轧机板型控制
热轧带钢生产中的板形控制范本

热轧带钢生产中的板形控制范本热轧带钢生产中的板形控制是一个关键的工艺环节, 对于产品的质量和成本都有着重要的影响。
本文将从板形控制的目标、过程、方法以及优化等方面进行详细的介绍。
一、板形控制的目标热轧带钢的板形控制的主要目标是使得钢带的板形达到设计要求, 即保持带钢在轧机出口处的平直度和边部的整齐度, 同时减小带钢在轧机出口处的侧弯、扭曲和波浪板形等缺陷。
对于一些对称性较好的带钢产品, 还需保持带钢两端表面与轧机的同心度。
二、板形控制的过程热轧带钢板形控制的过程主要包括前段控制、中段控制和后段控制三个阶段。
1.前段控制: 前段主要包括热轧连铸过程和热轧过程中的预弯矫直机、厚度控制等过程。
这一阶段的目标是减小带钢的不均匀厚度分布, 控制带钢的凸度和波浪度, 为后续的板形控制打下基础。
2.中段控制: 中段主要包括轧制机组控制和冷却控制等过程。
通过控制轧机的速度、压下力以及冷却速度等参数, 调整带钢的板形。
在轧制机组控制上, 采用辊形调整、辊系控制等技术手段来改变带钢板形。
在冷却控制上, 通过改变冷却方式、喷水的位置和喷水量等参数来调整带钢的板形。
3.后段控制:后段主要包括带钢的拉直和切割等过程。
通过采用拉直机进行带钢的拉直,使得带钢在轧机出口处达到平直度的要求。
同时,通过切割机对带钢进行切割,保证带钢的两端表面与轧机的同心度。
三、板形控制的方法热轧带钢板形控制的方法主要包括参数调整法、辊形调整法和辊系控制法。
1.参数调整法: 通过调整轧机的速度、压下力、冷却速度等参数来控制带钢的板形。
这种方法操作简单, 但对于复杂的板形控制要求, 效果较差。
2.辊形调整法: 通过调整辊系的形状来改变带钢板形。
辊形调整主要包括辊筒调整和辊系调整两种方法, 通过改变辊系的形状, 调整辊系的凸度、侧弯等参数来控制带钢板形。
3.辊系控制法:辊系控制主要是通过辊系控制技术来改变辊系间的关系,从而改变带钢的板形。
辊系控制主要包括辊系窜凸控制、动力控制和形态控制等方法,这些方法可以实现对辊系间的力学和几何关系进行控制,进而控制带钢的板形。
轧制厚度及板型控制
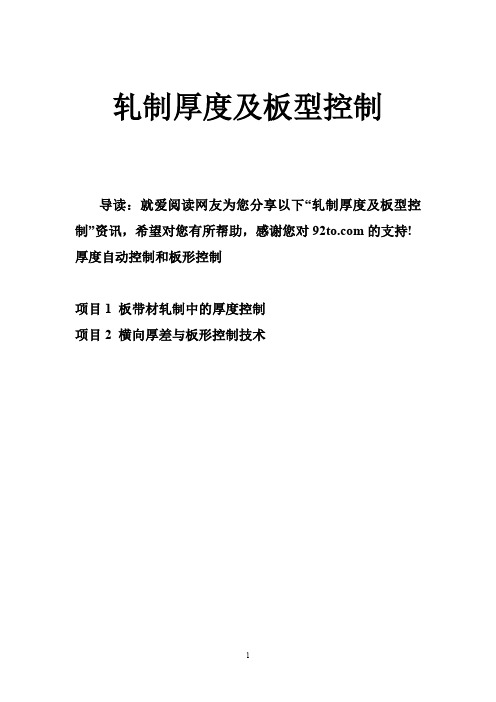
