(技术规范标准)安全技术规范
最新建筑施工现场安全管理安全技术规范(标准全检查标准

建筑施工现场安全管理安全技术规范(标准)安全检查标准施工现场安全管理的基本要求安全生产需要制度保证,需要技术支撑,为了确保安全生产,减少伤亡事故的发生,建设部颁发了一系列相关的安全生产法规、技术规范、标准,对企业和施工现场安全管理、文明施工以及施工工艺、安全操作要求等方面均作出了明确的规定,为提升建筑施工安全生产管理水平,确保安全生产提供了可靠的依据和坚实的基础。
安全管理的核心内容就是要在生产的整个过程中遵循和落实以上要求。
第一节安全管理•建筑施工现场安全管理有十个方面的内容,(插入评分汇总表)安全管理是建筑施工现场安全生产的关键工作,也是建筑施工现场安全管理工作的综合体现。
•施工现场安全管理落实,是造成生产安全事故的主要原因之一,在生产安全事故的分析中有89%都不是因技术解决不了的问题而造成生产安全事故,都是因违章等原因而造成(违章指挥、违章操作、违反劳动纪律等)。
我国建设工程安全生产状况(总体情况)根据建设部的统计数据,2014年全国共发生房屋建筑和市政工程建筑施工事故859起、死亡1012人,与2006相比,事故起数下降了3.27%,死亡人数下降了3.44%,其中共发生建筑施工较大及以上事故(一次死亡3人及3人以上事故)35起、死亡144人(其中重大事故2起,死亡21人),与2006相比,事故起数下降了10.26%,死亡人数下降了1.37%,具体如图1.1和图1.2。
通过2006年和2007年的建筑施工安全生产事故统计对比表明:虽然我国建设工程安全生产整体状况有所好转,但建筑安全生产形势仍然比较严峻。
主要表现在:一是事故总量仍然较大;二是下降幅度趋减;三是重特大事故多发。
这表明我国仍处在建筑施工频繁发生的时期,建筑安全生产形势又将面临新的考验。
(多年的统计数据及变化规律在有关文献上有分析)(一)事故多发的主要类型:主要是高处坠落、坍塌、物体打击、触电、起重伤害等。
(图)(二)事故发生部位(图)(三)发生事故工程基本建设程序履行情况(一)安全生产责任制•(1)企业应建立健全安全生产责任制,规定和落实企业各级领导、各个部门、各类人员在各自职责范围内对安全生产履行的职责和应负的责任。
(技术规范标准)尾矿库安全技术规范

尾矿库安全技术规程前言1 范围2 规范性引用文件3 术语和定义4 尾矿库等别及构筑物级别5 尾矿库建设6 尾矿库生产运行7 尾矿库安全检查8 尾矿库安全度9 尾矿库闭库10 尾矿再利用及尾矿库闭库后再利用11 尾矿车安全评价12 尾矿库工程档案附录A 上游式尾矿坝的渗流计算简法(资料性附录)附录B 坝体尾矿的平均物理力学指标(资料性附录)前言为规范尾矿库建设、运行、闭库及再利用,保障人民生命财产安全,依据《中华人民共和国安全生产法》、《中华人民共和国矿山安全法》和有关法律、行政法规及有关行业技术标准、规范、规定,制定本规程。
本规程的附录A、附录B是资料性附录。
本规程是由国家安全生产监督管理总局提出并归口。
本规程起草单位:中国有色工程设计研究总院、秦皇岛冶金设计研究总院。
本规程主要起草人:田文旗、曲忠德、伍绍辉、杨春福、时炜、王树。
1 范围本规程规定了尾矿库在建设、生产运行、安全检查、安全度、闭库、再利用、安全评价等方面的安全要求。
本规程适用于中华人民共和国境内金属、非金属矿物选矿厂尾矿库、氧化铝厂赤泥库。
