高炉冶炼过程能量利用计算分析
5 高炉冶炼过程的能量利用

(513)
高炉内水煤气置换反应:H2 + CO2 === H2O + CO接近平衡因此
( (
) ) ≈ const = 0.9 ~ 1.1.
西德巴格达弟经验关系:ηH2 ηCO = 0.88 + 0.1/ηCO 苏联巴巴柳金经验关系:
2009-4-15
16
1. 校正焦比,原,燃料成分整理
(1) 校正焦比:由铁损校正,总铁损可达1.0~1.5%,计入回收铁 (2) 成分整理:按元素或/和化合物的实际化学存在状态,将所有物料成分调整,换算成总和 为100%
成分整理诀窍:IF Sum = 99.5~100.0,THEN
余下的加入到CO2,H2O中,其它不变; 或 以MeXOY形式存在,加入到Rest中. Fe,CaO,SiO2不变; 根据数量按顺序酌情变更CO2,H2O,Rest,MgO,Al2O3量. (当用MgO,Al2O3平衡方程时,最好不要变动MgO,Al2O3成 IF 100.0 Sum > 2.0,THEN 或
4
(3) 高炉总直接还原度
Rd = 炉料中氧转入煤气过程中,直接还原方式夺取的氧量 =
炉料气化的总氧量
Od O 料气
(53)
R i = 1 Rd
=
Oi O
料气
Rd = (rd O
FeXO→Fe
+ OdSi,Mn,P,S O还总
)
(57) (58) (58)
5
Rd = Rd [1+ (O
焦挥 +
2009-4-15
北京科技大学 教授 博导 吴胜利
3
高炉炼铁基本原理与工艺
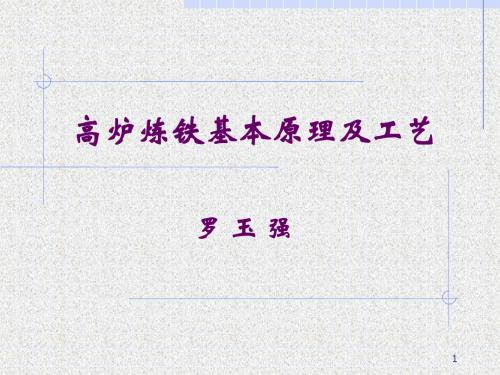
15
2.铁的间接还原与直接还原
(1)间接还原:用CO、H2为还原剂还原铁的氧化物,产物CO2、 H2O的还原反应。 特点:放热反应 反应可逆 (2)直接还原:用C作为还原剂,最终气体产物为CO的还原反应。 特点:强吸热反应 反应不可逆 (3)直接、间接还原区域划分:取决于焦碳的反应性 低温区 <800℃基本为间接还原 中温区 800~1100℃共存 高温区 > 1100℃全部为直接还原 (4)用直接还原度rd、间接还原度ri来衡量高炉C素利用好坏,评价 焦比。
9
2. (助)熔剂
(1)作用: 形成低熔点易流动的炉渣、脱S(碱性熔剂) (2)种类:
使用条件及作用
碱性
酸性
铁矿中脉石为酸性氧化物,包括:石灰石、白云石、石灰
铁矿中脉石为碱性氧化物,主要为:SiO2(只在炉况失常 时使用——(Al2O3)≥18%或排碱时) 高Al熔剂,主要为:含Al2O3高的铁矿(只在降低炉渣流动 性时使用)
24
五、高炉强化冶炼手段与方法
1.大风量 风量增加,炉内传热效果下降,ri降低,K 增加。风量应与还原性相适应 2.高风温 风温增加,传热推动力增加,但利用风温 的同时K势必降低,透气性将下降 3.富氧 富氧将使炉缸温度增加,但煤气总量下降, 不利于全厂能量平衡;富氧达到的效果与提高 风温相比,成本提高10倍。
10
中性
3 焦碳
①主要作用:
