橡胶衬里工艺流程.
橡胶衬里工艺流程

橡胶衬里工艺规程化工容器、阀门、管件衬胶工艺流程配合剂生胶铁件切、破胶检查素炼称量配合喷砂混炼清砂热炼出片刷胶浆下料、片料裁剪、刷胶浆贴合中间检查硫化成品检验入库一、铸件的验收以及铸件的热处理1、进厂衬胶的铁件,必须逐一按要求进行检查验收。
2、衬胶的铁件(包括铸件)必须符合下列标准:(1)表面应平整,不允许有毛刺或影响衬胶质量的突出点。
(2)铸件砂孔、缩孔必须肉眼可见底,并可用胶堵塞(不合要求的可补焊)。
(3)两面接合处不得成锐角,最少应为R3左右。
(4)铁件需衬胶面不得有被酸、碱腐蚀,或有不可清除的污物。
(5)焊接件的焊接处不得有明显高低不平和焊接缩孔,以及漏焊现象。
3、热处理出缸时放完汽压,待压力表指针回到零点后,即时打开缸门,并及时搬出全部铁件,不得闷缸。
4、经热处理后的衬胶铁件,应放置在干燥、清洁的地点,让其冷却。
二、喷砂工艺铲除旧胶:喷砂前需将损坏胶层剥离。
一般采用热处理剥离法,即加热需剥离的胶层,使之于钢材基体之间的胶黏层破坏,然后将之铲除。
1、石英砂的要求和处理:(1)石英砂的规格为2#;(2)石英砂在使用前应预先经干燥处理,不得含有水份及杂物;(3)石英砂在使用2-3次后,需经过16目/寸筛网过筛处理,以除去细粉。
2、喷砂操作规程:(1)喷砂人员必须穿戴好防护衣和手套;(2)储气罐压力达6kg/cm2时,打开罐底部阀门,排除罐内积水及油污,关闭阀门,继续充气至6-7kg/cm2,;(3)打开喷枪送气阀,先排除喷枪管内积水及油污,后将送砂管插入砂堆中,保持送砂压力在6kg/cm2以上进行喷砂;(4)喷枪口应与所喷物体距离50-80mm,其角度小于30°,从一点开始,逐渐向前移动;(5)操作过程中如发现水份较多时,应停止喷砂,进行放空排水,待无水时再进行喷砂;(6)喷好砂的铁件,需衬胶部位避免接触水及污物;(7)喷好砂的衬胶件,用干空气吹去灰尘后,及时刷上胶浆,时间最好不超过1小时。
橡胶衬里施工方案
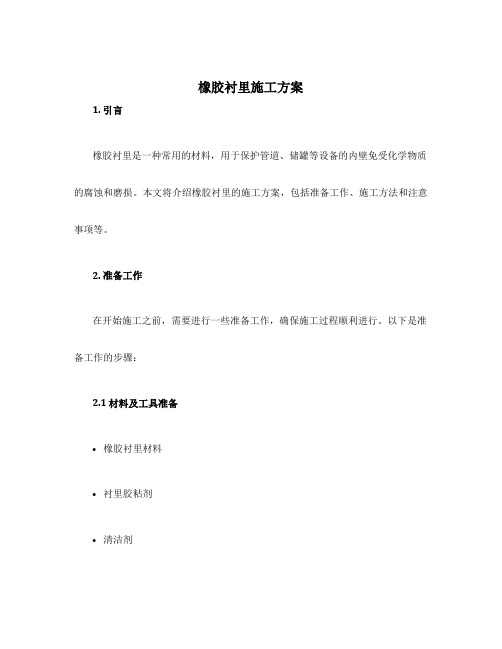
橡胶衬里施工方案1. 引言橡胶衬里是一种常用的材料,用于保护管道、储罐等设备的内壁免受化学物质的腐蚀和磨损。
本文将介绍橡胶衬里的施工方案,包括准备工作、施工方法和注意事项等。
2. 准备工作在开始施工之前,需要进行一些准备工作,确保施工过程顺利进行。
以下是准备工作的步骤:2.1 材料及工具准备•橡胶衬里材料•衬里胶粘剂•清洁剂•刷子和刮刀•打磨工具•铺设工具2.2 表面清洁在施工之前,需要彻底清洁待衬里的表面,以确保橡胶衬里能够充分附着。
2.3 检查和修复表面缺陷检查待衬里的表面,如果存在凹坑、裂缝或其他缺陷,需要进行修复。
修复方法可以包括填充和打磨等。
2.4 试验衬里胶粘剂在开始正式施工之前,要进行衬里胶粘剂的试验,以确保其适用于所选的橡胶衬里材料。
3. 施工方法在准备工作完成后,可以开始进行橡胶衬里的施工。
以下是施工的步骤:3.1 涂胶粘剂使用刷子或刮刀将衬里胶粘剂均匀涂抹在待衬里的表面上。
确保胶粘剂涂抹均匀,以实现最佳的附着性能。
3.2 铺设橡胶衬里在涂抹胶粘剂后的一段时间内,将橡胶衬里平铺在表面上。
确保橡胶衬里完全覆盖待衬里表面,并且没有皱折或空气泡。
3.3 粘合橡胶衬里使用辊轮或其他工具将橡胶衬里压紧,以确保其与表面充分粘合。
确保橡胶衬里与胶粘剂紧密接触,并且没有空隙。
3.4 清洁和修整在粘合橡胶衬里后,清洁并修整表面,以确保整个施工过程的美观和质量。
4. 注意事项在橡胶衬里施工过程中,需要注意以下事项,以确保施工质量和安全性:•使用合适的工具和设备,确保施工过程的安全性。
•严格按照施工工艺和制定的施工方案进行施工,不得随意更改。
•注意橡胶衬里材料的质量和储存条件,在施工之前进行检查。
•在施工过程中,遵循环保和安全规范,确保施工现场的安全和环保。
•在施工完成后,进行必要的检查和测试,确保施工质量达到预期要求。
结论本文介绍了橡胶衬里的施工方案,包括准备工作、施工方法和注意事项等。