其他湿式堆存工业废渣库、电厂灰渣库和干式处理的尾矿库可参照执行。
2 规范性引用文件下列文件中的条款通过本规程的引用而成为本规程的条款。
引用文件最新版本,以及其后的修订版均适用于本规程。
选矿厂尾矿设施设计规范尾矿设施施工及验收规程岩土工程勘察规范碾压式土石坝设计规范碾压式土石坝施工规范水工建筑物抗震设计规范构筑物抗震设计规范3 术语和定义下列术语和定义适用于本规程。
3.1 尾矿库 tailings pond筑坝拦截谷口或围地构成的、用以贮存金属非金属矿山进行矿石选别后排出尾矿或其他工业废渣的场所。
3.2 全库容 whole storage capacity尾矿坝某标高顶面、下游坡面及库底面所围空间的容积,包括有效库容、死水库容、蓄水库容、调洪库容和安全库容5部分。
3.3有效库容 effective storage capacity某坝顶标高时,韧期坝内坡面、堆积坝外坡面以里(对下游式尾矿筑坝则为坝内坡面以里),沉积滩面以下,库底以上的空间,即容纳尾矿的库容。
(技术规范标准)特种设备安全技术规范
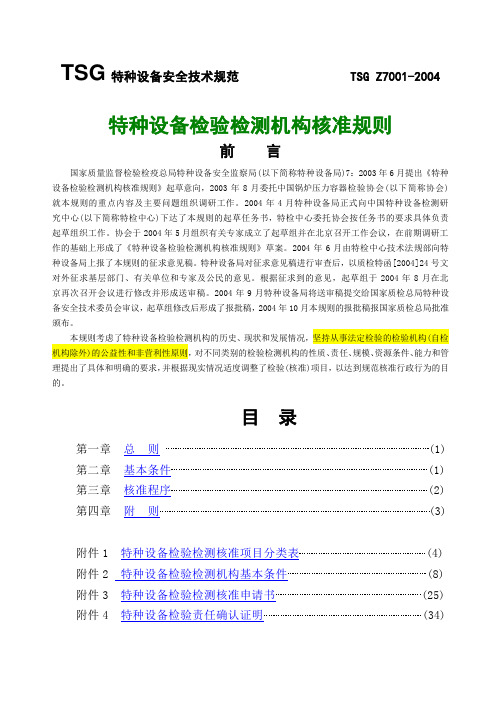
TSG特种设备安全技术规范 TSG Z7001-2004特种设备检验检测机构核准规则前言国家质量监督检验检疫总局特种设备安全监察局(以下简称特种设备局)7:2003年6月提出《特种设备检验检测机构核准规则》起草意向,2003年8月委托中国锅炉压力容器检验协会(以下简称协会)就本规则的重点内容及主要问题组织调研工作。
2004年4月特种设备局正式向中国特种设备检测研究中心(以下简称特检中心)下达了本规则的起草任务书,特检中心委托协会按任务书的要求具体负责起草组织工作。
协会于2004年5月组织有关专家成立了起草组并在北京召开工作会议,在前期调研工作的基础上形成了《特种设备检验检测机构核准规则》草案。
2004年6月由特检中心技术法规部向特种设备局上报了本规则的征求意见稿。
特种设备局对征求意见稿进行审查后,以质检特函[2004]24号文对外征求基层部门、有关单位和专家及公民的意见。
根据征求到的意见,起草组于2004年8月在北京再次召开会议进行修改并形成送审稿。
2004年9月特种设备局将送审稿提交给国家质检总局特种设备安全技术委员会审议,起草组修改后形成了报批稿,2004年10月本规则的报批稿报国家质检总局批准颁布。
本规则考虑了特种设备检验检测机构的历史、现状和发展情况,坚持从事法定检验的检验机构(自检机构除外)的公益性和非营利性原则,对不同类别的检验检测机构的性质、责任、规模、资源条件、能力和管理提出了具体和明确的要求,并根据现实情况适度调整了检验(核准)项目,以达到规范核准行政行为的目的。
目录第一章总则(1) 第二章基本条件(1) 第三章核准程序(2) 第四章附则(3)附件1 特种设备检验检测核准项目分类表(4) 附件2 特种设备检验检测机构基本条件(8) 附件3 特种设备检验检测核准申请书(25) 附件4 特种设备检验责任确认证明(34)特种设备检验检测机构核准规则第一章总则返回目录第一条为规范特种设备检验检测机构的核准工作,根据《特种设备安全监察条例》以及《特种设备检验检测机构管理规定》,制定本规则。
(技术规范标准)起重吊具与索具安全技术标准
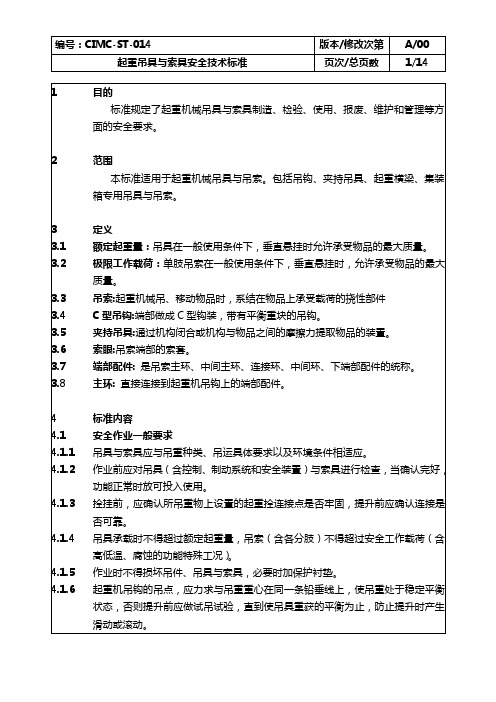