作为高炉热量主要来源的60~80%,其它热风提供 提供还原剂C、CO 料柱骨架,保证透气性、透液性
②质量要求:
含炭量:C↑ 灰份:10%左右,灰分低可使渣量↓ 含S量:<0.6% 生铁中[S]80%±来源于焦碳 强 度:M40 (kangsuiqd)、M10 (lmqd) 粒度组成:均匀 60mm 左右的 >80% ,大于 80mm 的 <10% ,大于 80mm的<10% 成分稳定(特指水分): 一般采用干熄焦 焦碳反应性: C+CO2=2CO开始反应的高低快慢→影响间接还原区的 范围从而影响焦比
国内外高炉炼铁系统的能耗分析
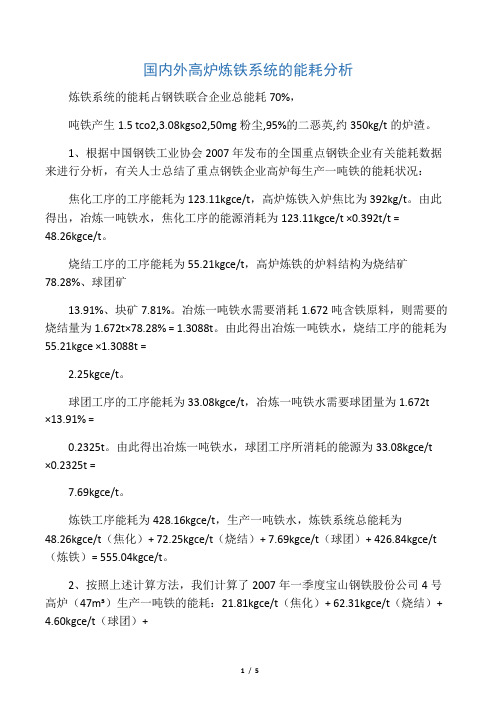
表12005年浦项制铁盒光阳厂炼铁有关能耗指标
项目工序能耗Kgce/t
烧结
66
57.4焦化
129.7
131.9炼铁
462.5
441.1入炉焦比Kgce/t炉料结构%
烧结比
76.4
70.9球团比
7.8
11.1块矿比
15.8
18.0xx
光阳494.7
492.1
表2全国重点钢铁企业能耗对比(单位Kgce/t)
高热值煤气回收利用率低是非高炉炼铁能耗高的“瓶颈”
2007年,我国重点钢铁企业的烧结、炼铁工序能耗与2006年相比进一步降低,炼铁生产部分工序能耗指标见表2。
2007年,全国重点钢铁企业高炉炼铁燃料比是529kg/t,浦项FINEX燃料比是740kg/t~750kg/t,澳大利亚Hismelt的煤耗在900kg/t(尚需1200℃风温和350kWh/t的电力)。这说明目前非高炉炼铁的能耗高于高炉冶炼生产工艺。
国内外高炉炼铁系统的能耗分析
炼铁系统的能耗占钢铁联合企业总能耗70%,
吨铁产生1.5 tco2,3.08kgso2,50mg粉尘,95%的二恶英,约350kg/t的炉渣。
1、根据中国钢铁工业协会2007年发布的全国重点钢铁企业有关能耗数据来进行分析,有关人士总结了重点钢铁企业高炉每生产一吨铁的能耗状况:
高炉热平衡计算

4 高炉热平衡计算4.1热平衡计算的目的热平衡计算的目的,是为了了解高炉热量供应和消耗的状况,掌握高炉内热能的利用情况,研究改善高炉热能利用和降低消耗的途径。
通过计算调查高炉冶炼过程中单位生铁的热量收入与热量支出,说明热量收支各项对高炉冶炼的影响,从而寻找降低热消耗与提高能量利用的途径,达到使高炉冶炼过程处于能耗最低和效率最高的最佳运行状态。
同时还可以绘制热平计算表研究高炉冶炼过程的基本方法[2]。
4.2热平衡计算方法热平衡计算的量论依据是能量守恒定律,即单位生铁投入的能量总和应等于中位个铁各项热消耗总和。
热平衡计算采用差值法,即热损失是以总的热量收入减去各项热量的消耗而得到的,即把热量损失作为平衡项,所以热平衡表面上没有误差,因为一切误差都集中掩盖在所有热损失之中。
根据计算的目的和分析的需要,热平衡可分为全炉热平衡与区域热平衡。
全炉热平衡是把整个高炉作为研究对象、计算它的各项热收入与支出,用来分析高炉冶炼过程令的能量利用情况。
