齿轮减速器设计计算
行星齿轮减速器的相关计算

行星齿轮减速器的相关计算行星齿轮减速器是一种常用的机械传动装置,其特点是结构紧凑、承载能力大、传动效率高。
在工程设计和机械计算中,对行星齿轮减速器的相关参数进行计算是必不可少的工作。
本文将详细介绍行星齿轮减速器的相关计算方法。
一、行星齿轮减速器的基本构造二、行星齿轮减速器的传动比计算传动比是指输入轴和输出轴的转速比,可以通过以下公式计算:i=(N_s+N_r)/N_s其中,i为传动比,N_s为太阳齿轮的齿数,N_r为行星齿轮的齿数。
行星齿轮减速器的传动比可以通过调整太阳齿轮和行星齿轮的齿数来实现。
三、行星齿轮减速器的传动效率计算η=(1-δ/100)*(1-ε/100)其中,η为传动效率,δ为齿间损失系数,ε为噪声损失系数。
行星齿轮减速器的传动效率受到齿轮的磨损和摩擦影响,一般情况下,传动效率在95%以上。
四、行星齿轮减速器的扭矩计算输入轴扭矩计算可以通过以下公式计算:T_in = P / (n * η)其中,T_in为输入轴扭矩,P为输出功率,n为输入轴转速,η为传动效率。
输出轴扭矩计算可以通过以下公式计算:T_out = i * T_in其中,T_out为输出轴扭矩,i为传动比,T_in为输入轴扭矩。
五、行星齿轮减速器的选择在实际工程中,选择合适的行星齿轮减速器需要考虑以下因素:1.承载能力:根据实际应用需求,选择承载能力适当的行星齿轮减速器。
2.传动比:根据需要的输出转速和输入转速,选择合适的行星齿轮减速器。
3.外形尺寸:根据实际安装空间,选择符合尺寸要求的行星齿轮减速器。
4.传动效率:选择传动效率高的行星齿轮减速器,以提高传动效率和节能效果。
5.稳定性:选择结构稳定、运行平稳的行星齿轮减速器,以减少振动和噪声。
六、行星齿轮减速器的基本计算流程1.确定输入功率、输入转速和输出转速。
2.根据输入功率和输入转速计算输入轴扭矩。
3.根据输入轴扭矩和传动比计算输出轴扭矩。
4.根据输出轴扭矩和输出转速计算输出功率。
行星齿轮减速器-课程设计计算说明书
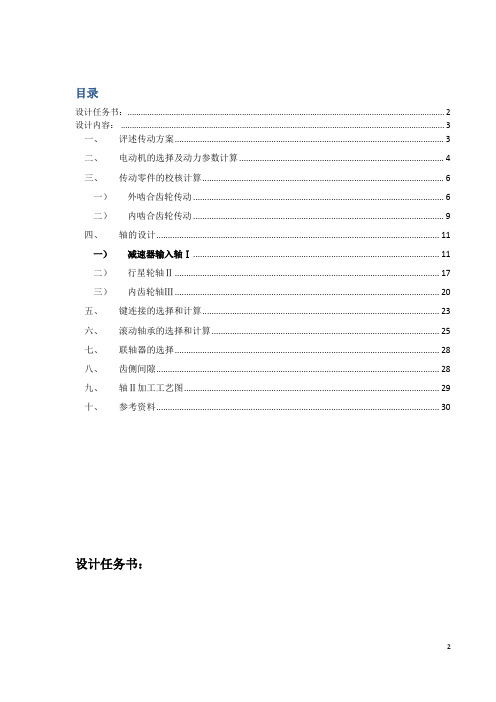
目录设计任务书: (2)设计内容: (3)一、评述传动方案 (3)二、电动机的选择及动力参数计算 (4)三、传动零件的校核计算 (6)一)外啮合齿轮传动 (6)二)内啮合齿轮传动 (9)四、轴的设计 (11)一)减速器输入轴Ⅰ (11)二)行星轮轴Ⅱ (17)三)内齿轮轴Ⅲ (20)五、键连接的选择和计算 (23)六、滚动轴承的选择和计算 (25)七、联轴器的选择 (28)八、齿侧间隙 (28)九、轴Ⅱ加工工艺图 (29)十、参考资料 (30)设计任务书:设计内容:一、 评述传动方案牵引速度为 1.5/v m s =,滚筒直径400D mm =,可求出滚筒转速(601000)/w n v =⨯⨯()(60100 1.5)/(400)71.62/min D r ππ=⨯⨯⨯=,由于工作情况为:室外,环境有灰尘,最高温度40℃,两班制,间歇双向运转,反向空转,断续周期工作制(S3),负荷持续率FC=56%,载荷有冲击,故应选YZR 系列电动机为原动机,它的转速约为750~1000r/min ,传动装置速比应为/(750~1000)/71.6210.47~13.96m w i n n === 可选如下图1-1、1-2两种方案:图1-1方案a 采用NW 分流式行星齿轮传动,卷扬机工作时制动器10制动,此时电动机1通过联轴器2驱动行星齿轮减速器,行星架上的滚筒5使钢丝绳7运动,从而牵引重物移动。
不需重物移动时,制动器6制动,制动器10松开,这时行星传动变成定轴传动,电动机和二级同轴式减速器空转,不用频繁地起动和制动电动机。
