无取向电工钢(硅钢)生产流程[S]、[C]、[N]的控制剖析
无取向硅钢 生产工艺

无取向硅钢生产工艺
无取向硅钢是一种特殊的电工钢,其具有较低的磁滞损耗和低的铁损耗,适用于制造高效率的电动机和变压器等电气设备。
无取向硅钢的生产工艺主要包括以下几个步骤:
1. 原材料准备:选用高质量的硅钢片原料,通常由硅铁合金和相关的辅助材料制成。
2. 钢液冶炼:将原料放入冶炼炉中进行冶炼,通常采用电爆炉或电弧炉等高温冶炼技术。
3. 钢液浇注:将冶炼后的钢液倒入浇注桶中,通过特定的浇注工艺将钢液注入连续浇铸机。
4. 连续浇铸:将钢液通过连续浇铸机均匀地注入狭缝状的铜板中,形成连续的钢带。
5. 热轧:使用连续热轧机将钢带进行轧制,逐渐减小钢带的厚度和宽度,并达到所需的规格和尺寸。
6. 轧制控制:通过控制轧制温度和压下力等参数,使得钢带的晶粒取向随机化,达到无取向特性。
7. 脱脂退火:将经过轧制的钢带进行退火处理,去除内部的应力和杂质,提高硅钢的磁性能和机械性能。
8. 制品加工:将退火后的钢带进一步切割、打孔、组装等,制成最终的电机或变压器的各种零部件。
9. 表面处理:对钢带进行模切、除锈、涂漆等表面处理,提高产品的外观和耐腐蚀性能。
10. 产品检验:对生产出的无取向硅钢进行严格的质量检验,包括磁性能测试、物理性能测试等。
以上是无取向硅钢的一般生产工艺流程,具体的工艺细节可能会因不同的生产厂家和产品规格有所不同。
新能源无取向硅钢 生产手册
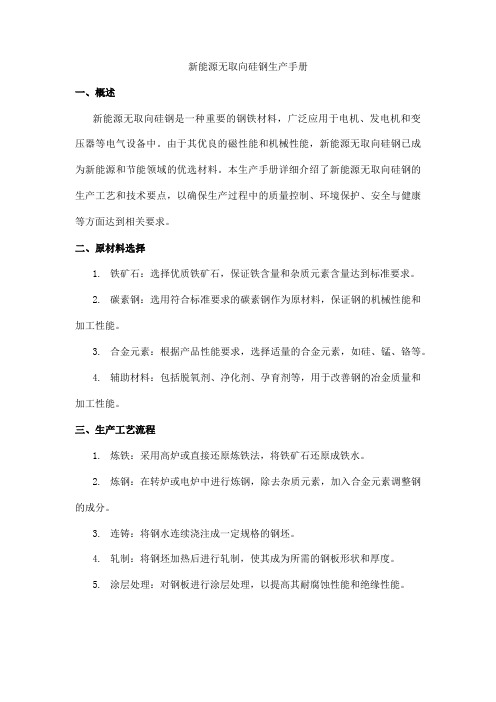
新能源无取向硅钢生产手册一、概述新能源无取向硅钢是一种重要的钢铁材料,广泛应用于电机、发电机和变压器等电气设备中。
由于其优良的磁性能和机械性能,新能源无取向硅钢已成为新能源和节能领域的优选材料。
本生产手册详细介绍了新能源无取向硅钢的生产工艺和技术要点,以确保生产过程中的质量控制、环境保护、安全与健康等方面达到相关要求。
二、原材料选择1.铁矿石:选择优质铁矿石,保证铁含量和杂质元素含量达到标准要求。
2.碳素钢:选用符合标准要求的碳素钢作为原材料,保证钢的机械性能和加工性能。
3.合金元素:根据产品性能要求,选择适量的合金元素,如硅、锰、铬等。
4.辅助材料:包括脱氧剂、净化剂、孕育剂等,用于改善钢的冶金质量和加工性能。
三、生产工艺流程1.炼铁:采用高炉或直接还原炼铁法,将铁矿石还原成铁水。
2.炼钢:在转炉或电炉中进行炼钢,除去杂质元素,加入合金元素调整钢的成分。
3.连铸:将钢水连续浇注成一定规格的钢坯。
4.轧制:将钢坯加热后进行轧制,使其成为所需的钢板形状和厚度。
5.涂层处理:对钢板进行涂层处理,以提高其耐腐蚀性能和绝缘性能。
6.质量检测与包装:对成品钢板进行质量检测,如外观、尺寸、磁性能等,符合标准要求的钢板进行包装。
四、质量控制1.成分控制:严格控制钢的化学成分,保证各合金元素含量在规定范围内。
2.冶金质量:优化炼铁和炼钢工艺,减少钢中的杂质元素和气体含量,提高钢的纯净度。
3.轧制质量控制:确保钢板在轧制过程中的温度、轧制力、轧制道次等工艺参数控制在规定范围内,以保证钢板组织和性能的稳定性。
4.涂层质量:对涂层材料和涂层工艺进行严格控制,以提高涂层的均匀性、致密性和附着力。
5.质量检测与控制:定期对生产过程中的各项工艺参数进行检测和控制,以确保产品质量稳定。
同时,对成品钢板进行严格的质量检测和控制,确保产品符合相关标准和客户要求。
五、环境保护与资源利用1.节能减排:优化炼铁和炼钢工艺,降低能耗和减少废弃物排放。
无取向硅钢 工艺设备和流程

