第1章 绪论(精密与特种加工)最新
精密与特种加工

精密与超精密加工技术
表7-3 几种典型精密零件的加工精度
零件
激光光学零件 多面镜
加 工 精 度
形状误差 0.1μm 平面度误差 0.04μm
表面粗糙度
Ra 0.01~0.05μm Ra <0.02μm
磁头
磁盘 雷达导波管
平面度误差 0.04μm
波度 0.01 ~0.02μm 平面度垂直度误差 < 0.1μm
精密与超精密加工技术
金刚石晶体的面网距和解理现象 ◎金刚石晶体的(111)晶面面网密度最大,耐磨性最好。
◎(100)与(110)面网的面间距分布均匀;(111)面网 的面间距一宽一窄(图) ◎ 在 距 离 大 的 ( 111 ) 面之间,只需击破一个 共价键就可以劈开,而 在 距 离 小 的 ( 111 ) 面 之间,则需击破三个共 价键才能劈开。
精密与特种加工
绪
论
一、精密与特种加工在制造业中 的地位与作用
• 精密加工 • 特种加工
二、课程性质和任务
第一章 精密切削加工
§1-1 概述
一、精密加工及其关键技术简介
• 精密加工及其重要性 • 精密加工关键技术 精密加工机床、金刚石刀具、 精密切削机理、稳定的加工环境、 误差补偿、精密测量技术
二、精密切削加工分类 三、精密加工与经济性
Ra <0.02μm
Ra <0.02μm Ra <0.02μm
卫星仪表轴承
天体望远镜
圆柱度误差 <0.01μm
形状误差 < 0.03μm
Ra <0.002μm
Ra <0.01μm
精密与超精密加工技术
102 加工误差(μm) 101 加工设备 车床,铣床 测量仪器 卡尺 百分尺 比较仪
精密加工1章绪论ppt课件

10
• 超精密加工:加工精度(尺寸和形状)高于0.1µm,加工表面粗
糙度小于Ra0.01µm之间的加工方法称为超精密加工。
• 如果在加工中能以原子级为单位去除被加工材料,即是加工的极
限,从这一角度来定义,可以把接近于加工极限的加工技术称为 超精密加工,也称纳米加工。
精选ppt
11
不同时期的精密和超精密加工精度
非金属材料 高分子材料 复合材料 无机硬脆材料
应用:光学、化学、电子 应用:航天、能源工业 应用:电子、原子能、能源
精选ppt
21
一、国防工业上的需求及应用
超精密加工技术与国防工业关系密切,如陀螺仪的加工涉及多项超精 密加工,导弹系统的陀螺仪质量直接影响其命中率,1kg的陀螺转子, 其 质 量 中 心 偏 离 其 对 称 轴 0.0005μm , 则 会 引 起 100m 的 射 程 误 差 和 50m的轨道误差。
高刚度化; 冷却、空调、防振;
镜 树脂结合剂金刚石砂
面
轮添加Mo2S2、WS2、 C等;
磨 铸铁基金刚石砂轮采
削 用电解腐蚀修整。
采用高速运算装置控制;
高刚度化的新方案:Tetraform 结构球壳结构
Al、Cu、塑料等软质材 料; 无电解Ni膜Ge,Si KDP、LiNbO3、玻璃
铁氧体 精细陶瓷 超硬合金 Ge、Si 玻璃
刃磨,成形,平面,内圆 平面,外圆,型面,细金属丝,槽 平面
精选ppt
16
四、精密切削、磨削、研磨实例
