高的要求。
本文针对我国高速轧机轧制过程中因箔材发生断带时造成轧辊表面损伤并易着火的技术问题,通过结合ABB/SIEMENS板形辊具有高精度压力检测特点,设计了铝板带箔轧机箔材断带高精度自动检测识别控制系统。
关键词:铝板带箔轧机、箔材断带、自动检测识别控制一、铝板带箔轧机箔材断带检测控制技术现状和问题:铝板带箔轧机在高速轧制过程中发生箔材断带时易造成轧辊表面损伤和着火。
主要是因为高速轧制过程中发生箔材断带时,由于轧制设备没有精确的箔材断带发生自动检测识别系统,仍然采用较为原始的断带检测装置进行反馈或依赖于作业人员发现箔材断带后按压急停控制按钮,控制系统不能迅速接收到箔材断带检测信号,存在断带控制处理严重滞后现象,在箔材断带信号滞后处理期间箔材脱开辊缝后轧制设备主传动轧辊仍维持高速运行,在轧辊辊缝中堆积大量废料并在此过程中造成轧辊表面损伤或着火。
我国目前轧制控制领域箔材断带检测方式的主流设计方案为在轧机出口侧加装光电对射开关,在轧机处于运行状态并已投张的情况下如果对射开关检测信号发生变化即视为铝板带箔断带发生。
但采用在轧机出口侧加装对射开关的设计方案存在几点弊端,⑴、存在断带检测信号滞后问题;⑵、存在铝板带箔断带后箔材刚好遮住对射开关造成检测不到箔材断带的问题;⑶、对射开关的位置变化、信号衰减等造成检测信号误反馈问题。
因此采用这种方式仍然不能彻底有效解决发生箔材断带后造成轧辊表面损伤和着火现象。
二、铝板带箔轧机箔材断带高精度自动检测识别控制系统设计方案:通过结合铝板带箔轧机中ABB/SIEMENS板形辊具有高精度压力检测特点,将ABB/SIEMENS板形辊张力检测信号、L1级厚度控制程序、传动系统控制程序和速度/张力信号进行组合编辑,开发设计箔材断带发生自动检测识别控制功能程序,将ABB/SIEMENS板形辊的张力检测信号传送给L1级厚度控制系统,再经由L1级厚度控制系统传送给传动控制系统,以板形辊检测的张力信号结合传动控制系统的速度信号和张力信号编辑程序功能块,在程序中自动检测识别箔材断带发生,再将断带信号反馈给L1级厚度控制系统以控制执行轧制设备开辊缝动作并通过传动控制系统瞬间驱动辊缝CO2灭火。
铝箔轧机的AFC控制系统
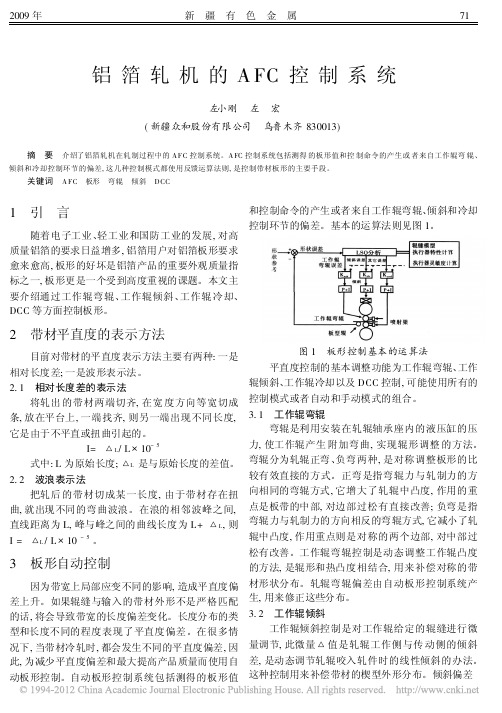
改变时, 快速改变工作辊弯辊来执行的。 3. 5 轧辊热凸度控制
在轧制过程中, 来自于板材塑性变形热、板材与 工作辊之间的摩擦热使工作辊发热。轧辊系统不均 匀热膨胀引起工作辊的热凸度。在特定的阶段采取 相应的弯辊、轧制油分段冷却来处理, 才能控制和弥 补热凸度带来的负面影响, 保证整卷板形的一致性, 获得良好板形。
( 上接 70 页)
整甲醇添加标准。经过一段时间的改造后, 冬季冻管 发生数量减少 73% 。
表 7 2007~ 2008 年冬季煤气冻管
日期
冻 管 环境温度 冻 管 最大冻管
( 根/月)
e
( 根/ d) ( 根/ d)
2007. 10. 1~ 30
45 + 5~ - 5 1. 5
15
2007. 11. 1~ 30
参考 文献
4 今后技术发展方向
随着八钢民用煤气管道使用年限的增加, 暴露的 问题也将逐渐增多, 笔者根据对内地大中城市居民用
112 5钢铁企业燃气设计参考资料6编写组. 钢铁企业燃气设 计参考资料. 冶金工业出版社, 1987.
