基于PLC的锅炉燃烧控制系统
基于PLC单片机控制中小型蒸汽锅炉智能燃烧系统

产。
4
3、锅炉引风控制
炉膛负压控制系统一般采用的控制流程图 如下图所示,调节原理比较简单属于单闭 环调节系统,它的输入量是炉膛负压输出 量是引风变频器,同时引入鼓风量作为前 馈信号。
给定蒸汽压力
+ -
引风调节单元
引风机变频器
锅炉系统
抗干扰滤波
炉膛负压信号
5
4、锅炉鼓风控制
鼓风控制系统一般采用的控制流程图如下图所示,
先通过蒸汽压力变送器经滤波后取得信号,与设 定蒸汽压力进行比较,判断出鼓风PID调节器调节 的方向和大小,通过鼓风PID调节单元计算出鼓风 变频器的输出大小
给定蒸汽压力
+ -
炉排调节单元
风煤比
炉排变频器
鼓风调节单元 抗干扰滤波
鼓风变频器 蒸汽压力信号
炉排系统
6
二、控制系统硬件设计
PLC不仅具有逻辑控制功能,而且还具有了 运算、数据处理和数据传送等功能 ,采用可编 程控制器设计的控制系统可以实现对锅炉精确地 实时自动控制,并且实现了整个系统的优化控制。 变频调速的基本原理是通过改变电动机工作电源 频率达到改变电机转速的目的,采用变频调速技 术来控制锅炉的泵与风机,可以使电动机不必总 在工频下运行,可以大大的节省电能。
2、程序设计结果,见论文P35~P37
13
四、上位机系统制作
MCGS (Monitor and Control Generated System, 通用监控系统)是一套用于快速构造和生成计算机 监控系统的组态软件,它能够在基于Microsoft (各种 32 位 Windows 平台上)运行,通过对现 场数据的采集处理,以动画显示、报警处理、流 程控制、实时曲线、历史曲线和报表输出等多种 方式向用户提供解决实际工程问题的方案,它充 分利用了 Windows图形功能完备、界面一致性好、 易学易用的特点,在自动化领域有着广泛的应用。
基于PLC的燃油锅炉控制系统设计讲解

基于PLC的燃油锅炉控制系统设计摘要目前燃油锅炉的应用越来越广泛,对燃油锅炉的科学研究也越来越多。
为解决我国燃油锅炉产业现状存在的主要问题,采用PLC等控制技术和设备对我国燃油锅炉控制系统进行适当改造。
FX2N系列PLC改造的燃油锅炉控制系统,根据自动控制基本原理实现了锅炉更高效率和更高可靠性的启动、停止、暂停和异常处理;在此控制系统中对锅炉燃烧各项参数等可进行高效检测、校正和调节;其中锅炉水位、压力等参数控制亦可由PLC实现控制。
首先是对燃油锅炉基本结构组成和运行原理进行研究和分析;主要研究WNS型卧式燃油锅炉,根据燃油锅炉控制系统的工艺要求设计控制方案;设置好具体参数,进行PLC的I/O口的估算和分配,选择三菱FX2N系列PLC作为控制系统核心,在此基础上设计出控制系统外部接线图,并对其它组成部件如变频器、电机等进行选择;最后根据系统流程图进行主电路接线图的设计,完成梯形图,最后进行程序的校验和仿真。
关键词:PLC, 燃油锅炉, 汽包水位Design of the boiler burner control system based on plcAbstractThe application of fuel boiler is more and more extensive, scientific study of the oil-fired boiler is also more and more. In order to solve the current problems of fuel boiler industry in China, using PLC control technology and equipment appropriate modification of control system of fuel boiler in china. Fuel boiler control system of FX2N