超精密车削切削力的试验研究
《单晶硅各向异性超精密切削仿真与实验研究》范文
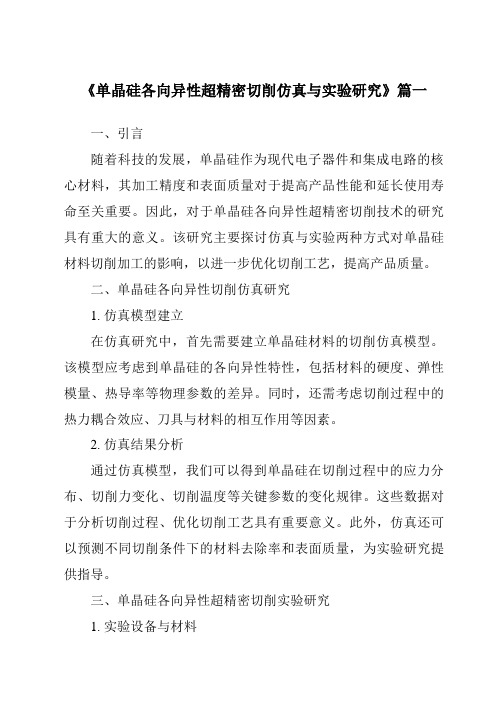
《单晶硅各向异性超精密切削仿真与实验研究》篇一一、引言随着科技的发展,单晶硅作为现代电子器件和集成电路的核心材料,其加工精度和表面质量对于提高产品性能和延长使用寿命至关重要。
因此,对于单晶硅各向异性超精密切削技术的研究具有重大的意义。
该研究主要探讨仿真与实验两种方式对单晶硅材料切削加工的影响,以进一步优化切削工艺,提高产品质量。
二、单晶硅各向异性切削仿真研究1. 仿真模型建立在仿真研究中,首先需要建立单晶硅材料的切削仿真模型。
该模型应考虑到单晶硅的各向异性特性,包括材料的硬度、弹性模量、热导率等物理参数的差异。
同时,还需考虑切削过程中的热力耦合效应、刀具与材料的相互作用等因素。
2. 仿真结果分析通过仿真模型,我们可以得到单晶硅在切削过程中的应力分布、切削力变化、切削温度等关键参数的变化规律。
这些数据对于分析切削过程、优化切削工艺具有重要意义。
此外,仿真还可以预测不同切削条件下的材料去除率和表面质量,为实验研究提供指导。
三、单晶硅各向异性超精密切削实验研究1. 实验设备与材料实验需要使用高精度的切削设备、刀具和单晶硅材料。
刀具的选择应考虑到其硬度、耐磨性、热稳定性等特性,以适应单晶硅的切削需求。
同时,为了确保实验数据的可靠性,需要使用高质量的单晶硅材料。
2. 实验方法与步骤在实验过程中,首先需要设定不同的切削条件,如切削速度、进给量、切削深度等。
然后,在相同的条件下进行多次切削实验,以获取稳定可靠的实验数据。
在切削过程中,需要实时监测切削力、切削温度等关键参数的变化。
此外,还需要对切削后的工件进行表面质量检测,如粗糙度、亚表面损伤等。
3. 实验结果分析通过对实验数据的分析,可以得出不同切削条件对单晶硅材料去除率和表面质量的影响规律。
同时,将实验结果与仿真结果进行对比,验证仿真的准确性。
此外,还可以通过分析亚表面损伤等数据,评估切削过程中材料的力学性能和热学性能的变化。
四、仿真与实验结果对比与分析通过对比仿真与实验结果,可以发现两者在单晶硅各向异性超精密切削过程中具有一定的相关性。
弱刚性超高强度铝合金零件精密切削试验研究

建 立 了切 削力的 经验模 型 , 同时利 用有 限元 软件 分析 零件 的加 工 变形 。 经检 测 , 算 变形 量 与 实际情 况基 计
本 一致 。 结合有 限元模 型 和切 削 力经验模 型优 化零件 的加 工参 数 , 并对 零件 夹紧 方式进行 改进 , 高 了加 提
工精 度 。
器 和数据 分 析 软 件 组 成 。试 验 前 对 测 力 仪 进 行 了
标定 。
和 f . =o 1mm/ , r用直 线 拟合 得 到 切 削速 度 改变 时
与切 削力 之 间关 系 。 刃倾 角 为 O时 : 。
= 2 - 0. 0 .9- 0 05×
= 5 .2— 0 0 .0 01×
F =
1 . 1 3— 0 0 2× . 00
0 2 . O
4 6 5 0
¨
7
0 2 9 9
M 砖 8
O 2 . 4
1 3 4 5
9 3 7 6 3 8
8 O 2 .1 . 7
6 6 2 3 4 S 0 5 5
2 8 64 . . 2
0 0 0 0 0
● ● ● ● ●
工变 质层 和刀 具耐 用度等 均 有影响 , 因此 , 了提 高 为 生产 效率 和降 低加 工 成 本 , 不仅 需要 考 虑 零 件 加工