4.2 吊具与索具的基本要求4.2.1 结构应力求简单、受力明确、减少应力集中的影响;4.2.2 承载件有足够的强度、刚度和稳定性;4.2.3 吊具上外露有伤人可能的活动零部件,应装设防护罩;4.2.4 检验合格的吊具与索具,其适当位置应有不易磨损的标记,并具有合格证书。
标记内容至少应包括:额定起重量、检验标志、生产编号、制造日期、制造单位;合格证书内容应包括主要技术性能参数。
4.2.5 应使用有合格证书的吊具与索具,并建立及健全安全使用、维护保养规程和相应的规章制度。
4.3 钩取、夹取、抓取取物装置4.3.1 吊钩4.3.1.1 一般要求a 吊钩缺陷不得焊补;吊钩表面应光滑,不得有裂纹、折叠、锐角等缺陷。
b 吊钩内部不得有裂纹和影响安全使用性能的缺陷;不得在吊钩上钻孔或焊接。
c 在吊钩(不含板钩)开口最短距离处,选定二个适当位置打印或镶嵌不易磨损的标志,测出标志间的距离,作为使用中检测开口度是否发生变化的依据。
4.3.1.2 C形吊钩见图a 应能保证在承载和空载时保持平衡状态。
b C形吊钩应有使卷材在吊运时不受损伤的保护措施。
4.3.2 板钩板钩一般应采用GB700中规定的Q235-A、Q235-B或GB1591中规定的16Mn钢制造。
钩片的纵轴,必须位于钢板的轧制方向,且钩片不允许拼接。
板钩钩片应用沉头铆钉连接,而在板钩与盛钢桶耳轴接触的高应力弯曲单位不得用铆钉连接。
叠片间不允许全封闭焊接,只允许有间断焊。
4.4.10.6 转锁、搭钩的开闭指示装置、安全保护(联锁)装置失灵。
4.5 吊索4.5.1 一般要求4.5.1.1 吊索基本结构型式a.单肢吊索;b.环形吊索;c.双肢吊索;d.三肢吊索;e.四肢吊索a.吊链;下端部配件;b.卸扣;c.链环;d.环眼吊钩;e.C形环眼吊钩4.5.1.2 下端部配件,一般应有自锁倾向或防止吊重滑落性能。
4.5.1.3 主环内宽应不小于所用起重机械承载吊钩截面最大宽度的1.2倍。
(技术规范标准)安全技术操作标准全部
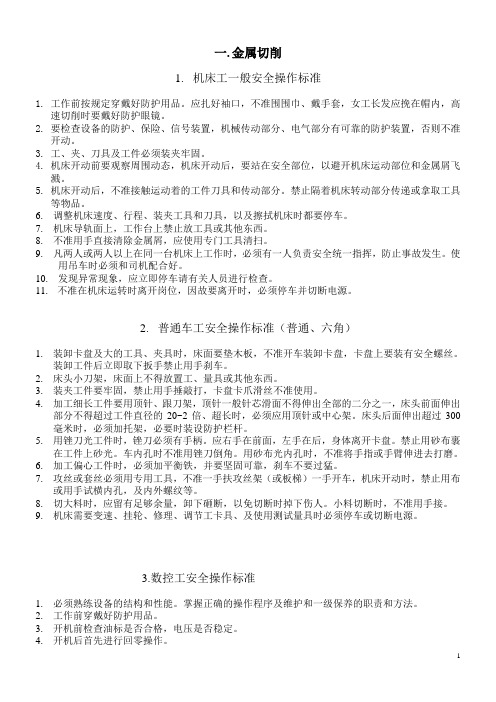
一.金属切削1.机床工一般安全操作标准1. 工作前按规定穿戴好防护用品。
应扎好袖口,不准围围巾、戴手套,女工长发应挽在帽内,高速切削时要戴好防护眼镜。
2.要检查设备的防护、保险、信号装置,机械传动部分、电气部分有可靠的防护装置,否则不准开动。
3.工、夹、刀具及工件必须装夹牢固。
4. 机床开动前要观察周围动态,机床开动后,要站在安全部位,以避开机床运动部位和金属屑飞溅。
5. 机床开动后,不准接触运动着的工件刀具和传动部分。
禁止隔着机床转动部分传递或拿取工具等物品。
6. 调整机床速度、行程、装夹工具和刀具,以及擦拭机床时都要停车。
7. 机床导轨面上,工作台上禁止放工具或其他东西。
8. 不准用手直接清除金属屑,应使用专门工具清扫。
9. 凡两人或两人以上在同一台机床上工作时,必须有一人负责安全统一指挥,防止事故发生。
使用吊车时必须和司机配合好。
10. 发现异常现象,应立即停车请有关人员进行检查。
11.不准在机床运转时离开岗位,因故要离开时,必须停车并切断电源。
2.普通车工安全操作标准(普通、六角)1.装卸卡盘及大的工具、夹具时,床面要垫木板,不准开车装卸卡盘,卡盘上要装有安全螺丝。
装卸工件后立即取下扳手禁止用手刹车。
2.床头小刀架,床面上不得放置工、量具或其他东西。
