7S知识培训(完美讲解总结)
7S管理培训经典版精编版

(二)整顿
合理安排物品放置的位置和方法,并进行必要的标识。
※ 目的: (1)工作场所一目了然。 (2)减少或消除找寻物品的时间。 (3)创造整齐、整洁的环境。 (4)消除积压物品(如设备的备用品等)。※主要活动: (1) 合理地决定物品的保管方法和布局。 (2) 彻底实施定点、定位存放管理。 (3)将物品、场所的有关内容(名称、数量、状态等) (4)进行标识。※实施要点: (1)三定原则:定物、定位、定量。 (2)标 识:在现场进行适当的标识。
(六)安全
安全就是消除工作中的一切不安全因素,杜绝一切不安全现象。
目的 目的是保障员工的人身安全,保证生产的连续安全正常的进行,同时减少因安全事故而带来的经济损失。主要活动 就是要求在工作中严格执行操作规程,严禁违章作业。 时刻注意安全 , 时刻注重安全。实施要点 清除隐患,排除险情,预防事故的发生。
6、为了维持整洁的工作环境,首先应采取什么措施? 答:为现场清洁制定出一套保养制度。7、当人们看到你的工作场所和设备非常肮脏时,是责怪清洁工人的失职呢?还是对你产生很坏的印象?答:当然会对我印象很坏。 8、“7S”中素养,对你自己来说,首先应着重哪点?答:首先必须了解自己的态度和习惯。
14、物品(包括原材料、辅助材料、成品、半成品、在制品、返修品、废品等)随意摆放有什么害处?答:①容易混料 ②不易识别数量和状态 ③增加无效劳动 ④增加寻找时间 ⑤浪费场地 15、若操作一台不整洁的机器,你会有什么感觉?答:不舒服,影响工作士气。16、如果对机器设备保养不讲究的人,对产品的质量会怎么样?答:对产品的质量也一定不会讲究。 17、机器设备保养不良,对其本身有什么害处?答:影响设备使用精度和使用寿命。18、工具使用后随意摆放有何坏处?答:增加找寻时间,工具易损坏和丢失。
7s管理培训资料解析

12、移动是否简洁
13、架子的后面或上面是否置放东西,
14、架子及保管箱内之物,是否有依 据所标示物品置放
15、危急品有否明确标示,灭火器是 否有定期点检
16、作业员的脚边是否有零乱的零件
17、同一的零件是否散置在几个不同 的地方
18、作业员的四周是否放有必要以上 之物〔工具、零件等〕
19、是否有在工场处处保管着零件
● 要站在新人、其他职场的人的立场来看,使得什 么东西该放在什么地方更为明确
● 要想方法使物品能马上取出访用 ● 另外,使用后要能简洁恢复到原位,没有回复或 误放时能立刻知道
〔三〕清扫的推行要领:
1、建立清扫责任区〔室内、外〕 2、开头一次全公司的大清扫 3、每个地方清洗洁净 4、调查污染源,予以杜绝或隔离,建立清扫基准,作为标准
三
1、 7S是最正确推销员〔Sales〕。被顾客赞扬为洁净洁净的工厂、对这样 的工厂有信念,乐于下订单于口碑相传,会有很多人来工厂参观学习。洁净明朗的 环境,会使大家希望到这样的厂工作 。
2、 7S是节省家〔Saving 〕。降低很多不必要的材料以及工具的铺张削 减"查找"的铺张,节省很多珍贵的时间,能降低工时,提高效率。
十一、干部在7S活动中之责任:
1、 协作公司政策,全力支持与推行7s 2、 参与外界有关7S教育训练,吸取7S技巧 3、 研读7S活动相关书籍,搜集广泛资料 4、 部门内7S之宣导及参与公司7S文宣活动 5、 规划部门内工作区域之整理、定位工作 6、 依公司之7S进度表,全面做好整理、定位、划线标示之作业 7、 帮助部属抑制7S之障碍与困难点 8、 熟读公司[7S运动竞赛实施方法]并向部属解释 9、 必要时,参与公司评分工作 10、7S评分缺点之改善和申述 11、催促所属执行定期之清扫点检 12、上班后之点名与服装仪容清查,下班前之安全巡查与确保
7S知识培训资料
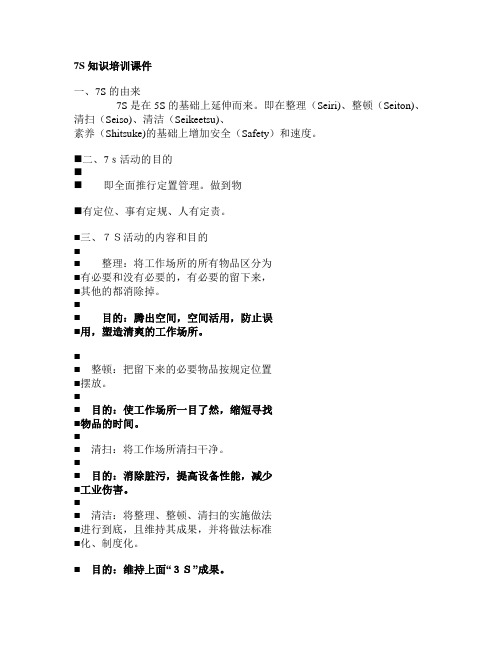
7S知识培训课件一、7S的由来7S是在5S的基础上延伸而来。
即在整理(Seiri)、整顿(Seiton)、清扫(Seiso)、清洁(Seikeetsu)、素养(Shitsuke)的基础上增加安全(Safety)和速度。
⏹二、7s活动的目的⏹⏹即全面推行定置管理。
做到物⏹有定位、事有定规、人有定责。
⏹三、7S活动的内容和目的⏹⏹整理:将工作场所的所有物品区分为⏹有必要和没有必要的,有必要的留下来,⏹其他的都消除掉。
⏹⏹目的:腾出空间,空间活用,防止误⏹用,塑造清爽的工作场所。
⏹⏹整顿:把留下来的必要物品按规定位置⏹摆放。
⏹⏹目的:使工作场所一目了然,缩短寻找⏹物品的时间。
⏹⏹清扫:将工作场所清扫干净。
⏹⏹目的:消除脏污,提高设备性能,减少⏹工业伤害。
⏹⏹清洁:将整理、整顿、清扫的实施做法⏹进行到底,且维持其成果,并将做法标准⏹化、制度化。
⏹目的:维持上面“3S”成果。
⏹素养:每位成员养成良好的习惯,并遵⏹守规则做事,培养积极主动的态度(也称⏹习惯性)⏹目的:培养有好习惯、遵守规则的员⏹工,营造团队精神。
⏹安全:人的行为安全化、物的状态安全⏹化、管理安全化。
⏹⏹目的:保证生产安全、消防安全、环境⏹安全。
⏹速度:减少和杜绝误工、待工、返工、⏹重工等浪费时间,每件事要在第一次就把⏹它做好,而且越做越好,越做越快。
⏹目的:通过以上做法达到提高效率和效⏹益的目的。
⏹⏹四、7S活动的功能:⏹1、提升生产经营单位形象⏹2、保障品质⏹3、提升效率⏹4、推行标准化⏹5、提高现场生产的安全性⏹五、开展7S活动的原则⏹1、自我管理的原则⏹2、勤俭办厂的原则⏹3、持之以恒的原则⏹六、7S活动推行的步骤⏹1、成立推行组织,制定激励措施⏹2、制定实施规划,形成书面制度⏹3、展开宣传造势,进行教育培训⏹4、全面实行7S,实行区域责任制⏹5、制定检查考核制度,并组织检查与考⏹核⏹七、7S活动的要求⏹1、从我做起⏹2、从小事做起⏹3、从现在做起⏹小知识:⏹习惯养成21天法则⏹习惯养成21天法则,是通过21天的重复练习,养成好习惯的一种方法。
7S教育管理知识培训

是
我
2、隶属(lìshǔ)设备〔滑台、任务台、料架 〕;
们
需
3、搬运设备台车、推车、拖车、堆高机;
要
4、正常运用的手工具、模治夹具;
的
东
5、正常的任务椅、板蹬;
西
6、尚有运用价值的消耗用品;
第十三页,共32页。
哪些(nǎxiē)是我们不需求 的东西
1、地板上的纸屑、灰尘、杂物、烟蒂、油污等;
2、地板上不再运用的机器设备、模治夹具等;
• 应树立清扫责任区;
• 找出污染源,予以消弭。
第十九页,共32页。
清洁(qīngjié)
◇ 维持清扫事先的现场及环境的整洁美观, 使工人觉得洁净卫生而发生无比(wúbǐ)的干劲 ;
◇ 现场时辰能坚持美观的形状; ◇ 加以维持前3S的效果、锲而不舍。
第二十页,共32页。
清洁(qīngjié)需留意的 重点
