焊管常用探伤方法及技术
管道焊口探伤、管道防腐检查及合格判定方法
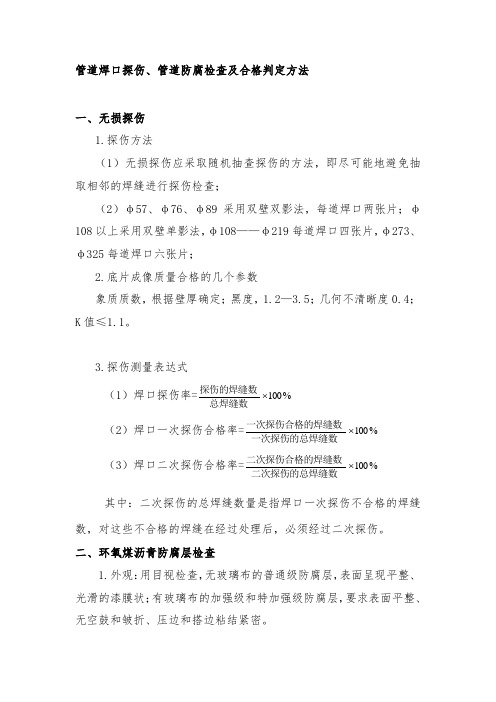
管道焊口探伤、管道防腐检查及合格判定方法一、无损探伤1.探伤方法(1)无损探伤应采取随机抽查探伤的方法,即尽可能地避免抽取相邻的焊缝进行探伤检查;(2)φ57、φ76、φ89采用双壁双影法,每道焊口两张片;φ108以上采用双壁单影法,φ108——φ219每道焊口四张片,φ273、φ325每道焊口六张片;2.底片成像质量合格的几个参数象质质数,根据壁厚确定;黑度,1.2—3.5;几何不清晰度0.4;K值≤1.1。
3.探伤测量表达式探伤的焊缝数(1)焊口探伤率=%100⨯总焊缝数一次探伤合格的焊缝数(2)焊口一次探伤合格率=%⨯100一次探伤的总焊缝数二次探伤合格的焊缝数(3)焊口二次探伤合格率=%⨯100二次探伤的总焊缝数其中:二次探伤的总焊缝数量是指焊口一次探伤不合格的焊缝数,对这些不合格的焊缝在经过处理后,必须经过二次探伤。
二、环氧煤沥青防腐层检查1.外观:用目视检查,无玻璃布的普通级防腐层,表面呈现平整、光滑的漆膜状;有玻璃布的加强级和特加强级防腐层,要求表面平整、无空鼓和皱折、压边和搭边粘结紧密。
2.厚度:用磁性测厚仪抽查,测管两端和中间共3个截面,每个截面测上、下、左、右共4个点,厚度达到加强级≥0.6 mm、特加强级≥0.8 mm要求者为合格;若不合格,再在该组内随机抽2根,如其中仍有不合格者,则全部为不合格。
3.粘结力:加强级和特加强级防腐层:用锋利刀刃垂直划透防腐层,形成边长约100mm、夹角约45o-60o的切口,从切口尖端撕开玻璃布。
符合下列条件之一可判定防腐层粘结力合格:(1)实干后的防腐层,撕开面积约50cm2,撕开处应不露铁,底漆与面漆普遍粘结;(2)固化后的防腐层,只能撕裂,且破坏处不露铁,底漆与面漆普遍粘结。
防腐检查每根随机抽查1个点,符合上述要求者为合格;若不合格,再在该组内随机抽2根,如其中仍有不合格者,则全部为不合格。
4.防腐层的绝缘性:用电火花检漏仪进行检测,以无漏点为合格。
管道焊口无损探伤

管道焊口无损探伤一、管道焊缝应按照设计要求的检验方法和数量进行无损探险伤二、管口焊接含量取定可参考下表:序号项目10米直管焊口含量(个)10米管件焊口含量(个)单根管取定长度(m)碳钢、不锈钢、铬钼钢、有缝低温钢管、≤DN2501.27 20.6 6碳钢、不锈钢、铬钼钢、有缝低温钢管、≥DN3001 20.6 8碳钢板卷管、DN200~600 1.56 20.6 6.4碳钢板卷管、DN700~900 1.96 20.6 6.4碳钢板卷管、DN1000~1400 2.48 20.6 4.8碳钢板卷管、DN1600~3000 2.38 20.6 4.8螺旋卷管0.67 20.6 12三、无损探伤的拍片张数按设计规定计算的探伤焊缝总长度除以定额取定的胶片有效长度计算。
定额取定的胶片有效长度为250mm,设若计无明确规定,可参照下表计算,结算时按现场实际拍片张数计算。