工具等
加工装置
材料
用途、零件等
金刚石刀具刃口锋利
镜 化;
面 利用CBN刀具切削钢;
切
金刚石刀具得结晶方 位选择;
GW89_特种加工绪论
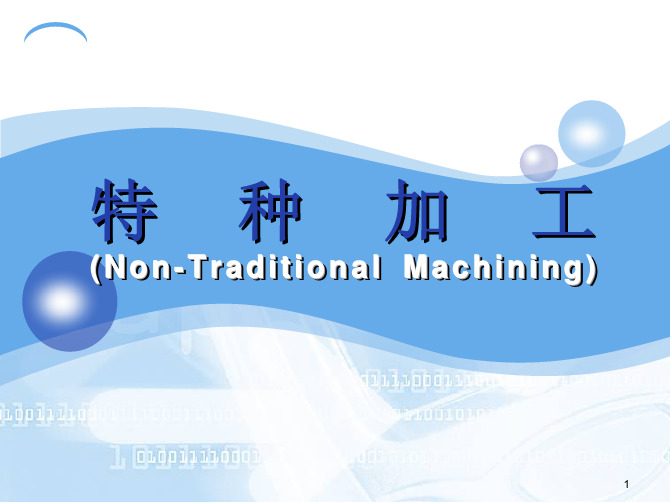
1943年,前苏联莫斯科大学的拉扎林柯夫妇在研 究开关触点(钨合金)遭受火花放电腐蚀损坏时发现 电火花的瞬时高温可以使得局部金属熔化、气化而被 蚀除,同时将开关触点浸没在油内可以使得放电蚀除 均匀并且可以预测大小,获得“以柔克刚”的效果,从 而发明了世界第一台电火花加工机床。
几乎是与此同时,美国人Harold Stark, Victor Harding, and Jack Beaver为了解决取出断在铝制液 压阀门内的钻头和丝攻的问题,也发明了电火花加工 的方法。
⑷.适合微细加工,有些特种加工,如超声、电化学、 水喷射、磨料流等不仅可加工尺寸微小的孔或狭缝, 还能获得高精度、极低粗糙度的加工表面;
⑸.两种或两种以上的不同类型的能量可相互组合形成 新的复合加工形式,加工能量易于控制和转换,加工 范围广,适应性强。
11
1.2 特种加工的分类
特种加工的分类目前还没有明确的规定,一般按能量 来源及形式以及作用原理进行划分。
5
扎连科夫妇试验用的钨开关自动点火系统
6
扎连科夫妇研制的第一台RC电路电火花加工机床
7
“电火花加工”方法的发明,使人类首次摆脱了传统的 以机械能和切削力并且利用比加工材料硬度高的刀具来 去除多余金属的历史,进入了利用电能和热能进行“以柔 克刚”加工材料的时代。于是一种本质上区别于传统加工 的特种加工便应运而生,并不断获得发展。
⑵.“以柔克刚”,特种加工的工具与被加工零件基本不 接触,加工时不受工件的强度和硬度的制约,故可加 工超硬脆材料和精密微细零件,甚至工具材料的硬度 可低于工件材料的硬度;
10
⑶.加工机理不同于一般金属切削加工,不产生宏观切 屑,不产生强烈的弹、塑性变形,故可获得很低的表 面粗糙度,其残余应力、冷作硬化、热影响度等也远 比一般金属切削加工小。
精密加工与特种加工教学大纲5篇
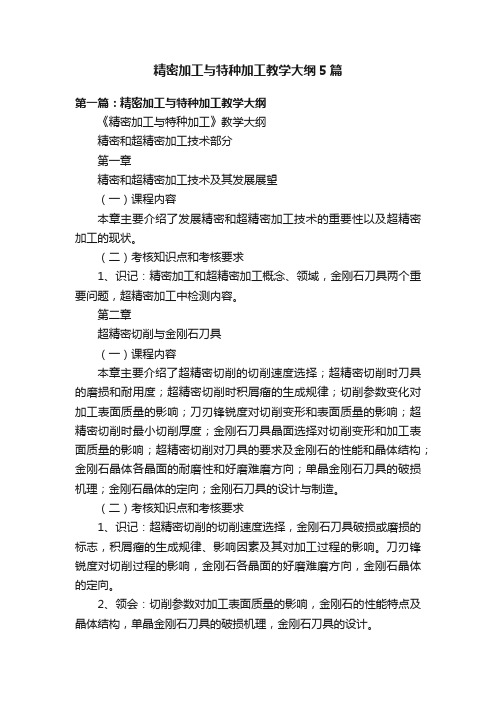
精密加工与特种加工教学大纲5篇第一篇:精密加工与特种加工教学大纲《精密加工与特种加工》教学大纲精密和超精密加工技术部分第一章精密和超精密加工技术及其发展展望(一)课程内容本章主要介绍了发展精密和超精密加工技术的重要性以及超精密加工的现状。
(二)考核知识点和考核要求1、识记:精密加工和超精密加工概念、领域,金刚石刀具两个重要问题,超精密加工中检测内容。
第二章超精密切削与金刚石刀具(一)课程内容本章主要介绍了超精密切削的切削速度选择;超精密切削时刀具的磨损和耐用度;超精密切削时积屑瘤的生成规律;切削参数变化对加工表面质量的影响;刀刃锋锐度对切削变形和表面质量的影响;超精密切削时最小切削厚度;金刚石刀具晶面选择对切削变形和加工表面质量的影响;超精密切削对刀具的要求及金刚石的性能和晶体结构;金刚石晶体各晶面的耐磨性和好磨难磨方向;单晶金刚石刀具的破损机理;金刚石晶体的定向;金刚石刀具的设计与制造。
