粗轧机厚度自动控制系统的应用
AGC控制

液压AGC控制技术的分析与应用摘要:综述板带轧钢厚度控制技术的发展和产生厚差的原因(主要有:温度、轧制力等)。
着重介绍了液压厚度自动控制的概念、原理、应用等。
关键词:液压AGC;原理;应用第一章液压AGC概念与原理1.1 液压AGC的概念厚度自动控制是通过测厚仪或传感器(如辊缝仪和压头等)对带钢实际轧出厚度进行连续地测量(或估算),并根据实测值与给定值相比较后的偏差信号,借助于控制回路和装置或计算机的功能程序,改变压下位置、轧制压力、张力、轧制速度等,把厚度控制在允许偏差范围之内的方法。
特制品的厚度自动控制在一定尺寸范围内的系统称为厚度自动控制系统,简称为AGC。
液压AGC就是借助于轧机的液压系统,通过液压伺服阀调节液压缸的油量和压力来控制轧辊的位置,对带钢进行厚度自动控制的系统。
1.2板带轧钢产生厚差的原因带钢厚度精度可分为一批同规格带钢的厚度异板差和每一条带钢的厚度同板差。
为此可将厚度精度分解为带钢头部厚度命中率和带钢全长厚度偏差。
从厚差分布特征来看,产生厚差的原因有以下几种: (1)头尾温差,这主要是由于粗轧末出口速度一般比精轧机入口速度要高,因而造成了带钢头部和尾部在空气中停留时间的不同。
( 2)加热炉内导轨在钢胚表面造成的低温段称为水印,由于此段温度变化率大,厚度变动比较“陡”。
(3)活套起套过猛,对带钢产生冲击,使颈部厚度变薄。
( 4 )咬钢时,由于速度设定不协调加上动态速降造成钢套过大,起套并投入高速控制后由于纠偏过快造成带钢拉钢,这一松一紧使厚度减薄,宽度拉窄。
(5)温度波动造成轧制力以及厚度波动。
(6)油膜轴承的油膜厚度发生变化使实际辊缝变化,从而影响轧件厚度。
(7)轧辊偏心将直接使实际辊缝产生高频周期变化。
为了克服或减轻这些干扰因素对成品厚度的影响,除了改进AGC 系统的结构外,还可以将它与各种先进的智能算法相结合,以提高其精度。
1.3液压AGC基本原理1.3.1液压AGC 的设备及其与工作液压AGC技术是将机械、液压、自动控制以及轧制工艺等专业紧密联系在一起的综合先进技术。
轧机厚度自动控制AGC系统说明

轧机厚度自动控制AGC系统使 用 说 明 书中色科技股份有限公司装备所自动化室二零零九年八月二十五日目 录第一篇 软件使用说明书第一章 操作软件功能简介第二章 操作界面区简介第三章 操作使用说明第二篇 硬件使用说明书第一章 接口板、计算机板跨接配置图 第三篇 维护与检修第一章 系统维护简介及维护注意事项第二章 工程师站使用说明第三章 检测程序的使用第四章 常见故障判定方法第四篇 泵站触摸屏操作说明第五篇 常见故障的判定方法附录:第一章 目录第二章 系统内部接线表第三章 系统外部接线表第四章 系统接线原理图第五章 系统接口电路单元图第一篇软 件 说 明 书第一章 操作软件功能简介.设定系统轧制参数;.选择系统工作方式;.系统调零;.显示时实参数的棒棒图、馅饼图、动态曲线;.显示系统的工作方式、状态和报警。
以下就各功能进行分述:1、在轧机靠零前操作手需根据轧制工艺,设定每道次的入口厚度、出口厚度和轧制力等参数。
也可以在轧制表里事先输入,换道次时按下道次按钮,再按发送即可。
2、操作手根据不同的轧制出口厚度,设定机架控制器和厚度控制器的工作方式,与轧制参数配合以得到较理想的厚差控制效果。
