起重机械事故案例分析
起重机械典型事故案例选编

起重机械典型事故案例选编起重机械是在工业生产和建筑施工过程中常用的一种设备,但由于操作不当、设备老化等原因,容易发生事故。
以下是典型的起重机械事故案例选编。
案例1:起重机坠落事故2024年,建筑工地上,一架塔式起重机突然发生倾覆坠落,导致多人受伤。
事故发生时,起重机正从地面上起吊一个重型构件,但由于操作不当,起重机失去平衡并迅速倾覆。
初步调查发现,起重机在安装过程中没有按照要求进行固定,并且操作人员没有正确操作起重机导致倾覆。
案例2:起重机翻车事故2024年,港口码头上的一台起重机在进行堆积货物作业时突然发生翻车事故,致使多人死亡。
事故发生时,起重机正在将货物装卸到一个船上,由于货物超出了起重机的额定载荷,导致起重机失去平衡并翻车。
经调查发现,事故的主要原因是操作人员没有正确评估起重机的承载能力,以及没有按照操作规程进行作业。
案例3:起重机维修事故2024年,工厂内的一台起重机在进行维修时发生事故,导致一人受伤。
事故发生时,维修人员正在对起重机的电气系统进行维修,但由于未采取必要的安全措施,工人触碰到高压线导致电击伤害。
事后调查发现,事故的主要原因是工人没有按照维修规范操作,未切断电源和通风设备。
案例4:塔吊溃落事故2024年,工地上的一座塔吊突然发生溃落事故,导致多人被埋压。
事故发生时,塔吊正在进行高空作业,突然出现横歪并迅速坍塌。
调查发现,事故的主要原因是塔吊的结构缺陷以及施工方没有及时检测和维护塔吊设备。
以上案例反映了起重机械事故的一些典型情况,这些事故都给工业生产和施工带来了较大的伤害和经济损失。
为了避免这类事故的再次发生,必须加强起重机械的操作培训,确保操作人员熟悉设备使用要求和安全规程。
同时,需加强设备的维护和定期检验,及时发现和排除潜在的安全隐患。
另外,应加强对起重机械的设计和制造质量监督,确保设备的安全性能符合标准。
只有全面落实安全措施,才能有效预防起重机械事故的发生。
起重机械伤人案例及分析

案例一 某国际大厦工程施工升降机 吊笼坠落事故
• 1、事故概况 1996年8月28日,某国际大厦工程SCD120/120施工 升降机发生故障,工人在维修过程中,吊笼从95.4米高度 坠落,造成吊笼内三名工人当场死亡的重大设备伤亡事故。 • 2、事故经过 1996年8月28日下午五时许,该施工升降机操作工向 现场设备员反映,开机时设备有异响,设备员派两名修理 工前往修理。经检查,修理工发现天梁导向滑轮损坏,则 开动一侧吊笼上升至26层,将该吊笼对重落地,修理工再 将吊笼顶部与配重连接的钢丝绳解开并固定在施工升降机 导轨架顶部横梁上,吊笼当即下滑一段距离,限速器动作, 制动吊笼下滑,此时吊笼停在离地面95.4m的高度上。修 理工用一段钢丝绳将吊笼临时悬挂在导轨架标准节上,然 后拆卸限速器。限速器一拆下,该吊笼立即从95.4m高空 坠落,造成吊笼内3人当场死亡的重大设备伤亡事故。
• 3、事故原因
• (1)事故直接原因 使用时施工升降机上极限开关曲臂未固 定,使高度电气限位功能失效,上极限限 位撞块、天轮架未安装,使高度机械限位 功能失效;无证上岗司机违章操作,将吊 笼开出导轨架,此时无任何安全保护装置 对吊笼起限位保护作用,导致吊笼冒顶倾 翻坠落,笼内人员当场死亡。