管道焊口透视拍片张数表序号管外径底片规格张数序号管外径底片规格张数1 ≤89 1502 12 ≤1020 300 132 ≤133 1504 13 ≤1220 300 153 ≤159 2404 14 ≤1420 300 184 ≤273 300 4 15 ≤1620 300 205 ≤377 300 5 16 ≤1820 300 236 ≤478 300 6 17 ≤2020 300 257 ≤529 300 7 18 ≤2220 300 288 ≤630 300 8 19 ≤2420 300 309 ≤720 300 9 20 ≤2620 300 3310 ≤820 300 10 21 ≤2820 300 3511 ≤920 300 12 22 ≤3020 300 38四:管道探伤计算方法:每10米管道含有1.27个焊缝,X射线张数=1.27×延长米数×一圈管道所需的张数×0.2。
钢管对接焊缝探伤方法
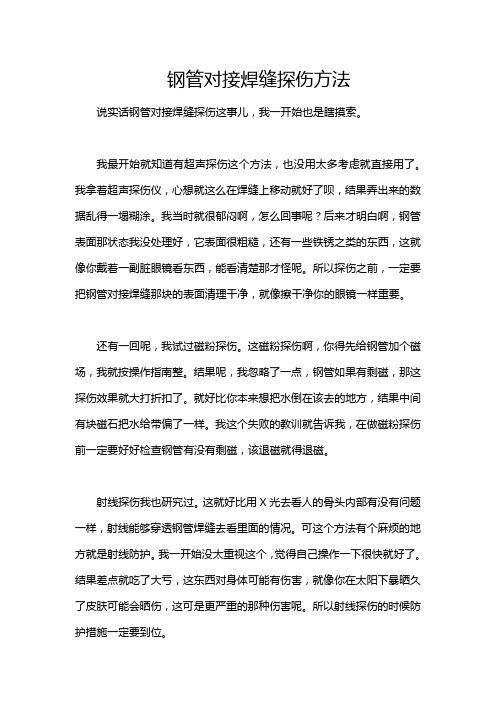
钢管对接焊缝探伤方法说实话钢管对接焊缝探伤这事儿,我一开始也是瞎摸索。
我最开始就知道有超声探伤这个方法,也没用太多考虑就直接用了。
我拿着超声探伤仪,心想就这么在焊缝上移动就好了呗,结果弄出来的数据乱得一塌糊涂。
我当时就很郁闷啊,怎么回事呢?后来才明白啊,钢管表面那状态我没处理好,它表面很粗糙,还有一些铁锈之类的东西,这就像你戴着一副脏眼镜看东西,能看清楚那才怪呢。
所以探伤之前,一定要把钢管对接焊缝那块的表面清理干净,就像擦干净你的眼镜一样重要。
还有一回呢,我试过磁粉探伤。
这磁粉探伤啊,你得先给钢管加个磁场,我就按操作指南整。
结果呢,我忽略了一点,钢管如果有剩磁,那这探伤效果就大打折扣了。
就好比你本来想把水倒在该去的地方,结果中间有块磁石把水给带偏了一样。
我这个失败的教训就告诉我,在做磁粉探伤前一定要好好检查钢管有没有剩磁,该退磁就得退磁。
射线探伤我也研究过。
这就好比用X光去看人的骨头内部有没有问题一样,射线能够穿透钢管焊缝去看里面的情况。
可这个方法有个麻烦的地方就是射线防护。
我一开始没太重视这个,觉得自己操作一下很快就好了。
结果差点就吃了大亏,这东西对身体可能有伤害,就像你在太阳下暴晒久了皮肤可能会晒伤,这可是更严重的那种伤害呢。
所以射线探伤的时候防护措施一定要到位。
后来我也知道另外一个方法叫着色探伤。
这个就简单一点,就像画画一样给焊缝涂上一层含有颜料的渗透剂,等一会儿渗透进焊缝缺陷里后,再把表面多余的擦去,然后涂上显像剂,有缺陷的地方颜料就会呈现出来,就像你把脏东西藏在布里头,现在用东西把脏东西吸出来显露在外面一样。
不过这个方法呢,检测的深度有限,只能发现比较表面的缺陷。
总之呢,不同的探伤方法各有利弊。
像那种不是很明显的内部缺陷,超声探伤和射线探伤可能更合适。
如果是比较简单看看表面可能有啥问题,着色探伤就可以了。
而且操作这些方法之前一定要先好好检查钢管的状态,把好基础这一关,探伤结果才更准呢。
焊缝探伤检测方法

焊缝探伤检测方法
焊缝探伤检测是在焊接过程中对焊缝进行质量控制的重要方法。
以下是一些常用的焊缝探伤检测方法:
1. 超声波探伤检测:通过将超声波传入焊缝中,利用超声波在不同介质中传播速度的变化来检测焊缝内部的缺陷和不良结构。
这种方法非常灵敏,并且可以在不破坏焊缝的情况下进行检测。