3、在泄油状态下,操作手通过在规定状态下对调零键的操作,最终实现系统的调零或叫靠零,以便厚调系统正常工作。
4、在轧制过程中,以棒棒图、馅饼图和动态曲线显示厚调系统的轧制速度、轧制压力、开卷张力、卷取张力、操作侧油缸位置、传动侧油缸位置、压力差和厚差等实时值。
(注意:轧机压靠前操作侧油缸位置、传动侧油缸位置显示为油缸实际移动位置。
轧机压靠后操作侧油缸位置、传动侧油缸位置显示的是辊缝值。
)5、显示系统的工作方式、系统状态和系统报警。
6、系统有两种与传动和测厚仪协调工作模式A.常用数据由厚控AGC发送到传动及测厚仪。
如人口厚度、出口厚度、轧制速度及张力等等。
传动以此为基准值,如调整需通过把手或其他方式加到此基准值上,然后返送回AGC。
浅述轧钢自动化控制系统应用优化
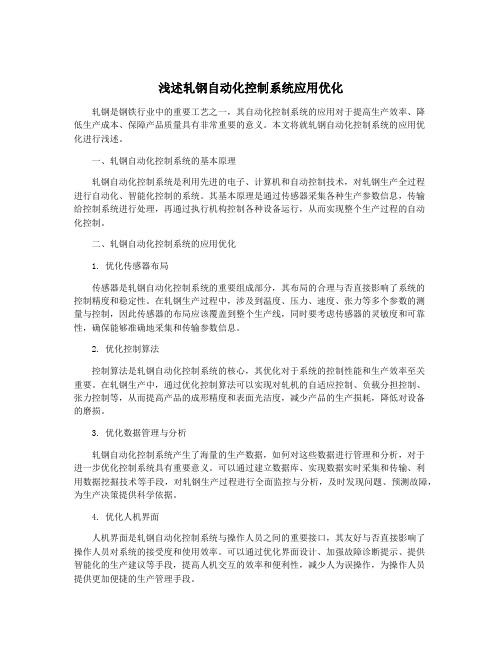
浅述轧钢自动化控制系统应用优化轧钢是钢铁行业中的重要工艺之一,其自动化控制系统的应用对于提高生产效率、降低生产成本、保障产品质量具有非常重要的意义。
本文将就轧钢自动化控制系统的应用优化进行浅述。
一、轧钢自动化控制系统的基本原理轧钢自动化控制系统是利用先进的电子、计算机和自动控制技术,对轧钢生产全过程进行自动化、智能化控制的系统。
其基本原理是通过传感器采集各种生产参数信息,传输给控制系统进行处理,再通过执行机构控制各种设备运行,从而实现整个生产过程的自动化控制。
二、轧钢自动化控制系统的应用优化1. 优化传感器布局传感器是轧钢自动化控制系统的重要组成部分,其布局的合理与否直接影响了系统的控制精度和稳定性。
在轧钢生产过程中,涉及到温度、压力、速度、张力等多个参数的测量与控制,因此传感器的布局应该覆盖到整个生产线,同时要考虑传感器的灵敏度和可靠性,确保能够准确地采集和传输参数信息。
2. 优化控制算法控制算法是轧钢自动化控制系统的核心,其优化对于系统的控制性能和生产效率至关重要。
在轧钢生产中,通过优化控制算法可以实现对轧机的自适应控制、负载分担控制、张力控制等,从而提高产品的成形精度和表面光洁度,减少产品的生产损耗,降低对设备的磨损。
3. 优化数据管理与分析轧钢自动化控制系统产生了海量的生产数据,如何对这些数据进行管理和分析,对于进一步优化控制系统具有重要意义。
可以通过建立数据库、实现数据实时采集和传输、利用数据挖掘技术等手段,对轧钢生产过程进行全面监控与分析,及时发现问题、预测故障,为生产决策提供科学依据。
4. 优化人机界面人机界面是轧钢自动化控制系统与操作人员之间的重要接口,其友好与否直接影响了操作人员对系统的接受度和使用效率。
可以通过优化界面设计、加强故障诊断提示、提供智能化的生产建议等手段,提高人机交互的效率和便利性,减少人为误操作,为操作人员提供更加便捷的生产管理手段。
5. 优化设备互联轧钢生产线上的设备繁多,各种设备之间的协同配合能够直接影响生产效率和产品质量。
轧钢生产过程中自动化控制技术的应用
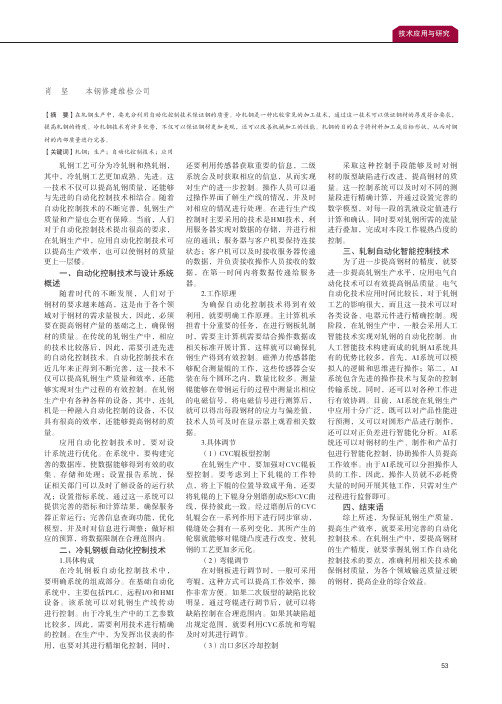
轧钢工艺可分为冷轧钢和热轧钢,其中,冷轧钢工艺更加成熟、先进。
这一技术不仅可以提高轧钢质量,还能够与先进的自动化控制技术相结合。
随着自动化控制技术的不断完善,轧钢生产质量和产量也会更有保障。
当前,人们对于自动化控制技术提出很高的要求,在轧钢生产中,应用自动化控制技术可以提高生产效率,也可以使钢材的质量更上一层楼。
