中国全连续棒材轧机的发展和进步20101117
中国轧钢技术的发展现状和展望

中国轧钢技术的发展现状和展望轧钢技术是指通过各种轧制工艺将钢锭、钢坯或钢材加工成所需形状和性能的产品。
作为钢铁工业的重要组成部分,轧钢技术的发展对于提高钢铁产品质量和降低能耗具有重要意义。
本文将介绍中国轧钢技术的发展现状、取得的成果、未来发展方向以及面临的瓶颈问题。
轧钢技术有着悠久的历史,经历了从初期的手动轧制到现代自动化轧制的发展过程。
中国轧钢行业在近几十年来取得了长足的进步,成为世界上最大的钢铁生产和消费国。
不过,与发达国家相比,中国轧钢技术还存在一定的差距,主要表现在工艺技术水平、装备水平和产品性能等方面。
高效轧制技术:中国已成功研发出了一系列高效轧制技术,如控轧控冷技术、连铸坯热装热送技术等,有效提高了轧钢生产效率和产品质量。
特种钢材开发:中国在特种钢材开发方面取得了重要突破,如高速铁路用钢、汽车用高强度钢等,达到了国际先进水平。
自动化智能化技术:随着自动化和智能化技术的发展,中国轧钢行业积极引进和研发相关技术,实现了生产线自动化、智能化控制,提高了产品质量和生产效率。
工艺技术水平较低:与发达国家相比,中国部分轧钢工艺技术水平还比较落后,如精密轧制、高效矫直等技术有待进一步提高。
装备水平不高:中国轧钢装备整体水平还有待提高,部分设备仍存在精度低、稳定性差等问题。
产品性能差距较大:部分轧制产品的性能与国际先进水平存在一定差距,如高强度钢材、高温合金等。
高效化:全球轧钢技术正在向高效化方向发展,通过提高生产效率、降低能耗来降低生产成本。
自动化智能化:随着人工智能、物联网等技术的发展,轧钢生产的自动化和智能化水平将得到进一步提升。
绿色环保:环保成为全球钢铁行业的共同课题,通过采用环保技术和设备来降低轧钢生产过程中的环境污染。
提升工艺技术水平:加大对高效轧制、精密轧制等技术的研发和应用力度,提高轧钢生产效率和产品质量。
优化产业结构:通过淘汰落后产能、推动企业兼并重组等方式,优化轧钢产业结构,提高产业集中度和竞争力。
棒材全连轧工艺优化
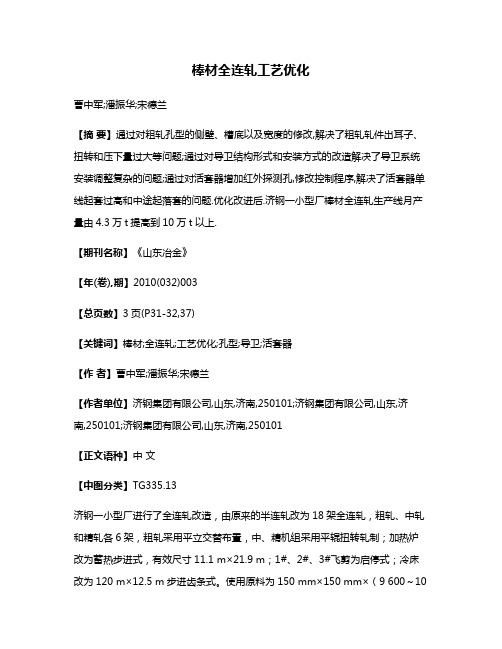
棒材全连轧工艺优化曹中军;潘振华;宋德兰【摘要】通过对粗轧孔型的侧壁、槽底以及宽度的修改,解决了粗轧轧件出耳子、扭转和压下量过大等问题;通过对导卫结构形式和安装方式的改造解决了导卫系统安装调整复杂的问题;通过对活套器增加红外探测孔,修改控制程序,解决了活套器单线起套过高和中途起落套的问题.优化改进后.济钢一小型厂棒材全连轧生产线月产量由4.3万t提高到10万t以上.【期刊名称】《山东冶金》【年(卷),期】2010(032)003【总页数】3页(P31-32,37)【关键词】棒材;全连轧;工艺优化;孔型;导卫;活套器【作者】曹中军;潘振华;宋德兰【作者单位】济钢集团有限公司,山东,济南,250101;济钢集团有限公司,山东,济南,250101;济钢集团有限公司,山东,济南,250101【正文语种】中文【中图分类】TG335.13济钢一小型厂进行了全连轧改造,由原来的半连轧改为18架全连轧,粗轧、中轧和精轧各6架,粗轧采用平立交替布置,中、精机组采用平辊扭转轧制;加热炉改为蓄热步进式,有效尺寸11.1 m×21.9 m;1#、2#、3#飞剪为启停式;冷床改为120 m×12.5 m步进齿条式。
使用原料为150 mm×150 mm×(9 600~10400)mm连铸坯,年设计能力为80万t,2009年年产量为120万t,目前月产10万t以上,最高成品轧机出口速度17.5 m/s。
