刀具切削部分几何参数的选择
刀具合理几何参数的选择

04
加工精度与表面质量保障 措施
加工精度影响因素剖析
机床精度
机床本身的制造精度、刚度、热稳定性等都 会直接影响加工精度。
刀具磨损
刀具在切削过程中会逐渐磨损,导致加工尺 寸和形状精度下降。
切削参数
切削速度、进给量、切削深度等参数的选择 不合理会导致加工精度降低。
工件材料
工件材料的硬度、韧性等物理特性对加工精 度也有一定影响。
主偏角优化
主偏角的大小会影响切削分力和径向力的大小,进而影响 加工精度和表面质量。需要根据具体加工要求选择合适的 主偏角。
刃倾角优化
刃倾角可以影响切屑的流向和切削刃的受力情况,通过调 整刃倾角可以改善切屑的排出效果和切削刃的受力状况, 提高加工精度和表面质量。
05
生产效率与经济效益提升 途径
生产效率现状分析
合理选择刀具材料
根据工件材料和加工要求选择适合的 刀具材料,如高速钢、硬质合金、陶 瓷等。
优化刀具几何参数
通过调整前角、后角、主偏角等参数, 降低切削力、切削热,提高刀具耐用 度。
采用涂层技术
在刀具表面涂覆一层或多层硬质薄膜, 提高刀具的硬度、耐磨性和耐热性。
控制切削用量
合理选择切削速度、进给量和背吃刀 量,避免过大的切削力导致刀具快速 磨损。
感谢您的观看
THANKS
刀具合理几何参数的选择
目录
• 刀具几何参数概述 • 切削力与切削热分析 • 刀具磨损与耐用度评估 • 加工精度与表面质量保障措施 • 生产效率与经济效益提升途径 • 总结与展望
01
刀具几何参数概述
定义与分类
刀具几何参数定义
描述刀具形状和尺寸的各参数, 包括切削刃形状、前角、后角、 主偏角、副偏角等。
第五章 切削用量及刀具几何角度的选择(机械制造技术A)

Thank you for your listening!
测试1:
1、积屑瘤在粗、精加工中各起什么作用?当其有害 时怎样抑制它?
2、影响积屑瘤大小的因素?精加工外圆时怎样抑制它? 为什么?
3、试推导变形系数ξ与剪切角Φ之间的关系。
4、单位切削力的定义?
5、切削用量三要素对切削力的影响与对刀具耐用度 的影响有什么不同?请利用指数公式对该问题进行 分析,并提出降低切削力和提高刀具耐用度的措施。
5.4 过渡刃与修光刃参数的选择
一、过渡刃及其参数选择 ⑴外圆车刀过渡刃参数:
过渡刃偏角
rs
1 2
r
过渡刃长度
bs=0.5~2mm
⑵切断刀过渡刃参数 过渡刃偏角 κrs=45° 过渡刃长度 bs=(0.20~0.25)ap
Κ'r
Κr
3)圆弧过渡刃
⑴高速钢车刀 r 0.5 ~ 5mm ⑵硬质合金车刀 r 0.5 ~ 2mm
3.负前角单面型 优点:刃口强度高。 缺点:刃口钝,对切削层的挤压严重。
使用场合: ⑴主要用于硬质合金车刀和铣刀; ⑵切削高强度、高硬度材料和切削淬火钢; ⑶当磨损主要发生在后刀面时。
4.正前角正倒棱 使用场合:适用于高速钢刀具 正倒棱尺寸参数:
br1 (0.5 ~ 1) f ; 01 0 ~ 5
在刀具前刀面上,切屑流出的方向与切削刃法线 间的夹角Ψλ称为流屑角。
主切削刃法线 主切削刃
(1)用测定切屑宽度bc的方法求流屑角:
cos
bc b
cos s
⑵实际切削角 ①流屑剖面:包含切屑流出方向和切削速度的剖面Pλ。 ②实际切削角:在流屑剖面内测量的角度 实际切削前角
sin oe cos sin n cos s sin sin s sin oe sin2 s cos2 s sin n
