复合材料的分层研究
复合材料用有限元分析

复合材料用有限元分析引言复合材料是由不同类型的材料组合而成的,具有优异的力学性能和轻质化的特点,在航空航天、汽车工程、建筑结构等领域得到广泛应用。
有限元分析是一种常用的工程分析方法,可用于预测复合材料结构在受力过程中的应力和变形情况。
本文将介绍复合材料用有限元分析的基本原理、建模过程、分析方法和结果解读。
有限元分析基本原理有限元分析基于有限元法,将复杂的结构分割成许多简单的单元,再利用数学方法求解这些单元的力学行为,最终得出整个结构的应力和变形情况。
复合材料的有限元分析一般采用3D固体单元或板单元,考虑复合材料的各向异性和层合板的分层结构。
有限元分析的基本原理可以总结为以下几个步骤:1.确定有限元模型:–根据复合材料结构的几何形状和材料性质,选择适当的有限元单元类型。
–确定网格划分方案,将结构划分为单元网格。
–确定边界条件和加载方式,包括约束条件和外部加载。
2.确定单元性质:–根据复合材料的材料力学性质,将其转化为有限元单元的材料刚度矩阵。
–考虑各向异性和分层结构,将材料刚度矩阵进行相应的转换。
3.确定单元相互连接关系:–根据结构的几何体系,确定单元之间的连接关系,包括单元之间的约束和边界条件。
4.求解方程组:–根据单元的刚度矩阵和边界条件,建立整个结构的刚度矩阵。
–考虑加载情况,求解结构的位移和应力。
5.结果后处理:–分析结构的应力和变形分布,评估结构的安全性和性能。
–对结果进行解读和优化。
复合材料有限元分析的建模过程复合材料的有限元分析建模过程与传统材料的有限元分析类似,但在材料性质和单元连接方面存在一些特殊性。
下面是复合材料有限元分析的建模过程的简要步骤:1.几何建模:–根据实际结构的几何形状,利用建模软件(如Solidworks或CATIA)进行3D建模。
–根据复合材料的分层结构,将各层材料的几何形状分别绘制。
2.材料定义:–根据复合材料的材料属性,定义合适的材料模型和参数。
–考虑复合材料的各向异性和分层结构,定义材料的力学参数。
高强玻纤复合材料的Ⅰ型断裂韧性仿真与试验分析

(b)断裂韧性 G=584J/m2
图 6 载荷 - 张开位移曲线
(a)0.25s
(b)0.5s
(c)0.75s
(d)1.0s
图 7 裂纹扩展过程
只有最终稳定区的数值。试验的最大载荷为 57.75N,仿真 的最大载荷为 61.76N,误差为 6.9%,同时通过对比断裂 韧性 G Ⅰ c 为 720J/m2 与 584 J/m2 的试验与仿真的结果(误 差分别为 8% 与 13.8%),试验与仿真吻合较好。
=
Kn
Ks
ε n
ε
s
tt
Kt ε t
(1)
式中,变量 tn、ts、tt 分别为界面法向和面外剪切方向的 名义应力;变量 εn、εs、εt 代表相应的名义应变,Kn、 Ks、Kt 为对应方向的刚度值。
本文层间单元损伤起始判据采用二次名义应力准则判
据,准则判据公式见公式 2。当法向与 2 个面外剪切方向的
◎ 61 万~ 200 万
中国科技信息 2021 年第 14 期·CHINA SCIENCE AND TECHNOLOGY INFORMATION Jul.2021 DOI:10.3969/j.issn.1001- 8972.2021.14.029
可实现度
可替代度
行业曲线
link
appraisement
应力比的平方和达到 1 时,层间损伤产生:
tn tn0
2
+
ts ts0
2
+
tt tt0
2
= 1
(2)
式中,变量 tn、ts、tt 分别为 1 个界面法向和 2 个面外 剪切方向的瞬时应力;变量 t0n、t0s、t0t 分别为 1 个界面法向和 2 个面外剪切方向的最大名义应力。
《复合材料》课程笔记

《复合材料》课程笔记第一章:复合材料概述1.1 材料发展概述复合材料的发展历史可以追溯到古代,人们使用天然纤维(如草、木)与土壤、石灰等天然材料混合制作简单的复合材料,例如草绳、土木结构等。
然而,现代复合材料的真正发展始于20世纪40年代,当时因航空工业的需求,发展了玻璃纤维增强塑料(俗称玻璃钢)。
此后,复合材料技术经历了多个发展阶段,包括碳纤维、石墨纤维和硼纤维等高强度和高模量纤维的研制和应用。
70年代,芳纶纤维和碳化硅纤维的出现进一步推动了复合材料的发展。
这些高强度、高模量纤维能够与合成树脂、碳、石墨、陶瓷、橡胶等非金属基体或铝、镁、钛等金属基体复合,形成了各种具有特色的复合材料。
1.2 复合材料基本概念、特点复合材料是由两种或两种以上不同物质以不同方式组合而成的材料,它可以发挥各种材料的优点,克服单一材料的缺陷,扩大材料的应用范围。
复合材料具有以下特点:- 重量轻:复合材料通常具有较低的密度,比传统材料轻,有利于减轻结构重量。
例如,碳纤维复合材料的密度仅为钢材的1/5左右。
- 强度高:复合材料可以承受较大的力和压力,具有较高的强度和刚度。
例如,碳纤维复合材料的拉伸强度可达到3500MPa以上。
- 加工成型方便:复合材料可以通过各种成型工艺进行加工,如缠绕、喷射、模压等。
这些工艺能够适应不同的产品形状和尺寸要求。
- 弹性优良:复合材料具有良好的弹性和抗冲击性能,能够吸收能量并减少损伤。
例如,橡胶基复合材料在受到冲击时能够吸收大量能量。
- 耐化学腐蚀和耐候性好:复合材料对酸碱、盐雾、紫外线等环境因素具有较好的抵抗能力,适用于恶劣环境下的应用。
例如,聚酯基复合材料在户外长期暴露下仍能保持较好的性能。
1.3 复合材料应用由于复合材料的优异性能,它们在各个领域得到了广泛的应用。
主要应用领域包括:- 航空航天:飞机、卫星、火箭等结构部件。
复合材料的高强度和轻质特性使其成为航空航天领域的重要材料,能够提高飞行器的性能和燃油效率。
复合材料的界面粘结性能研究
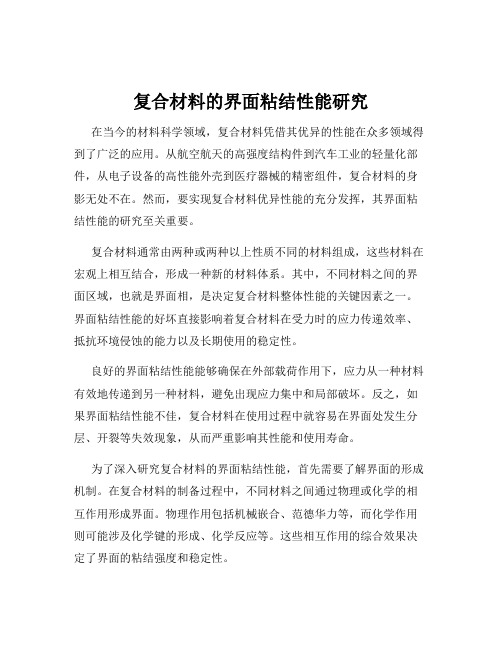
复合材料的界面粘结性能研究在当今的材料科学领域,复合材料凭借其优异的性能在众多领域得到了广泛的应用。