无取向硅钢工艺设备和流程英文回答:The process and equipment used in the production ofnon-oriented silicon steel are crucial in ensuring the quality and performance of the final product. Non-oriented silicon steel, also known as electrical steel, is widely used in the manufacturing of electrical equipment such as transformers, motors, and generators.The production process of non-oriented silicon steel typically involves the following steps:1. Raw material preparation: The main raw materials used in the production of non-oriented silicon steel are silicon and iron. These materials are carefully selected and processed to meet the required specifications.2. Melting and casting: The raw materials are melted ina furnace and then cast into thin slabs or billets. Thecasting process helps to remove impurities and ensure uniformity in the material.3. Hot rolling: The cast slabs or billets are then heated and passed through a series of rolling mills to reduce the thickness and shape the steel into coils or sheets. This hot rolling process improves the mechanical properties of the material.4. Cold rolling: The hot-rolled coils or sheets are further processed through cold rolling mills to achieve the desired thickness, surface finish, and dimensional accuracy. Cold rolling also enhances the magnetic properties of the silicon steel.5. Annealing: The cold-rolled silicon steel undergoes annealing, which involves heating the material to aspecific temperature and then slowly cooling it. Annealing helps to relieve internal stresses and improve the magnetic properties of the steel.6. Coating: In some cases, a thin coating is applied tothe surface of the silicon steel to enhance its electrical resistance and reduce the eddy current losses.7. Cutting and shaping: The coated or uncoated silicon steel is then cut into