轧制厚度及板型控制导读:就爱阅读网友为您分享以下“轧制厚度及板型控制”资讯,希望对您有所帮助,感谢您对的支持! 厚度自动控制和板形控制项目1 板带材轧制中的厚度控制项目2 横向厚差与板形控制技术项目1板带材轧制中的厚度控制一、厚度自动控制的工艺基础 1.p-h图的建立(1)轧制时的弹性曲线轧出的带材厚度等于理论空载辊缝加弹跳值。
轧出厚度:h=S0 +P/K―――轧机的弹跳方程S0 ――空载辊缝P――轧制压力K――轧机的刚度系数根据弹跳方程绘制成的曲线(近似一条直线)――轧机弹性变形曲线,用A 表示。
A(2)轧件的塑性曲线根据轧制压力与压下量的关系绘制出的曲线――轧件塑性变形曲线,用B表示。
B(3)弹塑性曲线的建立将轧机弹性变形曲线与轧件塑性变形曲线绘制在一个坐标系中,称为弹塑性曲线,简称P-h图。
注意A线与B线交点的纵坐标为轧制力A线与B线交点的横坐标为板带实际轧出厚度2. p-h图的运用由p-h图看出:无论A线、B线发生变化,实际厚度都要发生变化。
保证实际厚度不变就要进行调整。
例如:B线发生变化(变为B‘),为保持厚度不变,A线移值A',是交点的坐标不变。
C线――等厚轧制线作用:板带厚度控制的工艺基础板带厚度控制的实质:不管轧制条件如何变化,总要使A 线和B 线交到C线上。
p-h图二、板带厚度变化的原因和特点影响板带厚度变化的因素:1、轧件温度、成分和组织性能不均匀的影响温度↑→变形抗力↓→轧制压力↓→轧机弹跳↓→板厚度变薄↓变形抗力对轧出厚度的影响2、来料厚度不均匀的影响来料厚度↓→压下量↓→轧制压力↓→轧机弹跳↓→板厚度变薄↓来料厚度对轧出厚度的影响3、张力变化的影响张力↑→变形抗力↓→轧制压力↓→轧机弹跳↓→板厚度变薄↓张力对轧出厚度的影响4、轧制速度变化的影响通过影响摩擦系数和变形抗力来改变轧制压力。
摩擦系数↓→变形抗力↓→轧制压力↓→轧机弹跳↓→板厚度变薄↓摩擦系数对轧出厚度的影响5、原始辊缝的影响原始辊缝减小,板厚度变薄。
浅谈轧机板形控制系统的组成及控制原理

电荷放大器将压电传感器生成的电荷信号转换为电压。 旋转变送器(PCM 变送器)将这些电荷放大器的输出信号 转换为(PCM 编码的)数字信号。数据通过电缆从旋转变 送器传递给安装在控制柜内的 PCM 解码器插架(PCM 已 经停产,现在基本都采用集成的 SIKO 模块代替 IOP 模块及 PCM 插架)。下图是 SIKO 模块实物图。
[1] 阿 亨 巴 赫 .OPTIROLL i2 SFC and SCA Training[CP/ K].2004[2021.5]. 设备厂家 .
