换热设备的设计
换热器的选型和设计指南全

换热器的选型和设计指南全
1.温度和压力要求:在进行换热器选型和设计之前,需要明确设备所
需的温度和压力要求。
根据这些要求,可以选择合适的材料和换热器类型。
2.热交换面积计算:根据需要传递的热量和温度差,可以计算得到所
需的热交换面积。
热交换面积的计算是选择换热器类型和尺寸的基础。
3.材料选择:换热器的材料选择要考虑到介质的化学性质、腐蚀性以
及温度和压力要求。
常用的材料包括不锈钢、铜合金、钛合金等。
4.流体流动方式:流体可以采用并行流、逆流或交叉流方式通过换热器。
在选择流体流动方式时,需要考虑换热效率和压降等因素。
5.清洁程度要求:根据介质的清洁程度,可以选择适当的换热器类型。
尽量选择结构简单、易于清洁的换热器,以保证长期稳定的换热效果。
6.管束和散热面积:根据热量传递的需要,可以选择合适的管束形式
和散热面积。
管束的选择要考虑到介质的流速和传热系数等因素。
7.防堵塞设计:在换热器设计中要考虑到防止堵塞的问题。
可以采用
增加管道直径、添加过滤装置等措施来减少堵塞的风险。
8.设备布局和管道设计:在进行换热器的设计时,需要考虑到设备的
布局和管道的连接。
合理布局可以减少管道阻力和热量损失。
9.热媒选择:热媒的选择要根据介质的性质以及工艺流程的要求来进行。
常用的热媒有水、蒸汽、有机液体等。
10.清洗和维护考虑:在进行换热器设计时,要考虑到清洗和维护的
便捷性。
合理的设计可以降低维护成本和停机时间。
管壳式换热器设计总结
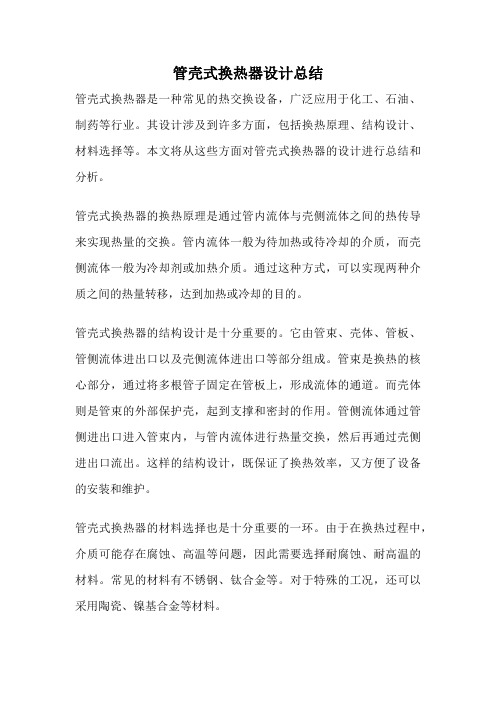
管壳式换热器设计总结管壳式换热器是一种常见的热交换设备,广泛应用于化工、石油、制药等行业。
其设计涉及到许多方面,包括换热原理、结构设计、材料选择等。
本文将从这些方面对管壳式换热器的设计进行总结和分析。
管壳式换热器的换热原理是通过管内流体与壳侧流体之间的热传导来实现热量的交换。
管内流体一般为待加热或待冷却的介质,而壳侧流体一般为冷却剂或加热介质。
通过这种方式,可以实现两种介质之间的热量转移,达到加热或冷却的目的。
管壳式换热器的结构设计是十分重要的。
它由管束、壳体、管板、管侧流体进出口以及壳侧流体进出口等部分组成。
管束是换热的核心部分,通过将多根管子固定在管板上,形成流体的通道。
而壳体则是管束的外部保护壳,起到支撑和密封的作用。
管侧流体通过管侧进出口进入管束内,与管内流体进行热量交换,然后再通过壳侧进出口流出。
这样的结构设计,既保证了换热效率,又方便了设备的安装和维护。
管壳式换热器的材料选择也是十分重要的一环。
由于在换热过程中,介质可能存在腐蚀、高温等问题,因此需要选择耐腐蚀、耐高温的材料。
常见的材料有不锈钢、钛合金等。
对于特殊的工况,还可以采用陶瓷、镍基合金等材料。
在管壳式换热器的设计过程中,还需要考虑一些其他因素。
首先是换热面积的确定,它与换热效果直接相关。
一般来说,换热面积越大,换热效果越好。
其次是流体的流速和流量,它们对换热器的换热效果和压力损失有着重要影响。
此外,还需要考虑到换热器的尺寸和重量,以及设备的安全性和可靠性等方面。
在实际应用中,还需要根据具体的工况和要求进行换热器的定制设计。