2. 射线探伤检测:利用射线(通常是X射线或γ射线)在焊
缝中的吸收和散射来检测焊缝内的缺陷。
这种方法可以探测到非常小的缺陷,并且可以用于检测深部焊缝。
3. 磁粉探伤检测:将磁性材料(如铁粉)喷洒在焊缝表面,通过施加磁场来检测焊缝中的裂纹和断裂。
这种方法适用于检测表面缺陷,并且可以快速、经济地进行。
4. 渗透探伤检测:将渗透剂涂覆在焊缝表面,待其渗透入表面裂纹或孔洞中,随后用显色剂着色,可看到颜色变化,以检测表面缺陷。
这些方法各有优势和适用范围,具体选择何种方法应根据焊缝的要求和实际情况来决定。
在进行焊缝探伤检测时,应根据操作规程严格执行,确保检测结果的准确性和可靠性。
焊接探伤检测有几种方法
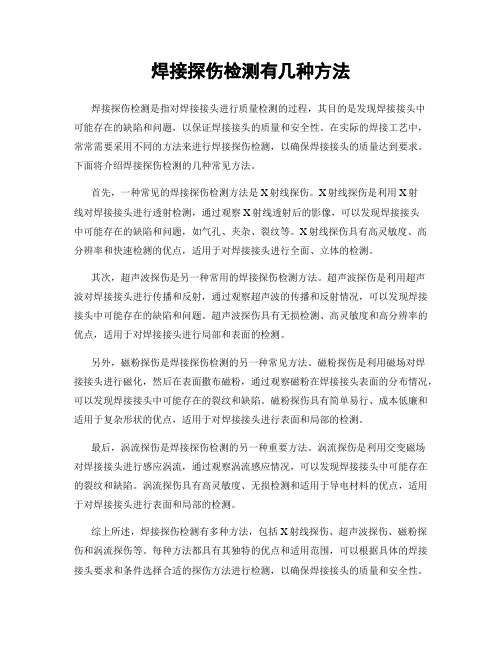
焊接探伤检测有几种方法焊接探伤检测是指对焊接接头进行质量检测的过程,其目的是发现焊接接头中可能存在的缺陷和问题,以保证焊接接头的质量和安全性。
在实际的焊接工艺中,常常需要采用不同的方法来进行焊接探伤检测,以确保焊接接头的质量达到要求。
下面将介绍焊接探伤检测的几种常见方法。
首先,一种常见的焊接探伤检测方法是X射线探伤。
X射线探伤是利用X射线对焊接接头进行透射检测,通过观察X射线透射后的影像,可以发现焊接接头中可能存在的缺陷和问题,如气孔、夹杂、裂纹等。
X射线探伤具有高灵敏度、高分辨率和快速检测的优点,适用于对焊接接头进行全面、立体的检测。
其次,超声波探伤是另一种常用的焊接探伤检测方法。
超声波探伤是利用超声波对焊接接头进行传播和反射,通过观察超声波的传播和反射情况,可以发现焊接接头中可能存在的缺陷和问题。
超声波探伤具有无损检测、高灵敏度和高分辨率的优点,适用于对焊接接头进行局部和表面的检测。
另外,磁粉探伤是焊接探伤检测的另一种常见方法。
磁粉探伤是利用磁场对焊接接头进行磁化,然后在表面撒布磁粉,通过观察磁粉在焊接接头表面的分布情况,可以发现焊接接头中可能存在的裂纹和缺陷。
磁粉探伤具有简单易行、成本低廉和适用于复杂形状的优点,适用于对焊接接头进行表面和局部的检测。
最后,涡流探伤是焊接探伤检测的另一种重要方法。
涡流探伤是利用交变磁场对焊接接头进行感应涡流,通过观察涡流感应情况,可以发现焊接接头中可能存在的裂纹和缺陷。
涡流探伤具有高灵敏度、无损检测和适用于导电材料的优点,适用于对焊接接头进行表面和局部的检测。
综上所述,焊接探伤检测有多种方法,包括X射线探伤、超声波探伤、磁粉探伤和涡流探伤等。
每种方法都具有其独特的优点和适用范围,可以根据具体的焊接接头要求和条件选择合适的探伤方法进行检测,以确保焊接接头的质量和安全性。
焊缝探伤检测方法

焊缝探伤检测方法焊接是制造业中常见的连接工艺,而焊缝的质量直接影响着焊接件的性能和安全性。
因此,对焊缝进行探伤检测是非常重要的。
本文将介绍几种常见的焊缝探伤检测方法,以供参考。
首先,常见的焊缝探伤检测方法之一是磁粉探伤。
这种方法利用磁粉在外加磁场下的磁性特性,通过磁粉在缺陷处的聚集来发现焊缝中的裂纹、夹杂等缺陷。
这种方法简单易行,对表面缺陷的检测效果较好,但对于深层缺陷的检测能力有限。