• (2)事故主要原因 • 1)管理混乱: • ① 安装单位未制定施工升降机安装的技术监管措 施和组织措施,未落实严格的安装验收手续,施 工升降机尚未安装结束就交付使用; • ② 安排无证人员安装设备、无证人员担任司机; • 2)设备使用单位未履行施工升降机交接验收手续, 就安排工人搭乘施工升降机,默许无证人员操作 施工升降机; • 3)施工升降机生产厂家未按订货合同完全履行相 应的安装技术指导、设备调试职责,技术人员在 施工升降机未安装结束的情况下就撤离现场; • 4)监理单位对尚未安装结束的施工升降机投入使 用的情况失察。
吊车事故案例法律分析(3篇)

第1篇一、案例背景某建筑公司在进行一栋高层住宅的建设过程中,因吊车操作不当导致吊车倾覆,造成现场施工人员3人死亡、5人受伤,直接经济损失达数百万元。
事故发生后,相关部门对事故进行了调查,认定该起事故为一起因吊车操作不当引起的重大责任事故。
本文将从法律角度对这起吊车事故进行案例分析。
二、事故原因分析1. 吊车操作人员违规操作根据事故调查报告,事故发生的主要原因是吊车操作人员违规操作。
操作人员未严格按照吊车操作规程进行作业,未对吊车进行全面检查,导致吊车存在安全隐患。
2. 施工单位管理不善施工单位在事故发生前,对吊车操作人员的安全培训、安全教育不到位,未对吊车进行定期检查和维护,导致吊车存在安全隐患。
3. 监理单位监管不力监理单位在事故发生前,对施工现场的安全生产监管不力,未及时发现和纠正施工单位存在的问题,导致事故发生。
三、法律分析1. 事故责任认定根据《中华人民共和国安全生产法》和《中华人民共和国行政处罚法》的相关规定,事故责任应依法认定。
本案中,吊车操作人员、施工单位、监理单位均存在违法行为,应承担相应的法律责任。
(1)吊车操作人员:吊车操作人员违规操作,直接导致事故发生,应承担主要责任。
(2)施工单位:施工单位未对吊车进行定期检查和维护,未对操作人员进行充分的安全培训和教育,应承担次要责任。
(3)监理单位:监理单位对施工现场的安全生产监管不力,未及时发现和纠正施工单位存在的问题,应承担次要责任。
2. 法律责任追究(1)吊车操作人员:吊车操作人员应承担刑事责任,根据《中华人民共和国刑法》的相关规定,可能构成重大责任事故罪。
(2)施工单位:施工单位应承担相应的行政处罚,如罚款、吊销安全生产许可证等。
(3)监理单位:监理单位应承担相应的行政处罚,如罚款、吊销安全生产许可证等。
3. 民事赔偿根据《中华人民共和国侵权责任法》的相关规定,事故受害人有权要求侵权人承担民事赔偿责任。
本案中,事故受害人可向吊车操作人员、施工单位、监理单位提起民事诉讼,要求其承担相应的民事赔偿责任。
起重事故伤害案例
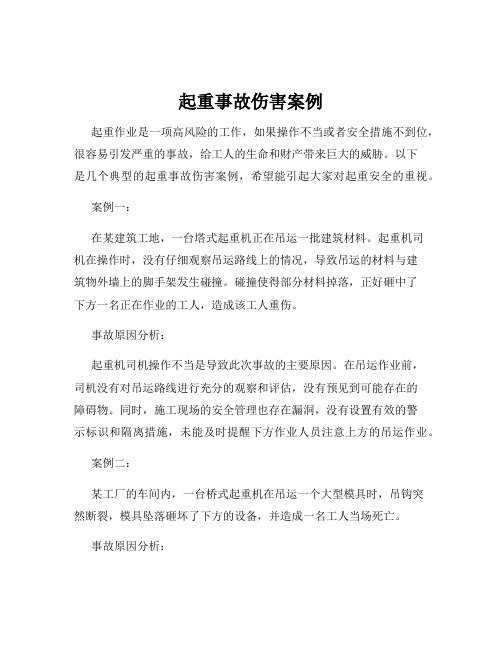
起重事故伤害案例起重作业是一项高风险的工作,如果操作不当或者安全措施不到位,很容易引发严重的事故,给工人的生命和财产带来巨大的威胁。
以下是几个典型的起重事故伤害案例,希望能引起大家对起重安全的重视。
案例一:在某建筑工地,一台塔式起重机正在吊运一批建筑材料。
起重机司机在操作时,没有仔细观察吊运路线上的情况,导致吊运的材料与建筑物外墙上的脚手架发生碰撞。
碰撞使得部分材料掉落,正好砸中了下方一名正在作业的工人,造成该工人重伤。
事故原因分析:起重机司机操作不当是导致此次事故的主要原因。