例如,在高温高压的条件下,需要采用密封性好、耐高温高压的结构和材料;在对流体的温度变化要求较高的情况下,需要采用多级换热器或增加管程等方式来提高换热效果。
管壳式换热器的设计需要考虑多个方面的因素,包括换热原理、结构设计、材料选择等。
合理的设计可以提高换热效率,降低能耗,满足工业生产的需求。
同时,还需要根据具体的工况和要求进行定制设计,以提高设备的安全性和可靠性。
换热设备典型焊接结构设计分析
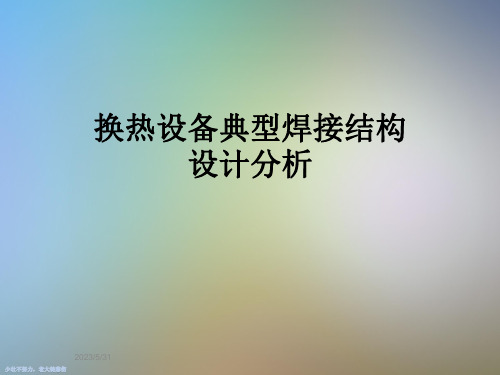
粉或着色),其合格级别为JB4730规定的I级。 注:进行100%无损检测或局部无损检测由标准:GB150、GB151等规
定。 2) 对口错边量b和棱角度E 对口错边量b直接导致结构不连续影响容器的应力分布均匀性。而错边 量b对应力分布的影响,主要取决于b与板厚δ之比b/δ,考虑工艺实现的 可能性,我国标准参照ASMEⅧ-1,按δ的不同,确定b的允许值,且A类 焊缝严于B类焊缝。详见图3-2和表3-1。
5) 焊缝间距
相邻筒体的A类焊缝间的距离,封头上A类焊缝端点与相邻筒体的A类焊 缝间的距离均应大于等于3δn,且大于100mm。
公司要求:200-300mm。在符合标准要求的情况下,尽量小,以利于接 管开孔(不至于开到焊缝上)。
4.换热设备常用焊接结构
换热设备的焊接接头的设计的合理性是保证其制造、运行安全可靠的基本 条件。换热装备焊接结构较常见的典型接头型式有:
度的场合。要求补强圈与壳体紧密贴合,并应有M10的讯号孔。
图4-5 有补强圈的T型接头
ቤተ መጻሕፍቲ ባይዱ
4.3 接管与法兰的焊接接头
钢制法兰与接管的连接,有角接和对接两种,如图4-6所示。角接结构主要 用于工作压力≤2.5MPa的容器,对接一般用于较高工作压力容器。铝、 铜制容器,主要采用活套法兰如图4-7所示。
图4-6 接管与法兰的焊接接头
加工和焊透,以最大限度地减少焊接缺陷。 4) 按等强度要求,接头的强度应不低于母材标准规定的强度下限值。 5) 焊缝外形应尽量连续、圆滑过渡,以减少应力集中。
3.压力容器焊缝形式及分类 3.1 压力容器焊接接头形式
板式换热器设计标准

板式换热器设计标准1. 引言板式换热器是一种常用的热交换设备,广泛应用于化工、石油、冶金、食品等行业。
板式换热器的设计标准对于确保设备的安全运行和高效传热至关重要。
本文将介绍板式换热器的设计标准及其要求。
2. 设计标准2.1 板式换热器的分类根据传热方式和结构特点,板式换热器可分为传统板式换热器、起泡器板式换热器、波纹板式换热器等几种类型。
不同类型的板式换热器具有不同的设计标准和要求。
2.2 设计原则板式换热器的设计应遵循以下原则:•确定换热器的传热面积和传热系数;•选择合适的流体流速;•确定板式换热器的结构参数,如板间距、板高度等;•确保换热器的压力临界条件;•确定板式换热器的材料和密封方式。
2.3 流体参数在板式换热器设计中,需明确各流体的流速、温度、压力等参数。
流体参数的选择应基于设备的工作条件、传热要求和流体特性。
2.4 热平衡板式换热器的设计应满足热平衡要求,即传热面积上的热量输入等于输出。
为了确保热平衡,设计中需考虑传热系数、流速、管道布局等因素。
3. 设计要求3.1 板式换热器的传热效率板式换热器的传热效率是评估设备性能的重要指标。