第9章刀具合理几何参数的选择及切削用量优化

刀具合理几何参数和切削用量的选择是否合理对刀具使用寿命、加工质量、生产效率和加工成本等有着重要影响。
刀具的“合理”的几何参数是指在保证加工质量的前提下能够获得最高刀具耐用度达到提高切削效率或降低生产成本目的的几何参数。
第一节概述什么是刀具的合理或最佳几何参数呢在保证加工质量的前提下能够满足生产效率高、加工成本低的刀具几何参数称为刀具的合理几何参数。
一般地说刀具的合理几何参数包含以下四个方面基本内容1 刃形刃形是指切削刃的形状有直线刃、折线刃、圆弧刃、月牙弧刃、波形刃、阶梯刃及其他适宜的空间曲线刃等。
刃形直接影响切削层的形状影响切削图形的合理性刃形的变化将带来切削刃各点工作角度的变化。
因此选择合理的刃形对于提高刀具使用寿命、改善已加工表面质量、提高刀具的抗振性和改变切屑形态等都有直接的意义。
2 切削刃刃区的剖面型式及参数通常将切削刃的剖面型式简称为刃区型式。
针对不同的加工条件和技术要求选择合理的刃区型式如锋刃、后刀面消振棱刃、前刀面负倒棱刃、倒圆刃、零度后角的刃带及其合理的参数值是选择刀具合理几何参数的基本内容。
图所示为五种刃区型式。
图常见的五种刃区形式a锋刃b消振棱c-负倒棱d-倒圆刃e刃带3 刀面型式及参数前刀面上的卷屑槽、断屑槽后刀面的双重刃磨、铲背以及波形刀面等都是常见的刀面型式。
选择合理的刀面型式及其参数值对切屑的变形、卷曲和折断对切削力、切削热、刀具磨损及使用寿命有着直接的影响其中前刀面的影响和作用更大。
4 刀具角度刀具角度包括主切削刃的前角γ0、后角а0、主偏角κr、刃倾角λs和副切削刃的副后角а??0、副偏角κ??r等。
刀具合理几何参数的选择主要决定于工件材料、刀具材料、刀具类型及其他具体工艺条件如切削用量、工艺系统刚性及机床功率等。
当确定了刀具几何参数后还需选定合理的切削用量才能进行切削加工。
在机床、刀具和工件等条件一定的情况下切削用量的选择最富有灵活性和能动性。
对于充分发挥机床和刀具的功能以取得生产的最大效益来说切削用量的选择如果得当就可能最大限度地挖掘出生产潜力倘若选择不当会造成很大的浪费或导致生产事故。
刀具几何参数和切削用量的合理选择

加工条件:工艺系统刚性差时,易出现振
动,应选取较小的后角αo;加工表面质量要求 较高时,为减轻刀具与工件之间的摩擦,应选
取较大的后角αo;尺寸精度要求较高时,应选 取较小的后角αo,以减小刀具的径向磨损值NB 值,如下图所示。
硬质合金车刀合理后角的参考值如下表所示。
② 后角αo的选择
切削厚度hD:粗加工时,切削厚度hD较大,要 求切削刃坚固,应选取较小的后角αo。精加工时, 切削厚度hD较小,磨损主要发生在后刀面上,为降 低磨损,应选取较大的后角αo。
工件材料:工件材料强度和硬度较高时,为提
高切削刃强度,应选取较小的后角αo;工件材料软、 塑性大时,后刀面磨损严重,应选取较大的后角αo; 工件材料脆性较大时,载荷集中在切削刃处,为提
负前角双面型:该形式的刀具使刀具的重磨次数 增加,最大程度地减少了前刀面和后刀面的磨损。同 时负前角的倒棱应有足够的宽度,以确保切屑沿该棱 面流出。
(3)倒棱
倒棱是增强切削刃强度的一种措施。在用脆性大 的刀具材料粗加工或断续切削时,磨倒棱能够减小刀 具崩刃,显著提高刀具耐用度(可提高1~5倍)。