工艺流程为:坯料→蓄热步进梁式加热炉→6架粗连轧→1#切头剪→6架中连轧→2#切头剪→6架精连轧→倍尺剪切→冷床冷却→定尺剪切→检验→打捆包装→成品入库。
主要产品为Φ12~Φ40 mm螺纹钢,其中Φ14、Φ16、Φ18、Φ20 mm规格采用两切分轧制,Φ12 mm规格采用三切分轧制。
粗轧采用箱—方—箱—方—椭—圆孔型系统,中、精轧采用椭—圆孔型系统。
中轧、精轧之间有30 m距离,是为超级钢轧制准备穿水冷却预留的空间。
中国钢铁轧制技术的进步与发展趋势

中国钢铁轧制技术的进步与发展趋势随着我国经济的快速发展,钢铁材料产量的需求呈现出爆发式增长。
为满足市场需求,钢铁轧制技术也在不断发展和进步。
本文将从技术层面探讨我国钢铁轧制技术的进步与发展趋势。
一、高端钢铁材料的需求趋势我国的钢铁产业从存量革命到优质化引领,经历了快速发展。
当前,我国产量已经达到了全球领先地位。
然而,仍然需要满足更高端的需求,例如重要工程和高端用途的钢铁材料。
这些钢铁材料需要较高的机械性能、化学成分和微观组织,才能满足设计和使用要求。
在这种情况下,提高钢铁材料的热加工技术是至关重要的。
因为钢材的热加工过程会改变其物理性能和微观结构。
例如,精确控制钢材的温度和时间可以影响钢材的硬度、强度、韧性和延展性。
所以,钢铁轧制技术的研究和发展变得尤为重要。
我国的钢铁轧制技术从20世纪初开始逐步完善。
最初,轧制主要依赖于人工劳动和手工车间。
20世纪60年代,我国引进外国轧机和轧制技术,开始实施全面改造和技术革新。
此后,新的轧机、轧制好工艺和工具被引入,使得我国的钢铁轧制产量和质量得到了提高。
目前,我国正处于钢铁产业优化升级的时期。
技术创新和成果转化为我国钢铁产业的发展带来了广阔的空间。
作为最具代表性的热加工工艺,钢铁轧制技术的发展已经成为制约或推动我国钢铁产业进一步发展的关键因素之一。
1. 轧制工艺自动控制和模型预测钢铁轧制工艺自动控制和模型预测是未来发展的应用方向之一。
在轧制过程中,自动控制技术可以实现较高精度的温度和厚度控制,提高轧制效率和质量。
预测模型可以辅助操作员及时调整工艺参数、解决工艺失控问题,并且通过基于数据的思考和分析,推动轧制技术的进步。
2. 智能轧机系统智能轧机系统是未来发展的另一个应用方向,在轧制过程中可以监测并控制轧机参数,提高管控能力和监测效果。
通过大数据和机器学习算法的支撑,这种系统能够对钢铁轧制遇到的各种问题进行预警或自动修复,提升生产工艺的智能化和自动化程度。
3. 信息化和数字化技术信息化和数字化技术可以改变轧制过程中的人工操作和决策过程,提高操作及决策的准确率和精度。
钢铁轧制技术的进步与发展趋势探索

钢铁轧制技术的进步与发展趋势探索摘要:改革开放以来,中国钢铁轧制技术取得了长足的进步。
工业和国民经济的发展,钢材需求量增大,推动了轧钢制造技术的进步与发展。
经过钢铁轧制技术自主创新,中国钢铁轧制技术已经跻身世界先进行列,基本完成了工业化过程。
关键词:钢铁轧制;技术进步;发展趋势近年来,我国钢铁工业在经历了快速发展后,进入了调整结构、转型发展的阶段。
钢铁企业在努力消化引进技术,提高管理与生产操作水平的同时,也在大力进行技术创新,着力开发绿色化、智能化的新技术、新工艺、新装备、新产品,不断增强核心竞争力。
一、中国轧钢技术的发展概况改革开放以来,特别是进入21世纪以来,中国钢铁工业飞跃发展,为中国社会进步和经济腾飞做出了巨大贡献。
作为钢铁工业的关键成材工序,轧钢行业在引进、消化、吸收的基础上,开展集成创新和自主创新,在轧制工艺技术进步、装备和自动化系统研制和引领未来钢铁材料的开发方面实现跨越式发展,为中国钢铁工业的可持续发展做出了突出贡献。
