精益生产案例-减少搬运浪费8.doc
消除生产中的8大浪费培训教材PPT课件讲义
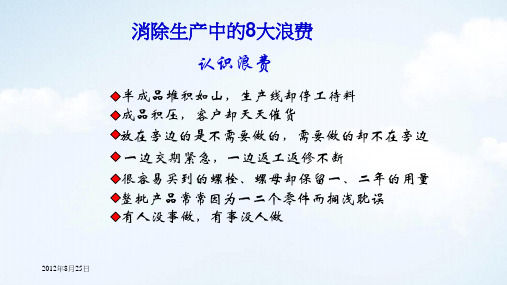
过剩的加工造成浪费
常见的加工浪费: ☆ 加工余量
☆ 过高的精度 ☆ 不必要的加工
过剩加工造成的浪费: ☆ 设备折旧 ☆ 人工损失
☆ 辅助材料损失 ☆ 能源消耗
2012年8月25日
库存 浪费
库存造成额外成本
常见的库存: ☆ 原材料、零部件
☆ 半成品 ☆ 成品 ☆ 在制品 ☆ 辅助材料 ☆ 在途品
库存的危害: ☆ 额外的搬运储存成本
消除生产中的8大浪费 认识浪费
半成品堆积如山,生产线却停工待料 成品积压,客户却天天催货 放在旁边的是不需要做的,需要做的却不在旁边 一边交期紧急,一边返工返修不断 很容易买到的螺栓、螺母却保留一、二年的用量 整批产品常常因为一二个零件而搁浅耽误 有人没事做,有事没人做
2012年8月25日
浪费新定义
除了使产品增值所需的材料,设备和人力资源之绝对最小量以外的东西
任何非必需的东西!
认识和消除所有浪费
2012年8月25日
等待浪费 搬运浪费
地下工厂
8 不良浪费
工
大 厂
动作浪费
常
浪 见
加工浪费
费 的
库存浪费
企业每生产一件产品就在制造一 份浪费。伴随企业运营中各业务 环节不被察觉或不被重视的浪 费,日本企业管理界将之形象地 比喻为“地下工厂”。
制造过多(过早)浪费
缺货损失
2012年8月25日
等待 浪费
2012年8月25日
等待பைடு நூலகம்创造价值
常见的等待现象: ☆ 物料供应或前工序能力不足造成待料
☆ 监视设备作业造成员工作业停顿 ☆ 设备故障造成生产停滞 ☆ 质量问题造成停工 ☆ 型号切换造成生产停顿
造成等待的常见原因: ☆ 线能力不平衡
精益生产管理八大浪费与解决方法(详细版)4.doc

精益生产管理八大浪费与解决方法(详细版)4大纲:(一)制造过早(多)的浪费(二)库存的浪费(三)不良修正的浪费(四)加工过剩的浪费(五)搬运的浪费(六)动作的浪费(七)等待的浪费(八)管理的浪费八大浪费是丰田生产方式中非常重要的一个观念。
丰田人认为要消除浪费,持续改善,企业才能保持良性运转,竞争力才会提升。
在丰田改善是探入人心的,有个说法就是跟他们谈话5分钟没有听到他们讲3次改善就不算丰田人。
改善的对象是浪费,认识浪费是改善的第一步,企业现场林林总总,哪些是有价值的,哪些是浪费,不是一般人可以一目了然的。
丰田人在长期作业和改善过程中对于浪费的内容进行了总结,共七种,被称为七种浪费。
它们分别是制造过早(多)的浪费、库存的浪费、不良修正的浪费、加工过剩的浪费、搬运的浪费、动作的浪费、等待的浪费共七种。
后来人们又加了一种浪费-管理的浪费,合称八种浪费。
下面我们从实用性角度剖析这八种浪费。
(一)制造过早(多)的浪费定义:所谓制造过早(多)就是前制程制造太早/过多,大于客户(或后制程)当期的最小需要量。
制造过早(多)浪费是八大浪费中的首恶,在精益生产中则被视为最大的浪费。
福特式思维告诉大家,在同样的时间内,生产量越多,效率越高,成本越低,企业越赚钱,所以企业自然有大批量连续生产的初始动力。
