外轮廓零件加工2
机械制图(含习题集)(第二版)(章 (10)
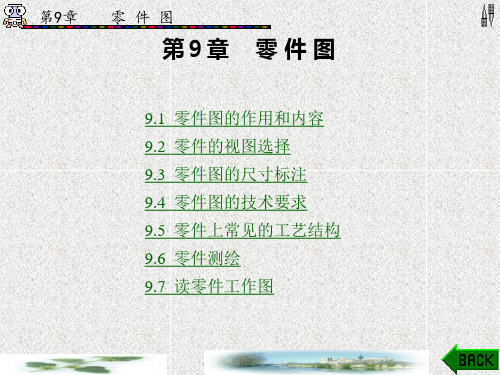
零件图上的尺寸是零件生产、加工、检验的重要依据之一。 标注尺寸时,应做到正确、完整、清晰,工艺合理。关于尺寸 标注的正确性、完整性、清晰性在前几章已经作过介绍,本章 着重介绍合理性问题。所谓合理性,是指标注的尺寸既要能保 证达到设计要求又要便于加工、测量和检验。
零件图上尺寸标注的基本步骤如下所述。
第9章 零 件 图
图9-4 吊钩的工作位置
第9章 零 件 图 2.其他视图的选择 主视图确定后,再按完整、清晰地表达零件各部分结构形
状和相对位置的要求,针对零件内外结构的具体情况,选择其 他必要的视图、剖视、剖面等,表达零件某些方面的结构,并 尽量减少视图的个数,以方便画图和读图。
第9章 零 件 图 9.2.2 典型零件的视图选择
括以下基本内容: (1) 一组图形:正确、清晰地表达出零件的各部分结构形
状。 (2) 一组完整的尺寸:正确、完整、清晰、合理地标注制
造零件和检验零件所需的全部尺寸。 (3) 必要的技术要求:如表面粗糙度、尺寸公差、形位公
பைடு நூலகம்差、热处理及表面处理等。 (4) 标题栏:填写零件的名称、数量、材料、比例、图号
方法如表9-2所示。
第9章 零 件 图
表9-2 常见孔的尺寸标注方法
零件的结构类型
普通注法
旁注法
说明
一般孔 光
精加工孔 孔
锥销孔
“ ”为孔 深符号
钻孔深度为 12,精加工孔 深为 10
“配作”是 指该孔与相邻 零件的同位锥 销孔一起加工
第9章 零 件 图
续表一
零件的结构类型
开槽沉头螺 钉沉孔
普通注法
第9章 零 件 图 1.主视图的选择 主视图是零件图图形的核心,其选择得恰当与否将直接
《数控车削技术训练》电子教案 09-项目九 加工综合件 表9-2-3 左端外轮廓加工程序单

程序 段号
加工程序
O9021 N10 G21 G97 G99; N20 T0101;
N30 M03 S800; N40 G00 X47 Z2;
N50 G71 U2 R1;
N60 G71 P70 Q170 U1 W0.05 F0.2;
N70 G0 X31;
程序说明
程序名(左端外轮廓加工程序) 公制尺寸编程,主轴转速单位 r/min,进给量单位 mm/r。 调用外圆车刀。 主轴正转,转速为 800 r/min。 车刀快速定位到靠近加工的部位(X47,Z2)。 应用 G71 循环粗加工,每次切深 2mm,每次退刀 1mm。 精加工轨迹的第一个程序段号为 N70,最后一个程序段 号为 N170;精加工余量 X 方向 1mm,Z 方向 0.05mm;粗 车进给量为 0.2mm/r。 描述精加工轨迹的第一个程序段。
பைடு நூலகம்
N80 G1 Z0 F0.1;
靠近轮廓起点,设置精车进给量为 0.1mm/r。
N90 N100 N110 N120 N130 N140 N150 N160 N170 N180 N190 N200 N210 N220 N230 N240 N250 N260
G1 X32 Z-0.5; G1 Z-10; G1 X36; G1 X38 Z-11; G1 Z-30; G1 X41 ; G1 X43 Z-31; G1 Z-40; G1 X47; G0 X100 Z200; M5; M0; M3 S1200; T0101; G0 X47 Z2; G70 P70 Q170; G0 X100 Z200; M30;
