连铸板坯表面纵向裂纹的形成原因
板坯边部纵裂纹产生的原因及解决措施
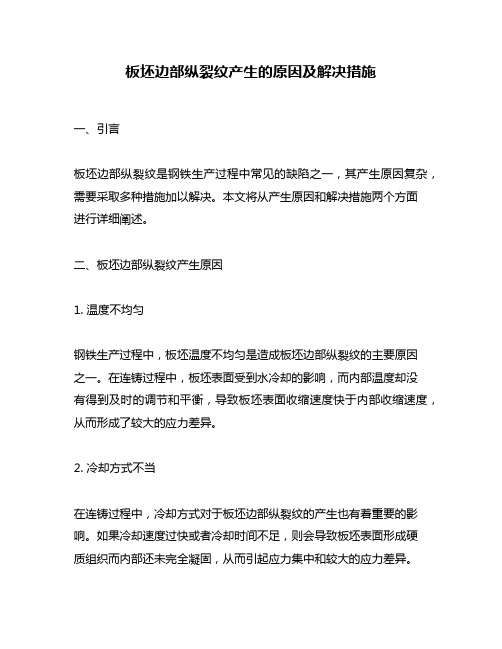
板坯边部纵裂纹产生的原因及解决措施一、引言板坯边部纵裂纹是钢铁生产过程中常见的缺陷之一,其产生原因复杂,需要采取多种措施加以解决。
本文将从产生原因和解决措施两个方面进行详细阐述。
二、板坯边部纵裂纹产生原因1. 温度不均匀钢铁生产过程中,板坯温度不均匀是造成板坯边部纵裂纹的主要原因之一。
在连铸过程中,板坯表面受到水冷却的影响,而内部温度却没有得到及时的调节和平衡,导致板坯表面收缩速度快于内部收缩速度,从而形成了较大的应力差异。
2. 冷却方式不当在连铸过程中,冷却方式对于板坯边部纵裂纹的产生也有着重要的影响。
如果冷却速度过快或者冷却时间不足,则会导致板坯表面形成硬质组织而内部还未完全凝固,从而引起应力集中和较大的应力差异。
3. 连铸机结构问题连铸机的结构问题也会对板坯边部纵裂纹的产生造成影响。
例如,如果连铸机的结构不合理或者设备老旧,就可能导致板坯内部温度不均匀或者冷却方式不当,从而引起板坯边部纵裂纹。
三、解决措施1. 调节温度钢铁生产过程中,调节温度是减少板坯边部纵裂纹的有效措施之一。
可以通过加强温度监测和调节系统来实现。
例如,在连铸过程中可以采用先进的热流体模拟技术来预测板坯内部温度分布情况,并及时调整冷却水量和喷淋位置等参数,以保证板坯内外温度平衡。
2. 改进冷却方式改进冷却方式也是减少板坯边部纵裂纹的有效措施之一。
可以通过增加喷淋头数量、改变喷淋角度、增加喷淋水量等方式来改善连铸过程中的冷却效果,并保证板坯表面和内部同时达到凝固要求。
3. 优化连铸机结构优化连铸机结构也是减少板坯边部纵裂纹的有效措施之一。
可以通过升级设备、改进结构、增加监测仪器等方式来提高连铸机的生产效率和准确性,从而保证板坯内部温度分布均匀和冷却方式合理。
四、总结综上所述,板坯边部纵裂纹是钢铁生产过程中常见的缺陷之一,其产生原因复杂,需要采取多种措施加以解决。
调节温度、改进冷却方式和优化连铸机结构是减少板坯边部纵裂纹的有效措施。
连铸坯表面裂纹形成及防止分析

浸入式水口对中,防止偏流 合理的浸入式水口设计(合适的出口直径,倾角) 合适的水口插入深度 合适的频率和振幅
(3) 结晶器振动
2 铸坯表面纵裂纹
(4) 出结晶器铸坯运行 二次冷却均匀性 (5) 调整钢水成分 钢中碳含量避开包晶区,C向下线或上线控制 钢中S<0.015% 残余元素Cu、As、Zn控制<0.1%
图2-4 拉速对纵裂纹的影响
2 铸坯表面纵裂纹
(3) 保护渣 液渣层厚度<10mm,纵裂纹增加(图2-5)。
图2-5 液渣层厚度对纵裂纹的影响
2 铸坯表面纵裂纹
(4) 结晶器液面波动 液面波动<±5mm,纵裂纹最少(图2-6);
图2-6 结晶器液面波动对纵裂纹的影响
2W (T1 T2 ) W
连铸坯表面裂纹 形成及防止
宋晔
内容
1 2 3 4 5 前言 铸坯表面纵裂纹 铸坯表面横裂纹 铸坯表面星形裂纹 结论
1.前言
连铸坯质量概念: ◆ 铸坯洁净度(夹杂物数量、类型、尺寸、 分布) ◆ 铸坯表面质量(表面裂纹、夹渣、气孔) ◆ 铸坯内部质量(内部裂纹、夹杂物,中 心疏松、缩孔、偏析) ◆ 铸坯形状缺陷(鼓肚、脱方)
2 铸坯表面纵裂纹
2.3 影响表面纵裂纹产生的因素
(1) 钢水成分
◆ [S]>0.015%,纵裂纹增加(图2-2);
◆ [C]=0.12~0.15%,纵裂纹产生严重(图2-3)
图2-2 钢中[S]与裂纹指数的关系
2 铸坯表面纵裂纹
