碱性蚀刻液直接电解工艺说明
碱性氯化铜蚀刻液(精)

碱性氯化铜蚀刻液1.特性1)适用于图形电镀金属抗蚀层,如镀覆金、镍、锡铅合金,锡镍合金及锡的印制板的蚀刻。
2)蚀刻速率快,侧蚀小,溶铜能力高,蚀刻速率容易控制。
3)蚀刻液可以连续再生循环使用,成本低。
2.蚀刻过程中的主要化学反应在氯化铜溶液中加入氨水,发生络合反应:CuCl2+4NH3→Cu(NH3)4Cl2在蚀刻过程中,板面上的铜被[Cu(NH3)4]2+络离子氧化,其蚀刻反应如下:Cu(NH3)4Cl2+Cu →2Cu(NH3)2Cl所生成的[Cu(NH3)2]1+为Cu1+的络离子,不具有蚀刻能力。
在有过量NH3和Cl-的情况下,能很快地被空气中的O2所氧化,生成具有蚀刻能力的[Cu(NH3)4]2+络离子,其再生反应如下:2Cu(NH3)2Cl+2NH4Cl+2NH3+1/2 O2→2Cu(NH3)4Cl2+H2O从上述反应可看出,每蚀刻1克分子铜需要消耗2克分子氨和2克分子氯化铵。
因此,在蚀刻过程中,随着铜的溶解,应不断补加氨水和氯化铵。
应用碱性蚀刻液进行蚀刻的典型工艺流程如下:镀覆金属抗蚀层的印制板(金、镍、锡铅、锡、锡镍等镀层) →去膜→水洗→吹干→检查修板→碱性蚀刻→用不含Cu2+的补加液二次蚀刻→水洗→检查→浸亮(可选择) →水洗→吹干3. 蚀刻液配方蚀刻液配方有多种,1979年版的印制电路手册(Printed Circuits Handbook)中介绍的配方见表10-4。
表10-4 国外介绍的碱性蚀刻液配方国内目前大多采用下列配方:CuCl2·2H2O 100~150g/l 、NH4Cl 100g/l 、NH3·H2O 670~700ml/12配制后溶液PH值在9.6左右。
溶液中各组份的作用如下:NH3·H2O的作用是作为络合剂,使铜保持在溶液里。
NH4Cl的作用是能提高蚀刻速率、溶铜能力和溶液的稳定性。
(NH4)3PO4的作用是能保持抗蚀镀层及孔内清洁。
碱性蚀刻制程讲义全
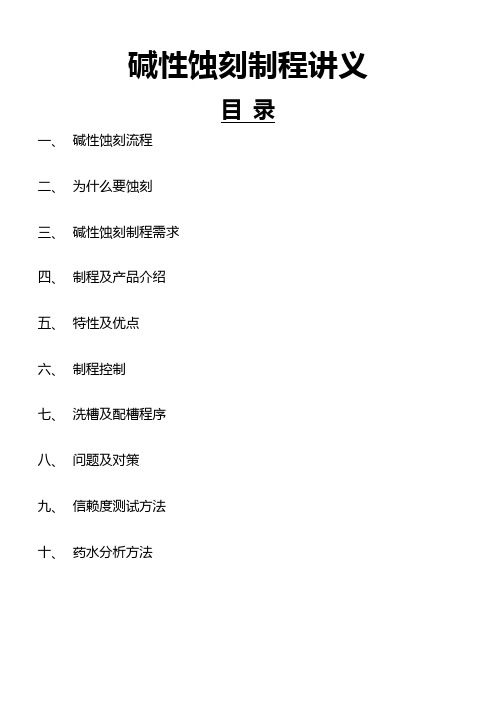
碱性蚀刻制程讲义目录一、碱性蚀刻流程二、为什么要蚀刻三、碱性蚀刻制程需求四、制程及产品介绍五、特性及优点六、制程控制七、洗槽及配槽程序八、问题及对策九、信赖度测试方法十、药水分析方法一、碱性蚀刻流程剥膜→水洗→蚀刻→子液洗→水洗→剥锡→水洗→烘干二、为什么要蚀刻将基板上不需要的铜,以化学反应方式予以除去,以形成所需要的电路图形三、蚀刻制程需求1.适宜的抗蚀剂类型2.适宜的蚀刻液类型3.可实现自动控制4.蚀刻速度要快5.蚀刻因子要大,侧蚀少6.蚀刻液能连续运转和再生7.溶铜量要大,溶液寿命长四、制程及产品介绍PTL-503B为全溶碱性蚀刻液,适用于图形电镀金属抗蚀层,如镀覆镍.金.锡铅合金.锡镍合金及锡的印制电路板蚀刻1.剥膜成份:NaOH功能:剥除铜面上之干膜,露出底层铜面特性:强碱性,适用于水平及垂直设备2.碱性蚀刻主要成份:NH3H2O NH3Cl Cu(NH3)4Cl2①.Cu(NH3)4Cl2:具有蚀刻能力,与板面Cu反应,生成不具蚀刻能力之Cu(NH3)2Cl,在过量氨水和氯离子存在的情况下,Cu(NH3)2Cl很快被空气氧化生成具有蚀刻能力之Cu(NH3)4Cl2②.NH3.H2O:提供蚀刻所需之碱性环境,并与NH4Cl一道完对Cu(NH3)2Cl之氧化再生③.NH4Cl:提供再生时之Cl-反应原理: Cu+Cu(NH3)4Cl2→2Cu(NH3)2Cl2Cu(NH3)2Cl+2NH4Cl+2NH4OH+O2→2Cu(NH3)4Cl2+2H2OCu+2NH4Cl+2NH4OH+O2→Cu(NH3)4Cl2+2H2O3.剥锡铅:PTL-601D/605 PTL-602A/602B1功能:剥除线路板表面锡金属抗蚀层,露出线路板之铜面,并保持铜面之光泽主要成份:HNO3①.双液型:PTL-602A/602B1A.A液a.