钢中氮含量的控制
钢中氮含量的控制
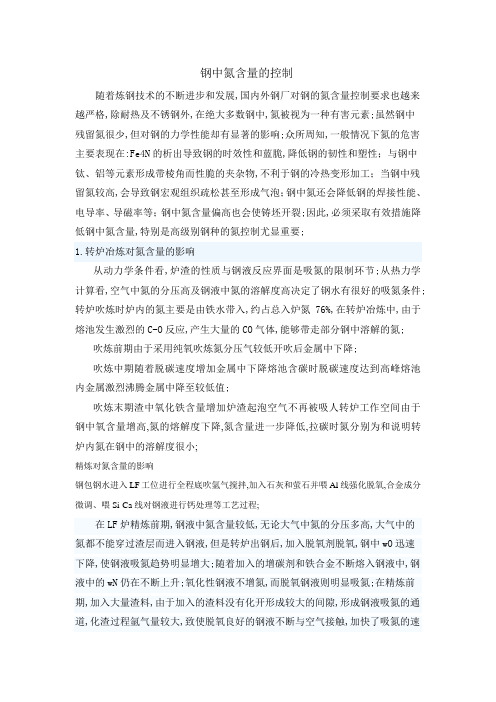
钢中氮含量的控制随着炼钢技术的不断进步和发展,国内外钢厂对钢的氮含量控制要求也越来越严格,除耐热及不锈钢外,在绝大多数钢中,氮被视为一种有害元素;虽然钢中残留氮很少,但对钢的力学性能却有显著的影响;众所周知,一般情况下氮的危害主要表现在:Fe4N的析出导致钢的时效性和蓝脆,降低钢的韧性和塑性;与钢中钛、铝等元素形成带棱角而性脆的夹杂物,不利于钢的冷热变形加工;当钢中残留氮较高,会导致钢宏观组织疏松甚至形成气泡;钢中氮还会降低钢的焊接性能、电导率、导磁率等;钢中氮含量偏高也会使铸坯开裂;因此,必须采取有效措施降低钢中氮含量,特别是高级别钢种的氮控制尤显重要;1.转炉冶炼对氮含量的影响从动力学条件看,炉渣的性质与钢液反应界面是吸氮的限制环节;从热力学计算看,空气中氮的分压高及钢液中氮的溶解度高决定了钢水有很好的吸氮条件;转炉吹炼时炉内的氮主要是由铁水带入,约占总入炉氮76%,在转炉冶炼中,由于熔池发生激烈的C-O反应,产生大量的CO气体,能够带走部分钢中溶解的氮;吹炼前期由于采用纯氧吹炼氮分压气较低开吹后金属中下降;吹炼中期随着脱碳速度增加金属中下降熔池含碳时脱碳速度达到高峰熔池内金属激烈沸腾金属中降至较低值;吹炼末期渣中氧化铁含量增加炉渣起泡空气不再被吸人转炉工作空间由于钢中氧含量增高,氮的熔解度下降,氮含量进一步降低,拉碳时氮分别为和说明转炉内氮在钢中的溶解度很小;精炼对氮含量的影响钢包钢水进入LF工位进行全程底吹氩气搅拌,加入石灰和萤石并喂Al线强化脱氧,合金成分微调、喂Si-Ca线对钢液进行钙处理等工艺过程;在LF炉精炼前期,钢液中氮含量较低,无论大气中氮的分压多高,大气中的氮都不能穿过渣层而进入钢液,但是转炉出钢后,加入脱氧剂脱氧,钢中wO迅速下降,使钢液吸氮趋势明显增大;随着加入的增碳剂和铁合金不断熔入钢液中,钢液中的wN仍在不断上升;氧化性钢液不增氮,而脱氧钢液则明显吸氮;在精炼前期,加入大量渣料,由于加入的渣料没有化开形成较大的间隙,形成钢液吸氮的通道,化渣过程氩气量较大,致使脱氧良好的钢液不断与空气接触,加快了吸氮的速度;另外在电极加热时,电弧最高温度可以达到6000℃;电弧作用到钢液上时,这部分钢液较其它部位的钢液温度高,超过2300℃;而当钢液温度超过2130℃时,发生如下反应:N2=2Ng 1Ng+Q=N 