设计时,需保证传热效率达到要求,并有效避免传热表面的堆积和腐蚀。
3.2 设备的安全运行板式换热器的设计应保证设备在正常工况下的安全运行。
设计中需考虑压力、温度、流速等因素,以确保设备的安全稳定运行。
3.3 板式换热器的清洁和维护为了保证板式换热器的正常运行,设计时应考虑清洁和维护的便捷性。
合理的板间距设计和换热板结构可以减少杂质的积聚,便于清理和维护。
3.4 设备的节能性在板式换热器设计中,节能是一个重要目标。
合理选择流体参数、优化换热结构和提高传热系数等措施可以提高设备的节能性能。
4. 结论板式换热器的设计标准包括设备分类、设计原则、流体参数、热平衡等要求。
合理的设计标准可以提高设备的传热效率、安全稳定运行、清洁维护和节能性能。
在实际应用中,设计者应根据具体情况,综合考虑各种因素,确保设计符合相关的规范和标准,以达到预期的效果。
换热设备设计换热设备设计

换热设备设计简介换热设备是工业领域中广泛应用的一种设备,用于在流体之间传递热量。
它具有高效、节能的特点,被广泛应用于石化、化工、电力等行业。
本文将介绍换热设备的设计原理和常见类型。
设计原理换热设备的设计原理基于热传导的基本原理。
通过将热源与冷源之间制造一定的传热面积和传热强度,使热量从热源传导到冷源,以达到热量传递的效果。
换热设备的设计需要考虑传热系数、传热面积和流体流动的速度等因素。
传热系数取决于流体的性质和流动状态,传热面积则是根据热量传递的需求来确定。
流体流动的速度要适中,过低可能会导致传热效果不佳,过高则会增加能耗。
常见类型换热设备根据传热的方式可以分为直接传热和间接传热两种类型。
直接传热直接传热是指热源和冷源直接接触,在接触区域内完成热量传递。
常见的直接传热设备有:1.管壳式换热器:管壳式换热器是一种常见的换热设备,由壳体和管束组成。
热源经壳体进入管束,在管束内与冷源进行热量交换。
2.板式换热器:板式换热器由一系列平行排列的金属板组成,热源和冷源交替流过板间隙,完成热量交换。
间接传热间接传热是指热源和冷源通过传热介质进行热量传递。
常见的间接传热设备有:1.蒸发器:蒸发器是一种将液体通过蒸发吸收热量,并将其转化为气体的设备。
热源通过蒸发器与蒸发介质进行热量交换。
2.冷凝器:冷凝器是一种将气体通过冷凝释放热量,并将其转化为液体的设备。
冷源通过冷凝器与冷凝介质进行热量交换。
设计考虑因素在进行换热设备设计时,需要考虑以下因素:1.传热效率:传热效率是评价换热设备性能的重要指标,它取决于换热系数和传热面积。
合理设计传热面积和优化流体流动方式可以提高传热效率。
2.压降:压降是流体在换热设备中流动时产生的压力损失。
过高的压降会增加能耗,因此需要尽量减小压降。
3.材料选择:换热设备需要能够承受高温、高压和腐蚀等环境条件,因此在设计中需要选择耐高温、耐腐蚀的材料。
4.清洗和维护:换热设备在使用过程中会积累污垢,需要定期进行清洗和维护。
翅片管式换热器设计标准

翅片管式换热器设计标准
翅片管式换热器是一种常见的换热设备,广泛应用于化工、石油、电力、冶金
等行业。
其设计标准对于保证换热器的性能和安全具有重要意义。
本文将从设计标准的角度出发,对翅片管式换热器的设计要点进行详细介绍。
首先,翅片管式换热器的设计应符合国家相关标准,如《换热设备设计规范》GB 50661-2011等。