在吊运作业前,司机没有对吊运路线进行充分的观察和评估,没有预见到可能存在的障碍物。
同时,施工现场的安全管理也存在漏洞,没有设置有效的警示标识和隔离措施,未能及时提醒下方作业人员注意上方的吊运作业。
案例二:某工厂的车间内,一台桥式起重机在吊运一个大型模具时,吊钩突然断裂,模具坠落砸坏了下方的设备,并造成一名工人当场死亡。
事故原因分析:经过调查,发现吊钩存在严重的疲劳裂纹,这是导致吊钩断裂的直接原因。
而工厂在设备维护方面存在疏忽,没有定期对起重设备的吊钩进行检查和维护,未能及时发现吊钩的安全隐患。
此外,操作人员在吊运前也没有对吊钩进行仔细的检查,没有及时发现吊钩的异常情况。
案例三:在一个港口码头,一台门式起重机在吊运集装箱时,由于起重机的制动系统突然失灵,导致起重机失控,撞上了旁边的一艘货轮,造成起重机严重损坏,货轮也受到了一定程度的损伤,同时还有两名工人受伤。
事故原因分析:起重机制动系统故障是此次事故的主要原因。
可能是由于制动系统的零部件老化、磨损或者维护不当,导致制动性能下降。
同时,港口的安全管理制度也不够完善,对于起重设备的日常检查和维护工作没有落实到位,没有及时发现并排除制动系统的故障隐患。
案例四:某物流仓库内,一台电动葫芦在吊运货物时,电动葫芦的钢丝绳突然断裂,货物坠落砸坏了仓库内的货架,并引发了火灾。
事故原因分析:钢丝绳断裂的原因是由于长期使用导致的磨损和锈蚀,超过了其承载能力。
塔式起重机事故案例分析
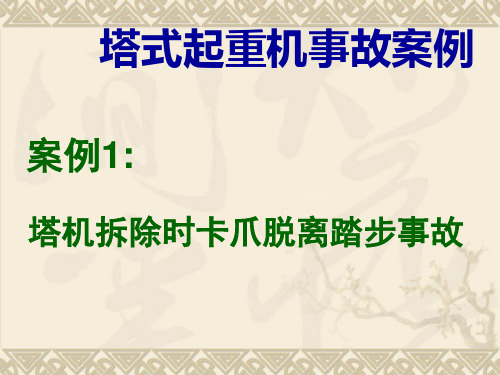
案例5:蚌埠05年“10.12”事故
坚硬的钢铁也变得如此柔软
蚌埠05年“10.12”事故原因:由于拆卸人 员操作不正确,拆卸时顶升横梁的位置应 在第13节标准下部耳板上,而实际拆卸顶 升横梁的位置却在上部耳板上,顶升油缸 的行程自锁功能失效,造成冒顶发生事故。
事故结论:拆卸单位的无安拆资质,则属 于违规安拆;现场从事安装缺乏基本塔吊 安全技术常识,作业现场又无专业技术指 挥,酿成大祸。
二)事故现场介绍及分析
主要结论:
A、操作失误或盲目蛮干
上述十几起事故中,经过调查发现操作人员绝大多数未 经过培训,有胆无识。但大部分却均持有安装资质证书。一 批假和尚,必然念歪经。
B、塔机本身在顶升机构部分缺少防油缸下铰点脱出的安全 装置。
目前,我国国产自升塔机中,绝大部分无此装置,留下 了事故隐患,反映了我国塔机标准规范与国际先进国家技术 方面的落后。只有少部分塔机设计单位,熟悉国际规范,在 设计中进行了有效设防。
二)事故现场介绍及分析
2、此时油缸继续收缩, 由于卡爪顶在踏步处, 使套架不能下落,而油 缸顶升横梁从下一踏步 上的凹口处离开。
二)事故现场介绍及分析
3、随着油缸的继续收回, 油缸顶升横梁从踏步上 凹口处彻底脱开。同时 踏步在卡爪的挤压下开 始变形,卡爪开始向下 移动,最终导致卡爪越 过踏步。套架上部约 30—40吨的重量突然下 落2.6---3米。一起事故就 这样地发生了。
塔机重大事故原因及应采取的对策
一、事故产生的根源
B、施工企业一味追求价格低廉,不认真考虑产品质量 和生产条件,或为了一己之私盲目采购低劣产品,为劣 质产品泛滥推波助澜。
