棒材轧机的自动控制系统
浅谈棒材中轧飞剪控制系统

浅谈棒材中轧飞剪控制系统本文介绍了河北钢铁集团棒材全连轧工程中轧飞剪的系统配置及控制理论,其控制系统。
飞剪全数字位置闭环1 概述河北钢铁集团棒材全连轧工程设计生产,主要产品为螺纹钢筋和圆钢棒材,全线轧机采用平立交替布置,并采用了高刚度短应力线精轧机、切分轧制工艺、在线热处理工艺、带密集链的步进式冷床、两级自动化控制等先进装备和技术,最高轧制速度为18m/s,轧线设备装备和自动化控制均达到国内同类轧线较高水平。
中轧飞剪的主要功能是切头、切尾及事故碎断,它关系到轧件能不能顺利进入精轧机组及成材率,故而对中轧飞剪剪切控制尤其重要,下面以河北钢铁集团棒材中轧飞剪为例,分析一下它的具体控制理论。
2 传动及自动化系统配置传动系统:采用西门子公司的全数字直流调速装置6RA70-25型,通过扩容,构成调速装置。
即得用西门子公司60A装置中的控制模块来控制,用国产晶闸管经过改装替换60A装置中的原装功率模块,做到以小带大,这样既保持了西门子装置系统的先进性,又大大降低了投资费用。
自动化系统:直流传动装置配套西门子公司的CBP2通讯板及T400工艺板来完成通讯和控制。
T400模板是SIMADYND系统新一代的工艺类型产品,它因有一个32位CPU板而具有极高的运算能力和强大功能。
T400的运算能力相当于功能强大的SIMADYND-D CPU,它可以做为选件插入西门子的交、直流驱动装置,数据由T400经驱动器的高速双口RAM传送到驱动器的主控制模块和通讯模块中。
T400模块的最小执行周期小于0.8ms,运算为浮点小数,并且与主控模块和通讯模块同步。
由于CBP2与T400都是以选件的形式内置于直流调速装置,这就大大的节省了成套空间,而且CBP2与T400之间的同步通讯保证了上位机发出的指令能及时的传达给T400工艺模板,并由后者完成最终的控制。
3 剪刃位置控制设计剪切位即两个剪刃完全闭合的位置为零位,安装接近开关,用于程序里面的位置复位及定位,T400通过飞剪电机后面的编码器及传动减速比来确定飞剪剪刃的位置(0°~360°),当接到剪切指令后开始起动加速,加速到一定角度时到达设定值,然后开始匀速运行直至到达剪切位置,整个剪切过程大约为250°;当剪切完成后到达减速位置,采用速度位置闭环PID调节给定的方式,到达停止位置速度为0,剪刃停在停止位置。
棒材打包机自动控制系统的设计及应用
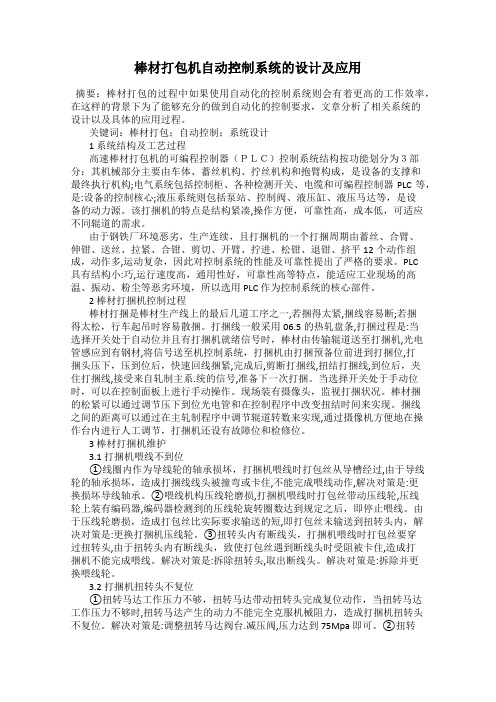
棒材打包机自动控制系统的设计及应用摘要:棒材打包的过程中如果使用自动化的控制系统则会有着更高的工作效率,在这样的背景下为了能够充分的做到自动化的控制要求,文章分析了相关系统的设计以及具体的应用过程。
关键词:棒材打包;自动控制;系统设计1 系统结构及工艺过程高速棒材打包机的可编程控制器(PLC)控制系统结构按功能划分为3部分:其机械部分主要由车体、蓄丝机构、拧丝机构和抱臂构成,是设备的支撑和最终执行机构;电气系统包括控制柜、各种检测开关、电缆和可编程控制器PLC等,是:设备的控制核心;液压系统则包括泵站、控制阀、液压缸、液压马达等,是设备的动力源。
该打捆机的特点是结构紧凑,操作方便,可靠性高,成本低,可适应不同辊道的需求。
由于钢铁厂环境恶劣,生产连续,且打捆机的一个打捆周期由蓄丝、合臂、伸钳、送丝、拉紧、合钳、剪切、开臂、拧进、松钳、退钳、挤平12个动作组成,动作多,运动复杂,因此对控制系统的性能及可靠性提出了严格的要求。