specific shapes and sizes accordingto the requirements of the end products. This may involve processes such as shearing, punching, or laser cutting.8. Quality control: Throughout the production process, strict quality control measures are implemented to ensure that the non-oriented silicon steel meets the required specifications and standards. This includes testing the material for its magnetic properties, electrical resistance, and mechanical strength.中文回答:无取向硅钢的生产工艺和设备在保证最终产品的质量和性能方面起着至关重要的作用。
无取向电工钢(硅钢)生产流程[S]、[C]、[N]的控制教材
![无取向电工钢(硅钢)生产流程[S]、[C]、[N]的控制教材](https://img.taocdn.com/s3/m/73071f07a300a6c30c229f8f.png)
NERC-CCT
—— 电工钢中[S]对磁性能的影响
钢中[S]含量增加,铁损增加,存在铁损急剧增加的[S]含 量,由此,电工钢中[S]控制成分为小于50ppm。
NERC-CCT
—— 电工钢中[N]对磁性能的影响
[N]含量在25ppm以上时,铁损急剧增加,由此,钢中[N] 含量控制应以25ppm为极限。
NERC-CCT
二、转炉流程生产无取向电工钢的关键工序
关键工序与任务: 铁水预处理工序,脱[S]、控制[N]; 转炉冶炼工序,脱[C]、脱[N]、控[S]; RH 精炼工序,脱[C]、脱[S]、控[N]; 连铸工序,控[C]、控[N]、控[S]。
NERC-CCT
—— 转炉流程脱硫工序的选择
1)铁水脱硫的优点:
—— 铁水中碳、硅含量高,提高了硫的反应能力, 从而有利于脱硫; —— 铁水中氧含量低,提高了渣-铁之间的硫分配 比,脱硫效率高; —— 铁水脱硫因其较好的动力学条件,脱硫剂利用 率高,而且脱硫速度快; —— 铁水脱硫费用低,如高炉、转炉、炉外精炼每 脱除1kg硫,其费用分别约为铁水脱硫的2.5倍、16 倍和6倍。
氮在α-Fe、γ –Fe、 δ –Fe、液态铁中的溶解度
氮在铁液中的溶解度
氮在铁中的溶解度
NERC-CCT
② 合金元素含量对氮在铁液中溶解度的影响
新能源无取向硅钢 生产手册

新能源无取向硅钢生产手册
摘要:
1.新能源无取向硅钢概述
2.新能源无取向硅钢的生产流程
3.新能源无取向硅钢的市场需求
4.新能源无取向硅钢的未来发展趋势
5.国内主要新能源无取向硅钢生产企业
正文:
一、新能源无取向硅钢概述
新能源无取向硅钢是一种高牌号、高品质的硅钢产品,主要用于新能源汽车驱动电机的生产制造。
随着我国新能源汽车市场的爆发式增长,新能源无取向硅钢的市场需求也日益旺盛。
二、新能源无取向硅钢的生产流程
新能源无取向硅钢的生产流程主要包括原料准备、熔炼、热轧、冷轧、退火、绝缘涂层等环节。
其中,熔炼环节是生产无取向硅钢的关键,需要严格控制熔炼温度、熔炼时间以及合金元素的加入顺序等参数。
三、新能源无取向硅钢的市场需求
在我国新能源汽车市场的推动下,新能源无取向硅钢的市场需求呈现快速增长态势。
据相关统计数据显示,2021 年我国新能源无取向硅钢的主流钢厂销量约为35 万-38 万吨,市场规模不断扩大。
四、新能源无取向硅钢的未来发展趋势
随着新能源汽车的高速发展以及驱动电机技术的不断提升,新能源无取向硅钢的未来发展趋势可观。