只有在合理的准备和严格的施工管理下,才能确保橡胶衬里的施工质量和使用效果。
酸罐橡胶内衬施工程序(3篇)
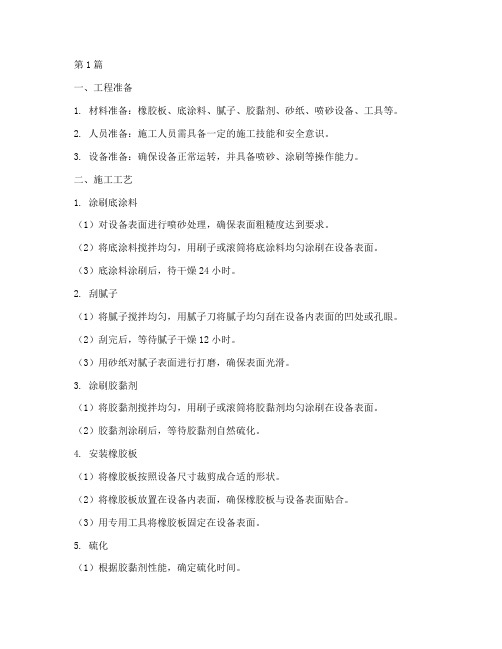
第1篇一、工程准备1. 材料准备:橡胶板、底涂料、腻子、胶黏剂、砂纸、喷砂设备、工具等。
2. 人员准备:施工人员需具备一定的施工技能和安全意识。
3. 设备准备:确保设备正常运转,并具备喷砂、涂刷等操作能力。
二、施工工艺1. 涂刷底涂料(1)对设备表面进行喷砂处理,确保表面粗糙度达到要求。
(2)将底涂料搅拌均匀,用刷子或滚筒将底涂料均匀涂刷在设备表面。
(3)底涂料涂刷后,待干燥24小时。
2. 刮腻子(1)将腻子搅拌均匀,用腻子刀将腻子均匀刮在设备内表面的凹处或孔眼。
(2)刮完后,等待腻子干燥12小时。
(3)用砂纸对腻子表面进行打磨,确保表面光滑。
3. 涂刷胶黏剂(1)将胶黏剂搅拌均匀,用刷子或滚筒将胶黏剂均匀涂刷在设备表面。
(2)胶黏剂涂刷后,等待胶黏剂自然硫化。
4. 安装橡胶板(1)将橡胶板按照设备尺寸裁剪成合适的形状。
(2)将橡胶板放置在设备内表面,确保橡胶板与设备表面贴合。
(3)用专用工具将橡胶板固定在设备表面。
5. 硫化(1)根据胶黏剂性能,确定硫化时间。
(2)在规定时间内,对设备进行硫化处理。
6. 检查(1)硫化完成后,对设备进行外观检查,确保橡胶内衬表面平整、无气泡、无裂缝。
(2)对设备进行功能检查,确保设备运行正常。
三、注意事项1. 施工过程中,注意安全操作,佩戴好防护用品。
2. 涂刷底涂料、腻子、胶黏剂时,保持室内通风良好。
3. 橡胶板裁剪时,确保尺寸准确,避免影响施工质量。
4. 硫化过程中,严格控制温度和时间,确保硫化效果。
5. 施工完成后,对设备进行验收,确保橡胶内衬质量符合要求。
四、总结酸罐橡胶内衬施工程序主要包括底涂料涂刷、腻子刮平、胶黏剂涂刷、橡胶板安装、硫化及检查等步骤。
施工过程中,需严格按照施工工艺进行操作,确保施工质量。
第2篇一、工程概述酸罐橡胶内衬工程是为了提高酸罐的耐腐蚀性能,延长设备使用寿命而进行的一项重要维护工程。
本工程采用橡胶材料对酸罐内壁进行衬里处理,施工过程中需严格按照以下程序进行。
橡胶衬里工艺规程完整

橡胶衬里工艺规程1总则1.1本规程适用于金属设备、管道及管件的橡胶衬里工程。
常用的橡胶衬里天然橡胶板新旧牌号对照参照表1。
表1常用天然橡胶板新旧牌号对照表1.2 设备、管道及管件的金属表面以软、硬橡胶作为覆盖层,能耐化学介质的腐蚀。
天然橡胶的耐腐蚀性能见表2。
表2天然橡胶的耐腐蚀性能1.3 常用硫化胶的物理机械性能见表31.4橡胶衬里在下列温度范围内保持其耐热稳定性:1.4.1 软橡胶在65〜70 C范围内;142 硬橡胶在30〜60 T范围内;143 当受热时间为1〜2小时,温度在80°C以下,软硬橡胶均可满足耐热要求。
2橡胶的质量要求和保管2.1 胶料的质量要求2.1.1 胶板表面完整平滑、无波纹、气泡、裂纹和打皱等缺陷。
2.1.2 胶板两侧及尾部应整齐,没有毛边、锯齿,厚薄均匀一致。
胶板规格、宽度800〜1000 毫米,长10 米以上,厚度(1)1.5 ± 0.25 毫米,(2)2± 0.25 毫米,(3)3± 0.5 毫米;2.1.3 胶板应无杂质和自然硫化现象;2.1.4 胶桨胶料应能全部溶于溶剂汽油中;2.1.5 硬质胶桨与金属结合扯离强度达4MPa以上。
2.2 胶板保管2.2.1 胶板应用垫布卷在木轴上并悬挂在支架上,避免挤压,互相粘结;2.2.2 胶板应保管在通风良好的半暗库内,避免阳光直射或温度过高(应离热源2米以上)而产生老化现象;2.2.3 保管库内温度一般为5〜25 C左右,其相对湿度在40〜50流右;2.2.4 贮存胶板时应避免与液体燃料、油类、酸、碱或其它易燃物质接触;2.2.5 凡自行加工的胶板,每卷不得超过50公斤,否则受压变形。
胶板上应用细布或塑料作垫布,卷在木轴上,不应用滑石粉代替垫布。