经过改革开放以来的持续发展,中国已经建设了一大批具有国际先进水平的轧钢生产线,比较全面地掌握了国际上最先进的轧制技术,具备了轧钢先进设备的开发、设计、制造能力,一大批国民经济急需、具有国际先进水平的钢材产品源源不断地供应国民经济各个部门,为中国经济与社会发展、人民幸福安康提供了重要的基础原材料。
作为一个发展中的国家,必须尽快掌握世界上的最先进的轧钢技术,引进、消化、吸收是必须的。
改革开放以来,以宝钢建设为契机,中国成套引进了热连轧、薄板坯连铸连轧、冷连轧、中厚板轧制、棒线轧制、长材轧制、钢管轧制等各类轧制工艺技术以及相应的轧制设备和自动化系统,开始了轧制技术的跨越式发展的第一步。
通过引进技术的消化吸收和再创新,中国快速掌握了轧钢领域的前沿工艺技术;通过设备的合作制造以及自主研发,中国掌握了重型轧机的设计、制造、安装的核心技术,逐步具备了自主集成和开发建设先进轧机的能力;利用先进的工艺和装备技术,以及严格科学精细的管理,开发了一大批先进的钢铁材料,满足了经济发展的急需,产品的质量水平不断提高。
中国轧钢技术的历史现状和未来走向
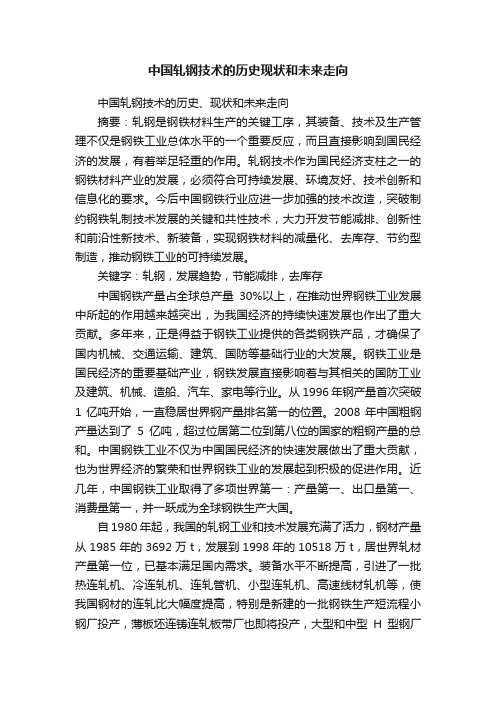
中国轧钢技术的历史现状和未来走向中国轧钢技术的历史、现状和未来走向摘要:轧钢是钢铁材料生产的关键工序,其装备、技术及生产管理不仅是钢铁工业总体水平的一个重要反应,而且直接影响到国民经济的发展,有着举足轻重的作用。
轧钢技术作为国民经济支柱之一的钢铁材料产业的发展,必须符合可持续发展、环境友好、技术创新和信息化的要求。
今后中国钢铁行业应进一步加强的技术改造,突破制约钢铁轧制技术发展的关键和共性技术,大力开发节能减排、创新性和前沿性新技术、新装备,实现钢铁材料的减量化、去库存、节约型制造,推动钢铁工业的可持续发展。
关键字:轧钢,发展趋势,节能减排,去库存中国钢铁产量占全球总产量30%以上,在推动世界钢铁工业发展中所起的作用越来越突出,为我国经济的持续快速发展也作出了重大贡献。
多年来,正是得益于钢铁工业提供的各类钢铁产品,才确保了国内机械、交通运输、建筑、国防等基础行业的大发展。
钢铁工业是国民经济的重要基础产业,钢铁发展直接影响着与其相关的国防工业及建筑、机械、造船、汽车、家电等行业。
从1996年钢产量首次突破1亿吨开始,一直稳居世界钢产量排名第一的位置。
2008年中国粗钢产量达到了5亿吨,超过位居第二位到第八位的国家的粗钢产量的总和。
中国钢铁工业不仅为中国国民经济的快速发展做出了重大贡献,也为世界经济的繁荣和世界钢铁工业的发展起到积极的促进作用。
近几年,中国钢铁工业取得了多项世界第一:产量第一、出口量第一、消费量第一,并一跃成为全球钢铁生产大国。
自1980年起,我国的轧钢工业和技术发展充满了活力,钢材产量从1985年的3692万t,发展到1998年的10518万t,居世界轧材产量第一位,已基本满足国内需求。
装备水平不断提高,引进了一批热连轧机、冷连轧机、连轧管机、小型连轧机、高速线材轧机等,使我国钢材的连轧比大幅度提高,特别是新建的一批钢铁生产短流程小钢厂投产,薄板坯连铸连轧板带厂也即将投产,大型和中型H型钢厂已投入生产,这些都成为我国轧钢生产的主力和样板。
中国轧钢技术的发展现状和展望

中国轧钢技术的发展现状和展望一、发展现状1.技术水平提升2.设备自主研发中国轧钢技术的另一个重要进展是设备的自主研发。
过去,中国的钢铁行业依赖于进口设备,但现在情况已经改变。
近年来,中国钢铁企业大力推动设备的自主创新和研发,不断提高设备制造水平,并逐步减少对进口设备的依赖。
3.品种多样化4.绿色环保在技术发展的同时,中国轧钢技术也在积极推动绿色环保。