未来的发展方向将主要集中在提高硅钢的性能、降低生产成本以及提高生产效率等方面。
五、国内主要新能源无取向硅钢生产企业
目前,我国新能源无取向硅钢的主要生产企业有包钢股份、望变电气等。
本钢薄板坯连铸机生产无取向电工钢的工艺优化

本钢技术年第期16 20115本钢薄板坯连铸机生产无取向电工钢的工艺优化佟亚男(本钢炼钢厂,辽宁本溪 117021)摘 要:针对本钢薄板坯铸机在生产无取向电工硅钢的过程中存在的铸坯拉断、中包增碳、增氮等问题,进行了连铸工艺优化。
通过采用新型无碳中间包覆盖剂、环保中间包干式料及专用结晶器保护渣后,降低了铸坯增碳量;通过控制钢包到中间包的增氮环节,降低钢水增氮;适当增大二冷水量,控制钢水过热度,防止铸坯拉断等生产事故的发生。
改进工艺后,精炼后到成品铸坯的平均增碳量能控制在10×10-6以内,平均增氮量能控制在4×10-6以内。
关键词:薄板坯连铸;无取向电工硅钢;增氮;增碳;工艺优化中图分类号:TF777 文献标识码:BTechnology Optimization of Producing Non-oriented Silicon Steel by BX STEELThin Slab CasterTONG Yanan(Steel Making Plant.,BX STEEL,Benxi Liaoning 117021)Abstract:The technology optimization has been adopted for preventing nitrogen increasing and carbonincreasing in Benxi thin slab producing non-oriented silicon steel. Measures accordingly were adopted andsatisfactory results were achieved.Keywords:thin slab casting;Non-oriented Silicon Steel;nitrogen increasing;carbon increasing;technologyoptimization本钢薄板坯铸机自2004年投产以来,现已具有年产280万t的生产能力,并生产出包括包晶钢、硅钢等在内的九大类钢种,其中硅钢生产的最高牌号50BW330,硅含量达到3.2 %。
无取向硅钢 生产工艺
无取向硅钢生产工艺无取向硅钢是一种特殊的硅钢材料,它在电力工业、电子工业、军工行业等领域中具有广泛的应用。
无取向硅钢的生产工艺是关键,下面我们来详细介绍一下。
无取向硅钢是一种冷轧电工钢板,由于其特殊的晶粒结构,具有较低的磁滞损耗和铁损耗,使得它在电机、变压器等电气设备中的应用十分重要。
无取向硅钢的生产工艺主要包括原材料准备、热处理、冷轧、退火、磁化等环节。
首先是原材料准备。
生产无取向硅钢的主要原材料是硅钢卷和冷轧钢板。
硅钢卷是通过高温处理的硅钢带制成的,具有较高的硅含量和较小的晶粒尺寸,冷轧钢板则是经过冷轧工艺后制成的。
这两种原材料的选择和质量对于生产无取向硅钢具有重要意义。
接下来是热处理环节。
热处理可以使硅钢卷的硅原子分布更加均匀,晶粒尺寸变小,从而增加硅钢卷的磁导率和磁饱和感应强度。
一般情况下,热处理温度在1100℃左右,时间在1小时左右。
然后是冷轧。
冷轧是无取向硅钢生产工艺中最重要的环节之一。
通过冷轧工艺可以进一步减小硅钢卷的晶粒尺寸,提高硅钢卷的磁导率和磁饱和感应强度。
冷轧后的无取向硅钢板表面平整度高、尺寸精度高、厚度均匀、硬度适中,可以满足各种电工设备的需要。
接着是退火。
退火是为了消除冷轧过程中产生的应力和晶界能量,使得硅钢板的晶粒尺寸进一步减小,提高硅钢板的磁导率和磁饱和感应强度。
退火温度在800℃左右,时间在1小时左右。
最后是磁化。
磁化是为了使无取向硅钢板的磁化强度达到要求。