122 钢铁企业煤气的生产与利用. 冶金工业出版社, 1987.
收稿: 2009- 03- 17
厚度自动控制系统
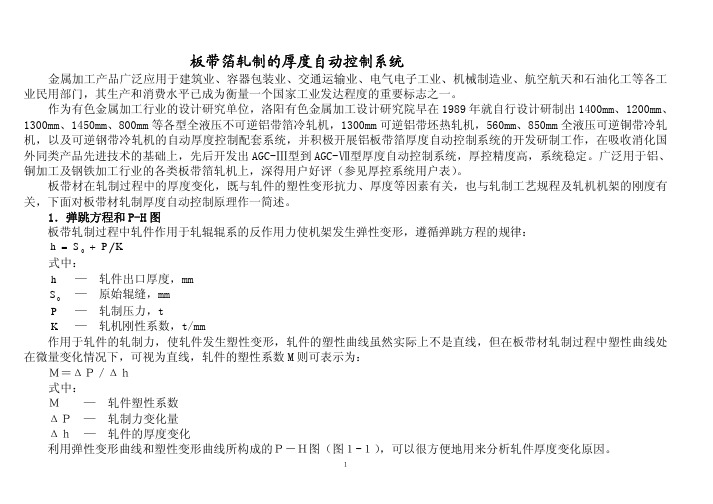
板带箔轧制的厚度自动控制系统金属加工产品广泛应用于建筑业、容器包装业、交通运输业、电气电子工业、机械制造业、航空航天和石油化工等各工业民用部门,其生产和消费水平已成为衡量一个国家工业发达程度的重要标志之一。
作为有色金属加工行业的设计研究单位,洛阳有色金属加工设计研究院早在1989年就自行设计研制出1400mm、1200mm、1300mm、1450mm、800mm 等各型全液压不可逆铝带箔冷轧机,1300mm 可逆铝带坯热轧机,560mm、850mm 全液压可逆铜带冷轧机,以及可逆钢带冷轧机的自动厚度控制配套系统,并积极开展铝板带箔厚度自动控制系统的开发研制工作,在吸收消化国外同类产品先进技术的基础上,先后开发出AGC-Ⅲ型到AGC-Ⅶ型厚度自动控制系统,厚控精度高,系统稳定。
广泛用于铝、铜加工及钢铁加工行业的各类板带箔轧机上,深得用户好评(参见厚控系统用户表)。
板带材在轧制过程中的厚度变化,既与轧件的塑性变形抗力、厚度等因素有关,也与轧制工艺规程及轧机机架的刚度有关,下面对板带材轧制厚度自动控制原理作一简述。
1.弹跳方程和P-H 图 板带轧制过程中轧件作用于轧辊辊系的反作用力使机架发生弹性变形,遵循弹跳方程的规律:K P S h 0+=式中:h — 轧件出口厚度,mm0S — 原始辊缝,mmP — 轧制压力,tK — 轧机刚性系数,t/mm作用于轧件的轧制力,使轧件发生塑性变形,轧件的塑性曲线虽然实际上不是直线,但在板带材轧制过程中塑性曲线处在微量变化情况下,可视为直线,轧件的塑性系数M 则可表示为:M=ΔP/Δh式中:M — 轧件塑性系数ΔP — 轧制力变化量Δh — 轧件的厚度变化利用弹性变形曲线和塑性变形曲线所构成的P-H图(图1-1),可以很方便地用来分析轧件厚度变化原因。
图1-1 弹性塑性变形的P-H图2.影响厚度变化的因素2.1 轧件的尺寸及性能的影响在其他条件不发生变化的情况下,轧件出口厚度的变化与其入口厚度的波动是成正比的,如图2-1所示,如果轧件入口厚度由0HH→,则会产生厚度波动h∆。
φ360×800mm铝箔粗轧机电气系统改造

3 操作控制系统 . 4 3 .开卷机控制系统 .1 2 操作控制 系统通过选用 P C L 实现操作 , 具 开卷机由两台磁粉制动器组成,并列联接 , 有过流 , 励磁保护功能,故障显示和报警功能。 主电路为单相全控桥整流电路,开卷张力由磁粉 4结束语 制动器磁场大 来控制 ,由张力公式 FIO D 小 =I.  ̄ V5 / 改造后取 消了原交流继电控制 系统 ,使系 q D知 ,只要磁通 随卷径 D正 比变化 , 张 统无级调速 , b / 则 速度提高且稳定,张力恒定,可靠 力恒定 。