Fti = 每个测量区铝箔张力 Fri= 每个传感器的径向力 HExit= 铝箔出口厚度
图 2 传感器受力模型
图 1 板形辊结构
收稿时间 :2021-05 作者简介 :郭明明,生于 1985 年,男,助理工程师,高级技师,研究方向 : 自动化控制、传动控制、设备管理。
铝箔两边张力 Fti 会产生一个向下的压力 Fri 即传感器的 径向压力。那压电传感器上会产生电荷脉冲。每个脉冲的强 度取决于轧制铝箔在铝箔横截面上的长度分布情况 , 铝箔精 确位置对覆盖少的传感器影响很大,以至于只有传感器覆盖 面积超过额定 50%,系统才可以使用测量。
M 冶金冶炼 etallurgical smelting
粗轧机横—轧“狗骨”轧制板型控制优化
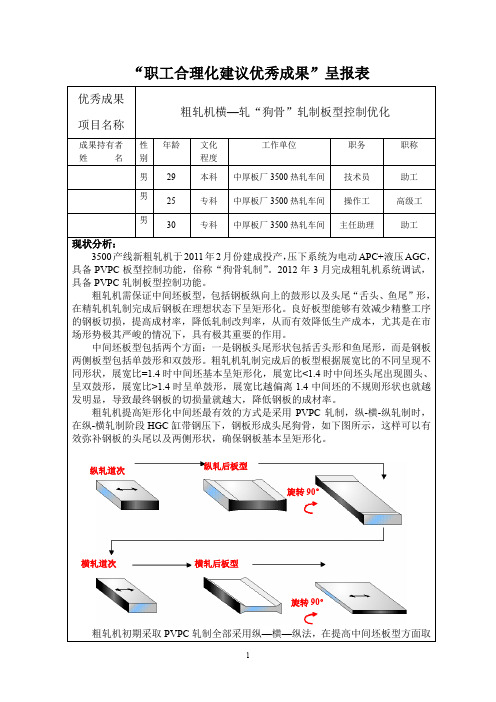
得了良好效果,证明 PVPC 功能是比较完善的。但全部采用此方法轧制又暴露出其 他一些问题:
1、轧制节奏相对较慢,但轧制节奏变慢,单位小时产量下降,从而增加了煤 气消耗和电力消耗等等,相应地增加了生产成本。
2、展宽比小于 1.3 的生产计划,钢板头尾板型控制不甚理想,“舌头”较大切 损量较大。所以,展宽比小于 1.3 的生产计划,为保证钢板定尺长度,需牺牲一定 的成材率。
“职工合理化建议优秀成果”呈报表
优秀成果 项目名称
粗轧机横—轧“狗骨”轧制板型控制优化
成果持有者
姓
名
性 年龄 别
文化 程度
工作单位
职务
职称
男 29
本科 中厚板厂 3500 热轧车间 技术员
助工
男 25
专科 中厚板厂 3500 热轧车间 操作工
高级工
男 30
专科 中厚板厂 3500 热轧车间 主任助理
从以上分析来看,我们既希望提高成材率的同时又不增加生产成本,这需要找 到一个兼顾成材率和生产成本的平衡点,即找到一个既能提高成材率又不增加单位 生产成本的方法。 实现项目的方法、措施:
在充分的验证的基础上提出对于展宽比小于 1.3 的生产计划,采取开启 PVPC 的横—纵轧制法,在横轧阶段形成“狗骨”,转钢后在纵轧阶段弥补钢板头尾“舌 头”形状,操作方式如下图所示
横轧道次
横轧后板型
旋转 90°
来料旋转 90°
利用轧制过程的 HGC 带钢压下,在钢板咬入后压下辊缝、在钢板即将抛出后抬 起辊缝在钢板头尾形成“狗骨”,转钢后纵轧阶段补偿头尾变形,能够保证钢板基 本呈矩形化,减少精整切损,提高钢板成材率,具体操作方式如下所示。
1、对展宽比大于或等于 1.5 的生产计划,粗轧机开启 PVPC,采用纵—横—纵 轧制。
中板厂粗轧机板型控制的优化

立辊 侧 压法通 过展 宽 侧压 、 轧侧 压 及 精 轧 精
阶段液 压 A WC控 制 , 现 钢 板 平 面形 状 矩 形 化 实
控 制 。以钢 板平 面不 均匀 部 分 面 积最 小 为 目标 ,
其中 日 本居领先地位 , 许多板材厂的成材率已达
到 9% , 5 切头 尾 和切 边 量 已降 到 4 。 国外 还 广 % 泛采用 液 压 AG 横 向板 型 控 制 和 计 算 机 控 制 , C、
pa t f i n , a e oo g t y ntec r n s u t n d t mi s jr n u n i c r.Atr a ig印一 l g g m k sa h ru hs d ur t i a o , e r n o f e cn f t s f kn n oJa t u o h e t i e e ma il ga o et
saecn o ara ,dsr e epe n s tso p t saecnr nruhn i em du l emUn lp t l bod eci s h r e t t u f l e hp ot l g i ml i t eim p t l o r b t s a a oo o g lnh a i g
1 1 1 立辊侧 压 法 ..