钢铁行业是一个高能耗、高排放的行业,但随着环保意识的增强,轧钢企业开始重视减少能源消耗和环境污染。
通过技术创新和改进,轧钢工艺不断优化,减少二氧化碳和废气的排放。
二、展望1.技术创新未来,中国轧钢技术将继续加大技术创新力度,提高技术水平和竞争力。
优化工艺流程、提升设备制造水平、加强智能化改造,将成为技术创新的重点。
同时,应加强与科研机构和高校的合作,加强基础研究,掌握核心技术,推动钢铁行业的创新发展。
2.提高产品品质随着轧钢技术的不断进步,未来的发展将更加注重产品品质的提高。
通过提升工艺与材料的结合性能,探索新型合金材料和加工工艺,以提高产品质量和性能。
同时,加强质量控制和监管,推动中国钢材产业向高质量发展。
3.绿色可持续发展未来,中国轧钢技术将继续积极推动绿色可持续发展。
技术创新将聚焦于节能减排和废弃物利用,通过提高能源利用效率、减少废弃物的生成和加强废弃物处理,实现钢铁行业的绿色转型。
4.国际合作总之,中国轧钢技术在过去几十年取得了长足的进步,但仍然面临着很多挑战。
未来,中国轧钢技术将继续发展,通过技术创新、产品品质提高、绿色可持续发展和国际合作,推动钢铁行业向更高水平发展,为中国经济的可持续发展做出更大贡献。
中国轧钢技术的发展现状和展望

中国轧钢技术的发展现状和展望
中国是全球最大的钢铁生产国,并且钢材产量持续增长。
轧钢技术是钢材生产
主要工艺之一,其发展对于提高钢铁生产效率、质量和节能减排具有重要意义。
当前,中国轧钢技术正朝着高效、智能、绿色的方向发展。
一方面,钢厂开始
采用先进的轧机和轧辊,并配合自动化控制系统和在线质检系统,以提高生产效率和品质;另一方面,环保和节能减排成为越来越重要的问题,钢厂开始采用清洁生产技术和新型炉料,例如废钢和可再生能源。
未来,随着工业4.0和数字化技术的普及,轧钢技术将会更加智能化,例如通
过物联网技术实现设备和生产过程的远程监控、预测性维护等。
同时,绿色和低碳依然是轧钢技术发展的重点,包括采用清洁生产技术、绿色制造和再生资源利用等。
总之,随着技术的不断进步和环保意识的加强,中国轧钢技术的未来发展有望实现高效、智能、绿色、低碳等目标。
中国轧钢技术的进步与展望(中文)通栏

中国轧钢技术的进步与展望张树堂陈其安王国栋周积智刘相华(中国金属学会轧钢学会)摘要在二十世纪最后10年,中国轧钢技术取得了很大进步,主要表现在:先进生产流程的逐步确立;轧钢生产装备、技术的现代化;国产化比例日益增高,新技术得到应用推广;轧钢产品的品种调整已取得初步成效,质量有了较大幅度提高;一些重大开发和研究项目取得了重大进展。
关键词轧钢技术现代化品种调整PROGRESS AND PROSPECT OF STEEL ROLLING TECHNIQUE IN CHINAZhang Shutang Chen Qi’an Wang Guodong Zhou Jizhi(CSM Institute of Metalworking)ABSTRACT In the last 10 years of 20th century, the progress of steel rolling technique in China was obtained and has mainly been observed in following areas: gradual set-up of advanced production route; modernization of steel rolling equipment and technique; increase of domestic manufacturing