过程 中 的切削 变形 , 同时还需 要优化 切 削用量 , 以获 得最 佳 的加工 效果 。
5 3 9 6 . . 6 7 1 . . 3 6 7 0 1 . . 7 1
0 3 。试 验 采用 聚 晶 金 刚 石 刀 具 , 角 为 0, 偏 .6 前 。主
角为 1 7 5 , 角 为 7 , 倾 角 为 O 和 6 的 2种 刀 1 . 。后 。刃 。 。
实验车削力的测定及经验公式的建立

实验 切削力实验一、实验目的和要求1. 了解切削测力仪的工作原理和测力方法和实验系统;2. 掌握背吃刀量sp a 进给量f 和切削速度c v 对切削力的影响规律;3. 通过实验数据的处理,建立切削力的经验公式。
二、实验及标定原理三向切削力的检测原理,是使用三向车削测力传感器检测三向应变,三向应变作为模拟信号,输出到切削力实验仪器内进行高倍率放大,再经A/D 板又一次放大之后,转换为数字量送入计算机的。
测力系统首先应该通过三向电标定,以确定各通道的增益倍数。
然后,再通过机械标定,确定测力传感器某一方向加载力值与三个测力方向响应的线性关系。
经过这两次标定,形成一个稳定的检测系统之后,才能进行切削力实验。
测量切削力的主要工具是测力仪,测力仪的种类很多。
有机械测力仪、油压测力仪和电测力仪。
机械和油压测力仪比较稳定、耐用。
而电测力仪的测量精度和灵敏度较高。
电测力仪根据其使用的传感器不同,又可分为电容式、电感式、压电式、电阻式和电磁式等。
目前电阻式和压电式用得最多。
图1 由应变片组成的电桥电阻式测力仪的工作原理:在测力仪的弹性元件上粘贴具有一定电阻值的电阻应变片,然后将电阻应变片联接电桥。
设电桥各臂的电阻分别是R 1、R 2、R 3和R 4,如果R 1/R 2=R 3/R 4,则电桥平衡,即2、4两点间的电位差为零,即应变电压输出为零。
在切削力的作用下,电阻应变片随着弹性元件发生弹性变形,从而改变它们的电阻。
如图1所示。
电阻应变片R 1和R 4在弹性张力作用下,其长度增大,截面积缩小,于是电阻增大。
R 2和R 3在弹性压力作用下,其长度缩短,截面积加大,于是电阻减小,电桥的平衡条件受到破坏。
2、4两点间产生电位差,输出应变电压。
通过高精度线性放大区将输出电压放大,并显示和记录下来。
输出应变电压与切削力的大小成正比,经过标定,可以得到输出应变电压和切削力之间的线性关系曲线(即标定曲线)。
测力时,只要知道输出应变电压,便能从标定曲线上查出切削力的数值。
切削力实验报告

切削力实验报告切削力实验报告引言:切削力实验是机械加工领域中重要的研究内容之一。
通过测量切削力的大小和方向,可以评估刀具性能、优化切削工艺以及提高加工效率。
本实验旨在通过实际操作和数据分析,深入了解切削力的变化规律和影响因素。
实验装置与方法:本次实验采用数控车床进行切削力的测量。
首先,选择适当的刀具和工件材料,并确定切削参数,如进给速度、切削深度和切削速度。
接着,安装刀具和工件,调整好机床的切削参数。
在实验过程中,通过力传感器测量切削力的大小和方向,并将数据记录下来。
最后,根据实验数据进行分析和总结。
实验结果与分析:在实验过程中,我们记录了不同切削参数下的切削力数据,并进行了分析。
首先,我们发现切削速度对切削力有着显著影响。
随着切削速度的增加,切削力呈现出逐渐增加的趋势。
这是因为切削速度增加会导致切削温度升高,材料的塑性变形能力下降,从而增加了切削力的大小。
此外,切削速度的增加也会引起切削过程中的振动,进而增加了切削力的变化幅度。