控制也 是一项 重 要 内容 , 两 项 指 标 除 了用 于表 这
征板材 的外形 质量 外 , 直 接与 负偏 差轧制有 关 , 还
因而 与成材率 密切 相关 。
1 国 内外板 型控 制 的现状 及我 厂现 状分析 1 1 国 内外 板型 控制 的现 状 . 国外不 少厂 家 已普遍 采 用 板 型 控制 新 技 术 ,
p r t o v n mp ae s li gmft r s h mm h p ee t f eta se a r m o s igmi a e e i mv d, h ut g i .. e ,t e d Au '¥ s a e d fc t r frb rf oh n o ru hn l h sb n mp e t e c t n i ls fpa e e h s b e e u e d sg i c te o o c b n f s h v e n a h e e . o so lt d a e n rd c d a inf a c n mi e e t a e b e c iv d n in i Ke wo d P a es a e c n r l Op i z t n, r m s a y rs lt h p o t , t o miai D u h p o e
中厚板轧机的板形控制

中厚板轧机的板形控制(壹佰钢铁网推荐)板形控制对于提高板带材质量意义重大,是板带压力加工的核心控制技术之一。
近年来,随着先进的板形控制技术不断涌现并日臻完善,促进了板带钢生产装备的进步和产业升级,生产效率和效益大幅提升。
然而,普通中厚板轧机一般为可逆式四辊轧机,常采用单机架或双机架结构布置,有些只具有简单的弯辊装置。
由于设备或工艺的原因,板形控制能力不强,制约了板材质量和成材率的提高。
所以,普通中厚板轧机的板形控制仍然是一个重要课题。
在轧制计划已知的条件下,中厚板轧机板形与板凸度控制手段主要有工作辊弯辊、压下负荷分配以及工作辊和支撑辊的初始辊型。
1. 工作辊弯辊技术。
液压弯辊技术是目前中厚板生产中常用的板形控制技术,其基本原理是通过对工作辊或支撑辊辊颈施加适当的弯辊力来瞬时地改变轧辊的有效凸度,从而改变承载辊缝形状和轧后钢板的延伸率沿横向的分布。
工作辊弯辊直接对辊缝形状产生影响,从而改变轧件的出口板凸度。
由于前面道次轧件较厚,凸度遗传效应小,而对板形和板凸度起决定性影响的轧制道次主要是后 3~4 道次,所以不必对一块钢坯所有轧制全部道次都采用弯辊进行板形控制,只需要在后几个关键道次采用弯辊进行板形和板凸度控制即可满足精度要求。
因此,前面道次不采用弯辊,尽量采取大压下量来发挥轧机的能力;最后三或四个道次采用弯辊控制。
2. 压下负荷分配。
在中厚板轧制时,压下负荷分配是板形与板凸度控制的重要手段。
压下负荷分配是通过调整各个道次的压下量使其轧制力改变,从而使承载辊缝形状发生改变,轧件的出口凸度也随之发生改变。
压下负荷分配可以根据生产中在线的板形情况进行适时调整,响应速度快,操作性和适应性较强。
不同的轧制阶段、不同的辊型、不同的轧件材质和不同的轧制温度等所对应的压下规程分配方法不同,所以应该根据实际情况进行动态的轧制负荷分配。
3. 工作辊和支撑辊的初始辊型。
轧辊辊型是影响板凸度的重要因素,所以,改善板形与控制板凸度常见的方法是进行工作辊辊型的合理设计。
热轧带钢生产中的板形控制(三篇)

热轧带钢生产中的板形控制热轧带钢是一种由连续轧机通过高温轧制过程中制造的带状钢材,具有广泛的应用领域,如建筑、机械制造、汽车工业等。