2在渣界面存在大量被电离的N,随着氧、硫在钢中的浓度急剧下降,吸氮趋势加强;被电离的N在裸露区域被钢液吸入,钢液中氮含量增加;渣料完全融化后,渣子覆盖在钢水表面;氩气压力降低,避免吹开渣层,这样隔绝了氮气跟钢水的接触,避免了N的吸入;精炼结束后,进行成分的微调和Ca处理过程中,会造成一定的增氮量,,喂线Ca-Si过程增氮,主要是由于Ca气化形成Ca气泡将钢液面吹开,造成裸露的钢液从空气中吸氮而产生的;Ca-Si线本身的增氮;如果渣层较厚线穿过渣层进人钢液而不把钢液面吹开,就有可能避免裸露钢液吸氮,这就是部分炉次喂线过程钢液没有增氮的原因;另外,LF炉渣碱度的控制也不容忽视,有研究表明:LF炉渣碱度不宜大于,否则渣的熔点升高,可能会有部分炉渣未完全熔化造成炉渣结构松散而存有空隙,使钢液吸氮的可能性增加;3.连铸浇铸对氮含量的影响连铸过程中为了防止钢包钢流和中间包钢流的二次氧化和吸氮,普遍采用保护浇注技术;连铸机连铸过程钢包到中间包之间的钢水保护采用大包长水口加氩气密封和中间包加覆盖剂保护钢液;中间包到结晶器的保护采用浸入式水口加连铸保护渣对钢液进行保护浇注,防止二次氧化和吸氮;由于该保护措施使得钢液与空气完全隔离,钢液从中间包到结晶器二次氧化和吸氮现象很弱,基本上不增氮;综上,连铸过程增氮主要发生在钢包到中间包之间的环节上,保护浇注系统的完善程度决定了,该阶段的保护工作是连铸段防止增氮的主要任务;连铸开浇时第一包钢水进入中间包开始阶段属于敞开浇铸,钢水会吸氮;连铸机长水口如密封不良,将会象一个抽气泵一样把空气从接缝处吸入;为防止在接缝处吸入空气,可以在接缝处通入Ar气,使长水口顶部形成正压区,基本可避免吸氮;综合分析以上因素,采取相应的措施,即可避免氮造成的皮下气泡等钢的质量问题;。
钢铁行业氮氧化物控制技术及对策
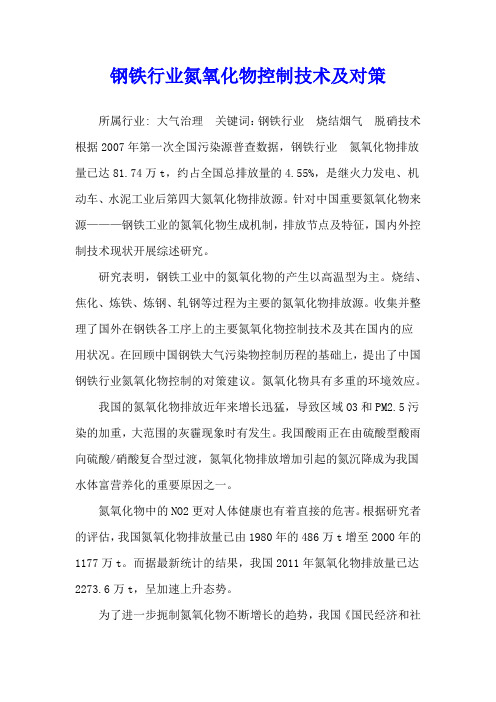
钢铁行业氮氧化物控制技术及对策所属行业: 大气治理关键词:钢铁行业烧结烟气脱硝技术根据2007年第一次全国污染源普查数据,钢铁行业氮氧化物排放量已达81.74万t,约占全国总排放量的4.55%,是继火力发电、机动车、水泥工业后第四大氮氧化物排放源。
针对中国重要氮氧化物来源———钢铁工业的氮氧化物生成机制,排放节点及特征,国内外控制技术现状开展综述研究。
研究表明,钢铁工业中的氮氧化物的产生以高温型为主。
烧结、焦化、炼铁、炼钢、轧钢等过程为主要的氮氧化物排放源。