从航空航天的高强度结构件到汽车工业的轻量化部件,从电子设备的高性能外壳到医疗器械的精密组件,复合材料的身影无处不在。
然而,要实现复合材料优异性能的充分发挥,其界面粘结性能的研究至关重要。
复合材料通常由两种或两种以上性质不同的材料组成,这些材料在宏观上相互结合,形成一种新的材料体系。
其中,不同材料之间的界面区域,也就是界面相,是决定复合材料整体性能的关键因素之一。
界面粘结性能的好坏直接影响着复合材料在受力时的应力传递效率、抵抗环境侵蚀的能力以及长期使用的稳定性。
良好的界面粘结性能能够确保在外部载荷作用下,应力从一种材料有效地传递到另一种材料,避免出现应力集中和局部破坏。
反之,如果界面粘结性能不佳,复合材料在使用过程中就容易在界面处发生分层、开裂等失效现象,从而严重影响其性能和使用寿命。
为了深入研究复合材料的界面粘结性能,首先需要了解界面的形成机制。
在复合材料的制备过程中,不同材料之间通过物理或化学的相互作用形成界面。
物理作用包括机械嵌合、范德华力等,而化学作用则可能涉及化学键的形成、化学反应等。
这些相互作用的综合效果决定了界面的粘结强度和稳定性。
目前,研究复合材料界面粘结性能的方法多种多样。
其中,微观分析技术如扫描电子显微镜(SEM)、透射电子显微镜(TEM)等可以帮助我们直观地观察界面的微观结构,包括界面的形貌、粗糙度、相分布等。
通过这些观察,我们能够了解界面的物理结合情况,并推测其对粘结性能的影响。
此外,力学性能测试也是评估界面粘结性能的重要手段。
常见的测试方法有拉伸试验、剪切试验、弯曲试验等。
通过这些试验,可以获得复合材料的强度、模量、断裂伸长率等力学性能参数,从而间接反映界面的粘结强度。
同时,化学分析方法如 X 射线光电子能谱(XPS)、傅里叶变换红外光谱(FTIR)等可以用于检测界面处的化学组成和化学键的变化,进而揭示界面的化学结合机制。
碳纤维复合材料力学性能研究进展

包 装 工 程第44卷 第21期 ·36·PACKAGING ENGINEERING 2023年11月收稿日期:2023-05-30基金项目:国家自然科学基金(12172344) *通信作者碳纤维复合材料力学性能研究进展段裕熙,张凯*,徐伟芳,陈军红,龚芹(中国工程物理研究院总体工程研究所,四川 绵阳 621999)摘要:目的 综述碳纤维复合材料这一热结构材料的力学性能研究进展,推进碳纤维复合材料的研制和应用。
方法 采用文献调研法,梳理和汇总国内外有关碳纤维复合材料力学性能的研究内容,对二维复合材料、针刺复合材料及三维编织复合材料3种结构进行性能影响因素分析。
结论 影响碳纤维复合材料静态和动态力学性能的因素主要有温度、应变率、密度等,提出应进一步开展碳纤维复合材料在多因素耦合及高温动态性能方面的研究。
关键词:碳纤维复合材料;静态力学性能;动态力学性能;三维编织复合材料 中图分类号:TB332 文献标识码:A 文章编号:1001-3563(2023)21-0036-10 DOI :10.19554/ki.1001-3563.2023.21.005Mechanical Property of Carbon Fiber CompositesDUAN Yu-xi , ZHANG Kai *, XU Wei-fang , CHEN Jun-hong , GONG Qin(Institute of Systems Engineering, China Academy of Engineering Physics, Sichuan Mianyang 621999, China) ABSTRACT: The work aims to explore recent advancements in the mechanical properties of carbon fiber composites for thermal structural applications, with the objective of promoting the development and utilization of carbon fiber composites. Through a comprehensive literature review, the current research status on the mechanical properties of carbon fiber composites was summarized, and the factors affecting the static and dynamic mechanical properties of 2D composites, needled composites, and 3D woven composites were analyzed. The results indicate that factors affecting the static and dynamic mechanical properties of carbon fiber composites include temperature, strain rate, density, et al. And further investigations are necessary in multi-factor coupling and high temperature dynamic properties of carbon fiber composites. KEY WORDS: carbon fiber composite; static mechanical properties; dynamic mechanical properties; three-dimensional weaving composite碳纤维由有机纤维经过一系列热处理转化而成,它是含碳量高于90%的无机高性能纤维,既具有碳材料的固有本征,又兼具纺织纤维的柔软可加工性。