ratio for new and revamping projects, adoption of new technique; primary result s of rolled product variety adjustment obtained, improvement of product quality; major progress of some R & D projects.KEY WORDS steel rolling technique, modernization, rolled product variety adjustment从1990年到1995年,中国钢铁产量年平均增长率达到了7.2%。
- 1、下载文档前请自行甄别文档内容的完整性,平台不提供额外的编辑、内容补充、找答案等附加服务。
- 2、"仅部分预览"的文档,不可在线预览部分如存在完整性等问题,可反馈申请退款(可完整预览的文档不适用该条件!)。
- 3、如文档侵犯您的权益,请联系客服反馈,我们会尽快为您处理(人工客服工作时间:9:00-18:30)。
中国全连续棒材轧机的发展和进步
地域:国内信息类别:行业动态行业类别:冶金装备制造
作者:发布人:钢铁行业管理审核发布时间:2010-11-17 09:10:40.0
1、概述
我国第一台全连续棒材轧机是1961年在首都钢铁公司建成的Φ300mm小型轧机,全套设备由前苏联引进。
原设计年产能力为30万t,后经多次技术改造和改进操作,实际年产能力达到82万t。
改革开放以后,在80年代大多引进国外二手全连续棒材轧机,如1988年原上钢一厂引进了德国全连续棒材轧机,此后,沙钢、涟源、承德、大连、无锡、陕西等厂均引进了国外二手全连续棒材轧机。
从90年代开始,我国开始引进和合作制造当时最先进的全连续棒材轧机。
这有两类情况:一种是全线引进国外设备,如1996年唐山钢铁公司从意大利达涅利公司全线引进的轧机,投产最大终轧速度达18m/s,设计年产能力为60万t,共设18台机架。
随后韶关钢铁公司、淮阴钢铁公司、广州钢铁公司等也引进了达涅利或Pomili公司的全连续棒材轧机。
另一类是合作制造,由国内公司技术总负责,部分引进国外设备。
到90年代后期国内设计制造的全连续棒材轧机(少量引进)也陆续建成投产,并出口国外,如向阿曼提供30万t/a全连续棒材轧机,向莫桑比克提供40万t/a棒材轧机,最近又和巴西签订出口两套长材轧机合同。
我国2009年生产棒材5565.4万t,钢筋12150.55万t,合计约17716万t,除了全连续棒材轧机生产了相当多部分外,其中一部分系由半连续棒材轧机生产的。
经过多年努力,我国已建成或正在建设的全连续棒材轧机有100台以上,是世界上拥有该类轧机最多的国家,并且有以下进展:
1)生产率大幅提高。
过去一套棒材生产线年产能力约30万t~50万t,现在提高到80万t~100万t;
2)品种显著增加。
过去一般生产规格为Φ10mm~35mm,现可生产规格Φ10mm~60mm,并且可生产直径为Φ50mm
大盘卷;
此外,为生产特殊钢大直径棒材,兴澄特钢和首钢宝业均先后建设了大规格棒材轧机(Φ80mm~300mm),由于年产能力不需过大(已达80万t~100万t/a),故建成半连续轧机,包括1架可逆式粗轧机和6架精轧机;
3)由于增加减定径设备,产品精度显著增加,一般均可达到德国DIN标准允许公差的1/4;
4)由于采用了多项先进技术,燃料、金属消耗显著降低,有害气体排放减少,成本降低。
2、全连续棒材轧机的技术进步
2.1全连续无扭高速轧制