• 彻底落实前3S的各种举措;
• 充沛应用宣传活动与各部门沟通;
• 〝整理(zhěnglǐ)〞、〝整理(zhěnglǐ)〞、〝清扫 〞是举措,〝清洁〞
•
是结果;
• 树立清洁反省、奖惩第二十一制页,共度32页。,使前3S规范化。
素养(sùyǎng)
◇ 经过前4S活动,构成(gòuchéng)良 好的习气;
7S —效率保证员 提高消费效率—— 模具、夹具、工具经过整理,无需寻觅时 间/增强设备保养,机器正常运转,缺陷率降低 /7S规范作业活动(huó dòng),初学者或新人一看
就懂,快 速上岗等
第八页,共32页。
7S —平安管理员 添加平安事故—— 员工了解平安作业的要求和防范知识/整 理整理后,通道不会被占用/物品放置、搬运方 法均思索了平安要素/风险品标识(biāozhì)、警示
车间7s培训工作总结

车间7s培训工作总结
在现代工业生产中,提高生产效率和管理水平是企业发展的关键。
为了达到这
个目标,许多企业都在进行车间7s培训工作,以提高员工的管理水平和工作效率。
在这篇文章中,我们将总结一下车间7s培训工作的效果和经验,以期对其他企业
的类似工作提供一些借鉴和参考。
首先,通过车间7s培训工作,我们的员工对于整个生产流程有了更清晰的认
识和了解。
在培训中,我们重点强调了“整理(Seiri)”和“整顿(Seiton)”这
两个环节,使得员工对于工作场所的整齐和物品摆放有了更为深刻的认识。
这些改变不仅使得工作环境更加整洁,也提高了员工对于工作的效率和质量的要求。
其次,通过培训,我们的员工对于“标准化(Seiketsu)”和“持续改进(Shitsuke)”有了更深入的理解。
在培训中,我们强调了持续改进的重要性,并
且鼓励员工提出自己的改进建议。
这样的做法不仅激发了员工的积极性,也为企业提供了更多的改进方向。
最后,通过车间7s培训工作,我们的员工对于“清扫(Seiso)”和“安全(Anzen)”有了更为严格的要求。
在培训中,我们强调了清洁和安全对于生产工
作的重要性,并且着重培养了员工的安全意识。
这些改变不仅提高了工作环境的整洁度和安全性,也减少了工作中的意外事故。
总的来说,通过车间7s培训工作,我们的员工在管理水平和工作效率上都取
得了显著的提高。
我们相信,通过不断的培训和改进,我们的企业将会在未来取得更加辉煌的成绩。
希望我们的经验能够对其他企业的类似工作提供一些借鉴和参考。
7S知识培训

21
一. 7S基本概念
1.8 推行7S旳旳作用及目旳
推行7S管理旳作用 a) 提供一种舒适旳工作环境; b) 提供一种安全旳作业场合; c) 塑造一种企业旳优良形象,提升员工工作热情
和敬业精神; d) 提升和稳定产品旳质量水平; e) 提升工作效率降低消耗; f) 增长设备旳使用寿命降低维修费用。 G) 降低各種風險事故旳發生,提升相關成本旳使用
價值. 22
一. 7S基本概念
1.8.2 推行7S管理旳目旳
a) 员工作业犯错机会降低,不良品下降,品质上升; b) 提升土气; c) 防止不必要旳等待和查找,提升了工作效率; d) 资源得以合理配置和使用,降低挥霍; e) 整齐旳作业环境给客户留下深刻印象,提升企业整
1
7S知識培訓綱要
--------发明一种舒适、整齐旳工作环境, 是每个企业管理者旳期望 .也是目视管
理之关键.
現場管理 從5S做起 ! 做好7S 同樣從5S做起 !