收集并整理了国外在钢铁各工序上的主要氮氧化物控制技术及其在国内的应用状况。
在回顾中国钢铁大气污染物控制历程的基础上,提出了中国钢铁行业氮氧化物控制的对策建议。
氮氧化物具有多重的环境效应。
我国的氮氧化物排放近年来增长迅猛,导致区域O3和PM2.5污染的加重,大范围的灰霾现象时有发生。
我国酸雨正在由硫酸型酸雨向硫酸/硝酸复合型过渡,氮氧化物排放增加引起的氮沉降成为我国水体富营养化的重要原因之一。
氮氧化物中的NO2更对人体健康也有着直接的危害。
根据研究者的评估,我国氮氧化物排放量已由1980年的486万t增至2000年的1177万t。
而据最新统计的结果,我国2011年氮氧化物排放量已达2273.6万t,呈加速上升态势。
为了进一步扼制氮氧化物不断增长的趋势,我国《国民经济和社会发展十二五规划纲要》已明确在“十二五”期间将氮氧化物排放量减少10%作为主要目标之一。
本研究针对我国重要氮氧化物来源———钢铁工业的氮氧化物生成机制,排放节点及特征,国内外控制技术现状开展研究分析,并提出了我国钢铁行业氮氧化物控制的对策建议。
1 我国钢铁工业的发展及氮氧化物排放现状我国钢铁工业经历了不平凡的发展历程,改革开放以来取得了举世瞩目的成就。
建国初期,粗钢产量只有15.8万t,而到2011年粗钢产量已达6.955亿t,是建国初期的4400倍,占世界总产量的45.5%。
然而钢铁工业快速发展所引起的环境污染问题也不容忽视。
40CrB冶炼过程中氮含量的控制
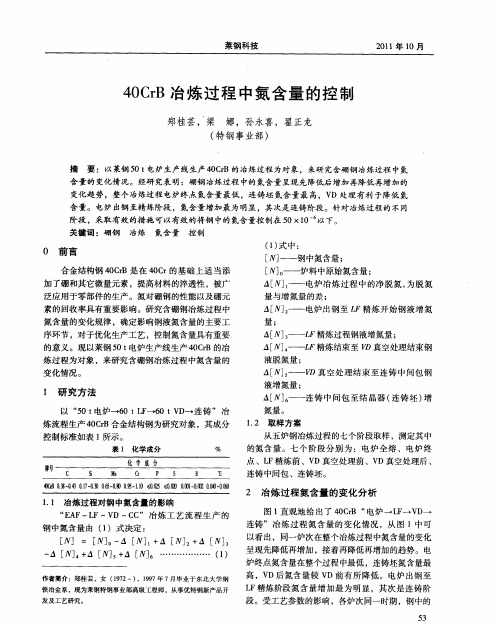
表 1 化学成分
— — — — — — — — — — — — 一
%
的氮含量。七 个阶段分别为 :电炉全熔 、电炉终
点 、L F精炼前 、V D真 空处 理前 、V D真 空处理 后 、 连 铸 中间包 、连 铸坯 。
4 Ⅻ U 8 U 3nl 【 X 3一 4 7 n揶 U6一 ; U 5 1】 ≤ 5 n{ 9一. U O u皿5 为工艺改进前 5炉 4 CB钢各 阶段氮 0r 含量的平均值与改进后新冶炼的 5炉 4 CB钢氮含 0r 量 平均 值 。
3 )针对冶炼过程 的不同阶段 ,采取有效的措 施可以有效将钢中的氮含量控制在 5 1 I以下。 0× 0 6
参 考 文献
[ ]祝真 祥 .转 炉冶 炼钢 中氮含 量 的控 制 [ ].本钢技 1 J
图 1 冶炼不 同时期氮含量 的变化
2 1 电炉 冶炼 过程 氮含量 变化 .
