硫磺回收装置操作规程
硫回收岗位操作规程

硫回收岗位操作规程前言硫回收岗位是一项关键性的工作,必须严格按照操作规程进行操作,以确保生产顺利进行,并保障工作人员的安全。
本文将详细说明硫回收岗位的操作规程。
硫回收岗位操作规程工作要求1.按照工艺流程,完成硫回收装置日常运行和异常处理。
2.如有异常情况,立即报告主管,并进行必要的现场处理。
3.保证岗位设备设施完好,并进行定期维护与保养。
4.严格按照岗位操作规程进行操作,确保生产质量,并保障自身安全。
5.遵守公司各项管理制度,保密公司机密。
操作流程1.在确认工艺流程正常的情况下,按照操作指导书进行操作。
2.在进行操作前,必须检查设备状态,确保设备能够正常运行。
3.操作前,应穿戴齐全安全装备,如防毒面具、防酸防噪音耳塞等。
4.电气控制方面,应检查电气线路、接线端子的紧固状况,并查看电气设备的运行状态。
5.机械方面,应检查设备、管道连接是否紧固。
6.地面清洁,要求操作区域整洁干净。
7.在操作过程中,需要时刻关注设备运行情况,确保设备运行正常稳定。
8.在设备出现异常情况时,应第一时间停车处理并报告主管。
安全防范1.严格执行操作规程,避免操作事故发生。
2.操作前,必须进行安全检查,确保设备运行正常。
3.在操作时,需要时刻检查设备状态,防止设备故障引发事故。
4.不得擅自进行设别改动,如需进行维护,应由设备维修人员进行操作。
5.操作过程中,必须戴上个人防护装备,切勿接触酸液。
6.在操作过程中,保持精神集中,防止疲劳驾驶引发事故。
7.紧急情况发生时,应立即停车并报告主管。
结语硫回收岗位的操作规程是岗位人员必须遵守的,只有严格按照操作规程进行操作,才能保障生产安全,并保障自身安全。
工艺生产到底,需要岗位人员严格按照操作规程进行操作,保证每一个细节的合理实施。
4千吨硫磺回收装置操作规程2014
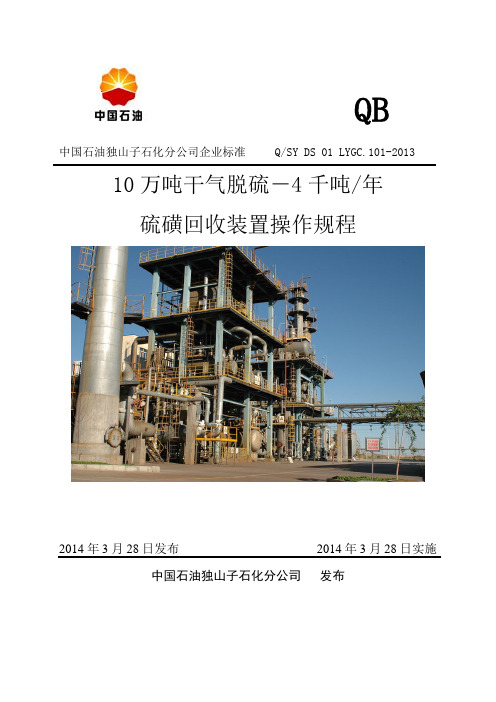
QB中国石油独山子石化分公司企业标准Q/SY DS 01 LYGC.101-2013 10万吨干气脱硫-4千吨/年硫磺回收装置操作规程2014年3月28日发布2014年3月28日实施中国石油独山子石化分公司发布生产装置操作规程审批表会签单位(人员)签字日期编制人2014年1月3日车间(站队)领导2014年1月5日直属单位技术部门2014年1月6日机动部门2014年1月6日调度部门2014年1月6日安全质量环保部门2014年1月7日分厂主管领导2014年1月15日公司科技信息处2014年1月16日公司生产运行处2014年1月16日公司机动设备处2014年1月16日公司安质环处2014年1月22日公司主管领导2014年3月27日版本Q/SY DS 01 LYGC.101-2013本标准参加编写人员车间主任审核:吕小军版本更新记录前言本规程是在Q/SY DS 01 JS JSH.078-2008版本的基础上,结合Q/SY DS 01 JS JSH.078-2011火炬单行本,根据近几年装置改造内容,重新对两本操作规程进行整合、换版修订。
本规程修订目的主要是对2008版操作规程的具体内容,根据近几年技措改造的内容进行修订,使之更适应实际操作。
对于装置开、停工规程,各种单体设备的操作规程、操作指南和事故处理预案按照程序文件要求进行编写。
对整个操作规程结构内容进行融合调整,使之成为联系紧密并协调的规程。
使原规程的内容更加全面,更完善,更接近实际生产,以便于操作人员能按此规程进行生产操作,并作为员工培训使用教材。
本规程执行中油独山子石化公司企业标准。
本规程实施后取代原硫磺回收装置操作规程2008版操作规程。
本规程由炼油厂技术处归口管理。
本规程起草单位:硫磺回收车间。
本规程于2013年10月第三次编写。
本规程主要编制人员:裴古堂、张卫成、郭为纲、叶全旺、李保廷、薛金贤、许显坤车间审核人:吕小军目录第一章工艺技术规程 (1)1.1装置概况 (1)1.1.1 硫磺回收装置简介 (1)1.1.2 一火炬简介 (3)1.1.3 工艺原理 (4)1.1.3 工艺流程说明 (6)1.1.4 原则流程图 (9)1.2工艺指标 (10)1.2.1 原料指标 (10)1.2.2 半成品、成品指标 (11)1.2.3 公用工程指标 (12)1.2.4 主要操作条件 (12)第二章操作指南 (15)一、岗位操作规定 (15)2.1 脱硫岗位操作原则 (15)2.2制硫岗位操作原则 (16)2.3 尾气加氢系统操作原则 (16)2.4 火炬岗位操作原则 (17)二、岗位操作指南 (18)2.1 脱硫岗位 (18)2.1.1干气脱硫塔C-101贫液进料量FIC-104 (风关阀) (18)2.1.2干气脱硫塔C-101液面LIC-101 (风开阀) (20)2.1.3 富液闪蒸罐V-102顶压力PIC-107 (风关阀) (22)2.1.4胺液储罐V-104/胺液储罐V-104B液面LI-105/LI-105B (24)2.1.5 再生塔C-102底温度TIC-114 (风开阀) (26)2.1.6 再生塔C-102底温度TIC-114B(风开阀) (28)2.1.7 再生塔回流罐V-103液位LIC-109-FIC-112(风关阀) (30)2.1.8 凝结水泵小流量保护控制阀FIC-011 (风关阀) (32)2.1.9 减温减压器(ME-101)操作 (33)2.2 制硫岗位 (35)2.2.1 一级硫冷器E-201管程出口温度TI-209 (35)2.2.2 二级硫冷器E-202管程出口温度TI-216 (140~190℃) (37)2.2.3 三级硫冷器E-203管程出口温度TI-217 (39)2.2.4 一级转化器R-201入口温度TI-219 (41)2.2.6 液硫捕集器V-209出口H2S/SO2比值 (45)2.2.7 酸性气焚烧炉F-203炉膛温度TIC-218 (风开阀) (47)2.2.8 酸性气燃烧炉F-201炉膛温度TIC-201 (49)2.2.9 汽包V-203操作 (51)2.2.10 加氢反应器R-301入口温度TIC-316(210~260℃) (53)2.2.11 尾气焚烧炉F-301操作 (55)2.2.12 急冷塔C-301操作 (57)2.2.13 尾气吸收塔C-302操作 (59)2.4火炬岗位 (60)2.4.1水封罐R-5/1水封控制 (60)第三章开工规程 (61)3.1开工统筹图 (63)3.2开工纲要(A级) (64)3.3开工操作(B级) (68)3.4开工说明(C级) (113)第四章停工规程 (116)4.1 停工统筹图 (116)4.2 停工纲要(A级) (117)4.3 停工操作(B级) (121)4.4 停工说明(C级) (153)第五章专用设备操作规程 (158)5.1尖嘴式造粒机开、停操作 (158)5.1.1尖嘴式造粒机工艺指标 (158)5.1.2 尖嘴式造粒机开机操作 (158)5.1.3 尖嘴式造粒机停机操作 (160)5.1.4开机辅助说明 (161)5.1.5 造粒机的日常检查和维护 (161)5.1.6常见问题现象及处理方法 (161)5.2离心式鼓风机操作 (162)5.2.1离心式鼓风机工艺指标 (162)5.2.2离心式鼓风机开机操作 (163)5.2.3离心式鼓风机停机操作 (175)5.2.4离心式鼓风机切换至罗茨风机操作 (178)5.3 包装秤、缝包机、输送机、折边机倒袋斜坡输送机操作 (179)5.3.1包装秤、缝包机、输送机、折边机倒袋斜坡输送机开机操作 (179)5.3.2包装秤、缝包机、输送机、折边机倒袋斜坡输送机停机操作 (181)5.4罗茨鼓风机操作 (183)5.4.1罗茨鼓风机工艺指标 (183)5.4.2罗茨鼓风机开机操作 (183)5.4.3罗茨鼓风机停机操作 (186)5.4.4罗茨鼓风机切换至离心风机操作 (188)第六章基础操作规程 (189)6.1 机泵的开、停与切换操作 (189)6.1.1 离心泵的开、停与切换操作 (189)6.1.2 磁力泵的开、停与切换操作 (230)6.2加热炉的开停与操作 (241)6.3硫磺回收装置安全阀前、后手阀操作规程 (279)6.4关键部位取样操作程序及注意事项 (281)6.4.1贫液取样操作 (281)6.4.2干气脱硫塔C-101富液取样操作 (283)6.4.3酸性气取样操作 (285)6.4.4干气脱硫塔C-101净化干气取样操作 (287)6.4.5过程气取样操作 (289)6.4.6烟气取样操作 (291)6.5 催化剂装填方案 (293)6.5.1制硫转化器R-201/202催化剂装卸方案 (293)6.5.2 加氢反应器R-301催化剂装卸方案 (299)第七章事故处理规程 (304)7.1事故处理原则 (304)7.2紧急停工方法 (305)7.3事故处理预案 (313)7.3.1 硫磺回收装置停电事故应急操作 (313)7.3.2 硫磺回收装置停风事故应急操作 (320)7.3.3 硫磺回收装置停蒸汽事故应急操作 (325)7.3.4 硫磺回收装置停除盐水事故应急操作 (328)7.3.5 硫磺回收装置停新水事故应急操作 (330)7.3.6 硫磺回收装置停循环水事故应急操作 (332)7.3.7 硫磺回收装置风机J-201B鼓风机故障停机事故应急操作 (335)7.3.8 硫磺库房着火事故应急操作 (339)7.3.9 硫磺回收装置造粒机房火灾事故应急操作 (342)7.3.10 硫磺回收装置酸性气分液罐V-201至酸性气燃烧炉F-201管线泄漏事故应急操作.. 