在设计过程中,应充分考虑换热器的工作条件、介质特性、换
热面积、流体流速等因素,确保设计符合标准要求。
其次,对于翅片管式换热器的翅片设计,应注意翅片的材质选择、形状结构、
间距等参数。
翅片的材质应具有良好的导热性能和耐腐蚀性能,常见的材质有铝合金、不锈钢等。
翅片的形状结构应合理设计,以增大传热面积,提高换热效率。
同时,翅片之间的间距也需经过合理计算,以确保介质在换热过程中的流体动力学性能。
另外,换热器管束的设计也是关键的一环。
管束的布置应符合流体介质的流动
特性,避免出现流阻过大、流动不均匀等问题。
管束的材质选择和尺寸设计也需要根据实际工况进行合理的选择,以确保管束在工作过程中具有良好的强度和稳定性。
此外,在翅片管式换热器的设计过程中,还需要考虑换热器的清洗和维护便利性。
合理的设计应考虑到换热器内部的结构,以便于清洗设备、维修设备等工作的进行,保证换热器的长期稳定运行。
总之,翅片管式换热器的设计标准涉及多个方面,需要综合考虑换热器的工作
条件、介质特性、材质选择、结构设计等因素。
只有严格按照设计标准进行设计,才能保证换热器具有良好的换热性能和安全稳定的运行。
换热器设备规范标准最新
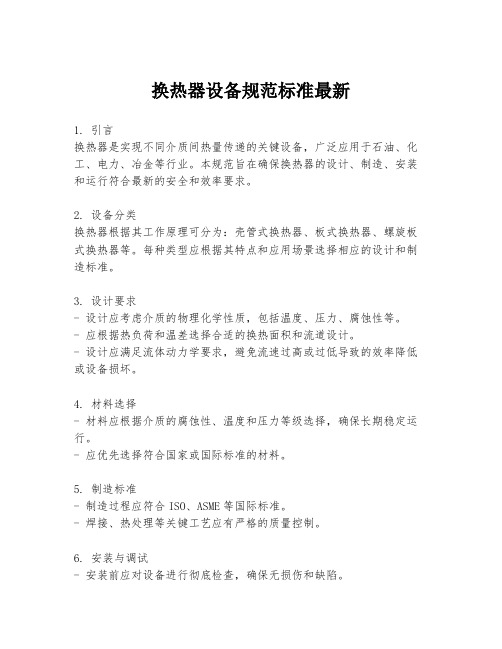
换热器设备规范标准最新1. 引言换热器是实现不同介质间热量传递的关键设备,广泛应用于石油、化工、电力、冶金等行业。
本规范旨在确保换热器的设计、制造、安装和运行符合最新的安全和效率要求。
2. 设备分类换热器根据其工作原理可分为:壳管式换热器、板式换热器、螺旋板式换热器等。
每种类型应根据其特点和应用场景选择相应的设计和制造标准。
3. 设计要求- 设计应考虑介质的物理化学性质,包括温度、压力、腐蚀性等。
- 应根据热负荷和温差选择合适的换热面积和流道设计。
- 设计应满足流体动力学要求,避免流速过高或过低导致的效率降低或设备损坏。
4. 材料选择- 材料应根据介质的腐蚀性、温度和压力等级选择,确保长期稳定运行。
- 应优先选择符合国家或国际标准的材料。
5. 制造标准- 制造过程应符合ISO、ASME等国际标准。
- 焊接、热处理等关键工艺应有严格的质量控制。
6. 安装与调试- 安装前应对设备进行彻底检查,确保无损伤和缺陷。
- 安装应严格按照设计图纸和制造商指导进行。
- 调试过程中应监测设备运行参数,确保达到设计要求。
7. 安全与环保- 设备应配备必要的安全装置,如压力释放阀、温度监控器等。
- 应采取措施减少噪音和振动,符合环保要求。
8. 运行与维护- 制定详细的操作规程,确保操作人员正确使用设备。
- 定期对设备进行检查和维护,及时发现并解决问题。
9. 质量保证- 制造商应提供完整的质量保证体系,包括材料证明、工艺流程记录、出厂检验报告等。
10. 附录- 附录包括换热器的典型设计参数、计算方法、故障排除指南等。
11. 结语本规范标准旨在指导换热器的设计、制造、安装和运行,以确保设备的安全、可靠和高效。
建议用户根据具体应用场景和最新技术发展,对本规范进行适当调整和更新。
请注意,上述内容为示例文本,实际的换热器设备规范标准应根据具体的行业标准和法规进行制定。
列管式换热器设计

列管式换热器设计列管式换热器设计⼀、概述1.概述与设计⽅案简介1.1换热器在不同温度的流体间传递热能的装置称为热交换器,简称为换热器。
