切削用量三要素讲解
切削用量三要素

对于外圆车削的深度可用下式计算:
ap=(dw-dm)/ 2 mm
对于钻孔工作: ap=dm/ 2
mm
上两式中
dw—— 待加工表面直径(mm) dm——已加工表面直径(mm)
切削用量及选择
2. 切削用量与切削过程的关系 2.1 对劳动生产率的影响
切削用量三要素vc、f 、 ap 虽然对加工质量、刀具耐用度
在上述情况下,如分二次走刀,第一次的ap也应比第二次大, 第二次的ap可取加工余量的1/3~1/4左右。
切削用量及选择
3 )切削表层有硬皮的铸锻件或切削不锈钢等冷硬较严重的材料时, 应尽量使背吃刀量超过硬皮或冷硬层厚度,以防刀刃过早磨损或破损。
4)在半精加工时,ap=0.5~2 mm 。
5)在精加工时,ap=0.1~0.4 mm 。
切削用量及选择
2.3 对刀具耐用度的影响
2.3.1 刀具耐用度
所谓刀具耐用度,是指一把新刀从开始切削直到 磨损量达到磨损标准为止,在这期间所使用的总的切 削时间,用T表示。
2.3.2 切削速度vc与刀具耐用度的关系
工件材料、刀具材料、几何角度选定后,切削速度是影响 刀具耐用度的主要因素。其原因是当提高切削速度时,单位时 间的金属去除率成正比例增加,刀具与工件及切屑间的摩擦加 剧,消耗于金属变形和摩擦的无用功增加,因而产生大量的热。 因此,提高切削速度的结果:摩擦热大量的积聚在切屑底层而 来不及传导出去,从而使切削温度升高。
形成了工件的外圆表面。在新的表面的形成过程中,工件上 有三个依次变化的表面(见下图):
待加工表面:即将被切去金属层的表面 加工 表 面: 切削刃正在切削着的表面 已加工表面:已经切去一部分金属形 成
切削用量三要素—7
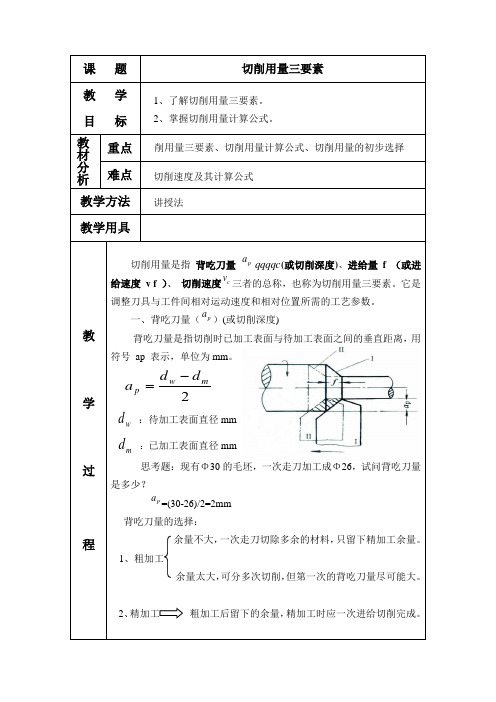
课题切削用量三要素教学目标1、了解切削用量三要素。
2、掌握切削用量计算公式。
教材分析重点削用量三要素、切削用量计算公式、切削用量的初步选择难点切削速度及其计算公式教学方法讲授法教学用具教学过程切削用量是指背吃刀量paqqqqc(或切削深度)、进给量f (或进给速度v f )、切削速度cv三者的总称,也称为切削用量三要素。
它是调整刀具与工件间相对运动速度和相对位置所需的工艺参数。
一、背吃刀量(pa)(或切削深度)背吃刀量是指切削时已加工表面与待加工表面之间的垂直距离,用符号ap 表示,单位为mm。
思考题:现有Φ30的毛坯,一次走刀加工成Φ26,试问背吃刀量是多少?pa=(30-26)/2=2mm背吃刀量的选择:余量不大,一次走刀切除多余的材料,只留下精加工余量。
1、粗加工余量太大,可分多次切削,但第一次的背吃刀量尽可能大。
2、精加工粗加工后留下的余量,精加工时应一次进给切削完成。
2mwpdda-=wd:待加工表面直径mmmd:已加工表面直径mmc v 教学过 程 二、进给量(f )(或进给速度 v f )进给量是指刀具在进给方向上相对工件的位移量,即工件每转一圈,车刀沿进给方向移动的距离,用符号 f 表示,单位为 mm/r ,如图所示。
进给量的选择:1、为了缩短加工时间,提高效率:粗加工时应选用较大的进给量。
2、为了保证表面质量及加工精度:精加工时应选用较小的进给量。
三、切削速度(c v )切削速度是指切削刃上选定点相对于工件主运动的瞬时速度,用符号c v 表示,单位为m/min 。