车 C0.5 倒角。 车φ32 外圆。 车φ32 右侧台阶。 车 C1 倒角。 车φ38 外圆。 车φ38 右侧台阶。 车 C1 倒角。 车φ43 外圆。 描述精加工轨迹的最后一个程序段。 快速退刀到(X100,Z200)的安全位置。 主轴停转。 程序暂停。 主轴正转,转速为 1200 r/min。 调用外圆车刀。 车刀快速定位到靠近加工的部位(X47,Z2)。 精加工左端外轮廓。 快速退刀到(X100,Z200)的安全位置。 程序结束。
2数控铣床加工工艺
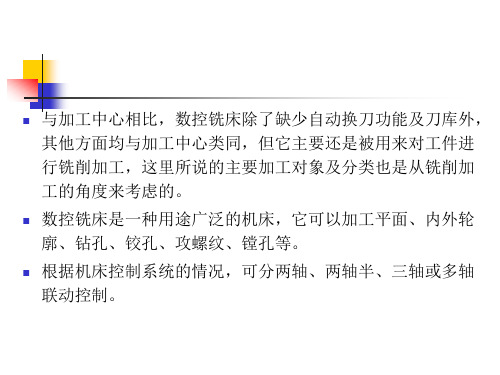
(1)准备功能及辅助功能 (2)机床坐标系及工件坐标系
1.机床坐标系 机床上固有的坐标系。机床坐标系的原点由设计厂家在设
计机床时确定。 一般情况下,铣床原点的位置可在启动机床后,使机床三
个坐标轴的坐标依次运动到其正方向的极限位置确定,机 床三个坐标轴所达到的这个位置就是机床坐标系原点 2.工件坐标系 工件坐标系原点在工件上或在夹具的某一点上,由编程人 员设定,其位置随工件和夹具在机床工作台上的安装位置 而定,所以又叫浮动原点或编程原点,一般在程序开头设 置。
序内往往需要采用不同的刀具和切削用量,对不同的表面 进行加工。 为了便于分析和描述较复杂的工序;在工序内又细分为工 步。下面以加工中心为例来说明工步划分的原则: 1) 同一表面按粗加工、半精加工、精加工依次完成全部加工 表面,按先粗后精加工分开进行。 2) 对于既有铣面又有镗孔的零件,可先铣面后镗孔。 3) 某些机床工作台回转时间比换刀时间短,可采用按刀具划 分工步,以减少换刀次数,提高加工效率。 总之,工序与工步的划分要根据具体零件的结构特点、技 术要求等情况综合考虑。
参考平面
R
工件上表面
主轴顺时针转动 Z
主轴逆时针转动
G85:镗孔循环
• 指令格式:G85 X_ Y_ Z_ R_ F_ K_ LF • G85与G84相同,只是在孔底主轴不反转
G98 初始平面
工件平面
G99 参考平面 Z点
G86:镗削循环
指令格式:G86 X_ Y_ Z_ R_ F_ K_ LF 和G81相同,只是在孔底主轴停,然后用快速返回
二、数控加工零件的工艺性分析
1. 零件图的几何尺寸标注及轮廓的几何要素 (1)要彻底读董图样 (2)要分析透零件的加工工艺性 (3)研究分析零件的精度 (4)研究分析零件的刚性 (5)研究分析零件的定位基准 (6)研究零件的毛坯和材料
《数控编程技术》作业2参考答案

《数控编程技术》作业2参考答案第4章基本功能指令的编程方法一、填空题1、用于控制开关量的功能指令是_______M_______。
2、T0400的含义是____取消4号刀补_________。
3、采用恒线速度控制车削带锥度的外圆时,若线速度为200米/分钟,最高转速限定在1300转/分钟,正确的编程格式为_____f200 f1300____________。
4、直线进给率的单位为______mm/min___________;旋转进给率的单位为__________r/min_______。
5、只有当机床操作面板上的“选择停止键”被按下,才能生效的暂停指令是__M01_______。
二、选择题1、G96 S150 表示切削点线速度控制在(c)。
(A)150 m/min (B)150 r/min(C)150 mm/min(D)150 mm/r2、程序结束,并返回到起始位置的指令是(d)。