其次,切削深度也对切削力有着明显的影响。
随着切削深度的增加,切削力呈现出逐渐增加的趋势。
这是因为切削深度的增加会导致切削面积增大,从而增加了切削力的大小。
此外,切削深度的增加也会引起切削过程中的切削力方向的变化,进而影响了切削力的分布情况。
最后,进给速度也对切削力有一定的影响。
我们观察到,随着进给速度的增加,切削力呈现出先增加后减小的趋势。
这是因为进给速度的增加会导致切削过程中的切削面积增大,从而增加了切削力的大小。
然而,当进给速度过大时,切削力会受到切削液的冲击和切削过程中的振动的影响,进而导致切削力的减小。
结论:通过本次实验,我们深入了解了切削力的变化规律和影响因素。
切削速度、切削深度和进给速度都对切削力有着明显的影响。
切削速度的增加会导致切削力的增加,切削深度的增加也会增加切削力的大小,而进给速度的变化则会引起切削力的先增加后减小的变化趋势。
这些实验结果对于优化切削工艺、提高加工效率具有重要的指导意义。
车削力实验报告

一、实验目的1. 了解车削力的产生原理和影响因素。
2. 掌握车削力实验的基本方法和步骤。
3. 分析不同切削参数对车削力的影响。
4. 计算车削力的理论值和实验值,验证理论公式。
二、实验设备与材料1. 实验设备:车削力实验台、车削力传感器、计算机、信号采集与分析系统、数据采集卡等。
2. 实验材料:45号钢棒、砂轮、刀具、工件夹具等。
三、实验原理车削力是切削过程中产生的力,主要分为三个方向:主切削力、径向切削力和轴向切削力。
车削力的产生与切削速度、切削深度、切削宽度、刀具几何参数等因素有关。
四、实验步骤1. 准备实验材料:将45号钢棒加工成所需形状的工件,并安装到工件夹具上。
2. 安装刀具:将刀具安装在车削力实验台上,调整刀具与工件的相对位置。
3. 调整实验参数:设置切削速度、切削深度、切削宽度等实验参数。
4. 进行实验:启动实验台,使刀具对工件进行切削,采集切削过程中的力信号。
5. 数据处理与分析:将采集到的力信号传输到计算机,利用信号采集与分析系统进行数据处理和分析。
五、实验结果与分析1. 主切削力分析(1)实验数据:在切削速度为100m/min、切削深度为2mm、切削宽度为10mm的条件下,测得主切削力为Fz=150N。
(2)理论计算:根据理论公式,计算主切削力为Fz=140N。
(3)误差分析:实验值与理论值之间的误差为7.14%,说明实验结果与理论公式基本吻合。
2. 径向切削力分析(1)实验数据:在切削速度为100m/min、切削深度为2mm、切削宽度为10mm的条件下,测得径向切削力为Fr=20N。
(2)理论计算:根据理论公式,计算径向切削力为Fr=18N。
(3)误差分析:实验值与理论值之间的误差为11.11%,说明实验结果与理论公式基本吻合。
3. 轴向切削力分析(1)实验数据:在切削速度为100m/min、切削深度为2mm、切削宽度为10mm的条件下,测得轴向切削力为Fa=10N。
(2)理论计算:根据理论公式,计算轴向切削力为Fa=9N。
影响单点金刚石超精密车削加工精度因素的研究

影 响单点金 刚石超 精密车削加工精度 因素的研 究
权 艳 红
( 云南广播 电视大学光电工程学院, 云南 昆明 6 5 0 5 0 0)
单 点金 刚石车 削( s P D T ) 加工技术 是获得纳米级
表 面 粗糙 度 及 形 状精 度 的加 工技 术 ,其 是 用超 精 密
