冷轧无取向电工钢
新钢冷轧无取向高效电工钢的发展与应用

t e d e l e c t r i c l a s t e e l a l e e x p l o r e d .
_
【
-
●
、
, 、 1 Ke y wo r d s . : e ic f i e n t e l e c t r i c a l s t el ;ma g n e t i c p r o p e r t y ;p r o c e s s e q u i p me n t ;t e c h n o l o g y
向 电 工 钢的 市场 应 用。
关 键
’
词 : 高效电工钢; 磁性能; 工艺装备; 工艺技术
中 图分类 号 : T G 1 4 2 . 7 7
文献标 志 码 : B
・
D e v e l o p me n t a n d A p p H c a U O n o f l I i 曲 E ic f i e n c y C o l d一 r o l e d
.
|
。
。
,
0 概 述
电工钢是电力 、 电子 和军事工业 中不 可缺少的
难度大、 技术保 密程 度高 , 每一条冷轧硅钢生产线 , 根据其装备条件 都 有独 特重大关键技术点。 目前
冷轧电工钢生产厂都追求更 紧凑 、 更环保 、 更低成本
的生产工艺 , 如 采用更加纯净的超低碳 原料 连铸 连 轧生产工艺、 低温板坯加热工艺 、 酸洗一冷轧联合 工 重要软磁合金 , 也是一种用量很大 的节能 型功能材 料, 主要用于制造电动机 压缩机、 发电机和变压器 艺来生产电工钢 , “ 同耐使用新型环保涂层 、 节能型高 ”。 等。为进_ - 一 步降低能耗 和减少环境污染 生产 厂家 温退火等技术开发高效电工钎 直 以来在不 遗余力地并发低铁损、 低污染 的电工 钢产 品。进入 2 1世纪以来 , 我国冷轧电工钢生产得 1 新钢 无取 向电工钢的 发展 到了迅猛发展 , 随着人们对环境保护的 日益重视 , 用 冷轧电工 钢是新钢三 大精 品之一。 2 0 — 0 8年新 户对冷轧 电工钢产品提出了更高 的要求。冷轧硅钢 技术含量高 、 生产工艺路线 长、 工艺复 杂 生产技术 钢开始自主研发无取向电工钢制造技术 , 从冶炼、 连
半工艺冷轧无取向电工钢的开发研究_董梅
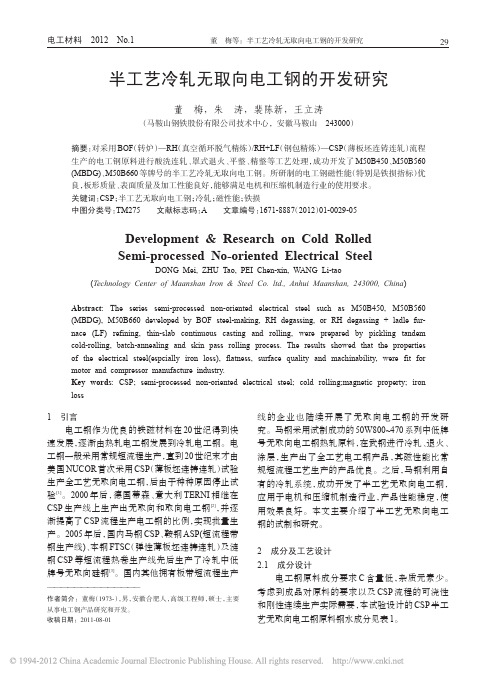
1引言电工钢作为优良的铁磁材料在20世纪得到快速发展,逐渐由热轧电工钢发展到冷轧电工钢。
电工钢一般采用常规短流程生产,直到20世纪末才由美国NUCOR 首次采用CSP (薄板坯连铸连轧)试验生产全工艺无取向电工钢,后由于种种原因停止试验[1]。
2000年后,德国蒂森、意大利TERNI 相继在CSP 生产线上生产出无取向和取向电工钢[2],并逐渐提高了CSP 流程生产电工钢的比例,实现批量生产。
2005年后,国内马钢CSP 、鞍钢ASP(短流程带钢生产线)、本钢FTSC (弹性薄板坯连铸连轧)及涟钢CSP 等短流程热卷生产线先后生产了冷轧中低牌号无取向硅钢[3]。
国内其他拥有板带短流程生产线的企业也陆续开展了无取向电工钢的开发研究。
马钢采用试制成功的50W800~470系列中低牌号无取向电工钢热轧原料,在武钢进行冷轧、退火、涂层,生产出了全工艺电工钢产品,其磁性能比常规短流程工艺生产的产品优良。
之后,马钢利用自有的冷轧系统,成功开发了半工艺无取向电工钢,应用于电机和压缩机制造行业,产品性能稳定,使用效果良好。