3.装夹工件要牢固,禁止用手捶敲打,卡盘卡爪滑丝不准使用。
4.加工细长工件要用顶针、跟刀架,顶针一般针芯滑面不得伸出全部的二分之一,床头前面伸出部分不得超过工件直径的20~2倍、超长时,必须应用顶针或中心架。
床头后面伸出超过300毫米时,必须加托架,必要时装设防护栏杆。
5.用锉刀光工件时,锉刀必须有手柄。
应右手在前面,左手在后,身体离开卡盘。
禁止用砂布裹在工件上砂光。
车内孔时不准用锉刀倒角。
用砂布光内孔时,不准将手指或手臂伸进去打磨。
6.加工偏心工件时,必须加平衡铁,并要坚固可靠,刹车不要过猛。
7.攻丝或套丝必须用专用工具,不准一手扶攻丝架(或板梯)一手开车,机床开动时,禁止用布或用手试横内孔,及内外螺纹等。
安全技术标准、规范和操作规程管理制度范本(五篇)
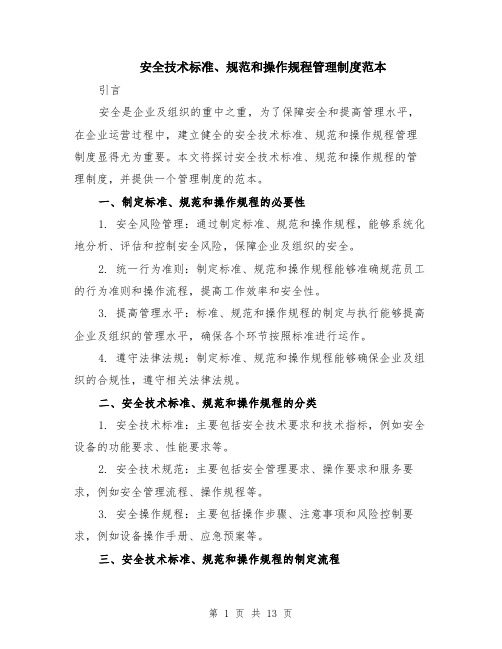
安全技术标准、规范和操作规程管理制度范本引言安全是企业及组织的重中之重,为了保障安全和提高管理水平,在企业运营过程中,建立健全的安全技术标准、规范和操作规程管理制度显得尤为重要。
本文将探讨安全技术标准、规范和操作规程的管理制度,并提供一个管理制度的范本。
一、制定标准、规范和操作规程的必要性1. 安全风险管理:通过制定标准、规范和操作规程,能够系统化地分析、评估和控制安全风险,保障企业及组织的安全。
2. 统一行为准则:制定标准、规范和操作规程能够准确规范员工的行为准则和操作流程,提高工作效率和安全性。
3. 提高管理水平:标准、规范和操作规程的制定与执行能够提高企业及组织的管理水平,确保各个环节按照标准进行运作。
4. 遵守法律法规:制定标准、规范和操作规程能够确保企业及组织的合规性,遵守相关法律法规。
二、安全技术标准、规范和操作规程的分类1. 安全技术标准:主要包括安全技术要求和技术指标,例如安全设备的功能要求、性能要求等。
2. 安全技术规范:主要包括安全管理要求、操作要求和服务要求,例如安全管理流程、操作规程等。
3. 安全操作规程:主要包括操作步骤、注意事项和风险控制要求,例如设备操作手册、应急预案等。
三、安全技术标准、规范和操作规程的制定流程1. 确定制定需求:根据企业及组织的实际需求,明确制定标准、规范和操作规程的范围和目标。
2. 收集资料:进行市场调研和文献检索,收集相关的技术资料和法律法规,为制定标准、规范和操作规程提供依据。
3. 制定草案:根据收集的资料,组织相关部门或专业人员,编写初稿。
4. 审核修改:由专业人员或审核小组对草案进行审核和修改,确保标准、规范和操作规程的准确性和合理性。
5. 审批发布:经过内部审核和相关部门的审批,确定标准、规范和操作规程的最终版本,并发布给相关部门和人员。
6. 实施与监督:将标准、规范和操作规程应用到实际操作中,并建立监督机制,确保规程的执行和有效性。
安全技术规范标准

安全技术规范标准一、机械安全风险评估在进行任何机械设备操作前,必须进行全面的机械安全风险评估,识别潜在的安全隐患。
风险评估应考虑设备的操作环境、使用频率、操作人员的熟练程度等因素。
基于风险评估结果,制定相应的安全操作规程和预防措施。
二、金属切削机床防护金属切削机床应配置合适的防护装置,如防护罩、防护网等,以防止切屑飞溅。
操作机床时应穿戴符合规定的防护用品,如防护眼镜、耳塞等。
机床应定期进行维护检查,确保设备处于良好的工作状态。