PLC具有结构小:巧,运行速度高,通用性好,可靠性高等特点,能适应工业现场的高温、振动、粉尘等恶劣环境,所以选用PLC作为控制系统的核心部件。
2 棒材打捆机控制过程棒材打捆是棒材生产线上的最后几道工序之一,若捆得太紧,捆线容易断;若捆得太松,行车起吊时容易散捆。
打捆线一般采用06.5的热轧盘条,打捆过程是:当选择开关处于自动位并且有打捆机就绪信号时,棒材由传输辊道送至打捆机,光电管感应到有钢材,将信号送至机控制系统,打捆机由打捆预备位前进到打捆位,打捆头压下,压到位后,快速回线捆紧,完成后,剪断打捆线,扭结打捆线,到位后,夹住打捆线,接受来自轧制主系.统的信号,准备下一次打捆。
当选择开关处于手动位时,可以在控制面板上进行手动操作。
现场装有摄像头,监视打捆状况。
棒材捆的松紧可以通过调节压下到位光电管和在控制程序中改变扭结时间来实现。
捆线之间的距离可以通过在主轧制程序中调节辊道转数来实现,通过摄像机方便地在操作台内进行人工调节,打捆机还设有故障位和检修位。
棒材生产的自动控制(DOC)
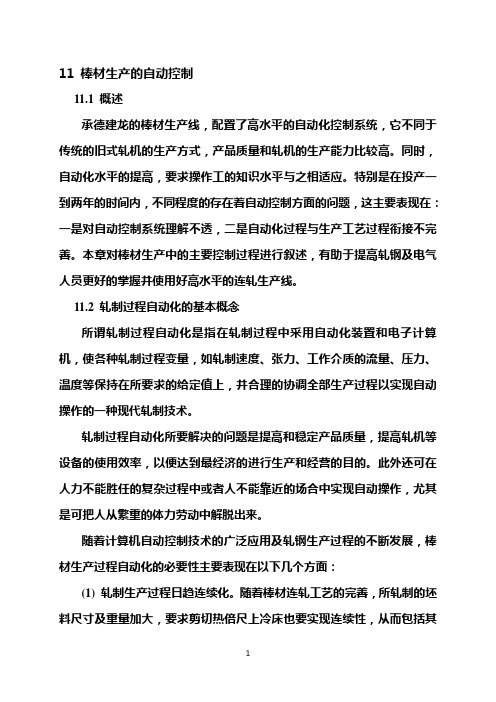
11 棒材生产的自动控制11.1 概述承德建龙的棒材生产线,配置了高水平的自动化控制系统,它不同于传统的旧式轧机的生产方式,产品质量和轧机的生产能力比较高。
同时,自动化水平的提高,要求操作工的知识水平与之相适应。
特别是在投产一到两年的时间内,不同程度的存在着自动控制方面的问题,这主要表现在:一是对自动控制系统理解不透,二是自动化过程与生产工艺过程衔接不完善。
本章对棒材生产中的主要控制过程进行叙述,有助于提高轧钢及电气人员更好的掌握并使用好高水平的连轧生产线。
11.2 轧制过程自动化的基本概念所谓轧制过程自动化是指在轧制过程中采用自动化装置和电子计算机,使各种轧制过程变量,如轧制速度、张力、工作介质的流量、压力、温度等保持在所要求的给定值上,并合理的协调全部生产过程以实现自动操作的一种现代轧制技术。
轧制过程自动化所要解决的问题是提高和稳定产品质量,提高轧机等设备的使用效率,以便达到最经济的进行生产和经营的目的。
此外还可在人力不能胜任的复杂过程中或者人不能靠近的场合中实现自动操作,尤其是可把人从繁重的体力劳动中解脱出来。
随着计算机自动控制技术的广泛应用及轧钢生产过程的不断发展,棒材生产过程自动化的必要性主要表现在以下几个方面:(1) 轧制生产过程日趋连续化。
随着棒材连轧工艺的完善,所轧制的坯料尺寸及重量加大,要求剪切热倍尺上冷床也要实现连续性,从而包括其他一些连续性生产过程在内,使得连轧棒材生产的加热、轧制及后部精整剪切、包装等生产过程全部实现了连续化。
人本身很难在较短的时间内完成各个连续性的生产环节,而计算机自动控制过程解决了这一难点,使连续化生产得以实现,从而大大提高了生产效率,提高了轧钢车间的机时产量,使得生产规模越来越大。
(2) 轧制速度不断提高。
轧制过程的连续化为轧制速度的提高创造了条件,机加工的精度的提高也为连续高速度生产创造了机械条件。
目前传统工艺棒材生产轧制速度达20m/s左右,高速棒材生产速度突破了40m/s,大大超过了老式轧机的轧制速度,这样对轧件在线跟踪控制提出了更高的要求,而计算机快速反应及高灵敏度的跟踪控制恰恰满足了这一点。
Φ300mm棒材机组倍尺飞剪自动控制系统
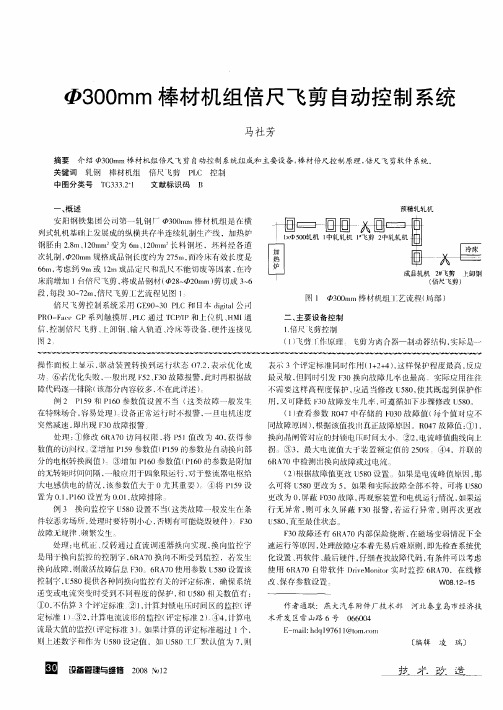