C、政府审批多元化,检查、许可、验收者多,负责任 者寡,懂专业者少。收了费,什么样的产品,什么样的 企业都可以取得市场准入资质,为不合法的企业披上了 合法的外衣甚至耀眼的光环,为劣质产品进入市场开了 方便之门。同时也给某些部门和人员创造了腐败的机会 顽固的地方保护主义,保护和纵容了非法企业,是责任 企业有恃无恐。
建筑工地起重机机械伤人事故案例及分析

起重机机械部件存 在故障或缺陷,导 致失灵或失控。
施工现场安全管理 不到位,缺乏有效 的安全防护措施。
事故发生时,现场 人员未能及时采取 有效的应急措施, 导致伤害扩大。
事故原因分析
起重机机械故障:如钢丝绳断裂、吊钩脱落等 操作人员失误:如未按照操作规程进行操作、疲劳驾驶等 安全防护措施不到位:如未安装安全防护装置、安全防护装置失效等 管理不善:如未对起重机进行定期维护和检查、操作人员无证上岗等
03
起重机机械伤人事故的预防措施
加强设备维护和保养
及时更换磨损、损坏的零部 件,避免设备带病作业。
定期检查起重机机械设备的 各项性能指标,确保设备正 常运行。
严格按照设备维护保养手册 进行保养,确保设备得到全
面、专业的维护。
建立设备维护保养档案,记 录设备的维修保养情况,方
便追踪和管理。
提高操作人员的安全意识和技能水平
事故造成的人员伤亡和财产损失
人员伤亡:起重机机械伤人事故会导致工人受伤甚至死亡
财产损失:事故发生后,工地需要停工整顿,设备维修等,造成财产损失
社会影响:起重机机械伤人事故会引起社会关注,影响企业形象 安全意识:事故的发生暴露了工人的安全意识薄弱,需要加强安全教育和 培训
02
起重机机械伤人事故的特点
财产损失:事故可能导致起重机或其他机械设备的损坏,造成重大财产损失
生产中断:事故可能影响建筑工地的正常施工,造成生产中断和工期延误
社会影响:起重机机械伤人事故可能引起社会关注和舆论压力,对相关企业和行业形象造成负 面影响
事故原因多种多样
设备故障:起重机机械部件损坏或失灵 操作失误:工人操作不当或违反安全规程 安全防护措施不到位:缺乏必要的安全保护装置或措施 管理不善:工地安全管理不严格,安全培训和检查不到位
起重机械安全事故案例分析(桥式_门式)

结构件损坏事故
安装和检修中的事故
触电事故
违章作业事故
4
取物装置事故
吊钩冲顶坠落
吊钩相撞坠落事故 吊钩钢丝绳脱槽事故 龙门梁脱钩事故 吊具使用不当引起的死亡事故 吊物工具脱出砸人事故 系物索断裂引发的伤亡事故
5
吊钩冲顶坠落之一
1. 事故简介
1988年11月29日,某厂电炉加料起重机主钩冲顶,拉 断钢丝绳,吊钩坠落,砸死一人
5. 事故的预防对策
加强安全管理和设备管理;加强员工的安全知识、技术 知识和操作技能培训;修复或更换吊钩组。
19
吊钩钢丝绳脱槽事故
1.事故简介
1989年3月9日,某烧结厂用桥式起重机吊钢板,在空钩下落 的过程中,吊钩滑轮组上的一侧钢丝绳脱槽,吊钩下落,砸 死 一人。
2. 事故发生过程
某钢铁公司烧结厂机修车间对一系列2号烧结机进行16小时 的定修。架工班班长甲安排工人乙带领3名架工将零米处的钢 板吊运到距地面15.8m高的炔结机平台上。乙安排一人开起重 机,另外二人到零米处撬钢板、绑绳扣,乙则站在烧结机平 台上指挥。在乙的指挥下,在对起重机设备进行检查后,就 对准吊装孔放钩,当空钩降至离地面5~6m处时,丙来到吊 装现场,主动帮助橇钢板,乙发现后立即指挥停降吊钩,此 时,吊钩滑轮组一侧的钢丝绳突然跳槽脱出滑轮外,导致空 钩加速下降,砸中丙的肩部,经医院抢救无效死亡。