倒棱宽度br1不可太大,以便切屑能沿前刀面 流出。br1的取值与进给量f有关,常取br1≈ (0.3~0.8)f。其中,精加工时取小值,粗加工
② 前角γo的选择
工件材料:工件材料的强度、硬度较低,塑
性较好时,应选取较大的前角γo;工件材料脆性较 大时应选取较小的前角γo;工件材料强度、硬度较 高时,应选取较小的前角γo,甚至负前角。
刀具材料:刀具材料的强度和韧度高时,如高 速钢,可选取较大的前角γo;反之,刀具材料的强度 和韧度差时,如硬质合金,应选取较小的前角γo。
刀具切削部分的几何参数

• 2.法平面 切削刃上选定点的法平面是过该点并与 切削刃垂直的平面,记作Pn;
• 3.假定工作平面 切削刃上选定点的假定工作平面 是过该点、垂直于基面并与进给方向平行的平面, 记该作点P且f;垂而直背于平基面面切和削假刃定上工选作定平点面的的背平平面面,是记过为 Pp
由Pγ、P S、P 0组成,两两垂直
a)正交正面参考系
由Pγ、Ps、Pn组成
刀具标注角度参考系 b)法平面参考系
由Pγ、Pf、Pp组成,两两垂直
c)假定工作平面参考系
三、正交平面参考系刀具的标注角度
• 在刀具工作图中标出的几何角度,是刀具设计、 制造、刃磨和测量的依据 。
• 1.正交平面参考系中的刀具标注角度 • (1) 基面Pr内的角度
主偏角有45、60、75、90°
在基面Pr内测量的 副切削平面与假定 工作平面Pf 的夹角。 作用:减小副切削
刃与工件已加工面
间的摩擦及振动。
副偏角大,刀尖强
度弱,已加工表面
残留面积大,粗糙 度值大。
• (2) 切削平面PS内的角度 • λs:在切削平面PS内测量的主切削刃S与基面
Pr间的夹角称刃倾角;
谢谢观赏!
2020/11/5
22
实体减小时为正。作用:减小 主后刀面与工件加工表面间的 摩擦、主后刀面的磨损。过大, 刀刃强度下降,导热体积减小, 主后ቤተ መጻሕፍቲ ባይዱ面磨损加快。粗加工和 承受冲击载荷时,选小值4°~ 6°,保证强度; 精加工时,选大值8°~12°, 保证表面质量。
副后角
➢实体减小时为正。 前角增大,刀具锋 利,切削轻快。但 过大,刀具强度下 降,导热体积减小 ,刀具寿命短。
刀具几何参数与刀具材料的合理选择-yxj资料

种类
碳素 工具 钢 合金 工具 钢
常用牌号
T8A、T10A T12A
9siCr 、 CiWMn
高速 钢
W9Mo3Cr 4V 、 W6Mo5Cr V2
硬度HRC (HRA)
60~64 ( 81 ~ 83) 60~65 ( 81 ~ 84)
63~69 ( 82 ~ 87)
抗弯强 度
( GP 2.4a5) ~ 2.75
2.刃倾角的选择
选择刃倾角时,应按照刀具的具体工作条件进行具体分析,一般情 况可按加工性质选取。精车λs =0o~5o;粗车λs =0o~-5o; 断续车削λs=-30o~-45o;大刃倾角精刨刀λs=75o~80o。
(1)控制切屑的流向 如图5-5所示,当λS =0o 时,切屑垂
直于切削刃流出;λS为负值时,切屑流向已加工表面; λS为正值时,切屑流向待加工表面。
用于机动复 杂的中速刀 具,如钻头、 铣刀、齿轮 刀具等
硬质 合金
陶瓷
( YG 类 ) 69~81 K 类 ( YT ( 89 ~ 类 ) P 类 93) ( YW 类 ) M类
SG4 、 ( 93 ~
AT6
94)
1500~
2100HV
1.08 ~ 2.16
0.4 ~ 1.115
800 ~ 1100