series PLC transformation, according to the basic principle of the automatic control of boiler high efficiency and high reliability of the start, stop, pause and exception handling; the boiler combustion parameters can effectively detect, correction and adjustment in the control system of boiler water level; wherein, parameters such as pressure control can realize control by PLC.The first is the research and Analysis on the basic structure of fuel boiler components and operating principle; the main research WNS horizontal oil-fired boiler, according to the process control system of fuel boiler design requirements of control scheme; set up specific parameters, estimation and allocation of PLC I/O port, select the Mitsubishi FX2N series PLC as the core of control system, based on the control system design of external wiring diagram, and other components such as the inverter, motor selection; finally, according to the design of main circuit wiring diagram for the system flow chart, complete ladder diagram, verification and simulation step procedure.Key words:PLC, fuel boiler, the drum water level目录第一章绪论 (1)1.1 课题研究的背景及意义 (1)1.2国内外研究现状 (1)1.3本设计研究的意图 (2)1.4 本文所做工作 (2)第二章锅炉燃烧的分析 (3)2.1 燃油锅炉的基本组成部分 (3)2.2 锅炉系统的结构 (3)2.3燃油锅炉的工作过程 (4)2.4设计方法 (5)第三章锅炉燃烧控制系统的设计 (6)3.1 燃油锅炉系统控制要求 (6)3.2 燃烧过程、水位高低控制 (6)3.3 燃油锅炉系统工艺流程 (7)3.4 确定燃油锅炉的设计方案 (7)3.5 工艺参数控制 (8)3.6 总体设计思路 (9)第四章硬件选择及设计 (11)4.1 PLC控制系统的设计步骤 (11)4.2 PLC机型的选择 (12)4.2.1 PLC容量估算 (13)4.2.2 其它器件的选型 (14)4.2.3系统的I/O接口以及硬件接线图 (14)4.3锅炉水位控制图 (17)4.4系统主电路接线图 (18)4.5电机及驱动控制选型 (19)4.5.1 电机及喷油泵的选型 (19)4.5.2 变频器选型 (19)4.5.3 检测元件选型 (19)第五章系统软件设计 (20)5.1 系统流程图 (20)5.2系统控制的梯形图 (21)5.2.1起动 (21)5.2.2 停止 (21)5.2.3 异常自动关火 (22)5.2.4锅炉水位控制 (22)5.3 系统总梯形图 (23)5.3.1系统运行控制 (23)5.3.2系统水位运行控制 (25)第六章结论 (29)6.1 成果评价 (29)6.2 作用意义 (29)6.3 应用范围和前景 (29)6.4 需要进一步改进之处 (29)参考文献 (30)谢辞 ................................................................................................... 错误!未定义书签。
基于PLC的锅炉燃烧控制系统设计_毕业设计论文正文

基于PLC的锅炉燃烧控制系统设计1 绪论1.1锅炉燃烧控制项目的背景改革开放以来,我国经济社会快速发展,生产力水平不断提高,在生产中,锅炉起着十分重要的作用,尤其是在火力发电中发挥重要作用的工业锅炉,是提供能源动力的主要设备之一。
锅炉产生的蒸汽可以作为蒸馏,干燥,反应,加热等各过程的热源,另外也可以作为动力源驱动动力设备。
工业过程中对于锅炉燃烧控制系统的要求是非常高的,要求锅炉燃烧控制系统必须满足控制精度高,响应速度快[1]。
作为一个非常复杂的设备,锅炉同时具有了数十个包括了扰动、测量、控制在内的参数,参数之间有着复杂的关系,并且相互关联[2]。
而锅炉燃烧过程中的效率问题、安全问题一直是大众关注的重要方面。
1.2锅炉燃烧控制的发展历史对于锅炉燃烧的控制,已经经历了四个阶段[3~5](1)手动控制阶段因为20世纪60年代以前,电力电子技术和自动化技术还没有得到完全发展,技术尚不成熟,因此,这个时期工业人员的自动化意识不强,锅炉燃烧的控制方式一般多采用纯手动的方法。
这种控制方法,要求进行控制的操作工人依靠他们的经验决定送风量,引风量,给煤量的多少,然后利用手动的操作工具等操控锅炉,该方法控制的程度完全取决于操作工人的经验。
因此,要求操作工人必须具有非常丰富的经验,这样无疑大大提高了操作工人的劳动强度,由十人的主观意识,所以事故率非常大,同时,也不能保证锅炉高效稳定的运行。
(2)仪器继电器控制阶段随着科技的不断进步,自动化技术以及电力电子技术快速提高,国内外以继电器为基础的自动化仪表工业锅炉控制系统也得到发展,并且广泛应用于实际生产过程。
在上个世纪60年代前期,我国锅炉的控制系统开始得到迅速发展;到了60年代的中后期,我国引进了国外全自动的燃油锅炉的控制系统;到了上个世纪的70年代末,我国逐渐自主研发了一些工业锅炉的自动化仪器,同时,在工业锅炉的控制系统方面也在逐步推广应用自动化技术。
在仪表继电器控制阶段,锅炉的热效率得到了提高,并且大幅度的降低了锅炉的事故率。
基于PLC的锅炉燃烧控制系统设计
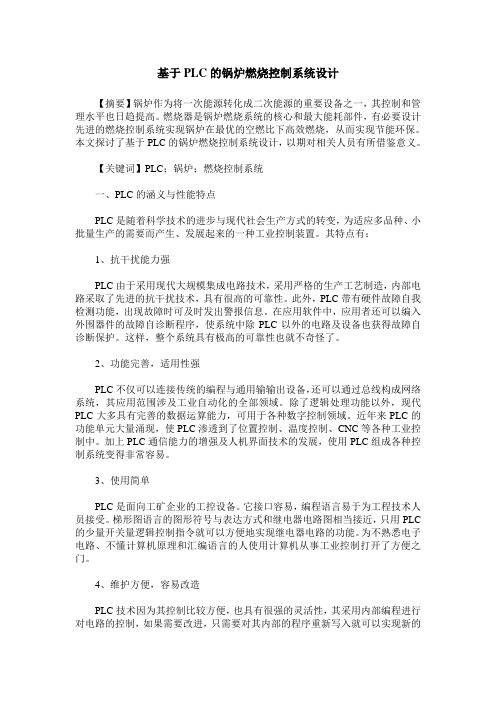
基于PLC的锅炉燃烧控制系统设计【摘要】锅炉作为将一次能源转化成二次能源的重要设备之一,其控制和管理水平也日趋提高。
燃烧器是锅炉燃烧系统的核心和最大能耗部件,有必要设计先进的燃烧控制系统实现锅炉在最优的空燃比下高效燃烧,从而实现节能环保。
本文探讨了基于PLC的锅炉燃烧控制系统设计,以期对相关人员有所借鉴意义。
【关键词】PLC;锅炉;燃烧控制系统一、PLC的涵义与性能特点PLC是随着科学技术的进步与现代社会生产方式的转变,为适应多品种、小批量生产的需要而产生、发展起来的一种工业控制装置。
其特点有:1、抗干扰能力强PLC由于采用现代大规模集成电路技术,采用严格的生产工艺制造,内部电路采取了先进的抗干扰技术,具有很高的可靠性。
此外,PLC带有硬件故障自我检测功能,出现故障时可及时发出警报信息。
在应用软件中,应用者还可以编入外围器件的故障自诊断程序,使系统中除PLC以外的电路及设备也获得故障自诊断保护。
这样,整个系统具有极高的可靠性也就不奇怪了。