磁化过程中需要控制磁场方向、大小和磁化时间等参数,以保证磁化效果符合要求。
无取向硅钢的生产工艺非常复杂,需要各个环节的严格控制。
只有通过完善的生产工艺,才能生产出优质的无取向硅钢板,为电气设备的发展做出贡献。
包钢无取向硅钢生产线生产工艺解析
包钢无取向硅钢生产线生产工艺解析硅钢是指含硅量在0. 5% ~ 4. 5% 左右的硅铁合金,是电力、电子和军事行业不可缺少的重要软磁合金,被称为钢铁产品中的“艺术品”。
经过对包钢薄板厂20万t硅钢生产工艺的探索与总结,钢板清洗质量、退火炉退火温度、涂覆膜厚度等因素,是影响硅钢成品性能的关键因素.优化前清洗段的清洗质量是降低炉辊结瘤概率的有效手段.保证退火炉的退火温度在750~950℃是细化钢板晶粒,调整组织,消除组织缺陷的核心工艺.涂覆膜均匀、厚度合理,保证在3.2~3.5 g/m2,是确保硅钢片免受各种腐蚀介质的侵蚀的重要措施。
1、硅钢生产工序铁水预脱硫处理→转炉冶炼→RH 处理→薄板坯连铸连轧→酸洗→冷轧→连续退火→涂层→卷取( 取样检验) →包装出厂在硅钢生产末段,即退火、涂层段,是直接决定硅钢成品的性能好坏及成品等级的阶段,如何管控好相应的工艺变得尤为重要。
2、退火涂层工艺解析2.1 前清洗段硅钢生产线主要控制的是退火与涂层两部分。
然而,在冷轧原料进入退火炉退火前,由于生产环境的不同,硅钢原料表面不可避免的包含一些污染物,这些污物主要包括:轧制过程中残留的乳化液、润滑油和铁粉,以及在冷硬卷存放过程中产生的锈和落上的尘土。
因此,必须对板带进行清洗,否则将严重影响最终成品表面质量,从而影响成品等级。
硅钢生产线在退火炉前专门设置了前清洗段,并且针对不同性质的杂质,设计不同种类的清洗介质,做到对症下药,有的放矢。
硅钢线前清洗段的清洗结构与清洗原因如下所述:前清洗段的布置结构依次为:碱浸洗段、碱刷洗段、电解清洗段、水刷洗段、水浸洗段、水漂洗段。
各段针对不同性质的杂质,分类清洗,主要清洗原理是:(1) 乳化液、润滑油:利用清洗液中NaOH的皂化反应初步去除板面上植物性油脂,在利用活性剂成分初步去除板面上的矿物性油脂。
结合刷洗和电解清洗深层次去除钢带表面的油脂。
(2) 铁粉:利用刷洗初步去除钢带外层的铁粉,利用电解清洗深层次去除钢带表面的铁粉。
无取向电工钢的流程
无取向电工钢的流程下载温馨提示:该文档是我店铺精心编制而成,希望大家下载以后,能够帮助大家解决实际的问题。
文档下载后可定制随意修改,请根据实际需要进行相应的调整和使用,谢谢!并且,本店铺为大家提供各种各样类型的实用资料,如教育随笔、日记赏析、句子摘抄、古诗大全、经典美文、话题作文、工作总结、词语解析、文案摘录、其他资料等等,如想了解不同资料格式和写法,敬请关注!Download tips: This document is carefully compiled by the editor. I hope that after you download them, they can help yousolve practical problems. The document can be customized and modified after downloading, please adjust and use it according to actual needs, thank you!In addition, our shop provides you with various types of practical materials, such as educational essays, diary appreciation, sentence excerpts, ancient poems, classic articles, topic composition, work summary, word parsing, copy excerpts,other materials and so on, want to know different data formats and writing methods, please pay attention!无取向电工钢是一种重要的电工材料,在电气行业中得到广泛应用。