(A)M00(B)M01(C)M02(D)M303、()。
(A)M00(B)M01(C)M02(D)M304、当执行M02指令时,机床(b)。
(A)进给停止、冷却液关闭、主轴不停(B)主轴停止、进给停止、冷却液关闭,但程序可以继续执行(C)主轴停止、进给停止、冷却液未关闭、程序返回至开始状态(D)主轴停止、进给停止、冷却液关闭、程序结束三、判断题1、恒线速控制的原理是当工件的直径越大,进给速度越慢。
(对)2、有些车削数控系统,选择刀具和刀具补偿号只用T指令;而铣削数控系统,通常用T指令指定刀具,用D、H代码指定刀具补偿号。
(对)3、用M02和M30作为程序结束语句的效果是相同的。
(错)四、简答题1、指令M00和M01有什么相同点?区别是什么?1. M00:程式停止.程式自動執行時.當執行到M00時,機台將停止執行下一動作。
2. M01:選擇性程式停止.與M00功能相同:當面板功能鍵打開.程式執行到M01時會停止,如功能鍵不打開則不執行。
端面切削循环指令G94讲解

限定最高转速2000r/min
G96 S200
启用恒线速度功能,切削速度为200m/min
G01 X40.0 F0.08;
Z-5.0; X0 Z0;
精车端面轮廓
G00 X61.0 Z2.0;
(转下页)
项目四 内、外轮廓加工
刀具 N220 N230 N240 N250
1号:93°端面车刀
G97 S500;
(粗车时主轴转速n为 500r/min,进给量f为 0.15mm/r)
图例
粗车斜端面,Z向留 0.3mm精加工余量
(粗车时主轴转速n 为500r/min,进给量f为 0.15mm/r)
(转下页)
项目四 内、外轮廓加工
步骤
图例
完成轮廓的精加工 (精车选择恒线速功 能,转速n为200m/min, 最高转速限2000r/min, 进给量f为0.08mm/r)
取消恒线速度功能
G00 X100.0 Z100.0;
M9;
程序结束部分
M30;
为保证零件端面加工的表面粗糙度要求,在精加工中 使用恒线速度功能编程。
项目四 内、外轮廓加工
三、加工准备
选用的机床为配备FANUC 0i系统的CKA6140型数控车床。
毛坯为φ60mm×22mm的圆钢。刀具使用机夹端面车刀。量具
3
进给量 背吃刀量 加工内容 主轴转速
(mm/r) (mm)
粗车端面 500r/min
0.15
2
精车端面 1000m/min 0.08
0.3
项目四 内、外轮廓加工
二、程序编制 任务2参考程序
刀具
1号:93°端面车刀
程序 段号
加工程序 O4020;
机械工程制图零件图尺寸标注2

§5 零件图上技术要求的注写
一组视图:结构形状
完整的尺寸:大小
技术要求:保证加工制造零件时的精度,满足零
件的使用性能。
零件图上的技术要求一般包括:
①表面质量
②极限与配合 ③形状和位置公差 ④材料及热处理
控制零件制 造质量的决 定性因素
一.表面质量
1.表面质量
表面质量是一种状况,包括粗糙度、波纹度、加工纹理等 ,主要的表面质量是表面粗糙度。 表面粗糙度指零件的加工表面上具有的较小间距的峰谷所 形成的微观几何形状特性。
二、标注尺寸注意事项
4.不能注成封闭的尺寸链
A
B
C
A
C
封闭尺寸链
应设置开口环
二、标注尺寸注意事项
5.应考虑测量方便 加工阶梯孔:一般是先做成小孔,然后依次加 工出大孔。因此,在标注轴向尺寸时,应从端 面标注大孔的深度,以便测量。
B
C
不好!
A
C
好!