(二)考核知识点和考核要求1、识记:超精密切削的切削速度选择,金刚石刀具破损或磨损的标志,积屑瘤的生成规律、影响因素及其对加工过程的影响。
刀刃锋锐度对切削过程的影响,金刚石各晶面的好磨难磨方向,金刚石晶体的定向。
2、领会:切削参数对加工表面质量的影响,金刚石的性能特点及晶体结构,单晶金刚石刀具的破损机理,金刚石刀具的设计。
第三章精密磨削和超精密磨削(一)课程内容本章主要介绍了精密和超精密磨削;精密磨削;超硬磨料砂轮磨削;超精密磨削;精密和超精密砂带磨削。
(二)考核知识点和考核要求1、识记:精密和超精密磨料加工方法分类,精密和超精密磨削的特点及其应用,精密和超精密磨削工艺,砂带磨削方式、特点、应用范围及其机理。
2、领会:精密磨削机理,精密磨削与超硬磨料砂轮的修整,超精密磨削机理及其特点。
第四章精密和超精密加工的机床设备(一)课程内容本章主要介绍了精密主轴部件;床身和精密导轨部件;进给驱动系统;微量进给装置;机床的稳定性和减振隔振;减少热变形和恒温控制。
第一章_精密与特种加工绪论
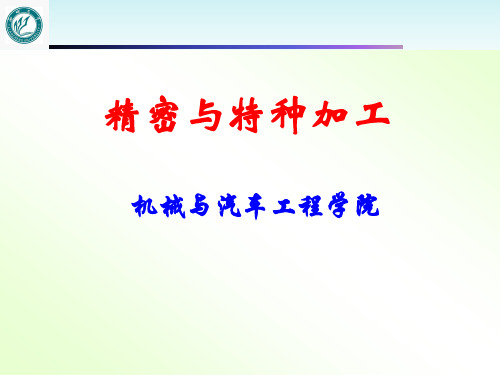
重要方面.在难切削材料、复杂型面、精细零件、低刚度
零件、模具加工、快速原形制造以及大规模集成电路等领 域发挥着越来越重要的作用。
0.1 精密与特种加工在制造业中的地位和作用
三. 精密加工现状
精密加工是指加工精度和表面质量达到极高精度的 加工工艺,通常包括精密切削加工和精密磨削加工, 在不同制造业发展时期其最高技术指标有所不同。
精密与特种加工技术综合地位和作用:
1) 2) 3) 精密与超精密加工和制造自动化是先进制造技术的两大 领域。 先进制造技术已经是一个国家经济发展的重要手段。 发展先进制造技术是当前各国发展国民经济的主攻方向 和战略决策,同时又是一个国家独立自主、繁荣富强、 经济持续稳定发展、科技保持先进领先的长远大计。 精密与特种加工技术水平是一个国家制造工业水平的重 要标志之一。 精密与特种加工技术已经成为国际竞争中取得成功的关 键技术。
0.1 精密与特种加工在制造业中的地位和作用 精密与特种加工技术引起机械制造领域内的变革: ⑴ 提高了材料的可加工性。 ⑵ 改变了零件的典型工艺路线。
⑶ 大大缩短新产品试制周期。
⑷ 对产品零件的结构设计产生很大的影响。 ⑸ 对传统的结构工艺性好与坏的衡量标准产生重 要影响。
0.1 精密与特种加工在制造业中的地位和作用
造面临着一系列严峻的任务(即作用):
0.1 精密与特种加工在制造业中的地位和作用
⑴ 解决各种难切削材料的加工问题。如硬质合金、钛合金、 淬火钢、金刚石、石英以及锗、硅等各种高硬度、高强度、 高韧性、高脆性的金属及非金属材料的加工。 ⑵ 解决各种特殊复杂型面的加工问题。如喷气涡轮机叶片、 锻压模等的立体成型表面,炮管内膛线、喷油嘴和喷丝头 上的小孔、窄缝等的加工。 ⑶ 解决各种超精密、光整零件的加工问题。如对表面质量 和精度要求很高的航天航空陀螺仪、激光核聚变用的曲面 镜等零件的精细表面加工,形状和尺寸精度要求在0.1μm 以上,表面粗糙度Ra要求在0.01μm以下。 ⑷ 特殊零件的加工问题。如大规模集成电路、光盘基片、 微型机械和机器人零件、细长轴、薄壁零件、弹性元件等 低刚度零件的加工。