2、功能完善,适用性强PLC不仅可以连接传统的编程与通用输输出设备,还可以通过总线构成网络系统,其应用范围涉及工业自动化的全部领域。
除了逻辑处理功能以外,现代PLC大多具有完善的数据运算能力,可用于各种数字控制领域。
近年来PLC的功能单元大量涌现,使PLC渗透到了位置控制、温度控制、CNC等各种工业控制中。
加上PLC通信能力的增强及人机界面技术的发展,使用PLC组成各种控制系统变得非常容易。
3、使用简单PLC是面向工矿企业的工控设备。
它接口容易,编程语言易于为工程技术人员接受。
梯形图语言的图形符号与表达方式和继电器电路图相当接近,只用PLC 的少量开关量逻辑控制指令就可以方便地实现继电器电路的功能。
为不熟悉电子电路、不懂计算机原理和汇编语言的人使用计算机从事工业控制打开了方便之门。
4、维护方便,容易改造PLC技术因为其控制比较方便,也具有很强的灵活性,其采用内部编程进行对电路的控制,如果需要改进,只需要对其内部的程序重新写入就可以实现新的控制要求。
基于plc的锅炉控制系统的设计方案
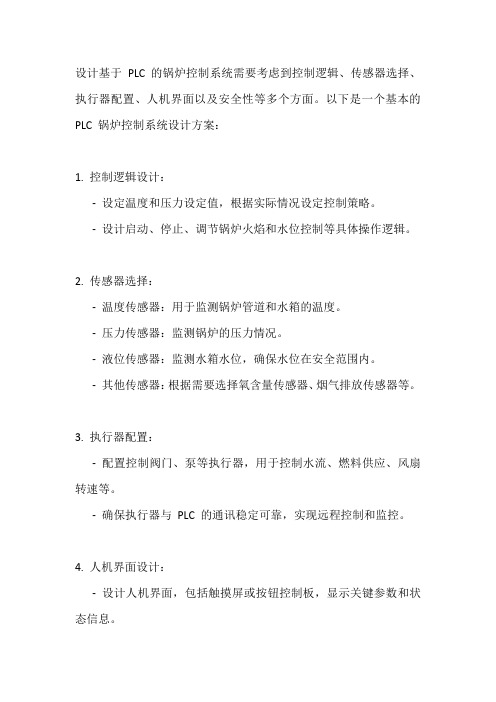
设计基于PLC 的锅炉控制系统需要考虑到控制逻辑、传感器选择、执行器配置、人机界面以及安全性等多个方面。
以下是一个基本的PLC 锅炉控制系统设计方案:1. 控制逻辑设计:-设定温度和压力设定值,根据实际情况设定控制策略。
-设计启动、停止、调节锅炉火焰和水位控制等具体操作逻辑。
2. 传感器选择:-温度传感器:用于监测锅炉管道和水箱的温度。
-压力传感器:监测锅炉的压力情况。
-液位传感器:监测水箱水位,确保水位在安全范围内。
-其他传感器:根据需要选择氧含量传感器、烟气排放传感器等。
3. 执行器配置:-配置控制阀门、泵等执行器,用于控制水流、燃料供应、风扇转速等。
-确保执行器与PLC 的通讯稳定可靠,实现远程控制和监控。
4. 人机界面设计:-设计人机界面,包括触摸屏或按钮控制板,显示关键参数和状态信息。
-提供操作界面,方便操作员设定参数、监控运行状态和进行故障诊断。
5. 安全性设计:-设计安全保护系统,包括过压保护、过温保护、水位保护等,确保锅炉运行安全。
-设置报警系统,当参数超出设定范围时及时警示操作员。
6. 通讯接口:-考虑与其他系统的通讯接口,如SCADA 系统、远程监控系统等,实现数据传输和远程控制。
7. 程序设计:-使用PLC 编程软件编写程序,包括控制逻辑、报警逻辑、自诊断等功能。
-测试程序逻辑,确保系统稳定可靠,符合设计要求。
以上是基于PLC 的锅炉控制系统设计方案的基本步骤,具体设计还需根据实际情况和需求进行调整和优化。
在设计过程中,还需遵循相关标准和规范,确保系统安全可靠、运行稳定。
基于PLC的锅炉供热控制系统的设计

基于PLC的锅炉供热控制系统的设计一、本文概述随着科技的不断发展,可编程逻辑控制器(PLC)在工业自动化领域的应用日益广泛。
作为一种高效、可靠的工业控制设备,PLC以其强大的编程能力和灵活的扩展性,成为现代工业控制系统的重要组成部分。
本文旨在探讨基于PLC的锅炉供热控制系统的设计,通过对锅炉供热系统的分析,结合PLC控制技术,实现对供热系统的智能化、自动化控制,提高供热效率,降低能耗,为工业生产和居民生活提供稳定、可靠的热源。
文章首先介绍了锅炉供热系统的基本构成和工作原理,分析了传统供热系统存在的问题和不足。
然后,详细阐述了PLC控制系统的基本原理和核心功能,包括输入/输出模块、中央处理单元、编程软件等。
在此基础上,文章提出了基于PLC的锅炉供热控制系统的总体设计方案,包括系统硬件选型、软件编程、系统调试等方面。
通过本文的研究,期望能够实现对锅炉供热控制系统的优化设计,提高供热系统的控制精度和稳定性,降低运行成本,促进节能减排,为工业生产和居民生活提供更加安全、高效的供热服务。
也为相关领域的研究人员和技术人员提供有价值的参考和借鉴。