一、自动化控制技术与设计系统概述随着时代的不断发展,人们对于钢材的要求越来越高,这是由于各个领域对于钢材的需求量极大,因此,必须要在提高钢材产量的基础之上,确保钢材的质量。
在传统的轧钢生产中,相应的技术比较落后,因此,需要引进先进的自动化控制技术。
自动化控制技术在近几年来正得到不断完善,这一技术不仅可以提高轧钢生产质量和效率,还能够实现对生产过程的有效控制。
在轧钢生产中有各种各样的设备,其中,连轧机是一种融入自动化控制的设备,不仅具有很高的效率,还能够提高钢材的质量。
应用自动化控制技术时,要对设计系统进行优化。
在系统中,要构建完善的数据库,使数据能够得到有效的收集、存储和处理;设置报告系统,保证相关部门可以及时了解设备的运行状况;设置指标系统,通过这一系统可以提供完善的指标和计算结果,确保服务器正常运行;完善信息查询功能,优化模型,并及时对信息进行调整;做好相应的预算,将数据限制在合理范围内。
二、冷轧钢板自动化控制技术1.具体构成在冷轧钢板自动化控制技术中,要明确系统的组成部分。
在基础自动化系统中,主要包括PLC、远程I/O和HMI 设备。
该系统可以对轧钢生产线传动进行控制。
由于冷轧生产中的工艺参数比较多,因此,需要利用技术进行精确的控制。
在生产中,为发挥出仪表的作用,也要对其进行精细化控制,同时,还要利用传感器获取重要的信息,二级系统会及时获取相应的信息,从而实现对生产的进一步控制。
操作人员可以通过操作界面了解生产线的情况,并及时对相应的情况进行处理。
在进行生产线控制时主要采用的技术是HMI技术,利用服务器实现对数据的存储,并进行相应的通讯;服务器与客户机要保持连接状态;客户机可以及时接收服务器传递的数据,并负责接收操作人员接收的数据,在第一时间内将数据传递给服务器。
液压AGC自动厚度控制系统介绍

一、液压AGC自动厚度控制系统简介液压AGC自动厚度控制系统是现代化轧机提高轧制精度必不可少的技术装备,是生产厂家在未来激烈市场竞争中取得优势的重要保证。
公司致力于液压AGC成套技术与装备的研发、推广。
公司建立了多学科相配套的AGC专业体系,可以集液压AGC自动厚度控制系统的设计、开发、制造、安装、调试于一体,为用户提供优质服务。
目前为止,本公司所推出的液压AGC自动厚度控制系统已经应用在国内外上百条冷轧、热轧带钢生产线上,完全可以满足带钢产品厚度的精确控制。
为了保证带钢产品的厚度精度和良好板型,本系统具有液压压下辊缝控制(AGC)、恒轧制压力控制(AFC)、测厚仪监控,对薄规格产品还可采用张力厚度控制等功能。
本系统工作可靠、操作方便、自我保护功能完备,并具有轧制工艺数据库,在轧制不同规格的带材时,只需要调出相应的轧制工艺即可在每次开始轧制以前设置轧制状态。
应用该系统后,冷轧带钢的厚控精度可以达到:0.15±0.003mm、0.3±0.006mm(纵向厚度偏差)二、系统主要控制功能1、辊缝位置闭环控制(APC);2、带钢厚度闭环控制(监控AGC、张力AGC、秒流量AGC、予控AGC);3、辊缝压靠压力设定及辊缝拨零操作;4、轧辊两侧压/抬同步控制;5、辊缝差设定与钢带纠偏控制;6、轧制力设定与报警;7、各项轧制工艺参数的采集、记录、显示和打印为轧制规程的优化提供参数。