其次,超声波探伤是另一种常用的焊缝探伤方法。
超声波探伤利用超声波在材料中的传播和反射特性来检测焊缝中的缺陷。
这种方法可以对焊缝进行全面、非破坏性的检测,对于各种形式的缺陷都有较好的检测能力。
但是,超声波探伤对操作人员的技术要求较高,且对焊缝的几何形状和材料性质有一定的限制。
另外,涡流探伤也是一种常见的焊缝探伤方法。
涡流探伤利用交变磁场在导电材料中产生涡流的原理,通过检测涡流的变化来发现焊缝中的缺陷。
这种方法对于表面和近表面的缺陷有较好的检测能力,对于导电性好的材料也有较好的适用性。
但是,对于非导电材料和厚度较大的材料,涡流探伤的效果就会大打折扣。
最后,X射线探伤也是一种常用的焊缝探伤方法。
X射线探伤利用X射线在材料中的透射和吸收特性来检测焊缝中的缺陷。
这种方法可以对焊缝进行全面、深层的检测,对于各种形式的缺陷都有较好的检测能力。
但是,X射线探伤设备价格昂贵,操作复杂,对操作人员的技术要求也很高。
综上所述,不同的焊缝探伤方法各有优劣。
在实际应用中,需要根据具体的焊接工艺、焊缝形式和材料性质选择合适的探伤方法。
同时,对于复杂的焊缝结构,也可以采用多种探伤方法相结合的方式,以提高检测的准确性和全面性。
希望本文介绍的焊缝探伤检测方法能对相关人员有所帮助。
直缝焊管检测要求一览表

直缝焊管检测要求一览表1. 引言本文档旨在总结和归纳直缝焊管的检测要求。
直缝焊管是一种常见的管道材料,其质量的好坏关系到管道系统的安全和可靠性。
因此,对直缝焊管进行全面、准确的检测是非常重要的。
2. 检测方法直缝焊管的检测可以采用多种方法,下面列举了常用的检测方法及其要求:- 磁粉探伤检测:通过对焊缝表面施加磁场和磁粉,检测焊缝中可能存在的裂纹和缺陷。
要求检测仪器的操作准确、灵敏度高,以确保能够准确地发现和评估焊缝的缺陷。
- 超声波探伤检测:利用超声波的传播和反射特性,检测焊缝中的缺陷。
要求检测仪器的频率范围、功率输出和接收灵敏度等参数符合标准要求,以确保能够准确地检测焊缝中的缺陷。
- 射线探伤检测:利用射线(如X射线或γ射线)的穿透能力,检测焊缝中的裂纹、夹杂物等缺陷。
要求检测仪器的辐射源和检测器的性能满足相应的标准,以确保能够准确地检测焊缝中的缺陷。
- 涡流检测:通过变化的电磁场和感应电流,检测焊缝中的裂纹和夹杂物等缺陷。
要求检测仪器的灵敏度和稳定性良好,以确保能够准确地检测焊缝中的缺陷。
3. 检测要求对直缝焊管的检测要求如下:- 检测方法和仪器的选择应符合相关标准和规范。
- 检测人员应具备相应的专业知识和技能,能够正确操作检测仪器,解读和评估检测结果。
- 检测过程中,应保证焊缝表面的清洁和光滑,以减少误判。
- 检测结果应详细记录,包括检测方法、检测仪器、检测参数、检测结果等信息。
- 对于发现的缺陷,应及时采取相应措施,修补或更换不合格的焊管。
- 检测完成后,应出具检测报告,详细说明检测过程和结果,以供参考和备案。
4. 结论本文档总结了直缝焊管的检测要求,包括常用的检测方法和相关要求。
通过严格按照检测要求进行检测,可以确保直缝焊管的质量和安全性,提高管道系统的可靠性和稳定性。
焊缝探伤检测方法
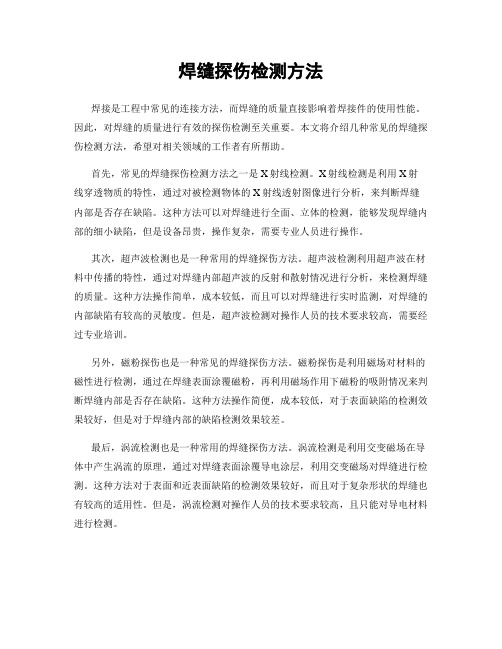