2
總述
7S基本概念 7S推行技巧 结束语
3
一. 7S基本概念
1.1 我们有下列“症状”吗?
a) 急等要旳东西找不到,心里尤其烦燥 b) 桌面上摆得零零乱乱,以及办公室空间有一种压抑感 c) 没有用旳东西堆了诸多,处理掉又舍不得,不处理又占用空间 d) 工作台面上有一大堆东西,理不清头绪 e) 每次找一件东西,都要打开全部旳抽屉箱柜狂翻 f) 环境脏乱,使得上班人员情绪不佳 g) 制定好旳计划,事务一忙就“延误”了 h) 材料、成品仓库堆放混乱,帐、物不符,堆放长久不用旳物品,占
2.2.4.1 落实整顿工作,根据“整顿”旳要点进行 2.2.4.2 决定放置场合 2.2.4.3 决定放置措施和放置量旳大小. 决定放置區域定位劃線旳措施 . 2.2.4.5決定每個放置區物品之責任管理者。
作业现场安全标准化(7S)基础知识培训

某些部门可以有特殊的规定
人 机 料 法 环
整理的延伸
电子资料 不必要的流程 消极的心态、理念 过长的会议时间
……on)
定义:必需品依规定定位、定方法摆放整 齐,明确标示。 目的:工作井然有序,不浪费时间寻找物 品。
10秒找出 所需工具
物料寻找百态图
所需物品没 有了 急忙订货
效用
维护方法
人或物挨碰触摸机 比较容易标识和 在纸张上过一层胶,防 会少的地方 方便随时标识 止挨碰角落或清洁造成 损害 适用场所区域的标 防潮、防水、易 阳光的照射会使胶质硬 识 于清洁 化脆弱、变色,尽量避 免阳光照射 适用于机械设备的 不容易脱落,时 定期翻新保养 危险警告和一些 刻保持体形作用, “小心有电”等位 易于清洁 置 用于一些化学物品 防火或腐蚀物等 保持清洁 或防火物(如:逃 离火警的方向指示 牌等)
塑胶
油漆
别类
整顿三定
定点
定类 定量
•明确具体的放置位置 •上面?下面?左边?右边?
•明确区分物品的所属种类
•使用颜色进行区分管理 •规定合适的数量
•容器、箱、桶的定量要明确
“7S”的定义与目的
3、清扫 (S eiso)
定义:清除现场内的污物,并防止故障的 发生。 目的:保持现场干净明亮,设备和工具使 用状态良好。
设备点检效率化
大扫除 • •作业要点、步骤、方法明确
防故障 求效益
•正常、异常容易判断
•时间、周期明确(看板等)
现场设备点检文件
设备点检作业指导书 设备点检定位盒路线指引图
点检路线指引
测温点检位置目视化
3.1、在设备上做 标识: 3.1.1颜色:用 红环白芯的图形 表示 3.1.2尺寸:外径 35mm内径10mm 3.2、点检位置编号标 识: 3.2.1点检位置标识用 标签打码机打印 (规格20*60mm), 打印字体用黑体,字 号。 3.2.1深颜色设备用黄 色标识,浅色设备用 绿色标识; 3.2.3粘贴在点检位置 下方
7S管理培训总结

7S管理培训总结通过人力资源部对7s的培训,现在对它有了一定的了解,总结如下:实施“7S”管理,能很好地展现企业文化理念,创建舒适、安全的工作环境,提升企业的整体形象,在规范化管理、员工素养、文明办公和安全节约等方面达到现代企业管理的要求。
最近,公司深入开展“7S”管理活动,组织举行培训、学习、贯彻,让我们对“7S”管理的基本内涵有了更深刻的理解。
“7S”(整理、整顿、清扫、清洁、素养、安全、节约)管理方式,保证公司优雅的办公环境,良好的工作秩序和严明的工作纪律,同时也提高工作效率,减少浪费节约物料成本和时间成本。
“7S”管理方式,正是企业文化的充分体现,是企业文化取得优秀成果和实现企业经营目标的重要手段,是弘扬企业文化“走在行业前面、争创一流企业”,使金州又好又快发展的有力保障。
实施“7S”管理,必须要有全体员工的激情参与,对照标准找差距,分析原因定措施,落实整改见成效,合理配置和使用资源,使生产、办公区域达到整洁、实用、规范的要求,减少浪费,减少物品取放查找时间,提高工作效率。
我认为“7S”管理中的“素养”是整个“7S”活动的核心和精髓,这与公司的管理规定、行为规范密不可分,与人员的素养和严格遵守规章制度的习惯和作风、主动积极的精神密不可分。