本文主要介绍了半工艺无取向电工钢的试制和研究。
2成分及工艺设计2.1成分设计电工钢原料成分要求C 含量低,杂质元素少。
考虑到成品对原料的要求以及CSP 流程的可浇性和刚性连续生产实际需要,本试验设计的CSP 半工艺无取向电工钢原料钢水成分见表1。
——————————————作者简介:董梅(1973-),男,安徽合肥人,高级工程师,硕士,主要从事电工钢产品研究和开发。
收稿日期:2011-08-01半工艺冷轧无取向电工钢的开发研究董梅,朱涛,裴陈新,王立涛(马鞍山钢铁股份有限公司技术中心,安徽马鞍山243000)摘要:对采用BOF (转炉)—RH (真空循环脱气精炼)/RH+LF (钢包精炼)—CSP (薄板坯连铸连轧)流程生产的电工钢原料进行酸洗连轧、罩式退火、平整、精整等工艺处理,成功开发了M50B450、M50B560(MBDG)、M50B660等牌号的半工艺冷轧无取向电工钢。
冷轧无取向电工钢卷板生产工艺

冷轧无取向电工钢卷板生产工艺说到冷轧无取向电工钢卷板的生产工艺,哎呀,这可不是个简单的活儿!如果你一开始觉得这不过是钢铁的事儿,那就大错特错了。
它可是电机、变压器、电力设备这些大佬们的心脏。
没它,电气设备的效率可就大打折扣了!你想想,那个把家里的空调、电冰箱给搞得哐哐响的电机,它的核心部分就是由这种冷轧无取向电工钢做成的。
这种钢就像是电气设备的“血液”,一旦出问题,整个系统都得乱套。
要说这工艺,真的是一点都不简单,讲起来可是有点“门道”的。
大家得知道,“冷轧”其实就是把钢板放在常温下,通过轧制把它压得越来越薄。
就像你用擀面杖擀面团一样,擀到你看那面团已经薄得能透光了。
而钢板呢,压得越来越薄之后,它的物理性质也发生了变化。
比起热轧钢板,冷轧钢板更坚硬,密度也更高。
要说到“无取向”,简单来说,就是钢的晶粒在生产过程中没有特意定向排列。
这样一来,钢板就可以从各个方向传递磁场,工作时能更高效地传导电流。
这就好比是你找了一条没有“死角”的电路,电流传导起来不费劲,设备运行也更顺畅。
说完了基础的概念,咱们接着来聊聊具体的生产流程。
冷轧无取向电工钢卷板的生产过程,分几步走。
第一步,就是钢铁冶炼。
没错,就是从矿石开始,先把铁矿石冶炼成铁水,然后再加入合金元素,比如硅,这可是关键的环节。
因为硅元素的加入,能大大提升电工钢的磁性性能。
然后呢,把熔化的金属倒进模具里,冷却成一个个大钢锭。
这时候,钢铁就像是刚出生的小婴儿,啥都不懂,一切都得通过“锻炼”来成长。
接下来的步骤就是轧制了。
钢锭进入轧机,就像是进了健身房,开始一轮又一轮的锤炼。
通过几道工序的反复压延,钢锭变得越来越薄,越来越长。
这一步像什么?像你拿着一张厚重的纸,不断把它折叠、压平,最后折成一张又薄又长的纸条。
这时候,钢板已经初步成型,但还不够,还得进行退火处理。
退火的作用就像是钢铁的“放松按摩”,让钢板的内应力得到释放,减少脆性,增强延展性。
钢板就像是累了一天的工人,经过这一轮休息,恢复了精气神。
马钢冷轧电工钢产品说明书-20101102