在换热器中⾄少要有两种温度不同的流体,⼀种流体温度较⾼,放出热量;另⼀种流体则温度较低,吸收热量。
在⼯程实践中有时也会存在两种以上流体参加换热的换热器,但它的基本原理与上述情形并⽆本质上的差别。
换热器是化学⼯业、⽯油⼯业及其它⼀些⾏业中⼴泛使⽤的热量交换设备,它不仅可以单独作为加热器、冷却器等使⽤,⽽且是⼀些化⼯单元操作的重要附属设备,因此在化⼯⽣产中占有重要地位。
由于⽣产中的换热⽬的不同,换热器的类型很多,不同类型的换热器各有优缺点,性能各异。
特别是随着化⼯⼯艺的不断发展,新型换热器不断出现。
在换热器设计中,⾸先应根据⼯艺要求选择适⽤的类型然后计算换热所需传热⾯积,并确定换热器的结构尺⼨。
虽然列管式换热器在传热效率、紧凑性和⾦属耗量等⽅⾯不及某些新型换热器,但它具有结构简单、坚固耐⽤、适应性强、制造材料⼴泛等独特的优点,因⽽在换热设备中仍占有重要的地位。
特别是在⾼温、⾼压和⼤型换热设备中仍占绝对优势。
1.2列管式换热器的选择列管式换热器的应⽤已有很悠久的历史,在化⼯⽣产中主要作为加热(冷却)器,冷凝器、蒸发器和再沸器使⽤。
现在,它被当作⼀种传统的标准换热设备在很多⼯业部门中⼤量使⽤,尤其在⽯油、化⼯、能源设备等部门所使⽤的换热设备中,列管式换热器仍处于主导地位。
按材质分为碳钢列管换热器,不锈钢列管换热器和碳钢与不锈钢混合列管换热器三种。
按结构分为单管程、双管程和多管程,传热⾯积1~500m2。
列管式换热器按结构特点,主要分为以下四种:①固定管板式换热器;②浮头式换热器;③U形管式换热器;④填料函式换热器。
列管换热器主要特点:1.耐腐蚀性:聚丙烯具有优良的耐化学品性,对于⽆机化合物,不论酸,碱、盐溶液,除强氧化性物料外,⼏乎直到100℃都对其⽆破坏作⽤,对⼏乎所有溶剂在室温下均不溶解,⼀般烷、径、醇、酚、醛、酮类等介质上均可使⽤。
- 1、下载文档前请自行甄别文档内容的完整性,平台不提供额外的编辑、内容补充、找答案等附加服务。
- 2、"仅部分预览"的文档,不可在线预览部分如存在完整性等问题,可反馈申请退款(可完整预览的文档不适用该条件!)。
- 3、如文档侵犯您的权益,请联系客服反馈,我们会尽快为您处理(人工客服工作时间:9:00-18:30)。
第六章换热设备的设计6.1 换热设备的分类和总体结构6.1.1 换热设备的分类按照传热方式的不同,换热设备可分为三类:1.混合式换热器——利用冷、热流体直接接触与混合的作用进行热量的交换。
这类换热器的结构简单、价格便宜,常做成塔状。
2.蓄热式换热器——在这类换热器中,热量传递是通过格子砖或填料等蓄热体来完成的。
首先让热流体通过,把热量蓄在蓄热体中,然后再让冷流体通过,把热量带走。
由于两种流体交变转换输入,因此不可避免地存在着一小部分流体相互掺和的现象,造成流体的“污染”。
这类换热器的结构紧凑,价格便宜、单位体积传热面大,故较适合于气—气热交换的场合。
3.间壁式换热器——是工业中最为广泛应用的一类换热器。
冷—热流体被一固体壁面隔开,通过壁面进行传热。
按照传热面的形状与结构特点它又可分为:(1)管式换热器——如套管式、螺旋管式、管壳式、热管式等。
(2)板面式换热器——如板式、螺旋板式、板壳式等。
(3)扩展表面式换热器——如板翅式、管翅式、强化的传热管等。