3457.3.11 硫磺回收装置酸性气去酸性气焚烧炉F-203管线硫化氢泄漏事故应急操作 (350)7.3.12 硫磺回收装置内酸性气分液罐V-103硫化氢泄漏事故应急操作 (353)7.3.13 硫磺回收装置内氢气线泄漏事故应急操作 (356)7.3.14 硫磺回收装置内催化干气线泄漏事故应急操作 (358)7.3.15 硫磺回收装置DCS故障事故应急操作 (360)7.3.16 硫磺回收装置内净化干气线泄漏事故应急操作 (366)7.3.17 硫磺回收装置内氮气线泄漏事故应急操作 (369)7.3.18 硫磺回收装置去新区高压瓦斯线泄漏事故应急操作 (374)7.3.19 硫磺回收装置去新区二联合富液线泄漏事故应急操作 (377)7.3.20 硫磺回收装置溶剂泵房着火事故应急操作 (379)7.3.21 硫磺回收装置Ⅰ火炬筒体冻凝事故应急操作 (381)7.3.22 废热锅炉F-202干锅事故应急操作 (383)7.3.23 自保阀故障应急操作 (387)7.3.24 尾气焚烧炉F-301异常熄火应急操作 (391)7.3.25 酸性气焚烧炉F-203异常熄火应急操作 (395)7.3.26 洪灾事件应急处置程序 (398)7.3.27地震灾害应急处置程序 (398)7.3.28放射(辐射)性污染事故应急处置程序 (398)7.3.29建筑物逃生应急处置程序 (399)7.3.30沙尘暴天气应急处置程序 (399)7.3.31暴风雪天气应急处置程序 (399)7.4 事故处理预案演练规定 (401)第八章操作规定 (403)8.1 定期工作规定 (403)8.2 长期操作规定 (404)第九章仪表控制系统操作法 (406)9.1 DCS系统概况 (406)9.2 主要工艺操作仪表逻辑控制说明及工艺控制流程图(DCS画面简图) (407)9.2.1 I/A仪表常用键的作用 (440)9.2.2 I/A仪表的一般使用要求 (440)9.2.3 锁机情况下的处理 (441)9.2.4 仪表的启运、投用 (441)9.2.5 I/A仪表的停运 (441)9.2.6 注意事项 (442)9.2.7 报警器及远传仪表 (442)9.3 装置自保的逻辑控制规程 (464)9.3.1装置自保的逻辑控制图 (464)9.3.2 装置自保的逻辑控制说明 (469)第十章安全生产及环境保护 (480)10.1 安全知识 (480)10.1.1 安全生产基本原则 (480)10.1.2 装置危险有害因素分布 (480)10.1.3中国石油天然气集团公司反违章六条禁令 (482)10.1.4中国石油天然气集团公司健康安全环境( HSE )管理原则 (483)10.1.5 公司十大禁令 (485)10.1.6 人身安全十大禁令 (485)10.1.7 防火防爆十大禁令 (485)10.1.8 防止静电危害十条规定 (486)10.1.9 防止中毒窒息十条规定 (486)10.1.10 防止硫化氢中毒十条规定 (487)10.1.11 防硫化氢中毒常识 (488)10.1.12 石油类火灾事故防护知识 (489)10.1.13 中毒现场抢救知识 (491)10.1.14 防护用具的使用 (492)10.1.15 触电救护知识 (496)10.1.16 烧伤救护知识 (497)10.1.17 人工呼吸与心脏复苏的操作方法 (497)10.1.18 创伤急救知识 (498)10.1.19 骨折急救知识 (499)10.1.20 颅脑外伤 (499)10.1.21 烧伤、烫伤急救知识 (500)10.1.22 冻伤、高温中暑急救知识 (500)10.2 安全规定 (501)10.2.1 装置区安全管理规定 (501)10.2.2 防止硫化氢中毒安全管理规定 (501)10.2.3 防火防爆安全管理规定 (502)10.2.4 进入有限空间安全管理规定 (503)10.2.5 成型造粒机安全管理规定 (503)10.2.6 叉车安全管理规定 (503)10.2.7 取样作业安全管理规定 (504)10.2.8 机泵安全管理规定 (504)10.2.9 焚烧炉安全管理规定 (504)10.2.10 容器脱液安全操作规程 (505)10.2.11 其它安全管理规定 (505)10.2.12 装置开工安全规定 (506)10.2.13 装置停工检修安全规定 (507)10.3 装置防冻、防凝措施 (508)10.4 本装置历史上发生的主要事故、处理方法及经验教训 (509)10.5 装置主要有毒物质性质 (509)10.6 装置主要有害物介质的有关参数 (509)10.6.1石油裂解气 (509)10.6.2 硫化氢 (511)10.6.3 氢气 (514)10.6.4 氮气 (516)10.6.5 硫磺 (519)10.6.6 柴油 (521)10.7化工三剂使用操作规程 (523)10.8废水排放及控制 (532)10.9 废气排放及控制 (532)10.10 废渣排放及控制 (533)10.11 噪声排放及控制 (534)10.12 环保设施及其他 (534)第十一章附录 (536)11.1设备明细表 (536)11.1.1 设备类 (536)11.1.2 仪表位号对照表 (546)11.1.3机泵润滑油(脂)规格、型号对照表 (548)11.2 主要设备结构图 (550)11.3装置平面布置图 (575)11.4可燃气体和硫化氢报警仪布置图 (577)11.5装置消防设施布置图 (580)11.6装置硫化氢分布图 (583)11.7 装置风险提示平面图 (584)11.8 装置工业视频监控分布图 (585)11.9 安全阀定压值 (586)11.10 控制参数报警值 (588)11.11取样点一览表 (590)11.12 统筹图 (591)11.13 附图 (597)第一章工艺技术规程1.1装置概况1.1.1 硫磺回收装置简介硫磺回收装置于2002年12月建成,设计处理炼厂干气10万吨/年,同时生产硫磺3000吨/年,属联合装置。
硫磺回收装置操作规程

硫磺回收装置操作规程硫磺回收装置操作规程⼀.介质特性硫化氢(H2S)相对密度1.189(⽓体),爆炸极限4.3-46%,⾃燃点;260°C, H2S 在空⽓中最⾼允许浓度10mg/m3,毒性。
强烈神经毒物对粘膜有明显刺激作⽤,浓度越⾼全⾝作⽤明显表现为中枢神精系统症状和窒息症状。
H2S是⼀种恶臭性很⼤的⽆⾊⽓体,H2S浓度达到是⼀定时会引起⽕灾爆炸。
硫磺熔点为119°C,沸点444.6°C饱和蒸汽压:0.13kpa,临界温度;1040°C,淡黄⾊不溶于⽔,燃烧时⽕焰温度1800°C.爆炸下限35mg/m3,引燃温度;232°C最⼤爆炸压⼒0.415mpa,遇⾼温及明⽕能引起燃烧。
⼆.开⼯规程开⼯检查1.系统试压⽓密合格,酸性⽓管道系统各点均⽆泄露。
2.管道上所有阀门仪表检查是否灵活启闭,仪表是否能正常⼯作。
3.⽔、电、⽓、风、燃料⽓正常4.废热锅炉及三级冷凝器是否正常在液位。
5.dcs是否显⽰⼯作正常。
6.风机试起,压⼒是否正常在45-55kpa。
7.酸性⽓引⾄炉前,压⼒是否在0.04-0.06mpa。
8.压缩空⽓备压引⾄启动球阀前0.4-0.6mpa。
9. 催化剂装剂⾼度在850-900mm,上部瓷球50mm下部瓷球100mm。
三.开⼯准备1.准备开⼯器具硫化氢报警仪消防设施完好备⽤:消防栓、灭⽕器。
安全防护⽤具齐全:隔热板、空⽓呼吸器、过滤器式防毒⾯具、便携式硫化氢报警仪、对讲机等。
2.打开风机吹扫炉膛。
同时给蒸汽煮炉,煮炉蒸汽压⼒为0.3-0.45mpa,(之前打开冷凝器及其三级冷凝器煮炉放空阀(开⾄1/3),关闭蒸汽出⼝阀门,然后开启两炉底部煮炉阀门。
)并打开蒸汽出⼝所有阀门(冷凝器及其三级冷凝器除外)。
进⾏预热管道及其冷凝器。
时炉内压⼒保持在0.3mpa左右。
伴热时间30分钟左右关闭蒸汽煮炉管道阀门,及其放空阀。
3.伴热关闭后引⽡斯⽓升温,调整配风量。
30kt硫磺装置操作规程.

30kt/a硫磺回收装置操作规程1.范围本标准主要叙述了硫磺回收装置的原理、流程、开停工、事故处理、单体设备操作方法及安全规程。
本标准适用于本企业30kt/a硫磺回收装置。
2.规范性引用文件Q/JSH G1102·01—2003《工艺技术操作规程管理标准》。
3.装置概况3.1装置组成该装置包括硫磺回收、尾气处理和溶剂再生三部分。
3.2设计处理量3.2.1硫磺回收部分规模为年回收硫磺30kt/a3.2.2溶剂再生部分规模为50t/h3.3工艺概况制硫部分采用克劳斯部分燃烧法处理酸性气生产硫磺,此法是将全部原料气引入制硫燃烧炉,在炉中按制硫所需的O2量严格控制配风比, 使H2S在炉中约65%发生高温反应生成气态硫磺。
未反应的H2S和SO2 再经过转化器,在催化剂的作用下,进一步完成制硫过程。
对于含有NH3和少量烃类的原料气用该法可将NH3 和烃类完全分解为N2、CO2 和H2O,使产品硫磺的质量得到保证。
从硫磺回收部分排出的制硫尾气,仍含有少量的H2S、SO2、COS、Sx 等物质,直接焚烧后排放达不到国家规定的环保要求。
为此,制硫部分的尾气需要继续进行尾气处理。
制硫尾气经过加氢还原吸收,将硫回收尾气中的元素S、SO2、COS和CS2 等,在很小的氢分压和极低的操作压力下(约0.02~0.03MPa),用特殊的尾气处理专用加氢催化剂,将其还原或水解为H2S,再用醇胺溶液吸收,吸收了H2S 的富液经再生处理,富含H2S 的气体返回上游硫回收部分,经吸收处理后的净化气中的总硫<500mg/m3。
溶剂再生部分采用成熟、可靠的热再生技术。
3.4装置特点1)硫磺回收装置是一个环保装置,它的社会效益远大于它的经济效益,装置安全、平稳、长周期运行才能使装置主要污染物的排放量和排放浓度(尤其是对硫、二氧化硫和其它含硫化合物)符合国家环保排放标准。
硫磺回收装置工艺技术比较复杂,介质易燃、易爆,并有腐蚀和毒性,操作不安全因素较多,因此自动控制系统必须具有高可靠性和高安全性。
硫磺回收装置操作规程