一种复合材料层合板分层扩展的修正内聚力模型

JournalofMechanicalStrength2021ꎬ43(5):1262 ̄1266DOI:10 16579/j.issn.1001 9669 2021 05 035∗20200713收到初稿ꎬ20200905收到修改稿ꎮ∗∗贾云龙ꎬ男ꎬ1992年5月生ꎬ河南周口人ꎬ汉族ꎬ航天行云科技有限公司主管设计师ꎬ硕士ꎬ主要从事振动与强度研究ꎮ一种复合材料层合板分层扩展的修正内聚力模型∗ACORRECTEDCOHESIVEZONEMODELINTHEINTERLAMINARFRACTUREOFCOMPOSITE贾云龙∗∗1㊀㊀徐㊀琳2㊀㊀项㊀斌1(1.航天行云科技有限公司ꎬ武汉430040)(2.武汉理工大学高性能船舶技术教育部重点实验室ꎬ武汉430063)JIAYunLong1㊀XULin2㊀XIANGBin1(1.LeobitTechnologyCo.ꎬLtd.ꎬWuhan430040ꎬChina)(2.KeyLaboratoryofHighPerformanceShipTechnologyofMinistryofEducationꎬWuhanUniversityofTechnologyꎬWuhan430063ꎬChina)摘要㊀针对复合材料的分层现象ꎬ考虑初始断裂韧性和裂尖材料损伤的影响ꎬ提出了一种修正内聚力模型ꎬ并给出了内聚力模型参数确定的方法ꎮ根据相关试验ꎬ采用该方法ꎬ获得了考虑初始断裂韧性和裂尖材料损伤的内聚力模型ꎬ基于该内聚力模型对试验进行了仿真分析ꎮ结果表明ꎬ与仅考虑初始断裂韧性获取的内聚力模型相比ꎬ考虑初始断裂韧性和裂尖材料损伤的内聚力模型ꎬ可以更加准确地模拟复合材料的分层现象ꎮ关键词㊀复合材料㊀内聚力模型㊀裂纹扩展㊀数值仿真中图分类号㊀TB332Abstract㊀Inordertoconsiderbothmaterialdamageofthecracktipandtheinitialfracturetoughnessꎬacorrectedcohesivezonemodel(CZM)thatconsiderstheinfluenceofmaterialdamageoftheinitialcrackpropagationhasbeenproposed.Thecorrectedcohesivezonemodeobtainedfromtheendnotchflexure(ENF)testhasbeenimplementedintheABAQUS/Standard.Theresultsshowthatitisnecessarytoconsiderbothmaterialdamageofthecracktipandtheinitialfracturetoughnessꎬandthecorrectedcohesivezonemodecanaccuratelysimulatethecrackpropagation.Keywords㊀CompositeꎻCohesivezonemodeꎻCrackpropagationꎻFEMCorrespondingauthor:JIAYunLongꎬE ̄mail:whutjiayunlong@foxmail.comꎬTel:+86 ̄27 ̄59393300Manuscriptreceived20200713ꎬinrevisedform20200905.㊀㊀引言复合材料结构由于具有高比模量㊁高比强度㊁优良的能量吸收性能㊁耐腐蚀性ꎬ越来越广泛地应用于船舶㊁航空航天等领域ꎮ层合复合材料结构㊁夹芯复合材料结构㊁胶接复合材料结构等受到了广泛关注[1 ̄8]ꎮ在复合材料结构的服役期间ꎬ材料界面的初始缺陷或应力奇异点ꎬ使复合材料结构的界面处极易产生分层破坏ꎬ导致复合材料结构的失效[9 ̄13]ꎮ目前ꎬ内聚力模型(CZM)广泛地用于研究复合材料分层的现象ꎮ内聚力模型使用界面应力与界面相对位移(Traction ̄Separation)描述复合材料的界面分层现象ꎮ通过选择合理的参数ꎬ内聚力模型可以很好地模拟复合材料的分层现象[14 ̄15]ꎮ对于复合材料II型界面分层现象ꎬ1982年RussellAJ和StreetKN利用端部缺口弯曲(ENF)试验进行了研究[16]ꎮ根据端部缺口弯曲试验ꎬ基于线弹性断裂力学的分析表明ꎬ随着预置的裂纹长度的变化ꎬII型裂纹的初始断裂韧性也随着变化[17]ꎮ基于内聚力模型ꎬ对端部缺口弯曲试验的分析表明ꎬII型裂纹的初始断裂韧性和预置裂纹的长度无关[18]ꎮ当裂纹扩展时ꎬ裂纹尖端附近材料产生损伤ꎬ这种损伤对于复合材料的分层现象不可忽视[19][20]2443 ̄2455ꎮ因此ꎬ没有考虑裂纹尖端附近材料损伤的线弹性断裂力学就不适用了ꎮ在研究复合材料II型分层现象的端部缺口弯曲试验中ꎬ断裂韧性的准确计算ꎬ须考虑裂尖处的材料损伤ꎮ内聚力模型是一种简单有效考虑裂尖材料损伤的方法[21]ꎮ基于端部缺口弯曲试验ꎬ文献[22]473 ̄487对II型裂纹进行了研究ꎮ文献[23]174 ̄181采用内聚力模型对该试验进行了有限元模拟ꎬ指出双线性内聚力模型㊀第43卷第5期贾云龙等:一种复合材料层合板分层扩展的修正内聚力模型1263㊀㊀不能模拟II型裂纹的扩展ꎮ考虑到裂尖材料损伤和初始断裂韧性ꎬ提出了一种确定内聚力模型参数的方法ꎮ基于相关试验结果ꎬ采用该方法得到了考虑初始断裂韧性和裂尖材料损伤的内聚力模型ꎮ基于该内聚力模型ꎬ采用商业有限元软件Abaqusꎬ对试验现象进行了仿真ꎮ结果表明ꎬ较其他方法得到的内聚力模型ꎬ该内聚力模型可以更准确地模拟复合材料结构的分层现象ꎮ1㊀理论基础1 1㊀内聚力模型在使用内聚力模型进行复合材料分层现象的研究中ꎬ双线性内聚力模型和梯形内聚力模型是比较常用的ꎬ如图1所示ꎮ图1㊀常用内聚力模型Fig.1㊀ThecommonformsofCZM在初始加载阶段ꎬ内聚力τ与界面相对位移δ∗成线性关系ꎻ当内聚力τ等于内聚力强度τC时ꎬ界面材料的刚度随着界面相对位移的增加开始衰减ꎻ当界面的相对位移等于界面相对位移临界值δf时ꎬ界面材料彻底失效ꎬ刚度变为零ꎮ应力位移曲线所围成的面积等于断裂韧性GIIcꎮ对于复合材料分层现象ꎬ断裂韧性通常随裂纹扩展而逐渐增加ꎬ可以用R曲线表示ꎬ如图2所示ꎮ结合内聚力模型ꎬ描述复合材料分层现象的R曲线可做如下[23]174 ̄181GIIδ∗()=GIIcꎬini+ʏδ∗0τδ()dδ(1)式中ꎬτ为裂尖材料损伤区的剪应力ꎻGIIcꎬini为界面材料的初始断裂韧性ꎻ裂尖位置的界面相对位移为δ∗ꎻδ是裂尖材料损伤区的界面相对位移ꎮ根据公式(1)即可得到内聚力模型[24]τδ∗()=∂GII∂δ∗(2)㊀㊀当试验获取GII ̄δ∗曲线后ꎬ根据公式(2)就可得到描述复合材料分层现象的内聚力模型ꎮ图2㊀R曲线示意图Fig.2㊀AschematicshapeofR ̄curvebehavior1 2㊀ENF试验端部缺口弯曲试件如图3所示ꎮ试件预置裂纹的长度为aꎬ宽度为bꎬ长度为2Lꎮ试件材料为等厚度单向层合板ꎬ纤维方向沿试件长度方向ꎮP为试验加载载荷ꎬΔ为加载点处的位移ꎮ图3㊀端部缺口弯曲试件Fig.3㊀Theendnotchedflexure(ENF)specimen为了考虑裂尖材料的损伤ꎬ文献[20]2443 ̄2455[25]877 ̄897提出了基于等效裂纹长度的修正梁理论(CBTE)ꎮ等效裂纹长度的公式如下[26]ae=38E1bh3CC3-2L33(3)CC=ΔP-3L10G13bh(4)式中ꎬae为等效裂纹长度ꎬ其考虑到了裂尖材料损伤以及剪切变形ꎮE1㊁G13是材料的弹性模量ꎮ基于等效裂纹长度ꎬ可得G=3P2ae264bD1(5)㊀㊀根据试验数据ꎬ采用上述公式(5)ꎬ可得界面材料的断裂韧性ꎮ同时ꎬ根据试验中记录的界面相对位移δ∗ꎬ即可得到GII ̄δ∗曲线ꎮ从而ꎬ根据公式(2)得到内聚力模型ꎮ但是ꎬ直接根据公式(2)得到的内聚力模型忽略了初始断裂韧性GIIcꎬiniꎬ导致内聚力模型τ ̄δ∗曲线所围区域的面积为GIIcꎬss-GIIcꎬini()ꎮ为了考虑初始断裂韧性GIIcꎬiniꎬ文献[23]174 ̄181使内聚力强度τC保持不变ꎬ通过增加δfꎬ使τ ̄δ∗曲线所围成的面积为GIIcꎬssꎬ以此对内聚力模型进行了修正ꎮ㊀1264㊀机㊀㊀械㊀㊀强㊀㊀度2021年㊀2㊀修正内聚力模型2 1㊀修正方法断裂韧性与界面相对位移的关系为FGIIcꎬδ∗()=0(6)式中ꎬGIIc为断裂韧性ꎻδ∗为界面相对位移ꎮ考虑到裂尖材料损伤λꎬ将式(6)改写如下FGIIcꎬδ∗ꎬλ()=0(7)㊀㊀获取内聚力模型的难点在于如何考虑裂尖材料损伤的影响ꎮ基于等效裂纹长度概念ꎬ文献[20]2443 ̄2455[25]877 ̄897提出了修正梁理论(CBTE)ꎬ以考虑裂尖材料损伤λ对断裂韧性GIIc的影响ꎮ借用上述思路ꎬ假设可用等效界面相对位移c考虑裂尖材料损伤λ对FGIIcꎬδ∗()=0的影响ꎬ如下FGIIcꎬδ∗-c()=0(8)㊀㊀根据公式(7)ꎬ将试验实测能量释放率与界面相对位移GII ̄δ∗曲线向右进行平移距离cꎬ即得到考虑裂尖材料损伤的GII ̄δ∗曲线ꎬ如图4所示ꎮ图4㊀GII ̄δ∗曲线的修正示意图Fig.4㊀TheschematicofthecorrectedGII ̄δ∗curve根据公式(2)对平移后的GII ̄δ∗曲线进行微分ꎬ就可以得到考虑裂尖材料损伤的内聚力模型τ ̄δ∗曲线ꎮ但是ꎬ根据公式(2)微分得到的内聚力模型τ ̄δ∗曲线含有未知量cꎮ考虑到τ ̄δ∗曲线所围成的面积须为GIIcꎬssꎬ依此得到c的大小ꎬ从而确定内聚力模型ꎮ2 2㊀修正结果对于端部缺口弯曲试验ꎬ文献[22]473 ̄487中获取的GII ̄δ∗试验拟合曲线如下GIIδ∗()=-56 2δ∗2+15 3δ∗+0 69(9)㊀㊀由式(8)可得到的未修正τ ̄δ∗曲线为τδ∗()=-112 4δ∗+15 3(10)㊀㊀根据本文的方法得到的τ ̄δ∗曲线为τδ∗()=-112 4δ∗+19 7(11)㊀㊀根据文献[23]174 ̄181的方法得到τ ̄δ∗曲线为τδ∗()=-67 7δ∗+15 3(12)㊀㊀上述τ ̄δ∗曲线的对比ꎬ如图5所示ꎮ根据图5ꎬ当直接采用这些内聚力模型进行有限元图5㊀修正前后τ ̄δ∗曲线对比Fig.5㊀Comparisonofτ ̄δ∗curves仿真时ꎬ在δ∗=0时ꎬ其应力位移关系的跳跃变化将导致数值求解的奇异性ꎮ为了克服在δ∗=0处的数值求解困难ꎬ引入一个很大的初始刚度KIIꎬ如图6所示ꎮ图6㊀初始刚度示意图Fig.6㊀SchematicoftheInitialstiffness3㊀数值分析3 1㊀网格和边界条件基于2 2节的内聚力模型ꎬ采用有限元软件Abaqusꎬ对端部缺口弯曲试验进行仿真模拟ꎮ试件的材料参数如表1所示ꎮ表1㊀试件材料参数Tab.1㊀Materialpropertiesofunidirectionalglass/epoxy参数Parameter值ValueE1/MPa18000E2/MPa2200E3/MPa2200G12/MPa1800G13/MPa1800G23/MPa1600ν120 29ν130 29ν230 38试件尺寸如图7所示ꎬ宽度为20mmꎬ试验支座和加载压头的半径均为2mmꎬ试验加载载荷为PꎬΔ为试验加载点处位移ꎮ仿真模型使用六面体单元(C3DR8)进行网格划分ꎻ胶层模型使用0厚度的内聚力单元(COH3D8)模拟ꎬ预置裂纹模型使用Seam裂纹模型模拟ꎬ两个试验㊀第43卷第5期贾云龙等:一种复合材料层合板分层扩展的修正内聚力模型1265㊀㊀图7㊀试件尺寸示意图Fig.7㊀TheENFspecimendimensions支座与一个加载压头使用解析刚体模拟ꎮ在裂纹尖端处㊁支座区域与加载点区域ꎬ取0 5mm网格尺寸ꎮ对于距离裂纹尖端㊁支座与加载点较远的区域ꎬ取1mm网格尺寸ꎮ沿试件的宽度方向ꎬ其网格的尺寸取1mmꎮ网格的划分情况如图8所示ꎮ仿真时ꎬ开启几何非线性ꎮ图8㊀网格划分示意图Fig.8㊀FiniteelementmodelofthetestedENFspecimens3 