பைடு நூலகம்
图2-3 含碳量对板坯宽面纵裂纹的影响
2 铸坯表面纵裂纹
(2) 拉速 拉速增加,纵裂纹指数增加(图2-4);
连铸板坯表面纵裂原因探究

连铸板坯表面纵裂原因探究
连铸板坯作为容易变形的金属坯料,在冷却变形过程中容易出现多种裂纹,其中纵裂最为常见。
针对连铸板坯表面纵裂现象,本文就其产生原因进行探究。
首先,表面纵裂常常是由于板坯的表面微细的成形不均匀导致的。
在铸造过程中,由于复杂的铸件形状,往往在表面上凸起或凹陷的微细尺寸会有些出入,并且会加快凝固层的冷却变形,从而使表面裂纹形成。
其次,表面纵裂也可能是由于浇口不合理而出现的。
正常的浇口应该是圆形的,但如果浇口不够均匀,表面纵裂就会产生。
此外,如果浇口太大,会导致板坯储存在浇口中的金属过多,使其凝固太快,从而导致表面纵裂的形成。
再者,当铸件温度过高的时候,表面纵裂也是可能出现的。
当板坯的温度过高时,凝固层会变得很薄,而且会加快凝固变形的过程,从而会出现表面纵裂现象。
最后,表面纵裂也可能是由于模具材料质量不佳导致的。
连铸板坯在流动过程中,会受到模具的影响,因此,模具质量的不佳会直接导致表面纵裂的发生。
总之,连铸板坯表面纵裂的原因多种多样,主要包括表面微细成形不均匀、浇口不合理、板坯温度过高、模具质量不佳等。
因此,为了防止表面纵裂的发生,可以采取一系列技术措施,以确保生产高质量的产品。
板坯边部纵裂纹产生的原因及解决措施

板坯边部纵裂纹产生的原因及解决措施板坯边部纵裂纹是钢铁生产过程中常见的问题之一,它会影响钢材的质量和使用寿命,因此必须采取措施加以解决。
本文将从产生原因和解决措施两个方面进行探讨。
一、产生原因
1.板坯温度不均匀:板坯温度不均匀是板坯边部纵裂纹产生的主要原因之一。
当板坯表面温度高于内部温度时,板坯边部会出现温度梯度,导致板坯边部产生应力,从而引起纵裂纹。
2.板坯结晶器结构不合理:板坯结晶器结构不合理也是板坯边部纵裂纹产生的原因之一。
结晶器结构不合理会导致板坯边部温度不均匀,从而引起纵裂纹。
3.轧制工艺不合理:轧制工艺不合理也是板坯边部纵裂纹产生的原因之一。
轧制工艺不合理会导致板坯边部应力过大,从而引起纵裂纹。
二、解决措施
1.优化板坯结晶器结构:优化板坯结晶器结构是解决板坯边部纵裂纹的有效措施之一。
合理的结晶器结构可以使板坯温度均匀,从而减少板坯边部应力,降低纵裂纹的发生率。
2.调整轧制工艺:调整轧制工艺也是解决板坯边部纵裂纹的有效措
施之一。
合理的轧制工艺可以使板坯边部应力适当,从而减少纵裂纹的发生率。
3.控制板坯温度:控制板坯温度也是解决板坯边部纵裂纹的有效措施之一。
合理的板坯温度可以使板坯温度均匀,从而减少板坯边部应力,降低纵裂纹的发生率。
板坯边部纵裂纹是钢铁生产过程中常见的问题之一,产生原因主要有板坯温度不均匀、板坯结晶器结构不合理和轧制工艺不合理等。
解决措施主要包括优化板坯结晶器结构、调整轧制工艺和控制板坯温度等。
只有采取有效的措施,才能有效地解决板坯边部纵裂纹问题,提高钢材的质量和使用寿命。
连铸坯在凝固过程中形成裂纹的原因

连铸坯在凝固过程中形成裂纹的原因随着市场竞争的日趋激烈,产品的质量已经成为占有市场的主要砝码,连铸坯作为炼钢厂的终端产品,其质量直接影响着轧材单位的产量和轧材质量,据统计炼钢厂连铸坯质量缺陷中约70%为连铸坯裂纹,连铸坯裂纹成为影响连铸坯产量和质量的重要缺陷之一,下面将对铸坯在凝固过程中裂纹的形成做简要分析:一、铸坯凝固过程的形成铸坯在连铸机内的凝固可看成是一个液相穴很长的钢锭,而凝固是沿液相穴的固液界面在液固相温度区间把液体转变为固体把潜热释放出来的过程。