滚筒用滑动轴承支撑在机架上。
传动比:5~25i =,可满足传动要求。
优点:外形尺寸小(减速器内置),电动机不用频繁启动适合狭窄工况下工作。
缺点:结构复杂,加工安装精度高,成本大,不易维修。
图1-2方案b 采用一级带传动和一级闭式齿轮传动,电动机带动带传动,齿轮传动,从而带动滚筒运动。
二级齿轮减速器课程设计计算说明书

机械设计课程设计设计说明书学院:机械工程学院班级:机电班学号:201520160218设计者:马兆叶指导教师:刘鸣2018年01月一、设计任务书 (1)(一)设计任务 (1)(二)设计题目 (1)二、传动总体方案设计 (1)(一)定传动方案 (1)(二)确定电机 (3)(三)分配传动比 (3)(四)计算各轴的转速、功率和转矩 (4)三、V带传动设计计算 (5)四、齿轮传动设计 (7)(一)高速级齿轮设计 (7)(二)低速级齿轮设计 (13)五、轴的传动设计 (19)(一)对轴I进行设计 (19)(二)对轴II进行设计 (22)(三)对轴III进行设计 (25)(四)轴Ⅲ的安全系数法校核 (28)六、轴承的选择与设计 (30)(一)轴I上滚动轴承的设计 (30)(二)轴II上滚动轴承的设计 (32)(三)轴III上滚动轴承的设计 (33)七、键联接的设计 (35)八、联轴器的计算与设计 (35)九、减速器润滑方式,润滑油牌号及密封方式的选择 (36)十、设计总结 (37)十一、参考文献 (38)一、设计任务书(一)设计任务详细的设计计算说明书:一份完整的减速器装配图:一张(A0图纸)零件图:两张(A3图纸)(二)设计题目铸工车间一造型用砂型运输带,系由电动机驱动传动装置带动,该减速器传动装置由一个两级齿轮减速器和其他传动件组成,运输带每日两班制工作,工作7年。
设计此传动装置。
运输带主动鼓轮轴输入端转矩Tw=750N/m主动鼓轮直径 D =400mm运输带速度v=0.66m/sw减速器设计寿命7年二、传动总体方案设计(一)定传动方案1.初选电机由《机械设计课程设计》教材可知初选电机同步转速为1500r/min2.计算总传动比a.计算工作机输入转速:由公式100060⨯=ww w n d v π可得min /014.6340060100066.0601000n r D v w w =⨯⨯⨯=⨯⨯=ππb.计算总传动比984.3936.0141500n n i =='='w 电 3.定传动方案及各部分初始传动比 齿轮传动装置传动比 10.004i ='齿轮 链传动装置传动比 2.143i ='链 带传动装置传动比 1.865i ='带 4.传动装置 (1)结构分析按照传动比分配以及传动特征分析可知,此传动系统采用三相异步交流电机,电动机输出轴与小带轮直接连接,将动力和运动由大带轮传递到二级展开式斜齿圆柱齿轮减速器,然后通过联轴器及闭式链传动将动力和运动传至砂型运输带。
二级圆柱齿轮减速器设计计算说明书

二级圆柱齿轮减速器设计计算说明书一、设计任务设计一用于带式运输机的二级圆柱齿轮减速器。
运输机工作经常满载,空载启动,工作有轻微振动,两班制工作。
运输带工作速度误差不超过 5%。
减速器使用寿命 8 年(每年 300 天)。
二、原始数据1、运输带工作拉力 F =______ N2、运输带工作速度 v =______ m/s3、卷筒直径 D =______ mm三、传动方案的拟定1、传动方案选用展开式二级圆柱齿轮减速器,其结构简单,效率高,适用在载荷平稳的场合。
2、电机选择选择 Y 系列三相异步电动机,其具有高效、节能、噪声低、振动小、运行可靠等优点。
四、运动学和动力学计算1、计算总传动比总传动比 i = n 电/ n 筒,其中 n 电为电动机满载转速,n 筒为卷筒轴工作转速。