氧化剂:用以将Sn/Pb氧化成PbO/SnOb.抗结剂:将PbO/SnO转成可溶性结构,避免饱和沉淀氧化 氧化 氧化 氧化 c. 抑制剂:防止A 液咬蚀锡铜合金 B. B 液a. 氧化剂:用以咬蚀铜锡合金b. 抗结剂:防止金属氧化物沉淀c. 护铜剂:保护铜面,防止氧化 ②. 单液型a. 氧化剂:用以将Sn/Pb 氧化成PbO/SnOb. 抗结剂:将PbO/SnO 转成可溶性结构c. 护铜剂:保持铜面,防止氧化 反应原理: 1. 咬Sn/PbSn/Pb SnO/PbO SnL/Pb L H 2SnO 3(H 2O)X (a) 2. 铜锡合金剥除Cu 6Sn 5 Cu 2++Sn 2+(溶解) Cu 3Sn Cu 2++Sn 2+(溶解)五、 特性及优点六、制程控制1.操作参数表2.槽液维护:补充:蚀刻液比重超过1.21或铜含量超过160g/L时,抽出1/5槽液并添加PTL-501B到原液位管理:A.定期检查自动控制之比重和槽液比重是否符合而做适当校正B.定期分析槽液PH值,铜含量,氯含量,并作成管制图C.每日下班时使用子液冲洗蚀铜机前后进出之滚轮,避免干燥氢氧化铜之累积D.长期不使用时,可多添加3-5%子液,避免NH3过量损失E.停机超过45-60日以上时,清洗蚀刻机槽维护如下:a.将槽液排出到预备槽b.用水喷洗5分钟后排放c.用3%(V/V)HCl清洗并喷洗5分钟后排放d.检查喷洒情况是否正常e.用水再清洗一次并检查加热器,冷却水管及滤钢板f.加水与约2%氨水或子液混合后喷洗5分钟后排放g.将槽液抽回F.氯化铵添加时请先在槽外以槽液溶解后,再加入蚀铜机G.(氯离子标准值-分析值)×NH4Cl/Cl×槽体积(L)×1000=添加氯化铵Kg量H.PH值在50℃时与常温会呈现不同的值,换算公式如下:PH(50)=PH(X)-0.21×(50-X)/10例如:24℃时PH=8.86,问50℃时的PH值是多少?8.86-0.21×(50-24)/10=8.86-0.21×2.6=8.314I. PH值的误差影响因素:温度越低,PH值越高,50℃与常温有时会差约0.04电极会慢慢老化,而此过程中无法得知不同厂牌或不同电极,会差约0.15校正用标准液会吸收空气中的CO2形成碳酸,若溶入标准液时,则影响准确性用PH4.0-7.0与用PH7.0-10.0做校正,也会不同J. 蚀铜液的PH值变数太多,通常只作参考,用滴定碱当量法是比较准确的K. 比重在50℃的值与常温时约差0.01,比重差0.01时,铜含量约差10g/L50℃25℃铜(g/L)1.190 1.200 1401.200 1.210 1501.210 1.220 1601.215 1.225 165七、洗槽及配槽程序1. 新线洗槽程序a.以清水清洗所有药水槽及水洗槽,然后排放b.将各水洗槽及药水槽注满清水,加入5-10g/L片碱,开启循环过滤系统,维持四小时以上然后将废液排除c.用清水冲洗各槽体,并排放d.将各槽注满清水,循环30分钟后排放e.将各槽注入1/2槽体积水,加入1-2%槽体积H2SO4,然后注满清水,开启循环过滤系统,维持1-2小时后排放f.用清水冲洗各槽体,并将水排放g.以清水注满各槽,开启循环过滤系统,维持30分钟后排放h.剥膜槽用5-10g/L NaOH,蚀刻槽用1-2% NH3.H2O,剥锡槽用1-2% HNO3再次循环清洗1小时后,即可进行全线配槽2. 配槽程序A.剥膜槽a.注入1/2槽体积清水,加入50g/L NaOH(NaOH需预先溶解后再加入槽,以免堵塞管道)b.补充水至标准液位,循环20-30分钟c.分析调整药水浓度d.升温至50℃B.蚀刻槽a. 取蚀刻母液PTL-503A(可由旧蚀刻线接取),加入蚀刻槽b. 分析调整母液浓度c. 升温至50℃C.剥锡铅槽a. 单液型剥锡铅液:直接将剥锡铅液原液加入槽(PTL-601D,PTL-605),搅拌均匀b. 