终点 钢液 中 的氮含量 略低 于全 熔钢 液 中的氮 含 量 ,电炉 氮含 量低 于 4 0×1 ~。这 是 由于莱 钢 5 0 0t
电炉铁水 兑入量 比例 不低 于 3 % ,形成 熔池 早 , 5
氮严重 ;钢包在电炉 与 L 之 间停留时间越长 ,氩 F 气流量越大 ,吸氮越严重。钢包内加入的大量增碳
剂 ,也 会使 钢液 大量 增氮 。
保精炼炉埋弧操作 ,降低钢液吸氮量 ;精炼过程避
免大氩气流量搅 拌钢液 ;加入钛 固氮;通过优化 L 精炼炉的操作 ,降低入 V F D炉 时钢液 中的氧硫 含量 ;V D真 空处理 过 程 ,熔 渣 量越 少 越 有 利 于 钢 液中氮的脱除;在保证钢渣不溢出的情况下 ,增加
氮在钢水中的行为及工艺控制研究

山西冶金SHANXI METALLURGY Total 188No.6,2020DOI:10.16525/14-1167/tf.2020.06.17试(实)验研究总第188期2020年第6期氮在钢水中的行为及工艺控制研究晏武,付有彭,张忠福,王哲,任涛,孙海坤,李毅(日照钢铁控股集团有限公司,山东日照276800)摘要:氮元素在钢水中含量过高会导致钢材强度升高,降低钢材的韧性及塑性,严重时会影响钢材的时效性并引发“蓝脆”。
本文介绍了炼钢工序增氮及脱氮的机理,并制定了控氮措施,对转炉工序、精炼工序、RH 真空处理阶段做出了针对性的调整,钢水氮得到了有效控制。
关键词:炼钢增氮危害脱氮中图分类号:TF711文献标识码:A文章编号:1672-1152(2020)06-0041-04收稿日期:2020-07-22第一作者简介:晏武(1988—),男,硕士,毕业于安徽工业大学冶金工程专业,主要从事炼钢工艺技术相关工作。
钢中的氮是以氮化物的形式存在,它对钢质量的影响表现出双重性,氮含量高的钢种长时间放置将会变脆,这一现象称为“老化”或“时效”。
原因是钢中氮化物(Fe 4N )的析出速度很慢,逐渐改变着钢的性能。
钢中氮含量高时,会使钢发生第一类回火脆性,即在250~450℃温度范围内,其表面发蓝,钢的强度升高,冲击韧性降低,称为“蓝脆”。
氮的存在会使铸坯产生结疤和皮下气泡,在轧制过程中产生裂纹和发纹。
氮含量增加,钢的焊接性能变坏,造成焊接热影响区脆化,降低磁导率、电导率。
对于某些钢种氮的存在对其性能有一定的益处,氮可以起到细化晶粒的作用,但由于氮元素原子半径较大,即使在真空条件下扩散速率也不是很大[1],所以如何有效将钢水中氮去除仍是困扰炼钢工序的一个难题。
1氮对钢的影响在590℃时氮在α-Fe 中最高溶解度时约为0.1%,室温下降到0.001%以下。
对于游离氮含量高的钢,在高温下较快冷却时,铁素体将会被饱和,长时间放置,性能将变脆。
LF精炼过程钢中硫、磷、氮、氧含量控制

LF精炼过程钢中硫、磷、氮、氧含量控制作者:钱丹丹陈志月闫若璞来源:《中国科技博览》2016年第07期[摘要]将转炉、平炉或电炉中初炼过的钢液移到另一个容器中进行精炼的炼钢过程,也叫“二次炼钢”。
炼钢过程因此分为初炼和精炼两步进行。