马社 芳
摘要 关键词 介绍 q30 m棒 材机组4 X - 剪 自动控 制系统组成和主要设备,  ̄0 m  ̄ . - E 棒材倍尺控制原理 , 尺飞剪软件系统 倍 轧钢 棒材机组 倍尺 剪 P C 控制 L
B
预精轧 轧机
中 图分 类 号 F 3 3 G 3. l 2
网 l q3 0 50 mm捧 材 机组 j 艺 流 程 ( J : 局部 ) 二 、 要 设备 控 制 主 1 尺 剪控 制 . 倍 () 1飞剪 作 原 理 剪 离 合器 一 制 动器 结 构 , 际是 一 实
P O F c P系 列触 摸 屏 ,I R — aeG P C通 过 T PI 上 f 、 I C/ P和 机 HM 通
在特殊场合 , 容易处理 )设备正 运仃时/报警 , 旦电机速度 : { 一
突然 减 速 . 现 F 0 障 报 警 即 3故
处理 : 修改 6 A 0访 问权 限 . P 1 R7 将 5 值改 为 4 , 0 获得 参 数值的访『仅 。 增加 P 5 口 】 19参数值( l9的参数是 F动换 部 P5 : I 分的电枢转换 值 ) 一@增加 P 6 参数值 ( l0的参数是附加 10 P6
的无 转 矩 时 间 间隔 , 般 廊 片 于 四象 限运 行 . 于整 流 器 电 怄给 一 j 对 大 电感 供 电的 情 况 , 参 数 值 大 于 0 该 尤 重 要 )
置 为 01P 6 ., l0没 置 为 0O , 障 排定值的 20 5 %:④4 ,并联 的
行无异 常 , 町永久屏蔽 F 0报警 , 运行 异常 , 则 3 若 则再 次更改
U 8 , 至 最 佳状 态 。 50 肓
棒材生产线自动控制系统改造设计与实现
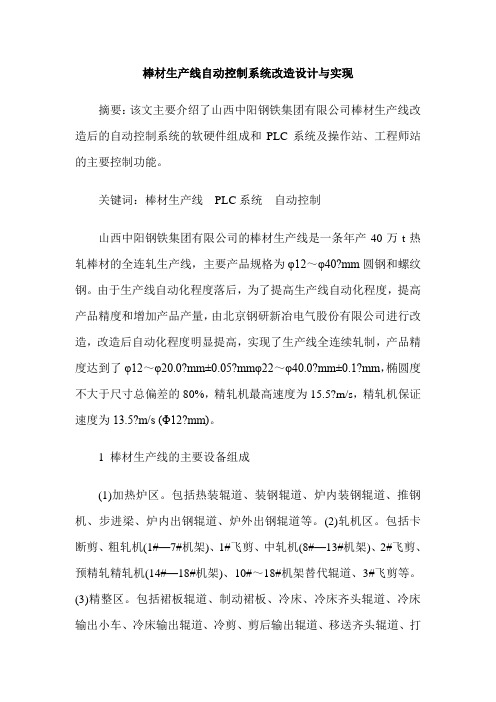
棒材生产线自动控制系统改造设计与实现摘要:该文主要介绍了山西中阳钢铁集团有限公司棒材生产线改造后的自动控制系统的软硬件组成和PLC系统及操作站、工程师站的主要控制功能。
关键词:棒材生产线PLC系统自动控制山西中阳钢铁集团有限公司的棒材生产线是一条年产40万t热轧棒材的全连轧生产线,主要产品规格为φ12~φ40?mm圆钢和螺纹钢。
由于生产线自动化程度落后,为了提高生产线自动化程度,提高产品精度和增加产品产量,由北京钢研新冶电气股份有限公司进行改造,改造后自动化程度明显提高,实现了生产线全连续轧制,产品精度达到了φ12~φ20.0?mm±0.05?mmφ22~φ40.0?mm±0.1?mm,椭圆度不大于尺寸总偏差的80%,精轧机最高速度为15.5?m/s,精轧机保证速度为13.5?m/s (Φ12?mm)。
1 棒材生产线的主要设备组成(1)加热炉区。
包括热装辊道、装钢辊道、炉内装钢辊道、推钢机、步进梁、炉内出钢辊道、炉外出钢辊道等。
(2)轧机区。
包括卡断剪、粗轧机(1#—7#机架)、1#飞剪、中轧机(8#—13#机架)、2#飞剪、预精轧精轧机(14#—18#机架)、10#~18#机架替代辊道、3#飞剪等。
(3)精整区。
包括裙板辊道、制动裙板、冷床、冷床齐头辊道、冷床输出小车、冷床输出辊道、冷剪、剪后输出辊道、移送齐头辊道、打包辊道、打包机、成捆器等。
2 轧线自动控制系统在本系统中通讯网络配置主要是由工业以太网(INDUSTRIAL ETHERNET)和Profibus-DP网,组成两层通讯网络系统。
系统配置如图1所示。