二、锅炉供热系统基础知识锅炉供热系统是一种广泛应用的热能供应系统,其主要任务是将水或其他介质加热到一定的温度,然后通过管道系统输送到各个用户端,满足各种热需求,如工业生产、居民供暖等。
该系统主要由锅炉本体、燃烧器、热交换器、控制系统和辅助设备等几部分构成。
锅炉本体是供热系统的核心设备,负责将水或其他介质加热到预定温度。
其根据燃料类型可分为燃煤锅炉、燃油锅炉、燃气锅炉、电锅炉等。
锅炉的性能参数主要包括蒸发量、蒸汽压力、蒸汽温度等。
燃烧器是锅炉的重要组成部分,负责燃料的燃烧过程。
燃烧器的性能直接影响到锅炉的热效率和污染物排放。
燃烧器需要稳定、高效、低污染,同时要适应不同的燃料类型和负荷变化。
热交换器是锅炉供热系统中的关键设备,负责将锅炉产生的热能传递给水或其他介质。
热交换器的设计应保证高效、稳定、安全,同时要考虑到热能的充分利用和防止结垢、腐蚀等问题。
基于PLC的锅炉控制系统
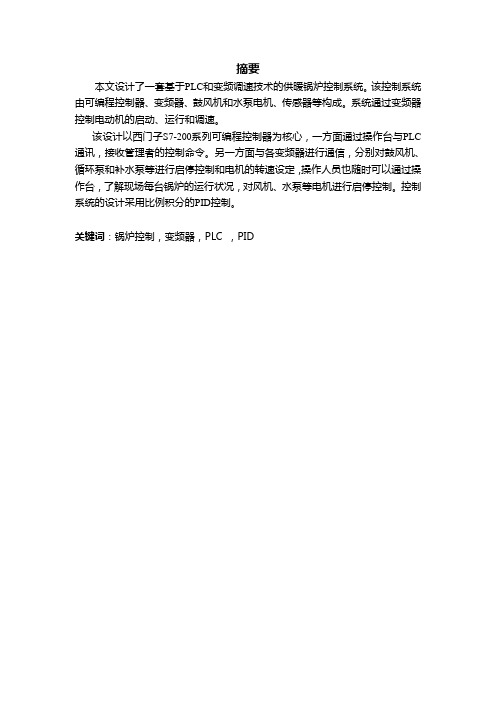
摘要本文设计了一套基于PLC和变频调速技术的供暖锅炉控制系统。
该控制系统由可编程控制器、变频器、鼓风机和水泵电机、传感器等构成。
系统通过变频器控制电动机的启动、运行和调速。
该设计以西门子S7-200系列可编程控制器为核心,一方面通过操作台与PLC 通讯,接收管理者的控制命令。
另一方面与各变频器进行通信,分别对鼓风机、循环泵和补水泵等进行启停控制和电机的转速设定,操作人员也随时可以通过操作台,了解现场每台锅炉的运行状况,对风机、水泵等电机进行启停控制。
控制系统的设计采用比例积分的PID控制。
关键词:锅炉控制,变频器,PLC ,PIDThe design of heating boiler auto control reformation system basedon PLC technologyAbstractIn this Paper,a heating boiler control system based on PLC and variable frequency Speed-regulating technology is designed. The control system is made up of PLC,transducers,electromotor units of Pumps and fans, sensors, etc. It can control electromotor starting,running and timing by means of transducers.The design is based on Siemens S7-200 series programmable controller as the core; on the one hand through the console it can communicate with the PLC, to receive control commands from managers. On the other hand it communicate with the variable frequency Speed-regulating, to fulfilled such as starting and stopping pump motor control and speed settings, the operator at console can find out at the scene of the operation of each boiler to fans, pumps and other motor control to start and stop. at any time.Key words:boiler control, variable