新能源无取向硅钢 生产手册
新能源无取向硅钢生产手册摘要:一、新能源无取向硅钢概述二、生产工艺与流程1.原料准备2.熔炼与铸造3.轧制与退火4.冷轧与退火5.热轧与退火6.成品处理与检验三、设备与技术要求四、产品质量与性能指标五、新能源无取向硅钢的应用领域六、行业现状与未来发展正文:一、新能源无取向硅钢概述新能源无取向硅钢,作为一种具有优良磁性能和良好加工性能的金属材料,广泛应用于新能源、电力、电子等领域。
其生产过程涉及到多个环节,从原料准备到成品处理,每一个环节都需要严格把控,以保证产品的质量和性能。
二、生产工艺与流程1.原料准备新能源无取向硅钢的生产首先需要准备合格的原料,主要包括硅铁、废钢、石灰石等。
这些原料需要经过严格的化学成分分析和物理检测,确保满足生产要求。
2.熔炼与铸造将准备好的原料放入炼钢炉中进行熔炼,熔炼过程中需要严格控制温度和炉内气氛,以防止氧化和污染。
熔炼完成后,将钢水倒入铸造模具中,形成铸坯。
3.轧制与退火铸坯经过轧制,逐步减小厚度,提高表面质量。
轧制过程中需严格控制轧制力、速度和温度,确保产品性能。
轧制完成后,进行退火处理,以消除内应力和改善组织结构。
4.冷轧与退火退火后的板材进行冷轧,冷轧过程中需严格控制轧制力和速度,以保证产品的厚度和平整度。
冷轧完成后,进行第二次退火处理,进一步消除内应力,提高磁性能。
5.热轧与退火冷轧板材经过热轧,提高厚度,优化表面质量。
热轧过程中需严格控制轧制参数,确保产品性能。
热轧完成后,进行第三次退火处理,提高磁性能。
6.成品处理与检验经过以上工艺流程,新能源无取向硅钢成品制成。
成品处理包括表面清洁、切割、包装等。
最后,对成品进行严格检验,确保产品质量符合标准。
三、设备与技术要求生产新能源无取向硅钢的设备主要包括炼钢炉、轧制设备、退火炉等。
设备应具备高精度、高稳定性、高自动化程度等特点。
技术要求主要包括严格控制熔炼、轧制、退火等环节的参数,以保证产品性能。
四、产品质量与性能指标新能源无取向硅钢的质量与性能指标主要包括磁性能、加工性能、化学成分等。
- 1、下载文档前请自行甄别文档内容的完整性,平台不提供额外的编辑、内容补充、找答案等附加服务。
- 2、"仅部分预览"的文档,不可在线预览部分如存在完整性等问题,可反馈申请退款(可完整预览的文档不适用该条件!)。
- 3、如文档侵犯您的权益,请联系客服反馈,我们会尽快为您处理(人工客服工作时间:9:00-18:30)。
高炉顺行; 高温; 高锰; 高硅。
NERC-CCT
四、转炉工序[C]、[S]、 [N]的控制
4.1
4.2
4.3
转炉冶炼工序脱[C] 转炉冶炼工序脱[N] 转炉冶炼工序控[S]
NERC-CCT
4.1 转炉冶炼工序脱[C]
—— 转炉终点碳、氧的控制:
根据RH真空脱碳原理,要求处理前初始钢水的 [C]和[O]应达到一定的范围,以求最佳脱碳效果。
—— 改进真空脱碳效果的措施
1)提高抽气速度,实行真空快速降压,提高脱碳速度; 2)尽可能加大插入管直径,加大驱动气体流量,增大钢水循环量,提高脱碳 速度; 300 3)强制(吹氧)脱碳。 改进前 250
[C](ppm)
强制(吹氧)脱碳的特点: 可提高初始[C],达到0.04~0.06%; 可降低初始[O],降至250~ 400ppm。 脱碳速度比传统RH脱碳快。
NERC-CCT
2)影响转炉“回硫”的因素分析
——铁水脱[S]扒渣对回硫的影响 ——入炉铁水[S]对回硫的影响 ——废钢种类对回硫的影响 ——石灰中[S]对回硫的影响
12 10 8
Δ [S]*10-5