马鞍山钢铁股份有限公司冷轧电工钢产品说明书二零一零年九月目1 2 3 录前言................................................................................................ 1 生产工艺介绍 ........................................................................ 2 种类与主要用途 .................................................................... 3 全工艺无取向电工钢 ............................................................ 4 3.1 3.2 3.3 3.4 4 牌号 .............................................................................. 4 典型磁性能 .................................................................. 5 尺寸、外形、重量及允许偏差 .................................. 5 涂层 .............................................................................. 5 半工艺无取向电工钢 ............................................................ 6 4.1 4.2 4.3 牌号 .............................................................................. 7 典型磁性能 .................................................................. 7 尺寸、外形、重量及允许偏差 .................................. 8 5 6 7 包装......................................................................................... 9 消除应力退火 ........................................................................ 9 环保及相关权威检测结果 .................................................. 10 冷轧电工钢产品说明书前言马钢现有两条全工艺无取向电工钢连续脱碳退火生产线,具备 40 万吨/年生 产能力,产品的厚度为 0.50mm 和 0.65mm,宽度为 800mm~1200mm,并可以根 据用户要求定制。
冷轧硅钢片涂层绝缘性
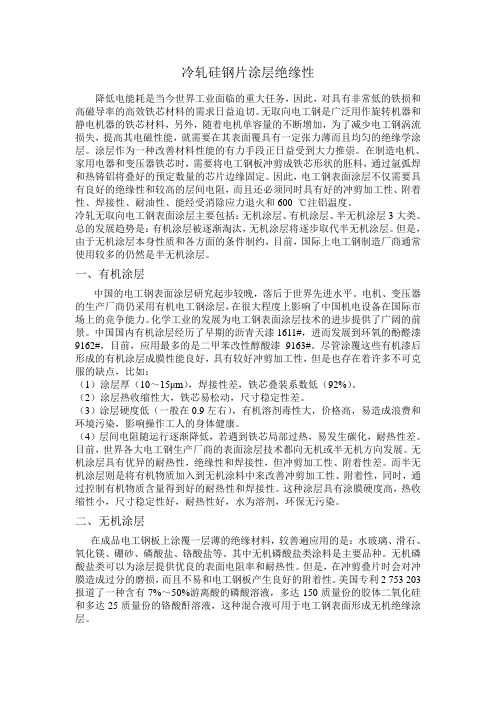
冷轧硅钢片涂层绝缘性降低电能耗是当今世界工业面临的重大任务,因此,对具有非常低的铁损和高磁导率的高效铁芯材料的需求日益迫切。
无取向电工钢是广泛用作旋转机器和静电机器的铁芯材料,另外,随着电机单容量的不断增加,为了减少电工钢涡流损失,提高其电磁性能,就需要在其表面覆具有一定张力薄而且均匀的绝缘学涂层。
涂层作为一种改善材料性能的有力手段正日益受到大力推崇。
在制造电机、家用电器和变压器铁芯时,需要将电工钢板冲剪成铁芯形状的胚料,通过氩弧焊和热铸铝将叠好的预定数量的芯片边缘固定。