双液型剥锡铅液:(PTL-602A/PTL-602B1)①.将PTL-602A原液加入剥锡铅线A段②.将95%槽体积PTL-602B1加入剥锡铅线B段,并缓慢加入5%槽体积H2O2(35%)③.将槽液搅拌均匀八、问题与对策:1. 蚀铜液常见问题与对策2. 剥锡/铅液常见问题及对策九、 信赖度测试方法1. 蚀刻均匀性测试a. 取1PNL 24”×18”之2/2 OZ 含铜基板,两面至少各分为25个方格b. 测各小方格铜厚H 1并依次作好记录c. 以正常之蚀板速度,将2/2 OZ 基板进行蚀刻d. 测蚀刻后各小方块铜厚H 2,并与蚀刻前所测铜厚,相对应作记录e. 以蚀刻前之铜厚H 1,减去蚀刻后之铜厚H 2,即为蚀刻之铜厚hf. 以蚀刻掉铜厚之最小值H min 除去蚀刻掉铜厚之最大值H max ,即为蚀刻之均匀性均匀性= >80%g. ,可调整上下喷压,若同一面均匀性差,可调整板面各区压力分布来改变2. 蚀刻速率测定a. 取一2/2 OZ 含铜基板,称重W 1(g)b. 将板放入蚀刻线,按正常之生产速度进行蚀刻后,取出洗净,吹干称重W 2(g),c. 计算:mil/mind. 计算:蚀刻速率3. 蚀刻因子测定方法a. 取一做完电镀铜锡之PCB 板,要求该板具有朝向各个方向之线路,并有不同线宽线距(3/3mil 至10/10mil)在全板纵横分布b. 将测试板放入蚀刻线,走完蚀刻后出c. 对不同线宽线距之线路作切片分析,如下图d. 蚀刻因子蚀刻因子通常控制在3-5 4. 蚀刻点测试a. 取1/1 OZ 之含铜基板数片(宽度与机台同宽,基板数量应能使基板覆盖整个蚀刻段)b. 将喷压固定,并将速度调整至正常蚀刻之速度c. 将含铜基板逐一放入蚀刻段,板与板之间距须一致,当第一片基板走出蚀刻段后,立即关闭蚀刻之喷淋,待水洗后将蚀刻板逐一按顺序取出d. 将蚀刻板逐一按原蚀刻放置顺序摆放好,观察经由喷洒所造成之残铜是否形成均匀之波峰波谷e. 观察残铜之波峰是否落于蚀刻段长度之70-80%,若在此围,则表示蚀刻点正常,蚀刻速度合适,若不在此围则需调整速度,使蚀刻点落于蚀刻段长70-80%围十、 分析方法㈠. 剥膜液NaOH 化学分析试剂:酚酞指示剂 0.1N HCl方法:a. 取槽液5ml 于250ml 锥形瓶中b. 加50ml纯水c. 加3-5滴酚酞指示剂d. 用1N HCl滴定,溶液由红色变成无色为终点计算:NaOH=0.8×1N HCl滴定ml数㈡. 蚀刻液PTL-503B化学分析①.铜离子含量分析试剂:PH=10缓冲液PAN指示剂(1%) 0.1M EDTA方法:a. 取槽液10ml于100ml容量瓶中,加纯水至刻度线b. 从上述溶液中取5ml于250ml锥形瓶中c. 加入30ml纯水并加入20ml PH=10缓冲液d. 加入4-6滴PAN指示剂e. 用0.1M EDTA滴定,溶液由蓝色变成草绿色为终点计算:Cu2+(g/L)=12.71×0.1M EDTA滴定ml数②.氯离子含量分析试剂:20% 乙酸20% K2CrO40.1N AgNO3方法:a. 取槽液10ml于100ml容量瓶中,加纯水至刻度线b. 从上述溶液中取5ml于250ml锥形瓶中c. 加入30ml纯水并加入20ml 20%乙酸,15ml 20% K2CrO4缓冲液d. 用0.1N AgNO3滴定,溶液中沉淀细碎并呈粉红色为终点计算:[Cl-](N)=0.2×0.1N AgNO3滴定ml数③.剥锡/铅液PTL-601D化学分析试剂:酚酞指示剂(1%) 0.1N NaOH方法:a. 取槽液2ml于250ml锥形瓶中b. 加入20ml纯水并加入3-5滴酚酞指示剂c. 用0.1N NaOH滴定,溶液由无色变成粉红色为终点计算:[H+](N)=0.5×0.1N NaOH滴定ml数④.剥锡/铅液PTL-605化学分析试剂:酚酞指示剂(1%) 0.1N NaOH方法:a. 取槽液2ml于250ml锥形瓶中b. 加入20ml纯水并加入3-5滴酚酞指示剂c. 