在实际超精密切削塑性材料时 ,主切削刃和前 刀面的主要任务是去除材料 ,切削层在前刀面的挤 压作 用 下发 生剪 切 滑 移 和塑性 变形 ,然 后 形 成 切 屑 沿前 刀面 流 出 , 如图 1 ( b ) 所示 。 前 刀 面的形 状直 接 影 响塑 性 变形 的程 度 、切 屑 的卷 曲形 式 和切 屑 刀具 之 问 的摩 擦 特 性 , 并 直 接 对 切 削力 、 切 削 温度 、 切 屑 的 折 断 方式 和 加工 表 面 品质 形成 显 著影 响 。主 切 削 刃 是 前 刀 面和后 刀 面 的交 线 ,实 际上前 刀 面 和后 刀 面 的交线 不 可 能为 理 想直 线 , 而 是 一微 观 交 接 的 曲线 。 该 曲线 的形状 可 以近似 用 与其 在 不 同位 置 的法 平 面 相交成交线的平均曲率半径来反映 ,称其为刃 口半 径p 。刃 口半径 越小 , 应 力越 集 中 , 变形 越 容易 , 切 削 力越 小 , 加工 表面 品质越 好 。 目前计算机仿真技术与求解方法 ,已经被广泛 应 用 于科 学研 究 的各 个 领域 ,此 方法 减 少 了物 理 实 验 的成 本 , 加 速 了实 验 的过 程 。 近年 来 , 有 限 元仿 真 1 单 点金刚石超精密 车削原 理 方 法也 被 广泛 的应 用 于 加工 过 程 的仿 真 中 ,作 为 一 种 预测 切 削力 与 工件 表 面 品质 的工具 ,如 图 2是 使 单点金刚石 车削加工技术是超精密加工中常用 用 MS C . Ma r c 进 行单 点金 刚石 车 削原 理 的仿 真 ,图 3 的 技术 。 由于 金 刚石 的硬 度 高 , 耐磨 性 强 , 导热 性 优 则是 通过 三维仿 真 的切 削力 变化 情况 。 越, 因此 , 金 刚 石刀 具 的刃 口可 以非 常锋利 ( 刃 口半 径 可 以小 于 0 . 0 5 m甚 至更 小) 。 在 理想状 态 下 , 采用 圆 2 影 响 加 工 精 度 的 因素 分 析 弧刃 单点 金 刚石刀 具进 行超 精 密车 削加 工时 , 在工 件 . 1 单 点金 刚石 机床设 备 加工表面形成轮廓峰和轮廓谷 , 它们之 ■
实验二车削力的测定及经验公式的建立

实验二车削力的测定及经验公式的建立实验内容
实验二是关于车削力的测定及经验公式的建立,实验的目的是在给定
的切削参数下,测定进给量和切削力的关系,建立经验公式并计算削削力
系数。
实验原理是利用一组力传感器探测加工过程中产生的力,并使用计
算机进行数据采集和处理,最终获得加工过程中的力-进给量和位移-时间
曲线。
实验装置
本实验使用的是XY201车削机,它是一台半自动的车削机,可以实现
精确定位和高速切削。
本实验使用的加工刀具是RCM系列双曲面刃式T型
车刀,最大切削行程为200mm,主轴转速为1000rpm,切削深度0.2mm。
刀具安装在车削机上,用双联传动带动主轴转动,实现定位和加工。
此外,实验使用了一组力传感器,探测刀具在加工过程中产生的力,并将收集到
的信号发送到计算机上,以获取力-进给量和位移-时间曲线。
实验过程
(1)实验准备工作:首先根据实验要求确定切削参数,调整车削机
的送给量,将力传感器安装在车削机上,将力传感器的信号连接到电脑,
启动车削机,将车刀以圆周的方式移动。
(2)实验测定:根据车削机的设定,控制进给量,每次变化0.1mm,记录力传感器的信号,获取力-进给量和位移-时间曲线。
超精密车削切削力的试验研究
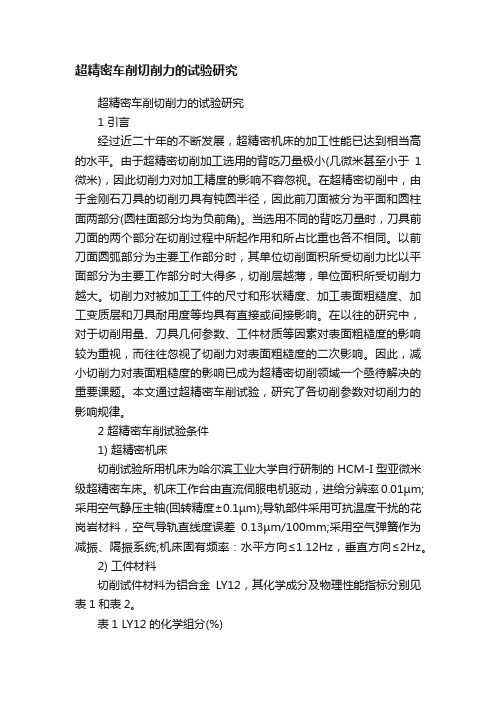