2.前角的选择原则 (1)主要根据工件材料的性质选择 (2)兼顾根据刀具材料的性质和加工性质 表5-1是硬质 合金车刀合理前角的 参考值。
3.前刀面型式(图5-3 前刀面型式)
(1)正前角平面型 如图5-3a所示,正前角平面型式的特点为:制造简单
能获得较锋利的刃口,但强度低,传热能力差。一般用于精加工刀 具、成形刀具、铣刀和加工脆性材料的刀具。
2-1 刀具切削部分几何参数
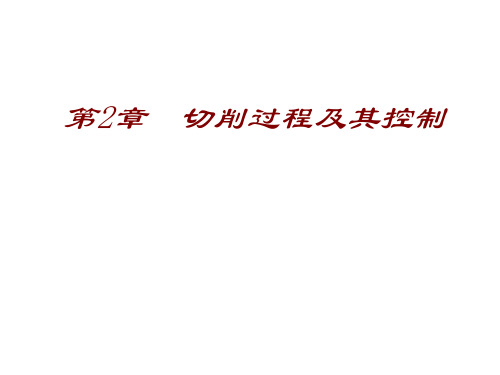
件上切去一部分金属,并在保证高生产率和低成本的前提下,
使工件得到符合图样要求的形状、尺寸精度和表面质量。为了 实现这一过程,必须具备以下三个条件:工件与刀具之间要有 相对运动,即切削运动;刀具材料必须具有一定的切削性能; 刀具必须具有适当的几何形状, 即切削角度。
2.1.1切削加工成形运动
以图2—1所示外圆车削为例,要切除工 件表面多余金属层,刀具与工件间必须有 相对运动,即工件必须作回转运动,刀具 作直线运动。 依其作用的不同,可把切削运动分为主运动 与进给运动。
1. 切削厚度 hD:在垂直于切削刃的方向上度量的切削层截面的 尺寸。hD反映了切削刃单位长度上工作负荷的大小 hD= f sinκr 2. 切削宽度 bD :沿切削刃方向度量的切削层截面的尺寸。 bD 影响刀具的散热情况 bD= ap/sinκr 3.切削层面积AD=hDbD=faP Κr为车刀主偏角,当工艺参数进给量f与背吃刀量ap确定后,主 偏角Κr越大,切削厚度越大hD ,切削宽度越小bD ,
3. 背吃刀量(切削深度) ap 背吃刀量ap是指主刀刃与工件切削表面接触长度,在主运动 方向及进给所组成的平面的法线方向上测量的值
车削外圆时 钻孔时
ap = (dw-dm)/2 ap = dm/2
dw-待加工表面直径
dm-已加工表面直径
a)车外圆
图2-2 切削用量 b)车端面 c)切槽
例题:
车外圆时工件加工前直径为62mm,加工后直径为56 mm,工件转速为4r/s,刀具每秒钟沿工件轴向移动2mm, 工件加工长度为110mm,切入长度为3mm,求v、f、ap
车削时的假设条件有:
①主切削刃处在水平面上,刀尖恰在工件中心 高度上: ②刀柄中心线垂直于工件轴线(假定进给方向); ③主运动方向与刀具底面垂直(不考虑进给运 动); ④工件已加工表面的形状为圆柱面。
机械制造技术基础 第二章 第七节 刀具合理几何参数的选择

3、前刀面形式的选择(负倒棱和刃口钝圆及卷屑槽) ⑴ 负倒棱 ① 负倒棱主要作用: 优点:增强切削刃,减小刀具破损;此外,刀具倒棱处的楔角较大,使散热条件也
3、副偏角的选择原则 ⑴ 在不引起振动的情况下 副偏角κγ’易取较小值。 精加工时, κγ’取得更小,有时还可磨出修光刃。 ⑵ 加工高硬度、高强度或断续切削 副偏角κγ’易取较小值。
⑶ 切断刀及切槽刀受结构及强度的限制 4、刀尖形式的选择
κγ’取值很小, κγ’=1°~3°。
⑴ 圆弧过渡刃 圆弧形过度刃不仅可提高刀具寿命,还可大大减小已加工表面粗糙度,精加工时常 采 用 圆弧过渡刃。但它需在专用磨床上刃磨。 ⑵ 直线形过渡刃 粗加工时,背吃刀量比较大,为减小径向分力Fy和振动,通常取较大的主偏角。但这 时刀尖强度较差,散热条件恶化。为改善这种情况,提高刀具寿命,常常磨出直线性的过 渡 刃。 通常,取κγε=0.5κγ,bε=0.5~2mm.