2.3 胶桨2.3.1 配制方法和要求2.3.1.1 配制时先将胶桨板表面的杂物除去(如滑石粉、棉绒毛等),然后用剪刀将胶板剪碎,置于配料桶中,注入溶剂汽油在常温下搅拌。
橡胶衬里工艺流程

橡胶衬里工艺规程化工容器、阀门、管件衬胶工艺流程一、铸件的验收以及铸件的热处理1、进厂衬胶的铁件,必须逐一按要求进行检查验收。
2、衬胶的铁件(包括铸件)必须符合下列标准:(1)表面应平整,不允许有毛刺或影响衬胶质量的突出点。
(2)铸件砂孔、缩孔必须肉眼可见底,并可用胶堵塞(不合要求的可补焊)。
(3)两面接合处不得成锐角,最少应为R3左右。
(4)铁件需衬胶面不得有被酸、碱腐蚀,或有不可清除的污物。
(5)焊接件的焊接处不得有明显高低不平和焊接缩孔,以及漏焊现象。
3、热处理出缸时放完汽压,待压力表指针回到零点后,即时打开缸门,并及时搬出全部铁件,不得闷缸。
4、经热处理后的衬胶铁件,应放置在干燥、清洁的地点,让其冷却。
二、喷砂工艺铲除旧胶:喷砂前需将损坏胶层剥离。
一般采用热处理剥离法,即加热需剥离的胶层,使之于钢材基体之间的胶黏层破坏,然后将之铲除。
1、石英砂的要求和处理:(1)石英砂的规格为2#;(2)石英砂在使用前应预先经干燥处理,不得含有水份及杂物;(3)石英砂在使用2-3次后,需经过16目/寸筛网过筛处理,以除去细粉。
2、喷砂操作规程:(1)喷砂人员必须穿戴好防护衣和手套;(2)储气罐压力达6kg/cm2时,打开罐底部阀门,排除罐内积水及油污,关闭阀门,继续充气至6-7kg/cm2,;(3)打开喷枪送气阀,先排除喷枪管内积水及油污,后将送砂管插入砂堆中,保持送砂压力在6kg/cm2以上进行喷砂;(4)喷枪口应与所喷物体距离50-80mm,其角度小于30°,从一点开始,逐渐向前移动;(5)操作过程中如发现水份较多时,应停止喷砂,进行放空排水,待无水时再进行喷砂;(6)喷好砂的铁件,需衬胶部位避免接触水及污物;(7)喷好砂的衬胶件,用干空气吹去灰尘后,及时刷上胶浆,时间最好不超过1小时。
3、喷砂后的衬胶件质量要求:(1)喷砂后的衬胶铁件应显示出均匀一致的金属本色,即应呈银灰色。
(2)凡应衬胶的部位都应有适当的粗糙度(毛糙度)(即衬胶部位不得抛光、打蜡)。
橡胶衬里工艺

橡胶衬里工艺首先需经复合橡胶加工制得未硫化胶料及配套用胶浆,然后在处理合格表面进行贴衬,最后经热硫化而完成的橡胶衬里全过程。
其衬胶施工工艺过程如图。
胶料贴合涂刷胶浆胶料检查胶浆料切块刷底涂料橡胶加工设备表面处理下料裁剪胶浆配制修整缺陷中间检查1、设备表面处理设备表面处理是确保施工质量的重要环节,也是防腐蚀施工的首道工序,它对衬胶层的质量和使用寿命起着决定作用。
通常,设备的衬胶制品热硫化检查修整表面处理采用加压式干法喷砂,最后可得到干净粗糙的设备表面。
2、胶浆的配制将胶浆料溶解在定量的溶剂中可制成粘稠状的胶浆,目前常用的溶剂为120#汽油。
选用胶浆时应符合下列要求:(1)所用的胶浆料应与衬里胶料是配套使用的产品;(2)胶浆料的正常贮存期不超过3个月,并无自硫现象;(3)胶浆料应无油污杂质,能全部溶解于溶剂中,并有一定的粘性和光滑性,不应有沉淀、结块和悬浮物以及其他不良现象;(4)硬质胶浆与金属表面的粘合时其扯离强度不小于6Mpa,软质胶浆与金属表面的粘接强度不应小于2Mpa。
配制胶浆装在密闭的容器内,贮存在阴凉通风的场所。
保存期不超过1个月,在贮存期内应注意温度变化不要太大,否则其中的硫磺可能析出,影响胶浆的质量。
3、胶料的裁剪衬里胶料在下料裁剪前应进行外观检查是否符合胶料的质量要求,如有气泡、针孔、较深的超标压痕等缺陷,其严重部位应剪除不用,超标的气泡可用针刺破、放气并用胶料填补,热烙压平。
胶料表面出现硫磺、滑石粉、线头杂物时须要刷除干净;如有油污、水珠应用干布蘸汽油擦净。
胶板裁剪时应注意下列几类:(1)根据图纸要求和衬里结构特点以及实物尺寸按一般板金工展开法进行下料。
(2)下料应准确,尽量减少衬里的接缝,充分利用胶料。
形成复杂的工件需要制作的样板,按照实样下料。
(3)衬胶层接缝应采用搭接形式,但多层衬胶的首层或转动部位可采用对接形式,为了增加接缝强度。