初炼:炉料在氧化性气氛的炉内进行熔化、脱磷、脱碳和主合金化。
精炼:将初炼的钢液在真空、惰性气体或还原性气氛的容器中进行脱气、脱氧、脱硫,去除夹杂物和进行成分微调等。
这样将炼钢分两步进行,可提高钢的质量,缩短冶炼时间,简化工艺过程并降低生产成本。
[关键词]LF精炼脱硫脱磷氮、氧含量 s非金属夹杂物中图分类号:U231.92 文献标识码:A 文章编号:1009-914X(2016)07-0277-011.引言:钢材的质量及性能是根据需要而确定的,不同的需要,要有不同的元素含量。
硫;是钢中的有害杂物,含硫较高的钢在高温进行压力加工时,容易脆裂,通常叫做热脆性。
磷;能使钢的可塑性及韧性明显下降,特别的在低温下更为严重,这种现象叫做冷脆性。
通常情况下,氮被视为钢中的有害元素,而氧元素主要以氧化物系非金属夹杂物的形式存在于钢中。
减少LF 炉精炼工艺过程钢液增氧、去除钢中氢含量是生产优质钢的关键环节。
此外,控制钢中夹杂物是提高钢材使用性能的有效途径。
2.转炉LF精炼脱硫与脱磷2.1脱硫2.1.1脱硫方法硫是钢中的长存元素之一,它会使大多数钢种的加工性能和使用性能变坏,因此除了少数易切削钢种外,它是需要在冶炼中脱除的有害元素。
硫在钢中以[FeS]形式存在,常以[S]表示。
钢中含锰高时,还会有一定的[MnS]存在。
目前炼钢生产中能有效脱除钢中硫的方法有碱性氧化渣脱硫、碱性还原渣脱硫和钢中元素脱硫三种。
2.1.2 脱硫影响因素脱硫影响因素与碱性氧化渣脱硫不同,LF碱性还原渣脱硫反应方程式为:[FeS]+(CaO)=(CaS)+(FeO)(1) [MnS]+(CaO)=(CaS)+(MnO)(2)由于钢中的[S]大部分以[FeS]形式存在,因此脱硫反应主要以式(1)为主。
中碳含硼钢氮含量的控制
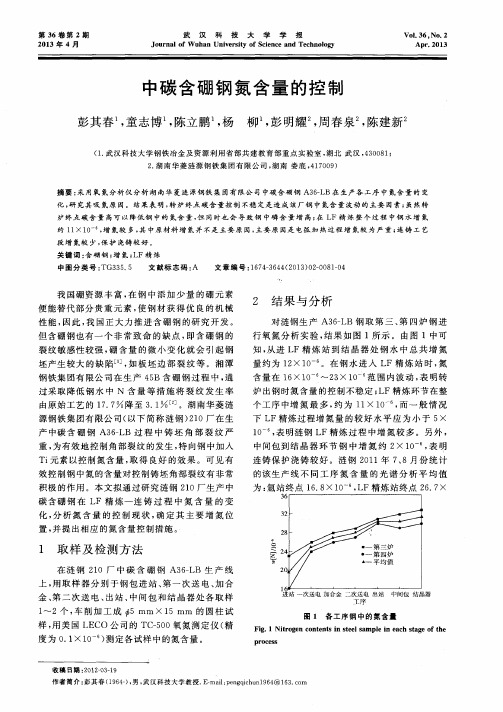
产 中碳 含 硼 钢 A3 6 一 L B过 程 中 铸 坯 角 部 裂 纹 严 重, 为有效 地控 制角 部裂 纹 的发生 , 特 向钢 中加入 Ti 元 素 以控制 氮含 量 , 取得 良好 的效果 。可见 有 效 控 制钢 中氮 的含量 对控 制铸 坯角 部裂 纹有 非常 积极 的作用 。本 文拟 通 过研究 涟钢 2 1 0厂生 产 中 碳含硼钢在 L F精 炼 一连 铸 过 程 中氮 含 量 的 变 化, 分 析 氮 含 量 的控 制 现 状 , 确 定 其 主 要 增 氮 位
度为 0 . 1 ×1 O ) 测 定各试 样 中的氮 含量 。
图 1 各 工 序 钢 中的 氮 含 量
Fi g. 1 Ni t r o g e n c o nt e nt s i n s t e e l s a m pl e i n e a c h s t a g e of t he
源钢 铁集 团有 限公 司 ( 以下 简称 涟 钢 ) 2 1 0厂在 生
个 工序 中增 氮 最 多 , 约为 1 1 ×1 0 一, 而一 般 情 况 下L F精 炼 过程增 氮 量 的 较好 水 平 应 为小 于 5 ×