超精密车削切削力的试验研究超精密车削切削力的试验研究1 引言经过近二十年的不断发展,超精密机床的加工性能已达到相当高的水平。
由于超精密切削加工选用的背吃刀量极小(几微米甚至小于1微米),因此切削力对加工精度的影响不容忽视。
在超精密切削中,由于金刚石刀具的切削刃具有钝圆半径,因此前刀面被分为平面和圆柱面两部分(圆柱面部分均为负前角)。
当选用不同的背吃刀量时,刀具前刀面的两个部分在切削过程中所起作用和所占比重也各不相同。
以前刀面圆弧部分为主要工作部分时,其单位切削面积所受切削力比以平面部分为主要工作部分时大得多,切削层越薄,单位面积所受切削力越大。
切削力对被加工工件的尺寸和形状精度、加工表面粗糙度、加工变质层和刀具耐用度等均具有直接或间接影响。
在以往的研究中,对于切削用量、刀具几何参数、工件材质等因素对表面粗糙度的影响较为重视,而往往忽视了切削力对表面粗糙度的二次影响。
因此,减小切削力对表面粗糙度的影响已成为超精密切削领域一个亟待解决的重要课题。
本文通过超精密车削试验,研究了各切削参数对切削力的影响规律。
2 超精密车削试验条件1) 超精密机床切削试验所用机床为哈尔滨工业大学自行研制的HCM-I型亚微米级超精密车床。
机床工作台由直流伺服电机驱动,进给分辨率0.01µm;采用空气静压主轴(回转精度±0.1µm);导轨部件采用可抗温度干扰的花岗岩材料,空气导轨直线度误差0.13µm/100mm;采用空气弹簧作为减振、隔振系统;机床固有频率:水平方向≤1.12Hz,垂直方向≤2Hz。
2) 工件材料切削试件材料为铝合金LY12,其化学成分及物理性能指标分别见表1和表2。
表1 LY12的化学组分(%)3) 金刚石刀具天然单晶金刚石具有极高的硬度、耐磨性和弹性模量,制成的刀具工作寿命长,尺寸耐用度高,切削刃极为锋利,可实现超薄切削,切削刃形可复映在已加工表面上,加工出超光滑表面;金刚石刀具与工件材料间抗粘结性好、摩擦系数低、加工表面完整性好。
- 1、下载文档前请自行甄别文档内容的完整性,平台不提供额外的编辑、内容补充、找答案等附加服务。
- 2、"仅部分预览"的文档,不可在线预览部分如存在完整性等问题,可反馈申请退款(可完整预览的文档不适用该条件!)。
- 3、如文档侵犯您的权益,请联系客服反馈,我们会尽快为您处理(人工客服工作时间:9:00-18:30)。
3航天支撑技术基金资助项目(项目编号:0223HIT 07)黑龙江省自然科学基金资助项目(项目编号:E01220)收稿日期:2002年9月超精密车削切削力的试验研究3王洪祥1 孙 涛1 张龙江1 张 昊2 1哈尔滨工业大学 2黑龙江省科技评估中心摘 要:通过超精密车削试验,分析了微薄切削时进给量和背吃刀量对切削力的影响规律,指出吃刀抗力F t的特殊变化将直接影响加工表面粗糙度,为保证超精密加工表面质量,应在合理范围内选取刀具进给量。
关键词:超精密车削, 切削力, 进给量, 背吃刀量Experimental R esearch on Cutting Force in U ltra 2precise TurningWang H ongxiang Sun T ao Zhang Longjiang et alAbstract :Based on the ultra 2precise turning experiments ,the in fluences of feeds and back cutting depth on the cutting force in