而区域热平衡是把高炉的某一个区域作为研究对象,计算和分析这个区域内的能量利用情况。
虽然计算热平衡的部位与方法不向,但计算的目的都是为寻找降低能耗的途径和确定一定冶炼条件下的能耗指标。
理论上可以以把高炉内的任何一个部位当作区域热平衡的计算对象,但由于决定向炉冶炼能耗指标的主要因素存在于高炉下部的高温区。
因此,常用高炉下部属温区热平衡进行计算。
本例采用第一热平衡法计算进行热平衡计算。
第一种热平衡法,亦称热工法热平衡。
它是根据羔斯定则,不考虑炉内的实际反应过程.耍以物料最初与最终状态所具有的热力学参数为依据,确定高炉内的过程中所提供和消耗的热量。
它的热收入规定为焦炭和喷吹物的热值(即全部C完全燃烧成CO2和H2全部燃烧成H2O时放出的热量)、热风与炉料带入的物理热及少量成渣热。
而热支出为氧化物、硫化物和碳酸盐的分解热,喷吹燃料的分解热,水分分解热。
脱S反应耗热,渣铁和炉顶煤气热焓与热值,冷却水代走的热量和炉体散热损失等项。
高炉炼铁的产能与运行效率分析

采用先进的控制技术,如自动控制系统、 专家系统等
加强设备维护和管理,减少设备故障和停 机时间
采用节能型工艺,如富氧炼铁、熔融还原 炼铁等
高炉炼铁的环保性能分析
环保性能评估指标
废气排放量:包括二氧化硫、氮氧化物、 颗粒物等
能源消耗量:包括煤炭、电力等
废水排放量:包括重金属、有机物等
环境影响评价:包括对周边环境的影响、 生态破坏程度等
能耗:能耗是衡量高炉炼铁运行效率 的另一个重要指标,包括燃料消耗、 电力消耗等。
设备利用率:设备利用率是指高炉炼 铁设备在运行时间占总运行时间的比 例,也是衡量运行效率的重要指标。
生产成本:生产成本包括原材料成 本、人工成本、设备折旧等,是衡 量高炉炼铁运行效率的综合指标。
影响运行效率的因素
原料质量:铁矿石、 焦炭等原料的质量 直接影响炼铁效率
备正常运行
产能优化案例
案例背景:某钢铁 公司高炉炼铁产能 不足,影响公司效 益
优化措施:采用先 进的生产工艺和技 术,提高设备利用 率
优化效果:产能提 高20%,成本降低 15%
启示:通过技术创 新和设备升级,可 以有效提高产能和 运行效率
高炉炼铁的运行效率分析
运行效率评估指标
产量:高炉炼铁的产量是衡量运行效 率的重要指标之一。
会影响产能
操作水平:工人的 操作技能和经验对
产能有重要影响
市场需求:市场需 求的变化也会影响
产能
提高产能的措施
优化原料配比:合理 选择铁矿石、焦炭等 原料,提高原料质量
采用先进的冶炼技术: 如富氧鼓风、喷煤等,
提高冶炼效率
改进炉型结构:采用 先进的高炉结构,提 高炉膛温度和热效率
加强设备维护和管理: 定期对高炉设备进行 检查和维护,确保设
480高炉最大利用系数_概述说明以及解释

480高炉最大利用系数概述说明以及解释1. 引言1.1 概述在现代工业生产中,高炉是一种重要的冶金设备,广泛应用于钢铁行业。
然而,在高炉的运行过程中,存在着能源消耗和物料利用率不足的问题。
为了提高高炉的效益和降低生产成本,许多研究机构和企业致力于提高高炉的最大利用系数。