三、磨削机械安全规程磨削机械应安装砂轮防护罩,防止砂轮碎裂造成的伤害。
磨削时应保持适当的砂轮转速和工作液供给,避免砂轮过热。
操作人员应经过专业培训,了解磨削机械的安全操作规程。
四、联锁装置设计选择联锁装置应确保在设备故障或异常情况下,能够自动切断危险源,保护人员安全。
联锁装置的设计应考虑设备的特定工作条件和操作要求。
联锁装置应定期进行测试和检查,确保其可靠有效。
五、普通磨具安全规则使用磨具前应检查其完整性,确保无裂纹、无损坏。
磨具的转速应与设备匹配,不得超速使用。
磨具使用过程中应保持干燥,避免与水或其他液体接触。
六、机械安全防护装置机械安全防护装置应定期检查和维护,确保其完整有效。
防护装置的设计应合理,不得影响设备的正常操作。
操作人员应了解防护装置的作用和使用方法,正确使用防护装置。
七、砂轮机安全防护砂轮机应安装防护罩和防护网,防止砂轮碎片飞溅。
砂轮机的安装应稳固可靠,不得有晃动或振动现象。
操作砂轮机时应穿戴符合规定的防护用品,如防护眼镜等。
八、冲压安全管理规程冲压设备应配置合适的安全保护装置,如光电保护、双手操作等。
冲压作业前应检查设备的工作状态和安全保护装置的有效性。
操作人员应经过专业培训,了解冲压设备的安全操作规程和应急措施。
九、木工平刨床管理规程木工平刨床应配置合适的防护装置,如防护罩、防护挡板等。
操作平刨床时应穿戴符合规定的防护用品,如防护手套、耳塞等。
平刨床应定期进行维护检查,确保刀具锋利、设备稳定。
安全技术规范

安全技术规范
首先,安全技术规范需要从系统的整体架构出发,对系统进行全面的安全设计。
在系统设计阶段,需要充分考虑系统的安全性能和安全功能,采用安全可靠的技术方案,建立健全的安全策略和控制机制,确保系统在设计阶段就具备了较高的安全性。
其次,安全技术规范需要在系统开发过程中严格执行安全标准和规范,采用安
全可靠的编程语言和开发工具,编写安全性能良好的代码,确保系统的安全性能和稳定性。
同时,安全技术规范还需要在系统运行和维护阶段,建立健全的安全管理机制,包括安全监控、安全审计、安全漏洞管理、应急响应等,及时发现和解决系统的安全问题,确保系统的安全运行。
在实际应用中,安全技术规范需要综合运用各种安全技术手段,包括网络安全、数据安全、身份认证、访问控制、加密技术、安全审计等,综合运用这些安全技术手段,保障系统的安全性。
总之,安全技术规范是信息系统安全保护的基础和关键,只有严格执行安全技
术规范,才能有效保障信息系统的安全。
希望各个相关单位和个人都能高度重视安全技术规范,加强安全意识,做好信息系统的安全保护工作,共同维护网络安全,为信息社会的发展做出积极贡献。
- 1、下载文档前请自行甄别文档内容的完整性,平台不提供额外的编辑、内容补充、找答案等附加服务。
- 2、"仅部分预览"的文档,不可在线预览部分如存在完整性等问题,可反馈申请退款(可完整预览的文档不适用该条件!)。
- 3、如文档侵犯您的权益,请联系客服反馈,我们会尽快为您处理(人工客服工作时间:9:00-18:30)。
安全技术规范国家技术监督局1990-12-18发布,1991-12-01实施1主题内容及适用范围本标准规定了起重机械超载保护装置的功能要求、技术要求、试验方法、检验规则和安全管理措施。
本标准适用于桥式重机、门式(半门式)超重机、塔式起重机、流动式起重机、门座(半门座)超重机、铁路起重机、电动葫芦、固定式起重机所使用的超载保护装置(以下简称“装置”)。