在固液界面间刚凝固的晶体强度和塑性都非常小,当作用于凝固壳的热应力、鼓肚力、矫直力、摩擦力、机械力等外力超过所允许的外力值时,在固液界面就产生裂纹,这就形成了铸坯内部裂纹。
而已凝固的坯壳在二冷区接受强制冷却,由于铸坯线收缩,温度的不均匀性,坯壳鼓肚、导向段对弧形不准,固相变引起质点如(AlN)在晶界的沉淀等,容易使外壳受到外力和热负荷间歇式的突变,从而产生裂纹就是表面裂纹。
二、连铸坯裂纹形态和影响因素连铸坯裂纹形态分为表面裂纹和内部裂纹,表面裂纹有纵向、横向角部裂纹、表面横裂和纵裂、网状裂纹和凹陷等,内部裂纹有中间、中心和矫直裂纹等。
连铸坯裂纹的影响因素:连铸坯表面裂纹主要决定于钢水在结晶器的凝固过程,它是受结晶器传热、振动、润滑、钢水流动和液面稳定性所制约的,铸坯内部裂纹主要决定于二冷区凝固冷却过程和铸坯支撑系统(导向段)的对弧准确性。
铸坯凝固过程坯壳形成裂纹,从工艺设备和钢凝固特性来考虑影响裂纹形成的因素可分为:1、连铸机设备状态方面有:1)结晶器冷却不均匀2)结晶器角部形状不当。
3)结晶器锥度不合适。
4)结晶器振动不良。
5)二冷水分布不均匀(如喷淋管变形、喷咀堵塞等)。
6)支承辊对弧不准和变形。
2、工艺参数控制方面有:1)化学成份控制不良(如C、Mn/S)。
2)钢水过热度高。
3)结晶器液面波动太大。
4)保护渣性能不良。
5)水口扩径。
6)二次冷却水分配不良,铸坯表面温度回升过大。
连铸板坯表面纵裂原因探究

连铸板坯表面纵裂原因探究连铸板坯表面纵裂是一种很常见的问题,这种现象会导致质量问题,影响后续工序,并增加板材的损耗。
因此,对于连铸板坯表面的纵裂机理及其原因的深入探究显得尤为重要。
第一,表面纵裂的形成机理。
在连铸过程中,由于液态铸锭造粒时所作用的拉拔力和铸锭不均的温度场,使各种尺寸的铸锭受力不均,把铸锭表面不平整,针织纹以及其他皱革状物出现,比较大的破坏原有大片薄膜结构,使表面出现纵裂。
第二,表面纵裂的成因。
连铸板坯表面纵裂的主要原因有:铸锭温度不均,液态铸锭造粒时所作用的拉拔力过大,液态铸锭温度不合适,液态铸锭含氧量太高,铸锭结构缺乏稳定性,表面物质含量过高,以及操作不当等。
第三,消除表面纵裂的技术措施。
针对连铸板坯表面纵裂的原因,可以采取以下技术措施来消除表面纵裂:(1)调节液态铸锭温度,把液态铸锭温度控制在一定范围内,使铸锭结构更加稳定;(2)减少熔炼后的液态铸锭氧化,减少表面物质的含量;(3)采用新型的拉拔装置,减少拉拔力的大小;(4)做好连铸操作规程,保证生产工艺的稳定性。
第四,未来的发展方向。
在以上的技术措施的基础上,为了进一步改善连铸板坯表面纵裂现象,未来发展的重点在于以下方面:(1)采用新型材料,使整体板坯结构更加稳定,从而改善表面纵裂现象;(2)实施连铸装备智能化,使连铸工艺运行得更加顺畅、稳定;(3)采用现代化的动力控制系统,改善铸锭的动力分布;(4)开展更多的科学研究,探索更有效的表面纵裂预防技术。
综上所述,连铸板坯表面纵裂是一种很常见的问题,其发生是由于铸锭温度不均、拉拔力过大、液态铸锭含氧量太高和铸锭结构缺乏稳定性等原因所导致,为了消除这一现象,应当调节液态铸锭温度、减少液态铸锭含氧量、采用新型拉拔装置、做好连铸操作规程等,未来还要探索新型材料、连铸装备智能化、现代化的动力控制系统以及更有效的表面纵裂预防技术,以期改善连铸板坯表面纵裂现象。
连铸板坯表面纵裂原因探究

连铸板坯表面纵裂原因探究
连铸板坯表面纵裂是目前钢铁行业中比较常见的一种缺陷,它主要指的是在铸钢板坯的表面有一条类似裂缝的状况,这种缺陷会降低板坯的使用质量,降低生产效率,影响铸钢行业的运营状况。