本文将对480高炉最大利用系数进行概述说明和解释。
首先我们将介绍480高炉最大利用系数的定义与意义,包括其作为评估指标的科学性和实用性。
接着,我们将分析影响480高炉最大利用系数的主要因素,包括原料配比与质量控制、燃料选择与燃烧技术以及炉况管理与操作优化。
然后,我们将介绍提高480高炉最大利用系数的方法与实践,包括工艺优化、设备改造与升级以及制度建设与人员培训。
最后,在结论部分,我们将总结文章主要观点和论点,并展望未来480高炉最大利用系数发展的可能性,并提出相关建议。
1.2 文章结构本文共分为五个部分。
首先是引言部分,下面将介绍480高炉最大利用系数的定义与意义。
第二部分将详细讨论影响480高炉最大利用系数的因素。
第三部分将介绍提高480高炉最大利用系数的方法与实践。
在第四部分,我们将总结文章的主要观点和论点,并展望未来480高炉最大利用系数发展的可能性。
最后,在第五部分,我们将提出相关建议。
1.3 目的本文旨在全面了解和探讨480高炉最大利用系数的概念及其应用。
通过深入分析影响其变化的因素,可以帮助企业在生产经营中更好地优化工艺和管理,提高生产效益和资源利用率。
此外,本文还旨在为相关技术人员提供参考,以促进钢铁行业的可持续发展和节能减排工作的推进。
2. 480高炉最大利用系数的定义与意义:2.1 定义:480高炉最大利用系数是指在高炉冶炼过程中,通过优化原料配比、燃料选择和操作管理等手段,使得高炉的生产能力充分发挥,实现高效率、低能耗、环保节能的一个指标。
该系数可以通过测量高炉的产能输出与设计产能之间的比值来计算。
具体而言,将设计产能除以实际产出得到一个百分比值,即为480高炉最大利用系数。
高炉炼铁工序能耗计算方法
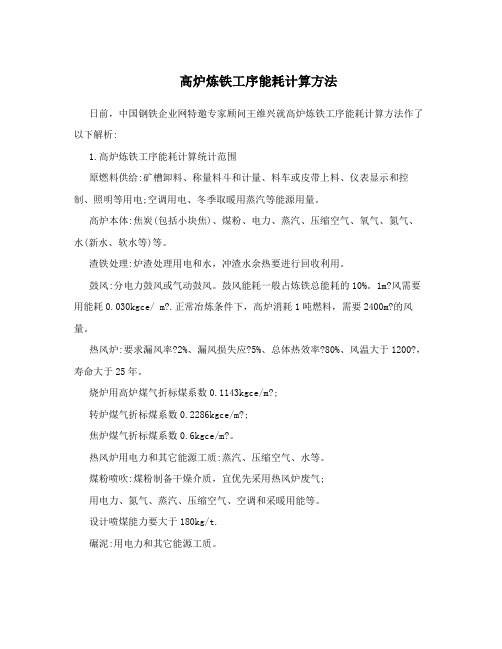
高炉炼铁工序能耗计算方法日前,中国钢铁企业网特邀专家顾问王维兴就高炉炼铁工序能耗计算方法作了以下解析:1.高炉炼铁工序能耗计算统计范围原燃料供给:矿槽卸料、称量料斗和计量、料车或皮带上料、仪表显示和控制、照明等用电;空调用电、冬季取暖用蒸汽等能源用量。
高炉本体:焦炭(包括小块焦)、煤粉、电力、蒸汽、压缩空气、氧气、氮气、水(新水、软水等)等。
渣铁处理:炉渣处理用电和水,冲渣水余热要进行回收利用。
鼓风:分电力鼓风或气动鼓风。
鼓风能耗一般占炼铁总能耗的10%。
1m?风需要用能耗0.030kgce/ m?.正常冶炼条件下,高炉消耗1吨燃料,需要2400m?的风量。
热风炉:要求漏风率?2%、漏风损失应?5%、总体热效率?80%、风温大于1200?,寿命大于25年。
烧炉用高炉煤气折标煤系数0.1143kgce/m?;转炉煤气折标煤系数0.2286kgce/m?;焦炉煤气折标煤系数0.6kgce/m?。
热风炉用电力和其它能源工质:蒸汽、压缩空气、水等。
煤粉喷吹:煤粉制备干燥介质,宜优先采用热风炉废气;用电力、氮气、蒸汽、压缩空气、空调和采暖用能等。