1 O ~, 表 明涟 钢 L F精炼 过 程 中增 氮 较 多 。另外 ,
2 . 湖 南 华 菱 涟 源钢 铁 集 团有 限公 司 , 湖南 娄底 , 4 1 7 O O 9 )
摘要 : 采 用 氧 氮 分 析 仪 分 析 湖 南华 菱 涟 源钢 铁 集 团有 限公 司 中碳 含 硼 钢 A 3 6 - L B在 生 产 各 工 序 中 氮含 量 的 变
化, 研 究 其 吸 氮 原 因 。结 果 表 明 , 转 炉 终 点碳 含 量控 制 不稳 定 是 造 成 该 厂钢 中氮 含 量 波 动 的 主要 因 素 ; 虽然 转
炼钢过程中钢水氮含量控制
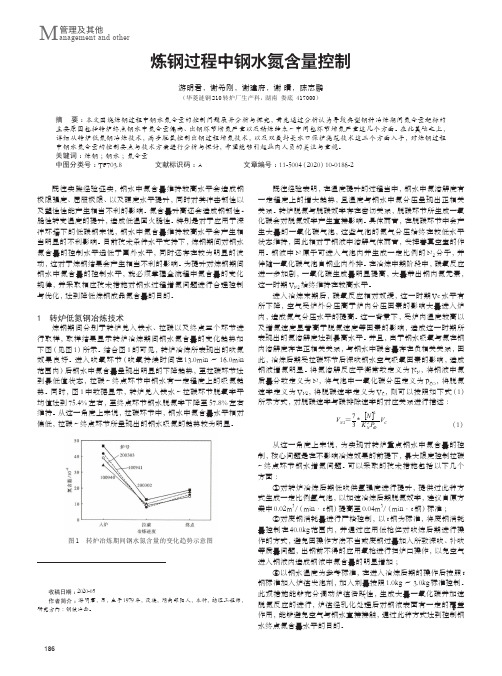
内,造成氮气分压水平的提高。这一背景下,受炉内温度较高以
及增氮速度显著高于脱氮速度等因素的影响,造成这一时期所
表现出的氮溶解度达到最高水平。并且,由于钢水吸氧与氮在钢
ቤተ መጻሕፍቲ ባይዱ
内溶解度存在正相关关系,与钢水中碳含量存在负相关关系,因
此,冶炼后期受拉碳环节后深吹钢水空气吸氧因素的影响,造成
钢液增氮明显。将氮溶解反应平衡常数定义为 KN,将钢液中氮 质量分数定义为 N,将气泡中一氧化碳分压定义为 PCO,将脱氮 速率定义为 VN2,将脱碳速率定义为 VC,则可以按照如下式(1) 所示方式,对脱碳速率与碳排除速率的对应关系进行描述 :
0.0*10-6 ~ 4.0*10-6
脱氧方式 不脱氧
11.0*10-6
3.0*10-6 ~ 22.0*10-6
12.0*10-6
5.0*10-6 ~ 22.0*10-6
铝铁脱氧
表 2 工艺优化前、后出钢环节增氮量示意表
平均值 11.3*10-6
应用前 区间
用。钢液中 N 原子可进入气泡内并生成一定比例的 N2 分子,并 伴随一氧化碳气泡自钢业内外排。在冶炼中期阶段中,碳氧反应
进一步加剧,一氧化碳生成量明显提高,大量带出钢内氮元素,
这一时期 VN2 始终维持在较高水平。 进入冶炼末期后,碳氧反应相对放缓,这一时期 Vc 水平有
所下降,空气受炉外分压高于炉内分压因素的影响大量进入炉
游明君,谢希刚,谢建府,谢 晴,陈志鹏
(华菱涟钢 210 转炉厂生产科,湖南 娄底 417000)
摘 要 :本文围绕炼钢过程中钢水氮含量的控制问题展开分析与探究,首先通过分析认为导致典型钢种冶炼期间氮含量超标的
主要原因包括转炉终点钢水中氮含量偏高、出钢环节增氮严重以及精炼结束 ~ 中间包环节增氮严重这几个方面。在此基础之上,
钢的纯净度评测及其控制