因此,电工钢表面涂层不仅需要具有良好的绝缘性和较高的层间电阻,而且还必须同时具有好的冲剪加工性、附着性、焊接性、耐油性、能经受消除应力退火和600 ℃注铝温度。
冷轧无取向电工钢表面涂层主要包括:无机涂层、有机涂层、半无机涂层3大类。
总的发展趋势是:有机涂层被逐渐淘汰,无机涂层将逐步取代半无机涂层。
但是,由于无机涂层本身性质和各方面的条件制约,目前,国际上电工钢制造厂商通常使用较多的仍然是半无机涂层。
一、有机涂层中国的电工钢表面涂层研究起步较晚,落后于世界先进水平。
电机、变压器的生产厂商仍采用有机电工钢涂层,在很大程度上影响了中国机电设备在国际市场上的竞争能力。
化学工业的发展为电工钢表面涂层技术的进步提供了广阔的前景。
中国国内有机涂层经历了早期的沥青天漆1611#,进而发展到环氧的酚醛漆9162#,目前,应用最多的是二甲苯改性醇酸漆9163#。
尽管涂覆这些有机漆后形成的有机涂层成膜性能良好,具有较好冲剪加工性,但是也存在着许多不可克服的缺点,比如:(1)涂层厚(10~15μm),焊接性差,铁芯叠装系数低(92%)。
(2)涂层热收缩性大,铁芯易松动,尺寸稳定性差。
(3)涂层硬度低(一般在0.9左右),有机溶剂毒性大,价格高,易造成浪费和环境污染,影响操作工人的身体健康。
(4)层间电阻随运行逐渐降低,若遇到铁芯局部过热,易发生碳化,耐热性差。
ASB 13-2012冷轧无取向电工钢带 鞍钢
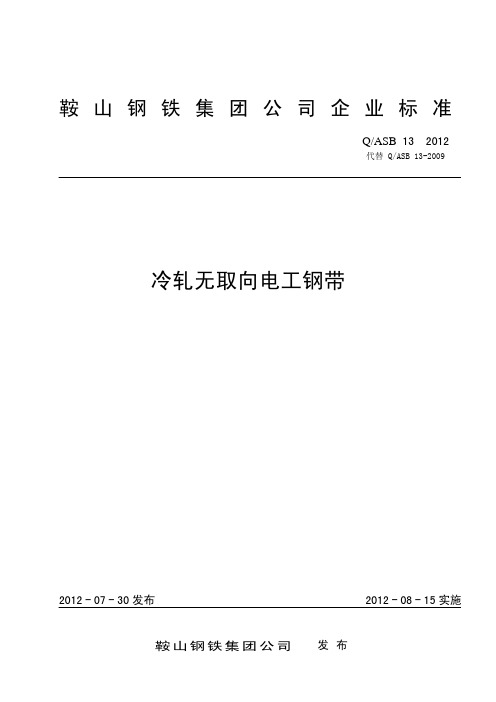
7.50
1.70
8.50
1.71
11.50
1.71
15.00
1.71
表3
最小弯曲 次数 10 10 10 10 10 10
叠装系数 ≥0.975
牌号
35AW230 35AW250
35AW270
35AW300 35AW330 35AW360
35AW400
35AW440 50AW230 50AW250 50AW270 50AW290 50AW310 50AW330 50AW350
10mm
图3 毛刺高度的测量方法 7.1.6 残余曲率的测量
残余曲率是通过测试钢带的底边和支撑板间的距离确定,钢带纵向的残余曲率应按图4进行测试。 测试残余曲率的试样为500+20.5 mm长、宽度等于交货宽度的钢带。 7.2 外观检查
钢带的外观应目视检查。 7.3 检验项目、取样及试验方法
每批钢带的检验项目、取样数量、取样方法、试样尺寸、试验方法应符合表4的规定。 7.4 测试温度
牌号
65AW600 65AW700 65AW800 65AW1000 65AW1300 65AW1600
公称厚度 mm
0.65
理论密度 kg/dm3 7.75 7.75 7.80 7.80 7.85 7.85
最大比总损耗 P1.5 最小磁极化强度 J5000
W/kg
T
5.80
1.66
6.80
1.67
3 定义及牌号表示方法
3.1 定义 3.1.1
比总损耗(简称铁损) 当磁极化强度随时间按正弦规律变化,其峰值为某一标定值,变化频率为某一标定频率时,单位质 量的铁芯所消耗的功率为比总损耗,单位为瓦特每公斤(W/kg),用符号PJ表示。 例如P1.5,表示无取向硅钢在磁极化强度为1.5T,频率为50Hz时,规定的最大铁损值。 3.1.2 磁极化强度 铁芯试样从退磁状态,在标定频率下磁极化强度按正弦规律变化,当交流磁场的峰值达到某一标定 值时,铁芯试样所达到的磁极化强度的峰值,单位为特斯拉(T),用符号JH表示。 例如J5000,表示无取向硅钢在5000A/m交变磁场(峰值),频率为50Hz时,规定的最小磁极化强度值。