作为一个整体的企业是如此,那么企业内各部门也是如此,特别是在一些制程较短,关联性较低的企业中,普遍实施计件工资,那么从最基础的员工开始就有多做、早做,甚至偷做的动力,在这种情况下,告知企业里所有人早(多)做是罪恶当然得不到掌声回应。
那么我们就来看看制造过早(多)的浪费。
制造过早(多)浪费的后果主要有三大类。
1.直接财务问题。
表现为库存、在制品增加,资金回转率低,制造时间变长,占用资金及利息,会造成库存空间的浪费,在现金流量表上很明显。
2.产生次生问题。
会产生搬运、堆积的浪费;先进先出的工作产生困难;产品积压造成不良发生,物流阻塞制程时间变长,现场工作空间变小,有滞留在库的风险,有不良品的风险。
八大浪费与改善方法案例
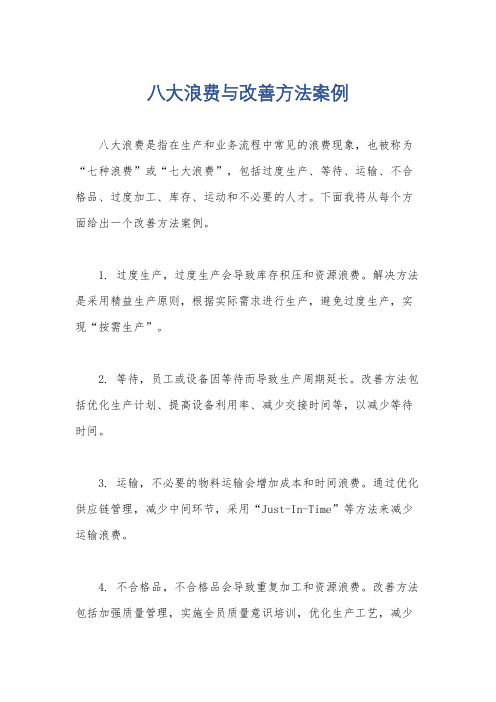
八大浪费与改善方法案例八大浪费是指在生产和业务流程中常见的浪费现象,也被称为“七种浪费”或“七大浪费”,包括过度生产、等待、运输、不合格品、过度加工、库存、运动和不必要的人才。
下面我将从每个方面给出一个改善方法案例。
1. 过度生产,过度生产会导致库存积压和资源浪费。
解决方法是采用精益生产原则,根据实际需求进行生产,避免过度生产,实现“按需生产”。
2. 等待,员工或设备因等待而导致生产周期延长。
改善方法包括优化生产计划、提高设备利用率、减少交接时间等,以减少等待时间。
3. 运输,不必要的物料运输会增加成本和时间浪费。
通过优化供应链管理,减少中间环节,采用“Just-In-Time”等方法来减少运输浪费。
4. 不合格品,不合格品会导致重复加工和资源浪费。
改善方法包括加强质量管理,实施全员质量意识培训,优化生产工艺,减少不合格品产生。
5. 过度加工,指超出产品要求的加工步骤,增加了成本和时间。
改善方法是重新评估生产流程,简化加工步骤,精简生产工艺。
6. 库存,过多的库存会增加资金占用和风险。
采用精益库存管理,通过精确预测和准确订单管理来降低库存水平,避免过多库存。
7. 运动,指员工不必要的移动或动作,增加了生产时间和疲劳。
改善方法包括优化工作站布局,减少不必要的移动,提高工作效率。
8. 不必要的人才,指员工的潜力未得到充分利用。
改善方法包括进行员工技能培训,激励员工提出改进建议,充分发挥员工的潜力。
通过以上改善方法案例,可以有效地减少八大浪费,提高生产效率,降低成本,增强企业竞争力。
同时,这些改善方法也体现了精益生产和持续改进的理念,对于企业的可持续发展具有重要意义。
精益化管理(八大浪费)

4. 让闲置的“动”起来
5.应付现象最常见
6. 拒绝“低效”反复发生
7. 管理必须真正有“理”可依
2024/8/5
41
八﹑管理浪费
(三) 浪费的产生: 管理能力: 政策规定的执行力 技朮层次: 认知高度;把握度; 标准化: 可行度;推广度; 企业素质: 整体素质
2024/8/5
42
八﹑管理浪费
(四) 浪费的消除:
2024/8/5
13
不良浪费案例- -对策&效果
改善对策:
增加EPE泡棉隔板﹐ 避免产品与真空盘相碰
改善效果:
碰挂伤不良率为0%, 取消两名重工人员
2024/8/5
14
二. 制造过多(过早)的浪费
(一)定义:是由制程设定过长﹑生产计划未平准化 ﹑工作负荷不平衡﹑超常规设计﹑多余检验等造 成的制造过多于下一道工序需求的浪费
我可以请求你们,每天至少做一小时
有价值的工作吗?