micro 2thin cutting are analyzed.I t is pointed out that the machined sur face roughness will be affected by the special change of cutting resisting force Ft ,the feeds of cutter should be selected in a rational range to ensure the ultra 2precise sur face quality.K eyw ords :ultra 2precise turning , cutting force , feed , back cutting depth 1 引言经过近二十年的不断发展,超精密机床的加工性能已达到相当高的水平。
由于超精密切削加工选用的背吃刀量极小(几微米甚至小于1微米),因此切削力对加工精度的影响不容忽视。
在超精密切削中,由于金刚石刀具的切削刃具有钝圆半径,因此前刀面被分为平面和圆柱面两部分(圆柱面部分均为负前角)。
当选用不同的背吃刀量时,刀具前刀面的两个部分在切削过程中所起作用和所占比重也各不相同。
以前刀面圆弧部分为主要工作部分时,其单位切削面积所受切削力比以平面部分为主要工作部分时大得多,切削层越薄,单位面积所受切削力越大。
切削力对被加工工件的尺寸和形状精度、加工表面粗糙度、加工变质层和刀具耐用度等均具有直接或间接影响。
在以往的研究中,对于切削用量、刀具几何参数、工件材质等因素对表面粗糙度的影响较为重视,而往往忽视了切削力对表面粗糙度的二次影响。
因此,减小切削力对表面粗糙度的影响已成为超精密切削领域一个亟待解决的重要课题。
本文通过超精密车削试验,研究了各切削参数对切削力的影响规律。
2 超精密车削试验条件(1)超精密机床切削试验所用机床为哈尔滨工业大学自行研制的HC M 2Ⅰ型亚微米级超精密车床。
机床工作台由直流伺服电机驱动,进给分辨率0101μm ;采用空气静压主轴(回转精度±011μm );导轨部件采用可抗温度干扰的花岗岩材料,空气导轨直线度误差0113μm/100mm ;采用空气弹簧作为减振、隔振系统;机床固有频率:水平方向≤1112H z ,垂直方向≤2H z [1]。
(2)工件材料切削试件材料为铝合金LY 12,其化学成分及物理性能指标分别见表1和表2[2]。
表1 LY12的化学组分(%)组成元素Cu Mn M g Al G B3190标准值3180~41900130~01901120~1180-测试值41501511142-表2 LY12的物理性能弹性模量E (×103MPa )7412切变模量G (×103MPa )2713剪切强度τ(MPa )252H BS 硬度(G Pa )1140强化系数n0132(3)金刚石刀具天然单晶金刚石具有极高的硬度、耐磨性和弹性模量,制成的刀具工作寿命长,尺寸耐用度高,切削刃极为锋利,可实现超薄切削,切削刃形可复映在已加工表面上,加工出超光滑表面;金刚石刀具与工件材料间抗粘结性好、摩擦系数低、加工表面完整性好[3]。
本切削试验所用刀具为英国C ontour Fine T ooling 公司生产的圆弧刃金刚石车刀,刀具前角γ0=0°,后角α0=7°,刀尖圆弧半径r ε=115mm ,切削刃01工具技术钝圆半径r n ≈190nm 。
(4)切削力测量系统为获得超光滑加工表面,除了采用超精密加工机床、金刚石刀具以及对加工环境进行严格控制外,还需利用测量仪器对加工过程进行实时监控、分析与优化。