Q-BQB 480-2009 全工艺冷轧无取向电工钢带

GB/T 19289-2003 电工钢片(带)的密度、电阻率和叠装系数的测量方法
Q/BQB 400
冷轧产品的包装、标志及检验文件
Q/BQB 401
冷连轧钢板及钢带的尺寸、外形、重量及允许偏差
3 术语和定义 3.1 铁损(比总损耗) iron loss ( specific total loss) 铁损是指在交变磁场下磁化试样时,消耗在试样上的无效电能。在给定频率和最大磁感应强度
3102.5-1993 定义为:
J=B-μ0H 式中,J是磁极化强度,B是磁感应强度,μ0是真空磁导率:4π×10-7H/m,H是磁场强度。
4 标准分享网 免费下载
Q/BQB480-2009
7.7 绝缘涂层
绝缘涂层应有良好的附着性。在剪切过程和供方规定的热处理条件下进行热处理时,涂层不得
3
Q/BQB480-2009
类型
牌号
公称厚度 mm
表4
理论密度 kg/dm3
铁损
P15/50 W/kg 不大于
磁感应强度b
BB50 T 不小于
叠装系数
% 不小于
B35A210
7.60
2.10
1.62
B35A230
7.60
2.30
1.62
B35A250
QWG(GG)04-2004 冷轧取向、无取向电工钢薄带
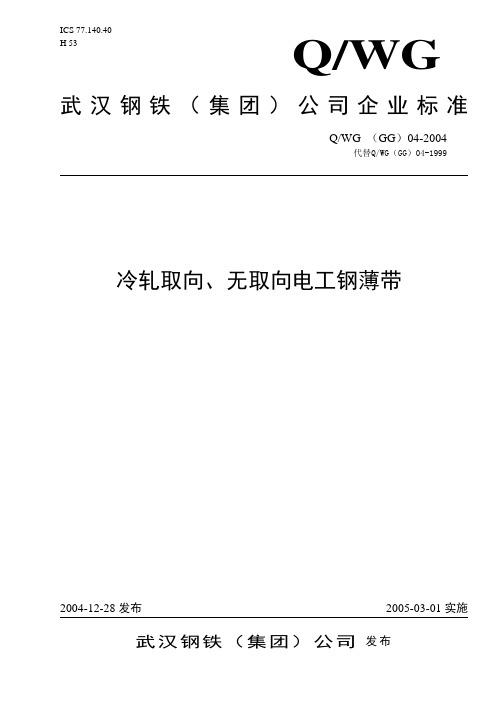
ICS 77.140.40 H 53
Q/WG
武汉钢铁(集团)公司企业标准
7.1 钢带验收由供方技术监督部门进行。
www.bzfxw.com 7.2 每一验收组批(卷)应取测试试样。试样应在钢卷的内、外圈端部不小于 3m 处截取。通过合理安
排测试顺序,同一套试样可用于测试不同的特性。 7.3 取向钢取纵向试样,无取向钢取纵、横向试样(各半)。 7.4 测试环境温度 23±5℃,相对湿度小于 80%。 7.5 按 GB/T 3655 测试磁特性时,允许使用 0.2kg 或 0.5kg 方圈测试,其试样重量为 0.2kg 或 0.5kg 左右。测试的铁损和磁感应强度值应精确到小数后 2 位,第 3 位铁损值非零进 1,磁感值非零舍去。 7.6 钢带的厚度用 0.01mm 精度的千分尺在离边部不小于 15mm 的任何地方测量。 7.7 钢带的宽度在垂直于钢带长度方向测量。 7.8 钢带的不平度测量是将钢片自由地放在平台上,除钢片本身重量外,不施加任何压力。用直尺进行 测量,测量最大波(全波)的高度 h 和波长 L,不平度等于(h/L)×100%。 7.9 钢带的镰刀弯测试是用直尺紧靠钢带的凹侧边,测量直尺与侧边的最大距离。 7.10 钢带的检验结果不符合本标准要求时可进行复验,复验应符合 GB/T247 的规定。
2 规范性引用文件
下列文件中的条款通过本标准的引用而成为本标准的条款。凡是注日期的引用文件,其随后所有的
修改单(不包括勘误的内容)或修订版均不适用于本标准,然而,鼓励根据本标准达成协议的各方研究
- 1、下载文档前请自行甄别文档内容的完整性,平台不提供额外的编辑、内容补充、找答案等附加服务。
- 2、"仅部分预览"的文档,不可在线预览部分如存在完整性等问题,可反馈申请退款(可完整预览的文档不适用该条件!)。
- 3、如文档侵犯您的权益,请联系客服反馈,我们会尽快为您处理(人工客服工作时间:9:00-18:30)。