2引用标准GB 998低压电器基本试验方法GB 4942.2低压电器外壳防护等级GB 2423.3电工电子产品基本环境试验规程试验Ca:恒定湿热试验方法3术语3.1超载保护装置safety devices against overloading起重机工作时,对于超载作业有防护作用的安全装置,包括起重量限制器、起重力矩限制器。
3.2动作点action point装机条件下,是指由于装置的超载防护作用,起重机停止向不安全方向动作时,起重机的实际起重量。
试验室条件下,是指判定到装置可以使起重机停止向不安全方向动作时,装置承受的实际载荷值。
3.3设定点set point装置标定时的动作点。
3.4综合误差combined error装置安装在起重机上,动作点偏离设定点的相对误差。
3.5动作误差action error在试验室条件下,装置动作点偏离设定点的相对误差。
3.6起重机状态crane configuration起重机在某一工况条件下的外部形状。
3.7电气型装置electric devices通过机械量与电量之间的转换达到规定功能的装置。
3.8机械型装置mechanical devices通过机械量之间的转换与开关(控制阀)配合达到规定功能的装置。
3.9故障failure装置丧失执行4.1条相应功能的能力或者综合误差超过规定值。
3.10不安全方向dangerous directions起重机超载时,吊物继续起升,臂架伸长,幅度增大及这些动作的组合。
3.11安全方向safety directions吊物下降,臂架缩短、幅度减小及这些动作的组合。
4功能要求4.1装置必须具备以下功能型式之一:a. 自动停止型。
当起升质量超过额定起重量时,应能停止起重机向不安全方向继续动作,同时应能允许起重机向安全方向动作;b. 综合型。
当起升质量达到额定起重量的90%左右时,应发出音响或灯光预警信号。
当起升质量超过额定起重量时,应能停止起重机向不安全方向继续动作,并发出声光报警信号,同时应能允许起重机安全方向动作。
4.2装置应能区别起重机实际超载与正常作业时吊物起升、制动、运行等产生的动载影响。
吊物挂碍(或与地面固结)时,应能立即执行规定的功能。
4.3装置正常工作时,应能自动地执行规定的功能,不得增加司机的额外操作。
4.4装置宜设有自动保险功能。
当装置内部发生故障时,能发出提示性报警信号。
5技术要求5.1电源开关使用电源的装置,在装置上不得装设可切断电源的开关。
5.2解除开关装置设置可以解除4.1条规定功能的开关时,必须同时安装开关锁定机构。
解除开关必须经主管人员同意方可开启使用。
5.3抗干扰性电气型装置应具有抗干扰措施。
5.4强度裕量装置的任何部件安装于起重机承载系统中时,其强度裕量不得小于该系统中承载零部件的强度裕量。
5.5材料和构造装置所用的电子元器件应严格筛选。
材料应选用具有足够强度和耐久性的材料,各安装件、联接件应有防松动措施,金属件应作防腐处理。
装置的构造应便于安装、调整、润滑和检修。
5.6综合误差5.6.1电气型装置不应超过±5%,机械型装置不应超过±8%。
综合误差计算方法如下:综合误差=(动作点-设定点)/设定点×100% (1)5.6.2对额定起重量随工作幅度变化的起重机,综合误差的有效范围应在使用说明书和产品铭牌上明确说明,原则上应能满足配用起重机的全部使用工况。