精密与特种加工技术(课件)【精选文档】

第一章概论第一节精密与特种加工的产生背景机械制造面临着一系列严峻的任务:⑴解决各种难切削材料的加工问题。
⑵解决各种特殊复杂型面的加工问题。
⑶解决各种超精密、光整零件的加工问题。
⑷特殊零件的加工问题。
第二节精密与特种加工的特点及其对机械制造领域的影响精密与特种加工是一门多学科的综合高级技术;精密加工包括微细加工、光整加工和精整加工等,与特种加工关系密切。
特种加工是指利用机、光、电、声、热、化学、磁、原子能等能源来进行加工的非传统加工方法(NTM,Non-Traditional Machining),它们与传统切削加工的不同特点主要有:①主要不是依靠机械能;②刀具的硬度可以低于被加工工件材料的硬度;③在加工过程中,工具和工件之间不存在显著的机械切削力作用。
精密与特种加工技术引起了机械制造领域内的许多变革:⑴提高了材料的可加工性。
⑵改变了零件的典型工艺路线。
⑶大大缩短新产品试制周期.⑷对产品零件的结构设计产生很大的影响。
⑸对传统的结构工艺性好与坏的衡量标准产生重要影响。
第三节精密与特种加工的方法及分类1.加工成形的原理分为去除加工、结合加工、变形加工三大类。
去除加工又称为分离加工,是从工件上去除多余的材料。
结合加工是利用理化方法将不同材料结合在一起。
又可分为附着、注入、连接三种。
变形加工又称为流动加工,是利用力、热、分子运动等手段使工件产生变形,改变其尺寸、形状和性能. 2.加工方法机理按机理精密与特种加工分为传统加工、非传统加工、复合加工。
第四节精密与特种加工技术的地位和作用先进制造技术已经是一个国家经济发展的重要手段之一。
发展先进制造技术是当前世界各国发展国民经济的主攻方向和战略决策,同时又是一个国家独立自主、繁荣富强、经济持续稳定发展、科技保持先进领先的长远大计。
从先进制造技术的技术实质而论,主要有精密、超精密加工技术和制造自动化两大领域。
精密与特种加工技术水平是一个国家制造工业水平的重要标志之一。
江苏自考02213 精密加工与特种加工

2213 精密加工与特种加工第一章概论 P1领会: 精密与特种加工技术基本概念,对材料可加工性和结构工艺性等的影响1.精密与特种加工技术基本概念精密加工含:微细加工、光整加工、精整加工特种加工(NTM):利用机、光、电、声、热、化学、磁、原子能的能源进行加工的非传统加工方法。
2.精密与特种加工对材料可加工性和结构工艺性的影响1)提高了材料的可加工性2)改变了零件的典型工艺路线3)大大缩短新产品试制周期4)对零件结构的设计产生很大的影响5)对传统的结构工艺性好与坏的衡量标准产生重要影响掌握: 精密与特种加工技术分类、应用特点1.按加工成形原理特点分类:1)去除加工(从工件上去除多余材料),分散流;2)结合加工(利用理化方法将不同材料结合在一起,分为附着<电镀、气相沉积>、注入<表面渗碳、离子注入>、连接 <焊接、粘接>),汇合流;3)变形加工——流动加工(利用力、热、分子运动等手段使工件产生变形改变其尺寸、形状、性能<锻造、锻造,液晶定向>),直通流。