frequency Speed-regulating, PLC technology目录1 绪论 (2)2 供暖锅炉改造设计思路 (2)2.1 供暖锅炉改造设计要求 (2)2.2 锅炉系统的结构 (3)2.3 整体方案选择 (3)3 变频调速在供暖锅炉控制中的应用 (4)3.1 变频调速基本原理 (4)3.2 变频调速在供暖锅炉系统中的应用 (5)4 锅炉控制系统总体设计 (5)4.1系统功能分析 (5)4.2 总体设计思路 (6)4.3 系统结构 (6)5 系统硬件设计 (7)5.1 可编程控制器PLC的选型 (7)5.2 PLC配置 (8)5.3 I/O接线 (9)5.4 变频器配置 (9)5.5 传感器与变送器 (11)5.5.1 压力变送器工作原理 (11)5.5.2 压力变送器选型 (11)5.5.3 温度传感器选型 (11)6 系统构成 (13)6.1 补水泵控制系统 (13)6.2 循环泵控制系统 (15)6.3 燃烧控制系统 (16)7 PID控制原理 (17)8 程序设计 (20)8.1 主程序设计 (16)8.2 子程序设计 (16)9 结束语 (26)致谢 (28)参考文献 (28)1 绪论锅炉是供热设备中最普遍的动力设备之一,它的功能是把燃料中的贮能,通过燃烧转化成热能,以蒸汽或热水的形式输向各种设备。
基于PLC的锅炉燃烧控制系统毕业设计正文

基于PLC的锅炉燃烧控制系统设计1 绪论1.1锅炉燃烧控制项目的背景改革开放以来,我国经济社会快速发展,生产力水平不断提高,在生产中,锅炉起着十分重要的作用,尤其是在火力发电中发挥重要作用的工业锅炉,是提供能源动力的主要设备之一。
锅炉产生的蒸汽可以作为蒸馏,干燥,反应,加热等各过程的热源,另外也可以作为动力源驱动动力设备。
工业过程中对于锅炉燃烧控制系统的要非常高的,要求锅炉燃烧控制系统必须满足控制精度高,响应速度快[1]。
作为一个非常复杂的设备,锅炉同时具有了数十个包括了扰动、测量、控制在的参数,参数之间有着复杂的关系,并且相互关联[2]。
而锅炉燃烧过程中的效率问题、安全问题一直是大众关注的重要方面。
1.2锅炉燃烧控制的发展历史对于锅炉燃烧的控制,已经经历了四个阶段[3~5](1)手动控制阶段因为20世纪60年代以前,电力电子技术和自动化技术还没有得到完全发展,技术尚不成熟,因此,这个时期工业人员的自动化意识不强,锅炉燃烧的控制方式一般多采用纯手动的方法。
这种控制方法,要求进行控制的操作工人依靠他们的经验决定送风量,引风量,给煤量的多少,然后利用手动的操作工具等操控锅炉,该方法控制的程度完全取决于操作工人的经验。
因此,要求操作工人必须具有非常丰富的经验,这样无疑大大提高了操作工人的劳动强度,由十人的主观意识,所以事故率非常大,同时,也不能保证锅炉高效稳定的运行。
(2)仪器继电器控制阶段随着科技的不断进步,自动化技术以及电力电子技术快速提高,国外以继电器为基础的自动化仪表工业锅炉控制系统也得到发展,并且广泛应用于实际生产过程。
在上个世纪60年代前期,我国锅炉的控制系统开始得到迅速发展;到了60年代的中后期,我国引进了国外全自动的燃油锅炉的控制系统;到了上个世纪的70年代末,我国逐渐自主研发了一些工业锅炉的自动化仪器,同时,在工业锅炉的控制系统方面也在逐步推广应用自动化技术。
在仪表继电器控制阶段,锅炉的热效率得到了提高,并且大幅度的降低了锅炉的事故率。
- 1、下载文档前请自行甄别文档内容的完整性,平台不提供额外的编辑、内容补充、找答案等附加服务。
- 2、"仅部分预览"的文档,不可在线预览部分如存在完整性等问题,可反馈申请退款(可完整预览的文档不适用该条件!)。
- 3、如文档侵犯您的权益,请联系客服反馈,我们会尽快为您处理(人工客服工作时间:9:00-18:30)。
基于PLC的锅炉燃烧控制系统
1、引言
燃烧控制系统是电厂锅炉的主控系统,主要包括燃料控制系统、风量控制系统、炉膛压力控制系统。