2、分配各级传动比根据经验,取高速级传动比 i1 ,低速级传动比 i2 ,应满足 i = i1 ×i2 。
3、计算各轴转速高速轴转速 n1 = n 电/ i1 ,中间轴转速 n2 = n1 / i2 ,低速轴转速 n3 = n2 。
4、计算各轴功率高速轴功率 P1 =Pd × η1 ,中间轴功率 P2 =P1 × η2 ,低速轴功率 P3 =P2 × η3 ,其中 Pd 为电动机输出功率,η1 、η2 、η3 分别为各级传动的效率。
5、计算各轴转矩高速轴转矩 T1 = 9550 × P1 / n1 ,中间轴转矩 T2 = 9550 × P2 /n2 ,低速轴转矩 T3 = 9550 × P3 / n3 。
五、齿轮设计计算1、高速级齿轮设计(1)选择齿轮材料及精度等级小齿轮选用______材料,大齿轮选用______材料,精度等级选______。
(2)按齿面接触疲劳强度设计确定公式内各计算数值,计算小齿轮分度圆直径 d1 。
(3)确定齿轮齿数取小齿轮齿数 z1 ,大齿轮齿数 z2 = i1 × z1 。
减速器齿轮阶次计算公式

减速器齿轮阶次计算公式一、减速器齿轮阶次的概念减速器齿轮阶次指的是在一个减速器系统中所有齿轮的齿数比之积。
它是用来表征齿轮系统速度比的一个重要参数。
减速器齿轮阶次的计算可以帮助工程师们确定齿轮系统的传动比,从而确定减速器的性能和稳定性。
二、减速器齿轮阶次的计算公式减速器齿轮阶次的计算公式如下:N = N1 * N2 * N3 * ...... * Nn其中,N代表减速器齿轮阶次,N1、N2、N3、...、Nn分别代表减速器中每个齿轮的齿数比。
三、减速器齿轮阶次的应用减速器齿轮阶次的计算在机械工程设计中有着非常重要的应用。
它可以帮助工程师们确定减速器系统的传动比,为设计和分析提供了重要的依据。
减速器齿轮阶次的计算还可以帮助工程师们评估减速器系统的性能和稳定性,从而为系统的改进和优化提供参考。
四、减速器齿轮阶次的影响因素减速器齿轮阶次的大小受多种因素的影响,主要包括齿轮的齿数比、齿轮直径、齿轮模数等。
在实际的设计和分析过程中,工程师们需要综合考虑这些因素,确定最合适的齿轮阶次,从而保证减速器系统的性能和稳定性。
五、减速器齿轮阶次的优化在实际的机械设计中,工程师们常常会对减速器齿轮阶次进行优化,以提高系统的传动效率和稳定性。
减速器齿轮阶次的优化通常包括选择合适的齿数比、齿轮直径和齿轮模数等,从而最大程度地降低系统的能量损失和振动噪声,并提高系统的传动效率。
六、结论减速器齿轮阶次计算是机械工程设计中非常重要的一部分。
它可以帮助工程师们确定减速器系统的传动比,为设计和分析提供重要的依据。
在实际的设计过程中,工程师们需要综合考虑齿数比、齿轮直径、齿轮模数等因素,对减速器齿轮阶次进行优化,从而提高系统的传动效率和稳定性。
希望本文能够对减速器齿轮阶次计算有所帮助。
各种减速器减速比计算公式
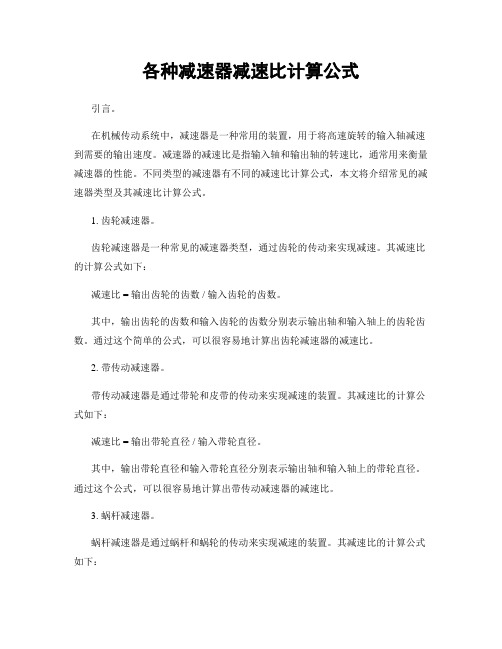
各种减速器减速比计算公式引言。
在机械传动系统中,减速器是一种常用的装置,用于将高速旋转的输入轴减速到需要的输出速度。
减速器的减速比是指输入轴和输出轴的转速比,通常用来衡量减速器的性能。
不同类型的减速器有不同的减速比计算公式,本文将介绍常见的减速器类型及其减速比计算公式。
1. 齿轮减速器。
齿轮减速器是一种常见的减速器类型,通过齿轮的传动来实现减速。
其减速比的计算公式如下:减速比 = 输出齿轮的齿数 / 输入齿轮的齿数。
其中,输出齿轮的齿数和输入齿轮的齿数分别表示输出轴和输入轴上的齿轮齿数。
通过这个简单的公式,可以很容易地计算出齿轮减速器的减速比。
2. 带传动减速器。
带传动减速器是通过带轮和皮带的传动来实现减速的装置。