三、主要技术性能指标1、辊缝(厚度)设定精度优于0.001mm2、带材厚度控制精度:±1.5~3%h(带钢厚度)本指标与测厚仪以及来料和轧机精度水平有关。
3、系统响应时间: 30-50 ms四、主要设备介绍1、液压泵站液压泵站主要由主液压泵、蓄能器、油箱,司服阀组,减压稳压阀组、循环过滤机构等组成。
2、压下油缸压下油缸采用优质锻造合金钢制作,经过三次无损探伤,以保证缸体的质量;结构采用特殊设计,油封采用进口产品;装有高分辨率的位移传感器以检测油缸的位移。
厚板轧机液压厚度自动控制系统的应用

中厚 板轧 机 在 我 国钢 铁 生产 中起 着举 足 轻 重 的作用 制 造等 工 业 领域 。 中厚 板 热 轧机 液 压 厚 度 自动控制 ( 简称液压 A C 技术 , G) 替代了传统的 电动 压 下 辊 缝 控 制 , 现 了 辊 缝 动 态 快 速 调 节 。 实 它是提高钢板质量 , 提高成材率 , 增强产品竞争力 的必要手段 , 已成为现代化轧机 的重要标志。 由德 国西 马克 公 司设 计 、 国第 一 重 型 机 械 中 集 团公 司为鞍 钢股份 鲅鱼 圈钢 铁分公 司制造 的 50 m 50 m厚 板 轧 机 是 当前 国 内最 高 装 机 水 平 的 厚 板轧机之一 , 采用两级计算机过程 自动控制 , 轧机 主传动采用全数字调速控制 , 厚调系统采 用电动 程序 自动压下和大载荷中厚板热轧机液压 A C G 技 术 。 其 中 大 载 荷 厚 板 轧 机 液 压 AG C技 术 在 50mm宽 度 、200大 载荷 厚 板 轧机 上应 用 为 国 50 1 0 t 内首 例 。
于 1m , 0 s 同时也 要求计 算 机要 有快 速 的反 应能 力 。为此 , 套 液 压 A C系 统 的 自动 控 制 采用 主 这 G 频很高的双 C U P 计算机 , 采样控制周期仅为2 s m。 为了增加系统 的可靠性 , 提高系统的投用率 , 该系统关键 检测设 备——位移传感器 、 压力传感
【 bt c】T i a i ed cs st a t c r cn o d fu i n dat eo t A s at h rc i us h m i s ut e otl ii le adavn g f h r s t l s e e n r u , r fc t s a e
h da l rw o nss m o eha ypaemi, rsns h aa ee du t n, n a e e y rui s d w yt f h ev lt l pee t tep rm t a js c e e t l r me ta dm kst h
轧钢生产过程中自动化控制技术的应用研究
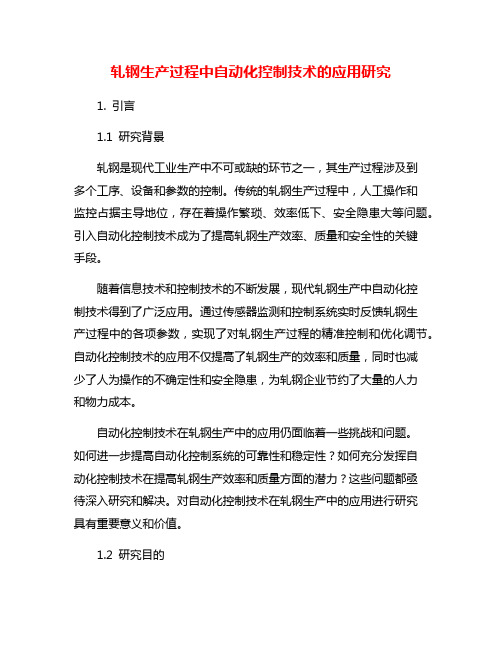
轧钢生产过程中自动化控制技术的应用研究1. 引言1.1 研究背景轧钢是现代工业生产中不可或缺的环节之一,其生产过程涉及到多个工序、设备和参数的控制。
传统的轧钢生产过程中,人工操作和监控占据主导地位,存在着操作繁琐、效率低下、安全隐患大等问题。
引入自动化控制技术成为了提高轧钢生产效率、质量和安全性的关键手段。
随着信息技术和控制技术的不断发展,现代轧钢生产中自动化控制技术得到了广泛应用。
通过传感器监测和控制系统实时反馈轧钢生产过程中的各项参数,实现了对轧钢生产过程的精准控制和优化调节。