工业以太网(INDUSTRIAL ETHERNET)主要是完成操作站同PLC设备和工厂管理机的数据、信息通讯功能;留有同上级工厂管理机之间的工业以太网通讯接口;操作站、工程师站、PLC之间的工业以太网通讯速率100Mbit/s;工业以太网通讯介质采用工业用光纤;Profibus-DP网主要是完成PLC设备同传动设备和远程I/O装置之间的数据、信息通讯功能。
棒材生产线自动控制系统改造设计与实现

在 轧 线 自动 化 系 统 中 , 除 可 编 程 续 控 的 单 调量 时, 下 游 机 架及 本 机 架 的延 伸率 都 制器 ( P L C) 外, 还 配 置 了工业 P C机作 为 工 会 发 生 变化 。 这 种 调 节 方法 主 要 用 于 本 机
作 站, 为 此 选 用 著名 的 美 国M i c r o s o f t ( 微 架 速 度不 适合 于上游 和 下 游机 架 的情 况 。 正
文章编 号: 1 6 7 4 - 0 9 S X ( 2 0 1 3 ) 0 6 ( c ) 一 0 0 6 9 — 0 2
山西 中阳 钢 铁 集 团 有 限 公 司 的 棒 材 生 冷 床 区的 自动 控 制 其 中P LC1 选 用 了2 个
Vl ;Vi +1 /E i +1
产线 是一 条年产4 0 万t 热 轧棒 材 的 全 连 轧 C P U4 1 6 - 2 D P , P LC 2 选 用 了1 个C P U 4 1 6 — 在 实际 中, 也是设定出口 机 架 的 速 度 和 生产 线, 主 要 产 品规 格 为 1 2 ~ 4 0 mm 2 DP , P L C3 选用了1 个C PU3 l 5 - 2 D P 进 行 各 机 架 的延 伸 率 来 计 算 各 机 架 的 基 准 速度 圆 钢 和 螺 纹 钢 。由于 生 产 线 自动 化 程 度 落 数 据 处 理 与 通 讯 。 在各 操 作点 、 操 作 台 设 给 定 还 有 就 是 各机 架 附 加 的速 度 给 定 , 包
1 棒 材 生产 线 的 主要设 备组 成
软) 公司的服务器/ 客 户 机 操 作 系统 , 系 统 常 情 况 下 因为 单 调 量 调 节会 同时 影 响 两 个 相邻机架的延伸率即秒流量相等的平衡,
棒材连轧二级过程控制系统的应用
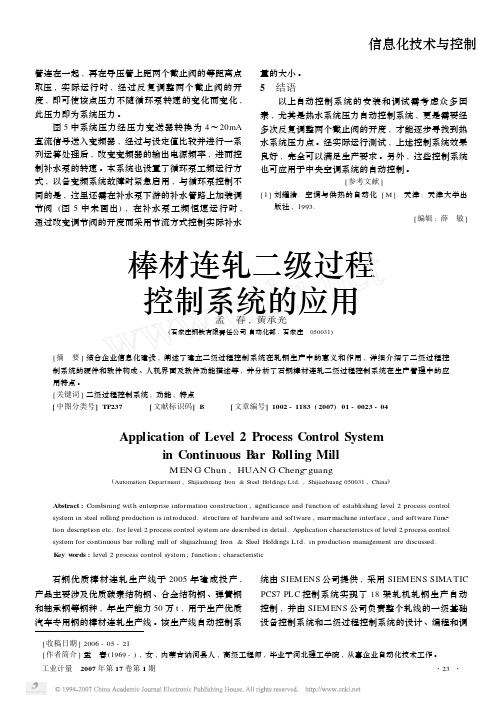
管连在一起,再在导压管上距两个截止阀的等距离点取压,实际运行时,经过反复调整两个截止阀的开度,即可使该点压力不随循环泵转速的变化而变化,此压力即为系统压力。
图5中系统压力经压力变送器转换为4~20mA 直流信号送入变频器,经过与设定值比较并进行一系列运算处理后,改变变频器的输出电源频率,进而控制补水泵的转速。
本系统也设置了循环泵工频运行方式,以备变频系统故障时紧急启用,与循环泵控制不同的是,这里还需在补水泵下游的补水管路上加装调节阀(图5中未画出),在补水泵工频恒速运行时,通过改变调节阀的开度而采用节流方式控制实际补水量的大小。
5 结语以上自动控制系统的安装和调试需考虑众多因素,尤其是热水系统压力自动控制系统,更是需要经多次反复调整两个截止阀的开度,才能逐步寻找到热水系统压力点。
经实际运行测试,上述控制系统效果良好,完全可以满足生产要求。
另外,这些控制系统也可应用于中央空调系统的自动控制。