其中以管式换热器应用作为广泛,其特点见表6-1所示。
表6-1 管壳式换热器的主要类型及特点6.1.2 管壳式换热器的总体结构管壳式换热器的总体结构均包括:管箱、管板、壳体、折流板或支承板、定距管、拉杆、分程隔板、接管、支座等。
如图6-1所示。
图6-1 常见管壳式换热器结构1—平盖;2—平盖管箱(部件);3—接管法兰;4—管箱法兰;5—固定管板;6—壳体法兰;7—防冲板;8—仪表接口;9—补强圈;10—壳体(部件);11—折流板;12—旁路挡板;13—拉杆;14—定距管;15—支持板;16—双头螺柱;17—螺母;18—外头盖垫片;19—外头盖侧法兰;20—外头盖法兰;21—吊耳;22—放气口;23—椭圆形封头;24—浮头法兰;25—浮头垫片;26—无折边球形封头;27—浮头管板;28—浮头盖(部件);29—外盖头(部件);30—排液口;31—钩圈;32—接管;33—活动鞍座;34—换热管;35—假管;36—管束(部件);37—固定鞍座;38—滑道;39—管箱垫片;40—管箱短节;41—封头管箱;42—分程隔板;43—悬挂式支座;44—膨胀节(部件);45—中间挡板;46—U形换热器;47—内导流筒;48—纵向隔板;49—填料;50—填料函;51—填料压盖;52—浮动管板;53—部分剪切环;54—活套法兰。
6.2管壳式换热设备设计的内容和步骤6.2.1 管壳式换热设备设计的内容管壳式换热设备设计的内容包括工艺设计和机械设计两方面。
本课程设计是把工艺参数、尺寸作为已知条件,在满足工艺条件的前提下,对换热设备进行强度、刚度及稳定性计算,并从制造、安装、检修、使用等方面出发进行结构设计。
换热设备设计任务书内容和格式按表6-2所示。
6.2.2 管壳式换热设备设计的步骤在阅读了设计任务书后,按以下步骤进行换热设备的机械设计。
○1了解设计条件;○2选材;○3按设计压力计算壳体和管箱壁厚;○4管子与管板连接结构设计;○5壳体与管板连接结构设计;○6管板厚度计算;○7折流板、支持板等零部件的结构设计;○8换热管与壳体在温差和流体压力联合作用下的应力计算;○9管子拉脱离和稳定性校核;○10判断是否需要膨胀节,如需要,则选择膨胀节结构型式并进行有关的计算;○11接管、接管法兰、支座等的选择及开孔补强设计等。
表6-2 换热设备设计任务书比例条件内容修改设计参数及要求修改标记修改内容签字日期壳程管程工作压力,MPa 1.43 1.53设计压力,MPa 1.57 1.68工作温度,℃310 420设计温度,℃310 420 单位名称介质碱洗气变换气工程名称推荐材料16MnR 20钢设计项目管/壳程数 1 1 条件编号传热面积,m2 70设备图号公称直径,mm 800位号/台数传热管直径,mm 38提出人日期传热管长度,m 3备注传热管根数,根205腐蚀情况微弱设计寿命接管表符号公称尺寸DN 连接面形式用途a 400 凹面变换气b 250 凹面碱洗气c 250 凹面碱洗气d 400 凹面变换气e 1/2”螺纹排水口表6-3 换热设备设计任务书简图与说明设计参数及要求壳程管程工作压力,MPa 1.43 1.53设计压力,MPa 1.57 1.68工作温度,℃310 420设计温度,℃310 420 介质碱洗气变换气管/壳程数 1 1 传热面积,m2 70公称直径,mm 800传热管直径,mm 38传热管长度,m 3传热管根数,根205腐蚀情况微弱设计寿命接管表符号公称尺寸DN 连接面形式用途a 400 凹面变换气b 250 凹面碱洗气c 250 凹面碱洗气d 400 凹面变换气e 1/2”螺纹排水口6.3 换热设备的设计示例6.3.1 管壳式换热器某合成氨厂变换工段中变换热器,系卧式固定管板式的管壳式换热器,如图6-2所示,其壳程圆筒内径为800mm 。