超精密车削选用的进给量和背吃刀量通常比普通车削小三个数量级,因此加工中产生的切削力也非常小(一般不超过1N ),为此,需要采用高精度、高灵敏度、高可靠性的切削力测量系统。
本切削试验采用的切削力测量系统如图1所示。
该测量系统由安装在机床刀架上的K istler 9256A1型高灵敏度压电式三向测力仪、5019B 型多通道电荷放大器、DynoWare System 数据采集系统软件、5261型A/D 转换卡、主机及显示系统等组成,附带的驱动软件可通过RS 2232C 接口对电荷放大器进行遥控,利用系统的多种图形显示功能可方便地对测量数据进行分析和研究。
图1 切削力测量系统示意图 3 进给量对切削力的影响进给量是影响切削力的重要因素之一。
通过切削试验,得到当背吃刀量a p =10μm 时进给量f 与主切削力F c 、吃刀抗力F t 的对应关系曲线如图2所示。
图2 进给量f 与切削力F c 、F t 的对应关系曲线由图可见,进给量f 对切削力的影响比较显著,F c 和F t 随着进给量的增大而增大。
当进给量f 大于一定值时,F c 和F t 的变化趋势与普通切削相同,即始终保持F c >F t ;当进给量f 小于一定值时,F c 和F t 则具有特殊变化规律,即出现F c >F t 的现象。
当背吃刀量a p =10μm ,进给量分别为f =5μm/r 、f =12μm/r 时,测力仪实际测得的切削力曲线分别如图3a 、3b所示。
(a )f =5μm/r(b )f =12μm/r图3 切削力测量曲线 4 背吃刀量对切削力的影响通过切削试验,得到当进给量f =10μm/r 时背吃刀量a p 与主切削力F c 、吃刀抗力F t 的对应关系曲线如图4所示。
图4 背吃刀量a p 与切削力F c 、F t 的对应关系曲线由图可见,当背吃刀量a p 小于一定值时,也会出现F t >F c 的现象;当背吃刀量a p 大于一定值时,则始终保持F c >F t 。
随着背吃刀量的增大,F c 、F t 值逐渐增大,且F c 的增幅大于F t 的增幅。
5 分析与讨论在超精密微薄切削时,出现F t >F c 现象的主要原因分析如下:作用于前刀面上的切削力主要与进给量f 和背吃刀量a p 有关,而作用于切削刃刃口和后刀面上的切削力除与f 和a p 有关外,还与切削刃钝圆半径r n 有关[4,5]。
当选用的进给量和背吃刀量与切削刃钝圆半径相比较大时,作用于切削刃刃112003年第37卷№5口和后刀面上的正压力比作用于前刀面上的正压力小很多,刀—工接触区以弹性变形为主,塑性变形较小。
由于刀具与工件只在刀尖附近很小区域内接触,其接触面积远小于刀—屑接触面积,因此刀—工之间的摩擦力也远小于刀—屑之间的摩擦力,此时容易出现F c >F t 的现象。
但当选用的进给量和背吃刀量与切削刃钝圆半径之比小到一定程度时,切削力的变化规律将发生变化。
随着进给量和背吃刀量的逐渐减小,与刀—屑接触面积相比,刀—工接触面积逐渐增大,刀—工接触区以塑性变形为主,刀具与工件之间的挤压和摩擦在切屑形成过程中起着关键作用。
此时,作用于切削刃刃口和后刀面上的切削力在总切削力中所占比例较大,而作用于前刀面上的切削力在总切削力中所占比例相对较小,因此就会出现F t >F c 的现象。
由于F t 的这种特殊变化将对已加工表面粗糙度产生直接影响,因此在超精密微薄切削时,应视具体情况合理选择进给量范围,以保证加工获得的表面粗糙度值较小。