6
吊钩冲顶坠落之一
3.事故原因分析
(1)在起升主钩、下降副钩作业时,因主钩起升高度限位 器的触头发生粘连,使限位器失效,导致主钩继续上升冲 顶坠落。 (2)在起升主钩、下降副钩作业时,当主钩起升到位后, 司机将上钩控制器手柄拉到零位,但因操作不慎,使控制 器手柄从零位移动,造成主钩继续上升。 (3)管理部门未按要求对起重机进行定期检查保养,木 未对主钩起升高度限位器触头进行定期更换而埋下事故隐
案例分析丨各类吊车事故分析及经验总结

案例分析丨各类吊车事故分析及经验总结(1)超载自行式动臂起重机的起重量是随着起重臂的倾角变化而变化的,《起重机安全管理规程》指出:“起重量和起重臂倾角应符合设计要求”,又规定“起重机械禁止超负荷运行。
”在实际工作中由于对所吊物品的重量估计不清,或对安全注意不够而超负荷运行,使起重机失去稳定而造成“翻车”。
(2)支腿不在一个水平面上发生翻车这类事故的根本原因是:支腿接触的地面软硬不一,造成支腿不均匀下陷,如1973年9月18日,一辆16T轮胎汽车起重机吊装一接收器,由于地形低洼有水,前轮停在100mm*100mm的木排上,后轮停在钢轨上,四个支腿各垫在一个枕木上。
起吊一个直径为10m的接收器,起重臂在额定起重量为 2.5t 的位置上,指挥人员说重量只有1t,第一、二次试吊正常,第三次起吊,造成“翻车”事故,后来查出原因是支腿不在一个水平面上,加之超重导致的。
预防支腿下陷的主要实施如下:支腿必需支承在平坦而坚实的地面上,一般应使用垫板。
支腿不能支承在挖方地基附近,防止滑坡。
支腿不能支承在各种埋设物(地下管道,地下工程的出入口处)上,防止塌陷。
(3)回转过快起重机在起吊物品之初,一般不会翻车,翻车常发生在回转过程中。
例如某厂用轮胎吊扣楼板,构件距楼大约15~20m,吊车在楼和构件中间工作,地势北高南低,有风、雪,在吊第一块时,起重臂工作幅度为10m,倾角600,起升完毕,转臂大约450,车有些前倾、工地有人喊“危险”,司机急刹车,但发现板下有人,就又转臂,躲开人后又刹车,由于回转过急而翻车了。
这是因为回转会产生离心力,回转越快,离心力越大,同时还因转到顺风等不利于稳定的方位上,这些因素叠加在一起造成了此次翻车事故。
以此要注意回转速度不应过快。
(4)变幅,伸缩臂操作程序错误在起吊满负荷时,只能收回起重臂(由大幅度变小幅度,由长起重臂变短起重臂),不能伸臂或落臂,否则会翻车。
例如,在某施工工地,有一辆Q51型汽车起重机在回转半径为305m是,可以起吊3t。
- 1、下载文档前请自行甄别文档内容的完整性,平台不提供额外的编辑、内容补充、找答案等附加服务。
- 2、"仅部分预览"的文档,不可在线预览部分如存在完整性等问题,可反馈申请退款(可完整预览的文档不适用该条件!)。
- 3、如文档侵犯您的权益,请联系客服反馈,我们会尽快为您处理(人工客服工作时间:9:00-18:30)。
取决于安全仪表及其功能的质检工作, 取决于安全仪表及其功能的质检工作 , 只有在 场的安全人员才能完成。 场的安全人员才能完成。 在这一阶段应重视人员培训(体现在各种操作证 在这一阶段应重视人员培训 体现在各种操作证 上)。 。 在技术设计、研制阶段进行的完善分析的工作 在技术设计 、 在本阶段继续进行。 在本阶段继续进行。需要对过去的危险分析进行 客观的审查以核实已经按文件规定的方式对危险 提出了改进措施。 提出了改进措施。所有改进措施都应当在最终可 接受性审查过程中予以审查和核实。 接受性审查过程中予以审查和核实。