冷轧取向电工钢1 定义:冷轧取向硅钢是指含2.9%~3.5%Si,钢板晶体组织有一定规律和方向的冷轧电工钢。
一般指具有高斯织构的单取向硅钢片,即(110)晶面平行于轧制面、[001]晶向平行于轧制方向的硅钢。
还有一种冷轧双取向(立方织构{100}<001>)硅钢。
两种硅钢晶粒与轧制方向的示意见图1:(a)高斯织构(b)立方织构冷轧取向硅钢按磁性分为普通取向硅钢片(GO)和高磁感取向硅钢片(Hi —B)。
普通取向硅钢片(GO)和高磁感取向硅钢片(Hi—B)性能见表1,工艺比较见表2。
表1表2取向硅钢以追求其轧制方向上具有高取向度为出发点,力求获得具有{110}<001>高斯织构的晶粒均匀的产品,以满足其使用时在长度方向上具有高磁性能的需要。
对于厚度大于0.3mm的普通取向硅钢(GO),目前比较流行的生产方法是采用抑制剂的二次再结晶法生产。
即以MnS(或MnSe)为抑制剂和二次中等压下率冷轧法。
Hi-B钢按采用的抑制剂和制造工艺不同可分为三种方案:(A)日本新日铁发展的以AIN为主以MnS为辅的抑制剂和一次大压下率冷轧法,其磁性高且稳定,部分产品经激光照射细化磁畴。
是最通用的Hi-B产品制造工艺。
(B)日本川崎发展的以MnSe(或MnS) +Sb为抑制剂和二次中等压下率冷轧,最终退火经二次再结晶和高温净化二段式退火工艺。
其磁性略低于(A)方案且较不稳定。
高牌号中常加入少量钼。
(C)美国GE和ALC公司发展的以N十B+S晶界偏聚元素为抑制剂和一次大压下率冷轧法。
因为固溶硫含量较高,锰含量较低,Mn/S≤2.1,热轧板边裂严重,其磁性也较低且不稳定,现已很少采用。
2 用途:冷轧取向硅钢又称冷轧变压器钢,用于制造各类变压器的铁芯。
3 轧制工艺流程:冷轧无取向硅钢通用的轧制工艺流程如图2所示。
生产具有高斯织构的硅钢,关键在于利用二次再结晶。
为了实现二次再结晶,通常需要在合金中添加正常晶粒长大抑制剂,如MnS等。
晶粒长大抑制剂必须能以参杂的形式弥散地分布在合金基体内,在二次再结晶发生时,能够有效地阻止基体晶拉的正常长大,同时,又要求在最后的高温退火中可方便地消除掉,以免恶化产品的磁性能。
在二次再结晶中、二次晶粒长大的取向核主要依靠适当的冷轧工艺和再结晶退火来产生。
由于相变会破坏晶粒取向,因此在热处理过程中保持单相至关重要。
目前,工业上生产具有高斯织构硅钢的典型工艺可概述如下:初始成分——约3.2%Si,≤0.03%C,0.06~0.10%Mn,0.03%S 。
钢坯加热到1400℃进行热轧成厚度为1.1~2.5mm的薄板。
经常化及酸洗除去除氧化皮后,通过两次冷轧将薄板轧到0.25~0.36mm的最后厚度。
在两次冷轧之间,需将钢板在800~1000℃还原气氛中进行中间退火。
两次冷轧的总压下率为85%左右。
随后,钢板在800℃左右进行湿氢脱碳退火,以便把碳含量降低到0.003%的水平。
最后,钢板需在1100~1200℃干氢中再进行一次高温退火。
在以上工艺中,钢板在800℃退火期间,细小的MnS颗粒是必要的晶粒长大抑制剂,而在最后的高温退火时,其中的S通过和氢反应生成硫化氢从基休中逸出,剩下的Mn将溶解在铁的晶格中。
用这样的工艺生产的硅钢片晶粒粗大,直径为1~5mm,而且90%以上的晶粒具有(110){001}取向。
因此,沿其轧向具有优异的磁性能。
例如,在磁场为0.8kA/m 时,磁感应强度可达1.82T。
相近成分的非取向硅钢,在同样磁场下的磁感应强度只有1.45T。