5.7设定点5.7.1设定点的调整应使起重机在正常工作条件下可吊运额定起重量。
5.7.2设定点的调整要考虑装置的综合误差。
在任何情况下,装置的动作点不得大于110%额定起重量。
5.7.3设定点宜调整在100%--105%额定起重量之间。
5.8信号5.8.1预警信号音响预警信号持续时间应大于等于5s,并与报警信号有明显区别。
灯光预警信号应使用黄色,必须在司机视野范围内清晰可见。
5.8.2报警信号音响报警信号应与起重机环境噪音有明显区别。
距发音部位1m及在司机位置测量均不应低于75dB(A)。
灯光报警信号应使用红色,必须在司机视野范围内清晰可见。
5.9显示误差5.9.1具有起重量或起重力矩显示功能的装置,相对于动作点的显示误差在试验室条件下不应超过±3%,装机条件下不应超过±5%。
显示误差计算方法如下:显示误差=(显示值-实测值)/实测值×100% (2)5.9.2装机试验确认后的显示误差及其对起重机的有效适用范围应在产品铭牌上明确说明。
5.10动作误差电气型装置不应超过±3%;机械型装置不应超过±5%。
动作误差与综合误差的计算方法相同。
5.11耐振动冲击性装置应能承受起重机工作所引起的振动和冲击,不得因振动和冲击试验影响其安全性能。
5.12温度适应性装置-20--+60℃的环境温度条件下应正常工作。
5.13耐电压波动能力使用电源的装置,在以下电压范围内应正常工作。
a. 外接电网供电:-15%--+10%额定电压;b. 蓄电池供电:-15%--+35%额定电压。
5.14绝缘能力使用电源的装置,绝缘电阻不应低于1MΩ,并应能通过规定的耐压试验。
5.15过载能力取力传感器应能承受配用起重机规定的最大载荷试验。
5.16防护等级装置的防护等级应符合以下规定:a. 装置室内部分:IP42;b. 装置室外部分:IP44,传感器IP65。
5.17可靠性装置在规定的使用条件下,累积工作3000h,不得出现故障。
注:规定的使用条件是指起重机按正常条件工作,用户按制造厂规定的维护调整方法和周期对装置进行维护和调整。
5.18疲劳强度取力传感器在起重机中级载荷状态下的寿命不得低于5×10^3次应力循环。
6试验方法6.1试验室试验6.1.1一般规定6.1.1.1除6.1.6、6.1.7、6.1.8、6.1.9和6.1.13条试验外,每项试验后,均按6.1.2条检测动作误差,应符合5.10条规定。
具有显示功能的装置,同时检测显示误差,应符合5.9条规定。
具有预警信号的装置,同时检测预警信号,应符合5.8.1条规定。
对每个测试点均应反复试验三次。
6.1.1.2开始试验直至6.1.13条试验结束,不得调整装置设定点。
6.1.1.3如果没有特殊说明,试验顺序从6.1.2条至6.1.3条依次进行。
蓄电池供电的装置,可不做6.1.7、6.1.8和6.1.9条试验。
6.1.2动作误差试验6.1.2.1试验方法将装置组成一个完整系统,模拟起重机工况进行试验,对应每个测试点,加载使装置动作。
6.1.2.2测试点的选择对额定起重量不变的起重机,测试点为装置设定点。
对额定起重量不随工作幅度变化的起重机,测试点为最大工作幅度点。
对额定起重量随工作幅度变化的起重机,测试点应不少于起重机特性表(曲线)范围内所对应的五个点,并应尽可能包括最大、中间和最小三个点。
6.1.3振动试验振动试验过程中,装置为非通电状态。