因此,研究连铸板坯表面纵裂的原因,对于钢铁行业来说具有重要意义。
首先,连铸板坯表面纵裂形成的原因可以归结为四大类,即工艺因素、材料因素、结构因素、设备因素。
在四大因素中,工艺因素是造成连铸板坯表面纵裂的主要因素,从料头到成品,从工艺流程到参数设置,连铸工艺铸造中几乎每一个环节都可能导致连铸板坯表面纵裂的形成。
其次,在冶炼中缺陷的材料可能会造成连铸板坯表面纵裂,而板坯结构变形也可能导致板坯表面纵裂的出现。
此外,设备故障,如冷却不均匀或设备老化,也会导致连铸板坯表面纵裂的形成。
要有效控制连铸板坯表面纵裂的形成,应从四个方面着手:第一,严格把控连铸工艺参数,做到技术标准控制,定期检验确保各环节工艺符合要求;第二,提升冶炼质量,提高冶炼材料的质量,做到成分精确;第三,优化板坯结构,采用合理的结构和冷作参数,以避免因冷作过度造成表面纵裂;第四,定期检测设备,及时更换老化的设备,保证工艺设备的正常运行。
此外,针对已产生的连铸板坯表面纵裂,也可以采取一些措施来缓解。
一是加大轧制参数,通过轧制平整板坯表面,消除表面缺陷;二是通过焊接和补焊,消除已经存在的表面纵裂;三是采用再结晶技术来填补表面纵裂,提高板坯的力学性能。
综上所述,连铸板坯表面纵裂的原因复杂,要想有效地控制纵裂的发生,就需要从工艺、材料、结构、设备等方面着手,合理采取措施,降低缺陷比例,保证生产质量。
连铸坯发纹裂纹产生的原因

连铸坯发纹裂纹产生的原因连铸坯发纹裂纹是指在连铸过程中,坯料表面产生裂纹的现象。
这种现象在连铸过程中非常常见,如果没有正确的处理,会影响连铸坯的质量和后续加工工艺,甚至可能导致产量的降低。
连铸坯发纹裂纹的产生原因非常多样化,主要包括以下几个因素。
首先,连铸坯发纹裂纹的产生与坯料的化学成分有关。
在连铸过程中,如果坯料中含有不溶于钢液的硬质夹杂物,这些夹杂物会被硬质粒子剪切或滚动而产生裂纹。
此外,坯料中如果含有超过允许值的硫、磷等元素,会导致钢液的黏度增加,使连铸过程中液面波动较大,从而增加坯料表面的应力,进一步促进裂纹的发生。
其次,连铸坯发纹裂纹的产生与连铸工艺参数有关。
连铸过程中的拉速度、浇注速度、结晶器冷却剂的喷射速度等参数的过大或过小都会导致连铸坯表面产生应力,从而引发裂纹的产生。
此外,连铸过程中,如果坯料温度过低或结晶器冷却不均匀,也会导致坯料表面产生裂纹。
再次,连铸坯发纹裂纹的产生与结晶器的表面状况有关。
结晶器的表面状况会直接影响连铸坯表面的光滑度和均匀度。
如果结晶器表面存在磨损、凹凸不平等缺陷,会导致连铸坯表面产生过多的应力,从而引发裂纹的产生。
此外,连铸坯发纹裂纹的产生还与连铸辊的形状和磨损程度有关。
连铸辊的形状不合理或磨损过度会导致钢坯的厚度不均匀,在拉伸过程中产生裂纹。
在连铸工艺中,如果连铸辊的温度过高或过低,也会导致连铸坯的拉伸和表面温度不均匀,从而引发裂纹的产生。
最后,连铸坯发纹裂纹的产生还与工艺操作和设备维护有关。
操作不当会导致坯料表面的应力增加,设备维护不到位会降低连铸过程的稳定性,从而增加坯料发纹裂纹的风险。
为了减少连铸坯发纹裂纹的发生,可以采取以下措施:1.优化坯料的化学成分,减少夹杂物的含量,控制硫、磷等元素的含量。
2.合理调整连铸工艺参数,包括拉速度、浇注速度、结晶器冷却剂的喷射速度等,以减小坯料表面的应力。
3.对结晶器进行检修和维护,保持其表面的光滑度和均匀度。
- 1、下载文档前请自行甄别文档内容的完整性,平台不提供额外的编辑、内容补充、找答案等附加服务。