自动化控制技术的应用不仅提高了轧钢生产的效率和质量,同时也减少了人为操作的不确定性和安全隐患,为轧钢企业节约了大量的人力和物力成本。
自动化控制技术在轧钢生产中的应用仍面临着一些挑战和问题。
如何进一步提高自动化控制系统的可靠性和稳定性?如何充分发挥自动化控制技术在提高轧钢生产效率和质量方面的潜力?这些问题都亟待深入研究和解决。
对自动化控制技术在轧钢生产中的应用进行研究具有重要意义和价值。
1.2 研究目的本研究旨在探讨轧钢生产过程中自动化控制技术的应用现状和发展趋势,分析自动化控制技术在轧钢生产中的影响和作用。
通过深入研究,我们旨在找出如何更好地利用自动化技术提高轧钢生产效率和产品质量,减少人为干预带来的误差和浪费,实现轧钢生产的智能化管理和控制。
我们还希望借助本研究为轧钢企业提供科学的自动化控制技术应用方案和建议,促进轧钢行业向智能化、绿色化方向发展,提高行业整体竞争力和可持续发展能力。
通过对自动化控制技术在轧钢生产中的研究,我们可以为轧钢行业的技术创新和转型升级提供有益参考,推动轧钢生产过程的现代化和智能化进程。
1.3 研究意义轧钢生产过程中自动化控制技术的应用研究具有重要的研究意义。
随着科技的不断发展,自动化控制技术已经在轧钢生产中得到广泛应用,有效提高了生产效率和产品质量,降低了生产成本,改善了工作环境和劳动条件。
中厚板生产中自动化控制系统的应用与优化

中厚板生产中自动化控制系统的应用与优化摘要:中厚板轧制自动化系统反映了线材轧制控制的自动化程度,采用中厚板轧机自动控制系统不仅可以提高生产质量和利用率,而且可以满足特殊的控制要求。
从AGC绝对厚度控制、轧区跟踪系统和自动轧制三个方面介绍了自动控制优化的实际应用关键词“绝对AGC”;中厚板;自动化系统钢铁行业是典型的制造生产过程包括各种钢铁工业,具有很高的针对性和渗透性。
生产过程不仅包括成本、质量和效率等市场竞争因素,还包括资源、能效和可承受性等因素,以及过程排放、环境兼容性和工业生态系统等可持续发展因素。
一、中厚板生产工艺概述轧制产品(各种钢材)作为钢铁行业长流终端技术,直接服务于各行各业。
轧钢工艺的品种和质量首先代表了钢铁行业的整体生产水平,经过检查和清理的坯料被送到铸坯车间原料跨进行切割所需的长度。
按类型、来源、钢种和生产计划储存。
推料机将一个轧制坯料一个接一个推入辊道,并将其送入加热炉;送料机将板材加热至1150-1250℃后将其推入热炉,板材通过辊子输送至轧机。
除鳞箱经过首先氧化铁皮从高压水中去除;然后进入轧机。
四辊可逆式轧机。
轧机配有锥形工作辊,用于轧制工件。
高压水去除轧制表面的氧化铁。
通用13-17次往复轧,至最终产品的尺寸,轧制后,钢板由钢板矫直机矫直,钢板矫直后由冷床冷却。
在生产过程中,钢板的加工主要包括厚度、宽度、钢板长度等物理尺寸。
为了提高轧制板材的机械性能,通常在轧机后部安装快速冷却装置,将轧制板材冷却到一定温度,以获得所需的板材性能。
厚板自动轧制系统的控制功能包括:将工件从原来的厚度、宽度和长度轧制到所需的厚度、宽度和工件长度。
快速冷却板具有良好的机械性能。
计划在该地区增加产量,以提高生产速度和生产率。
在生产过程中,操作者必须在生产过程中进行指导和控制,维修人员必须有一定的控制手段,以便于错误的处理。
二、案例分析1.AGC厚度绝对控制。