用0.1N NaOH滴定,溶液由无色变成粉红色为终点计算:[H+](N)=0.5×0.1N NaOH滴定ml数⑤.剥锡/铅液PTL-602A/B1化学分析A. PTL-602A含量分析试剂:甲基红指示剂(0.1%) 1N NaOH方法:a. 取5ml槽液于250ml锥形瓶中b. 加入50ml纯水c. 加入3-5滴甲基红指示剂d. 用1N NaOH溶液滴定,颜色由红色变成黄色为终点计算:PTL-602A(N)=0.2×1N NaOHB.PTL-602B1含量分析←酸当量分析试剂:甲基红指示剂(0.1%) 1N NaOH方法:a. 取5ml槽液于250ml锥形瓶中b. 加入50ml纯水c. 加入3-5滴甲基红指示剂d. 用1N NaOH溶液滴定,颜色由红色变成黄色为终点计算:PTL-602B1(N)=0.2×1N NaOH滴定ml数↑双氧水含量分析试剂:35% H2SO40.1M KMnO4方法:a. 取1ml槽液于250ml锥形瓶中b. 加入50ml纯水c. 加入20ml 35% H2SO4溶液d. 用0.1N KMnO4溶液滴定,颜色由无色变成微红色为终点计算:35% H2O2(%)=4.91×0.1M KMnO4滴定ml数。
碱性氯化铜蚀刻液原理及基础配方
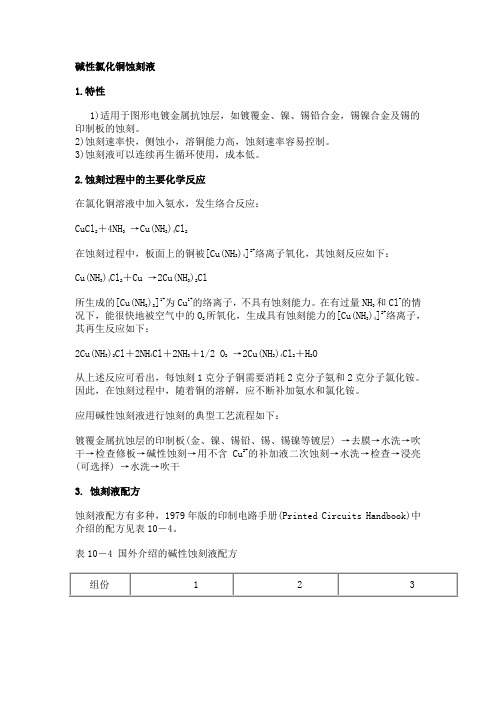
碱性氯化铜蚀刻液1.特性1)适用于图形电镀金属抗蚀层,如镀覆金、镍、锡铅合金,锡镍合金及锡的印制板的蚀刻。
2)蚀刻速率快,侧蚀小,溶铜能力高,蚀刻速率容易控制。
3)蚀刻液可以连续再生循环使用,成本低。
2.蚀刻过程中的主要化学反应在氯化铜溶液中加入氨水,发生络合反应:CuCl2+4NH3→Cu(NH3)4Cl2在蚀刻过程中,板面上的铜被[Cu(NH3)4]2+络离子氧化,其蚀刻反应如下:Cu(NH3)4Cl2+Cu →2Cu(NH3)2Cl所生成的[Cu(NH3)2]1+为Cu1+的络离子,不具有蚀刻能力。
在有过量NH3和Cl-的情况下,能很快地被空气中的O2所氧化,生成具有蚀刻能力的[Cu(NH3)4]2+络离子,其再生反应如下:2Cu(NH3)2Cl+2NH4Cl+2NH3+1/2 O2→2Cu(NH3)4Cl2+H2O从上述反应可看出,每蚀刻1克分子铜需要消耗2克分子氨和2克分子氯化铵。
因此,在蚀刻过程中,随着铜的溶解,应不断补加氨水和氯化铵。
应用碱性蚀刻液进行蚀刻的典型工艺流程如下:镀覆金属抗蚀层的印制板(金、镍、锡铅、锡、锡镍等镀层) →去膜→水洗→吹干→检查修板→碱性蚀刻→用不含Cu2+的补加液二次蚀刻→水洗→检查→浸亮(可选择) →水洗→吹干3. 蚀刻液配方蚀刻液配方有多种,1979年版的印制电路手册(Printed Circuits Handbook)中介绍的配方见表10-4。
表10-4 国外介绍的碱性蚀刻液配方国内目前大多采用下列配方: CuCl2·2H2O 100~150g/l 、NH4Cl 100g/l 、NH3·H2O670~700ml/12配制后溶液PH值在9.6左右。
溶液中各组份的作用如下:NH3·H2O的作用是作为络合剂,使铜保持在溶液里。
NH4Cl的作用是能提高蚀刻速率、溶铜能力和溶液的稳定性。
(NH4)3PO4的作用是能保持抗蚀镀层及孔内清洁。
碱性蚀刻循环再生直接电解工艺(80吨)

按操作规范以此为原材料调配成合格 蚀刻子液回用到蚀刻机进行蚀刻工 80 作,从而能实现资源的循环利用,达 到保护环境的目的
碱性蚀刻废液直接电解工艺是与蚀刻生产线联动的闭合循环系统,是消除 PCB 铜蚀刻废液二次污染的有效措施和重大革新。该系统再生液回收利用率达 100%,金属铜的回收率达 100%。整个系统主要由两部分组成: 1.铜提取系统, 通过阴阳极复合板直接电解提取高纯度铜,电沉积法降低蚀刻废液中的铜离子 浓度;2.蚀刻液储存和成分调节系统,将已降低铜含量的蚀刻液即行业中称为 的电解再生液通过成分调节,使其各项指标达到生产所需的要求,此时行业中 称之为蚀刻再生子液,通过比重控制进行自动添加返回至蚀刻生产线进行蚀刻 工作使,从而实现资源的循环利用及废液的零排放,达到清洁生产的目的。