可在对接缝上加贴同一胶号的橡胶条,进行盖缝保护。
天然橡胶板衬里施工工艺
天然橡胶板衬里施工工艺D-280 阳极液放尽槽一.材料名称: 底层:天然橡胶板(δ=2mm)面层:天然硬橡胶板(δ=2mm)底胶:与天然硬橡胶配合胶浆1.质量要求符合HG-540-67中的有关规定.2.胶板内不应有大于0.5mm的夹杂物.3.胶板上允许每平方米不超过5个5mm2以下的气泡存在.4.橡胶板的规格:厚度在2±0.3mm,宽度不小于500mm,长度不小于5m.二.基层处理方法:喷砂除锈:达到GB8923-88《涂装前钢材表面锈蚀等级》Sa3级标准.三.施工工艺流程(见图)橡胶衬里工艺流程图四.具体施工工艺.1.检查衬里设备是否符合规程规定要求,检查胶板、胶浆的质量,备好加热烙铁的设备、垫布等辅助材料.2.喷砂后的设备表面除去灰尘,用棉纱蘸汽油擦净表面.3.胶浆按照配比进行配置,采用搅拌机搅拌均匀后方可使用.4.胶料在喷砂处理后的8小时内进行涂刷.5.每涂刷一次都应待胶液干燥后再涂刷下一道胶浆,第一遍不少于20~30分钟,第二遍不少于30~40分钟,第三遍管道不少于3小时,设备不少于1.5小时。
6.衬里胶板的剪裁。
检查胶板,去除胶板表面杂物,根据图纸或实物尺寸按照扳金工展开下料,下料时留出胶板搭接缝的余量。
下料时接缝的搭接留料宽度,依据接缝的形式和设备的直径不同来选择。
对接时留量为10~20mm,为了增加接缝的强度,可在接缝处再贴一块宽30~50mm的同种胶板。
采用搭接时一般的搭接宽度为30~50mm,搭接或对接时,接缝处的胶板边缘要割出10~15mm的坡口,以便两块胶板紧密结合。
7.缺陷处理○1胶条塞填法○2挂线排气法○3真空抽吸法以上3种方法均可处理好缺陷。
8.贴衬橡胶板刷完胶浆的设备和胶板干燥后即可进行贴衬,贴衬胶板的方法主要有三种,现采用冷贴热移法。
○1贴衬胶板,将剪裁好并已涂胶浆干燥的胶板用清洁的垫布垫好、卷好、送入设备。
贴衬程序是:立式设备一般先衬底部,后由上往下衬垂直面;卧式设备先衬上半部,后衬下半部,设备的连接管口,使接缝顺着介质流动的方向搭接胶板遍铺遍取出垫布,铺设时应防止将胶板拉长。
橡胶衬里施工技术方案
橡胶衬里施工技术方案橡胶衬里是一种防腐蚀、耐磨损的材料,广泛应用于各种化工设备、储罐、污水处理设备等。
橡胶衬里的施工技术方案包括以下几个方面:1.材料准备和预处理:首先,需要准备好所需的橡胶衬里材料,包括橡胶片、胶粘剂、填料等。
在施工前,需要对材料进行预处理,如将橡胶片放置在室内自然展开一段时间,使其回复弹性,避免在施工过程中产生变形或开裂。
2.衬里面板的制作:根据设备的尺寸和形状,将橡胶片切割成适当的尺寸,并按照设备内部的曲率进行修剪。
然后,将橡胶片用胶粘剂粘贴在金属板上,确保其与金属板紧密粘接。
3.衬里面板的安装:在进行面板安装前,需要先将设备表面清洁干净,确保无油污、灰尘等杂质。
将橡胶面板按照设备内部的形状和尺寸,一个个粘贴在设备表面,确保每个面板之间的缝隙均匀,并用压力机或胶棒加压,使其与设备表面紧密贴合,排除空气。
4.补强和修补:在施工过程中,有时会出现橡胶面板的破损或缺失,需要进行补强和修补。
一般采用补片的方法,将橡胶片按照破损部位的形状修剪成合适的尺寸,用胶粘剂粘贴在破损处,确保与原衬里面板紧密贴合。
5.焊接和密封处理:在一些需要连接或固定的部位,如法兰、排气口等,需要采用焊接或密封处理,以确保其密封性。
橡胶衬里可以使用热压机进行焊接,将衬里面板进行热熔处理,使其与金属接头紧密连接。
对于需要密封的部位,可以使用密封胶或胶粘剂,填补缝隙,确保密封效果。
6.耐磨层涂覆:为了增加橡胶衬里的耐磨性能,可以在衬里面板上涂覆一层耐磨层。
耐磨层可以采用橡胶胶粘剂、橡胶嵌入物、金属焊丝等材料制成。
将耐磨层涂覆在衬里面板上,使其具有更高的耐磨性。
7.质量检验和保养:在施工完成后,需要对衬里施工进行质量检验,检查施工过程中是否存在问题,如是否有漏胶、气泡、开裂等情况。
对于存在问题的部位,需要进行修补和处理。