当主运动是旋转运动时,切削速度是指圆周运动的线速度,即:——切削速度,m/minn ——主轴转速,r/min d ——工件待加工表面直径,mmπ ——圆周率, 3.14例1:车削直径为50mm 的工件,若选主轴转速为600r/min ,求切削速度的大小?解:由公式得:练习: 车削直径为300mm 的铸铁带轮外圆,若切削速度为60m/min ,求车床主轴转速?解:由公式 得:d v n c π1000=min /2.94min /10005014.36001000m m d n V c =⨯⨯==πmin /69.63min /30014.36010001000r r d v n c =⨯⨯==π教学过程四、切削三要素的选择原则:切削用量是衡量车削运动大小的参量。
切削用量三要素讲解

切削用量三要素讲解切削用量是指在机械加工过程中,为了能够获得所需的加工结果,所需要使用的切削刀具的数量。
切削用量的大小直接影响切削加工的效果和成本。
在进行切削加工时,要考虑切削用量的三个要素,即切削宽度、切削深度和进给量。
切削宽度是指刀具沿工件表面的宽度。
切削宽度的大小直接影响切削过程中的切削力、切削温度和切削表面质量。
一般来说,切削宽度越大,切削力越大,切削温度也会相应增加。
此外,切削宽度的大小还决定了每分钟切削量的大小,即工件在单位时间内被切削的体积。
因此,在切削宽度的确定上需要考虑到切削力和切削温度的限制,以及加工效率的要求。
切削深度是指刀具在一次进给中所切下的工件表面的厚度。
切削深度的大小直接影响切削过程中的切削力、切削温度和切削表面质量。
一般来说,切削深度越大,切削力也会相应增加。
此外,切削深度的大小还决定了每分钟切削量的大小。
因此,在切削深度的确定上需要考虑到切削力的限制,以及加工效率的要求。
进给量是指刀具在单位时间内的移动距离。
进给量的大小直接影响切削过程中的切削力、切削温度和切削表面质量。
一般来说,进给量越大,切削力越大,切削温度也会相应增加。
此外,进给量的大小还决定了每分钟切削量的大小。
因此,在进给量的确定上需要考虑到切削力的限制,以及加工效率的要求。
在确定切削用量时,需要综合考虑切削宽度、切削深度和进给量的影响,并找到适合的平衡点。
切削用量的过大或过小都会对切削加工效果产生不利影响。
过大的切削用量会导致切削力过大,加剧刀具磨损和变形,使切削表面质量下降,同时还会增加切削过程中的切削温度,进而影响工件的尺寸精度和表面质量。
而过小的切削用量会使加工效率降低,增加加工时间和成本。
因此,在确定切削用量时,需要根据具体材料、工件形状、加工要求等因素进行综合考虑。
一般来说,在保证切削力、切削温度和切削表面质量在合理范围内的前提下,尽可能选择较大的切削宽度、切削深度和进给量,以提高加工效率。
车床切削用量介绍

车床切削用量介绍车床切削用量介绍切削用量包括切削速度、进给量和背吃刀量(切削深度),俗称切削三要素。
它们是表示主运动和进给运动最基本的物理量,是切削加工前调整机床运动的依据,并对加工质量、生产率及加工成本都有很大影响。
1.切削速度它是指在单位时间内,工件与刀具沿主运动方向的最大线速度。
车削时的切削速度由下式计算:式中:——切削速度(m/s或m/min) ;——工件待加工表面的最大直径(mm);——工件每分钟的转数(r/min)。
由计算式可知切削速度,与工件直径和转数的乘积成正比,故不能仅凭转数高就误认为是切削速度高。
一般应根据与,并求出,然后再调整转速手柄的位置。
切削速度选用原则:粗车时,为提高生产率,在保证取大的切削深度和进给量的情况下,一般选用中等或中等偏低的切削速度,如取50~70m/min (切钢),或40~60m/min(切铸铁);精车时,为避免刀刃上出现积屑瘤而破坏已加工表面质量,切削速度取较高(100 m/min以上)或较低(6 m/min以下),但采用低速切削生产率低,只有在精车小直径的工件时采用,一般用硬质合金车刀高速精车时,切削速度100~200 m/min (切钢)或60~100m/min(切铸铁)。