目前大部分电厂的锅炉燃烧控制系统仍然采用PID控制。
燃烧控制系统由主蒸汽压力控制和燃烧率控制组成串级控制系统,其中燃烧率控制由燃料量控制、送风量控制、引风量控制构成,各个子控制系统分别通过不同的测量、控制手段来保证经济燃烧和安全燃烧。
如图1所示。
图1 燃烧控制系统结构图
2、控制方案
锅炉燃烧自动控制系统的基本任务是使燃料燃烧所提供的热量适应外界对锅炉输出的蒸汽负荷的要求,同时还要保证锅炉安全经济运行。
一台锅炉的燃料量、送风量和引风量三者的控制任务是不可分开的,可以用三个控制器控制这三个控制变量,但彼此之间应互相
协调,才能可靠工作。
对给定出水温度的情况,则需要调节鼓风量与给煤量的比例,使锅炉运行在最佳燃烧状态。
同时应使炉膛内存在一定的负压,以维持锅炉热效率、避免炉膛过热向外喷火,保证了人员的安全和环境卫生。
2.1 控制系统总体框架设计
燃烧过程自动控制系统的方案,与锅炉设备的类型、运行方式及控制要求有关,对不同的情况与要求,控制系统的设计方案不一样。
将单元机组燃烧过程被控对象看作是一个多变量系统,设计控制系统时,充分考虑工程实际问题,既保证符合运行人员的操作习惯,又要最大限度的实施燃烧优化控制。
控制系统的总体框架如图2所示。
图2 单元机组燃烧过程控制原理图
P为机组负荷热量信号为D+dPbdt。
控制系统包括:滑压运行主汽压力设定值计算模块(由热力系统实验获得数据,再拟合成可用DCS折线功能块实现的曲线)、负荷—送风量模糊计算模块、主蒸汽压力控制系统和送、引风控制系统等。
主蒸汽压力控制系统采用常规串级PID控制结构。
2.2 燃料量控制系统
当外界对锅炉蒸汽负荷的要求变化时,必须相应的改变锅炉燃烧的燃料量。
燃料量控制是锅炉控制中最基本也是最主要的一个系统。
因为给煤量的多少既影响主汽压力,也影响送、引风量的控制,还影响到汽包中蒸汽蒸发量及汽温等参数,所以燃料量控制对锅炉运行有重大影响。
燃料控制可用图3简单表示。
图3 燃料量控制策略
其中:NB为锅炉负荷要求;B为燃料量;F(x)为执行机构。
设置燃料量控制子系统的目的之一就是利用它来消除燃料侧内部的自发扰动,改善系统的调节品质。
另外,由于大型机组容量大,各部分之间联系密切,相互影响不可忽略。
特别是燃料品种的变化、投入的燃料供给装置的台数不同等因素都会给控制系统带来影响。
燃料量控制子系统的设置也为解决这些问题提供了手段。
2.3 送风量控制系统
为了实现经济燃烧,当燃料量改变时,必须相应的改变送风量,使送风量与燃料量相适应。
燃料量与送风量的关系见图4。
图4 燃料量与送风量关系
燃烧过程的经济与否可以通过剩余空气系数是否合适来衡量,过剩空气系数通常用烟气的含氧量来间接表示。
实现经济燃烧最基本的方法是使风量与燃料量成一定的比例。
送风量控制子系统的任务就是使锅炉的送风量与燃料量相协调,可以达到锅炉的最高热效率,保证机组的经济性,但由于锅炉的热效率不能直接测量,故通常通过一些间接的方法来达到目的。
如图5所示,以实测的燃料量B作为送风量调节器的给定值,使送风量V 和燃料量B成一定的比例。
图5 燃料量空气调节系统
在稳态时,系统可保证燃料量和送风量间满足
选择使送风量略大于B完全燃烧所需要的理论空气量。
这个系统的优点是实现简单,可以消除来自负荷侧和燃料侧的各种扰动。
2.4 引风量控制系统
为了保持炉膛压力在要求的范围内,引风量必须与送风量相适应。
炉膛压力的高低也关系着锅炉的安全和经济运行。
炉膛压力过低会使大量的冷风漏入炉膛,将会增大引风机的负荷和排烟损失,炉膛压力太低甚至会引起内爆;反之炉膛压力高且高出大气压力的时候,会使火焰和烟气冒出,不仅影响环境卫生,甚至可能影响设备和人生安全。
引风量控制子系统的任务是保证一定的炉膛负压力,且炉膛负压必须控制在允许范围内,一般在-20Pa左右。
控制炉膛负压的手段是调节引风机的引风量,其主要的外部扰动是送风量。