由于开卷机初始卷径大 , 逐步变小 ,因 性增强 , 产品质量有了大幅提高 ,同时增加了装 mn (0 -4 )mm /X 2 0- 0 5 此磁通的变化也应 从大变小,由工艺提出卷径变 机容量,能够生产超宽、超大规格的产品,大大 成品最大卷重 20g 5 k 化为 40 m 2m ,倍数为 60 8=.倍 ,磁通最大 拓宽了市场,开发了新产品 , 0/ 03 1 -3 加大了定货量 , 提 1 2主要 备参数 设 变化范围为 3 倍,初始励磁 电流 i,大小取决 高 了 . 3 0 经济效益,达到了改造的技术要求。 主传动直流电机功率 12w 3k ,电压 4 0 于卷径大小 ( 4V 最大为 8 ) A。 参 考文 献 电流 3 2 ,转速 6 0 m n 4A 0 # i; 联动时 ,随着线速 v和转速 N ,卷径 D参 [】陈伯 时. 1 自动控制 系统 [ 】. 】 北京: Ⅵ 机械工业 出 卷取直 流电机功率 2k ,电压 40 ,电 与调节 , 2w 4V 卷径 D的计算采用 A 5 3 D 3 集成除法器。 版社 随着 V / N表示的卷径变化 ,磁通也变化 , 施加磁 【 机械电子工业部, 2 1 天津电气传动设计研究所. 电 开卷机采用 2台9 W 2 V 2 / 磁粉制动器。 4 场调节器的信号为 A = 0D (O D D- D 初始卷径 , - - 对 气自 动化技术手册 f . 机械工业出 S 北京: 1 版社. 2改造技术要求 应 0 ,D为实测卷径) 。 系统能平 滑调速 ,且稳定,动稳态调节精 3. . 开卷机动态补偿问题 2 2 度差<o,调 节张力差<%,厚度公差< 50 / 5 厚度× 开卷机 动态补偿采用恒值 补偿方法 ,动态 ( 接 8 上 7页J 问题。 由于 Iv 数据包头的扩展 P6 5 能轧制成品最大宽度 50 m %, 2m ,具有保 护和 轴矩 M= D35d/= xv t j Z7xn tK d/。动态补偿电路 包头中提供 IS C G / d d P E 加密功能 ,因此主机可以进行 报警功能。 如图 3 。 端到端的加密, 以提供端到端的安全性。 对于提供 3轧机改造方案 虚拟专网服务的运营商来说 , 可以提供 IS C PE 数
浅谈轧机板形控制系统的组成及控制原理

电荷放大器将压电传感器生成的电荷信号转换为电压。 旋转变送器(PCM 变送器)将这些电荷放大器的输出信号 转换为(PCM 编码的)数字信号。数据通过电缆从旋转变 送器传递给安装在控制柜内的 PCM 解码器插架(PCM 已 经停产,现在基本都采用集成的 SIKO 模块代替 IOP 模块及 PCM 插架)。下图是 SIKO 模块实物图。
[1] 阿 亨 巴 赫 .OPTIROLL i2 SFC and SCA Training[CP/ K].2004[2021.5]. 设备厂家 .