2.按加工方法机理分类:传统加工(使用刀具进行切削加工)、非传统加工(利用机、电、声、热、化学、磁、原子能等能源进行加工)、复合加工(采用多种加工方法)3.技术特点:1)不主要依靠机械能,而主要依靠其他能量去除工件材料2)工具的硬度可低于被加工工件材料的硬度,有些不需要工具;3)加工过程中,工具与工件之间没有显著的机械切削力,适合精密加工低刚度零件;4.特种加工技术的应用:1)难切削材料的加工;2)特殊复杂型面的加工;3)各种超精密、光整零件的加工;4)特殊要求零件的加工。
可以加工任何硬度、强度、韧性、脆性的金属、非金属、复合材料,适合于加工复杂、微细表面、低刚度的零件,有些还进行超精密加工、镜面加工、光整加工及纳米级加工。
第二章金刚石刀具精密切削加工 P11领会:精密切削加工方法、种类及其实现条件,超精密机床组成及其关键部件1.超精密加工方法1)按加工方式分为:切削加工、磨料加工<固结磨料、游离磨料>、特种加工、复合加工;2)按机理分类:去除加工、结合加工、变形加工,还可分为传统加工(指利用刀具切削加工、固结磨料和游离磨料加工)、非传统加工(指利用电、磁、声、光、化学、核等能量对材料进行加工处理)、复合加工(多种加工方法结合),目前以切削、磨削、研磨的传统方法占主导。
重庆大学精密与特种加工课件第一章概要
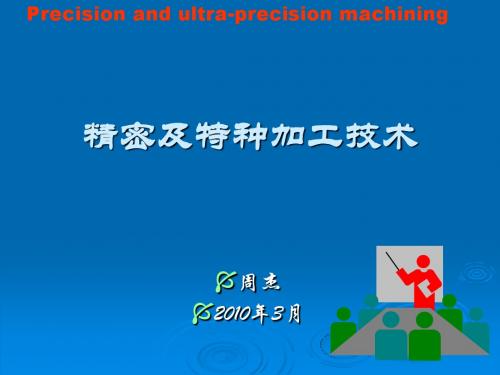
1.4 超精密加工现状及发展趋势
影响精密和超精密加工的因素
被加工材料
用精密和超精密加工的零件,其材料的化学成分、 物理力学性能、加工工艺性能均有严格要求。例如, 要求被加工材料质地均匀,性能稳定,无外部及内部 微观缺陷;其化学成分的误差应在10-2~10-3 数量级, 不能含有杂质;其物理力学性能,如拉伸强度、硬度、 延伸率、弹性模量、热导率和膨胀系数等应达到105~10-6数量级;材料在冶炼、铸造、辗轧、热处理等 工艺过程中,应严格控制熔渣过滤、辗轧方向、温度 等,使材质纯净、晶粒大小匀称、无方向性,能满足 物理、化学、力学等性能要求。 2018/11/12 22
2018/11/12 15
2018/11/12
16
服役的哈勃望远镜
狮子座螺旋星系
2018/11/12
宇宙深处的星体
银河系环形星群
17
1.3 精密和超精密加工的需求
信息产品中的需求 计算机上的芯片、磁板基片、光盘基片等都 需要超精密加工技术来制造。录像机的磁鼓、 复印机的感光鼓、各种磁头、激光打印机的多 面体、喷墨打印机的喷墨头等都必须进行超精 密加工,才能达到质量要求。
应
用
切削加工