没有人员素质的提高,“7S”各项活动就不能开展,就是开展了也坚持不了。
因此,我们应努力提高自身素养,规范自身行为,在平时的工作中,提高文明标准,增强团队意识,养成按规定行事的良好工作习惯,做到“四懂、四会”,达到“7S”管理要求。
节约是对整个“7S”管理过程的补充和指导,我们应积极响应国家建设资源节约型社会的要求,在企业中秉持勤俭节约的原则,以主人翁的心态对待企业的资源,厉行节约,降本增效。
通过对“7S”管理的学习培训,我对“7S”管理有了一个清晰、系统的认识,增强了开展工作的信心,相信通过我们全体员工的努力,一定会达到现场整洁有序、工作高效顺畅的目标,促进企业管理水平上台阶、上水平。
- 1、下载文档前请自行甄别文档内容的完整性,平台不提供额外的编辑、内容补充、找答案等附加服务。
- 2、"仅部分预览"的文档,不可在线预览部分如存在完整性等问题,可反馈申请退款(可完整预览的文档不适用该条件!)。
- 3、如文档侵犯您的权益,请联系客服反馈,我们会尽快为您处理(人工客服工作时间:9:00-18:30)。
二
整理
1、整理步骤
整理
区分需要与不需要的事、物,再对不需要的事、物加以处理。
现场检查 制定基准 现场的改善
分类
判断“要” 与“不要”
归类
处理
2、整理目的
减少空间
减少物品 减少错误
• 腾出空间,改善和增加作业面积
• 现场无杂物,人行道通畅,提高工作效率
• 防止误用、误送。
心情舒畅
• 塑造清爽的工作场所。
• 不同的人去做,结果是一样的。
※ 以下数字范围1~40,请找出其中缺少的2个数字
※ 如果这样再找一遍能够快多少?
3、整理浪费
寻找浪费 等待浪费 重复浪费 变更浪费 延迟浪费
• 没有标识导致寻找时间的浪费
• 摆放不合理导致停止和等待的浪费。
• 认为没有而多余购买的浪费。
• 现场混乱导致计划变更而产生的浪费。
3、7S作用
故事一: 企业形象就 是竞争力
4、7S实施原则
全员 参与
持续 改善
持之 以恒
规范 高效
自己 动手
5、7S误区
7S管理误区: 把7S管理当做大扫除。 例:
1、认为7S管理太简单,芝麻小事,没有什么意义。 2、工作问题点很多,与7S无关。 3、现在比以前已经好很多了,有必要再搞吗? 4、工作上已经够忙的了,哪有时间再做7S管理。 5、7S管理这么简单,却要劳师动众,有必要吗? 6、就是我想做好,别人呢? 7、做好了有什么好处? 8、到目前为止没有推行7S管理,企业不照样在发展吗? 9、不做7S管理不是照样能生产吗?
• 现场混乱导致交期延迟而产生的浪费。
场地浪费
• 没有定点、定量导致场地的浪费。
4、三区域都要明确,且一目了 然
• 所有物品原则上都要明确其放置方法:竖放、 横放、斜置、吊放、钩放等。
• 标识是使现场一目了然的前提。好的标识是指: 任何人都能十分清楚任何一堆物品的名称、规 格等参数。
5、三定原则
定点
定容 定量
• 明确具体的放置位置。
故事二: 肓人家庭
• 明确使用容器的大小、材质。
• 规定合适的数量。
6、注意事项
一般公司的画线标准:
序号 1 2 3 4 5 项目 主通道 厂区道牙线 大型车间、仓库 辅通道 区域线 说明 主要通道 防撞提示 室内主要通道 辅助通道 固定区域 门活动的范围之内禁止堆放 主要指现场物品摆放定位 厂区内所有消防器材附近禁止堆放 7 消防设施 厂区内所有灭火器材附近禁止堆放 8 9 警示区 货架、办公室物 品定位 存在安全隐患的部位 台面物品定位及柜内物品区域线 线宽 12cm 12cm 12cm 10cm 5cm 2cm 5cm 以消防门 推开基准 5cm 5cm 1.5cm 颜色 黄色 黄黑相间色 黄色 黄色 黄色 黄色 黄色 黄色 黄色 黄黑间隔色 黄色 示范
资金的浪费
移动浪费
人力浪费
管理浪费
• 管理非必需品的场地和人力浪费。
• 库存管理及盘点时间的浪费。