图24 轧制工艺4.1 热轧工艺1)铸坯3%Si钢导热率低,铸坯急冷或急热都可能产生裂纹,甚至断坯。
铸坯冷到600℃以前以<20℃/h速度慢冷可防止裂纹。
铸坯切断至进入加热炉的时间要保证<10h,否则由于表层与中心区的温差而引起抑制剂固溶状态和组织状态不同,使成品P增高。
17为防止以后高温加热时柱状晶过于粗化,铸坯冷到650~750℃保温5~10h 或以10℃/h速度慢冷使碳化物分布均匀,铸坯加热温度可降到1350℃以下,热轧板晶粒均匀。
铸坯冷到A1相变点附近或A1~950℃范围保温>30min,可在铸坯中形成小晶粒和使第二相溶解度发生变化,也可使加热温度降低约100℃。
2)加热加热温度:GO钢——l350~1370℃ Hi-B钢——1380~1400℃铸坯最好在铸坯表面冷到的>1000℃,中部>1200℃时装炉。
如不能做到,铸坯装炉时的表面温度应>250℃,当硅含量提高到 3.25%~3.45%时最好>300℃,避免加热后出现晶界裂纹。
以MnS或MnSe为抑制剂的铸坯必须经高温加热,使铸坯中>1μm的粗大MnS 固溶(主要存在于铸坯板厚方向的等轴晶中心区内),热轧过程中再以≤50n m的细小弥散状MnS析出。
按取向硅钢的成分,在平衡状态下MnS固溶温度约为1320℃(AlN固溶温度约为1280℃),因此GO铸坯加热温度规定为l350~1370℃。
MnS+A1N万案的Hi-B钢由于锰和碳含量高于GO,所以规定为1380~1400℃。
此时晶粒粗化到10~70mm。
为防止柱状晶反常长大,铸坯加热到约1250℃后,以>150℃/h速度快加热,使许多晶粒同时开始快速长大到彼此相碰,保证柱状晶尺寸小于30mm,以后不出现线晶。
实验证明,铸坯厚度方向中心区温度为1360℃时,晶粒100%长大,产品出现线晶;铸坯厚度方向中心区温度为1345℃时,72%晶粒长大,产品无线晶。
因此,控制中心区温度为1310~1340℃保温15~70min。
按一般加热方式,铸坯下表面温度比上表面低,下表层(110){001}组分强度减弱,二次再结晶不完善,磁性不均匀,如果加热到1250℃以上,控制上下表面温差<70℃,最好<40℃,则热轧板上下表层(110){001}组分强度相近,二次再结晶完善。
3)粗轧铸坯出炉后先除鳞,经4~6道粗轧和用立辊调整板宽。
每道压下率平均分配,第一道最好>30%来破坏柱状晶。
薄板坯厚度为30~40mm。
切头后进行精轧。
细小MnS是在精轧阶段析出,因此必须控制好粗轧后和进入精轧的薄板坯温度、时间和厚度。
一般采用大压下率高速轧制以保证薄板坯温度高。
对G0钢来说,进入精轧的温度控制在1160±20℃。
对AlN+MnS 方案Hi-B钢控制在≥1190℃,目的是在尽量少析出AlN。
4)精轧开轧温度:GO钢1160℃±20℃;Hi-B钢≥1190℃。
终轧温度:GO钢950℃±10℃;Hi-B钢1000℃~1060℃。
卷取温度:550℃。
精轧一般采用六机架四辊连轧机轧6道,每道压下率递减,轧制速度尽量快并增大冷却水量和提高冷却速度。
MnS从约1200℃开始析出,在1100~1150℃的γ相数量最多的温度下析出速度最快,<950℃基本停止析出。
在1200℃到950℃轧制时间控制企50~180s,在精轧过程中产生的大量位错成为MnS析出核心,促使MnS以细小弥散状更快和更均匀析出。
精轧后立即喷水冷却到约550℃卷取。
这可使碳化物弥散分布在晶粒内(针状Fe3C),有利于以后获得细小均匀初次晶粒。