Fti = 每个测量区铝箔张力 Fri= 每个传感器的径向力 HExit= 铝箔出口厚度
图 2 传感器受力模型
图 1 板形辊结构
收稿时间 :2021-05 作者简介 :郭明明,生于 1985 年,男,助理工程师,高级技师,研究方向 : 自动化控制、传动控制、设备管理。
铝箔两边张力 Fti 会产生一个向下的压力 Fri 即传感器的 径向压力。那压电传感器上会产生电荷脉冲。每个脉冲的强 度取决于轧制铝箔在铝箔横截面上的长度分布情况 , 铝箔精 确位置对覆盖少的传感器影响很大,以至于只有传感器覆盖 面积超过额定 50%,系统才可以使用测量。
M 冶金冶炼 etallurgical smelting
- 1、下载文档前请自行甄别文档内容的完整性,平台不提供额外的编辑、内容补充、找答案等附加服务。
- 2、"仅部分预览"的文档,不可在线预览部分如存在完整性等问题,可反馈申请退款(可完整预览的文档不适用该条件!)。
- 3、如文档侵犯您的权益,请联系客服反馈,我们会尽快为您处理(人工客服工作时间:9:00-18:30)。
800mm电子铝箔轧机板形自动控制系统(洛阳有色金属加工设计研究院黄利斌河南洛阳471039)摘要:本文介绍我院自主开发设计的800mm电子铝箔轧机板形自动控制系统的性能、组成及功能。
关键词:电子铝箔,板形仪,板形自动控制系统,分段冷却控制,板形目标曲线1.前言随着加工工业逐步采用高速自动作业线,特别是电子铝箔对板厚板形精度要求日益严格。
目前,板厚自动控制技术(AGC,Automatic Gauge Control)已日益成熟,厚度控制精度得到了解决。
而板形自动控制(AFC,Automatic Flatness Control),由于影响因素极其复杂,给板形控制带来很大困难,板形控制已成为国内外轧机界研究热点之一。
国外这几年也先后有多家公司和研究机构推出了不同种类的板形自动控制系统,实践生产效果不错,但由于价格非常昂贵,国内目前引进的很少。
1999年,我院成立新技术开发中心,把板形自动控制系统作为重点开发项目,通过近3年多努力终于取得成功,该系统借鉴了国外同类产品的先进经验、控制方法和模型,适用于冷轧铝薄带材板形自动控制的计算机自动控制系统。
2002年12月板形自动控制系统在由我院总包的新疆众和股份有限公司800mm电子铝箔轧机上成功运行,各项指标达到设计要求,控制精度接近国际水平,受到用户好评。
目前,应用于河南顺源铝业有限公司的1850mm铝箔轧机板形自动控制系统已安装就绪,进入最后的调试阶段。
本文仅对800mm电子铝箔轧机自动控制系统的性能、组成及功能作些介绍,以供读者参考。
2.轧机参数及控制精度新疆众和股份有限公司800mm电子铝箔轧机的主要参数如下:轧机形式:四辊不可逆铝箔冷轧机轧机尺寸:ф200mm/ф480mm ×800mm最大轧制力: 2600KN最大轧制速度:1200m/min来料宽度:420—640mm来料厚度: 0.6mm开卷张力:180—5700N卷取张力:80—4300N通过有关技术人员的共同努力,经过现场调试实验,在投入板形自动控制系统且正常稳定轧制条件下达到以下控制效果:厚度范围:0.32mm—0.017mm最大轧制速度:900m/min板形控制精度:0.1mm: ±15I0.065mm: ±20I3.系统组成图1是板形自动控制系统的框图。
AFC整套系统由检测部分、控制部分、执行部分组成。
检测部分选配了西安建筑科技大学生产的非接触激振测频式动态板形仪。
板形仪作为检测板形的传感器在整套系统中起着关键作用,它对板形的检测精度直接影响后续的控制精度。
如图所示,板形自动控制系统的核心是板形控制部分,它主要由板形信号处理单元,中央处理单元和过程信号I/O单元三部分组成。