然而,在热轧带钢生产过程中,由于各种因素的影响,往往会出现板形问题,即钢带在轧制过程中出现不平整、弯曲或起波等现象。
这不仅影响了带钢的质量和性能,还会给下道工序的加工带来困难和影响。
因此,热轧带钢生产中的板形控制至关重要。
板形问题的产生原因多种多样,下面将分析几个主要的因素,并介绍相应的控制措施。
1. 型辊和辊系的设计和调整:型辊是轧制过程中起着塑性变形和形状控制作用的关键元件。
首先,型辊的选择应根据带钢的要求和钢种的性质进行选择,以确保能够得到所需的板形公差。
其次,型辊和辊系的调整是关键,应确保辊系的轴线垂直于水平线,并且各辊之间的间隙和压力均匀,以避免板形问题的产生和扩大。
2. 加热温度的控制:加热温度是热轧带钢生产中的重要参数之一,直接影响到钢材的塑性变形和板形控制。
在加热过程中,应控制好加热温度的均匀性和稳定性,避免温度过高或不均匀导致的板形问题。
此外,还应注意控制加热速度和冷却速度,以控制好板坯的温度梯度,避免板坯的不均匀热胀冷缩引起的板形问题。
3. 轧制工艺的优化:轧制工艺是实现板形控制的关键。
首先,应合理选择轧制规范,确定合适的轧制温度和轧制比例,以控制好板材的塑性变形和减小残余应力。
其次,应注意轧制过程中的控制,在控制好板材的进给速度和板坯的温度梯度的同时,要控制好辊系的磨损和辊承力等参数,以避免板形问题的产生。
4. 板形测量和反馈控制:板形问题的产生往往是由于辊系和工艺参数的变化引起的,因此要及时发现和识别板形问题的存在和变化,就需要进行板形的测量和反馈控制。
目前,常用的板形测量方法主要有激光束法、光干涉法和摄像机法等,通过对板形的实时测量和分析,可以及时调整辊系和工艺参数,以达到板形控制的目的。
总之,热轧带钢生产中的板形控制是一个复杂的问题,需要从多个方面进行综合分析和控制。
浅谈宁钢1780精轧机的板型调整
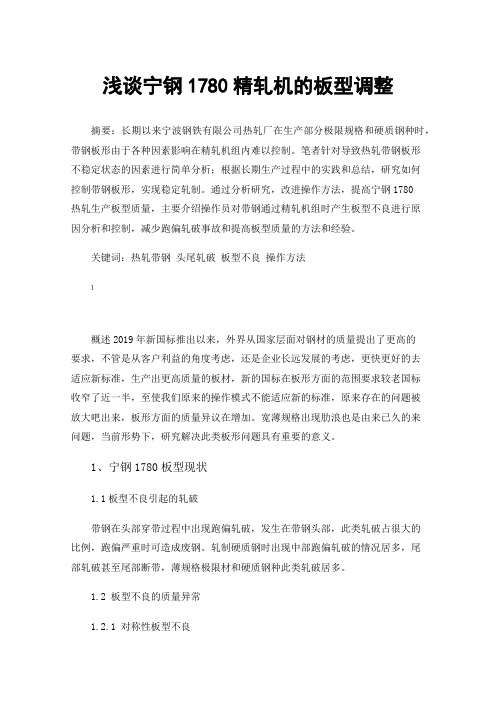
浅谈宁钢1780精轧机的板型调整摘要:长期以来宁波钢铁有限公司热轧厂在生产部分极限规格和硬质钢种时,带钢板形由于各种因素影响在精轧机组内难以控制。
笔者针对导致热轧带钢板形不稳定状态的因素进行简单分析;根据长期生产过程中的实践和总结,研究如何控制带钢板形,实现稳定轧制。
通过分析研究,改进操作方法,提高宁钢1780热轧生产板型质量,主要介绍操作员对带钢通过精轧机组时产生板型不良进行原因分析和控制,减少跑偏轧破事故和提高板型质量的方法和经验。
关键词:热轧带钢头尾轧破板型不良操作方法概述2019年新国标推出以来,外界从国家层面对钢材的质量提出了更高的要求,不管是从客户利益的角度考虑,还是企业长远发展的考虑,更快更好的去适应新标准,生产出更高质量的板材,新的国标在板形方面的范围要求较老国标收窄了近一半,至使我们原来的操作模式不能适应新的标准,原来存在的问题被放大吧出来,板形方面的质量异议在增加。
宽薄规格出现肋浪也是由来已久的来问题,当前形势下,研究解决此类板形问题具有重要的意义。
1、宁钢1780板型现状1.1板型不良引起的轧破带钢在头部穿带过程中出现跑偏轧破,发生在带钢头部,此类轧破占很大的比例,跑偏严重时可造成废钢。
轧制硬质钢时出现中部跑偏轧破的情况居多,尾部轧破甚至尾部断带,薄规格极限材和硬质钢种此类轧破居多。
1.2 板型不良的质量异常1.2.1 对称性板型不良对称性板型不良的主要表现形式是中间浪和双边浪,宁钢1780热轧生产线应用的是CVC可变凸度调节系统,出现此类浪型一般是在硬度跨层别,由软钢换硬钢时易出现中间浪,由硬钢换软钢时易出现双边浪。