--大野耐一
2024/8/5
51
课程实践计划
序号 1
实践项目
具体内容5W2H
备注
识别并消 除浪费
发现八大浪费各1个以上,并 用照片、视频、数据等形式展
现;
至少提出2个浪费的解决方法
一周内完 成
2024/8/5
52
ቤተ መጻሕፍቲ ባይዱ
作业:识别生产中的八种浪费
序号 看到什么 浪费类型
双手同时进行动作
缩短动作的距离
轻松动作
2024/8/5
37
动作浪费案例-现状描述
车间抛磨工序:作业员把修整好的产品直接放置在地 面,造成重复盛装、点数,影响产品质量
重 复 动 作 浪 费 时 间
搬运的浪费改善案例

搬运的浪费改善案例搬运是指在物流过程中将货物从一个场所转移到另一个场所的活动。
搬运过程中存在很多浪费,例如时间浪费、人力浪费、能源浪费等。
针对这些浪费,下面将介绍一个改善案例来减少搬运过程中的浪费。
这个案例是一个电子产品仓库的改善案例。
原仓库的布局不合理,搬运物品的路线太长,导致搬运过程耗时长,效率低下。
为了改善这一情况,仓库管理团队决定进行重新布局。
首先,他们进行了仓库内环境的分析,发现很多货物都是由仓库的一侧运往另一侧,因此他们决定重新设计货物流动的路径。
根据货物的流动情况,将不同类型的货物按照使用频率进行划分,将高频率使用的货物放置在靠近入口的位置,而低频率使用的货物放置在远离入口的位置。
这样一来,搬运员只需要走短距离就能够搬运到货物,大大减少了搬运时间。
其次,为了进一步提高搬运效率,在仓库内设置了标识和指示牌。
他们在每一个货物摆放区域的上方设置了明显的标识,包括货物的种类和编号,在每一个转角和交叉口处设置了指示牌,标明不同的区域和路线。
这些标识和指示牌的设置,方便了搬运员快速找到所需货物,并且保证了货物的流动路径清晰可见,避免了搬运员的迷路和浪费时间。
另外,他们还引入了一些仓库自动化设备,如货架上的自动传送带和堆垛机器人。
这些设备可根据搬运员的指令自动将货物从储存区域送至搬运区域。
通过使用这些自动化设备,不仅能够减少人力搬运的工作量,还能够提高搬运的安全性和准确性。
最后,他们建立了一个搬运作业的标准化操作程序。
这个程序包括了货物的摆放标准、操作流程、安全操作规范等。
每一个搬运员都需要经过培训并按照这个程序进行操作。
标准化操作程序的实施,有助于提高搬运员的工作效率和工作质量,并减少人为因素导致的搬运浪费。
这个案例中的改善措施,在搬运过程中有效地减少了时间浪费、人力浪费和能源浪费。
通过重新布局仓库,合理设置货物流动的路径,并引入自动化设备和标准化操作程序,成功地改善了搬运过程中的浪费问题,提高了搬运效率,降低了成本,提升了客户满意度。
精益生产管理之八大浪费与解决方法(十六)

精益生产管理之八大浪费与解决方法(十六)七、等待的浪费(二)第二种情况就是解决人本身等待的问题。
举例:T公司铣削制程有4台机器,每台机器l个人,分别每人看1台,作业流程分别为:①人取产品,装夹产品(10秒)。
②机器作业,人等待(60秒)。
③人取产品,装夹产品(l0秒),然后依次循环。
则周期时间10+10=70秒,人的利用率为10/70=14.3%,机器利用率60/7O=85.7%。
在此案例中,机器作业时间远长于人作业时间,造成人等待和利用率只有14%。
见图4。
(7)品质问题造成的停机等待。
生产中良率不会是100%,但稳定的生产中品质是可控的,变异很小的,是可以在生产计划时预见的。
而造成停机等待的品质问题指的是突然的批量性的问题,这时会造成生产的混乱,会安排重新生产、修机修模、返工、工程重新验证、找客户签样板等。
这个问题导致的等待和来料原因导致的等待有相似之处,就是比较突然,非连续性和可预见性,通常在这时人和机就在等待。
(8)最小搬运量定额太高,搬运批次少。