案例3 案例3:起重机掉道事故
一、事故发生过程: 事故发生过程: 时间、地点、事件; 时间、地点、事件; 事故现场; 致害物、起因物空间位置,环境状态等) 事故现场;(致害物、起因物空间位置,环境状态等) 设备基本状况; 参数、操作方式、完好状态等) 设备基本状况;(参数、操作方式、完好状态等) (作业流程);(复杂工艺的) 作业流程) 复杂工艺的) 事故过程介绍。 简单明了,真实,有依据,去伪存真) 事故过程介绍。(简单明了,真实,有依据,去伪存真) 二、事故原因分析(直接;间接;主要;从属。) 事故原因分析(直接;间接;主要;从属。 三、事故结论: 事故结论: 四、事故预防措施建议: 事故预防措施建议: 五、(检验责任的反思:) 检验责任的反思:
使用(运行—维护 五个阶段。 维护) 使用 ( 运行 维护 ) 五个阶段 。 前四个阶段的 结束点是主要控制点。 结束点是主要控制点。 制造阶段是安全技术检验和监察的重要环节。 制造阶段是安全技术检验和监察的重要环节 。 从加工制造一开始, 从加工制造一开始,质量控制部门就是产品测试 和检查的主要负责部门。所以监督检验中与质量 和检查的主要负责部门。 控制部门配合是绝对必要的。根据产品的复杂性, 控制部门配合是绝对必要的。根据产品的复杂性, 派安全检验人员去制造厂亲身监督有关试验和核 实得出产品最终可接受性的关键试验的结论。 实得出产品最终可接受性的关键试验的结论。在 进行质量检验的地方,此种监督是必要的, 进行质量检验的地方,此种监督是必要的,因为
二、事故发生机理 海因里希: 海因里希:多米诺骨牌效应 人、物、环境三要素。 环境三要素。
三、事故的统计分析 海因里希: 55万次事故统计中得出这样的结 海因里希 : 从 55 万次事故统计中得出这样的结 在涉及同一对象的330次同类事故中, 330次同类事故中 论:在涉及同一对象的330次同类事故中,有300 次未产生伤害, 29次产生轻微伤害 次产生轻微伤害, 次未产生伤害 , 29 次产生轻微伤害 , 1 次产生严 重伤害。 这一统计规律称为 330 事故模型 。 其中 330事故模型 重伤害 。 这一统计规律称为330 事故模型。 90%为险肇事故,伤害事故不到10 10% 90%为险肇事故,伤害事故不到10%,严重事故只 它说明了事故的广泛性, 有0.3%。它说明了事故的广泛性,即比我们看到 的伤害事故要多得多。 的伤害事故要多得多。险肇事故没有严格的先后 顺序,不知孰先孰后。所以伤害事故具有偶然性、 顺序,不知孰先孰后。所以伤害事故具有偶然性、
案例5 案例5:机体挤伤事故
致事故的频数最高, 约占40 40% 致事故的频数最高 , 约占 40 % 占 ; 其次是吊运时 捆绑方法不当, 约占24 24% 再次是超载, 捆绑方法不当 , 约占 24 % 占 ; 再次是超载 , 约占 在挤压碰撞造成的事故中, 8 % 。 在挤压碰撞造成的事故中 , 人在起重机与结 构物之间或在两机之间作业时, 构物之间或在两机之间作业时 , 因机体运行或回转 导致的事故最多, 40% 以上, 导致的事故最多 , 占 40 % 以上 , 其次是吊物或吊 具在吊运过程中摆动碰撞造成事故, 约占25 25% 具在吊运过程中摆动碰撞造成事故 , 约占 25 % ; 再次是吊运后的物件摆放不稳倾倒砸人, 15% 再次是吊运后的物件摆放不稳倾倒砸人 , 占 15 % 以上。 以上。