Al钢废钢方式对Δ [S] 的影响
11
7.3
7.6
6 4 2 0 1 3.2
4.8
2
3 废钢方式
4
[C],ppm
240 220 200 180 160 140 120 100 80 60 40 20 0 0 5 10 15 550mm 650mm 750mm
20
脱碳时间 ,min
不同浸渍管径下脱碳比较
300 250
650mm内径,供气流量90Nm3/h
[C](ppm)
原操作 快速降压
[C](ppm)
改进后
30
处理时间(分)
RH-KTB RH
改进前后的降碳曲线 效果:RH真空脱碳可在15~20分钟之内, 将钢水中的碳降低到(10~15)×10-6 。最佳 脱碳效果可达10ppm。
0
2
4
6
8
10
12
14
16
RH、RH-KTB工艺脱碳曲线
NERC-CCT
③ 金属镁脱硫
金属镁脱硫的基本反应式: Mg(g)+[S]=MgS(s) 主要优点: 脱硫能力强,速度快,脱硫后渣量少、铁损少、热损少; 脱硫反应为放热过程,适应温低铁水脱硫。 主要缺点: 价格昂贵,容易挥发。 措施: 制作成钝化镁粒; 添加CaO进行复合喷吹。
广泛用于喷吹法脱硫工艺
氮在α-Fe、γ –Fe、 δ –Fe、液态铁中的溶解度
氮在铁液中的溶解度
氮在铁中的溶解度
NERC-CCT
② 合金元素含量对氮在铁液中溶解度的影响
C、Si:降低溶解度;
Nb、V、Cr、Mn、Zr、Ti、Al:增加溶解度; Mo、Ni、Co :影响不大。
NERC-CCT
③ 低氮铁水的获得
铁水[N]含量:30~40ppm 低氮铁水的措施:
NERC-CCT
2)铁水脱硫的方法
铁水脱硫可分为四大类:
• • • • 投入法(铺撒法) 铁水容器转动法(摇包法) 机械搅拌法(KR法) 喷吹法(鱼雷罐、铁水包)
3)当前最常用的铁水脱硫方法
机械搅拌法(KR)与喷吹法:
KR——日本、韩国等亚洲国家 喷吹法——俄罗斯、中国等国家
NERC-CCT
4)常用铁水脱硫剂
1)
氮在铁中的溶解
在一定温度,1atm大气压下,[N]在钢中存在形式:
间隙固溶体;
—— 自由状态的氮原子,
—— 化合物状态的氮原子,AlN、TiN、ZrN、VN、Fe4N。
2)影响氮在钢中溶解度的元素
铁的状态或晶体结构; 温度与氮气分压; 合金元素含量。
NERC-CCT
① 铁的状态或晶体结构对氮的溶解度的影响
5.1 RH脱碳技术 5.2 RH脱硫技术 5.3 RH处理控氮
部分内容源于余志祥教授讲学
NERC-CCT
5.1 RH脱碳技术
真空条件下脱碳行为的特点:
① 决定真空脱碳速度的主要参数之一是体积传质系数 ak , 与真空室截面(Av)、钢水循环量(Q)及钢水碳含量(Cv)成正比: ak ∝ Av0.32 . Q1.17 . Cv1.48; ② RH真空脱碳速度的限制环节是钢水侧碳和氧的传质阻力, [%C ] 0.66 由碳扩散向氧扩散转变的临界条件为: [% O]
副 枪 一 硫
终 点 硫
到 Ar 站 硫
Ar 站 结 束 硫
成 品 硫
NERC-CCT
3)控制转炉回硫的主要措施
扒除脱硫后铁水面上的脱硫渣; 选用低硫废钢; 控制转炉炉料中硫含量,严格相关技术标准; 选择回硫稳定的脱硫工艺。
NERC-CCT
五、RH精炼工序[C]、[S]、 [N]的控制
NERC-CCT
—— 电工钢中[Mn]对磁性能的影响
钢中[Mn]的作用: 1、形成MnS,防止FeS引起的热脆; 2、扩大γ相区; 3、Mn/S≥10,保证良好热加工性能和MnS粗化; 4、改善组织和织构。
NERC-CCT
—— 电工钢中[Al]对磁性能的影响
钢中Als的作用: 1、Als≥0.15%,其作用与Si的作用相同,提高ρ值,缩小γ相区, 促进晶粒长大,粗化AlN,改善织构,减轻时效; 2、Als在50~140ppm,P15显著增加; 3、 Als≤30ppm, P15显著降低;