设计喷煤能力要大于180kg/t.碾泥:用电力和其它能源工质。
除尘和环保:主要是电力(大企业环境保护用电力占炼铁用电的30%左右)、水等。
,铸铁机:电力、水等。
扣除项目:回收利用的高炉煤气,热值按实际回收量计算;TRT余压发电量(电力0.1229kgce/kwh)2.炼铁工序能耗计算方法炼铁工序能耗=(C+I+E-R)?T式中:T-合格生铁产量,铸造铁产量要用折算系数进行计算(见表1);C-焦炭(干全焦,包括小块焦)用量。
折热量,28435kJ。
标煤量0.9714kgce/t 焦炭. I-喷吹煤折热量,20908kJ ; 折标煤量0.7143kgce/t原煤。
E-加工能耗(煤气、电、耗能工质等)折标煤量:煤气折标煤系数见热风炉栏目。
电力折标煤系数0.1229kgce/kwh.. 耗能工质折标煤系数:氧气0.1796kgce/m?;氮气0.0898 kgce/kwh. 压缩空气0.040kgce/m?,新水0.257 kgce/kwh软水0.500 kgce/m?,蒸汽0.12 kgce/kwh.R-回收高炉煤气、电力折热量. 高炉煤气折标煤系数0.1143kgce/Nm? 电力折标煤系数0.1229kgce/kwh。
铁冶金学——第五章 高炉能量利用2

5.2.1 炉缸燃烧反应机理及煤气组成
由诸表可见,增加鼓风湿度(加湿鼓风),则煤气中H2、 CO含量增加,N2相对减少;喷吹燃料,其中C-H化合物分解, 使炉缸煤气含H2量显著增加,CO、N2相对降低;富氧鼓风时, 由于N2减少,因而CO相对增加。它们都程度不同的富化了还 原性煤气,对降低焦比和强化高炉都很有效(详见第十章第 五、六、七节)。
5.2.2 炉缸燃烧反应过程的研究
研究炉缸反应过程,是通过测量风口区成分、温度、压 力的变化和渣、铁成分等来进行的。研究工具和方法主要 有水冷取样管,快速摄影、录像机,内窥探测仪,高炉解 剖,模型模拟实验等。
5.2.2 炉缸燃烧反应过程的研究
一、炉缸风口水平煤气成分和温度的变化 研究证明,炉缸燃烧反应过程是逐渐完成的。在风口前, 沿炉缸半径的不同位置上,由于燃烧条件不同,生成的煤 气成分各异。图7-1是所谓炉缸燃烧反应的经典曲线。它 说明以下几个关系。 1. O2与CO2:风口前O2充足,与C激烈燃烧生成大量CO2 〔反应(5-1)〕,O2激烈降低及至消失,CO2迅速升高达 到最大值。
前者为完全燃烧,发生在氧过剩的地方;后者为不完全燃烧, 发生在碳过剩,氧不足的地方。燃烧反应在气-固界面上 进行,即氧(或CO2,H2O)扩散到碳的反应表面,并为 碳原子所吸附,形成CxOy型的复合物,而后CxOy在气相 中O2的冲击下或高温的作用下,再分解为CO2和CO,并 且从反应表面脱附而转移到气相中。
5.2.2 炉缸燃烧反应过程的研究
2. CO2与CO:CO2达最大值后,逐渐降低;已出现的CO 则迅速升高〔反应(5-4)〕,在燃烧带边缘,CO接近达 到理论值34.7%,而向炉缸中心则高达40~50%,甚至更 高,这是由于直接还原反应也产生大量CO的结果。