DNV动力定位规范
DNV规范电气章节5
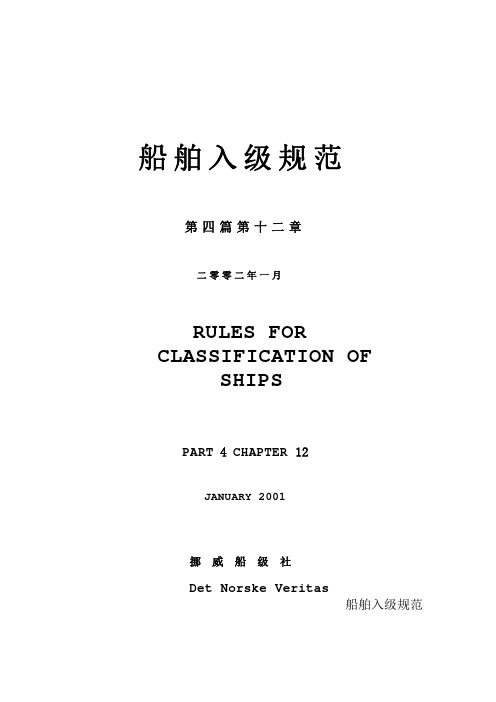
船舶入级规范第四篇第十二章二零零二年一月RULES FOR CLASSIFICATION OFSHIPSPART 4 CHAPTER 12JANUARY 2001挪威船级社Det Norske Veritas船舶入级规范新造船舶机械与系统主船级 第4篇第12章GMDSS 及内部通信2001年1月节 页 1 GMDSS(全球海难及安全系统) (1)2 内部通信 (10)规范更改说明综述理事会2000年12月和2001年6月确定了包括增补和修订在内的现行规范版本,并以此更换本章的1999年7月版。
本章规范的更改于2002年1月1日生效。
本章在被新的修订版替换之前有效。
改版前对规范所作的少量修正和勘误,仅列表刊载在序言分册中,不发增刊。
序言分册通常于每年1月及7月修改。
修改过的各章将发给本规范的所有订户。
建议再版本的购买者核对刊印在第0篇第1章第1节的规范各章的最新目录,以确认该章为现行版本。
主要更改●综述— 新的机械方案要求重新调整第4篇的机械部分内容。
调整的结果是将第9章改编入第12章。
勘误和澄清除了上述的规范修正外,还对规范中某些已发现的错误作了改正,对原规范的措词也做了一些澄清。
第1节 GMDSS(全球性海难及安全系统) (1)A. 一般要求 (1)A 100 适用范围 (1)A 200 GMDSS 装置入级 (1)A 300 型式认可 (2)A 400 改进及附加 (2)A 500 术语、定义及缩写 (2)A 600 免除 (3)B. 船舶要求 (3)B 100 功能要求 (3)B 200 无线电装置 (3)B 300 无线电设备–通则 (4)B 400 无线电设备–海区A1 (4)B 500 无线电设备–海区A1和A2 (5)B 600 无线电设备–海区A1,A2和A3 (6)B 700 无线电设备–海区A1,A2,A3和A4 (7)B 800 值班 (7)B 900 电源 (7)B 1000 性能标准 (8)B 1100 维护要求 (9)B 1200 无线电记录 (9)B 1300 无线电救生装置..................... 9 第2节 内部通信.. (10)A. 一般要求 (10)A 100 应用 (10)A 200 入级 (10)A 300 设计文件 (10)A 400 ATOS 或厂商生产认证书 (10)A 500 船上测量及功能测试 (10)A 600 术语、定义及缩写 (10)B. 船用要求–主船级 (11)B 100 双向电话通信 (11)B 200 播音系统/ 全船报警装置 (11)B 300 电力要求 (12)C. 船用要求–附加等级 (12)C 100 渔船 (12)C 200 油船 (12)C 300 定期无人值班机舱 (12)C 400 动力定位系统 (13)C 500 海上安全 (13)目录A.一般要求A 100 适用范围101 本章要求符合国际海上人命安全公约(SOLAS)第3章和最近修正的第4章中提及规则的第6条,即有关无线电救生装置的内容。
UT771

UT771摘要:本文简要介绍DP(Dynamic Positioning System)动力定位系统的定义,入级附加标志(DP1,DP2,DP3)的基本要求,现以海工平台供应船UT771 WP的工程项目实例进行动力定位系统设计研究,该船入级满足DNV动力定位2级要求,并在DNV检测下进行安装与测试,试验满足DNV动力定位2级要求,主要包括DP操作站,DP主控制箱,信号接口箱, 外围设备, 位置参考系统, 传感器, 独立操作杆系统和相关的操作模式,该文是规则的快速指南,有助于改善船厂,船东和制造商对动力定位系统有更深入的了解,对国内其他准备建造动力定位系统船舶项作一个参考。
关键词:动力定位,位置参考系统,冗余1 定义1.1动力定位船舶:系指仅用推进器的推力保持其自身位置(固定的位置或预先确定的航迹)的船舶。
1.2动力定位系统:系指使动力定位船舶实现动力定位所必须的一整套系统,包括下列分系统:(1)动力源系统(2)推进器系统(3)动力定位控制系统(4)独立操作杆系统1.3入级标志:(1)DYNPOS AUT(DP1)——安装有动力定位系统的船舶,可在规定的环境条件下,自动保持船舶的位置和首向,同时还应设有独立的集中手动船位控制和自动首向控制。
有一套备用遥控推进控制系统和一套备用位置参考信号系统。
(2)DYNPOS AUTR(DP2)——安装有动力定位系统的船舶,在出现单个故障(不包括一个舱室或几个舱室的损失)后,可在规定的环境条件下,在规定的作业范围内自动保持船舶的位置和首向。
自动位置保持系统,技术设计有冗余。
(3)DYNPOS AUTRO(DP3)——安装有动力定位系统的船舶,在出现任一故障(包括由于失火或进水造成一个舱室的完全损失)后,可在规定的环境条件下,在规定的作业范围内自动保持船舶的位置和首向。
自动位置保持系统,技术设计和布置有冗余。