③ 当钢水[C]≤0.05%进行脱碳时,脱碳速度的限制性环节为 碳在钢液侧的扩散,反应速率可表达为:
d [% C ] F D ([% C ] [% C ]P ) dt V
NERC-CCT
—— 脱碳影响因素的分析
插入管直径对脱碳速度的影响: 脱碳速度随插入管内径的增大而增大; 循环量Q与插入管内径d4/3成正比。最大限 度延长内径为700~750mm的时间段。 真空降压制度对脱碳的影响 快速降压可加大脱碳速度; 其脱碳速度增大主要体现在脱碳的前5分钟内。
• 形成CO、O2气泡、惰性气体Ar气 泡为氮的去除创造良好条件; • 转炉终点氮含量可达:10~15ppm。
新日铁八幡厂氧气转炉炼钢过程[N]的变化
NERC-CCT
—— 氧气流量对转炉终点[N]的影响
—— 渣层厚度对转炉终点[N]的影响
NERC-CCT
4.3 转炉冶炼工序控[S]
1)转炉吹炼过程“回硫”的控制
0.5×2
0.3~0.5 30~60
喷吹速度/kg· min-1
6~15
NERC-CCT
脱硫效果:
o [S]≤0.005%的比例达到9.92%; o [S]平均为0.003%; o [S]最低可控制到0.002%以下;
o “深脱”的平均脱硫率达到90%。
NERC-CCT
3.2 铁水预处理控[N]
NERC-CCT
—— 电工钢中[S]对磁性能的影响
钢中[S]含量增加,铁损增加,存在铁损急剧增加的[S]含 量,由此,电工钢中[S]控制成分为小于50ppm。
NERC-CCT
—— 电工钢中[N]对磁性能的影响
[N]含量在25ppm以上时,铁损急剧增加,由此,钢中[N] 含量控制应以25ppm为极限。
200 150 100 50 0 0 5 10 15
350 300 250 200 150 100 50 0 0
插入管供气流量90Nm3 /h
550mm 650mm 720mm 750mm
处理时间(min)
20
5
10
处理时间(min)
15
20
快速降压前后的降碳曲线
不同插入深度下的脱碳曲线
NERC-CCT
主要缺点:
易吸水,运输和存贮需要采取特殊安全措施; 比较昂贵; 脱硫渣对环境污染较大。
NERC-CCT
② 石灰系脱硫剂
CaO脱硫的基本反应式: CaO(s)+[S]=CaS(s)+[O]
纯CaO的脱硫能力低于CaC2,脱硫速度慢,脱硫效果不 稳定;
添加适量C等反应促进剂,形成复合石灰系脱硫剂,提 高脱硫效率; 提高脱硫效率的主要措施: 加大搅拌 增大反应面积 提高铁水温度 适用于KR机械搅拌脱硫工艺
Central Iron & Steel Research Institute
NERC-CCT
无取向电工钢(硅钢) 生产流程[S]、[C]、[N]的控制
钢铁研究总院 连铸技术国家工程研究中心
仇圣桃
2008.11
目
录
一、 [C]、[S]、 [N]对无取向电工钢的危害
二、转炉流程生产无取向电工钢的关键工序 三、铁水预处理工序 [S]、 [N]的控制
① 碳化钙系脱硫剂 CaC2脱硫的基本反应式: CaC2+[S]=CaS(s)+2[C] CaC2脱硫能力较强。在动力学条件较好时,最低 [S]可达 0.001%,广泛用于机械搅拌和喷吹脱硫方法; 提高脱硫速度的主要措施包括:减小CaC2粒度、强化搅拌、 提高铁水温度等; 添加适量的碳和CaCO3等成份,形成复合CaC2脱硫剂,有利于 提高脱硫效率。
5
入炉铁水[S]对Δ [S]的影响
0.03
硫含量(%)
0.06 0.05 0.04 0.03 0.02 0.01 0
入 炉 硫
铁水未扒渣与扒渣回硫对比图
未扒渣Q235-B 扒渣Q235-B
0.02
Δ [S] ,%
0.01 0 -0.01 -0.02 -0.03 0 0.01 0.02 0.03 铁水[S],% 0.04 0.05 0.06
铁水脱硫
钢 种
深
中低牌号无取向硅钢 [S]≤ 60 ppm 高牌号无取向硅钢 [S]≤ 50 ppm √ √