其减速比的计算公式如下:减速比 = 输出带轮直径 / 输入带轮直径。
其中,输出带轮直径和输入带轮直径分别表示输出轴和输入轴上的带轮直径。
通过这个公式,可以很容易地计算出带传动减速器的减速比。
3. 蜗杆减速器。
蜗杆减速器是通过蜗杆和蜗轮的传动来实现减速的装置。
其减速比的计算公式如下:减速比 = 蜗轮的齿数 / 蜗杆的螺旋线数。
其中,蜗轮的齿数和蜗杆的螺旋线数分别表示输出轴和输入轴上的参数。
通过这个公式,可以很容易地计算出蜗杆减速器的减速比。
4. 行星齿轮减速器。
行星齿轮减速器是通过行星齿轮的传动来实现减速的装置。
其减速比的计算公式如下:减速比 = (太阳轮齿数 + 行星轮齿数) / 太阳轮齿数。
其中,太阳轮齿数和行星轮齿数分别表示输出轴和输入轴上的齿数。
通过这个公式,可以很容易地计算出行星齿轮减速器的减速比。
结论。
通过以上介绍,我们可以看到不同类型的减速器有不同的减速比计算公式。
这些公式可以帮助工程师们在设计和选择减速器时进行准确的计算,以满足实际的工程需求。
同时,了解这些公式也有助于我们更好地理解不同类型减速器的工作原理和性能特点。
希望本文对大家有所帮助,谢谢阅读!。
单级圆柱齿轮减速器的课程设计有图

K K小齿轮传递的转矩= z/ zz/cos/cos初选齿宽系数K K K=1Y==端面重合度近似为S10/510=14=====102 ==()aT判断危险截面的并验算强度 右起第四段剖面C 处的当量弯矩最大,而其直径与相邻段相差不大,所以为危险截面。
已知2ec M =558N.m ,由课本1-σ]=60MP a aB MP 640=σ a MP a MP T 1551=- 3224//(0.1)ec W M D ==558/(0.1×365)=20.31N.m ≤[1-σ] D 处虽仅受转矩但其直径较小,故该面也为危险截面:2)=0.6×871.44=522.864N.m31/(0.1)D W M D ==522.864/(0.1×350)=41.83≤[1-σ]十.设计总结经过两周紧张的课程设计,终于体会到了什么叫设计。
原来设计并非自己想的那么简单、随便,比如说,设计减速器时,里面的每一个零件几乎都有其国家标准,我们设计时必需得按标准进行设计,最后才能符合要求。
我觉得从事设计工作的人一定得要有很好的耐性,并且要有足够的细心,因为设计过程中我们要对数据不断的计算,对图形不断的修改,这需要耐心。
因此,我觉得我们有必要从现在就开始培养这样一种耐心的工作态度,细心的工作作风,以便以后更快的进入到工作中,避免不必要的错误。
我觉得,虽然这次设计出的结果与自己所想的有一定差距,但我想至少是自己动手了,并且通过这次设计,使自己更明白自己在这方面的欠缺和不足之处,懂得要从头到尾自己设计出一样东西是多么的难。
因此,我想在剩下的一年半时间里,我会针对自己专业方面欠缺知识进行提高,拓宽。
我想不管谁找出了自己的弱点,一定要努力的去改进、提高它,这样自己才会不断的进步,虽然“人无完人”,但我想我们不断的改进、提升自己,最后会使自己成为比现在的自己更强,更优秀的人的,再次感谢辅导老师的指导与帮助!机械设计课程设计说明书十一.参考资料[1]《机械设计课程设计》,中国矿业大学出版社,张建中主编,2006年9月第2版;[2]《机械设计(第八版)》,高等教育出版社,濮良贵,纪名刚主编,2006年5月第八版;[3]《工程机械构造图册》,机械工业出版社,刘希平主编[4]《机械制图(第四版)》,高等教育出版社,刘朝儒,彭福荫,高治一编,2001年8月第四版;[5]《互换性与技术测量(第四版)》,中国计量出版社,廖念钊,古莹庵,莫雨松,李硕根,杨兴骏编,2001年1月第四版。
机械设计基础 双级圆柱齿轮减速器 设计计算说明书 西安交通大学

轴