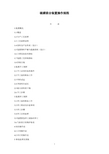
硫磺联合装置操作规程目录1.装置概况1.1概述1.2生产工艺原理1.3工艺流程说明1.4原料及产品性质(设计)1.5装置物料平衡与能量消耗(设计)1.6主要设备技术指标1.7装置工艺控制指标1.8控制方案2.装置开工规程2.1开工必须具备的条件2.2开工前的准备工作2.3单机试运2.4全面吹扫试压2.5耐火材料的干燥2.6开工步聚3.装置停工规程3.1停工前的准备工作3.2停工要求及注意事项3.3停工步骤3.4停工后的处理3.5装置紧急停工或临时停工3.6气柜的日常维护检查4岗位操作法4.1正常操作法4.2非正常操作法5事故处理及预案5.1应急救援指挥系统5.2指挥部成员的职责5.3报警办法5.4事故处理通则5.5DCS内操室硫磺联合装置常用开关自保开关(旋钮)5.6事故预案6安全生产规定6.1日常生产安全规定6.2开、停工安全规定6.3装置检修安全规定6.4防火防爆安全规定6.5防冻防凝安全规定6.6防止硫化氢中毒规定7直接作业环节作业项目HSE控制程序7.1阻火器拆装清理7.2罐气柜脱油、脱水操作程序7.3机泵检修操作程序7.4压力表、温度计更换程序7.5扫线7.6装置伴热投停程序7.7安全阀拆卸、安装程序7.8DN50以下阀门更换或法兰换垫7.9采样控制程序8附录8.1安全阀规格表8.2设备汇总表8.3装置平面图8.4装置原则流程8.5装置工艺自控流程1.硫磺联合装置概况1.1概述硫磺车间共有五套装置,即60t/h污水汽提装置、200t/h溶剂再生装置、10000t/a硫磺回收装置、5000t/a 硫磺回收装置、低压瓦斯回收装置。
该装置采用单塔常压汽提工艺处理酸性水,硫化氢和氨同时被汽提,酸性气为硫化氢和氨混合气。
原料酸性水经脱气除油后进入汽提塔上部。
塔底用1.0MPa蒸汽加热汽提,酸性水中硫化氢、氨被汽提,自塔顶经冷凝分液后酸性气送至硫磺回收部分,塔底得到合格净化水,净化水可作为催化、常压等生产装置注水回用。
硫磺车间操作规程

温度 (℃)
蒸汽压 (毫米汞柱)
温度 (℃)
蒸汽压 (毫米汞柱)
49.7
0.00034
242
8.4
78
0.002
245
10.0
104
0.01
265
20.0
131.9
0.081
306.5
53.5
135
0.10
342
106
141
0.13
363
176
157
0.33
374
240
172
0.63
393
436
181
第二篇 酸水汽提装置操作规程
17. 装置概况…………………………………………………………………………………… 51 18. 产品及副产品说明………………………………………………………………………… 51 19. 原料、公用工程系统……………………………………………………………………… 52 20. 动力消耗定额……………………………………………………………………………… 53
2. 产品及副产品说明………………………………………………………………………… 1
3. 原料、化学品、公用工程名称及规格…………………………………………………… 3 4. 原料、燃料及动力消耗定额……………………………………………………………… 5 5. 生产方法及工艺原理、物料平衡………………………………………………………… 6 6. 装置副产品及“三废”的应用与处理…………………………………………………… 8 7. 工艺流程简述……………………………………………………………………………… 8 8. 主要操作条件及技术指标………………………………………………………………… 9 9. 装置的开、停工…………………………………………………………………………… 11 10.0.1 万吨硫磺回收装置开停工方案……………………………………………………… 15 11.0.4 万吨硫磺回收装置及尾气处理系统开停工方案…………………………………… 21 12.0.1 万吨硫磺装置岗位操作法…………………………………………………………… 31 13. 事故处理…………………………………………………………………………………… 34 14.0.4 万吨硫磺装置及尾气处理系统岗位操作法………………………………………… 36 15. 主要工艺调节参数的计算公式…………………………………………………………… 45 16. 硫磺回收安全技术规程…………………………………………………………………… 46
硫磺回收装置操作手册A
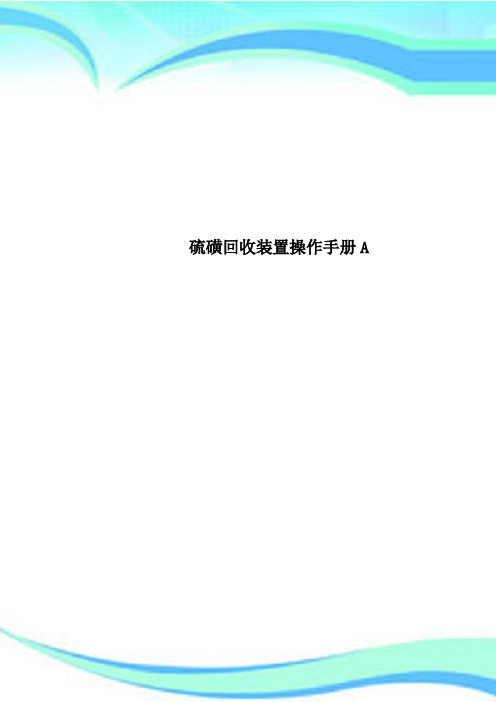