分别完成板形信号的采集和处理、板形控制信号的计算、输出板形控制信号控制各执行机构等任务,形成闭环自动板形控制。
本地操作站和远程操作站主要用于人机操作界面,显示板形控制系统及过程状态信息。
在远程操作站上还可以根据用户需要打印所需要的数据、曲线等信息。
分别面向维修工程师和轧机操作手。
板形控制系统除输出轧辊倾斜控制信号、自动弯辊控制信号和自动冷却喷射控制信号之外,还提供有过程I/O接口,与轧机的其他控制系统(如轧机厚度自动控制系统、轧机传动系统等)进行信号联系,根据联系信号的状态进行控制及连锁,保证系统安全、可靠地完成其控制功能。
800mm电子铝箔轧机板形自动控制系统检测部分控制部分执行部分板形信号处理单元板形控制单元操作站单元 AGC 冷却系统MIC2000工控机 MIC2000工控机一体化工控机AI/AO AO CANDI/DO DOCAN CAN动态板形仪图14.AFC与外系统信号的联系4.1与AGC系统的联系1.来自AGC系统的信号⑴AGC系统就绪(触点信号,闭合有效,2A/30VDC)⑵总的倾斜量(传动侧位置-操作侧位置,模拟量信号±10V对应最大倾斜值)当AGC工作于压力环时,为传动侧压力-操作侧压力.2.去AGC系统的信号⑴倾斜控制误差(±10V<=>±2mm)⑵倾斜控制自动(触点信号,2A/30VDC)⑶AFC系统就绪4.2与传动系统的联系来自传动系统的信号⑴卷取张力(0—10V<=>0—最大张力)⑵带材速度(0—10V<=>0—最大速度)⑶张力范围(触点信号,2A/30VDC)⑷卷取张力建立(触点信号,2A/30VDC)4.3与弯辊系统的联系1.来自弯辊系统的信号⑴弯辊控制系统就绪(触点信号,闭合有效,2A/30VDC)⑵正弯压力(0—10V<=>0—最大正弯压力)(实测值)⑶负弯压力(0—-10V<=>0—最大负弯压力)(实测值)⑷弯辊参考(给定):±10V<=>±最大弯辊给定2.去弯辊系统的信号⑴弯辊控制误差(触点信号,闭合有效,2A/30VDC)⑵弯辊控制自动4.4与分段冷却控制系统的联系1.来自分段冷却控制系统的信号⑴分段冷却控制系统就绪(触点信号,闭合有效,2A/30VDC)⑵冷却液压力(0—10V<=>0—10bar)⑶冷却液打开(触点信号,2A/30VDC)2.去分段冷却控制系统的信号⑴冷却喷嘴的开/关控制信号(触点信号,共16路,2A/30VDC)⑵冷却控制自动(触点信号,2A/30VDC)4.5与板形检测系统的联系测量传感器个数: 7个;1.板形仪7个传感器的测量宽度间距77.5;77.5;83.0;83.0;77.5;77.5(1—7中心距476mm)可测板宽范围520mm;2.与AFC系统的数据交换方式:12位D/A板;3.信号分辨率:100/2048 (I/bit);4.信号范围:±100I;5.板形仪输出到AFC的板形信号的刷新频率:0.5秒;6.板形仪的测量精度:±5I。
5.硬件要求和软件环境本板形自动控制系统采用研华的MIC2000硬件系列。
控制部分的软件采用DOS加TURBO C++可使控制程序精炼、高效。
人机交互部分的软件采用微软公司的系统软件、开发软件(Windows2000系统平台配以Microsoft visual C++)可使人机界面简便易学、易操作。
5.1 硬件环境.采用研华公司的工业控制计算机(工业PC),具有性价比高,可靠性好、抗干扰能力强等优点。
.该系统采用模块化设计使硬件配置方便灵活。
.工控机和上位机工作站均为研华的产品,配套兼容性好。
.具有强大的通讯功能,可以通过专用的CAN总线将各部分连接在一起,构成CAN总线计算机控制网络,各部分之间的信息交换通过CAN总线实现。