如下:
蚀刻工艺 产品附价值 碱性蚀刻工
蚀刻废液 艺
价值所在
废液含大量 的金属铜
数量(吨)
能否实现资源循环利用
低价委外处理,既不能实现资源的循
80
环利用,还可能在转移的过程中会造
成二次污染
碱性直接电 解铜回收工
艺
电解铜 电解再生液
纯度高的单 质铜
含有大量蚀 刻液成分
直接高价售给冶炼厂进行进一步提纯 8
碱性蚀刻循环再生直接电解工艺
一、背景 为了响应国家环保政策,进一步节能减排,减少蚀刻废液在转移过程中带来
的环境污染及重金属的二次污染,结合本司的现有实际情况,引进碱性蚀刻循 环再生直接电解工艺。 二、工艺流程图
三、工艺原理 通过设计标准化的碱性直接电解槽,石墨板作为阳极,单面上铜的不锈钢
板(特殊处理)作为阴极,再在电解过程中加入少量的添加剂,使得碱性蚀刻 废液中的铜离子通过电沉积后以块状铜单质出现在阴极板上,不间断的工作使 得电解槽中碱性蚀刻废液中的铜离子浓度下降,并控制在一定的铜离子浓度(通 过流量控制器进行恒量补充相应量蚀刻废液),从而得到一个稳态运行的系统, 电解提铜后的高氨氮水再通过补加相应物料达到蚀刻子液的参数标准后完全回 用至蚀刻生产线进行蚀刻工作,实现零排放。
蚀刻工艺(酸性、碱性、微蚀)

PCB外层电路的蚀刻工艺在印制电路加工中﹐氨性蚀刻是一个较为精细和覆杂的化学反应过程, 却又是一项易于进行的工作。
只要工艺上达至调通﹐就可以进行连续性的生产, 但关键是开机以后就必需保持连续的工作状态﹐不适宜断断续续地生产。
蚀刻工艺对设备状态的依赖性极大, 故必需时刻使设备保持在良好的状态。
目前﹐无论使用何种蚀刻液﹐都必须使用高压喷淋﹐而为了获得较整齐的侧边线条和高质量的蚀刻效果﹐对喷嘴的结构和喷淋方式的选择都必须更为严格。
对于优良侧面效果的制造方式﹐外界均有不同的理论、设计方式和设备结构的研究, 而这些理论却往往是人相径庭的。
但是, 有一条最基本的原则已被公认并经化学机理分析证实﹐就是尽速让金属表面不断地接触新鲜的蚀刻液。
在氨性蚀刻中﹐假定所有参数不变﹐那么蚀刻的速率将主要由蚀刻液中的氨(NH3)来决定。
因此, 使用新鲜溶液与蚀刻表面相互作用﹐其主要目的有两个﹕冲掉刚产生的铜离子及不断为进行反应供应所需要的氨(NH3)。
在印制电路工业的传统知识里﹐特别是印制电路原料的供货商们皆认同﹐并得经验证实﹐氨性蚀刻液中的一价铜离子含量越低﹐反应速度就越快。
事实上﹐许多的氨性蚀刻液产品都含有价铜离子的特殊配位基(一些复杂的溶剂)﹐其作用是降低一价铜离子(产品具有高反应能力的技术秘诀)﹐可见一价铜离子的影响是不小的。
将一价铜由5000ppm降至50ppm, 蚀刻速率即提高一倍以上。
由于在蚀刻反应的过程中会生成大量的一价铜离子, 而一价铜离子又总是与氨的络合基紧紧的结合在一起﹐所以要保持其含量近于零是十分困难的。
而采用喷淋的方式却可以达到通过大气中氧的作用将一价铜转换成二价铜, 并去除一价铜, 这就是需要将空气通入蚀刻箱的一个功能性的原因。
但是如果空气太多﹐又会加速溶液中的氨的损失而使PH值下降﹐使蚀刻速率降低。
氨在溶液中的变化量也是需要加以控制的, 有一些用户采用将纯氨通入蚀刻储液槽的做法, 但这样做必须加一套PH计控制系统, 当自动监测的PH结果低于默认值时﹐便会自动进行溶液添加。
碱性蚀刻液铜回收工艺
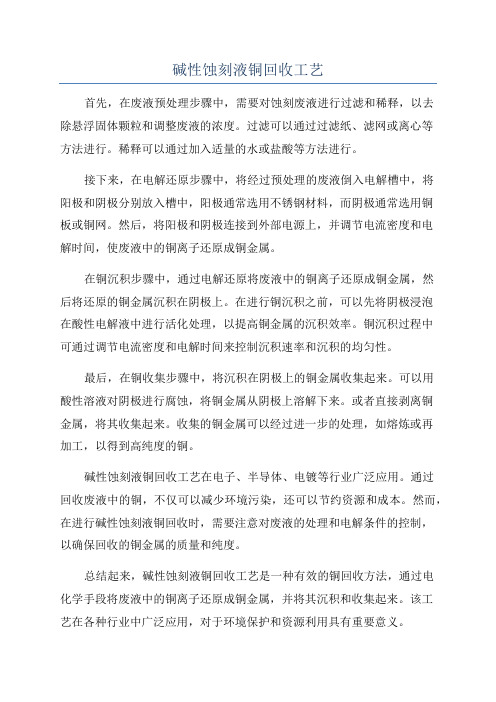
碱性蚀刻液铜回收工艺首先,在废液预处理步骤中,需要对蚀刻废液进行过滤和稀释,以去除悬浮固体颗粒和调整废液的浓度。
过滤可以通过过滤纸、滤网或离心等方法进行。
稀释可以通过加入适量的水或盐酸等方法进行。