厚钢板轧机的自动控制系统采用AGC绝对厚度控制系统建立轧制宏微观跟踪平台,根据L2系统数据和自动轧制的主要功能,实现可逆自动轧制过程。
- 1、下载文档前请自行甄别文档内容的完整性,平台不提供额外的编辑、内容补充、找答案等附加服务。
- 2、"仅部分预览"的文档,不可在线预览部分如存在完整性等问题,可反馈申请退款(可完整预览的文档不适用该条件!)。
- 3、如文档侵犯您的权益,请联系客服反馈,我们会尽快为您处理(人工客服工作时间:9:00-18:30)。
粗轧机厚度自动控制系统的应用
【摘要】粗轧机是设置在热连轧生产线的关键设备,用于将板坯轧制成规定的中间坯。
本文介绍了厚度自动控制系统在粗轧机厚度控制中的实际应用,并介绍了相关的经验公式。
【关键词】厚度轧制力辊缝位置控制
1.概述
厚度自动控制系统的控制量主要是压下量,即为了控制轧件厚度,就要控制轧辊位置,轧辊位置控制为厚度自动控制服务,这样自动厚度控制系统就有外环为厚度环、内环为轧辊位置环的串级控制系统,轧辊位置自动控制系统是厚度自动控制系统的执行机构。
本文介绍的1750热轧线粗轧机的辊缝调节是通过调节上辊压下量来实现的,下辊无上抬功能。
在粗轧机的传动侧和操作侧各安装有一台压下电机和压下液压缸。
粗轧机轧辊位置自动控制系统包括电动位置自动控制系统和液压位置自动控制系统两部分。
电动位置自动控制系统进行粗调,液压位置自动控制系统进行精调。
粗轧机辊缝调节在空载下进行,在轧制过程中辊缝不进行调节。
2.厚度自动控制(AGC)
2.1厚差产生的原因
厚差分为同板差和异板差。
异板差是指在相同工艺、设备参数条件下,同一批材料中的不同轧件(不同块或不同卷)轧出厚度不均。
异板差主要原因是来料参数(厚度、宽度、轧机入口温度)发生了变化,但未重新对轧机进行设定,即未做到动态设定。
下面讨论的是同板差。
在轧机一定的情况下,轧机弹性刚度系数K为常数,根据轧机弹跳方程:h=f(S,P,K),轧出厚度h与空载辊缝S和轧制力P有关。
因此,凡是引起空载辊缝和轧制力变化的因素都是厚差产生的原因。
厚差产生的原因及消除方法如下表。
表1 厚差产生的原因及消除方法
除了以上厚差产生原因外,对于配置了厚度自动控制系统的轧机,轧机的自动设定不准确、控制系统结构和控制参数设计整定不合理、辊缝、轧制力、张力、温度等测量仪表精度低等因素也是产生厚差的原因。
2.2 AGC的种类
按照控制结构的不同,AGC分为前馈AGC、反馈AGC和补偿AGC。
前馈AGC又称预控AGC,反馈AGC包括压力AGC、厚度仪AGC、张力AGC、连轧AGC。
补偿AGC包括油膜厚度补偿AGC、尾部补偿AGC、轧辊偏心补充AGC。
按照AGC系统使用的操作量的不同,AGC分为压下AGC、张力AGC和速度AGC。
压下AGC是靠调整压下即调整辊缝来消除影响轧制压力造成的厚差。
压力AGC分为厚度计AGC、动态AGC、绝对值AGC等等。
张力AGC是靠调整前后张力来改变轧件塑性刚度系数来控制轧件的厚度的。
速度AGC是靠调整轧制速度来控制厚度的。
2.3厚度计AGC
本文介绍的1750热轧线粗轧机厚度自动控制系统采用的是厚度计AGC(或称GM-AGC)。
在轧制过程中,68
69
任何时刻的实际轧制力和空载辊缝都可以检测到,因此,可以用轧机弹跳方程计算出任何时刻的实际轧出厚度。
在这种情况下,就等于把整个机架作为测量厚度的“厚度计”,这种检测厚度的方法称为厚度计方法(简称GM ),以区别用测厚仪直接检测厚度的方法。