二、标注尺寸注意事项
5.应考虑测量方便
另外,由设计基准注出中心至某面的尺寸, 不易测量时,若这些尺寸对设计要求影响不
(过盈配合)
H6 H6 s9 t9
H7 H7 H7 H7 H7 H7 H7 s6 t6 u6 v6 x6 y6 z6
H8 H8 H8 s7 t7 u7
基轴制:基本偏差为一定的轴的公差带与不同基 本偏差的孔的公差带形成各种配合的一种制度。
基准轴的上偏差为零,并用代号h表示。如 F7/h6、G7/h6、K8/h7等都属于基轴制的配合。
件具有互换性,不要求零件的尺寸做得绝对准确, 而只是要求在一个合理的范围内。这种允许尺寸的 变动量,称为尺寸公差(简称公差)。
3.基本概念
任务6 具有非圆曲线轮廓的零件加工编程与操作第2版(FANUC)

能 报
4.手动安装φ20mm粗加工两刃立铣刀至主轴。
国
5.用铣刀直接对刀,将X、Y对刀值输入G54地址,设置工件坐标系零点偏置 值,G54地址中的Z地址须为0。在每把刀的刀补界面输入Z对刀值及刀具半径补偿
值。工件坐标系的原点设在工件上表面的对称中心。
1166
四、任务实施
勤 学
(二)零件加工
苦
6.输入程序,并反复检查。检查无误后,自动状态下进行外轮廓粗加工。
勤 学 苦 练
技 能
任务六 具有非圆曲线轮廓的零件
报
加工编程与操作
国
11
一、任务导入
勤 (一)任务描述
学
使用FAUNC系统数控铣床,对如图2-40所示的非圆曲线
苦
练
类零件进行编程及加工。
技 能 报 国
图2-40 二维椭圆零件
22
一、任务导入
勤
学 (二)知识目标
苦 1.掌握FANUC数控系统宏指令的使用与编程。 练 2.掌握FANUC数控系统条件转移或循环语句在非圆曲线轮廓编
抬刀,取消刀具长度补偿,回到机床原点
1133
四、任务实施
勤 (一)编写零件加工程序
学
表2-37 加工主程序
苦
N80 M00;
(机床动作暂停,手工装φ20mm 三刃立铣刀)
练
N90 M03 S500 G00 X62. Y5.; (设置T2主轴转速,快移至加工定位点,)
N100 G01 G43 Z5. F1000 H02; 带入刀具长度补偿,下移至工件上5mm处
练
7.粗加工完毕后,机床暂停,手动测量工件,如数据与理想状态相符,则不
需修改精铣刀刀补值。
2机械零件的钳加工课程标准

10.錾子的使用方法及使用注意事项
11.锉刀的类型及使用范围
12.锉刀的使用方法及使用注意事项
13.去毛刺的方法
14.用砂纸抛光的方法
15.开瓶器的质量分析及评价方法
16.现场5s管理规程7.对工作完成情况的评价
一、评价形式
1.自我评价:学习准备及计划实施的学习效果,工作页填写情况
建议课时
教学建议
与说明
学习任务1:开瓶器的制作
1.能通过各种渠道获取信息,并向老师咨询信息的可靠性并表述出所获取开瓶器的材料、价格、形状信息
2.能绘制零件草图
3.能在毛坯上利用划线工具根据样板描绘出起瓶器轮廓
4.能安全使用手工工具或设备去除工件余料
5.能够安全使用榔头击打錾子进行錾削
6.能正确使用台虎钳夹紧零件
5.能规范使用钻床,合理选择钻头对孔进行加工,并能正确保养钻床。
6.能正确使用游标卡尺、刀口直尺、刀口角尺对錾口榔头进行检测,并准确记录测试结果。
7.能按加工工艺步骤对錾口榔头进行加工。并用专业术语进行交流。
8.能对錾口榔头进行淬火处理。
9.能根据现场管理规范要求,清理场地,归置物品并按环保要求处理废弃物。
机电一体化技术专业基本技能培养课程标准
课程名称
机械零件的钳加工
基准学时
390
工作任务描述
机电一体化技术人员根据零件加工图,手工操作钳工常用工量具及钻床等,通过划线、锯削、锉配、刮削、研磨、钻孔、扩孔、锪孔、铰孔、攻螺丝和套螺纹等进行零件的内、外轮廓及孔等加工。在工作过程中,技术人员以小组合作或独立工作的形式,使用专用软件和工具,遵守“6S”管理的工作要求,自觉安全文明工作,并填写工作记录,保存相关资料。
- 1、下载文档前请自行甄别文档内容的完整性,平台不提供额外的编辑、内容补充、找答案等附加服务。
- 2、"仅部分预览"的文档,不可在线预览部分如存在完整性等问题,可反馈申请退款(可完整预览的文档不适用该条件!)。
- 3、如文档侵犯您的权益,请联系客服反馈,我们会尽快为您处理(人工客服工作时间:9:00-18:30)。
N230 G00 G40 X100. Z100. ;快速退刀至换刀点,取消刀尖半径补偿
N240 T0200 ;取消2号刀补
N250 M30 ;主程序结束并返回程序开始
8、固定形状粗车复合循环指令G73
固定形状粗车循环指令G73适用于毛坯轮廓形状与零件轮廓形状基本接近的铸、锻毛坯件。走刀路线如图1-37所示
指定圆心I、K
指定半径R
绝对方式
G03 X40. Z-30. I0 K-5. F0.1
G03 X40. Z-30. R5. F0.1
增量方式
G03 U10. W-5. IO K-5. F0.1