合金钢和冷装钢在加热在炉时间不足的时候易出现中间浪。
出现此类情况系统无法准确做出设定,需要人工进行干预。
1.2.2 非对称性板型不良非对称性板型不良的主要表现形式是单边浪和镰刀弯,宁钢1780热轧产生单边浪大多数情况是在头部几十米,以薄3.0mm以下规格居多,严重影时响客户使用,需要切除,成材率损失严重。
- 1、下载文档前请自行甄别文档内容的完整性,平台不提供额外的编辑、内容补充、找答案等附加服务。
- 2、"仅部分预览"的文档,不可在线预览部分如存在完整性等问题,可反馈申请退款(可完整预览的文档不适用该条件!)。
- 3、如文档侵犯您的权益,请联系客服反馈,我们会尽快为您处理(人工客服工作时间:9:00-18:30)。
" # $%&D B CD %E F G& B C H I B JK B I! H I L FML J J
NO P Q R S T 6 U -V:W X R 6 Y Z [ 5 Q P \ 05 T Z T [ 6 ’ ( 3 ; [ 6 Y ; [ R P 6 ] 4 R 4 T 4 75 ^ _ 7 ‘ ; 6 5 a 5 Y Z X \ b[ 5 ; T [ 6 c O :W d T 6 -Od R [ 6 ^ 7 6 Y ’ 1 ( 3 ; [ 6 Y ; [ R e [ 53 4 7 7 a W f 5 T g. 5 * + ,-.] 1 E h D H I E & H i64 ; 7j [ ] R ]5 ^ ] Z 6 4 ; 7 4 R ‘[ 6 [ a Z ] R ]5 ^ ] ; [ g 7‘ 5 6 4 f 5 a 5 6) 4 f R gkR a a 01 1 / p 2 3 4 5 6 7 l ][ 6 [ a Z 4 R ‘k7 4 ; 5 m ] 91 :1 3 ; 5 ; 7 4 l ]R 6 ^ a T 7 6 ‘ 7^ T 6 ‘ 4 R 5 6 k7 4 ; 5 m ][ ]n7 a a[ ]o 2 g ; 5 4 5 7 a [ ] 4 R ‘[ 6 [ a Z 4 R ‘k7 4 ; 5 m ]n7 f 7‘ 5 kj R 6 7 m4 5] 4 T m Z4 ; 7R 6 ^ a T 7 6 ‘ 75 ^ 4 ; 7R 6 4 7 f k7 m R [ 4 7f 5 a a ] 1_ [ q R [ a k5 r 7 k7 6 4 5 64 ; 74 f [ 6 ] r 7 f ] 74 ; R ‘ s 6 7 ] ]7 f f 5 f [ 6 m4 ; 7] 4 f R g] ; [ g 75 6] s R 6g [ ] ] ; 7j 7 ] 4 / m f [ Y Y R 6 Y[ k5 T 6 4n[ ]m 7 4 7 f kR 6 7 m [ 6 m4 ; 74 f [ 6 ] r 7 f ] 74 ; R ‘ s 6 7 ] ]7 f f 5 f; [ ]j 7 7 6f 7 m T ‘ 7 mj Z < ,=>? ,=/ 1 ] 4 f R g] ; [ g 7n[ ]5 j r R 5 T ] a ZR kg f 5 r 7 m V6 m^ T f 4 ; 7 f k5 f 74 ; 7f 5 a a R 6 Y^ 5 f ‘ 75 ^ ] s R 6 ,=1 g [ ] ]n[ ]f 7 m T ‘ 7 mj Z?=>) / / tG u vB I w D -.kR a a ] ; [ g 7 ‘ 5 6 4 f 5 a ) * + ,-.