2㊀仿真结果及分析将仿真结果与试验结果进行对比ꎬ如图9所示ꎮ由图9可知ꎬ相较于文献[23]174 ̄181中的内聚力模型ꎬ本文方法得到的内聚力模型ꎬ其仿真结果与试验结果的吻合度更高ꎮ文献[23]174 ̄181的内聚力模型对初始断裂韧性GIIcꎬini进行了考虑ꎬ修正前后ꎬ内聚力强度τC=15 30MPaꎮ采用考虑裂纹尖端材料损伤和初始断裂韧性的方法获取的内聚力模型ꎬ其内聚力强度τC=19 72MPaꎮ从仿真结果P ̄Δ来看ꎬ考虑初始断裂韧性和裂尖材料损伤的内聚力模型可以更准确地对试验现象进行模拟ꎮ仿真GII ̄δ∗曲线与试验GII ̄δ∗曲线的对比ꎬ如图10所示ꎮ对于仿真所得断裂韧性GII都是从零开始ꎬ随着界面相对位移δ∗的增加逐渐而增加ꎬ并最终趋于稳定值ꎮ试验实测断裂韧性GII是从0 69N/mm开始逐渐增加ꎬ这是由于在裂纹开始扩展之前ꎬ裂尖材料产生损伤ꎬ耗散了能量ꎮ因此ꎬ在使用内聚力模型进行仿真时ꎬ需在内聚力模型中考虑裂尖材料损伤的影响ꎮ根据图10ꎬ采用本文方法得到GII ̄δ∗曲线与文献[23]174 ̄181的GII ̄δ∗曲线存在较大差异ꎮ其原因是本文的内聚力模型考虑了初始断裂韧性和裂尖材料损图9㊀有限元计算值与试验值的比较Fig.9㊀ComparisonbetweentheexperimentalandnumericalP ̄Δ图10㊀GII ̄δ∗曲线的比较Fig.10㊀ComparisonofGII ̄δ∗curves伤ꎬ文献[23]174 ̄181的内聚力模型仅考虑了初始断裂韧性ꎮ综上ꎬ较于仅考虑初始断裂韧性的内聚力模型ꎬ考虑初始断裂韧性和裂尖材料损伤影响的内聚力模型ꎬ可以更准确地模拟复合材料的分层现象ꎮ4㊀结论针对复合材料的分层现象ꎬ考虑初始断裂韧性和裂尖处材料的损伤ꎬ提出了一种修正内聚力模型ꎬ并对文献[22]473 ̄487中的试验进行了仿真ꎮ主要结论如下:1)内聚力模型的能否准确模拟复合材料裂纹扩展现象取决于内聚力模型的获取方法ꎮ2)考虑初始断裂韧性和裂尖材料损伤ꎬ给出了一种内聚力模型的获取方法ꎮ3)仿真结果表明ꎬ计及初始断裂韧性和裂尖材料损伤的内聚力模型可以更准确地模拟复合材料分层现象ꎮ参考文献(References)[1]㊀蔡忠云ꎬ唐文勇ꎬ陈念众ꎬ等.复合材料船体层合板的极限强度分析[J].船舶力学ꎬ2009(1):72 ̄81.CAIZhongYunꎬTANGWenYongꎬCHENNianZhongꎬetal.Ultimatestrengthanalysisofcompositelaminatedshippanels[J].JournalofShipMechanicsꎬ2009(1):72 ̄81(InChinese).[2]㊀孙枭雄ꎬ任慧龙ꎬ唐㊀宇.轻质夹芯复合材料结构强度评估方法㊀1266㊀机㊀㊀械㊀㊀强㊀㊀度2021年㊀研究[C].纪念船舶力学创刊二十周年学术会议ꎬ2017:435 ̄450.SUNXiaoXiongꎬRENHuiLongꎬTANGYu.Investigationonstrengthassessmentmethodsforlightensandwichcompositestructure[C].AcademicConferencetoCommemoratethe20thAnniversaryofthePublicationofShipMechanicsꎬ2017:435 ̄450(InChinese). [3]㊀曾海艳ꎬ严仁军ꎬ徐㊀琳ꎬ等.弯曲载荷下复合材料夹芯 L 型接头强度和疲劳试验研究[J].船舶力学ꎬ2017ꎬ21(12):1540 ̄1550.ZENGHaiYanꎬYANRenJunꎬXULinꎬetal.Experimentalstudyonstrengthandfatigueofsandwichcompositel ̄jointunderbending[J].JournalofShipMechanicsꎬ2017ꎬ21(12):1540 ̄1550(InChinese).[4]㊀王纬波ꎬ李永胜.复合材料板与钢板胶接㊁螺接与混合对接接头的力学特性研究[J].船舶力学ꎬ2011ꎬ15(9):1052 ̄1064.WANGWeiBoꎬLIYongSheng.Mechanicalbehaviorsofadhesively ̄bondedꎬboltedandhybridcomposite ̄to ̄steeljoints[J].JournalofShipMechanicsꎬ2011ꎬ15(9):1052 ̄1064.[5]㊀胡明勇ꎬ王安稳ꎬ姜㊀伟ꎬ等.复合材料层合板的动力响应和横向应力分析[J].船舶力学ꎬ2008(5):778 ̄784.HUMingYongꎬWANGAnWenꎬJIANGWeiꎬetal.Dynamicresponseandtransversestressesanalysisofcompositelaminatedplates[J].JournalofShipMechanicsꎬ2008(5):778 ̄784(InChinese).[6]㊀陈㊀悦ꎬ朱㊀锡ꎬ李华东ꎬ等.含分层缺陷复合材料夹芯梁力学特性及失效模式的试验研究[J].海军工程大学学报ꎬ2016(6):65 ̄70.CHENYueꎬZHUXiꎬLIHuaDongꎬetal.Mechanicalbehaviorandfailuremodesofcompositesandwichcolumnswithface/coredebond[J].JournalofNavalUniversityofEngineeringꎬ2016(6):65 ̄70(InChinese).[7]㊀赵㊀洁ꎬ陆㊀华ꎬ王明春.筋条分层损伤复材加筋壁板的稳定性分析及修理[J].