轴
轴
图 2 轴的布置简图 考虑到相邻齿轮间不发生干涉,计入尺寸 s=10mm。 考虑齿轮与形体内壁沿轴向不发生干涉,计入尺寸 k=10mm。 为保证滚动轴承放入箱体轴承座孔内,计入尺寸 c=5mm。 初取轴承宽度为
3 根轴的支承跨距分别为
(2)高速级轴(1 轴)的设计 ①选择轴的材料及热处理 轴上小齿轮的直径较小,采用齿轮轴结构。轴的材料及热处理和齿轮
设计小结及体会·····························22 参考文献································22
设计计算说明书
———双级圆柱齿轮减速器
计算及说明
一、设பைடு நூலகம்任务书 1. 设计任务
设计带式输送机传动系统。要求传动系统中含有两级圆柱齿轮减速器和 开式圆柱齿轮传动。 2. 原始数据
1.高速级斜齿圆柱齿轮的设计计算··················· 4 2.低速级直齿圆柱齿轮的设计计算··················· 4 七、减速器轴的设计计算························· 8 1.绘制轴的布置简图和初定跨距···················· 8 2.高速级轴的设计·························· 8 3.中间轴的设计···························11 4.低速级轴的设计··························13 八、滚动轴承的选择与计算························16 1.高速级轴上滚动轴承的选择·····················16 2.中间轴上滚动轴承的选择······················16 3.低速级轴上滚动轴承的选择·····················17 九、键连接和联轴器的选择与计算·····················17 1.高速级轴上键连接和联轴器的选择··················17 2.中间轴上键连接和联轴器的选择···················17 3.低速级轴上键连接和联轴器的选择··················18 十、箱体及附件设计···························19 1.窥视孔和窥视孔盖·························20 2.通气器······························20 3.定位销······························21 4.启箱螺钉·····························21 5.油标尺······························21 6.放油孔及螺塞···························21 7.起吊装置·····························21 十一、减速器的润滑方式与密封······················21
- 1、下载文档前请自行甄别文档内容的完整性,平台不提供额外的编辑、内容补充、找答案等附加服务。
- 2、"仅部分预览"的文档,不可在线预览部分如存在完整性等问题,可反馈申请退款(可完整预览的文档不适用该条件!)。
- 3、如文档侵犯您的权益,请联系客服反馈,我们会尽快为您处理(人工客服工作时间:9:00-18:30)。
如图1所示球磨机传动简图,试设计其单级圆柱齿轮减速器。
已知晓齿轮传递的额定功率P=250KW ,小齿轮的转速n1=750r/min,名义传动比i=3.15,单向运动,满载工作时间50000h 。
(1) 选择齿轮材料
小齿轮:37SinMoV ,调质,硬度320-340HB