2 系统配置DNV 船级社对动力定位系统不同的入级标志有不同的系统配置要求。
DNV规范

DNV规范(船舶)1998A500 非破坏性试验(NDT)501 一般,焊接接头外表面(包括管子内部可能的区域)要经过外观检查,按管系的级别和接头型式进行无损检测。
对接接头:✧外径大于76.1mm的I级管系,要求100%射线检测,✧外径大于101.6mm的II级管系和外径≤76.1mm的I级管系,至少要10%射线检测。
根据验船师要求,对各种材料要做焊接程序过程控制认可。
角焊:✧对外径大于76.1mm的I级管系,法兰联接的角焊,要求100磁粉检测。
✧对外径大于101.6mm的II级管系和外径≤76.1mm的I级管系,按验船师要求做磁粉检测抽查。
对热油管系对接接头至少附加10%射线检测。
503当焊接质量被认可的条件下,超声波检测可以代替射线检测,对非铁磁性材料,用着色渗透代替磁粉检查。
504NDT是靠操作者根据认可的计划、使用合适的设备和程序来完成的,射线检测要在管线上容易被标识的位置做出标记。
505射线检测按照ISO5817《钢电弧焊焊接接头缺陷质量等级参考》,对于I级管管系焊接用B级质量等级验收,其它用C级。
表面检查(MT、PT)满足ISO5817 B级要求。
506无损检测期间缺陷修理根据验船师同意执行,所有焊接修理要用相关联的检验方法。
D100 无损探伤的范围101 I级压力容器,无损探伤按如下执行:a)筒体、外壳和封头纵向对接焊接接头须100%射线探伤。
b)筒体、外壳和封头环向对接焊接接头须按长度的25%射线探伤。
c)小管和大径管环向对接焊接接头须按总数的10%射线探伤。
d)对筒体外壳嵌入式平板要用超声波检测环缝和平板联接处的层状撕裂。
板厚不大于15mm的外壳板探测范围至少10%,板厚大于15mm至少焊缝总长的20%。
填角焊见第5部分图8,要对表面做100%磁粉检验。
e)对外径超过100mm的竖管和支管,所有与外壳联接处的焊缝及加强板要做磁粉探伤,对于外径不大于100mm,要做点状(少量)检查,外壳与加强板的焊接接头也要做磁粉检测。
dnv规范
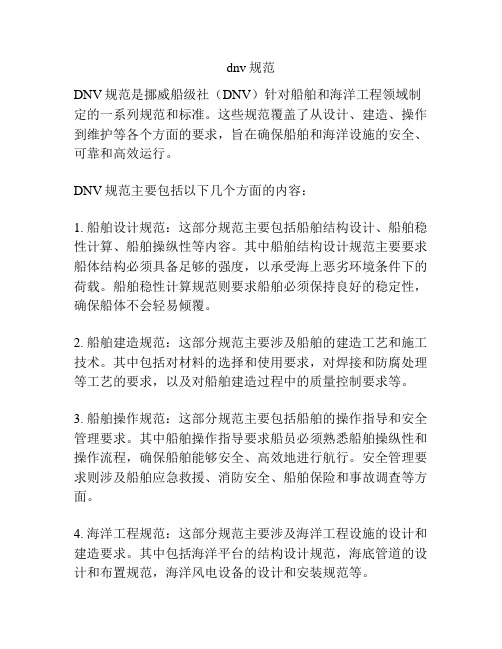
dnv规范
DNV规范是挪威船级社(DNV)针对船舶和海洋工程领域制定的一系列规范和标准。
这些规范覆盖了从设计、建造、操作到维护等各个方面的要求,旨在确保船舶和海洋设施的安全、可靠和高效运行。
DNV规范主要包括以下几个方面的内容:
1. 船舶设计规范:这部分规范主要包括船舶结构设计、船舶稳性计算、船舶操纵性等内容。
其中船舶结构设计规范主要要求船体结构必须具备足够的强度,以承受海上恶劣环境条件下的荷载。
船舶稳性计算规范则要求船舶必须保持良好的稳定性,确保船体不会轻易倾覆。
2. 船舶建造规范:这部分规范主要涉及船舶的建造工艺和施工技术。
其中包括对材料的选择和使用要求,对焊接和防腐处理等工艺的要求,以及对船舶建造过程中的质量控制要求等。
3. 船舶操作规范:这部分规范主要包括船舶的操作指导和安全管理要求。
其中船舶操作指导要求船员必须熟悉船舶操纵性和操作流程,确保船舶能够安全、高效地进行航行。
安全管理要求则涉及船舶应急救援、消防安全、船舶保险和事故调查等方面。
4. 海洋工程规范:这部分规范主要涉及海洋工程设施的设计和建造要求。
其中包括海洋平台的结构设计规范,海底管道的设计和布置规范,海洋风电设备的设计和安装规范等。
总之,DNV规范是船舶和海洋工程领域的重要标准,它不仅
涵盖了船舶和海洋工程设施的设计、建造、操作等方面的要求,更重要的是,它为保障船舶和海洋设施的安全和可靠运行提供了一系列具体的指导和标准。
同时,DNV规范的持续更新和
改进也为船舶和海洋工程行业的发展提供了重要支持。
DNV动力定位简介

the joystick system manufacturer.)
Program(s) for tests and trials (Usually delivered by the control system
manufacturer(s).)
Class Notation DYNPOS AUTS
In addition (not shown):
– 1 Joystick with automatic heading
– Manual levers – 3 UPS`s – Separation is NOT shown for all equipment
�
T = required also for type approved systems Usually delivered by the DP control system manufacturer
Documentation
Thruster documentation
( II )
– According to main class and Pt.6 Ch.7 Sec.4. – Additional calculations and procedures on request (Usually not requested.)