机械强度ꎬ2016ꎬ38(4):871 ̄874.ZHAOJieꎬLUHuaꎬWANGMingChun.Stabilityanalysisandrepairofstiffenedcompositewallslabwithadelaminatongatthestringerinterface[J].JournalofMechanicalStrengthꎬ2016ꎬ38(4):871 ̄874(InChinese).[8]㊀刘㊀佶ꎬ许希武.Z ̄pin增强对自动铺丝复合材料T型接头拉脱㊁剪切性能影响的试验研究及数值模拟[J].机械强度ꎬ2017ꎬ39(3):527 ̄533.LIUJiꎬXUXiWu.Experimentandsimulationstudyontheeffectofz ̄pinreinforcedonthepull ̄offandshearcarryingcapacityoffiberplacementcompositeT ̄joints[J].JournalofMechanicalStrengthꎬ2017ꎬ39(3):527 ̄533(InChinese).[9]㊀马存旺ꎬ李志国ꎬ鲁国富ꎬ等.整体复合材料结构分层特性研究进展(一)[J].飞机设计ꎬ2014(5):31 ̄39.MACunWangꎬLIZhiGuoꎬLUGuoFuꎬetal.Developmentondelamiantioncharacteristicsofintegratedcompositestructures:PartI[J].AircraftDesignꎬ2014(5):31 ̄39(InChinese).[10]㊀OdessaIꎬFrostigYꎬRabinovitchO.Modelingofinterfacialdebondingpropagationinsandwichpanels[J].InternationalJournalofSolidsandStructuresꎬ2017(148/149):67 ̄78.[11]㊀YazdaniSꎬRustWJHꎬWriggersP.Delaminationonsetandgrowthincompositeshells[J].Computers&Structuresꎬ2018(195)(SupplementC):1 ̄15.[12]㊀TsaiMYꎬMortonJ.Anexperimentalinvestigationofnonlineardeformationsinsingle ̄lapjoints[J].MechanicsofMaterialsꎬ1995ꎬ20(3):183 ̄194.[13]㊀曹㊀勇ꎬ冯蕴雯ꎬ薛小锋ꎬ等.夹持力对填充孔复合材料层合板层间应力的影响分析[J].机械强度ꎬ2015ꎬ37(5):904 ̄909.CAOYongꎬFENGYunWenꎬXUEXiaoFengꎬetal.Impactanalysisofbolt ̄clampingforcetofilled ̄holelaminatesinterlaminarstress[J].JournalofMechanicalStrengthꎬ2015ꎬ37(5):904 ̄909(InChinese).[14]㊀CavalliMNꎬThoulessMD.Theeffectofdamagenucleationonthetoughnessofanadhesivejoint[J].JournalofAdhesionꎬ2001ꎬ16(1):75 ̄92.[15]㊀胡波涛ꎬ柴亚南ꎬ陈向明ꎬ等.后屈曲复合材料加筋板筋条 ̄蒙皮界面失效表征[J].机械强度ꎬ2019ꎬ41(6):1473 ̄1479.HUBoTaoꎬCHAIYaNanꎬCHENXiangMingꎬetal.Stiffener ̄skininterfacefailurecharacterizationofthestiffenedcompositepanelatpost ̄bucklingstage[J].JournalofMechanicalStrengthꎬ2019ꎬ41(6):1473 ̄1479(InChinese).[16]㊀RussellAJꎬStreetKN.Factorsaffectingtheinterlaminarfractureenergyofgraphite/epoxylaminates[J].ProgressinScienceandEngineeringofComposite(ICCM ̄IV)ꎬ1982:279 ̄286. [17]㊀BachrachWEꎬHicksTRꎬHabasZSꎬetal.Mixedexperimental ̄structuralmodelforinterlaminarshearfracturetoughness[J].JournalofAerospaceEngineeringꎬ1991ꎬ4(1):108 ̄125. [18]㊀OuyangZꎬLiG.Nonlinearinterfaceshearfractureofendnotchedflexurespecimens[J].InternationalJournalofSolidsandStructuresꎬ2009ꎬ46(13):2659 ̄2668.[19]㊀MouraMꎬMoraisA.EquivalentcrackbasedanalysesofENFandELStests[J].EngineeringFractureMechanicsꎬ2008ꎬ75(9):2584 ̄2596.[20]㊀BlackmanBRKꎬBrunnerAJꎬWilliamsJG.ModeIIfracturetestingofcomposites:Anewlookatanoldproblem[J].EngineeringFractureMechanicsꎬ2006ꎬ73(16):2443 ̄2455.[21]㊀MoSNꎬBelytschkoT.Extendedfiniteelementmethodforcohesivecrackgrowth[J].EngineeringFractureMechanicsꎬ2002ꎬ69(7):813 ̄833.