- 2、"仅部分预览"的文档,不可在线预览部分如存在完整性等问题,可反馈申请退款(可完整预览的文档不适用该条件!)。
- 3、如文档侵犯您的权益,请联系客服反馈,我们会尽快为您处理(人工客服工作时间:9:00-18:30)。
第16卷第5期2004年10月钢铁研究学报JOU RNA L OF IRON AN D ST EEL RESEAR CHV ol.16,N o.5O ct.2004作者简介:周有预(1946-),男,大学本科,教授级高工; 收稿日期:2003-06-12; 修订日期:2003-11-21#企业之窗#连铸板坯表面纵向裂纹的形成原因周有预, 罗德信[武汉钢铁(集团)公司技术中心,湖北武汉430080]摘 要:对连铸板坯表面纵向裂纹的形成原因进行了分析研究,发现浸入式水口在浇注过程中损坏和结晶器保护渣性能不佳是主要因素。
采取了相应的改进措施后,钢板表面线状缺陷的发生率大幅度降低。
关键词:连铸;板坯;表面纵向裂纹;浸入式水口;结晶器保护渣中图分类号:T G24917 文献标识码:A 文章编号:1001-0963(2004)05-0075-04Formation Reason for Longitudinal Crack on Surface ofContinuous Casting SlabZHOU You -yu, LUO De -x in[Wuhan Iron and Steel (G roup),W uhan 430080,China]Abstract:T he fo rmation reaso n of the longitudinal cracks on the surface of the co ntinuous casting slab was analy zed.It is mainly attr ibut ed to the damage o f the submerged nozzle during casting and so me undesir -able properties of the mould powder.T his problem has been successfully solved after applying some coun -ter measures.Key words:continuous casting ;slab;sur face long itudinal cracks;submer ged nozzle;mould powder连铸板坯的表面纵向裂纹会给其热轧、冷轧材带来相关的缺陷,必须查明原因以便采取正确的措施予以防范。
笔者发现连铸板坯表面纵向裂纹是钢板表面线状缺陷的源头,为此分析了板坯表面纵向裂纹的形成原因。
采取了针对性的措施后,大幅度降低了钢板表面线状缺陷的发生率。
1 板坯缺陷的检验武汉钢铁(集团)公司在一段时间内生产的XYB 和SS400冷轧钢板(厚0115mm )表面频繁出现线状缺陷。
该缺陷不光滑,呈灰色,沿轧向延伸,宽度为115~15mm,有的部位出现孔洞(见图1)。
金相检验表明:该处存在FeO 和大量密集分布的氧化物圆点。
对上述薄板的原料)))厚6mm 的XYB热轧图1 冷轧薄板线状缺陷的宏观特征Fig 11 Macrostructure of linear defect in cold rolling sheet板进行跟踪检查,发现了同样沿轧向延伸的线状缺陷,它不同于非金属夹杂物和氧化铁皮引起的表面缺陷,尺寸长短不一,有的贯穿整卷带坯,通常其宽度为015~215mm,深0105~0110mm 。