6+00O+HP平台供应船动力定位系统简介

32 动力定位系统的工作方式[ . 4 1
a 自动控制方式 : ) 自动 F A。 和具体船配各系
统进行模拟故障试验, 验证单一的设备或系统( 包括
b 单手柄控制方式 : ) 手动控制船位, 控制船前、
后、 右运动; 左、 自动或手动控制船首向; 。手动控制方式 : ) 分别手动控制各推力器的起 动、 停止、 螺距、 转速或方向;
船( 定点控位、 预定航迹、 跟踪水下机器人即R V O )
等均必须配有动力定位装备。 另外 , 动力定位装备带
来的经济效益剧增, 一条新建的6 H 00 0 P平台供应
船装上动力定位装备, 其租价随即上升到近6 倍。 由 此可见 , 船舶动力定位必然越来越受到人们的普遍
关注 。
定点控位精度可在 3 以内。 m
和船舶运动姿态等外部信号, 动控制主柴油机( 自 推
进螺旋桨)首尾侧推和舵机等动力装置, 、 使船舶对 抗所受风、 浪和流等外力带来的横移、 纵移、 转向和 摇摆, 保持既定的船位, 或通过设定沿着预定的轨迹 运动, 或跟踪水下信标 , 配合海上特殊的调查作业 , 或保持海上施工。在 6 级风、 k 1 n流以下的海况下,
一.牟
一
群r( .p o r s i m
} 』
靴 烹忍 州l
所示 :
40 , 5 V)和一台10 的应急/ 9k W 停泊柴油发电机组
( 4 0 。 AC V) 5
其配电系统( 分区供电严格对称) 如图1 示意 :
a流抹 ^
1 4 枯侧推
6 0 k 1 .
汇涯排 C
汇流排 E
10 11印 H 4 31 z
应急配电饭汇流排
4 0 1 1 3 1 6 F 4 P 0,
DNV挪威船级社规范2003版_中文_6.7动力定位系统
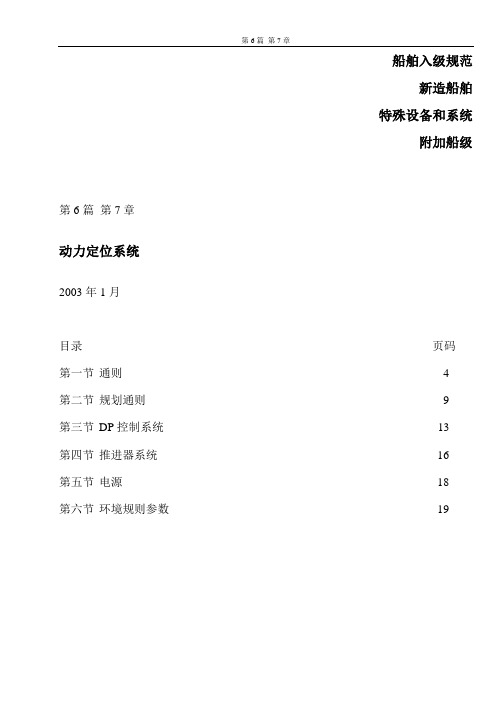
第6篇第7章船舶入级规范新造船舶特殊设备和系统附加船级第6篇第7章动力定位系统2003年1月目录页码第一节通则 4第二节规划通则9第三节DP控制系统13第四节推进器系统16第五节电源18第六节环境规则参数19规范更改说明综述本章为上一版本的重版,也包含一些在2002年7月版本的第0部分第1章第3节列出的修改和勘误,除此之外,没有别的修改。
本章在被新的修订版替换之前有效,改版前对规范所作的少量修正和勘误,仅列表刊载在第0部分第1章第3节中,不会发行新的副刊。
第0部分第1章通常于每年1月及7月修订。
修正过的各章将发给本规范的所有订户,建议再版本的购买者核对刊印在第0篇第1章第1节规范各章的最新目录,以确认该章为现行版本。
目录第1节通则 4A.规则 4 A 100 范围 4 A 200 入级符号 4A 300 环境入级参数 4B. 定义 4 B 100 通则 4 C.证书 5 C 100 通则 5 D.送审文件 5 D 100 通则 5 D 200 ern计算 5 D 300 仪表与自动化 5 D 400 推进器文本 5 D 500 电源系统文本 5 D 600 故障模式响应分析(FMEA) 6 D 700 操作手册 7 D 800 试验和海试程序 7 E.完整的DP系统测试 7 E 70 通则 7 E 200 测量系统 7 E 300 推进器 7 E 400 电源 7 E 500 联合操纵 7 E 600 完整的DP系统测试 8 E 700 DYNPOS-AUTR和DYNPOS-AUTRO的冗余测试8 F.变更8 F 100 船东义务 8第2节规划通则9 A. 通则9A 100 通则 9B. 冗余和故障模式9 B 100 通则9 B 200 冗余9 B 300 故障模式9 B 400 独立性9B 500 对DYNPOS-AUTRO的一般要求10C. 系统规划10 C 100 通则10 C 200 DP控制中心 11 C 300 位置控制系统的规划 11 C 400 控制面板的规划和布置 11C 500 数据通讯链的规划与布置 12D. 内部通讯 12 D 100 通则 12 第3节 DP控制系统13A. 通用要求13A 100 通则13B. 系统规划13B 100 操纵杆推进器控制13B 200 推进器控制模式选择13C. 位置参照系统13C 100 通则13D. 传感器14D 100 通则14F. 监测14F 100 通则14F 200 因果分析15第4节推进器系统16A. 通则16A 100 适用范围16A 200 推进器配置16A 300 推进器控制16A 400 指示16第5节电源17A. 通则17A 100 通则17A 200 发电机的容量和数量17A 300 电源管理(对DYNPOS-AUTR和DYNPOS-AUTRO)17A 400 主配电板和分配电板的规划17B. 控制系统电源18B 100 通则18B 200 软件制造18C. 辅助系统(对DYNPOS-AUTR和DYNPOS-AUTRO)18C 100 通则18C 200 燃油18C 300 冷却水18第6节环境规则参数 19A. 内容描述19A 100 通则19第1节通则A规则A100范围101本节中的规范要求适用于船舶或移动海上平台(后称舰船)的动力定位系统。
概述海上钻井平台的动力定位系统

概述海上钻井平台的动力定位系统动力定位(Dynamic Positioning)系统已经广泛应用于海洋作业船、海洋科考船、深海半潜式钻井平台以及为钻井平台服务的穿梭油轮、储油加工等船舶,目前建造的海洋工程船如风车安装船、穿梭油轮、MPF1000FDPSO和半潜式钻井平台如Sevan650、GM4000等都装备了动力定位系统,这些船根据用途装备的动力定位设备等级不同,因此设备的配置和入级标志也不同,下面作个简单的介绍。
1 动力定位功能及系统组成1.1 动力定位功能动力定位(以下简称DP)是完全依靠推进力方式而不是锚泊方式保持船位(固定位置或预定航线)。
其基本工作原理是利用计算机对接收的卫星定位信号(DGPS)、环境参数(风、浪、流)以及船舶传感器输入的船舶位置信号,自动地与计算机中模拟的预定船位进行比较,推算出保持这一位置需要的各推进器的推力、速度和方向,自动控制推进器工作。
反复地进行比较判断计算和执行控制,使船舶在规定的环境条件下,位置保持在精度允许的范围内。
1.2 DP系统组成DP主要有3大系统组成:电力系统;控制系统;推进系统。
1.2.1 DP电力系统:发电机组;配电系统;功率管理系统。
1.2.2 DP控制系统:计算机及自动控制系统;独立操纵杆系统(手动控制);传感器系统[电罗经、移动参照传感器(MRU)、风向风速传感器];位置参照系统[卫星参照系统GPS、激光参照系统(Laser)、雷达参照系统、无线电参照系统、水声参照系统、张紧索参照系统(Tautwire)]。
2 DP设备等级国际海事组织(IMO)通过的《海上移动式钻井平台构造和设备规则1989修正案》中详细地规定了DP设备等级,其文Msc./Cire.645《采用动力定位系统船舶导则》中规定了DP系统的设备等级分别为3级,即:Class1、Class2、Class3(为叙述方便,本文用DP1、DP2、DP3代表3个动力定位设备等级)。
- 1、下载文档前请自行甄别文档内容的完整性,平台不提供额外的编辑、内容补充、找答案等附加服务。
- 2、"仅部分预览"的文档,不可在线预览部分如存在完整性等问题,可反馈申请退款(可完整预览的文档不适用该条件!)。
- 3、如文档侵犯您的权益,请联系客服反馈,我们会尽快为您处理(人工客服工作时间:9:00-18:30)。
RULES FOR CLASSIFICATION OFD ET N ORSKE V ERITASVeritasveien 1, NO-1322 Høvik, Norway Tel.: +47 67 57 99 00 Fax: +47 67 57 99 11SHIPSNEWBUILDINGSSPECIAL EQUIPMENT AND SYSTEMSADDITIONAL CLASS PART 6 CHAPTER 7DYNAMIC POSITIONING SYSTEMSJANUARY 2004This booklet includes the relevant amendments and correctionsshown in the July 2007 version of Pt.0 Ch.1 Sec.3.CONTENTS PAGESec.1General Requirements (5)Sec.2General Arrangement (11)Sec.3Control System (15)Sec.4Thruster Systems (18)Sec.5Power Systems (19)Sec.6Environmental Regularity Numbers (21)CHANGES IN THE RULESComments to the rules may be sent by e-mail to rules@For subscription orders or information about subscription terms, please use distribution@Comprehensive information about DNV and the Society's services is found at the Web site © Det Norske VeritasComputer Typesetting (FM+SGML) by Det Norske Veritas Printed in NorwayIf any person suffers loss or damage which is proved to have been caused by any negligent act or omission of Det Norske Veritas, then Det Norske Veritas shall pay compensation to such person for his proved direct loss or damage. However, the compensation shall not exceed an amount equal to ten times the fee charged for the service in question, provided that the maximum compen-sation shall never exceed USD 2 million.In this provision "Det Norske Veritas" shall mean the Foundation Det Norske Veritas as well as all its subsidiaries, directors, officers, employees, agents and any other acting on behalf of Det Norske Veritas.General.The present edition of the rules includes additions and amendments decided by the board in November 2003, and supersedes the January 2003 edition of the same chapter.The rule changes come into force on 1 July 2004.This chapter is valid until superseded by a revised chapter. Supple-ments will not be issued except for an updated list of minor amend-ments and corrections presented in Pt.0 Ch.1 Sec.3. Pt.0 Ch.1 is normally revised in January and July each year.Revised chapters will be forwarded to all subscribers to the rules.Buyers of reprints are advised to check the updated list of rule chap-ters printed Pt.0 Ch.1 Sec.1 to ensure that the chapter is current.Main changes—Steering gears shall be designed for continuous operation whenthey form part of the DP-system. Testing requirements to steer-ing gear shall also be specified.—The specific requirement for certification of UPS used for DPcontrol systems is removed. Certification of UPSs now shall fol-low main class requirements in Pt.4 Ch.8 Electrical Systems.