.硬件包括:CPU型号MIC-2352,模入板MIC-2718,模出板MIC-2728,数字量输入板MIC-2730,数字量输出板MIC-2750,通讯板MIC-2630,PCL-841,软驱板MIC-2120等。
5.2 软件环境.上位机(操作台计算机): 操作系统Windows 9X/me/2000/NT, 支撑软件Microsoft visual C++6.0以上,上位机应用程序.下位机(控制计算机): 操作系统DOS6.22,下位机应用程序6.控制功能介绍由我院开发的板形自动控制系统,主要应用于冷轧带箔轧机上。
既可以接受来自接触式板形测量装置的板形误差信号,也可以接受来自非接触式板形测量装置的板形误差信号。
通过最小二乘算法,找到最佳的控制函数的组和,这些控制函数被用于控制弯辊、工作辊倾斜、分段冷却等执行机构,通过轧辊倾斜、工作辊弯曲及分段冷却等控制手段,对轧机出口侧带材板形进行控制,以此消除板形误差,使之达到操作手给定的目标板形。
800mm电子铝箔轧机检测部分选配了西安建筑科技大学生产的非接触激振测频式动态板形仪,板形自动控制系统的控制主要完成以下功能:.自动轧辊倾斜控制功能.自动轧辊弯曲控制功能.自动轧辊冷却控制功能.板形控制目标的生成与修正.矫正补偿功能.板形控制系统的操作与过程状态的显示图2AFC系统采用了图形化界面,所以操作比较简单.如上图2为板形系统主控画面,共分6个主要显示区:包括控制、参数设定、目标曲线选择、显示、系统功能等。
在此状态下操作手可根据需要对参数和控制方式进行设置,或者进入其他显示画面,如测量曲线、板形检查、板形分析(曲线比较、补偿分析)、冷却键盘。
图3图3用来显示AFC系统的模拟量输入信号的名称和数值和数字量输入信号的名称和状态(信号有效,绿色小灯亮;信号无效,绿色小灯灭)。
单击窗口左下角的退出键返回主控画面。
图4图4 窗口的左上部分用来显示板形误差曲线/给定目标曲线;左中部分用来显示冷却喷嘴控制状态;左下部分用来显示检查曲线/剩余误差/总补偿量(通过在窗口左底部分右面的下拉框选择,缺省选定为检查曲线);并可在窗口左底部分左面的下拉框选择显示左上、左下部分曲线的单位(I-unit或N/mm^2)。
在窗口右半边的倾斜控制区显示了倾斜控制的控制状态(自动/手动)及实际的误差量CE、输出控制量CO;弯辊控制区显示了弯辊控制的控制状态(自动/手动)及实际的误差量CE、输出控制量CO;冷却控制区显示了冷却控制的控制状态(自动/手动)及实际的冷却量;目标曲线区显示了当前目标曲线号/当前目标幅值/检查目标曲线号;轧制数据区显示了给定的带材卷号/带材宽度/带材出口厚度/带材刚度系数和实测轧制速度/张力的值以及AFC系统的控制状态(就绪/未就绪);单击窗口左下角的退出键返回主控画面。
图5图5显示了工作辊喷嘴的控制状态和模式,在喷液控制方式下,按如下操作:.自动模式点击后喷嘴系统及处于自动控制模式。
.设置将所有喷嘴设置为自动方式(前提:自动方式有效)。
.手动/自动将某喷嘴切换为手动/自动方式(自动方式键面为绿色)。
.ON/OFF 将手动控制某喷嘴的开/闭,开(ON)键面为绿色同时对应喷嘴的方灯变绿。
.手动模式点击后喷嘴系统及处于手动控制模式。
.全开将所有喷嘴设置为常开(前提:手动控制模式有效)。
.全开将所有喷嘴设置为常闭(前提:手动控制模式有效)。
.测试将测试所有喷嘴。
.退出将返回主控画面。
7.结束语我院板形自动控制系统在新疆众和股份有限公司800mm电子铝箔轧机上成功运用,标志着我院板形自动控制系统由前期的实验阶段走向了应用阶段。
板形自动控制系统是现代高速轧机必不可少的组成部分,实践证明板形的检测精度直接影响着板形的控制精度,我院轧机电气设计工程人员的新目标将是进一步改进和完善新近开发的板形自动控制系统,并配合机械工程人员开发研制板形测量辊,早日把我院板形自动控制系统大量的推向市场。