[22]㊀AnyfantisKNꎬTsouvalisNG.ExperimentalandnumericalinvestigationofModeIIfractureinfibrousreinforcedcomposites[J].JournalofReinforcedPlastics&Compositesꎬ2011ꎬ30(6):473 ̄487.[23]㊀Heidari ̄RaraniMꎬGhasemiAR.AppropriateshapeofcohesivezonemodelfordelaminationpropagationinENFspecimenswithR ̄curveeffects[J].TheoreticalandAppliedFractureMechanicsꎬ2017(90):174 ̄181.[24]㊀SuoZꎬBaoGꎬFanB.DelaminationR ̄curvephenomenaduetodamage[J].JournaloftheMechanicsandPhysicsofSolidsꎬ1992ꎬ40(1):1 ̄16.[25]㊀BlackmanBRKꎬKinlochAJꎬParaschiM.ThedeterminationofthemodeIIadhesivefractureresistanceꎬGIICofstructuraladhesivejoints:Aneffectivecracklengthapproach[J].EngineeringFractureMechanicsꎬ2005ꎬ72(6):877 ̄897.[26]㊀DeMoraisAB.NovelcohesivebeammodelfortheEnd ̄NotchedFlexure(ENF)specimen[J].EngineeringFractureMechanicsꎬ2011ꎬ78(17):3017 ̄3029.。
含分层缺陷复合材料层合板压缩强度试验研究
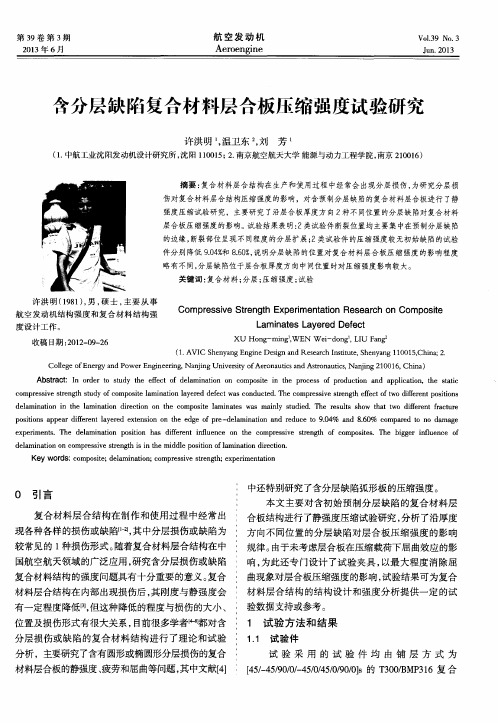
( 1 . AVI C S h e n y a n g E n g i n e De s i g n a n d Re s e a r c h I n s t i t u t e , S h e n y a n g 1 1 0 0 1 5 , Ch i n a ; 2 .
第3 9卷 第 3期
2 0 1 3年 6月
航 空 发 动 机
Ae ro e n g i n e
V0 1 - 3 9 No. 3
J u n . 2 0 1 3
含分层缺 陷 复合材 料层 合板压缩 强度试验研 究
许洪 明 , 温卫 东 , 刘 芳 。
( 1 . 中航工业沈阳发动机设计 研究 所 , 沈阳 1 1 0 0 1 5 ; 2 . 南京航空航天大学 能源与动力工程学 院, 南京 2 1 0 0 1 6 )
许洪明( 1 9 8 1 ) , 男, 硕士 , 主 要 从 事 航空 发动机 结构 强度和 复合 材料 结构 强
度设计 工作 。 收稿 日期 : 2 0 1 2 — 0 9 — 2 6
Co mp r e s s i v e St r e n g t h Ex p e r i me n t a t i o n Re s e ar c h o n Co mp o s i t e
c o mp r e s s i v e s t r e n g t h s t u d y o f c o mp o s i t e l a mi n a t i o n l a y e r e d d e f e c t w a s c o n d u c t e d . T h e c o mp r e s s i v e s t r e n g t h e f f e c t o f t wo d i f f e r e n t p o s i t i o n s d e l a mi n a t i o n i n t h e l a mi n a t i o n d i r e c t i o n o n t h e c o mp o s i t e l a mi n a t e s w a s ma i n l y s t u d i e d .T h e r e s u l t s s h o w t h a t t wo d i f f e r e n t f r a c t u r e p o s i t i o n s a p p e a r d i f f e r e n t l a y e r e d e x t e n s i o n o n t h e e d g e o f p r e - d e l a mi n a t i o n a n d r e d u c e t o 9 . 0 4 % a n d 8 . 6 0 % c o mp a r e d t o n o d a ma g e e x p e i r me n t s .T h e d e l a mi n a t i o n p o s i t i o n h a s d i f f e r e n t i n l f u e n c e o n t h e c o mp r e s s i v e s t r e n g t h o f c o mp o s i t e s .T h e b i g g e r i n l f u e n c e o f d e l a mi n a t i o n o n c o mp r e s s i v e s t r e n g t h i s i n t h e mi d d l e p o s i t i o n o f l a mi n a t i o n d i r e c t i o n . K e y wo r d s : c o mp o s i t e ; d e l a mi n a t i o n ; c o mp r e s s i v e s t r e n g t h ; e x p e i r me n t a t i o n