6.1.3.1按表1规定条件进行试验。
表 1━━━━┯━━━━━━┯━━━━━━━━━━━━━━━━振动频率│ Hz加速度│振时间hHz │ g ├──────┬────┬────││上下│左右│前后────┼──────┼──────┼────┼────30 │ 4 │ 4 │ 2 │ 2━━━━┷━━━━━━┷━━━━━━┷━━━━┷━━━━6.1.3.2振动试验后,零部件不得松动、脱落、破损、导线不得断开。
6.1.4冲击试验冲击试验过程中,装置为非通电状态。
6.1.4.1按表2规定条件进行试验。
表 2━━━━━━┯━━━━━┯━━━━━━━━━━━━━━冲击加速度│冲击时间│冲击次数│├────┬────┬────g │ ms │上下│左右│前后──────┼─────┼────┼────┼────30 │<18 │ 3 │ 3 │3━━━━━━┷━━━━━┷━━━━┷━━━━┷━━━━6.1.4.2合格评定同6.1.3.2条。
6.1.5温度试验温度试验过程中,装置为非通电状态。
6.1.5.1将装置放入高温试验箱,待箱内温度达到60℃后,历时16h,取出后在30min 内完成测试。
6.1.5.2将装置放入低温试验箱,待箱内温度达到-20℃后,历时16h,取出后在30min内完成测试。
6.1.6电压波动试验交流供电时,分别施加110%及85%额定电压60min及10min;蓄电池供电时,分别施加135%及85%的额定电压60min及10min。
在试验过程中期和后期按6.1.2条检测动作误差。
6.1.7抗干扰试验在装置的供电电源上迭加一个具有下述参数的尖脉冲电压:脉冲幅值:1000V;脉冲宽度:0.1--2μs;脉冲频率:5--10Hz。
施加的时间不少于30min,在此期间装置应工作正常,检测动作误差应符合5.10条规定。
6.1.8绝缘电阻试验按GB 998第6.2.2条选择试验用兆欧表,在装置的电源进线端与外壳金属部分之间进行试验,绝缘电阻值应符合5.14条相应的规定。
6.1.9耐压试验按GB 998第6.3条进行试验,在装置的电源进线端与外壳金属部分之间施加试验电压。
电压等级按表3选择。
表 3━━━━━━━━━━━━━━━┯━━━━━━━━━━━测试部分额定电压Ue(V) │试验电压(V)───────────────┼───────────Ue≤60│ 500───────────────┼───────────60<Ue≤125│ 1000───────────────┼───────────125<Ue≤250│ 1500───────────────┼───────────250<Ue≤500│ 2000───────────────┼───────────500<Ue≤750│ 2500━━━━━━━━━━━━━━━┷━━━━━━━━━━━6.1.10湿热试验湿热试验过程中,装置为非通电状态。
试验前,装置应先通过6.1.8和6.1.9条试验。
试验方法按GB 2423.3规定进行。
试验时间48h,试品取出恢复2h后,进行6.1.8和6.1.9条规定的试验。
6.1.11防护等级试验防护等级按5.16条规定。
试验方法和合格评定按GB 4942.2第6章和第7章相应规定进行。
6.1.12过载能力试验对取力传感器施加相当于配用起重机规定的最大载荷试验值,加载三次。