5、整理注意事项
6、整理举例 明确场所的基准: 不用的东西--------------处理掉 不太常用的东西----------放在较远的地方 偶尔使用的东西----------安排专人保管 经常使用的东西----------放在身旁附近 拿来拿去花时间的东西----只留下必要的数量
2、7S内容
整理 整顿 清扫 清洁 安全 节约 素养 区分必需品和非必需品,现场不放置非必需品 物品固定位置并标识,将寻找物品的时间为降为零 清扫到没有赃污的干净状态,注重细微之处 将整理、整顿、清扫进行到底,并制度化
消除隐患,保障员工的人身安全和生产正常
减少浪费、降低成本 遵守规定,积极向上,文明与团队精神
整顿
整顿
是把需要的事、物加以定量和定位。
通过上一步整理后,对生产现场需要的留下的物 品,进行科学合理的布置和摆放,以便最快速地取 得所要之物,在最简捷、有效的规章制度、流程下 完成工作。 生产现场物品的合理摆放使得工作场所一目了然 ,整齐的工作环境有利于提高工作效率,提高产品 质量,保障生产安全。
3、整理作用
削除浪费
减少差错
• 削除资源的浪费,有利于减少库存,节约资金。 • 削除管理上的混放、混料等差错事故,有效地防 止误用、误送。 • 有效地利用空间、可以使现场无杂物、通道顺畅, 增大作业空间面积。 • 对物料、物品进行分类、有序的放置,减少寻找 时间,提高工作效率。
空间利用 减少寻找时间
7S知识培训
目录:
一 二 三 四
基本知识 整理
六
七 八 九 十
素养
安全 节约
整顿
清扫
7S工具
7S制度
五
清洁
一
基本知识
一
基本知识
1、7S定义
7S管理是指生产现场中对人员、机 器、材料、方法等生产要素进行有 效管理的活动。 它提出的目标简单、明确,就是要 为员工创造一个干净、整洁、舒适、 科学合理的工作场所和空间环境。 它的最终目的是提升人的素质,为 企业造就一个高素质的优秀群体。
6、整理举例
保管场所确定:
使用频率 不用 少用 全年一次也未使用 平均2个月~1年用1次 处理方法 废弃 特别处理 分类管理 集中场所
(工具室、仓库)
建议场所 待处理区
普通
常用
1~2个月用1次或以上
1周使用数次
置于车间内
工作区内
各摆放区
如机台旁
1日使用数次
每小时都使用
随手可得
流水线旁
个人工具箱
三
2、整理目的
场所明确 明亮整洁
• 工作场所清楚明了。
• 工作环境明亮、整洁。
减少库存 心情舒畅
• 消除过多的积压物品。
• 工作秩序井然
3、整理作用
提高效率
• 提高工作效率,减少浪费和非必须的作业。
减少寻找
异常曝光
• 将寻找时间减少为零。
• 出现异常情况能马上发现。
现场有序
有执行力
• 创造一目了然的现场,即使非本岗位的人员也能 明白要求和做法。
5、7S误区
走出7S管理误区的要点:
1、理解7S管理的精髓。 2、开始从上至下施加“压力”,以后全面开花。 3、把现在无用的多余物品放在现场是一种浪费。 4、在不影响生产的情况下,原材料、半成品、在制品越少越好。 5、要承认“问题永远存在”。 6、不断改善是提升管理的基础,不要轻视“小打小闹”,由量变到质变。 7、培养员工务实的工作作风,少谈精神,少减口号,注重实际效果。
提高产品质量 降低管理难度
• 减少碰撞,保障生产安全,提高产品质量。
• 有序的工作场所更便于管理,大大降低管理难度。 • 使员工心情舒畅,工作热情高涨。
心情舒畅
4、整理浪费
空间的浪费
• 场地老是不够用,感觉越来越窄 • 零件或产品因过期而不能使用,造成资金的 浪费。 • 场所狭窄,物品不断移动的工时浪费
2、7S内容
整理 整顿 清扫 清洁 安全 节约 素养 区分必需品和非必需品,现场不放置非必需品 物品固定位置并标识,将寻找物品的时间为降为零 清扫到没有赃污的干净状态,注重细微之处 将整理、整顿、清扫进行到底,并制度化
消除隐患,保障员工的人身安全和生产正常
减少浪费、降低成本 遵守规定,积极向上,文明与团队精神