接下来,在电解还原步骤中,将经过预处理的废液倒入电解槽中,将阳极和阴极分别放入槽中,阳极通常选用不锈钢材料,而阴极通常选用铜板或铜网。
然后,将阳极和阴极连接到外部电源上,并调节电流密度和电解时间,使废液中的铜离子还原成铜金属。
在铜沉积步骤中,通过电解还原将废液中的铜离子还原成铜金属,然后将还原的铜金属沉积在阴极上。
在进行铜沉积之前,可以先将阴极浸泡在酸性电解液中进行活化处理,以提高铜金属的沉积效率。
铜沉积过程中可通过调节电流密度和电解时间来控制沉积速率和沉积的均匀性。
最后,在铜收集步骤中,将沉积在阴极上的铜金属收集起来。
可以用酸性溶液对阴极进行腐蚀,将铜金属从阴极上溶解下来。
或者直接剥离铜金属,将其收集起来。
收集的铜金属可以经过进一步的处理,如熔炼或再加工,以得到高纯度的铜。
碱性蚀刻液铜回收工艺在电子、半导体、电镀等行业广泛应用。
通过回收废液中的铜,不仅可以减少环境污染,还可以节约资源和成本。
然而,在进行碱性蚀刻液铜回收时,需要注意对废液的处理和电解条件的控制,以确保回收的铜金属的质量和纯度。
总结起来,碱性蚀刻液铜回收工艺是一种有效的铜回收方法,通过电化学手段将废液中的铜离子还原成铜金属,并将其沉积和收集起来。
该工艺在各种行业中广泛应用,对于环境保护和资源利用具有重要意义。
碱性蚀刻液循环再生系统

碱性蚀刻液循环再生系统
一、技术简介
碱性蚀刻液循环再生系统是专门针对PCB印制线路板厂生产中产生的碱性蚀刻废液而设计的,采用先进的封闭式自体循环和平行式无损分离技术(CSC-PLS)进行金属铜的分离和蚀刻液的回用,经严格有效的工艺过程,实现了溶液的长期循环再生和100%铜回收率的目标,同时将生产运行成本控制到最低。
该系统与蚀刻机在线闭环连接,自动循环运作。
二、设备说明
1、工艺流程
蚀刻机中溢流出的碱性蚀刻废液进入母液罐,再用泵送入电解槽。
调整主机内铜离子浓度、氯离子浓度和碱度至规定标准,然后通电电解。
取出产品电解铜,将溶液泵至再生子液罐,并检测溶液各离子浓度、pH值,根据检测结果调整各成分含量,调整完毕再次检测,合格后泵入子液罐中待PCB厂家使用。
三、环保指标
◆该系统采用封闭式自体循环和无损分离技术(CSC-PLS)实现了废液的100%回用
◆在整个过程中无固体废弃物、废液、废气产生
◆完全符合国家清洁生产、节能减排的环保要求
四、特点及优势
◆本系统采用PLS平行式无损分离技术,整个过程无需使用任何萃取剂、添加剂,真正实现了对废蚀刻液的无损分离,保证了蚀刻液回用的质量。
◆本系统采用CSC封闭式自体循环技术对废蚀刻液进行循环再生,整个过程既不带入其他外来物质,也没有产生有害物质,更不会破坏溶液成分,再生蚀刻液性能可以与新购子液相媲美,特别适用于高精度PCB 板制作。
◆该系统稳定性强,设备操作简便,便于维护。
采用一站式闭环控制系统,使设备运行更加可靠,运行成本为同行业最低。
碱性蚀刻液萃取电解铜操作规范

碱性蚀刻液萃取电解铜设备操作规范深圳市宇众环保科技有限公司二O一三年4月1日固定电话:86-0755-******** 传真:*************移动电话:180****6488办公地址:广东省深圳市宝安区沙井镇上寮5区新沙路丰盛大厦808网址: ;邮箱:***************目录1.清洗 (3)2.测试搅拌、泵、过滤器的运行情况 (3)3.调配电解槽电解液的酸度 (3)4.调配水洗液的酸度 (4)5.调节好萃取缸1、2、3、4的液位 (4)6.设备的启动、操作及注意事项 (5)7.停机 (7)8.参数检测方法 (8)9.蚀刻液循环系统保养细则 (9)10.了解氨气及其防范措 (10)11.附表 (11)1.清洗1.1先用毛巾清理安装时缸里的灰尘和胶丝;1.2再用自来水清洗2~3次,直至把各个缸清洗干净为止;1.3清洗干净后,试水,往各个缸注自来水(至每个缸容积的3/4),检查各个缸的性能,是否有漏夜;2.测试搅拌、泵、过滤器的运行情况2.1到电控箱的【泵浦界面】把搅拌、泵逐个逐个打开,逐个检查各搅拌、泵是否反转异常等;2.2如果发现异常,立刻停止启动,及时处理异常后才能试运;2.3检查各个过滤器的运行情况,查看其是否压力过大等问题,及时做好处理措施,防止压力过大损坏泵;2.4检查各管道是否通畅,是否接好,是否漏液;2.5检查完各个设备正常工作后,准备下阶段的工作。