G03 U10. W-5. R5. F0.1
注意:
①R也有正负之分,当圆弧所对的圆心角α≤180°时,R取正值;当圆弧所对的圆心角α≥180°时,
编程
实例
讲解
教学
过程
G90锥面切削循环
注意:
①车削前,必须用G00设立循环定位起点,其坐标值一般可按如下简便公式计算:
X定 =2D大端 - d小端 ,Z定一般取为1~3 mm。
②编程时,应注意R的符号,确定的方法是:锥面起点坐标X值大于终点坐标X值时为正,反之为负,具体形式如图4-22所示。
③计算R的数值时,是利用切削起、终点的X坐标值,而不是锥体大、小端直径值,其计算公式为:R=(X起-X终)/2,而不是R=(D大-d小)/2。
注意:
①使用G71时,零件沿X和Z方向必须是单调递减或单调递增。
②顺序号“ns”和“nf”之间的程序段所包含的任何F、S、T功能都被忽略,而在G71程序段中的F、
S、T功能才有效。注意:S、T指令可与G71指令分段书写。
例10、如图所示,利用G71编制加工程序。
分析:根据零件加工特点,设程序起点如图所示。粗加工时,被吃刀量为3mm,进给量为0.3mm/r,主轴转速为600r/min;精加工时,余量X向为1mm(直径值),Z向为0.2mm,进给量为0.1mm,主轴转速为1000r/min 。
N50 G71 P60 Q170 U1. W0.2 F0.3 ;精车余量:X向为1mm,Z向为0.2mm,
N60 G00 G42 X0 ;快速至精车起刀点,调用刀尖半径右补偿
N70 G01 Z0 F0.3 ;以工进速度靠近工件
N80 G03 X20. Z0 R10. F0.1 ;加工SR10的半球
黑板画图+
定位循环起点P0(80,2)。
经计算得,A点坐标为(18,2),即X起= 18 ; 又由图知X终= 50 ,根据公式R=(X起-X终)/2,得R = -16 。其加工程序见下表。
画图
讲解
教学
过程
O0006;程序名
N10 G00 X100. Z100. T0101;快速运动到程序起点,换1号刀并调用1号刀补
R取负值。
②用R编程时,只适用于非整圆的圆弧插补,即圆弧所对的圆心角α<360°;而对于整圆加工只能
用终点、圆心法编程。
画图
讲解
教学
过程
例9:加工如图所示零件,刀尖从工件原点O开始对轮廓进行精加工,编制其加工程序段。
圆弧加工实例
分析:两圆弧相切于A点,在直角三角形AEF中,已知AF = 28 ,EF = 22 ,根据AE2+ EF2= AF2,得AE= 17.32 ,所以A颠得Z坐标为ZA= -(28+17.32)=-45.32 。由此得到圆弧起点坐标为: O(0,0),A(44,-45.32) ,B(44,-75)。
N80 X50. R-16. ;锥面第四次循环切削
N90 G00 X100. Z100.;快速退刀至换刀点
N100 T0100;取消刀补
N110 M30;主程序结束并返回程序开始
3、圆弧加工工艺路线的确定
在圆弧车削中,如果就把圆弧加工出来,吃刀量太大,容易打刀,所以,试车削圆弧时,需要多刀加工,先将大余量切除,最后精车得到所需圆弧。
仿真软件演示讲解
教学
过程
N90 G01 X28. ;加工Ф30端面
N100 X30. Z-1. F0.1 ;加工C1倒角
N110 Z-15. ;加工Ф30外圆
N120 X60. Z-35. ;加工锥
N130 Z-50. ;加工Ф60外圆
N140 X70. ;加工Ф80端面
N150 G02 X80. Z-55. R5. F0.1 ;倒R5圆角
G73指令格式为:
G00 XαZβ
G73 UΔiWΔkRd
G73 PnsQnfUΔuWΔwFfSsTt
程序段中各字母含义为:
Δi— 粗车时径向切除的总余量,即各段余量中最大余量,半径值,单位为mm。
Δk— 粗车时轴向切除的总余量。
d— 重复加工次数。
注意:使用G73时,不强调零件沿X和Z方向单调递减或单调递增。
其他字母含义与G71相同,但G73是仿行循环,每一道的切削路线的轨迹形状与零件轮廓形状是相同的,只是位置不同。
黑板画图+
仿真软件演示讲解
教学
过程
例12、如图所示, 利用G73编制加工程序。
N160 G01 Z-75. ;加工Ф80外圆
N170 X90. ;加工Ф85端面
N180 G00 X100. Z100. ;快速退刀至换刀点
N190 T0100 ;取消1号刀补
N200 T0202 M03 S1000 ;换2号精车刀,调转速为1000r/min
N210 G00 X90. Z12. ;快速运动到循环起点(90,12)处
G71指令格式为:
G00 XαZβ
G71 UΔdRe
G71 PnsQnfUΔuWΔwFfSsTt
程序段中各字母含义为:
α、β— 粗车循环起刀点位置坐标。
在车削圆柱毛坯料粗车外径时,α值应比毛坯直径稍大1~2mm,β值应离毛坯右端面2~3mm;在镗削圆筒毛坯料粗镗内径时,α值应比毛坯直径稍小1~2mm,β值应离毛坯右端面2~3mm.