钢的纯净度估测及其控制<The Evaluation Methods and Control of Steel Cleanliness>1.引言随着社会发展和科技进步, 对钢质量, 尤其对它的纯净度(cleanliness)要求越来越高. 除了要降低钢中非金属氧化物夹杂物(non-metallic oxide inclusions)的含量, 控制其尺寸、形貌和成分外, 就洁净钢(clean steel)而言, 还要求控制其硫(S)、磷(P)、氢(H)、氮(N), 甚至碳(C), 并且要尽可能减少钢中金属杂质元素(metallic impurity elements), 诸如: 砷(AS)、锡(Sn) 、锑(Sb)、硒(Se)、铜(Cu)、锌(Zn)、铅(Pb)、镉(Cd)、碲(Te)、铋(Bi)等.不同钢种因其不同的应用场合和条件,对上述要求也各不相同。
例下表所示:表1 对不同钢种典型的纯净度要求(Typical steel cleanliness requirements for various steel grades)钢中的金属杂质元素(metallic impurity elements)通常被视为残余元素(trace elements).由于它们在炼钢和精炼过程很难去除,所以在钢中不断累积,成为废钢供应的一大问题。
鉴于钢中如存在超量的残余金属元素,会造成晶间偏析(intergranular segregation)、有害析出物和其它一些问题。
目前,在钢的生产过程中为了克服钢中残余元素造成的危害,尤其是电炉炼钢,通常采用严格控制废钢的种类和用量。
近年来世界各国普遍采用高炉铁水、直接还原铁、海绵铁、碳化铁或其它相对纯的铁来替代废钢,旨在降低钢中残余元素含量。
从钢中残余元素角度讨论钢纯净度问题近年来已有不少相关研究的报道和论文发表。
我们今天主要讨论钢厂普遍存在,大家又十分关注并想得到解决的问题:〈低碳铝镇静钢氧化物夹杂对其纯净度的影响〉。
- 1、下载文档前请自行甄别文档内容的完整性,平台不提供额外的编辑、内容补充、找答案等附加服务。
- 2、"仅部分预览"的文档,不可在线预览部分如存在完整性等问题,可反馈申请退款(可完整预览的文档不适用该条件!)。
- 3、如文档侵犯您的权益,请联系客服反馈,我们会尽快为您处理(人工客服工作时间:9:00-18:30)。
钢中氮含量的控制
随着炼钢技术的不断进步和发展,国内外钢厂对钢的氮含量控制要求也越来越严格,除耐热及不锈钢外,在绝大多数钢中,氮被视为一种有害元素。
虽然钢中残留氮很少,但对钢的力学性能却有显著的影响。
众所周知,一般情况下氮的危害主要表现在:Fe4N的析出导致钢的时效性和兰脆,降低钢的韧性和塑性;与钢中钛、铝等元素形成带棱角而性脆的夹杂物,不利于钢的冷热变形加工;当钢中残留氮较高,会导致钢宏观组织疏松甚至形成气泡;钢中氮还降低钢的焊接性能、电导率、导磁率等;钢中氮含量偏高也会使铸坯开裂。
因此,必须采取有效措施降低钢中氮含量,特别是高级别钢种的氮控制尤显重要。
转炉炼钢各工序过程对增氮的影响及建议
1、过程增氮主要发生在转炉终点至小平台吹Ar结束,其次是浇铸期间增氮。
对方坯钢种而言,出钢过程平均增氮约30×10-4%,浇铸过程平均增碳约5×10-4%;对板坯钢种而言,出钢过程平均增氮约10×10-4%,浇铸过程平均增氮约9×10-4%。
方坯LF处理过程增氮不明显。
2、脱氧程度较深的钢种在出钢过程、LF处理及浇铸过程增氮更严重,铸坯氮含量更高;含氮量较高的原辅料(如沥青焦增碳剂、SiCaBa等)直接加入钢液中对钢液增氮有重要影响。