—Requirement for certification of the independent joystick systemrequired for notations DYNPOS-AUT , DYNPOS-AUTR and DYNPOS-AUTRO introduced.—The new rules give opening for one of the three gyros requiredfor notation DYNPOS-AUTR and DYNPOS-AUTRO to be re-placed by a heading device based upon another principle, as longas this heading device is type approved as a THD (Transmitting Heading Device) as specified in IMO Res. MSC.116 (73).—The possibility for letting the independent joystick system use the same redundant network as the DP control system is re-moved. In the new rules the independent joystick system may share the communication link with the manual control, but not with the DP-control system.—More specific requirements to the effect of failures in the inde-pendent joystick control system.—Power supply for the independent joystick system is now re-quired to be independent of the DP control system UPSs.—The input power supply to the redundant UPSs is now required derived from different sides of the main switchboard.—Specification of power supply arrangement for position reference systems (PRS). The requirement is now that the power supply shall be in line with the overall redundancy requirements. PRSs shall still be powered from UPS.—The requirement for full separation between fuel oil systems de-signed with redundancy for notation DYNPOS-AUTR is clari-fied.—The new rules require FMEAs for Power Management Systems.—Requirement for DP-Control centre arrangement and layout doc-umentation is introduced.Corrections and ClarificationsIn addition to the above stated rule requirements, a number of correc-tions and clarifications have been made in the existing rule text.Amended,Rules for Ships, January 2004see Pt.0 Ch.1 Sec.3, July 2007 Pt.6 Ch.7 Contents – Page 3D ET N ORSKE V ERITASCONTENTSSEC. 1GENERAL REQUIREMENTS.......................... 5A.The Rules. (5)A 100Rule application................................................................5A 200Class notations..................................................................5A 300Environmental regularity number, ern .. (5)B.Definitions (5)B 100General..............................................................................5C.Certification...........................................................................6C 100General (6)D.Documentation (6)D 100General..............................................................................6D 200ern calculation..................................................................6D 300Instrumentation and automation .......................................6D 400Thruster documentation....................................................7D 500Electric power system documentation..............................7D600DP-Control centre arrangement andlayout documentation........................................................7D 700Failure mode and effect analysis (FMEA)........................7D 800Operation manuals............................................................8D 900Programme for tests and trials (9)E.Survey and Test upon Completion (9)E 100General..............................................................................9E 200Measuring system.............................................................9E 300Thrusters ...........................................................................9E 400Electric power supply........................................................9E 500Independent joystick thruster control system....................9E 600Complete DP-system test..................................................9E 700Redundancy tests for DYNPOS-AUTR andDYNPOS-AUTRO ..........................................................9F.Alterations. (10)F 100Owner obligations (10)SEC. 2GENERAL ARRANGEMENT......................... 11A.General (11)A 100General (11)B.Redundancy and Failure Modes (11)B 100General............................................................................11B 200Redundancy.....................................................................11B 300Failure modes..................................................................11B 400Independence..................................................................11B500General separation requirements forDYNPOS-AUTRO (11)C.System Arrangement (12)C 100General............................................................................12C 200DP-control centre............................................................12C 300Arrangement of positioning control systems..................13C 400Arrangement and layout of control panels......................13C 500Arrangement and layout of data communication links (13)D.Internal Communication (14)D 100General (14)SEC. 3CONTROL SYSTEM ....................................... 15A. General Requirements (15)A 100General (15)B.System Arrangement (15)B 100Independent joystick thruster control system.................15B 200DP-control system...........................................................15B 300Thruster control mode selection.. (15)C.Positioning Reference System (15)C 100General (15)D.Sensors (16)D 100General............................................................................16E.Display Units.. (17)E 100General (17)F.Monitoring (17)F 100Alarm system..................................................................17F 200Consequence analysis (17)SEC. 4THRUSTER SYSTEMS.................................... 18A.General.. (18)A 100Rule application..............................................................18A 200Thruster configuration....................................................18A 300Thruster control...............................................................18A 400Indication (18)SEC. 5POWER SYSTEMS........................................... 