(9)管理造成的人、机等待(如安排不当、开会、操作不熟练等)。
3.等待浪费的影响。
(1)延长L/T。
等待对生产周期有直接的影响。
等待的累计时间越长,产品的生产周期自然就越长。
(2)成本压力增加。
机器及人力闲置直接导致成本中固定成本部分的平均摊销变大,增加了成本压力。
4.等待浪费的消除方法。
(1)平衡产能。
第一种情况:利用生产线平衡法、制程间产能平衡法对生产线/制程进行平衡分析。
如下图所示。
改善前有A-F共6个工站(制程),生产线不平衡,平衡率只有82%,等待较多。
而改善后减少了一个工站,只有A一E共5个工站(制程),同时平衡率96%,减少了很多等待。
第二种情况:在产能平衡中经常用到的,对于生产速度不同,标准工时差异大的制程通常采用机器数量调节与班(日)生产时间调节的方式。
如上图等待浪费示意图(1)例子所示可以改善成为等待浪费示意图(3)的样子。
精益生产之八大浪费.doc

精益生产之_八大浪费11.不良、修理的浪费所谓不良、修理的浪费,指的是由于工厂内出现不良品,需要进行处置的时间、人力、物力上的浪费,以及由此造成的相关损失。
这类浪费具体包括:材料的损失、不良品变成废品;设备、人员和工时的损失;额外的修复、鉴别、追加检查的损失;有时需要降价处理产品,或者由于耽误出货而导致工厂信誉的下降。
2.加工的浪费加工的浪费也叫过分加工的浪费,主要包含两层含义:第一是多余的加工和过分精确的加工,例如实际加工精度过高造成资源浪费;第二是需要多余的作业时间和辅助设备,还要增加生产用电、气压、油等能源的浪费,另外还增加了管理的工时。
3.动作的浪费动作的浪费现象在很多企业的生产线中都存在,常见的动作浪费主要有以下12种:两手空闲、单手空闲、作业动作突然停止、作业动作过大、左右手交换、步行过多、转身的角度太大,移动中变换“状态”、不明技巧、伸背动作、弯腰动作以及重复动作和不必要的动作等,这些动作的浪费造成了时间和体力上的不必要消耗。
4.搬运的浪费从精益生产的角度看,搬运是一种不产生附加价值的动作,而不产生价值的工作都属于浪费。
搬运的浪费具体表现为放置、堆积、移动、整列等动作浪费,由此带来物品移动所需空间的浪费、时间的浪费和人力工具的占用等不良后果。
国内目前有不少企业管理者认为搬运是必要的,不是浪费。
因此,很多人对搬运浪费视而不见,更谈不上去消灭它。
也有一些企业利用传送带或机器搬运的方式来减少人工搬运,这种做法是花大钱来减少工人体力的消耗,实际上并没有排除搬运本身的浪费。
5.库存的浪费按照过去的管理理念,人们认为库存虽然是不好的东西,但却是必要的。
精益生产认为,库存是没有必要的,甚至认为库存是万恶之源。
由于库存很多,将故障、不良品、缺勤、点点停、计划有误、调整时间过长、品质不一致、能力不平衡等问题全部掩盖住了。
例如,工厂生产线出现故障,造成停机、停线,但由于有库存而不至于断货,这样就将故障造成停机、停线的问题掩盖住了,耽误了故障的排除。
生产中关于搬运浪费.doc
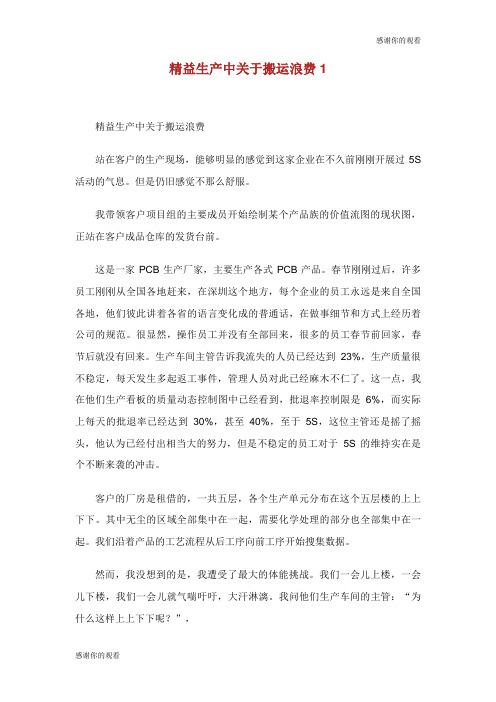
精益生产中关于搬运浪费1精益生产中关于搬运浪费站在客户的生产现场,能够明显的感觉到这家企业在不久前刚刚开展过5S 活动的气息。
但是仍旧感觉不那么舒服。
我带领客户项目组的主要成员开始绘制某个产品族的价值流图的现状图,正站在客户成品仓库的发货台前。
这是一家PCB生产厂家,主要生产各式PCB产品。
春节刚刚过后,许多员工刚刚从全国各地赶来,在深圳这个地方,每个企业的员工永远是来自全国各地,他们彼此讲着各省的语言变化成的普通话,在做事细节和方式上经历着公司的规范。
很显然,操作员工并没有全部回来,很多的员工春节前回家,春节后就没有回来。