施工完成后,还需要定期进行保养,检查衬里的状况,如有破损和老化等情况,及时进行修补或更换。
总之,橡胶衬里施工技术方案涉及材料准备、表面处理、面板制作与安装、补强与修补、焊接与密封处理、耐磨层涂覆和质量检验与保养。
橡胶衬里施工技术方案强烈推荐
橡胶衬里施工技术方案强烈推荐橡胶衬里作为常用的防腐材料,被广泛应用于化工、电力、冶金等各个行业。
其具有优异的性能,如耐腐蚀、耐磨损、耐高温、抗老化等,是一种性价比高的防腐材料。
为了保证橡胶衬里的防腐效果,施工过程中需要严格控制工艺和工作流程。
下面就橡胶衬里施工技术方案进行详细介绍。
一、前期准备工作:1. 地基处理:清洁表面,去除松散混凝土、油污、灰尘及其他物质。
2. 基层处理:腐蚀采取除锈、打磨、喷砂等方法,切割吊顶防水被面,清理零散构件、扳手盖等遮蔽物。
3. 清洗处理:使用清洗剂洗刷地面,并彻底清洗积水沟,排干道中杂物及污水。
4. 水泥垫层:在混凝土地面上依次进行水泥砂浆、耐酸砂浆、普通砂浆层的抹灰和压平,保证基础整体性能。
5. 预埋件处理:钢筋预埋件洗刷去锈、涂刷防锈油。
二、胶皮材料施工:1. 混合胶料:按比例将A、B两部分胶料进行搅拌,保持混合均匀,避免过量混合。
2. 手工绕线:将胶皮材料绕于管件内,两层钢丝网套入,管道内外对接处喷1~2次涂料。
3. 机械绕线:将机械绕线机器的引线接通,将胶;皮材料由机器带动,绕于管件内,两层钢丝网套入,管道内外对接处喷1~2次涂料。
4. 填充胶料:用不锈钢填充器将胶皮材料中的气泡、缝隙等填满,确保胶皮材料等厚度,表面平滑饱满。
填缝时要注意不要引起反弹,应将填缝杆理直、理顺、实满,每次压实找平后即可填下一缝。
三、橡胶衬里辅料施工:1. 胶皮材料:经过再次混合后,进行单层或者双层涂敷,干燥过程中避免阳光直射或暴雨、强风等。
要按规定时间涂干第一层,然后再涂第二层着量,一定要保证厚度规格。
2. 过度滑线:将待处理管道端口用自攻螺丝固定钢片,然后用电动机将钢片全长套在管子上,确保钢片与管口连接紧密,然后使用过度滑线器进行滑线。
3. 开始衬里:衬里时应将衬材的塑化剂分装并注入胶皮材内,再将其放入被衬物内,用麻袋翻折,将胶皮材料周围的空气从中隔离出来,保证衬材将物体内的空气隔绝。
橡胶衬里方案
橡胶衬里施工方案一、衬里施工工艺二、施工工器具1. 展开下料剪裁过程中所用的工具,有钢板尺、弯尺、划规和剪刀等工具。
2.涂刷和配制胶浆的容器,有:各种规格的胶浆桶、各种毛刷等。
3.衬胶用的垫布,一般采用绝缘绸、薄膜和胶板隔离布。
三、施工程序及技术要求1.设备表面的处理是采用加压干法,机械喷砂除锈,清除金属表面的氧化物和油污等一切杂质,使其表面呈现出均匀一致的金属本色,并具有一定的粗糙度的设备表面。
处理后的表面应达到一级标准,即符合GB8923-88中的Sa3级的质量要求。
2.导电胶泥采用:天华化工机械及自动化研究设计院防腐蚀工程技术研究所研制生产的乙烯基酯树脂型TH-300JD导电胶泥;2.1使用温度:液态:≤120℃;2.2标准涂层:约80-100um;2.3施工方法:刮板、抹子涂抹施工;2.4胶泥配方(重量百分比):主剂:引发剂:促进剂=100:1.5-2:1-1.5;2.5涂层间隔时间:2h-30d指触干燥约4h;2.6操作条件:操作周围环境温度:5℃以上;操作周围环境湿度:不大于85%。
3. 涂刷底涂料:3.1在金属表面经喷砂处理后或导电层施工完毕经验收合格,并办理隐蔽工程记录后,立即涂刷一遍底涂料。
3.2使用前应搅拌均匀,薄薄地涂刷一层,不能漏涂或涂成花面。
3.3涂刷底涂料的作用主要有两条:一是增强胶黏剂与基体间的剥离强度;二是防止基体表面处理后二次生锈,影响胶板同基体的粘结强度。
4. 刮腻子:涂完第一遍底涂料后,对金属表面的凹坑处和焊缝的凹处或孔眼,应用腻子刮平、减少打磨。
腻子刮完后12h要对其表面进行打磨光滑,干燥24h以后再涂刷一遍底涂料。
涂完后最短4h,最长15d可涂刷胶黏剂,否则时间过长易发生第二次生锈。
4.1 涂刷胶黏剂:胶黏剂配制时要严格按配比准确称重,随用随配,配制量要保证2h内用完。