大齿轮:35SiMn ,调质,硬度,280-300HB 。
传动简图 由图14-1-83和图14-1-112按MQ 级质量要求取值,得。
、和、22lim F 21lim F 22lim 21lim H /300N/320N/760/800mm N mm mm mm N H ====σσσσ(2)初步确定主要参数
1) 按接触强度初步确定中心距
按斜齿轮从表14-1-65选取476=αA ,按齿轮对称布置,速度中等,冲击载荷较大,取载荷系数K=2.0。
按表14-1-69,选8.0=d ϕ,则38.0=a ϕ,按表14-1-67圆整取齿宽系数35.0=a ϕ。
齿数比 15.3==i u
许用接触应力2
lim /6847609.09.0:mm N H H P H P =⨯=≈σσσ 小齿轮传递的转矩1T m N n P T ⋅=⨯==
3183750
2509549954911 中心距a 32
3215.45668415.335.031832)115.3(476)1(mm u KT u A a HP a a =⨯⨯⨯+=+≥σϕ 取 a=500mm
2)初步确定模数、齿数、螺旋角、齿宽、变位系数等几何参数
=n m (0.007~0.02)a=(0.007~0.002)×500=3.5~10mm
取m n =7mm
由公式
4.34)1
5.31(*7500*2)1(2cos 1=+=+=u m a Z n β 取 Z 1=34
Z 2=Iz=3.15*34=107.1
取 Z 2=107
实际传动化比 i 0=
147.33410721==z z
螺旋角 554195002)10734(7arccos )(arccos
21'''=⨯+⨯=+= za z z m n β
齿宽 mm b a 17550035.0=⨯==ψ 取 180
小齿轮分角圆直径 mm z m d n 135.24155419cos 347cos 11='
''⨯== β 大齿轮分角圆直径 865.75855419cos 1077cos 12='''⨯==
βz m d n
采用高度变位,查得:x 1=0.38 x 2=-0.38
齿轮精度等级为7级
(3)齿面接触强度核算
1)分度圆上名义切向为F 1 N d T F 26400135
.241318320002000111=⨯== 2)使用系数K A
原机动为电动机,平均平稳,工作机为水泥磨,有中等冲击,查表14-1-71 K A =1.5。
3)动载系数K V
齿轮线速度 m n d v 5.9100060750
135.2411000601
1=⨯⨯⨯=⨯=ππ/s
由表14-1-80公式计算传动精度系数C
32.3)(825.2)(144.1)(5048.0++--=pt n f In m In z In C Z=Z 1=30 f pt =25um(大轮) 062.832.325825.2)(144.1)(5048.0=++--=In m In z In C n 圆整取C=8 K V =1.25
4)螺旋线载荷分布系数βH K
由表14-1-88,齿轮装配时对研跑合 262.11801023.0)135.241180(18.012.11023.0)(
18.012.132321=⨯⨯++=⨯+=--b d b K H β 5)齿轮载荷分配系数βH K
mm N b F K A /22180/264005.1/1=⨯=
查表14-1-92得:1.1=βH K
6) 节点区域系数Z H
0=∑X 55419'''= β 47.2=H Z
7) 弹性系数Z H 由表14-1-95 2/8.189mm N Z =∑
8 重合度系数
纵向重合度 315.17