生产车间主管告诉我流失的人员已经达到23%,生产质量很不稳定,每天发生多起返工事件,管理人员对此已经麻木不仁了。
这一点,我在他们生产看板的质量动态控制图中已经看到,批退率控制限是6%,而实际上每天的批退率已经达到30%,甚至40%,至于5S,这位主管还是摇了摇头,他认为已经付出相当大的努力,但是不稳定的员工对于5S的维持实在是个不断来袭的冲击。
客户的厂房是租借的,一共五层,各个生产单元分布在这个五层楼的上上下下。
其中无尘的区域全部集中在一起,需要化学处理的部分也全部集中在一起。
我们沿着产品的工艺流程从后工序向前工序开始搜集数据。
然而,我没想到的是,我遭受了最大的体能挑战。
我们一会儿上楼,一会儿下楼,我们一会儿就气喘吁吁,大汗淋漓。
我问他们生产车间的主管:“为什么这样上上下下呢?”,他说:“我们当初就是这样设计的。
”“你们的产品每天就这样上上下下吗?”“是呀,一直这样。
”“为什么不按照生产工艺流程的顺序设计呢?”“我们当初设计的时候根本没有考虑这么多,这样也干了多年了。
”“那你们的产品流程就这样人为的被中断了,工序间的在制品数量将是十分惊人的,每个产品从投料到生产完工的时间被人为的拉长了。
”这位负责人很惊诧,“是的,的确时间很长,我们一直苦恼赶工的问题,客户经常催交,我们的及时交货率一直很低,为此,领导正在**地开始策划办一个分公司。
- 1、下载文档前请自行甄别文档内容的完整性,平台不提供额外的编辑、内容补充、找答案等附加服务。
- 2、"仅部分预览"的文档,不可在线预览部分如存在完整性等问题,可反馈申请退款(可完整预览的文档不适用该条件!)。
- 3、如文档侵犯您的权益,请联系客服反馈,我们会尽快为您处理(人工客服工作时间:9:00-18:30)。
精益生产案例-减少搬运浪费8
编者按:从JIT的角度来看,搬运是一种不产生附加价值的动作,而不产生价值的工作都属于浪费。
搬运的浪费具体表现为放置、堆积、移动、整列等动作浪费,由此而带来物品移动所需空间的浪费、时间的浪费和人力工具的占用等不良后果。
所谓“大件产品”是指比汽车还大的玩意(纯属个人定义),比较笨重的家伙,比如火车、飞机、轮船等,节拍时间比较长(一般来说是以天或者小时计算的),搬运工具以行车、铲车为主,因此搬运成为了这类企业最典型的浪费之一。
之前有看过波音公司的精益生产案例,但体会不是直接的。
大量的搬运存在整个流程中:包括车体的搬运、零件的搬运,这些时间可能占据整个组装生产一半以上,这些搬运都是吊在半空中进行的,站在那里几分钟就可能有心惊肉跳的感觉。
不管从效率还是从安全考虑,这些搬运都亟待改善。
在精益生产方式中,其中有一点提到要“减少行车和叉车”的搬运模式,而且最好是取消。
从短期来说,要消除这些行车的搬运方式还是相当困难,但最起码通过缩短搬运路线可以减少很多。
改变内容包括:生产线改造,把固定的生产线改成流水线,代加工的车体可以依次通过生产线,将出口与入口分开,减少车体的搬运次数和搬运距离。
把按零件分类储存的方式改变为按工序将零件集中放置的方式,减少零件搬运路线和时间。
可实现的效果包括搬运距离缩短,总装工序的周期时间减少并能节约很多场地。
如果场地足够,或把仓库等进行重新布局,有可能将涂装、焊接都连接起来,整个产品生产周期和效率都将大幅度改进。
华致赢企管认为:国内目前有不少企业管理者认为搬运是必要的,不是浪费。
因此,很多人对搬运浪费视而不见,更谈不上去消灭它。
也有一些企业利用传送带或机器搬运的方式来减少人工搬运,这种做法是花大钱来减少工人体力的消耗,实际上并没有排除搬运本身的浪费。
减少搬运的浪费最重要的是减少搬运的次数,所以企业生产还是要符合后拉式看板生产,以达到在接到订单后就生产所需产品的数量,生产完后直接运送到客户手里,以减少库存的产生,减少了搬运的次数。