熔断钼、钨等高熔点材料,硬质合金 球,磁盘,反射镜,多面棱镜 油泵油嘴,化学喷丝头,印刷电路板 集成电路基片的外圆、平面磨削 平面、空、外圆加工,硅片基片 平面、空、外圆加工,硅片基片 硅片基片 刻槽,切断,图案成形,破碎 孔,沟槽,狭缝,方孔,型腔 切断,切槽 模具型腔,大空,切槽,成形 刻模,落料,切片,打孔,刻槽 在玻璃、红宝石、陶瓷等上打孔 打孔,切割,光刻 成形表面,刃磨,割蚀 打孔,切断,划线 划线,图形成形 刃磨,成形,平面,内圆 平面,外圆,型面,细金属丝,槽 平面
- 1、下载文档前请自行甄别文档内容的完整性,平台不提供额外的编辑、内容补充、找答案等附加服务。
- 2、"仅部分预览"的文档,不可在线预览部分如存在完整性等问题,可反馈申请退款(可完整预览的文档不适用该条件!)。
- 3、如文档侵犯您的权益,请联系客服反馈,我们会尽快为您处理(人工客服工作时间:9:00-18:30)。
课程安排与概述
总 学 时:32(含4学时实验课)
时 间:第8周-第12周 相对松散:精密与超精密加工;特种加工;方法间缺乏 紧密的内在逻辑联系
课程特点:
内容多样:涉及精密超精密加工、多种特种加工方法
基本要素:基本原理、基本工艺特征、主要用途
精密与特种加工技术
2
第一章 绪论
精密与特种加工的产生与特点
案例4:微小或易变形零件/特征的加工(续)
精度:超精密/精密
微型发动机
尺寸:特征尺寸为微纳米
微型麦克风
微型泵
材料:金属或硅
精密与特种加工技术
10
第一章 绪论
精密与特种加工的产生与特点
Miniature 0.1m-0.1mm
MEMS 0.1mm-0.1μm
NEMS 100nm-0.1nm
民
现代小型、超小型的成像设备,如摄相机、照相机等上的各种透镜
用
产 品
,特别是光学曲面透镜,激光打印机、激光打标机等上的各种反射
镜都要靠超精密加工技术来完成。至于超精密加工床、设备和装置 当然更需要超精密加工技术才能制造。
精密与特种加工技术
25
第一章 绪论
精密与特种加工的产生与特点
精密与特种加工技术
案例3:光学镜片的加工
精度:超光滑,廓形超精密
形状:曲面,非球面
材料:大都是硬脆材料
精密与特种加工技术
8
第一章 绪论
精密与特种加工的产生与特点
精密与特种加工的产生与特点
案例4:微小或易变形零件/特征的加工
喇叭形网孔滤网
刮胡刀网罩
喷气管
薄壁零件
精密与特种加工技术
9
第一章 绪论
精密与特种加工的产生与特点
超薄膜的均匀生长问题
第一章 绪论
精密与特种加工的产生与特点
特种加工技术的产生与特点
产生背景
陶瓷,玻璃,硅,金 刚石,不锈钢,钛合 金,高温镍基合金等
1
难切削材料的加工问题
曲面;非规则几何型 面;功能表面等
四大加 微纳尺度;低刚度; 工问题
薄壁;易氧化;非圆 孔;深小孔等
2
特殊复杂表面的加工问题
3
超精密表面的加工问题
主要内容
精密与特种加工的产生与特点
精密与特种加工的分类
精密与特种加工对机械制造工艺的影响
精密与特种加工的地位与发展趋势
精密与特种加工技术
3
第一章 绪论
精密与特种加工的产生与特点
案例1:集成电路芯片(chips)的制造
特殊材料:硅 超高精度:微纳米 微纳尺度:微纳米 封装 芯片
硅片
精密与特种加工技术
0.1微米级,微量进给和定位精度要达到0.01微米级。
环境条件:要求苛刻,须保持恒温、恒湿和空气洁净,并采取有效的防 振措施。