3.调配电解槽电解液的酸度3.1把电解槽里的自来水调至约8m3,把试水时多余的自来水排掉(如有杂物用水瓢捞出来,以防堵泵和管道);3.2把AC缸的循环泵P7开启、打开冷凝水阀门(把阀门开到最大);3.3穿戴好防化服、水鞋、手套等劳保,加入纯度较高的硫酸(约2.8吨、浓度98%),加硫酸时,不能单独进行,旁边一定要有人监视(由于加的量比较多,可多人轮换添加)3.4在添加的过程中,隔着十几分钟,用烧杯取少量的电解液,拿温度计测量是否过热,如果温度过高(高于40℃),停止添加,待冷却后再添加;3.5添加完后,循环15—20分钟后,取少量到化验室化验,酸度控制在170—220g/L;(一般刚开始调试时先把酸度调到170,具体要看反萃取效果来调酸度,在反萃取效果、油液分层效果好的基础上尽量减低酸度。
- 1、下载文档前请自行甄别文档内容的完整性,平台不提供额外的编辑、内容补充、找答案等附加服务。
- 2、"仅部分预览"的文档,不可在线预览部分如存在完整性等问题,可反馈申请退款(可完整预览的文档不适用该条件!)。
- 3、如文档侵犯您的权益,请联系客服反馈,我们会尽快为您处理(人工客服工作时间:9:00-18:30)。
一、工程概况
➢建设单位:深圳市宇众环保科技有限公司;
➢项目:碱性蚀刻液处理系统:30T/月;
➢原液:碱性蚀刻液:含铜量110-130g/L;
二、设计总导则
➢技术设计总导则:本套系统处理工艺是基于充分考虑以下因素的基础上而制定
➢原液的铜离子含量;
➢废水站处理要求;
➢工艺设计的可靠性;
➢设备对原液铜离子改变的适应能力;
➢操作的简便性;
➢投资和运行的费用;
➢设备便于保养和清洁的功能;
➢处理质量的稳定性;
➢本技术总则用于本工程的蚀刻液处理系统。
它提出了该系统的功能设计、制造、性能、安装和调试方面的技术要求。
➢需方即使未规定所有的技术要求和适用标准,供方应提供一套满足本技术方案和所列标准的高质量系统设备及其相应服务。
➢供方应提供高质量的设备。
这些设备应是技术先进、经济上合理、成熟可靠的设备,能满足需方的各项要求。
所有设备的设计、制造和安装应
保证工作的可靠性,并保证尽可能的减少维修量。
➢在签订合作协议之后,需方有权提出因规范标准和规程发生变化而产生的一些补充要求,具体项目由双方共同商定。
三、项目介绍
在电子线路版(PCB)蚀刻过程中,蚀刻液中的铜含量渐渐增加。
蚀刻液要达到最佳的蚀刻效果,每公升蚀刻液需含120至180克铜及相应分量的蚀刻盐(NH4CI)及氨水(NH3)。
要持续蚀刻液中上述各种成份的浓度最佳水平,蚀刻用过后的(以下称[用后蚀刻液])溶液需不断由添加的药剂所取缔。
本系统主要应用直接电解法,可以在回收铜的同时回收蚀刻剂,将大量原本需要排放的[用后蚀刻液]再生还原成为可再次使用的[再生蚀刻液]。
只需极少量的补充剂及氨水,补偿因运作时被[带走]而失去的部份。
从而取代蚀刻子
还可以降低PCB 厂家的生产成本。
使用本系统的主要效益
1.再生液可回收利用,节省物料,降低生产成本。
2.再生液可回收利用,降低治理污水成本。
3.响应国家政策,节能减排,污染基本为零排放,。
4.做到清洁生产,降低工厂环保压力。
四、电解原理
电解缸的蚀刻液阳极阴极通电后,溶液中的铜离子(Cu)向阴极移动,到达阴极后获得电子而在阴极析出纯铜(亦称氯化铜)。
由于这些离子与铜离子相比不易析出,所以电解时只要适当调节电位差即可避免这些离子在阳极上析出。