第七节
刀具几何参数
刀具合理几何参数的选择
刀具的切削角度(γo、αo、κr、κr’、λs) 前刀面的形式(平的、带倒棱的、带卷屑槽的前刀面)
切削刃的形状(直线型、折线形、圆弧形) 合理几何参数:在保证加工质量的前提下,能够获得最高刀具寿命,从而能够达到提高切削 效率或降低生产成本目的的几何参数。
Leabharlann 、刃倾角的选择1、刃倾角主要的作用 ⑴ 控制切屑流出方向
λs=0°时,切屑近似沿垂直切削刃的方向流出; λs>0°时,切屑流向待加工表 面; λs<0°时,切屑流向已加工表面。
- 1、下载文档前请自行甄别文档内容的完整性,平台不提供额外的编辑、内容补充、找答案等附加服务。
- 2、"仅部分预览"的文档,不可在线预览部分如存在完整性等问题,可反馈申请退款(可完整预览的文档不适用该条件!)。
- 3、如文档侵犯您的权益,请联系客服反馈,我们会尽快为您处理(人工客服工作时间:9:00-18:30)。
Kr ’
3.影响已加工表面质量
减小Kr进可以使工件表面残留面积高度减小, 从而使已加工表面粗糙度值减小。
4.影响断屑效果、排屑方向
增大Kr会使hD增厚,bD减小,有利于切屑折断, 有利于孔加工刀具使切屑沿轴向顺利流出。
二、合理主偏角的选择原则
粗加工时, 硬质合金车刀一般选用较大 的主偏角(Kr=60~75),以利于减少振
切削刃强度及抗冲击能力 增加,且有一定的减压和 消振作用。
适用于陶瓷等脆性材料刀具。
后角及后面形状的选择
后角的作用主要
1) 减小主后刀面与工件之间的摩擦,提高已加工表 面质量和延长刀具寿命; 2) 配合前角调整切削刃和刀头部分锋利程度、强度和 散热条件; 3) 小后角车刀在特定的条件下可抑制切削时的振动。
主偏角减小,则刀尖角r增大,
使刀尖强度提高,散热体积增大。 主偏角较小的刀具在切入时,最 先与工件接触处是远离刀尖的地 方,因而可减少因切入冲击造成 的刀尖损坏。
2.影响切削分力比值及切削层单位面积切削力
当Kr减小时,由于hD 减小,变形系数增大, 使切削层单位面积切削力 Ff 有所增大;在ap和f相同时, 使切削功率有所增加。但 Kr1 更主要的是会使背向力Fp Kr2 增大,容易引起工艺系统 振动。当工艺系统刚度不 足时,会使刀具寿命降低。
动、断屑和采用较大的切削深度。 加工硬度高的材料,如冷硬铸铁和淬硬钢 时,在系统刚性好,切削深度不大时.取
较小的主偏角(Kr=10~30),以利于提
高刀具耐用度。
工艺系统刚性较好时,取较小的主偏角可 提高刀具耐用度;刚性不足,加车削细长
轴时,应取大的主偏角,可取Kr=90~93,
以减小背向力ap,减少振动。 需要从中间切入及仿形加工的车刀,应取 较大主偏角; 车阶梯轴则需用Kr=90的偏刀;
三、副偏角的作用及选择
1. 副偏角Kr的作用 减小副切削刃及副后面与已加工表面之间的摩擦。 副偏角 Kr的大小主要影响刀具耐用度和已加 工表面质量。
Kr 对刀具耐用度的影响
副偏角太小或太大刀具耐用度 都不高,其存在着一个合理值
这是因为:
副偏角过小会增加参加切削工作的刀刃 长度,增大副后刀面与已加工表面间的摩擦, 同时也易引起振动; 而副偏角过大致使刀尖强度降低和散热 条件恶化,结果会使刀具耐用度降低。
孤立地选择某一角度并不能得到所希望的合理值。 例如:改变前角将使刀具的合理后角发生变化。
在加工硬度较高的材料时,为增加刀刃强度, 一般取较小的后角。