由于同学对车床的操作不熟练,不宜采用高速切削。
2.进给量 ?它是指在主运动一个循环(或单位时间)内,车刀与工件之间沿进给运动方向上的相对位移量,又称走刀量,其单位为mm/r。
即工件转一转,车刀所移动的距离。
进给量选用原则:粗加工时可选取适当大的进给量,一般取0.15~0.4 mm/r;精加工时,采用较小的进给量可使已加工表面的残留面积减少,有利于提高表面质量,一般取 0.05~0.2 mm/r。
3.背吃刀量(切削深度)车削时,切削深度是指待加工表面与已加工表面之间的垂直距离,又称吃刀量,单位为mm,其计算式为:式中: dw——工件待加工表面的直径(mm);dm——工件已加工表面的直径(mm)。
三、4.切削用量的选择与应用
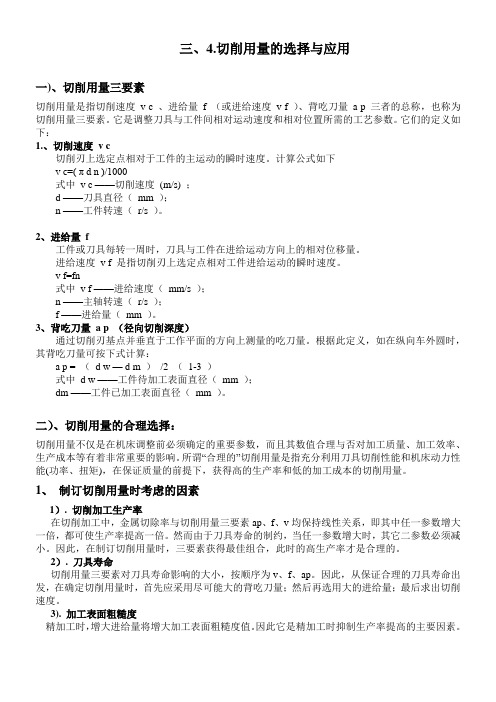
三、4.切削用量的选择与应用一)、切削用量三要素切削用量是指切削速度v c 、进给量 f (或进给速度v f )、背吃刀量a p 三者的总称,也称为切削用量三要素。
它是调整刀具与工件间相对运动速度和相对位置所需的工艺参数。
它们的定义如下:1.、切削速度v c切削刃上选定点相对于工件的主运动的瞬时速度。
计算公式如下v c=( π d n )/1000式中v c ——切削速度(m/s) ;d ——刀具直径(mm );n ——工件转速(r/s )。
2、进给量 f工件或刀具每转一周时,刀具与工件在进给运动方向上的相对位移量。
进给速度v f 是指切削刃上选定点相对工件进给运动的瞬时速度。
v f=fn式中v f ——进给速度(mm/s );n ——主轴转速(r/s );f ——进给量(mm )。
3、背吃刀量 a p (径向切削深度)通过切削刃基点并垂直于工作平面的方向上测量的吃刀量。
根据此定义,如在纵向车外圆时,其背吃刀量可按下式计算:a p = ( d w — d m )/2 (1-3 )式中 d w ——工件待加工表面直径(mm );dm ——工件已加工表面直径(mm )。
二)、切削用量的合理选择:切削用量不仅是在机床调整前必须确定的重要参数,而且其数值合理与否对加工质量、加工效率、生产成本等有着非常重要的影响。
所谓“合理的”切削用量是指充分利用刀具切削性能和机床动力性能(功率、扭矩),在保证质量的前提下,获得高的生产率和低的加工成本的切削用量。
1、制订切削用量时考虑的因素1). 切削加工生产率在切削加工中,金属切除率与切削用量三要素ap、f、v均保持线性关系,即其中任一参数增大一倍,都可使生产率提高一倍。
然而由于刀具寿命的制约,当任一参数增大时,其它二参数必须减小。
因此,在制订切削用量时,三要素获得最佳组合,此时的高生产率才是合理的。
2). 刀具寿命切削用量三要素对刀具寿命影响的大小,按顺序为v、f、ap。
切削用量三要素

切削用量三要素在机械加工过程中,切削用量是影响切削加工质量和生产效率的重要因素之一。
正确的切削用量选择可以提高切削工具的寿命,减少切屑生成,确保加工质量和提高生产效率。
切削用量的选择与切削速度、进给速度和切削深度等因素密切相关,这三个要素可以被认为是切削用量的决定因素。
一、切削速度切削速度是切削用量中最直接影响切削加工的因素之一。
切削速度的选择应考虑切削材料的硬度、切削工具的材料和形状、切削液的冷却效果等因素。
通常情况下,切削速度过高会导致切削工具的快速磨损,增加切削工具的更换次数和维护成本;而切削速度过低则会降低生产效率。
因此,在实际加工过程中,需要合理选择切削速度,以确保切削加工的效果和经济性。
二、进给速度进给速度是指切削工具在单位时间内切削工件的移动速度。