涂刷时要求均匀,避免漏涂、花涂和厚薄不均。
4.2 衬贴胶板:(1)将晾胶完毕的胶板用塑料薄膜或绸布做衬布把胶板卷好,按指定位置将胶板平铺到基体表面上,铺胶板要平直整齐,随铺随将衬布抽出,此时应注意胶板坡口处的含缝。
- 1、下载文档前请自行甄别文档内容的完整性,平台不提供额外的编辑、内容补充、找答案等附加服务。
- 2、"仅部分预览"的文档,不可在线预览部分如存在完整性等问题,可反馈申请退款(可完整预览的文档不适用该条件!)。
- 3、如文档侵犯您的权益,请联系客服反馈,我们会尽快为您处理(人工客服工作时间:9:00-18:30)。
橡胶衬里工艺规程化工容器、阀门、管件衬胶工艺流程配合剂生胶铁件切、破胶检查素炼称量配合喷砂混炼清砂热炼出片刷胶浆下料、片料裁剪、刷胶浆贴合中间检查硫化成品检验入库一、铸件的验收以及铸件的热处理1、进厂衬胶的铁件,必须逐一按要求进行检查验收。
2、衬胶的铁件(包括铸件)必须符合下列标准:(1)表面应平整,不允许有毛刺或影响衬胶质量的突出点。
(2)铸件砂孔、缩孔必须肉眼可见底,并可用胶堵塞(不合要求的可补焊)。
(3)两面接合处不得成锐角,最少应为R3左右。
(4)铁件需衬胶面不得有被酸、碱腐蚀,或有不可清除的污物。
(5)焊接件的焊接处不得有明显高低不平和焊接缩孔,以及漏焊现象。
3、热处理出缸时放完汽压,待压力表指针回到零点后,即时打开缸门,并及时搬出全部铁件,不得闷缸。
4、经热处理后的衬胶铁件,应放置在干燥、清洁的地点,让其冷却。
二、喷砂工艺铲除旧胶:喷砂前需将损坏胶层剥离。
一般采用热处理剥离法,即加热需剥离的胶层,使之于钢材基体之间的胶黏层破坏,然后将之铲除。
1、石英砂的要求和处理:(1)石英砂的规格为2#;(2)石英砂在使用前应预先经干燥处理,不得含有水份及杂物;(3)石英砂在使用2-3次后,需经过16目/寸筛网过筛处理,以除去细粉。
2、喷砂操作规程:(1)喷砂人员必须穿戴好防护衣和手套;(2)储气罐压力达6kg/cm2时,打开罐底部阀门,排除罐内积水及油污,关闭阀门,继续充气至6-7kg/cm2,;(3)打开喷枪送气阀,先排除喷枪管内积水及油污,后将送砂管插入砂堆中,保持送砂压力在6kg/cm2以上进行喷砂;(4)喷枪口应与所喷物体距离50-80mm,其角度小于30°,从一点开始,逐渐向前移动;(5)操作过程中如发现水份较多时,应停止喷砂,进行放空排水,待无水时再进行喷砂;(6)喷好砂的铁件,需衬胶部位避免接触水及污物;(7)喷好砂的衬胶件,用干空气吹去灰尘后,及时刷上胶浆,时间最好不超过1小时。
3、喷砂后的衬胶件质量要求:(1)喷砂后的衬胶铁件应显示出均匀一致的金属本色,即应呈银灰色。
(2)凡应衬胶的部位都应有适当的粗糙度(毛糙度)(即衬胶部位不得抛光、打蜡)。
(3)喷砂后的铁件要有专人检查质量,发现漏喷,或已喷但又生锈斑的必须重新补喷。
或者发现水斑、油污等,必须处理后重新喷砂。
三、衬里胶板工艺1、塑混炼塑炼硬质胶的塑炼胶可塑度一般为0.56~0.6。
混炼混炼加料顺序如下:天然橡胶或合成橡胶→软化剂→胶木粉→其它配合剂→硫黄。
2、出片出片采用压延出片。
出片后用水充分冷却,但水冷后,水分必须挥发干净,否则要影响产品质量(如气泡、脱层等)。
4、胶片厚度分3+0.4mm、5.0+0.5mm等几种。
5、胶板不应有大于0.5mm的外来杂质,但允许有垫布本身粘附的线毛、线头、垫布折皱等造成的印痕,然而该处胶厚应在规定的公差范围内。
6、在规定的存放条件下胶板6个月内不应产生自硫现象,胶浆胶在两个内不产生自硫现象。
衬里胶板的工艺流程如图:天然橡胶→切胶→破胶→塑炼→精炼→压延出片合成橡胶→清除包装检查→入库四、衬胶用浆的制备及刷胶工艺1、胶浆制备:胶浆胶料的制备胶浆用的塑炼胶可塑度一般应较高,太低了易焦烧,太高了影响胶浆的粘性。
硬质胶浆,塑炼胶的可塑度为0.52-0.6,对混炼胶要求各种配合剂充分分散均匀,否则会影响胶浆质量。