案例4 案例4:起升绳断绳事故
一、事故发生过程: 事故发生过程: 时间、地点、事件; 时间、地点、事件; 事故现场; 致害物、起因物空间位置,环境状态等) 事故现场;(致害物、起因物空间位置,环境状态等) 设备基本状况; 参数、操作方式、完好状态等) 设备基本状况;(参数、操作方式、完好状态等) (作业流程);(复杂工艺的) 作业流程) 复杂工艺的) 事故过程介绍。 简单明了,真实,有依据,去伪存真) 事故过程介绍。(简单明了,真实,有依据,去伪存真) 二、事故原因分析(直接;间接;主要;从属。) 事故原因分析(直接;间接;主要;从属。 三、事故结论: 事故结论: 四、事故预防措施建议: 事故预防措施建议: 五、(检验责任的反思:) 检验责任的反思:
案例2 案例2:卷筒驱动侧板断裂事故
一、事故发生过程: 事故发生过程: 时间、地点、事件; 时间、地点、事件; 事故现场; 致害物、起因物空间位置,环境状态等) 事故现场;(致害物、起因物空间位置,环境状态等) 设备基本状况; 参数、操作方式、完好状态等) 设备基本状况;(参数、操作方式、完好状态等) (作业流程);(复杂工艺的) 作业流程) 复杂工艺的) 事故过程介绍。 简单明了,真实,有依据,去伪存真) 事故过程介绍。(简单明了,真实,有依据,去伪存真) 二、事故原因分析(直接;间接;主要;从属。) 事故原因分析(直接;间接;主要;从属。 三、事故结论: 事故结论: 四、事故预防措施建议: 事故预防措施建议: 五、(检验责任的反思:) 检验责任的反思:
(日本每年起重机事故死亡100多人,占工作事故总 日本每年起重机事故死亡100多人, 100多人 人数的6.5%左右)。 人数的6.5%左右)。 6.5%左右 根据事故资料统计, 根据事故资料统计 , 造成人员伤害事故的起重机械 主要集中在桥式和门式起重机、 塔式起重机、 流动 主要集中在桥式和门式起重机 、 塔式起重机 、 式起重机、 施工升降机等四类, 式起重机 、 施工升降机等四类 , 合计占起重机械事 故的80%左右。 故的80%左右。 80 造成起重机械伤害事故的直接原因, 造成起重机械伤害事故的直接原因 , 排在前四位的 有 : 吊物坠落、 挤压碰撞、 触电、 高处坠落, 合计 吊物坠落 、 挤压碰撞 、 触电 、 高处坠落 , 占起重机械事故的80 % 以上。 占起重机械事故的 80% 以上 。 在吊物坠落造成的 80 事故中,因吊索具缺陷(如钢丝绳断、脱钩等) 事故中,因吊索具缺陷(如钢丝绳断、脱钩等)导
起重机械典型事故 案例分析与思考
辽宁省安全科学研究院王福绵
起重机械典型事故案例分析
------兼谈检验注意事项 兼谈检验注意事项 一、几个基本概念 二、事故发生机理 三、事故的统计分析 四、起重机械典型事故案例分析