但在加工特别硬的材料,如淬硬钢时,通常采用负 前角,这时楔角已较大,如适当增加后角,不仅使 切削刃易于切入工件,而且还可提高刀具耐用度。
刀具前角和刃倾角的选择也常常是互相影响的。 强力切削时,切削面积大,切削力也大,为强化刀刃, 前角适宜取小一些。但此时如采用太小前角会导致切 屑变形太大。可以采用较大前角,而同时采用负的刃 倾角及负倒棱来强固刀刃;采用过渡刃来强化刀尖, 从而达到满意的效果。
比平前刀面可取较大前角且改善了卷屑 和断屑条件,但刃磨不如平前面简便。 各种高速钢刀具,加工纯铜、铝合金等低 强度、低硬度的硬质合金刀具。
切削刃强度及抗冲击能力增加, 在同样条件下允许采用较大的 前角,提高了刀具寿命。
加工各种钢材等塑性材料的硬 质合金车刀。 加工铸铁等脆性材料用的硬质 合金、陶瓷刀具。 零度倒棱,适用于高速钢刀具。
如加工灰铸铁取o=5~15。
前角数值随脆性材料强度和硬度的增大而逐渐减小。 在加工淬火钢、冷硬铸铁等高硬度难加工材料时,宜取负 前角。 实验证明,用正前角硬质合金车刀加工高硬度淬火钢时, 切削刃几乎一开始切削就会发生崩刃。
前角选择:具体加工条件
粗加工时或断续切削时,切削力和冲击较大,为 使切削刃有足够强度,宜取较小前角;
项目七
刀具选择
子项目1
刀具角度选择
问题1:切削力的影响
问题2:切削温度的影响
问题3:刀具寿命的影响
为什么要选择刀具角度
因为它影响:切削加工生产率
刀具耐用度 加工质量 加工成本 刀具角度选择的依据? 工件材料 刀具材料 切削用量
工艺系统刚性
机床功率
1 前角及前刀面形状的选择
Pr
γo2 γo1
前角决定
2.影响切削刃的锋利程度。
当s0的斜角切削时,由于切屑在前刀面 上流向的改变,使实际前角增大;同时,刃倾角 增大还可减小刀刃的钝圆半径,使切削刃变得锋
利。如切下极薄切屑的精车刀、精刨刀多采
用45~75的大刃倾角。
3.影响切削分力的大小。
当负刃倾角绝对值增大时,背向力Fp显著增
大,将导致工件变形及引起振动。
硬脆刀具材料、加工高强度、高硬度(如淬火钢) 的车刀、铣刀、面铣刀等。
在加工塑性材料时,为使切屑卷成螺旋形或折断 成C形,使之易于排出和清理,常在前刀面上制成 卷断屑槽。
卷断屑槽可作成直线圆弧型、直线型和全圆弧型三种。
全圆弧型适用于切削紫铜、不锈钢等高塑性材料, 0可增大至25 ~ 30。 直线圆弧型和直线型断屑槽适用于切削碳素钢、合金 结构钢、工具钢等,0=5~15。
主、副偏角及刀尖形状的选择
• 主偏角的功用
• ①影响已加工表面残留面积的高度 • ② 影响各切削分力的比例 • ③影响刀尖的强度和刀具耐用度 • ④影响断屑
主、副偏角及刀尖形状的选择
一、主偏角对切削加工的影响
1.对刀具耐用度影响很大。随着主偏角减小,刀具 耐用度提高。这是因为:
当背吃刀量ap和进给量f相同时,主偏角 的变化将改变切削层形状,使切削层参数 发生变化,从而影响切削刃上的负荷。 当主偏角Kr减小时,由于切削层公称宽度 bD(=ap/sinKr)增加,切削层公称厚度 hD(=fsinKr)减小,使作用在主切削刃单位 长度上的负荷减轻。
影响刀具耐用度和加工表面质量。
合理后角的选择
当 hD( 或进给量 f) 很小时 ( 精加工 ) ,磨损主要发生 在后刀面上,为减小磨损和增加切削刃的锋利程度, 宜取较大的后角。 当切削厚度很大时,前刀面上月牙洼磨损显著,这 时取较小后角可以增强切削刃和加大散热体积。