双平整轧机是宝钢集团公司从日本引 进的六辊 -.轧机 / 在引进整套机组同时 / 相应的生 产工艺和设备控制参数也完全由日方提供 @ 但在几 年的生产中发现日方提供的工艺控制参数并非十分 完善 / 特别是生产规格扩大后 / 原来的控制工艺参数 更难适应 @为了进一步优化 ) * + ,-.轧机的生产及 工艺参数 / 对) * + ,-.双平整 轧 机 工 艺 参 数 及 设 备 特性进行了全面的研究 / 提出了新的工艺控制参数 / 取得了明显的实效 @ ! ! " # $%&双平整机组的基本参数及存在的问题 ! x ! ) * + ,-.双平整机组的基本参数 第一 ) * + ,-.双 平 整 机 组 的 设 备 基 本 参 数 是 y 机 架 和 第 二 机 架 轧 机 均 为 六 辊 -. 轧 机 8 轧辊尺寸 是z 而第 * { ,kk| * } ,kk| ) , , ,kk~) * + ,kk! z z
A A
u
u
t + X = xB y = = b xE X v= x. + / . 式中
u
u
+ } .
u
u
u
u
u
t + X = wB y = = b wE X v= w. AA 中间辊弹性弯曲影响函数矩阵 & y = ~ 支撑辊弹性弯曲方程
+ j .
将支撑辊分解为两个悬臂梁 % 分别求出左 * 右两 部分的挠度 t b w和 t b x% + 1 .
间 辊边部位置距带钢边 部 ( $% &) o , >+ * ,kk/ #‘
万方数据
A
联系人 y 魏立群 / 副教授 / 上海 ’ 上海应用技术学院材料工程系 + , , + o < (
第 h期
魏立群等 9 / 0 1 234轧机板形控制的研究
!l ’ !
第 二 架 的 !" 第 二 架 的 !" # # $取 的 大 一 些 % $取 得 小 一些 & ’ ( ) 存在的问题 能满足常规规 根 据 日 方 提 供 的 生 产 工 艺 参 数% 格品种的轧制 & 但要进一步提高产品板形及横向厚 度 的控制精度 * 拓展生产规格 + 如 ,-材及 薄 而 宽的 轧 件. 等方面显得比较困难 & 为了 进一 步 发 挥 / 0 1 2 有必要弄清该轧机的板形综合控 34 轧 机 的 潜 力 % 制 能 力% 以 提 高 其 板 形 控 制 的 能 力&根 据 / 0 1 234 轧机 的 生产状况 及 设 备 特 性 % 采用了计算机模拟仿 真 的 计 算 方 法% 模拟了 / 0 1 234 轧 机 的 生 产 及 34 轧机的板形控制特性 % 并取得了成功 & ) ’ 5 ) 678轧机板形控制研究的基本方法 为了研究 / 建立 0 1 234轧 机的板形 控 制特 性 % 下面几个方面的计算模型 9 + / .轧件的变形抗力和平整轧制压力模型 : + 1 .轧辊的热凸度统计计算模型 : + ; .34轧机的辊系受力计算模型 : + 0 .34轧机的辊系弹性变形计算模型 & 在此基础上 % 开发了 / 0 1 234轧 机板 形 控 制的 计 算 机 仿真程序 % 以现场实测统计数据回归分析并 确 定了计算模型 的 相 关 计 算 参 数 % 建立理论统计计 分析 / 算 模型 & 通过模拟现场轧 制状况 % 0 1 234轧 机的板形控制特性 % 最终确定最佳的板形控制参数 & ) ( ’ 轧件变形抗力及平整轧制压力模型 + / .轧件变形抗力模型 采用常用的 < 理论统计变形抗力模型 9 = >?