画图
讲解
教学
过程
例:如下图,G00、G01编制精加工程序
O0005;程序名
N10 G00 X100. Z100. T0101;快速运动到程序起点,换1号刀
N20 M03 S500;主轴正转,转速为500r/min
N30 G00 X45. Z2.;快速运动到起刀点(40,2)处
N40 G01 Z0 F0.2;工进至端面
G90指令格式为:
G00 XZ
定位点坐标
圆锥面切削终点相对于循环起点的增量坐标值 进给速度
G90 X(U)Z(W)RF;
圆锥面切削终点的绝对坐标 值 圆锥切削起点与切削终点的半径差
如图1-21所示,刀具从循环起点(当前刀具所在位置)开始按矩形路线循环,最后又回到循环起点,图中1(R)、4(R)表示刀具以G00速度快速运动,2(F)、3(F)表示刀具以F指定的进给速度切削加工,其加工顺序按1 2 3 4进行。
N20 M03 S500;主轴正转,转速为500r/min
N30 G00 X80. Z2.;快速运动到循环起点(60,2)处
N40 G90 X72.5 Z-30. R-16. F0.3;锥面第一次循环切削
N50 X65. R-16. ;锥面第二次循环切削
N70 X57.5 R-16. ;锥面第三次循环切削
1、锥面加工工艺确定
锥面车削一般有三种路线,如图所示。
第一如图1所示,矩形路线,这种方法计算麻烦,在编程中很少采用。
第二如图2所示,平行母线路线,即和锥体母线平行循环车削,这种方法适用于车削大、小两端直径之差较大的圆锥面。
第三如图3所示,三角形路线,这种方法适用于车削大、小两端直径之差较小的圆锥面。
②不论是用绝对值编程还是用增量值编程,I、K均为圆心在X、Z轴方向上相对于圆弧起点的坐标增量(等于圆心坐标减去圆弧起点的坐标);I为半径值。
6、终点/圆弧半径编程
G02/G03指令格式为:
圆弧终点相对圆弧起点的增量坐标 进给速度
G02/G03 X(U)Z(W)RF;
圆弧终点绝对坐标圆弧半径
例8:如图所示,刀尖从A点运动到B点,写出圆弧插补的程序段。
教案
课题
外轮廓零件加工2
备注
授课
课时
4
课型
理实
一体化
教具
黑板+软件
准备
教具
清点
学生
教学
目标
1、了解外轮廓零件的数控车削工艺,正确选用工、夹、量、刀具;
2、掌握数控程序的基本结构,正确运用编程指令编制外轮廓零件的数控加工程序;
3、掌握数控车床的操作流程,培养操作技能和文明生产的习惯。
教学
要求
1、掌握外轮廓零件的编程,并能完成外轮廓零件的工艺分析及加工;
值得注意的是,圆弧插补顺、逆方向是在国际标准机床坐标系(即后置刀架坐标系)下规定的,由于数控车削的加工对象为回转体类零件,因此,只要按其中某一坐标系判定出G02或G03,不管是前置刀架数控车床还是后置刀架数控车床,编程指令一致。如下图所示。
画图
讲解
教学
过程
G02/ G03的插补方向
后置刀架前置刀架
5、终点、圆心坐标编程
2、会对零件进行精度检测;
教学
内容
1、圆弧、沟槽、螺纹编程与加工;
2、常用外轮廓循环指令代码;
3、外轮廓加工精度控制与误差纠正措施;
教学
过程
导入新课:
锥面与圆弧加工是车削加工中最常见的的加工之一,锥面与圆弧车削走刀路线比外圆和端面复杂,且形式多样,因此,在编制锥面与圆弧加工程序之前,必须确定最佳加工路线。
G02/G03指令格式为:
圆弧终点相对圆弧起点的增量坐标 进给速度