轧后急冷也防止析出AlN。
4.2 常化GO钢热轧板一般不经常化处理。
以A1N为抑制剂时热轧板或最后冷轧前必须在氮气下高温常化。
常化的作用:为析出大量细小AlN。
同时使热轧板组织更均匀和再结晶晶粒数量更多。
具体来说有:a) 常化前后织构无明显变化,通过同位再结晶使再结晶比例增多;b) 升温和保温时热轧板中Fe3C、珠光体、Si3N4和细小AlN固溶,淬在100℃水中后在晶粒内析出许多10~20nm细小ε—碳化物、Fe3C、Fe16N2和A1N。
金相组织为铁素体、珠光体和硬的贝氏体;c)冷轧时细小析出物(主要为ε—碳化物)、固溶碳和氮以及贝氏体都可钉扎位错,使位错密度明显增高和更快地加工硬化,再结晶生核位置增多,初次再结晶晶粒细小均匀;d)脱碳退火后沿晶界附近形成更多的{111}<112>晶粒,过渡带的{110}<001>晶粒数量减少,也就是Σ9重合位向晶粒增多,同时AlN抑制能力加强,{110}<001>,二次晶粒容易长大;e)高温常化后采用二次冷轧法(第二次经大压下率冷轧)时,中间退火后原热轧板中粗大的{211}<011>~{100}<011>晶粒减少,{110}和{111}晶粒增多,晶粒细小均匀。
因为常化后粗大晶粒中含更多的固溶碳和ε—碳化物,冷轧时位错密度更高,更容易再结晶。
再经大压下率冷轧和脱碳退火后{111}晶粒更多和{110}晶粒减少。
一般常化制度:1050~1150℃(最好1100~1120℃)×4~5min。
常化后严格控制开始急冷温度和冷却速度,因为10~50nm AlN就是在冷却过程中通过γ→α相变而析出。
一般在空冷到约900℃后喷水冷却。
常化温度、时间、开始快冷温度和冷却速度与钢中Als和氮含量有关。
如Als含量高,应慢冷;Als含量低,采用快冷。
常化温度过高或时间过长,热轧板中细小MnS聚集粗化、使磁性降低。
4.3 酸洗常化处理后进行喷丸处理和在80~90℃的2%~4%HCl中酸洗1~2min,并将热轧带每边剪掉20~30mm准备冷轧。
4.4 冷轧热轧板常化和酸洗后应尽快冷轧,如果停放时间长,钢中固溶碳和氮析出形成不稳定第二相,使冷轧时碳和氮钉扎位错作用减弱,退火后再析出的AlN尺寸增大,磁性降低。
1)以AlN为主要抑制剂的大压下率冷轧法a)预热:冷轧前硅钢带一般预热到50~80℃。
b)道次压下率:3%Si钢变形抗力大,一般在20辊轧机冷轧,经5~7道冷轧到0.30~0.35mm厚,平均每道压下率为25%~33%。
合适的压下率为82%~90%,最好为85%~88%。
c)冷轧时效:为进—步降低铁损,现在生产上广泛采用冷轧时效工艺。
前几道使用粗面工作辊,每道经约30%大压下率冷轧,关闭润滑系统和快速轧制。
依靠轧制时的变形热将冷轧钢带温度提高到200~250℃。
冷轧时效的作用是使硅钢中固溶碳和氮数量增多,就是使钢中存在的不稳定碳化物和氮化物在时效处理时固溶。
冷轧时固溶碳和氮聚集在位错处,阻碍位错运动,位错群成直线排列,改变了正常滑移系统,促使形成更多的过渡带,冷轧后使再结晶织构发生变化。
同时由于固溶氮(约10ppm)更均匀分布在基体中,以后退火时新形成一批细小AlN加强抑制力。
2)以MnS为主要抑制剂的二次冷轧法a)预热:冷轧前钢卷温度控制在50~80℃。
b)第一次冷轧:经3—4道冷轧,总压下率为60%~70%。
c)中间退火:中间退火制度为850~950℃×2.5~4.0min。
温度过低,初次再结晶不完善。