55419sin 180sin =⨯'''⨯==∑ππββ n m b 端面重合度 93.0,79.0,58.1721,64.2438.01341212
211=∑=∑=-=+=+a a n n x z x z 则 667.193.0)38.01(79.0)38.01()1()1(2211=⨯-+⨯+=∑-+∑+=∑a n a n a x x 查得 775.0=∑Z
9) 螺旋角系数βZ 993.055419cos cos ='''== ββZ
10) 小齿轮、大齿轮的单对齿合数Z B 、Z D
按表14-1-94的判定条件,由于。
,取1,10.1315.1==>=∑D Z Z ββ 11)计算接触应为H σ
由表14-1-70公式可得
u
u b d F Z Z Z K K K Z H H V A B H 1111+⨯=∑ββσ =147.31147.3135.24126400993.0775.08.89.147.21.1262.125.15.10.1+⨯⨯
⨯⨯⨯⨯⨯⨯⨯⨯ =521.1N/mm 2
由于212/1.5211mm N Z Z H H B d ====σσ,所以
12) 寿命系数Z NT
应力循环次数 9111025.2500007506060⨯=⨯⨯==t n L N 8221018.750000133.37506060⨯=⨯⨯
==t n L N 由表14-1-96公式计算 944.0)10
25.210()10(0706.0990706.0191=⨯==L NT N Z 02.1)10071810()10(057.099
057.029
2
=⨯==L NT N Z 13) 润华油膜影响系数Z L Z V Z R
由表14-1-98,经展成法滚、插的齿轮副85.0410=>R V L Z Z Z Z m R ,μ
14) 齿面工作硬化系数Z W
Z W =1.08 Z W2=1.11
15) 尺寸系数Z X
由表14-1-99 Z X =1.0
16) 安全系数S H
S H =33.11
.5210.108.185.0944.08001111=⨯⨯⨯⨯=H X W R V L NT HLim Z Z Z Z Z Z σσ 40.11
.5210.111.185.002.17602222=⨯⨯⨯⨯=H X W R V L NT HLim Z Z Z Z Z Z σσ S H1,S H2均达到表14-1-100规定的较高可度时,最小安全系数S Hmin =1.25~1.30的要求。
齿面的接触强度核
算通过。
(4)轮齿弯曲强度核算
1)螺旋线载荷分配系数K FB
K FB =(K HB )
N ()22
)
/(/1/h b h b h b N ++= mm b 180= mm m h n 75.15725.225.2=⨯== 22
)75.15/180(75.15/1801)75.15/180(++=N =0.913 24.1)262.1(913
.0==βF K
2) 螺旋线载荷分配系数αF K 1.1==ααH F K K
3) 齿廊系数αF Y
当量齿数 36.3555419cos 34
cos 331
1='''== βz z n 28.11155419cos 107
cos 332
2='''== βz z n
由图14-1-98 2.17Y 1F =α 2.30Y 2F =α
4) 应力修正系数αS Y 由图14-1-103 1.81Y 1S =α 1.69Y 2S =α
5) 重合度系数∑Y n
Y α∑+=∑75
.0
25.0 b
a
an β2cos ∑=∑
由表14-1-104知 []2)cos (sin 1arccos n b αββ-= 9885.0)20cos 55419(sin 1)cos (sin 1cos 2
2='''-=-= n b αββ。