焊缝探伤检测方法焊接是工程中常见的连接方法,而焊缝的质量直接影响着焊接件的使用性能。
因此,对焊缝的质量进行有效的探伤检测至关重要。
本文将介绍几种常见的焊缝探伤检测方法,希望对相关领域的工作者有所帮助。
首先,常见的焊缝探伤检测方法之一是X射线检测。
X射线检测是利用X射线穿透物质的特性,通过对被检测物体的X射线透射图像进行分析,来判断焊缝内部是否存在缺陷。
这种方法可以对焊缝进行全面、立体的检测,能够发现焊缝内部的细小缺陷,但是设备昂贵,操作复杂,需要专业人员进行操作。
其次,超声波检测也是一种常用的焊缝探伤方法。
超声波检测利用超声波在材料中传播的特性,通过对焊缝内部超声波的反射和散射情况进行分析,来检测焊缝的质量。
这种方法操作简单,成本较低,而且可以对焊缝进行实时监测,对焊缝的内部缺陷有较高的灵敏度。
但是,超声波检测对操作人员的技术要求较高,需要经过专业培训。
另外,磁粉探伤也是一种常见的焊缝探伤方法。
磁粉探伤是利用磁场对材料的磁性进行检测,通过在焊缝表面涂覆磁粉,再利用磁场作用下磁粉的吸附情况来判断焊缝内部是否存在缺陷。
这种方法操作简便,成本较低,对于表面缺陷的检测效果较好,但是对于焊缝内部的缺陷检测效果较差。
最后,涡流检测也是一种常用的焊缝探伤方法。
涡流检测是利用交变磁场在导体中产生涡流的原理,通过对焊缝表面涂覆导电涂层,利用交变磁场对焊缝进行检测。
这种方法对于表面和近表面缺陷的检测效果较好,而且对于复杂形状的焊缝也有较高的适用性。
但是,涡流检测对操作人员的技术要求较高,且只能对导电材料进行检测。
综上所述,针对不同的焊缝情况,可以选择适合的探伤方法进行检测。
在实际工程中,可以根据具体情况综合运用多种探伤方法,以确保焊缝质量的可靠性和安全性。
希望本文介绍的焊缝探伤检测方法能够对相关工作者有所帮助。
- 1、下载文档前请自行甄别文档内容的完整性,平台不提供额外的编辑、内容补充、找答案等附加服务。
- 2、"仅部分预览"的文档,不可在线预览部分如存在完整性等问题,可反馈申请退款(可完整预览的文档不适用该条件!)。
- 3、如文档侵犯您的权益,请联系客服反馈,我们会尽快为您处理(人工客服工作时间:9:00-18:30)。
焊管常用探伤方法及技术曹雷(阜新华通管道有限公司,辽宁阜新123000)摘要:介绍了焊管常用的3种探伤方法(漏磁探伤、涡流探伤和超声波探伤)及技术。
分析了3种探伤方法的优缺点:漏磁探伤灵敏度高,能很好地分辨出焊管内外壁缺陷,但长管体、大壁厚管在漏磁探伤后需做消磁处理;涡流探伤检测速度快,但受趋肤效应的限制,很难发现工件深处的缺陷;超声波探伤穿透能力强、缺陷定位准确、成本低、速度快,但探伤操作需经耦合,在北方严冬环境下耦合时焊管易冻结,给探伤作业带来不便。