电能转变为化学能的过程,即直流电通过电解槽,在电极溶液界面上进行电化学反应的过程 。
通电时,在外电场的作用下,蚀刻液中的正、负离子分别向阴 、阳极迁移 ,离子在电极 - 溶液界面上进行电化学反应。
在阴极上进行还原反应。
电解是一种非常强有力的促进氧化还原反应的手段,许多很难进行的氧化还原反应,都可以通过电解来实现。
例如:可将熔融的氟化物在阳极上氧化成单质氟,熔融的锂盐在阴极上还原成金属锂。
电解工业在国民经济中具有重要作用,许多有色金属和稀有金属的冶炼及金属的精炼,基本化工产品的制备,还有电镀、电抛光、阳极氧化等,都是通过电解实现的。
五、技术路线
铜蚀刻子液
PCB 使用:蚀刻
铜蚀刻废液
无损分离铜-蚀刻液再生
循环使用
蚀刻液组分调控
铜蚀刻再生液
铜蚀刻液循环再生技术路线
3.1核心技术及创新性分析
该系统由三部分组成:
➢自控铜无损分离系统。
➢铜电积系统。
➢蚀刻液存储及组份调节系统。
自控铜无损分离系统:
是将废蚀刻液中的铜离子通过富铜剂从废液中无损分离铜离子,并将铜离子移送到铜电积系统,释放铜离子后的贫铜剂再回到此系统继续工件。
铜电积系统:
富铜剂中的铜离子释放到此系统中,通过电积提取高纯度电解铜。
蚀刻液存储及组份调节系统:系统将已降低铜含量的蚀刻液通过组份调节,使Cu²+、Clˉ、PH值达到生产要求,待生产所用。
系统工作时,整个系统物料实现无排放封闭式循环运行。
3.2系统对外界的要求
➢由需方将蚀刻液液送至设备安装处;
➢由需方将电源线输送至电控柜上;
➢由需方提供设备安装所需场地,占地约10-20平方;
六、技术资料清单
1. 工艺总说明、平面布置图;
2.电气图;
3 操作手册;
4.安装、调试、售后服务内容
➢调试工作:现场安装结束后由深圳市宇众环保科技有限公司部全面负责系统的调试工作;
➢培训工作:在现场进行系统调试的同时,结合现场调试实际情况对操作员进行现场培训;
➢对操作员讲解系统设备的技术图纸资料、操作手册、培训结束后可全面掌握全套系统的工艺流程、设备工作原理、操作规程、并能独立进操作与维护全套系统,进行一般性的故障排除和维修。
六、环保效益分析
我们的技术开发战略是从污染源头来预防而不是被动地从事后治理污染的角度出发。
对PCB企业各工序的污染源特征进行本质分析,以确定其采用循环使用、清洁生产的技术可能性;针对各工序(即污染源)产出的不同类型液体废物(废蚀刻液、一次洗涤废水、)之具体特点,分别实行资源化、和无害
化战略,对其有价值部分进行回收,有用部分进行完全回用,以确保PCB企业蚀刻工序在生产品质上更稳定、含铜废液零排放、使生产成本大幅降低(≥75%)。
七、设备图片
八、工艺流程
九、项目动力准备说明
1.处理30吨碱性蚀刻废液所需水、电、气见下表
序号名称单位用量备注
1 冷却水m3/h 30 2寸管接驳,贵司提供,或在现场安装一台4P 的冰水机
2 电力负荷kva 300 贵司提供,接至现场指定位置
3 废气处理量m3/h 2000 我司安装废气吸收塔,贵司提供场
地
4 自来水m3/h 20 2寸管接驳,贵司接至现场指定位置
贵司承担,如需我司安装,则另外计算费用。
2.项目动力接入点说明
项目用电由贵司配送,根据项目实施用地布局接入指定位置;
●配送DI水与冷却水至项目布局指定位置。
十、蚀刻液直接电解设备清单
项目主体设备规格说明(单套处理量30T/月)
编号设备名称单位数量规格备注
1 电解槽个 1 2500*1200*1200mm
2 循环槽个 1
3 抽风系统套 1
4 设备托盘个 1
5 净化塔套 1
6 储罐个 4 3T
7 组分调节剂补充缸个 1 /
8 冷却系统套 1
9 阳极片块12 1000*660*20mm
10 阴极片块24 1000*660*1.5mm
11 磁力泵个 3
12 整流器个 1
13 电控柜个 1
14 铜条批 1
15 钛螺丝批 1
16 管阀件批 1
17 电器配件批 1
18 控制系统套 1。