[参考文献][1]刘耀浩.空调与供热的自动化[M ].天津:天津大学出版社,1993.[编辑:薛 敏]棒材连轧二级过程控制系统的应用孟 春,黄承光(石家庄钢铁有限责任公司自动化部,石家庄 050031) [收稿日期]2006-05-21 [作者简介]孟 春(1969-),女,内蒙古讷河县人,高级工程师,毕业于河北理工学院,从事企业自动化技术工作。
[摘 要]结合企业信息化建设,阐述了建立二级过程控制系统在轧钢生产中的意义和作用,详细介绍了二级过程控制系统的硬件和软件构成、人机界面及软件功能描述等,并分析了石钢棒材连轧二级过程控制系统在生产管理中的应用特点。
[关键词]二级过程控制系统;功能;特点[中图分类号]TP237 [文献标识码]B [文章编号]1002-1183(2007)01-0023-04Application of Level 2Process Control Systemin Continuous B ar R olling MillM EN G Chun ,HUAN G Cheng 2guang(Automation Department ,Shijiazhuang Iron &Steel Holdings Ltd 1,Shijiazhuang 050031,China )Abstract :Combining with enterprise information construction ,significance and function of establishing level 2process control system in steel rolling production is introduced.structure of hardware and software ,man 2machine interface ,and software func 2tion description etc.for level 2process control system are described in detail.Application characteristics of level 2process control system for continuous bar rolling mill of shijiazhuang Iron &Sleel Holdings Ltd.in production management are discussed.K ey w ords :level 2process control system ;function ;characteristic 石钢优质棒材连轧生产线于2005年建成投产,产品主要涉及优质碳素结构钢、合金结构钢、弹簧钢和轴承钢等钢种,年生产能力50万t ,用于生产优质汽车专用钢的棒材连轧生产线。
棒线材复合轧线自动控制系统

穿水冷却辊道( 或替换辊道) 3 飞剪一冷床输人辊 一 #
变的基础上新 增一条线材生产 线 , 两者共用 加热炉和粗
轧( 6架轧机) 、中轧( 6架轧机) 及棒材精轧( 架轧机) 6 的工
道一冷床 ; 当生产线工作在 线材模 式下 , 工艺流程为 : 加 热钢坯 一 出炉辊 道 一粗 轧机 组 一 l# 飞剪 一 中轧机组
经验 交 流
T ch l aIC o m un c to e i rc m l a i ns
《 动 化 技 术 与 应 用 2 自 01 0年第 2 9卷第 6期
机前夹送辊 一吐丝机 一风冷辊道 一集卷 站 。工作原理 ¨
一
艺设备 , 从棒材分段剪( # 飞剪) 3 后设分钢道岔 , 接线材精