19A.General.. (19)A 100General............................................................................19A 200Number and capacity of generators................................19A 300Power management (for DYNPOS-AUTR andDYNPOS-AUTRO ).......................................................19A 400Main and distribution switchboards arrangement (19)B.Control System Power Supply (applies to DYNPOS-AUT , DYNPOS-AUTR and DYNPOS-AUTRO ) (20)B 100General (20)C.Auxiliary Systems (Applies toDYNPOS-AUTR and DYNPOS-AUTRO ) (20)C 100General............................................................................20C 200Fuel oil............................................................................20C 300Cooling water (20)SEC. 6ENVIRONMENTAL REGULARITYNUMBERS.......................................................... 21A.Concept Description.. (21)A 100General (21)Rules for Ships, January 2004Amended, Pt.6 Ch.7 Contents – Page 4see Pt.0 Ch.1 Sec.3, July 2007D ET N ORSKE V ERITASAmended,Rules for Ships, January 2004see Pt.0 Ch.1 Sec.3, July 2007 Pt.6 Ch.7 Sec.1 – Page 5D ET N ORSKE V ERITASSECTION 1GENERAL REQUIREMENTSA. The RulesA 100Rule application101 The rules in this chapter apply to systems for dynamic positioning of ships and mobile offshore units, termed hereaf-ter as, vessels. These rules do not include requirements or rec-ommendations in regard to the vessels operation or other characteristics.Guidance note:Requirements, additional to these rules may be imposed by the national authority with whom the vessel is registered and/or by the administration within whose territorial jurisdiction it is in-tended to operate. Where national legislative requirements exist,compliance with such regulations shall also be necessary.---e-n-d---of---G-u-i-d-a-n-c-e---n-o-t-e---102 The requirements in these rules are additional to the rules for main class.Guidance note:In particular see the relevant sections of:Pt.4 Ch.1 Machinery Systems, General Pt.4 Ch.2 Rotating Machinery, General Pt.4 Ch.3 Rotating Machinery, DriversPt.4 Ch.4 Rotating Machinery, Power Transmissions Pt.4 Ch.5 Rotating Machinery, Driven Units Pt.4 Ch.8 Electrical InstallationsPt.4 Ch.9 Instrumentation and Automation.---e-n-d---of---G-u-i-d-a-n-c-e---n-o-t-e---A 200Class notations201 Vessels built and tested in compliance with the require-ments in this chapter and the requirements of the rules for main class may be assigned one of the class notations given in Table A1.Guidance note:IMO MSC/Circ.645 "Guidelines for vessels with dynamic posi-tioning systems", dated 6 June 1994, has defined equipment classes with the following correlation to these rules:---e-n-d---of---G-u-i-d-a-n-c-e---n-o-t-e---A 300Environmental regularity number, ern301 Vessels with one of the class notations listed in 201 will be given an environmental regularity number (ern). It will be entered as a notation in the "Register of vessels classed with DNV" as ern(a, b, c) where a, b, c are integer numbers re-flecting probable regularity for keeping position in a defined area. See Sec.6 for details on the ern concept.B. DefinitionsB 100General101 Consequence analysis: An automatic monitoring func-tion in the DP-control system, checking the ability of the vessel to maintain position under current weather conditions if the worst case single failure should occur.Guidance note:For detailed information and requirements to the consequence analysis function see Sec.3 F200.---e-n-d---of---G-u-i-d-a-n-c-e---n-o-t-e---102 DP-control system: All control systems and compo-nents, hardware and software necessary to dynamically posi-tion the vessel. The DP-control system consists of the following:—dynamic positioning control system (computer system)—sensor system—display system (operator panels)—positioning reference system—associated cabling and cable routing.Guidance note:The DP-control system will normally consist of one or more computers. This is often referred to as the DP-system, but is only a part of the DP-system by rule terminology.---e-n-d---of---G-u-i-d-a-n-c-e---n-o-t-e---103 Dynamic positioning system (DP-system): The complete installation necessary for dynamically positioning a vessel comprises of the following systems:—power system —thruster system —DP-control system—independent joystick system (when applicable).104 Dynamically positioned vessel (DP-vessel): A vessel which automatically maintains its position (fixed location or predetermined track) exclusively by means of thruster force.Guidance note:In this context thruster force may include propulsion and steeringTable A1 Class notations Notation Scope DYNPOS-AUTS dynamic positioning system without redun-dancy DYNPOS-AUT dynamic positioning system with an inde-pendent joystick system back-up and a posi-tion reference back-up DYNPOS-AUTR dynamic positioning system with redundancyin technical design and with an independent joystick system back-upDYNPOS-AUTRO dynamic positioning system with redundancyin technical design and with an independent joystick system back-up. Plus a back-up dy-namic positioning control system in an emer-gency dynamic positioning control centre, designed with physical separation for compo-nents that provide redundancyDNV class notation IMO equipment class DYNPOS-AUTS Not applicableDYNPOS-AUT IMO equipment class 1DYNPOS-AUTR IMO equipment class 2DYNPOS-AUTRO IMO equipment class 3Rules for Ships, January 2004Amended,Pt.6 Ch.7 Sec.1 – Page 6 see Pt.0 Ch.1 Sec.3, July 2007D ET N ORSKE V ERITAS(rudder) forces, see Sec.4.