对缺陷部位进行金相观察,发现存在条带分布的FeO,周围基体中有大量密集分布的氧化物圆点(见图2)。
将试样侵蚀后观察,FeO 周围有明显的脱碳和晶粒长大现象(见图3),无过热、过烧现象。
以上这些事实,说明该缺陷的形成与加热炉的加热工艺无关,在连铸坯进入加热炉之前已经存在这类缺陷。
基于上述分析,对该类钢种的连铸坯(断面尺寸为210mm @1100mm)逐一进行检查,在XYB 钢的连铸坯上发现了表面纵向裂纹。
该裂纹主要分布在宽面的纵向中心线附近,分布范围占坯宽的1/3,其宽窄和长短不一,细小裂纹肉眼难辨,最宽的裂纹可达5mm,最长的裂纹贯穿整块铸坯的定尺长度,达918m 。
连铸坯表面纵向裂纹的形貌见图4。
用磁粉探伤法探测了4块有此类纵向裂纹的铸坯,确定和测量了裂纹的范围后送热轧加热炉按常规加热制度加热,出炉冷却后再次探伤。
结果显示:加热后铸坯上的裂纹范围与加热前基本对应,加热前探测出的裂纹80%仍然存在,仅有少量裂纹在加热过程中因铸坯表面的氧化而消失。
探伤后将该批铸坯再次加热、轧制,结果在热轧板的相应部位产生上述的线状缺陷。
由此判断,此类缺陷是由连铸板图2 热轧板缺陷部位的FeO 及氧化物圆点Fig 12 FeO and oxide dot at defective portion ofhot rollingplate图3 缺陷部位的脱碳及晶粒长大特征Fig 13 Decarburization and grain growth at def ectiveportion图4 连铸板坯表面纵向裂纹的形貌Fig 14 M orphology of longitudinal crack on surf ace ofcontinuous casting slab坯宽面上的纵向裂纹引起的。
2 影响因素分析对冶炼和连铸工艺进行了跟踪调查,重点关注连铸用功能性耐火材料的使用情况,对保护渣等辅助材料进行了取样分析。
结果表明:石英质浸入式水口在浇注过程中损坏和结晶器保护渣性能不佳是产生该纵向裂纹的主要原因。
211 石英质浸入式水口随机跟踪观察了4浇次共11炉(每炉约80t 钢水)XYB 钢的连铸过程。
其中,第1浇次在浇注过程中水口底部穿孔(4个孔,孔直径约10mm ),第2浇次在注毕时水口沿侧孔熔断,残断部分漂浮在结晶器内的钢液表面上。
跟踪观察还发现:当水口发生底部穿孔时,结晶器内渣面呈呆滞死板状;而浸入式水口沿侧孔熔断过程中可见到渣面被穿漏的钢水扰动。
对浸入式水口的蚀损部位进行岩相分析,用扫描电镜测定了该处的元素分布。
蚀损断面由基体向表层依次是非晶态二氧化硅、鳞石英、硅酸盐玻璃体和附着的刚玉。
水口基体含SiO 2约100%,其蚀损部位的化学成分列于表1。
由表1可见,蚀损部位CaO 的含量较高,并有NaO 和K 2O,说明该处附集有结晶器保护渣。
结合岩相分析可以看出,浇注过程中石英质浸入式水口表1 水口蚀损部位的化学成分Table 1 Composition of SEN at erosion portion %视场NaO Al 2O 3SiO 2K 2O CaO 13153671297511395019792813382217343140860178002314113214267711512014232004年 钢 铁 研 究 学 报 第16卷因附着结晶器保护渣后生成低熔点的复合氧化物而熔损,随之由外层剥蚀、内层析晶而逐层损坏。
结晶器保护渣主要由CaO -SiO 2-Al 2O 3三元系组成,并添加了多种助熔剂,在高温下对石英质耐火材料的侵蚀性很强。
浇注过程中,钢液表面的水平高度波动或水口侧孔变形扩大均会加剧保护渣对水口的破坏作用。