2# 飞剪一精轧机组( 作为线材的预精轧机组 ) 一穿水
冷 却辊道 ( 或替换辊道 ) 3 飞剪 前夹送 辊一分钢道岔 一 #
收稿 日期 :2 1 — — 01 2 00 0
一
夹送 辊 一线材 飞剪 一 线材精 轧机 组 一水冷 段 一吐 丝
6 0万吨棒线材复合 线有 两种工作模 式 , 当生产 线工
年进行 6 0万吨棒 线材 复合技改 , 电投钢铁为股 份公司提 供3 0万吨优质 线材 , 提高 企业持续盈利能力 。
6 吨棒 线材复合技 改方案 是 : 0万 现有棒材生产 线不
作在棒 材模 式下 , 艺流程 为 : 工 加热钢坯 一 出炉 辊道 一 粗轧机组一 l 飞剪一 中轧机组一 2 飞剪 一精轧机组 # #
有2 5万 吨金属制 品生产能力 , 特殊 品种 、特殊结构 、高 附加值 、重 要用途 钢 丝绳 的生 产与 技术居 国 内同行前 列 。结 合两企业 的行业特征和 经营现状 , 以及未来 行业 发展趋 势 , 发挥两个企业上下游产业链 的结合优势 , 0 7 2 0 ~ Nhomakorabea鼠
- 1、下载文档前请自行甄别文档内容的完整性,平台不提供额外的编辑、内容补充、找答案等附加服务。
- 2、"仅部分预览"的文档,不可在线预览部分如存在完整性等问题,可反馈申请退款(可完整预览的文档不适用该条件!)。
- 3、如文档侵犯您的权益,请联系客服反馈,我们会尽快为您处理(人工客服工作时间:9:00-18:30)。
轧钢厂一车间棒材轧机的自动控制系统
轧钢厂一车间棒材生产线是由包头钢铁设计研究院设计。
该套年产量60万t的棒材轧机于2003年5月建成投产以后,设备运行基本稳定可靠,单位小时产量已经达到了原设计水平。
1主要工艺设备和系统配置
1.1工艺设备概况
该套轧机为连续式,由7台∮550mm(3台)/∮450mm (4台)可逆初轧机、1台切头切尾和事故碎断用的切头飞剪、、4台∮380mm中轧机、1台气钢推动的事故卡断剪、6台∮320㎜平立式精轧机(12H、14H、16H三架水平轧机和13V、15V、17V三架立式轧机组成)、6个活套装置、精轧后辊道、1台成品倍尺飞剪、冷床输入辊道(四段)、裙板拔钢装置、步进式冷床及横移装置、冷床输出辊道、冷剪和成品收集等设备组成,该轧机出口速度最高可达15m/s,可生产∮16~50㎜规格的圆钢和螺纹钢。
1.2系统配置
根据工艺和生产的要求,在轧制线上配备了2套工控微机(在主操作台)和5套plc装置(在主电PLC室)。
Plc1 主要用于轧机辅助设备控制(如液压站、辊道、风机等);Plc2主要完成轧制线17台直流电机的速度级联调速控制,6个活套的控制,切头飞剪和冷床的控制;Plc3用于成品倍尺飞剪区域设备的控制(整套引进意大利DANELI公司)、plc4用于精整区所有设备的控制、plc5用于冷剪设备的控制(整套引进意大利DANELI公司)。
2套工控微机各含有1个操作键盘、1台监控器CRT和1台主机。
2套工控微机都设在主操作台站内,其中,1套工控微机用于轧制表的输入和轧制速度等显示。
另1套工控微机用于监控并显示现场设备所处的状态,可记录当前和历史数据,它的CRT显示内容与前1套工控微机的内容基本相同,但是,在主操作室内,各输入参数既可供显示,也能做修改。
2主操作站功能和CRT显示
主操作站内的工控微机有一个人机对话监控系统,主要用于输入各种轧制和控制用参数。
轧机监控系统的画面构成和相互调用关系.