---e-n-d---of---G-u-i-d-a-n-c-e---n-o-t-e---105 Failure: An occurrence in a component or system caus-ing one or both of the following effects:—loss of component or system function—deterioration of functional capability to such an extent thatthe safety of the vessel, personnel, or environment is sig-nificantly reduced.Guidance note:For vessels that shall comply with DYNPOS-AUTRO require-ments, the definition of single failure has no exceptions, and shall include incidents of fire and flooding, and all technical break-downs of systems and components, including all electrical and mechanical parts. Loss of stability (e.g. as a result of flooding) is not a relevant failure mode.For vessels that shall comply with DYNPOS-AUTR require-ments, certain exceptions will be allowed in the definition of sin-gle failure. Flooding and fire shall not be considered beyond main class requirements. Failure of non-moving components,e.g. pipes, manual valves, cables etc. may not need to be consid-ered if adequate reliability of a single component can be docu-mented, and the part is protected from mechanical damage.---e-n-d---of---G-u-i-d-a-n-c-e---n-o-t-e---106 Joystick: A device for readily setting of vectorial thrust output including turning moment.107 Operational mode: The manner of control under which the DP-system may be operated, e. g.:—automatic mode (automatic position and heading control)—joystick mode (manual position control with selectable au-tomatic or manual heading control)—manual mode (individual control of pitch and speed, azi-muth, start and stop of each thruster)—autotrack mode (considered as a variant of automatic posi-tion control, with programmed movement of reference point).108 Position keeping: Maintaining a desired position within the normal excursions of the control system and the environ-mental conditions.109 Positioning reference system: All hardware, software and sensors that supply information and or corrections neces-sary to give position and heading reference, including power supply.110 Power system: All components and systems necessary to supply the DP-system with power. The power system includes:—prime movers with necessary auxiliary systems includingpiping —generators —switchboards—uninterruptible power supplies (UPS) and batteries —distribution system including cabling and cable routing —for DYNPOS-AUTR and DYNPOS-AUTRO : powermanagement system (PMS).111 Redundancy: The ability of a component or system to maintain or restore its function when one failure has occurred.Redundancy can be achieved, for instance, by installation of multiple components, systems or alternative means of per-forming a function.112 Reliability: The ability of a component or system to per-form its required function without failure during a specified time interval.113 Thruster system: All components and systems necessary to supply the DP-system with thrust force and direction. The thruster system includes:—thruster with drive units and necessary auxiliary systemsincluding piping —thruster control—associated cabling and cable routing—main propellers and rudders if these are under the controlof the DP-system.114 Worst case failure: Failure modes related to the class no-tations as follows:—for DYNPOS-AUTS and DYNPOS-AUT , loss of posi-tion may occur in the event of a single fault—for DYNPOS-AUTR , loss of position is not to occur inthe event of a single failure as specified in Sec.2 B301—for DYNPOS-AUTRO , loss of position is not to occur inthe event of a single failure as specified in Sec.2 B302.C. CertificationC 100General101 The following equipment in the DP-system shall be cer-tified:—dynamic positioning control system—independent joystick control system with auto heading.Other equipment in the DP-system shall be certified according to relevant parts of Pt.4 as for main class.Guidance note:Additionally, components and systems should be certified ac-cording to main class requirements.---e-n-d---of---G-u-i-d-a-n-c-e---n-o-t-e---D. DocumentationD 100General101 The documentation submitted, shall include descriptions and particulars of the vessel and cover the requirements given in 200 to 700, as appropriate.D 200ern calculation201 Calculation of the environmental regularity number evaluation, ern , shall be submitted for approval. The position holding performance shall be quantified according to the con-cept for ern , see Sec.6.D 300Instrumentation and automation301 For general requirements related to documentation of in-strumentation and automation, including computer based con-trol and monitoring, see Pt.4 Ch.9 Sec.1.Guidance note:For description of documentation types, see Pt.4 Ch.9 Sec.1. Ta-ble C1 and C2.---e-n-d---of---G-u-i-d-a-n-c-e---n-o-t-e---302 For the control systems listed, documentation shall be submitted according to Table D1:DYN Dynamic positioning control and monitoring system JOY Independent joystick system TCM Thruster control mode selection PRS Position reference system(s)VEO Wind, VRS and gyroPMSPower Management System.D 400Thruster documentation401 Documentation shall be submitted as required for mainAmended,Rules for Ships, January 2004see Pt.0 Ch.1 Sec.3, July 2007 Pt.6 Ch.7 Sec.1 – Page 7D ET N ORSKE V ERITASclass.402 The following shall be submitted for information:—thrust output and power input curves —response time for thrust changes—response time for direction changes for azimuth thrusters —anticipated thrust reductions due to interaction effects.D 500Electric power system documentation501 Documentation shall be submitted as required for main class.502 Electrical load calculation during dynamic positioning operation shall be submitted for approval. For vessels with the notations DYNPOS-AUTR and DYNPOS-AUTRO the load calculations shall also reflect the situation after the maximum single failure(s).Guidance note:This documentation may be a part of the power consumption bal-ance as required in Pt.4 Ch.8 Electrical Installations.