(浆胶成份:天然生胶、氧化镁、硫磺、促进剂D、松香、硫酸钡、滑石粉、氧化铁红、红丹)(1)将浆胶剪成小片后,投入搅拌机内,并按2:1的比例加入120#汽油进行搅拌,直至全部溶解。
(2)将调制好的胶浆按1:4,1:6,1:8三种比例用120#汽油稀释,停放8小时后方可使用。
(3)调制好的胶浆,使用前必须搅拌均匀,才可向铁件上涂刷。
2、衬胶件涂刷规程(1)胶浆顺序涂胶顺序胶浆浓度干燥时间(小时)夏季冬季第一次胶料汽油1:8 1-2 2-3第二次胶料汽油1:6 2-3 3-4第三次胶料汽油1:6 3-4 4-5第四次胶料汽油1:4 3-4 4小时以上(2)在涂刷胶浆第一次胶浆前,必须检查一下喷砂后的衬胶件是否符合质量要求,不合要求则需重喷。
(3)涂刷胶浆时,应由下而上均匀一致的按顺序进行涂刷,不允许有积胶流痕,也不应太厚,避免出汽泡。
(4)涂刷胶浆后的表面如附有杂物,应在干燥前除净,漏刷部分及胶落处应进行补刷。
(5)衬胶件凸凹不平处、空隙、砂眼等需在涂末次胶后,用胶浆条填塞、补平,并用小辊压实。
然后再用1:4胶浆涂刷一次。
(6)涂刷胶浆后的衬胶件,必须保持清洁。
(7)涂刷最后一次胶浆至贴胶片之间隔时间不得超过24小时,否则要补刷一次胶浆。
(8)胶浆干燥时间可供参考,特别应注意胶浆未干(一定要干至不粘手),绝不能贴胶片。
3、胶片刷浆操作要点:(1)胶片涂刷顺序涂刷顺序胶浆浓度干燥时间(分钟)夏季冬季第一次胶料汽油1:6 20-50 40-70第二次胶料汽油1:4 50-80 75-100 (2)刷胶浆之前,将准备好的胶片需刷胶的一面向上,平整地放在平台上,检查规格尺寸是否与贴胶物体件需要尺寸相符,然后用干布将胶片上的水份擦净,待干燥后,刷第一次胶浆。
(3)刷胶时应由上至下,均匀一致按顺序涂刷,每次涂刷时胶片表面不应有积胶流痕,也不宜过厚。
(4)胶片搭接部分需多涂刷一次。
(5)刷最后一次胶浆到用片时间不得超过12小时。
(6)涂胶后的胶片更应注意保持清洁。
五、衬里胶板裁剪工艺衬里胶板根据设备的几何形状,加上接缝、边量和加工量等进行裁剪。
具体步骤如下。
1、胶板使用前应检查外观质量、牌号和规格是否符合要求。
裁剪时,应根据部件情况,尽量减少接缝数量。
2、胶板如有气泡杂质,应刺穿或剔除,然后涂上胶浆,并用同种胶料填补,加热烫平。
胶板上的硫磺粉、棉绒和线头等,应用刷子清除。
3、金属壳体清理后,根据其表面形状的尺寸进行胶板裁剪。
裁剪时,必须留出足够的搭接边,并将搭接边切成10-25mm坡口。
4、裁剪管道接板时,应按小于管道内径的原则计算其周长(不包括接缝部分)。
其总长度应等于管道实际尺寸加上法兰翻边部分。
另根据实体情况,增加5cm-10cm的裁剪余量。
5、接缝应根据设备结构情况,确定削边或搭接方向。
接缝可采用搭接形式。
六、成型与贴合工艺1、衬胶管道、阀门、胶片需成型其要点:(1)将刷好胶浆的胶片,根据衬胶件结构情况,确定搭接方向。
(2)搭接成筒状形时,胶浆面向外,筒内要放好衬布以防止胶片互相粘接。
(3)搭接时由一端向另一端缓缓进行搭实,不得用力拉胶片,以防胶片搭头出角。
(4)搭接处两斜坡要对准搭接,不得有过搭或搭不齐现象。
(5)搭接好,将成型好的胶筒或胶片外面用布包裹好备用。
2、贴合前的准备(1)贴合前先检查衬胶件刷过胶浆的部位有无灰尘及杂物,如有应用少量汽油擦去。
(2)检查衬胶件需贴胶部位胶浆是否刷齐,如发现漏刷,必须先补刷胶浆,而且要待胶浆干后方可进行贴胶。
(3)检查衬胶件表面有无尚未补平的空隙、砂眼及凹凸不平现象。
如有则需用胶浆片填增,压实后再刷一次1:4胶浆,待其干后再贴胶片。
3、贴合工艺及操作要点:(1)贴合胶片顺序,应视设备具体结构情况而定。
a一般阀门壳体先贴筒子,后贴上盖口和法兰口。
b管道先贴筒子,后贴法兰口。
c立式设备应由下向上贴合,卧式设备应由上向下贴合。
(2)贴管道、阀门壳体及其它筒状物体时。
A、将用布包裹好的胶筒子穿入筒内。
放正部位,逐步抽出内、外裹布,封好两端口,并将白布垫在出口处,徐徐通入2kg/cm2左右的冷风,使胶片压实在衬胶件上。