我国新建现代化棒材轧机全部采用15~20架轧机连续轧制,为避免轧制过程扭曲,粗、中、精轧均采用平、立交替布置,精轧机终轧速度有很大提高,一般均在18m/s以上,个别工厂如包头钢铁公司于2007年投产的棒材轧机最大终轧速度达35m/s。
全连续无扭高速轧制带来的好处,一是生产率有很大提高,年产能力达60万t~80万t,少数轧机如首钢宝业集团由达涅利公司引进的棒材轧机,沙钢新建No.3棒材轧机年产能力均为100万t/a;二是无扭轧制、提高了产品质量;三是免去往复轧制,来回输送,减少温度损失,节约能耗;四是连续轧制,有利于控温控轧,实行TMCP工艺。
2.2新型蓄热式加热炉
采用新型蓄热式加热炉的优点:一是可利用低热值煤气如纯高炉煤气;二是预热温度高,空气预热温度可达1000℃,煤气也可进行预热,排烟温度可低于150℃,热效率可达到70%以上,节能效果达20%~30%,从而也减少CO2和NO2的排放量;三是提高加热炉生产率,炉底应力由以往的500kg/m2?h~600kg/m2?h提高到850kg/m2?h~900
kg/m2?h,提高产量15%~20%。
我国新建全连续棒材轧机在有低热值煤气如高炉煤气可提供作为燃料时一般均采用此项技术。
2.3热装热送技术
合格连铸坯通过热装辊道,直接进入加热炉进行加热和均热,热装温度可达600℃以上,其效益非常明显。
(1)钢坯入炉温度每提高100℃,可降低燃耗6%左右。
(2)提高生产率。
加热炉较冷装料时可提高10%左右。
(3)减少烧损量、提高成材率。
500℃热装可降低烧损量0.5%~1.0%。
2.4增加减、定径设备
在新建全连续棒材轧机时(特别是合金钢棒材轧机)多增加减定径设备,如江阴兴澄特钢于2006年夏投产的棒材轧机即有5道次Kocks/Danieli减定径机;大冶特钢公司于2005年投产的棒材轧机也从达涅利公司引进减定径机组,华菱集团湘潭钢铁公司2006年投产的棒材轧机从Kocks公司引进Φ370mm三辊五机架减定径机。
海南光原公司、宁夏电投钢铁公司、大连钢厂、河南济源公司、邯郸钢铁公司等都设有减定径机,对提高产品精度、解决棒材轧制过程中温度控制问题都有明显的效果。
设置减定径机架数各厂有所不同,优质钢棒材轧机大多设置5架,也有设置4架的。
2.5 TMCP技术
TMCP技术的原理是通过控制轧制温度和轧制后冷却速度、冷却的开始温度和终止温度,最终控制钢材的组织类型、形态和分布来提高钢材的力学性能,通过TMCP利用钢材余热可替代正火,淬火-回火(回火需离线)处理,改善钢材的力学性能,减少热处理消耗。
为实现该工艺,需要采用高刚度大功率的轧机以及高效的快速冷却系统和相关的控制数学模型。
具备超细晶粒钢生产能力的棒材TMCP生产线所生产的钢材强度高,可节约合金资源。
与一般工艺生产出来的钢筋相比,可大量节约钢材,对资源利用、环境保护都十分有益。
如抚顺新抚钢80万t/a棒材轧机采用TMCP工艺以20MnSi 钢批量生产出400MPa、500MPa级高强度钢筋,以Q235成功生产出355MPa、400MPa级高强度钢筋。
20MnSi钢、Q235钢生产超细晶粒钢筋(HRB400)代替强度低的HRB335(20MnSi钢)可节约钢材约14%以上。
2.6低温轧制
将开轧温度控制在950℃左右,在选择轧机机架钢度和主电机容量时均适应此要求,以达到总体节能和减少金属烧损的效果。
2.7切分轧制
对小规格棒材进行切分轧制可以提高轧机生产率,并可使生产大、小规格时产量差别不大,以利于协调生产,增加加热炉等设备利用率,沙钢三棒材轧机(2006年投产)生产Φ14mm以下棒材时进行四切分轧制,Φ16mm、Φ18mm
信息来源:北京钢铁设计研究总院相关连接关键字:。