---e-n-d---of---G-u-i-d-a-n-c-e---n-o-t-e---503 For vessels with the notation DYNPOS-AUTRO , the following shall be submitted for approval:—cable routing layout drawing—fire and flooding separation arrangement.Guidance note:For the cable routing layout drawing it is recommended that col-ours are used to indicate the cable routes that are designed and physically arranged to provide redundancy.---e-n-d---of---G-u-i-d-a-n-c-e---n-o-t-e---Guidance note:The cable routing layout drawing shall indicate all cables rele-vant to the DP system, e.g. power cables, control cables, cables used for indication etc.---e-n-d---of---G-u-i-d-a-n-c-e---n-o-t-e---D 600DP-Control centre arrangement and layout docu-mentation601 For notations DYNPOS-AUTS , DYNPOS-AUT ,DYNPOS-AUTR and DYNPOS-AUTRO drawings showing the physical arrangement and location of all key components in the DP-control centre shall be submitted.602 For notation DYNPOS-AUTRO drawings showing the physical arrangement and location of all key components in the emergency DP-control centre shall be submitted.D 700Failure mode and effect analysis (FMEA)701 For vessels with the notations DYNPOS-AUTR and DYNPOS-AUTRO , documentation of the reliability of the dynamic positioning system is required in the form of a failure mode and effect analysis (FMEA).702 The purpose of the FMEA shall give a description of the different failure modes of the equipment when referred to its functional task. Special attention shall be paid to the analysis of systems that may enter a number of failure modes and thus induce a number of different effects on the dynamic position-ing system performance. The FMEA shall include at least the information specified in 703 to 705.703 A breakdown of the dynamic positioning system, into functional blocks shall be made. The functions of each block shall be described. The breakdown shall be performed to such a level of detail that the functional interfaces between the func-tional blocks are shown.704 A description of each physically and functionally inde-pendent item and the associated failure modes with their fail-ure causes related to normal operational modes of the item shall be furnished.705 A description of the effects of each failure mode alone on other items within the system and on the overall dynamic positioning system shall be made.Guidance note:Description of FMEA systematic may be found in IEC Publica-tion 60812 and IMO HSC Code, Annex 4.---e-n-d---of---G-u-i-d-a-n-c-e---n-o-t-e---706 FMEA(s) and redundancy test program(s) shall be kept on board. The FMEA(s) and redundancy test program(s) shall at all times be updated to cover alterations to the DP-system hardware or software.Guidance note:This is not to be understood as a requirement for an FMEA for the software. However the FMEA (or other relevant documenta-tion) should include identification of the software version(s) in-stalled, and documentation giving this information should be updated when new versions are installed.---e-n-d---of---G-u-i-d-a-n-c-e---n-o-t-e---Rules for Ships, January 2004Amended,Pt.6 Ch.7 Sec.1 – Page 8 see Pt.0 Ch.1 Sec.3, July 2007D ET N ORSKE V ERITASD 800Operation manuals801 Operation manuals according to Table D1 shall be kept on board. The manuals shall include information on the DP-system, its installation and structure as well as operation and maintenance.Guidance note:These manuals cover the technical systems. Manuals for DP op-erations are not normally included and may be produced sepa-rately, according to operational requirements.---e-n-d---of---G-u-i-d-a-n-c-e---n-o-t-e---802 They shall at least cover the following:—definitions of symbols and nomenclature—functional description—operating instructions, normal conditions —operating instructions, failure conditions —man and machine communication systems —back-up systems —monitoring—maintenance and periodical performance test —fault-finding procedures.Functional description—different functions including back-up functions shall beexplained in detail.Table D1 Requirements for documentation of instrumentation systemsD010D020D030D040D050D060***)D070D080D090D100D110D120D130D140D150D160For class notation DYNPOS-AUTS :DYN X X X X X X X **)**)**)**)X X *),**)TCM X X X X X X **)**)X PRS X X X X X *),**)VEO X X X X X For class notation DYNPOS-AUT :DYN X X X X X X X **)**)**)**)X X *),**)JOY X X X X X **)X *),**)TCM X X X X X X **)**)X PRS X X X X X *),**)VEO X X X X X For class notation DYNPOS-AUTR :DYN X X X X X X X X **)**)**)**)X X *),**)JOY X X X X X **)X *),**)TCM X X X X X X X **)**)X PRS X X X X X *),**)VEO X X X X X PMS ****)*),**)For class notation DYNPOS-AUTRO :DYN X X X X X X X X X **)**)**)**)X X *),**)JOY X X X X X **)X *),**)TCM X X X X X X X X **)**)X PRS X X X X X X *),**)VEO X X X X X XPMS ****)*),**)Instrumentation systems:Documentation types:DYN Dynamic positioning control and monitoring system JOY Independent joystick system TCM Thruster control mode selection PRS Position reference system(s)VEO Wind, VRS and gyro PMS Power Management System ****)D010 System philosophy (T)D020 Functional description D030 System block diagrams (T)D040 User interface documentation D050 Power supply arrangement (T)D060 Circuit diagramsD070 Instrument and equipment list (T)D080 Cable routing layout drawing (T)D090 Failure mode and effect analysis (FMEA) and redundancy test procedure (T)D100 Software quality plan, based upon life cycle activities D110 Installation manual D120 Maintenance manualD130 Data sheets with environmental specifications D140 Test program for testing at the manufacturer (T)D150 Test program for quay/sea trial (T)D150 Operation manual(T)Required also for type approved systems.