例如:高速钢立铣刀,由于每齿进给量很小,后角取到 16,而圆片铣刀当 每齿进给量为 0.01mm时,后角取30。车刀后角的变动范围比前角要小。粗 车时,因 hD较大,为保证切削刃强度取较小后角 (4 ~ 8);而精车时, hD 较小.为保证已加工表面质量,取较大后角 8~12。切断刀的进给量较小, 且考虑进给运动对工作后角的影响.宜取较大后角10~12。
采用负前角:通常在用脆性刀具材料 加工高强度高硬度工件材料 易产生崩刃
选择时考虑:刀具材料
高速钢刀具的前角 > 硬质合金刀具+5~10。
陶瓷刀具的脆性更大,故前角常取负值(多在-4~-15范围) 以改善刀具受力时的应力状态,并选负的刃倾角(取0~-10) 与之配合以改善切入时承受冲击的能力。 立方氮化硼(CBN)由于脆性更大,都采用负前角高速切削。
后角归纳为 尽量小
① 粗加工:ao↓ , 精加工:ao ↑
② 塑性材料:ao ↑ 脆性材料:ao ↓, 硬度高:ao,强度高ao ↓
③ 工艺系统:刚度高ao ↓
归纳总结
车刀的副后角
车刀的副后角一般取其等于
主后角。
切断刀及切槽刀的副后角,
由于受其结构强度的限制, 只能取得很小, 0=1 ~ 2 。
高速钢的强度高,韧性好;硬质合金脆性大,怕冲击,易崩刃。
选择时考虑:工件材料
塑性材料:切屑呈带状,沿刀具前面流出时和前面接触长度较 长,摩擦较大,为减小变形和摩擦,一般都采用正Байду номын сангаас角。
强度、硬度高:单位切削力大,切削温度容易升高,前角宜取
小值。为了提高切削刃强度,增加刀头导热面积和容热体积, 脆性材料时,塑性变形小,切屑呈崩碎状,切削力集中,易 崩刃,前角小一些。
• 1)粗加工λS< 0(保护刀尖)精加工λS> 0 (使FP小些) • 2)断续切削:λS< 0(保护刀尖)
• 3)工件σb、HB大:λS< 0(保护刀尖)
• 4)系统刚性差:λS> 0(使FP小些)
• 5)微量切削:λS取大值(使刀具实际刃口 半 径 ↓)
注意:刀具各角度之间是互相联系互相影响的。
二、后刀面形状及选择
为减少刃磨后面的劳动量,提高刃磨质量, 常把后面作成双重后面,b1取l~3mm。
消振棱
沿着后刀面磨出负后角倒棱面,倒棱角 01=-5~-10,倒棱面宽b1=0.1~0.3mm。
它可以增加后刀面与加工表面的接触面积,在切
削时能产生同振动位移方向相反的摩擦阻力,不仅可 以减小振动,也可对工件表面起一定的熨压作用,从 而提高加工表面质量。 这是车削细长轴和镗孔时常采取的消振措施之一。
刀具后角:切削条件
工件材料的强度、硬度较高时,为加强切削刃, 宜取较小后角(0=5~7)。
工件材料塑性较大,加工硬化严重时,为减小后 刀面摩擦,应取较大后角(10 ~ 12)。 当采用负前角刀具加工高硬度高强度材料时,宜 采用较大后角(12 ~ 15),
工艺系统刚性较差时,为避免振动,应适当减小 后角。
刃倾角对刀具耐用度的影响如下图所示。
在不同的加工条件下,也存在着一个合理数值。
二、合理刃倾角的选择原则
1.加工一般钢料和灰铸铁,粗车取s=0~5, 精车时取s=0~+5;有冲击负荷时, s=-5~-15;当冲击特别大时,可取 s=-30~-45。
2.加工高强度钢、高锰钢、淬硬钢时,可取 s=-5~-15或负数的绝对值更大一些。 3.工艺系统刚性不足时,尽量不采用负刃倾角。
Kr 对加工表面质量的影响
在副偏角较小时,加工表面粗糙 度值较小。