! " # $%&轧机板形控制的研究
魏立群 张杏耀 柳谋渊 徐耀寰 彭 俊 何建锋
上海应用技术学院 ( ’
摘
上海宝钢集团公司 ( ’
要 在综合分析了 ) 采 用 了 01 的解析法8 的影 * + ,-.轧机的板形控制的基础上 / 1 2 3 4 5 6 7 91 :1 3 ; 5 ; 7 4 响函数法以及三维光弹性分析相结合的方法/ 研究了 ) 轧 机 中 间 辊 的 抽 动 量 对 平 整 轧 制 带 钢 的 横 向 * + ,-. 厚度差和板形的影响 / 并确定出中间辊的最佳 抽 动 位 置 / 使得 ) * + ,-.轧 机 平 整 轧 件 的 横 向 厚 度 差 下 降 幅 度 达到 < 轧件的板形明显提高 / 同时平整的轧制压力下降 ?=>) 取得明显的实效 @ ,=>? ,=8 ,=/ 关键词 -.轧机 板形 控制 A
u u
u
u
u
u
u
u
t X { vx B y v+ v= xE z x.E y c v
u u
u
+ .
+ / 2GH >>1. 式中
u
u
u
u
u
t X { vw B y v+ v= wE z w.E y c v y vAA 工作辊弹性弯曲影响函数矩阵 :
+ r .
式中
AA 累积变形量 : D 视钢种材料不同而变 &根据现场 * * AA 常数 % C C C / 1 ; 结合实测材料的变 平 整 的 钢 种 而 言% 形抗力曲线 % 确定常数 C * * & C C / 1 ; 平整轧制压力模型 + 1 . 根据 / 采用 0 1 234轧机平 整轧 制的 工 艺特 点 %
根 据 现 场 的 实 测 的 轧 辊 辊 身 长 度 的 温 度 分 布%
) ( l / 0 1 234轧机辊系受力及弹性变形计算模型 根 据 文献 ‘ 提供 的 34六辊 轧 机 的 ne / d m‘ 0 d 的解析法和 pe 的影响函数法 相 e o < [ O L f Ge < q O q f [ 辊系变形系统的单元离散划分 * 辊系变 结合的方法 * 形协调处理的方法 % 建立 / 0 1 234轧机 的辊 系受力 及弹性变形计算模型 &用矩阵方法计算 / 0 1 234轧 机的弹性变形共用 / 其中 r个力 A 变形关 /个方程 % 系方程 * 1个平衡方程 * ;个变形协调关系方程 & + / .力 A 变形关系方程 s 工作辊弹性弯曲方程 将 工 作 辊 分 解 为 两 个 悬 臂 梁% 分别求出左右两 部分的挠度 t t vw% vx%
E
AA 弯辊力的影响函数矩阵 & y c | 中间辊弹性弯曲方程 将 中 间 辊 分 解 为 两 个 悬 臂 梁% 分别求出左右两 部分的挠度 t t = w% = x%
u u
u
u
u
u
计算公式的基本结构 & # # I J K L M N O P M 3= J J QB R @ ST U + VEW . X Z Y [ 式中 RAA 轧件宽度 : @AA 平均变形抗力 : U AA 轧辊压扁半径 : T AA 应力状态系数 & X Y F] \YBC D ^