硫磺回收装置操作手册A————————————————————————————————作者: ————————————————————————————————日期:8万吨/年硫磺回收装置工艺手册目录1 前言2 概述2.1 装置组成2.2 设计基础2.3 设备3工艺流程3.1 硫回收部分工艺说明3.2 尾气处理部分工艺说明3.3 胺液再生部分工艺说明3.4 液硫脱气及液硫成型部分工艺说明4 工艺原理及操作条件4.1工艺原理4.2主要操作条件5 装置开工前的准备5.1 系统及设备检查5.2 单机试运行5.3系统清扫5.4 煮炉操作5.5 烘炉和烘器5.6 催化剂装填5.7 水联运5.8 系统吹扫和系统气密6装置开车操作程序6.1系统升温6.2硫回收部分开车6.3尾气净化系统的生产准备6.4尾气加氢催化剂预硫化6.5装置的正常运行7装置停车操作程序7.1装置停工操作7.2制硫部分系统吹扫7.3尾气处理系统吹扫和尾气加氢催化剂钝化7.4急冷水系统和胺液系统的处理8 装置故障停工操作8.1急冷水系统和胺液系统的处理8.2 故障停工操作9 长期停工的维护10安全、环保、健康技术规定1 前言本工艺手册仅适用于海南炼化续建项目8万吨/年硫磺回收装置。
本工艺手册提供了硫磺回收装置总的操作指南。
在本装置工作的所有操作人员和维护人员都要经过良好的培训和熟悉所有的设备,并能熟练地操作和维护、维修。
在装置的实际运行过程中,对于可能出现的各种问题和情况,工艺手册不可能全部预见到并包括进去。
由于原料性质是变化的,操作条件可能相应变化,因此,工艺手册中叙述的所有条款,都要经过试运行和装置实际操作经验加以修正,才能适应生产情况的变化。
2 概述2.1装置组成硫磺回收装置由制硫、尾气处理、液硫脱气、尾气焚烧及液硫成型五部分组成。
2.2设计基础2.2.1装置能力装置能力:硫化氢富气的流量大约为9900Nm3/h;硫磺产量约为79200吨/年。
克劳斯硫回收操作规

克劳斯硫回收操作规程1. 岗位任务及意义我厂所采用的原料煤硫含量较高, 如果不加以回收,就会污染空气。
本岗位接受低温甲醇洗岗位送来的硫化氢尾气, 通过克劳斯回收装置回收,并制成固体硫磺。
本装置H2S的总转化率90-95 %; COS不发生克劳斯反应,通过尾气烟囱直接放空。
年产硫磺1 万吨,回收硫磺不仅经济效益可观还可以消除污染。
2. 工艺原理及流程叙述2.1工艺原理克劳斯法回收硫的基本反应如下:H2S+ 1/2Q—S+ H2O (1)H2S+ 3/ 2Q2—SQ+ H2Q (2)2H2S + SQ—3S+ 2H2Q (3)反应(1)(2)在燃烧室中进行,在温度1150C— 1300C,压力0.06MPa 和严格控制气量的条件下,将硫化氢燃烧成二氧化硫,为催化反应提供(H2S+ CS)/SQ为2/1的混合气体。
此气体通过ALQ基触媒,按反应(3)生成单质硫。
2.2流程叙述来自上游甲醇洗工序的酸性气温度为37.2 C,压力为0.22MPaG经进料管分离罐(V1301)分出挟带液后,按一定比例分成两股,其中一股去HtS 燃烧炉(F1301)。
该流股经过控制阀后压力降为0.06 MPaG 进入HS燃烧炉(F1301),在H2S燃烧炉(F1301 )中,酸性气和一定比例的反应空气发生燃烧反应,反应生成SO2 的和燃烧反应剩余的H2S进一步发生部分克劳斯反应,反应后的酸性气体温度可达800C以上。
高温酸性气随后进入H2S余热回收器(E1301)回收器废热并副产蒸汽,同时将反应生成的单质硫部分冷凝。
HS余热回收器(E1301)—共有四程换热管(PASS什4)回收本工序工艺气的废热,高温酸性气废热的回收是通过其中的第一、二换热管(PASS、PASS2进行的。
高温酸性气全部通过PASS1后温度降为600C,然后分成两股,其中一股流经PASS2温度进一步降至185C,然后和未经过PASS2勺流股混和。
通过调整两个流股的比例可使混合后的温度控制在约300 C o混合后的酸性气流股和进料器分离罐(V1301 )后未进入H2S燃烧炉(F1301)的旁路酸性气体混合后温度降至230C、压力0.04MPaG进入克劳斯反应器(R1301)—段。
- 1、下载文档前请自行甄别文档内容的完整性,平台不提供额外的编辑、内容补充、找答案等附加服务。
- 2、"仅部分预览"的文档,不可在线预览部分如存在完整性等问题,可反馈申请退款(可完整预览的文档不适用该条件!)。
- 3、如文档侵犯您的权益,请联系客服反馈,我们会尽快为您处理(人工客服工作时间:9:00-18:30)。