进给速度的选择应综合考虑切削材料的硬度、切削工具的材料和形状、工件表面质量要求等因素。
进给速度过高会导致切削工具与工件之间的磨擦增加,容易引起工件表面质量的损坏;而进给速度过低则会降低生产效率。
因此,在实际加工过程中,需要根据具体情况选择合适的进给速度,以确保加工质量和生产效率。
三、切削深度切削深度是指切削工具切削工件的深度。
切削深度的选择应综合考虑切削工具的结构和刚度、切削材料的硬度、工件的形状和材料等因素。
切削深度过大会导致切削力和切削温度的增加,容易引起切削工具的磨损和断刀现象;而切削深度过小则会降低生产效率。
因此,在实际加工过程中,需要根据具体情况选择合适的切削深度,以确保切削加工的质量和经济性。
综上所述,切削用量的选择应综合考虑切削速度、进给速度和切削深度等三个要素。
合理选择这三个要素可以提高切削工具的寿命,减少切屑的生成,确保加工质量和提高生产效率。
在实际加工过程中,需要根据具体情况进行调整和优化,以达到最佳的切削效果。
切削用量的内容
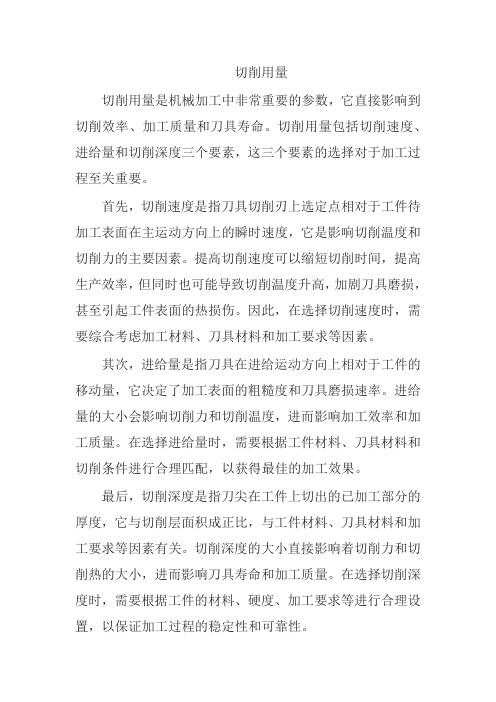
切削用量
切削用量是机械加工中非常重要的参数,它直接影响到切削效率、加工质量和刀具寿命。
切削用量包括切削速度、进给量和切削深度三个要素,这三个要素的选择对于加工过程至关重要。
首先,切削速度是指刀具切削刃上选定点相对于工件待加工表面在主运动方向上的瞬时速度,它是影响切削温度和切削力的主要因素。
提高切削速度可以缩短切削时间,提高生产效率,但同时也可能导致切削温度升高,加剧刀具磨损,甚至引起工件表面的热损伤。
因此,在选择切削速度时,需要综合考虑加工材料、刀具材料和加工要求等因素。
其次,进给量是指刀具在进给运动方向上相对于工件的移动量,它决定了加工表面的粗糙度和刀具磨损速率。
进给量的大小会影响切削力和切削温度,进而影响加工效率和加工质量。
在选择进给量时,需要根据工件材料、刀具材料和切削条件进行合理匹配,以获得最佳的加工效果。
最后,切削深度是指刀尖在工件上切出的已加工部分的厚度,它与切削层面积成正比,与工件材料、刀具材料和加工要求等因素有关。
切削深度的大小直接影响着切削力和切削热的大小,进而影响刀具寿命和加工质量。
在选择切削深度时,需要根据工件的材料、硬度、加工要求等进行合理设置,以保证加工过程的稳定性和可靠性。
综上所述,切削用量的选择对于机械加工过程至关重要。
在实际应用中,需要根据工件材料、刀具材料、加工要求等因素综合考虑,选择合适的切削用量,以达到提高加工效率、减小刀具磨损、保证加工质量的目的。
同时,还需要密切关注加工过程中的切削力和切削热的变化,及时调整切削用量,以保证加工过程的稳定性和可靠性。
切削用量三要素计算公式

切削用量三要素计算公式
切削用量三要素计算公式是针对切削加工过程中的切削速度、进给速度和切削深度的综合计算公式。
其公式如下:
切削用量 = 切削速度× 进给速度× 切削深度
其中,切削速度是指每分钟刀具与工件接触点的实际切削速度,单位为米/分钟;进给速度是指每分钟工件相对于刀具的前进速度,单位为毫米/分钟;切削深度是指一次切削中切削刃进入工件的距离,单位为毫米。
通过计算切削用量,可以帮助确定切削加工过程中工具和工件之间的力和能量转化,为实现理想的加工效果提供依据。
- 1、下载文档前请自行甄别文档内容的完整性,平台不提供额外的编辑、内容补充、找答案等附加服务。
- 2、"仅部分预览"的文档,不可在线预览部分如存在完整性等问题,可反馈申请退款(可完整预览的文档不适用该条件!)。
- 3、如文档侵犯您的权益,请联系客服反馈,我们会尽快为您处理(人工客服工作时间:9:00-18:30)。