加工系统:系统误差和随机误差都应控制在 0.1微米级或更小。
精密与特种加工技术
18
第一章 绪论
超精密加工方法 (Methods)
精密与特种加工的产生与特点
超精密切削加工,超精密磨削、研磨和抛光,超精密微细加工
35
第一章 绪论
精密与特种加工对制造工艺的影响
精密与特种加工技术对制造工艺的影响
精密超精密加工对制造工艺的影响 提高制造精度 提高产品质量和性能 提高产品可靠性 促进产品小型化 增强零件互换性,提高装配生产率,促进装配自动化
精密与特种加工技术
23
第一章 绪论
精密与特种加工的产生与特点
陀螺仪
哈勃望远镜用大型透镜
曲面镜
精密与特种加工技术
反射镜
第一章 绪论
典型应用 信 息 产 品
精密与特种加工的产生与特点
计算机上的芯片、磁板基片、光盘基片等都需要超精密加工技术来 制造。录像机的磁鼓、复印机的感光鼓、各种磁头、激光打印机的 多面体、喷墨打印机的喷墨头等都必须进行超精密加工,才能达到 质量要求。
精密与特种加工技术
15
第一章 绪论
特点
历史性 相对性 发展性 不普及性 保密性 尖端性
精密与特种加工的产生与特点
与测量技术关联性
机理
不同加工精度等级的去除机理
精密与特种加工技术
16
第一章 绪论
精密与特种加工的产生与特点
各类加工方法所能达到的精度及其发展趋势预测(日本TANIGUCHI, 1983年)
超精密加工刀具 (Tool)
单晶金刚石刀具;超硬砂轮;砂带;研磨具/膏;抛光垫等 超精密加工机床设备(Machine tool)
超精密机床,超精密机床主轴、导轨、进给驱动系统
超精密加工中的测量技术(Measuring technique) 在线检测与误差补偿,微位移机构,激光测量
超精密加工的支撑环境 (Environment)
(ECAM)。
精密与特种加工技术
29
第一章 绪论
精密与特种加工的分类
精密与特种加工技术的分类
精密与特种加工技术
30
第一章 绪论
特种加工技 术
精密与特种加工的分类
热作用特种 加工
电化学作用 特种加工
化学作用特 种加工
机械作用特 种加工
组合作用特 种加工
复合能量特 种加工
快速成型
电
激
弧
光
电场作
用下的 氧化还 原反应
空气环境和热环境,振动环境,其它环境工
恒温:±1℃~±0.02℃,甚至达到±0.0005℃。 恒湿:湿度应保持在55%~60%,防止机器的锈蚀、石材膨胀,以及一些仪器,如激光干涉仪的零点漂移等。 超净:洁净度要求1000~100级,100级是指每立方英尺空气中所含大于0.5μm的尘埃不超过100个,依此类推。
航空发动机(最难制造的部件)
精密与特种加工技术
6
第一章 绪论
精密与特种加工的产生与特点
精密与特种加工的产生与特点
案例2:航空发动机涡轮叶片的加工
材料特殊:耐高温镍基合金和涂层 形状复杂:变截面,空间多维 结构复杂:曲孔,异型孔等
精密与特种加工技术
7
第一章 绪论
精密与特种加工的产生与特点
精密与特种加工的产生与特点
20世纪60年代:适应核能、大规模集成电路、激光和航空航天
等尖端技术的需要