山东天宏新能源化工有限公司10000T/a硫磺回收装置操作规程目录第一章概述-------------------------------------------------(1)第二章工艺原理及流程----------------------------------(2)第一节工艺原理-------------------------------------------(2)第二节工艺流程叙述--------------------------------------(3)第三节主要控制方案--------------------------------------(4)第四节工艺指标--------------------------------------------(5)第五节主要生产控制分析---------------------------------(10)第六节岗位管辖范围与岗位任务综述------------------(10)第三章设备与仪表明细表-----------------------------------(11)第四章装置的开工--------------------------------------------(17)第五章装置的停工--------------------------------------------(23)第六章岗位操作法--------------------------------------------(26)第七章事故预案-----------------------------------------------(34)附:工艺流程图第一章概述根据新的大气污染物综合排放标准(GB16297-1996),二0一一年一月后新上的硫磺回收装置的SO2的排放量要小于960mg/Nm3,因此10000T硫磺回收装置设计时配套了尾气回收装置,该装置设计硫磺收率99.89%,焚烧后尾气中尾气SO2的排放量为578mg/Nm3(1.87Kg/h)。
该装置于2010年底向上海河图设计院提出初步设计委托,2011年9月20日完成中交,该装置设计方面具有以下特点:1.将两级制硫转化器和尾气加氢反应器组合在一起,成为三位一体的整体设备。
2.进一、二级反应器的过程气温度由高温掺合阀自动控制,进加氢反应器的尾气与焚烧炉高温烟气换热,并设换热旁路自动调节反应器入口温度,省去加氢还原炉一台。
3.进燃烧炉酸性气和空气采用调节器进行比例调节。
4.一冷、二冷、蒸汽发生器为组合式,共用一个壳程,发生0.3MPa蒸汽,减少了控制和调节回路。
5.三级冷凝冷却器产生的0.13MPa蒸汽经乏汽冷凝器用循环水取热,凝结术返回三级冷凝器重复使用。
6.尾气急冷塔和尾气吸收塔为单体并列式。
7.本装置尾气吸收用贫胺溶剂由本装置供给、吸收后富液送至置再生。
8.硫磺成型采用钢带造粒机。
第二章工艺原理及流程第一节工艺原理1.克劳斯部分该装置的克劳斯硫磺回收部分仍采用直流式的部分燃烧法,两级转化,其主要的反应式如下H2S + 1.5 O2 === H2O + SO22 H2S + SO2 ===3 S + 2 H2O2 H2S + SO2 === 3/x Sx + 2 H2O2.尾气回收部分尾气回收部分采用的是还原吸收法,克劳斯尾气混合掺入氢以后,被加热到300摄氏度,在钴、钼(CT6-5B)催化剂的作用下,尾气中携带的单质硫、SO2进行加氢反应,COS、CS2进行水解反应。
反应式如下:SO2 + 3 H2 === H2S + 2 H2OS8 + 8 H2 === 8 H2SCOS + 2 H2O === 2 H2S + CO2经加氢反应所有的硫都被转化成H2S,然后经MDEA吸收后送气体到脱硫装置的胺液再生部分,已脱除了H2S的尾气焚烧后经高空排放。
3.液硫脱气工艺用克劳斯工艺生产的液体硫磺,在过程的不同阶段都可以产生H2S,据监测,装置出来的硫中H2S的浓度在余热锅炉处为500-700PPm,在一、二、三级冷凝冷却器尾气捕集器出口H2S的浓度分别为180-280、70-110、10-30、5-10PPm,混合后H2S的含量约为250-300PPm,H2S在液硫中以聚合硫化物(H2Sx)的形式存在。
在液硫脱气工艺中,气氨起着催化剂的作用,将气氨直接注入液硫中,可显著的促进多硫化物分解成H2S,从而提高工艺效率。
该工艺过程用下式表示:H2Sx (注氨) 溶解态的H2S (气体接触与雾化)H2S脱气操作温度应保持在140-155℃之间,脱气时间一般为12小时。
4.加氢催化剂预硫化的过程与原理加氢催化剂中的活性组分钴/钼以氧化态形式存在,经硫化处理后将其变成流化态,活性组分才对加氢还原起催化作用。
预硫化期间催化剂上的硫含量能达3%(W)左右,完全硫化后硫含量约为6%(W)。
预硫化是放热反应,应防止催化剂过热。
首先按30℃/h升温速度将反应器催化剂床层温度升高至200℃。
并采样分析确认氧含量小于0.4%(V)。
在维持床层200℃的情况下,慢慢向加氢反应器中注氢,当反应器入口氢含量达3%(V)时,引入酸性气体,调节反应器入口气流中含有约1%(V)的H2S进行硫化。
当反应器进出口H2S含量基本相当时,将反应器入口氢含量提高至6%(V)并将催化剂床层温度升至250℃进行硫化。
反应器进出口H2S含量相当后,再将床层温度升至300℃,仍待进出口H2S含量相当后结束预硫化操作。
第二节工艺流程叙述来自100万吨催化装置,污水汽提及脱硫部分的酸性气进入制硫燃烧炉(F-201),在炉内约有65%(V)的H2S进行克劳斯反应转化为硫,余下的H2S中有1/3转化为SO2。