*)One copy shall be submitted to approval centre for information only.**)Shall be available during certification and trials. Reference is made to Pt.4 Ch.9. Not to be submitted to the approval centre.***)For essential hardwired circuits (for emergency stop, shutdown, interlocking, mode selection systems, back-up selection systems,etc.). Details of input and output devices and power source for each circuit.****)FMEA for PMS systems is in addition to requirements given in Pt.4 Ch.9.Amended,Rules for Ships, January 2004see Pt.0 Ch.1 Sec.3, July 2007 Pt.6 Ch.7 Sec.1 – Page 9D ET N ORSKE V ERITASOperating instructions—description of the normal operation of the equipment, in-cluding adjustments and change of limit values, possible modes of presentation, starting and stopping systems —description of operation of the DP-system in different op-erational modes—description of transition from one operational mode to an-other.Fault-finding procedures—description of fault symptoms with explanation and rec-ommended corrective actions—instructions for tracing faults back to functional blocks orsystems.D 900Programme for tests and trials901 A programme for tests and trials including redundancy tests shall be submitted for approval. The requirements for the programme are described in E.E. Survey and Test upon CompletionE 100General101 Upon completion, the dynamic positioning system shall be subjected to final tests. The program shall contain test pro-cedures and acceptance criteria.Guidance note:It is assumed that prior to the DP-control system test, all systems and equipment included in the dynamic positioning system have been tested according to main class. This should at least include:-load test according to main class -transfer of thruster control-manual override of thruster control -emergency stop -“ready” signals-failure in thruster command/feedback signals -communication systems-main alarm system as for main class and E0 (if applicable).---e-n-d---of---G-u-i-d-a-n-c-e---n-o-t-e---E 200Measuring system201 All sensors, peripheral equipment, and reference sys-tems shall be tested as part of the complete DP-system.202 Failures of sensors shall be simulated to check the alarm system and the switching logic.E 300Thrusters301 Functional tests of control and alarm systems of each thruster shall be carried out.302 All signals exchanged between each thruster and the DP-system computers shall be checked.303 The different modes of thruster control shall be tested.Proper operation of mode selection shall be verified.E 400Electric power supply401 The capacity of the UPS batteries shall be tested.E 500Independent joystick thruster control system501 All functions of the independent joystick system shall be tested.E 600Complete DP-system test601 The complete DP-system shall be tested in all operation-al modes, with simulation of different failure conditions to tryout switching modes, back-up systems and alarm systems.602 Positioning shall be performed on all possible combina-tions of position reference systems (PRS), and on each PRS as a single system. Selecting and de-selecting of PRS shall also be tested.603 During sea trials the offset inputs for each position ref-erence system and relevant sensors in the dynamic position control system should be verified and demonstrated to the at-tending surveyor by setting out the offsets on drawings. It should be verified that these fit with the actual placing of the equipment.604 Manual override, as required by Sec.3 B202 and Sec.4A302 shall be demonstrated during normal operation and fail-ure conditions.605 A duration test shall be carried out for at least 8 hours with the complete automatic system in operation. All failures shall be recorded and analysed.Guidance note:The time spent on DP operational tests may normally be deduct-ed from the time required for the duration test.---e-n-d---of---G-u-i-d-a-n-c-e---n-o-t-e---606 A high seas trial shall be carried out with full system op-eration for at least 2 hours. The weather conditions must be such that an average load level on the thrusters of 50% or more is required.Guidance note:The test described in 606 is dependent on weather conditions and may be omitted if satisfactory results were obtained from the test described in 605.---e-n-d---of---G-u-i-d-a-n-c-e---n-o-t-e---607 For steering gears included under DP-control a test shall be carried out verifying that maximum design temperature of actuator and all other steering gear components is not exceeded when the rudder is continuously put over from border to border within the limits set by the DP-control system, until tempera-ture is stabilized.Guidance note:The test should be carried out with the propeller(s) running with an average propulsion thrust of not less than 50%, unless the con-trol system ensures that rudder operation is performed at zero propulsion thrust only, upon which the test may be carried out without the propeller(s) running. The test may be carried out at the quay and in any steering gear control mode. Number of steer-ing gear pumps connected and rotation speed are to be the maxi-mum allowed during DP operation.---e-n-d---of---G-u-i-d-a-n-c-e---n-o-t-e---E 700Redundancy tests for DYNPOS-AUTR and DYN-POS-AUTRO701 A selection of tests within each system analysed in the FMEA shall be carried out. Specific conclusions of the FMEA for the different systems shall be verified by tests when redun-dancy or independence is required.702 The test procedure for redundancy shall be based on the simulation of failures and shall be performed under as realistic conditions as practicable.。