换热管规格为φ38×3的无缝钢管,共205根,管长3m 。
工作条件:壳程介质为碱洗液(脱碳后的氮氢混合气),压力为1.43Mpa ,最高温度为310℃;管程介质为变换气(含有二氧化碳的氮氢混合气),压力为1.53Mpa ,最高温度为420℃。
有工艺计算得沿长度平均的壳程圆筒金属温度为274℃,换热管金属温度为350℃。
试对该换热器进行材料选择、结构设计及强度计算。
结构草图如图6-2所示,下面分别进行壳程圆筒、管箱封头及圆筒、法兰、管板,以及U 形膨胀节设计及计算。
图6-2 卧式带膨胀节的固定管板换热器1—变换气入口接管;2—锥形封头;3—设备法兰;4—管板;5—碱洗气出口接管;6—补强圈;7—筒体;8—膨胀节;9—换热管;10—定距管;11—折流板;12—碱洗气入口接管; 13—变换器出口接管;14—鞍式支座。
6.3.1.1 壳程圆筒根据工作条件选择壳程圆筒的材料为16MnR 钢板。
在常温时许用应力为170Mpa ,在设计温度310℃时的许用应力为142MPa ,屈服限为227Mpa 。
按GB150-98式(6-1)壳程圆筒计算厚度 []c i tcp D 2P δσφ=- (6-1)式中 计算压力c P 1.1 1.43 1.57MPa =⨯=; 内直径i D 800mm =材料许用应力[]t142MPa σ=焊缝系数φ=0.85(采用双面焊、局部无损探伤)以上数值代入式(6-1)得1.578005.24mm 21420.85 1.57δ⨯==⨯⨯-按GB150-98碳素钢或低合金钢容器的最小厚度不小于3mm ,该厚度值不包括厚度附加量C=2mm 即e 6mm δ=。
壳程圆筒的液压试验及压力试验时应力校核。
试验液体为水,试验压力PT 按下式[][]T t 170P 1.251.25 1.572.35MPa 142σσ==⨯= 压力试验时,圆筒的总体薄膜应力按下式()()T i e T ts e P D 2.3580061850.90.9227204.3MPa 2260.85δσσδφ++===<=⨯⨯⨯⨯6.3.1.2 管箱(1)锥形封头如图6-2所示为带折边锥形封头,根据工作条件选择锥形封头材料为15CrMoR (正火加回火)钢板。
在常温时许用应力为150MPa ,在设计温度420℃时的许用应力为115.6MPa ,屈服限为229.4MPa 。
图6-3 锥形封头按GB150-98式(6-10),式(6-11) 过渡段厚度[]'c ih tckP D 20.5P δσφ=- (6-10)与过渡段相接处的锥壳厚度 []'c ih tcfP D 0.5P δσφ=- (6-11)式中 计算压力Pc=1.1×1.53=1.68MPa 内直径Di=800mm材料许用应力[σ]t=115.6MPa焊缝系数φ=0.85(采用双面焊、局部无损探伤)系数K=0.682(采用标准封头r/D i =0.15, α=30℃)f=0.554(同上)K 、f 值分别由GB0-98表6-4、表6-5查得。