关键词:焊管检测;漏磁探伤;涡流探伤;超声波探伤中图分类号:TG115.28;TG441.7%%文献标志码:B%文章编号:1001-2311(2012)04-0072-03Commonly -used NDT Methods and Techniques for Weld PipesCao Lei(Fuxin Huatong Piping Co.,Ltd.,Fuxin 123000,China )Abstract :Described in the paper are the three commonly -used NDT methods and techniques for weld pipe flaw inspection ,i.e.,the MFL detection ,the eddy -current detection and the ultrasonic detection.Also analyzed are the advantages and disadvantages of these methods.The MFL method features high sensitivity which ensures satisfactory identification of both outer and inner flaws of the pipe ,but in case of long large -sized heavy -wall pipe ,demagnetization is necessary to be carried out upon ending of the detection.As for the eddy -current method ,although the detection speed is rather high ,it is so difficult to find out any flaw located deep in the workpiece due to the Kelvin skin effect.And speaking of the ultrasonic method ,the advantages are high penetrating force ,high flaw -positioning accuracy ,low operation cost ,and high detection velocity ,but medium coupling is needed for the detection ,which may cause ,in winter ,the trouble of freezing of the pipe ,particularly in hi -latitude areas ,thus make it rather difficult to keep the detection operation going smoothly.Key words :Weld pipe detection ;Magnetic flux leakage (MFL )detection ;Eddy -current detection ;Ul -trasonic detection在焊管的制造和使用过程中,为保证焊缝质量而进行的无损检测是尤为重要的。
焊管常用的无损检测方法有:适用于距焊管表面5mm 以上的离线全管体漏磁探伤、涡流探伤和超声波探伤;验证距焊管表面5mm 以上焊接质量的在线漏磁探伤和涡流探伤;适用于厚壁焊管的离线焊缝全管体超声波探伤;验证厚壁焊管焊接质量的超声波探伤。