本监控系统从轧钢的工艺特点和操作要求出发,包括了轧机系统的所有主要工艺流程、检测参数、设备状态的显示,也集中了轧钢系统的监视和控制得到完全的统一。
操作人员可以及时准确地了解系统的当前状态,并方便、迅速、可靠地对设备作出相应的调整,既简化了操作人员的工作,又使系统随时处于监控状态,提高了系统的安全性和可靠性。
在“轧制配置表”画面中,可输入和显示轧制规格、出口机架速度、机架的配置等参数(而成品倍尺长度以及剪机参数则由操作人员在外商提供的OP17操作面板上输入),也可以调用原来存储在计算机中的轧制程序。
在“轧制参数表”中,可输入和显示各个机架的工作辊径和延伸率,并显示机架的轧辊圆周线速度。
在“轧机”画面中,可输入和显示飞剪的切头长度、活套的高度、电机转速等。
,可保存最新的故障信息。
3级联调速控制和活套起、落套控制
在棒材连轧机中,为保证产品质量,以成品基架-末基架为基准基架,保持其速度不变并作为其基准速度设定,其上游基架速度根据金属秒流量相等原理,自动按比例设定,在轧制过程中来自活套闭环控制的调节量和人工的手动干预调节量,依次按逆轧制方向对其前面上游的各基架的速度作增减,实现级联控制。
在轧制调试初期,或新品种试生产期间,或生产过程中各种因素的影响,会使速度级联关系发生变化,需要进行人工干预,调节机架的速度,使全轧线的运行保持稳定。
从轧件咬入轧辊至速度反馈控制响应之前,由于负荷的突然变化,该机架的电机会产生一个
动态速降,为改善转速动态响应的过渡过程,系统引入了过速控制环节。
过速控制的逻辑信号来自热金属检测器。
当N-1机架前的热金属检测器检测到轧件头部时,第N机架的速度基准值自动增加一个△V。
N-1机架咬钢后,N-1机架的速度基准值自动还原。
这样,随着轧件的流动,一个个机架的转速依次过速、还原,完成过速控制过程。
过速控制可以改善动态品质,以获得快速、稳定的最佳过渡过程。
△V的值在调试中确定,操作人员在生产过程中也可以调整优化该数值。
头部微张力控制:微张力控制的目的是使中轧机组各机架之间的轧件按微小的张力进行轧制。
微张力控制是保证高速棒线材轧机顺利轧制和提高产品质量的必要手段。
张力控制是一个复杂的过程,高速棒线材一般采用“电流—速度”间接微张力控制法,它的基本思想是:张力的变化是由线材的秒流量差引起的,而调整轧机的速度就能改变秒流量,以达到控制张力的目的。
其控制方法同轧机速度的级联调速方向有关,如果级联速度为逆调,则需控制各机架的前张力;如果级联速度为顺调,则需控制各级机架的后张力,即:当钢坯咬入下一机架后,根据本机架同下游机架之间的堆拉关系来调整下机架的速度设定,使本机架与下机架之间的张力维持在设定值。
在启动活套控制之前,起套辊必须先启动。
当活套扫描器测到轧件头部后延迟一段时间,确保轧件咬入下一个机架后,起套辊才能启动;而在前一个活套扫描器或热金属检测器检测到轧件尾部以后延迟一段时间,使轧件尾部即将离开前一机架时,起套辊才复原。
起套辊起动、复原的延迟时间由电气人员可操作,活套高度的设定可以通过相应的画面来调整优化。
轧件跟踪和模拟过钢测试
轧辊的工作辊径、轧机出口速度和各机架的延伸率确认以后,计算机能自动计算出轧件从一个热金属检测器到下一个热金属检测器所需的运行时间,即理论时间。
在轧制过程中,热金属检测器可以测得轧件运行的实际时间,若实际时间比理论时间超出某一个百分比值,切头剪将自动对轧件进行碎断剪切。
这个超出的百分比数值由操作人员通过画面直接确定。