燃烧时所需的空气有离心鼓风机(C-201AB)供给,C-201AB出口压力由鼓风机入口蝶阀控制在0.05MPa,进炉的空气量按比例控制调节。
自F-201的排出的高温过程气(约1300℃),一小部分通过两个高温掺合阀分别调节第一、第二级转化器(R-201、R-202)的入口温度,其余部分进入制硫余热锅炉(E-201)冷却至350℃,同时E-201壳程产生1.0MPa(kg)的饱和蒸汽。
从E-201出来的过程气,由一级冷凝冷却器(E-204A)冷却至170℃,在E-204A 中被冷凝下来的液体硫磺与过程气分离后自底部流出进入封硫罐(V-205A),顶部出来的过程气经高温掺合阀(SV-201)调节至240℃后进入一级转化器,并在克劳斯催化剂(LS-931、LS-821)的作用下进行有机硫分解及催化转化反应生成硫磺,反应后的过程气有二级冷凝冷却器(E-204B)冷却至160℃,冷却下来的硫磺自E-204B底部流入V-205B,顶部出来的过程气再经高温掺合(SV-202)至220℃进入R-202进行二级催化转化,反应后的过程气经E-205冷凝冷却后,温度又从236℃降至130℃。
液体硫磺自E-205底部流进V-205C,顶部出来的过程气经尾气分离罐(V-204)分液后,进入尾气处理部分。
经尾气分离罐(V-204)除硫后的尾气与硫磺回收装置的尾气混合,再经过混氢,然后进入尾气换热器(E-208),与尾气焚烧炉(F-202)出口的高温烟气换热至300℃后进入加氢反应器(R-203),在钴、钼催化剂的作用下进行的加氢和水解反应,使尾气中的SO2、元素硫、有机硫还原与水解为H2S。
加氢反应后366℃的高温气体进入尾气急冷塔(T-201),经与急冷水逆流接触,水洗冷却至40℃再进入尾气吸收塔(T-202),再由MDEA吸收了H2S后进入尾气焚烧炉(F-202),在700℃高温下,将尾气中残留的硫化物焚烧成SO2。
焚烧后的尾气首先经尾气余热锅炉(E-207)冷却至430℃,然后经气气换热器(E-208)冷却至300℃再经80米的烟囱排放。
E-201、E-207、E-204发气分别经压控PY-204、PV-248、PY-205调节后并入1.0MPa、0.3MPa系统,其上水分别由FY-211、FY-248、LY-205自动控制。
E-205发生0.13或0-0.4MPa(g)蒸汽经PV-206后进入A-201,由空冷冷凝冷却后的凝结水循环使用,E-205的液面由室外不定期地补充。
T-201中的急冷水主要来源为凝结水与尾气中所携带的近30℃的反应水,塔底部的急冷水由P-204AB抽出后分两路,一路经FY-244、FT-244冷却水后返回塔顶作为水洗冷却水,并控制塔顶温度<40℃,一路经LY-241、FT-101、打入污水汽提装置,并控制T-201底部液面。
进入T-202的贫胺液来自气体脱硫装置的P-301/AB出口,自塔的上部进入,富液自塔底由P-205AB抽出,做为富液直接回到脱硫装置的再生部分进行胺液再生。
F-202的供风是来自C-203ABC,炉膛温度由瓦斯流量控制(FT-247),进炉的风量由FT-246与瓦斯流量(FT-247)按比例控制。
E-207的炉后温度是手动调节E-207的中心孔的开度来调整。
第三节主要控制指标一、比例控制方案该方案空气量调节分两路,其一是空气量随酸性气量变化构成比例控制系统,从而基本保证空气,酸气比值近似于1.33:1;其二是H2S/SO2与空气流量构成比例系统,进一步对空气、酸气配比进行修正,从而保证过程气中H2S与SO2的比值始终2:1。
二、两级转化器入口温度控制保证转化器入口温度稳定时提高硫转化率的基本条件之一,设计采用能够自动控制的高温掺合阀控制一、二级转化器入口温度。
这种直接掺合的温度控制方案具有反应灵敏,控制精度高的特点。
三、鼓风机停机自保控制在正常生产过程中当鼓风机意外停机时,自保系统动作,打开酸性气放火炬TV-208B 从而保证装置的安全生产。
四、F-202火焰监测连锁控制系统在正常生产过程中,当F-202火灭时,自保系统动作,关闭瓦斯进F-202阀TV-248打开氮气吹扫阀,关闭尾气阀进F-202阀门,打开尾气放火炬阀TV-248。
第四章装置的开工第一节开工前的准备一、全面大检查1.检查所有设备、管线、法兰等是否安装完毕,符合工艺要求。
2.检查F-201、F-202耐火衬里砌筑情况是否良好,内部杂物是否清理干净,防爆门、看火孔、火嘴等安装是否符合要求。
3.检查高温掺合阀、考克、蝶阀等安装情况,开关是否灵活。
4.检查各安全阀是否安装就位,定压值是否符合规定并加有铅封。
5.联系仪表检查仪表安装情况,并进行校验合格好用。
6.检查各设备的接地、照明是否完好。
7.应拆加的盲板是否已拆加。
8.检查记录表是否准备齐全,化验室各项目是否准备就绪。
9.装置区域清扫干净,各种脚手架拆除。