3、深吹及出钢时间长造成终点氮含量增加;废钢消耗量对
转炉终点氮含量有一定影响,尤其是废钢消耗量>100kg/t时终点钢水氮含量明显上升。
4、钢水裸露吹氩、LF处理过程中不加或少加泡沫渣、浇铸过程长水口密封不好及中包钢液覆盖不良均会造成增氮。
5、为有效控制钢中氮含量以改善钢水质量,建议开展提高复吹透气砖基础使用寿命、脱氧工艺优化、LF炉精炼工艺优化及连铸长水口保护浇铸等技术研究。
低碳高氮马氏体不锈钢的特性
很早以前,人们就知道氮元素通过固溶强化后可以提高不锈钢的强度和耐蚀性。
由于氮是生成奥氏体的强力元素,因此它作为高价镍的替代元素,主要用于奥氏体不锈钢的生产。
近年来,为进一步探索氮的作用,有关采用添加更多氮的加压熔炼法、机械铣削法和固相吸收法等生产高氮不锈钢的研究报告也引起人们的关注。
另一方面,在不锈钢中,马氏体不锈钢的最大特点是硬度比铁素体不锈钢或双相不锈钢高。
尤其是,以提高硬度为主的高碳马氏体不锈钢由于其硬度和耐磨损性好,可用于制作刀具、量具、轴承和金属模等。
但是,由于马氏体不锈钢的耐蚀性通常比其它不锈钢明显差,因此在使用马氏体不锈钢时,应充分注意腐蚀环境,有时还需要采取表面处理等防锈措施。
对马氏体不锈钢使用氮时,为保持马氏体组织,因此要限制
Cr等合金元素添加量,由此造成在常压熔炼时的最大氮含量为0.15%左右,提高耐蚀性的效果通常也不尽人意。
为了一面保持马氏体组织,一面在钢中添加大于0.15%的氮,因此需要采用前面所述的加压熔炼等特殊生产方法。
在使用加压ESR的例子中,15Cr钢的氮含量达到了0.33%,在保持硬度660HV(相当于58HRC)左右的状态下,耐蚀性明显提高。
另外,虽然采用感应加压熔炼炉生产的含氮0.5%的18Cr钢的硬度略低(56HRC),但耐蚀性超过了SUS316。
关于氮可提高钢的硬度和耐蚀性的潜在作用还有许多需要研究的东西。
日本采用能够加压到2.0MPa的高频感应炉,用氮替代碳,试制了以提高耐蚀性为目的的高氮马氏体不锈钢,重点调查了淬火条件和回火条件对硬度及耐蚀性的影响,由此研究了在最佳热处理条件下氮提高钢的硬度和耐蚀性的潜在能力,并得出以下结论。
(1)试制的高氮马氏体不锈钢HNS-A~C在退火处理后,可将硬度降低到95HRB左右,冷加工性比SUS440C好。
(2)试制的高氮马氏体不锈钢HNS-A~C在淬火-深冷-回火处理后,硬度为56~60HRC左右,同时耐蚀性超过SUS304。
(3)得出了高氮马氏体不锈钢的硬度和耐蚀性与淬火时Cr2N 的固溶状态及回火时Cr2N的析出状态有相互关系的结论,作为最佳热处理条件是,通过淬火处理使Cr2N固溶时,在使Cr2N固溶到不会使耐蚀性变差的同时,一面抑制Ms点的过度下降,一
面确保固溶氮量,在此最佳条件下,可以获得最高硬度,并在723K周围抑制耐蚀性因Cr2N的再析出而变差。
(4)高氮马氏体不锈钢在氯化物离子腐蚀环境下的耐蚀性至少比SUS440C好,耐蚀性接近SUS316。