作为调节对象,炉膛烟道的惯性很小,无论在内扰和外扰下,都近似一个比例环节。
一般采用单回路调节系统并加以前馈的方法进行控制,如图6所示。
图6 引风量控制子系统
图中为炉膛负压给定值,S为实测的炉膛负压,Q为引风量,V为送风量。
由于炉膛负压实际上决定于送风量和引风量的平衡,故利用送风量作为前馈信号,以改善系统的调节性能。
另外,由于调节对象相当于一个比例环节,被调量反应过于灵敏,为了防止小幅度偏差引起引风机挡板的频繁动作,可设置调节器的比例带自动修正环节,使得在小偏差时增大调节器的比例带。
对于负压S的测量信号,也需进行低通滤波,以抑制测量值的剧烈波动。
3、系统硬件配置
在锅炉燃烧过程中,用常规仪表进行控制,存在滞后、间歇调节、烟气中氧含量超过给定值、低负荷和烟气温度过低等问题。
采用PLC对锅炉进行控制时,由于它的运算速度快、精度高、准确可靠,可适应复杂的、难于处理的控制系统。
因而,可以解决以上由常规仪表控制难以解决的问题。
所选择的PLC系统要求具有较强的兼容性,可用最小的投资使系统建成及运转;其次,当设计的自动化系统要有所改变时,不需要重新编程,对输入、输出系统不需要再重新接线,不须重新培训人员,就可使PLC系统升级;最后,系统性能较高。
硬件结构图如图7所示。
图7 硬件结构图
根据系统的要求,选取西门子PLCS7-200 CPU226 作为控制核心,同时还扩展了2个EM231模拟量输入模块和1个CP243-1以太网模块。
CPU226的IO点数是2416,这样完全可以满足系统的要求。
同时,选用了EM231模块,它是AD转换模块,具有4个模拟量输入,12位AD,其采样速度25μs,温度传感器、压力传感器、流量传感器以及含氧检测传感器的
输出信号经过调理和放大处理后,成为0~5V的标准信号,EM231模块自动完成AD转换。
S7-200的PPI接口的物理特性为RS-485,可在PPI、MPI和自由通讯口方式下工作。
为实现PLC与上位机的通讯提供了多种选择。
为实现人机对话功能,如系统状态以及变量图形显示、参数修改等,还扩展了一块Eview500系列的触摸显示屏,操作控制简单、方便,可用于设置系统参数,显示锅炉温度等。
还有一个以太网模块CP243-1,其作用是可以让S7-200直接连入以太网,通过以太网进行远距离交换数据,与其他的S7-200进行数据传输,通信基于TCPIP,安装方便、简单。
4、系统软件设计
控制程序采用STEP7-MicroWin软件以梯形图方式编写,其软件框图如图8所示。
图8 软件主框图
S7-200PLC给出了一条PID指令,这样省去了复杂的PID算法编程过程,大大方便了用户的使用。
使用PID指令有以下要点和经验:
(1)比例系数和积分时间常数的确定。
应根据经验值和反复调试确定。
(2)调节量、给定量、输出量等参数的标准归一化转换。
(3)按正确顺序填写PID回路参数表(LOOP TABLE),分配好各参数地址。
5、结束语
单元机组燃烧过程控制系统在某火电厂发电机组锅炉协调控制系统中投入使用。
实际运行情况表明:由于引入负荷模糊前馈,使得锅炉燃烧控制系统作为协调控制的子系统,跟随机组负荷变化的能力显著提高,风煤比能够在静态和动态过程中保持一致;送、引风控制系统在逻辑控制系统的配合下运行的平稳性和安全性提高,炉膛负压波动减小,满足了运行的要求;在机组负荷不变时,锅炉燃烧稳定,各被调参数动态偏差显著减少,实现了锅炉的优化燃烧;采用非线性PID调节方式,解决了引风挡板的晃动问题。
采用西门子的PLC控制,不仅简化了系统,提高了设备的可靠性和稳定性,同时也大幅地提高了燃烧能的热效率。
通过操作面板修改系统参数可以满足不同的工况要求,机组的各种信息,如工作状态、故障情况等可以声光报警及文字形式表示出来,主要控制参数(温度值)的实时变化情况以趋势图的形式记录显示,方便了设备的操作和维护,该系统通用性好、扩展性强,直观易操作。