系统还设置了模拟过钢测试功能。
在轧制第1根棒材之前,操作人员可以在画面上按照轧件流程依次点亮热金属检测器,就能模拟显示出实际过钢时的控制响应,包括过速控制、剪机的剪切和起套辊的动作等。
倍尺飞剪的长度和短尺控制
倍尺长度和速度的调整量及剪刃位置的修改可以由操作员在OP17面板上改变(在OP17操作面板上可以进行对倍尺的优化,例如尾部短尺小于9米时,可以把此短尺舔加到倒数第2、3根倍尺上,使得此短尺不在出现,但此优化效果也并不是很理想,因为它还并不成熟)。
在倍尺飞剪前后设有3个热金属检测器,其中,剪后面的1个热金属检测器主要用于尾部短尺控制,前面的2个主要用于倍尺剪切控制,飞剪为曲柄式/回转式,启停工作制,按棒材规格可选带与不带飞轮。
以第17机架出成品为例,当轧件到达剪前第1个热金属检测器时,启动PLC2中的脉冲计数器对17机架电机上的增量编码器发出的脉冲计数。
设剪刃从初始位S0运行到剪切位Sc转过的弧长为C,则剪刃从初始位到剪切位所需运行时间为:Tf=C/Vf
式中Vf为倍尺飞剪的剪刃线速度。
从PLC3发出剪切指令到倍尺飞剪制动器松开所需时间为T0。
设倍尺长度为Lm,对应的轧件运行时间为Tm=Lm/Vm (Vm为轧件运行的速度)
从剪前热金属检测器到剪刃剪切位,轧件运行时间T1为T1=L1/Vm (L1为剪前热金属检测器到剪刃剪切位的长度)
从轧件头部到达剪前第一个热金属检测器开始,经延时T2时间发出第1次剪切指令,即有T2=Tm+T1-Tf-T0
设增量编码器的每转脉冲数与17架电机转速的乘积为P,则经T2时间,计数器的脉冲数A1为A1=T2×P
从轧件头部到达剪前第一个热金属检测器开始,经计数A1个脉冲发出第1次剪切指令。
在发出第1次剪切指令后,即开始第2次剪切脉冲计数。
第2次及以后各次的脉冲计数是从前一次剪切指令发出开始的,则有Aī=Tm×P式中ī=2,3,4----为剪切序数。
每发出一次剪切指令时都对脉冲计数器清零。
从轧件离开剪前第2个热金属检测器时,开始尾部短尺剪切控制。
检测器测到轧件尾部并延时⊿t后,程序对脉冲计数器强制清零复位且封锁剪切指令。
为分析方便,先假设⊿t=0,此时剩余轧件的长度可分为二段计算。
第1段从检测器到剪刃剪切位,其折合成品的长度Ln 为Ln=L1+L2+L3×R6+L4×R5×R6式中R5、R6分别为16、17机架的延伸率。
第2段从剪刃剪切位到剩余轧件的头部,设其长度为LB,则Lb的最小可能值为零(倍尺飞剪刚巧执行剪切指令并到达剪刃位);Lb的最大可能值为
Lb max=Lm-Vm(Tf+T0) (倍尺飞剪即将执行剪切指令)。
所以,剩余轧件长度L1(L1=Lb+Ln)可能范围为
Ln≤L1<Ln+Lm-Vm(Tf+T0)
如果△t>0,则当程序封锁剪切时,轧件尾部至剪刃剪切位的长度为Ln-Vm△t.,此时,剩余轧件的长度范围为
Ln-Vm△t≤L1<Ln+Lm-Vm(Tf+T0+△t)
由上式可以看出,△t越小,最后一段短尺料的下限值就越大,同时,最后一段不剪切轧件的上限值也越大。
,过短轧件装上冷床会产生穿蜗牛事故,过长轧件超出冷床台面长度会引起堆钢,所以必须选择正确的△t值的,以兼顾二者的关系和要求。
操作人员可在相关画面上调整△t的大小,来控制最后一根轧件的长度范围。
棒材经倍尺剪剪切后,经过穷板的上位、中位、下位延时被拔上冷床(上、中、下位的时间可以由操作员在主操作站改变)最后一根短尺经剪后的热金属检测器后经延时被送上冷床。
结束语。