B、将两端布抽出,剪去封口多余胶料,用布球由里向外拉出以排除气泡。
如需翻边的,则进行翻边操作。
在翻边时,不得用力拉伸胶片,以防影响胶片厚度。
C、用烧热铲刀割除多余胶料。
如需搭接时则应在割口处涂刷胶浆,待干燥后再贴合胶片。
(3)贴平胶片,法兰口时,应先用布隔离,待放正后徐徐抽布,用光辊由一端向前推压,以排除空气,防止产生气泡。
用小牙辊滚压时,也应由一端向另一端逐步地向前移动滚压,严格防止产生气泡。
(4)贴胶过程中。
不允许使胶片拉伸,影响胶片均匀厚度。
(5)硫化后需要进行加工的衬胶件,衬里的厚度留出加工余量。
(6)衬胶件需贴两层胶片或三层胶片时,其各层搭接处理不得重复在一处,每层贴合时要先涂刷胶浆,待干燥后再贴另一层胶片。
(7)各层胶贴合好后,贴胶人要检查贴合外观质量。
即检查有无气泡、高低不平以及没有滚压实的地方。
如有应及时处理,高低不平处用铲刀铲平,未压实处补充滚实,有气泡的地方用针或热铲从泡的一边斜放气泡,然后用辊赶出空气,并滚压牢实,如需衬胶的补胶后,再用电火花检查一下是否穿电,如穿电则需进一步处理好。
(8)经自检后的衬胶件,停放24小时后,再由专职检验员进行中间检查外观质量,确认符合要求,再用电火花检验器检查有无穿电现象,如有应做好标记,交贴合操作人员及时修理,再进行检查,直至不穿电为止。
七、硫化加压蒸汽混气恒压硫化:加压蒸汽混气恒压硫化此法为衬胶制件在硫化罐内用直接蒸汽进行硫化的一种传统硫化方法。
加压蒸汽硫化法的热载体是蒸汽。
饱和蒸汽的压力与温度存在着一定的依存关系,实际操作中根据胶料的品种等选定硫化制度,严格控制罐内的蒸汽压力和硫化时间,而不测定温度和正硫化点,就能得到质量合格的硫化制品。
加压蒸汽硫化法按照硫化全过程的压力变化又可分为分段硫化法和恒压硫化法。
厚度较大的衬胶层和硬胶制件,一般采用分段硫化的方法。
蒸汽压力逐段升高并逐段保压、降压。
硫化压力的升降和保压时间取决于衬胶层的厚度、胶种和承载材料的量。
分段硫化的目的是使硫化这一热反应所放出的热量及时均衡的导出,不致发生胶料的内部受热焦化,影响衬里的质量。
厚度在8mm以下的各种加压蒸汽硫化衬胶的分段硫化制度见表5-14所示。
恒压硫化法是采用压缩空气和蒸汽的恒压混气硫化操作,在蒸汽升压前和降压时通入0.3Mpa(3kgf/cm2)的压缩空气,使硫化罐内的压力在硫化全过程中始终保持恒定压力。
操作时先向罐内送入压缩空气0.3Mpa,然后逐渐通入蒸气,置换冷空气,保持压力不变(约40分钟),当冷空气置换完后,保持蒸汽压力在0.3Mpa约3小时,随后逐渐送入压缩空气,相应降低蒸汽压力,最终将蒸汽全部置换,这时罐内的温度已降至约40℃,硫化便告结束。
混气恒压硫化法具有工艺简便、效率高、粘接强度大、合格率高等优点。
混气恒压硫化制度见表5-15所示。
表5-14 加压蒸汽分段硫化制度工序硬质胶半硬胶软硬复合胶压力,MPa 时间,min 压力,MPa 时间,min 压力,MPa 时间,min升压保压升压保压升压保压降压保持降压保持降压合计0~0.150.150.15~0.30.30.3~0.150.15~02053018030202850~0.150.150.15~0.240.240.24~0.30.30.3~0.240.240.24~0.150.150.15~03030202020180~2403040302030450~4800~0.10.10.20.20.2~0.280.280.28~0.150.150.15~02010101020180201030320 表5-14 加压蒸汽混气恒压硫化制度工序硬质胶软质胶压力,MPa 时间min压力,MPa 时间min 空气蒸汽空气蒸汽升压置换保持置换降压降温合计0~0.30.3~00~0.30.3~00~0.30. 30.003~20401804010603500~0.250.25~00~0.250.25~00~0.250.250.25~02030150401060310 八、衬里质量检验和缺陷修补1、目测检验:观察衬里有无突起,气泡及接头不牢等缺陷。