当浸入式水口在浇注过程中熔断或底部穿孔时,钢流改变了设定的流线而冲向其他部位或直接下冲(如图5所示),使铸坯的凝固壳变薄或熔损,降低了该部位的坯壳强度而产生铸坯表面的纵向裂纹。
当浸入式水口在渣线部位被侵蚀穿透时,由此处漏出的钢水与保护渣互相搅拌,破坏了保护渣的3层结构,不仅影响熔渣向弯月面的填充,还使保护渣的保温性能变差、钢水面氧化、铸坯产生夹渣。
当浸入式水口底部穿孔或注流从断口直接下冲时,铸坯内的高温区下移,钢液表面的温度下降,使保护渣表面呈/板结0状。
此时保护渣无法发挥其功能,结晶器内初生坯壳与结晶器壁之间无正常厚度的渣膜进行润滑,坯壳冷凝收缩受阻时也容易产生表面纵向裂纹。
212 结晶器保护渣XYB 钢使用粉状的结晶器保护渣。
跟踪观察中发现结晶器内钢液表面上粉渣呈堆、团状,铺展性欠佳。
开浇15min 左右即有渣条出现,且出现的频率较高。
取样化验的结果显示:渣条中Al 2O 3的含量高达1415%,而粉渣中该含量仅为7184%。
这表明该渣在浇注过程中吸收了钢水中的Al 2O 3后性)))出流钢水的设定流线;----从穿孔和断口流出钢水的异常流线图5 结晶器内钢水流动的示意图Fig 15 Scheme of molten steel movement in mould能发生了突变。
若不及时清除渣条,当其移近结晶器壁时就有可能被夹入弯月面,从而显著恶化铸坯的冷凝和润滑条件,严重时会引发漏钢事故。
对保护渣样进行熔融特性测定,发现它有/分熔0现象,即在试样的升温过程中,部分低熔点物料先行熔化并流失,而大部分物料的半球点高达1250e ,1300e 下的熔化时间长达50s 。
连铸过程使用/分熔0倾向严重的保护渣,会造成难熔物料聚集并粘附在铸坯的凝固壳表面,造成铸坯表面夹渣或裂纹[1]。
为改善连铸坯的质量,必须对结晶器保护渣的配方和制备工艺进行调整,以改进其熔融特性和铺展特性。
3 改进措施及其效果311 改进措施基于上述分析,更换了浸入式水口和结晶器保护渣的材质。
用铝碳质水口取代石英质水口浇注XYB 及同类钢种。
对两种材质的浸入式水口的使用情况进行了观察。
石英质水口一般浇注2、3炉即损坏,出现底部穿孔、沿侧孔扩大甚至熔断、沿渣线熔断等;而铝碳质水口一般可浇注4、5炉,停浇原因一般为水口结瘤或水口沿渣线穿漏。
试验中,当水口损坏后及时更换中间包,以减轻因水口损坏对铸坯质量造成的影响。
针对结晶器保护渣存在的问题对其进行了改进,调整了化学成分,研制了改进型颗粒保护渣。
还对保护渣的制备工序(如破碎、混拌、造粒、干燥)进行了严格的控制。
取样检验表明:改进型颗粒保护渣无分熔现象,浇注过程中渣层厚度稳定在8~12mm 的范围内,渣面铺展性良好,很少产生渣条。
312 改进效果XYB 钢浇铸成板坯后,送热轧厂轧成热轧卷,再送冷轧厂加工成镀锡板。
表2给出采取改进措施前后镀锡板线状缺陷的发生率。
显然,6月和7月份镀锡板线状缺陷的发生率较高,8月份采取改进表2 采取改进措施前后镀锡板线状缺陷的发生率Table 2 Occurrence rate of linear defect in tin -platebefore and af ter improvement月份6(改进前)7(改进前)8(改进后)9(改进后)缺陷发生率/%731122716961773162第5期 周有预等:连铸板坯表面纵向裂纹的形成原因 10月措施后该类缺陷的发生率明显下降,至12月已降至0196%。
4讨论连铸过程中浸入式水口的损坏改变了设定的钢水流入方向,明显地增加了铸坯缺陷的发生率。