6 结论本文通过对铝合金的超精密车削试验,分析了微薄切削时进给量和背吃刀量对切削力的影响及其变化规律,提出了微薄切削时F t 的特殊变化将对加工表面粗糙度产生直接影响的观点。
在超精密切削时,并非选用进给量越小则获得的加工表面粗糙度值越小,因此应考虑切削力变化的影响,在合理范围内选取进给量,以保证超精密加工的表面质量。
参考文献1 赵 奕.脆性材料超精密车削脆塑转变及影响表面质量因素的研究.哈尔滨工业大学博士学位论文,1999,66~672 郑修麟.材料的力学性能.西安:西北工业大学出版社,20003 袁哲俊,王先逵.精密和超精密加工技术.北京:机械工业出版社,19994 J D Drescher.T ool force ,tool edge and sur face finish relation 2ships in diam ond turning.Ph.D.Dissertation ,1992,26~355 Christopher Arcona.T ool force ,chip formation and sur face fin 2ish in diam ond turning.Ph.D.Dissertation ,1996,48~55第一作者:王洪祥,副教授,工学博士,哈尔滨工业大学机电学院机械设计教研室,150001哈尔滨市收稿日期:2002年9月Ni 基变形高温合金小孔攻丝扭矩的试验研究韩荣第哈尔滨工业大学摘 要:采用修正齿丝锥和标准丝锥对Ni 基变形高温合金G H4169难加工材料进行了小孔螺纹攻丝对比试验。
试验结果表明,与标准丝锥相比,采用修正齿丝锥可显著减小攻丝扭矩,且切削锥角较大的修正齿丝锥加工效果较好。
关键词:高温合金, 攻丝, 扭矩, 修正齿丝锥, 切削锥角Experimental I nvestigation on Small 2hole T apping Torqueof Deformable Ni 2base H igh 2temperature AlloyHan R ongdiAbstract :A small 2hole tapping contrast experiment is carried out on G H4169,a kind of deformable nickel 2base high 2tem 2perature alloy ,with a standard tap and a m odified 2tooth tap.The results show that the tapping torque with a m odified 2tooth tap can be greatly reduced com pared to that with a standard tap ,and the better machining effect can be achieved by using a m odified 2tooth tap with a bigger cutting cone angle.K eyw ords :high 2tem perature alloy , tapping , torque , m odified 2tooth tap , cutting cone angle 1 引言高温合金(又称为耐热合金或热强合金)是多组元成分的复杂合金,具有优良的热强性能、热稳定性能及热疲劳性能,可在600~1000℃的高温氧化气氛及燃气腐蚀条件下工作。