对产品质量的追求 硬盘或光学零件:极低表面粗糙度和极高几何尺寸精度
,Ra≤0.1nm,精度≤10nm
对产品小型化的追求 电子器件;M/NEMS;表面积/体积,工件的表面质
量及其完整性越来越重要
对产品高可靠性的追求 Ra,耐磨性好,精度,运动稳定好,工作寿命
主要意义
超精密加工是国家制造工业水平的重要标志之一
超精密加工所能达到的精度、表面粗糙度、加工尺寸范围和几何形状是一 个国家制造技术水平的重要标志之一。例如:金刚石刀具切削刃钝圆半径的 大小是金刚石刀具超精密切削的一个关键技术参数,日本声称已达到2nm, 而我国尚处于亚微米水平,相差一个数量级。 尖端技术领域、国防工业和微电子工业等都精密超精密加工作支撑。 当代的精密工程、微细工程和纳米技术是现在制造技术的前沿,也是明天 技术的基础。
氧化还
原反应
磨粒、
水、混 合物的 冲击或 划擦
不同能 量的先 后作用
两种或 两种以 上能量 同时作 用
激光与 热作用 形成的 不同的 加工方 法
电子束 等离子 体
精密与特种加工技术
31
第一章 绪论
精密与特种加工的分类
电火花加工(Electro discharge machining)
激光加工(Laser beam machining)
学仪器、大规模集成电路、民用产品等。
世界发展概况
美国是开展研究最早的国家。
日本是当今世界上超精密加工技术发展最快的国家 。 我国的超精密加工技术在70年代末期有了长足进 步,80年代中期出现了 具有世界水平的超精密机床和部件。源自精密与特种加工技术21
第一章 绪论
意义与典型应用
精密与特种加工的产生与特点
精密与特种加工技术
32
第一章 绪论
精密与特种加工的分类
电化学加工 (Electrochemical machining)
化学加工 (Chemical machining)
精密与特种加工技术
33
第一章 绪论
精密与特种加工的分类
超声加工(Ultrasonic machining)
水射流加工(Water jet machining)
长.
对产品高性能的追求
制造精度直接关联产品质量(性能,可靠性,寿命) 制造技术发展与提高的核心:自动化智能制造;精密与超精密加工
精密与特种加工技术
14
第一章 绪论
定义
精密与特种加工的产生与特点
不是指某一特定的加工方法,也不是指比某给定的加工精度高一个数量级 的加工技术,而是指在机械加工领域中,某一个历史时期所能达到的较(最)高 加工精度的各种精密加工方法的总称。 精密加工:加工精度在0.1~1µm,加工表面粗糙度在Ra0.02~0.1µm之 间的加工方法。 超精密加工:加工精度高于0.1µm,加工表面粗糙度小于Ra0.01µm的加 工方法(光整加工、精整加工等 )。 目前超精密加工己进入纳米级,并称之为纳米加工及相应的纳米技术(极限 加工技术)。
不是主要依靠机械能,而是主要用其他能量(如电、化学、 光、声、热等)
实现
加工工具硬度可以低于被加工材料的硬度 加工过程中工具和工件之间一般不存在显著的机械切削力 各种加工方法可以任意复合、扬长避短,形成新的工艺方法,更突出其优