一、几个基本概念和问题 1、 事故 : 是一个或一系列导致人员伤亡或疾 、 事故: 设备或财产的损失和破坏、 病、设备或财产的损失和破坏、造成环境危害的 意外事件。 意外事件。 2、 危险 : 一种已存在或潜在的条件 , 其发生 、 危险: 一种已存在或潜在的条件, 可导致意外事故。 可导致意外事故。 3、 安全 : 是消除能导致人员伤亡或疾病 、 设 、 安全: 是消除能导致人员伤亡或疾病、 备或财产的损失和破坏、造成环境危害的条件。 备或财产的损失和破坏、造成环境危害的条件。 4、 寿命周期 : 将寿命周期分为概念形成 ( 初 、 寿命周期: 将寿命周期分为概念形成( 步设计) 技术设计(设计确认) 研制、制造、 步设计)、技术设计(设计确认)、研制、制造、
最后, 最后 , 将生产阶段和研制阶段的结果编成安全 报告,判定并用文件的形式最终确认产品安全性。 报告,判定并用文件的形式最终确认产品安全性。 报告还应揭示在使用环境中的安全正确的使用方 报告的内容基本就是从分析、 法。报告的内容基本就是从分析、试验和设计标 准制定过程所得到的数据。报告应作出关于产品 准制定过程所得到的数据。 安全完整性的肯定结论和确定已判定的危险的控 制方式。 制方式。 使用阶段进行培训和积累资料(从产品故障、 使用阶段进行培训和积累资料 ( 从产品故障 、 现场安装故障以及出现的事故和偶然事件收集资 料)。安全管理在此阶段必须追究可能出现的任
3.9 3.3 3.3
表中的起重伤害事故起数和和死亡人数, 表中的起重伤害事故起数和和死亡人数,是指 起重机本体直接造成的事故数, 起重机本体直接造成的事故数,而在起重机械作 业中由于吊物坠落造成的物体打击、 业中由于吊物坠落造成的物体打击、因起重机电 气系统漏电或吊臂触碰高压线等造成的事故、 气系统漏电或吊臂触碰高压线等造成的事故、因 起重机吊臂运动造成的人员坠落事故,则分别归 起重机吊臂运动造成的人员坠落事故, 类于物体打击、触电、高处坠落等事故类型。 类于物体打击、触电、高处坠落等事故类型。因 而,实际起重机械作业中所造成的起重事故数量, 实际起重机械作业中所造成的起重事故数量, 要比表中的数量大得多, 要比表中的数量大得多,约占工矿企业事故总数 的15%左右,这是因为事故类型的划分造成的。 15%左右,这是因为事故类型的划分造成的。
起重机械事故状况及简要分析
近三年全国工矿企业及起重伤害事故统计表
年份
事故起数
工矿企业 起重伤害故比例
起数% 起数 人数% 人数
2002 9616 2003 11454 2004 11063
431 438 415
7929 10881 10470
310 359 346
4.5 3.8 3.8
何问题,判定危险状况, 何问题 , 判定危险状况 , 与设计人员一起提出 改进措施,并由安全人员进行审查。 改进措施,并由安全人员进行审查。对改进措施 中的设计变更,安全人员也应进行审查。 中的设计变更,安全人员也应进行审查。 5、 安全责任 : 已由使用者 、 制造者 、 安装维 、 安全责任: 已由使用者、 制造者、 修者、向设计者、检验者、监察者延伸。 修者、向设计者、检验者、监察者延伸。 6、 检验意义 : 检验促进安全技术的发展 , 安 、 检验意义: 检验促进安全技术的发展, 全技术的发展使预测危险的能力提高。 全技术的发展使预测危险的能力提高。减少危险 的措施正用于新产品、新工艺的开发。 的措施正用于新产品、新工艺的开发。