以上数值代入式(6-10)、式(6-11)得 'h 0.682 1.688004.70mm 2115.60.850.5 1.68δ⨯⨯==⨯⨯-⨯'h 0.554 1.688007.64mm 115.60.850.5 1.68δ⨯⨯==⨯⨯-⨯取h 7.7mm δ=,附加厚度c=2mm 选取he 10mm δ= 锥形封头的水压试验压力[][]T ct 150P 1.25P 1.25 1.682.27MPa 115.6σσ==⨯= 壳程圆筒和封头计算参见GB150-98。
(2)管箱法兰选JB/T4703-2000长颈对焊法兰PN=2.5MPa ,DN800,材料为15CrMo 。
法兰密封面型式为凹凸面,连接尺寸(参阅图6-4)如下: D i =800mm δ0=16mm D b =915mm δ1=26mm D f =960mm H=115mmD 4=863mmδf =52mm (不包括厚度附加量)垫片采用金属包垫片865×825JB/T4706-200由GB150-98表9-2查得m=3.75,y=52.4MPa 选32个材料为35CrMoA 等长双头螺栓M24×160JB/T4707-2000。
○1螺栓计算 预紧状态下需要的最小螺栓载荷按式GB150-98式(9-4)计算: a a G W F 3.14D by ==(6-12)式中 垫片有效密封宽度b垫片接触宽度865825N 20mm 2-== 按GB150-98表9-1得垫片基本密封宽度0N 2010mm 22b ===由于b>6.4mm 则b 8mm ===垫片压紧力中心直径G 4D D 2b 86328847mm =-=-⨯=垫片比压力y=52.4MPa (见GB150-98表9-2) 以上数值代入式(9-2)得6a W 3.14847852.4 1.11510N =⨯⨯⨯=⨯操作状态下需要的最小垫片压紧力按GB150-98式(9-5)计算: 2p p G c G c W F F 0.785D P 6.28D bmP =+=+(6-13)式中 由上已知b=8mm ,DG=847mm 垫片系数m=3.75管程设计压力p=1.68MPa以上数值代入式(9-5)得2p 666W 0.785847 1.68 6.288478 3.75 1.680.946100.26810 1.21410=⨯⨯+⨯⨯⨯⨯=⨯+⨯=⨯预紧状态下需要的最小螺栓面积按GB150-98式(9-6)计算:[]aa b W A σ=(6-14)操作状态下需要的最小螺栓面积按GB150-98式(9-7)计算: []pp tbW A σ=(6-15)式中常温下螺栓材料许用应力[σ]b=228MPa 在设计温度420℃下螺栓材料许用应力[]tb 163.6MPa σ=代入式(9-6)、式(9-7)得62a 1.11510A 4890mm 228⨯==62p 1.21410A 7420.5mm 163.6⨯==需要的螺栓面积2m p A A 7420.5mm ==实际螺栓面积()22b 002A n d d 20.75mm 320.78520.75410815.73mm π=⋅==⨯⨯=b m A A >所需螺栓面积足够。