根据轧机弹跳方程测得的厚度和厚度偏差信号进行厚度自动控制的系统称为厚度计AGC 。
2.3.1 厚度计AGC 控制原理,见图1。
图1 厚度计AGC 控制原理 2.3.2 测厚计回路辊缝计算,见公式:
其中:
s load :实际辊缝[mm]
s noload :实际无载辊缝[mm]
s Str,A :工作点上的轧机弹跳[mm]
s bearing :轴承偏心 [mm]
k :补偿因数
C g,A :工作点上的弹跳常数 [kN/mm]
F R,act :实际轧制力 [kN]
F R,preset :轧制力设定[kN]
2.3.3 机架特性
机架特性描述了轧制力和机架弹性之间的关系。
有载辊缝增大、测量位置值和轧制力增加都是是由于机架变形引起的。
轧机弹跳公式:s s C F F Str Str A g A act eset =+⋅-,,Pr ()1
其中:
s Str :总的轧机弹跳
s Str,A :工作点上的轧机弹跳轧制力
F act :轧辊辊径
F Preset :板坯宽度
C g,A :弹跳系数
弹跳系数公式: 1
C F g A w A ,f =∂∂
( )
s s load noload = + + ⋅ ⋅ - + s k C F F s Str A g A R act R p reset bearin g , , , , 1
其中:
:工作点上的轧机系数[kN/mm]
C
g,A
A:工作点
2.3.4 过载保护
为了避免对设备的损害,厚度自动控制中添加了一个过载保护控制单元。
通过此控制单元提供一个附加设定值,当轧制力超限时使辊缝自动打开。
3.厚度计AGC的特点
3.1 可以克服直接测厚仪AGC的检测滞后,提高了系统灵敏度,但是对于压下机构的电气和机械系统以及计算机控制时程序运行等的时间滞后仍然不能消除。
3.2 可以消除轧件和工艺方面等多种原因通过轧制压力造成的厚差,如轧件温度、化学成分、摩擦系数、轧前轧件厚度、宽度等因素变化,适应范围广。
3.3 控制精度较低。
用轧机弹跳方程间接测厚难以测出轧辊热膨胀和磨损、偏心运转、油膜轴承浮动效应、压下螺丝的回松以及初始辊缝的设定误差等因素引起的厚度变化。
3.4 对轧辊偏心运转引起的高频变化的厚差难以控制(如采用电动压下系统,则不能控制),容易引起压下系统误动作。
3.5 厚差控制过程中,轧制力为正反馈变化过程。
当测出的轧制力大于设定值时,厚度计AGC会认为轧出厚度偏大而调小辊缝,轧制力会进一步增大,这样,轧制力很容易超出允许范围,而不能进一步减小厚差。
此外,轧制力变化引起轧辊挠度变化,导致板形变化,不利于板形稳定。
3.6当轧件塑性刚度系数M很大或轧机刚度系数K不大时,压下效率很低,压下移动的距离大部分转变为轧机弹性变形,严重时完全不起作用,因此在轧件变形抗力较大时,不采用调压下的厚度计AGC,而改用调节张力的方法来消除厚差。
4.结束语
由于轧机负荷辊缝的实时直接测量至今尚未解决,通过检测轧制力和辊缝位置信号,根据轧机弹跳方程计算轧出轧件厚度进行厚度控制的压力AGC系统一直是厚度控制系统的核心。
热轧1750mm生产线AGC 系统运行稳定,产品的厚度控制精度不断提高,取得了很大经济效益,也为AGC系统进一步优化奠定了基础。
参考文献
[1] 李登超,参数检测与自动控制,北京:冶金工业出版社,2004。
70。