本文将结合生产经验,对焊管常用的探伤方法及技术作简要介绍,并对其优缺点进行分析比较。
1焊管全管体漏磁探伤漏磁探伤是指铁磁材料被磁化后,其表面和近表面缺陷在材料表面形成漏磁场,通过检测漏磁场发现缺陷的无损检测技术。
漏磁探伤对管材的表面状态要求不高,检出深度较大,在国外的焊管检测中被大量使用,国内特别是石油用焊管的检测也已普遍采用。
在生产检测中,曾出现过漏磁探伤检测不出焊管透壁大孔洞的现象,除了管理及人员因素外,这与仪器、探头性能及缺陷尺寸形状等都有关系。
笔者根据实践经验,总结出影响焊管全管体漏磁探伤精度的主要因素有以下几点。
曹雷(1983-),男,工程师,从事石油钢管生产工艺和石油天然气管道管件的研究工作。
STEEL PIPE Aug .2012,Vol.41,No.4钢管2012年8月第41卷第4期检测技术72(1)磁化强度。
当磁化强度较低时,漏磁场偏小,且增加缓慢;当磁感应强度达到饱和值的80%左右时,缺陷漏磁场的峰值随着磁化强度的增加会迅速增大,但当铁磁材料进入磁饱和状态时,外界磁化强度的增大对缺陷磁场强度的影响不大。
因此,磁路的设计应尽可能使被测材料达到近饱和磁化状态。
(2)缺陷的方向、位置和尺寸。
缺陷的方向对漏磁检测精度的影响很大,当缺陷主平面与磁化磁场方向垂直时,产生的漏磁场最强。
同样的缺陷位于管道表面时漏磁场最大,且随着埋藏深度的增大而逐渐减小,当埋藏深度足够大时,漏磁场将趋于零。
因此,可以用来检测的焊管壁厚一般为6~15mm;降低灵敏度的情况下,可检测壁厚为20mm。
缺陷的尺寸大小对漏磁场影响也很大,当缺陷宽度相同而深度不同时,漏磁场随着缺陷深度的增加而增大,在一定范围内两者近似成直线关系。
缺陷宽度对漏磁场的影响并非单调变化,在缺陷宽度很小时,随宽度的增大漏磁场有增加的趋势;但当宽度较大时,宽度增大,漏磁场反而缓慢下降。
(3)提离值。
当提离值超过裂纹宽度的2倍时,随着提离高度的增加,漏磁场强度迅速下降。
传感器支架的设计必须使探头在被检测钢管表面扫查时的提离值保持恒定,一般要小于2mm,常取1mm。
(4)探伤速度。
在探伤过程中应尽量保持匀速进行,速度不同会造成漏磁信号形状不同,但一般不至于造成误判。
(5)焊管表面质量。
焊管表面的油漆等涂层厚度对探伤灵敏度的影响非常大,随着涂层厚度的增加,探伤灵敏度急剧下降。
从目前的仪器性能来看,当涂层厚度≥6mm时,已经无法获得有效的缺陷识别信号。
焊管表面粗糙度的不同使传感器与被检表面的提离值发生动态变化,从而会影响探伤灵敏度的一致性,另外还会引起系统振动而带来噪声,所以要求被检测焊管表面应尽量光滑平整。
焊管表面的氧化皮和铁锈等杂物,也可能在探伤过程中产生伪信号,应及时确认或复检[1-3]。
2焊管全管体涡流探伤涡流探伤方法的特点有:①不需要耦合剂,可以非接触进行;②探伤速度快,能够实现在线生产(可达3m/s,正常生产时为2m/s),另外调整和更换规格时间短(一般为10~20min);③可以对高温焊管焊缝进行检测;④探伤结果可靠性高。
由于涡流探伤速度快,穿过式线圈涡流探伤法多年来广泛用于检测焊管质量,特别是其致密性,但难以检测出铁磁性焊管焊缝中的纵向裂纹。
因此在高标准的涡流探伤中,一般采用探针式线圈涡流探伤法[4]。
对于焊管焊缝中常常产生的“内毛刺吸附”,涡流探伤设备往往会误报为缺陷。
频繁出现涡流探伤过程中内毛刺因电磁力吸附在焊缝上,离开涡流磁场后钢管接触自动消磁装置,没有磁力吸引后内毛刺自动掉落,再进行手工复探又没有缺陷显示的尴尬问题。
由于趋肤效应的影响,随着被检焊管与检测线圈之间距离的增加,其检测灵敏度将逐渐减小,因此,对于同样大小的缺陷,处于管内壁所反映出来的信号幅度将小于管外壁上的缺陷。
焊管全管体涡流探伤设备在探测焊管外表面和内表面缺陷方面的能力,是由多种因素所决定的,但最主要的还是取决于被检焊管的壁厚和涡流激励频率及磁饱和强度;同时,在选择仪器参数时,还应考虑被检焊管导电率和导磁率等物理参数对涡流探伤精度的影响。
3焊管全管体超声波探伤焊管全管体超声波探伤主要分为直接接触法和液浸法。
(1)直接接触法。
超声波探头与试件探测面之间涂有很薄的耦合剂层,因此可以看作两者直接接触。
直接接触法操作方便,探伤图形较简单,判断容易,检出缺陷灵敏度高,是实际探伤中使用最多的方法。
但该方法对被检测试件探测面的精度要求较高[5]。
(2)液浸法。
将超声波探头和工件浸于液体中以液体作耦合剂进行探伤的方法,称为液浸法。
耦合剂可以是油,也可以是水。
液浸法又分为全浸没式和局部浸没式。
该方法适用于表面粗糙的试件,探头不易磨损,耦合稳定,探测结果重复性好,便于实现自动化探伤。
不过液浸法中声波在管壁中的传播衰减是很严重的,一个较好的解决方案是以水膜法代替水浸法进行声耦合。
曹雷:焊管常用探伤方法及技术钢管2012年8月第41卷第4期检测技术734焊管焊缝超声波探伤1)焊缝离线探伤焊管由传输辊道送到探伤区,升起旋转托辊,将钢管焊缝在托辊上手动旋转至焊缝某点位置。
探伤小车运行,各组探头按顺序延时下落在焊管上,探伤用耦合剂为焊管生产线的乳化液,接受传感信号自动喷淋在焊缝及两侧。
因为超声波离线系统布置于水冷和空冷后,焊缝偏离的影响变得很重要,所以在焊缝离线探伤中,焊管焊缝纵向线状缺陷检测采用两组共6个探头,每组3个探头,分布在焊缝两侧,双向检测,共占用6个通道,在焊缝扭转(偏离)15mm 范围内均可正常探伤。
单个纵向探头探伤覆盖范围为焊缝垂直方向12.7mm (焊缝两侧各6.4mm ),在焊缝垂直方向12.7mm 宽的区域内焊缝厚度(最大13.72mm )方向无盲区覆盖。
焊缝横向线状缺陷及点状缺陷检测也要考虑钢管焊缝的少量扭转(偏离)。
因此采用两组6个探头,每组3个探头,前后分布,即使焊缝扭转(偏离),探头也始终能覆盖探伤区,由于覆盖区域宽,可对焊缝及左右5mm 进出扫查,达到全焊缝覆盖双向检测,更好地保障了探伤质量控制精度,横向探头共占用6个通道。
设备总计占用12个通道。
探头布置如图1所示。
为了防止探头磨损,尽量减少探头与焊管直接接触,钢管企业与探伤设备生产研发机构共同设计研究了探靴与探头套的升级改进。
在探伤设备的升级中,已有大部分焊管生产厂采用以离线探伤PLC+工控机的控制模式,提高设备控制精度,避免管端盲区,探伤系统大多采用成对探头实现耦合监测,2个探头组成一对,对称位于焊缝的两侧,且触发时间不同。