复合材料分层断裂的三种模式

复合材料分层断裂的三种模式社会的不断进步,使得人们的生活水平在很大程度上得到了提高,复合材料分层断裂的三种模式就是通过改变室内的热湿环境,为人们的居住生活提供一个舒适健康的环境。
复合材料分层断裂的三种模式的应用越来越广泛,一个良好的复合材料分层断裂的三种模式设计,不仅可以提高人们生活舒适度,还可以提高工作学习效率。
随着我国民众环保意识的增强,不再单单一味追求舒适的居住环境,更多的开始关注节能减排、绿色环保、和谐自然的居住环境。
1.1复合材料分层断裂的三种模式引言概述复合材料分层断裂的三种模式在最近几十年飞速发展的过程之中,其整体的产业耗能占比已经接近我国社会整体能耗的三分之一,而对于复合材料分层断裂的三种模式的整体使用来说,其能耗在建筑整体能耗之中的占比达到了40-50%,复合材料分层断裂的三种模式以其出色的节能性和环保性,受到越来越多的关注,同时也被不断推广。
但是,复合材料分层断裂的三种模式在施工中往往不受重视,导致发生了很多问题,而且我国的复合材料分层断裂的三种模式的设计和施工往往由不同单位承包,其对于问题的理解方式不同,相对应的利益关系也存在很大区别,导致很难有完美的配合。
加之,设计人员和施工人员的素质不同,复合材料分层断裂的三种模式可能由于缺乏施工经验而凭空想象,造成设计不合理;施工人员对设计理解度不够,达不到设计要求,造成设计效果大打折扣等。
复合材料分层断裂的三种模式的施工质量好坏直接和影响了建筑物的使用质量好坏,加强复合材料分层断裂的三种模式的施工复合材料分层断裂的三种模式管理,有利于提高复合材料分层断裂的三种模式质量。
因此,对复合材料分层断裂的三种模式进行工程复合材料分层断裂的三种模式管理是非常有意义的,也是非常重要的。
由于社会的发展,人们的生活水平得到了大大提高,在这种大形势下,相应的物质需求也就急速膨胀,而复合材料分层断裂的三种模式基本的居住工程也成了社会最为关注的重点复合材料分层断裂的三种模式之一。
- 1、下载文档前请自行甄别文档内容的完整性,平台不提供额外的编辑、内容补充、找答案等附加服务。
- 2、"仅部分预览"的文档,不可在线预览部分如存在完整性等问题,可反馈申请退款(可完整预览的文档不适用该条件!)。
- 3、如文档侵犯您的权益,请联系客服反馈,我们会尽快为您处理(人工客服工作时间:9:00-18:30)。
复合材料的分层缺陷
引言
目前被广泛用于飞机承力构件的纤维增强树脂基复合材料(CFRP)主要是层合板与层合结构。
在层合板的制造过程中,常由于许多不确定的因素,使复合材料结构发生分层、孔隙、气孔等等不同形式的缺陷;同时,复合材料层合板在装配与服役过程中所受到低能冲击很容易引发各种形式的损伤。
由于增强纤维铺设方向的不一致常导致铺层间刚度的不匹配,引发较高的层间应力,而层间应力的主要传递介质是较弱的树脂基体,因此对于复合材料层合板,分层是其主要的损伤形式。
有报导统计,复合材料层合板在加工、装配和使用过程中产生的分层损伤,占缺陷件的 50%以上[1]。
分层常存在于结构内部,无法根据表面状态检测出来,并且分层的存在极大地降低了结构的刚度,特别在压缩载荷作用下,由于发生局部屈曲而导致分层扩展,使结构在低于其压缩强度时发生破坏。
在飞机研制与制造过程中,复合材料层合板的分层损伤问题一直是难以解决的结构问题之一,也是影响CFRP 在结构组分中应用的主要限制因素。
因此,如何充分地结合试验测试,利用数值模拟的方法评估分层的许和容限,成为决定飞机结构综合性能的亟待解决的关键问题。
1.1分层产生的原因
Pagano 和 Schoeppner [2] 根据复合材料构件的形状,将分层产生的原因分为两类。
第一类为曲率构件,工程中常见的曲率构件包括扇形体、管状结构、圆柱形结构、球形结构和压力容器等;第二类为变厚度截面,工程中常见于薄层板与补强件连接区域、自由边界处、粘合连接处及螺栓接合处等。
在上述结构件中,临近的两铺层极易在法向和剪切向应力作用下发生脱胶和形成层间裂纹。
以外,温湿效应、层板制备和服役状态等亦是分层产生的原因。
由于纤维与树脂的热膨胀系数以及吸湿率均存在差异,因此,不同铺层易在固化过程产生不同程度的收缩并在吸收湿气后产生不同程度的膨胀,不同程度的收缩与膨胀所产生的剩余压力是导致分层的源头之一
[3, 4] 。
在层合板的制备过程中,由于手工铺设质量具有分散性,极易形成富树脂区,进而引发树脂固化时铺层间的收缩程度差异,使层间具有较低的力学特性,极易形成分层[5, 6] 。
在服役过程中,低速冲击所产生的横向集中力是层合板结构形成分层的重要原因之一。
冲击引发的临近铺层间的内部损伤、层合板制造过程中工具的掉落、复合材料部件的组装及维修以及军用飞机及结构的弹道冲击等均会引发层间分层。
1.2 分层的种类
Bolotin [5, 6] 将分层分为内部分层(Internal delaminations)和浅表分层(Near-surface delaminations)两类。
其中,内部分层源自层合板的内部铺层,由于树脂裂纹和铺层界面间相互作用而形成,它的存在会降低结构件的承载能力。
特别是在压缩载荷作用下,层合板的弯曲行为受到严重影响(如图1)。
虽然分层将层合板分为两个部分,但是由于两个子层板变形间的相互作用,层合板呈现相似的偏转状态,发生整体屈曲。
图1 内部分层及对结构稳定性的影响
浅表分层产生于层合板接近表面的浅层位置,呈现出比内部分层更为复杂的分层行为。
分层区域的变形受到厚子板的影响相对更小,浅表处的分层部分并不一定受较厚的子板的牵制而变形,因此对于浅表分层,不仅需要考虑浅表分层的扩展,还需要考虑分层子板的局部稳定性。
根据载荷形式及分层状态可将浅表分层分为如图 2所示的种类。
图2 浅表分层的种类
在分层产生后,内部分层和浅表分层在静承载和疲劳载荷作用下可能发生分层扩展,层合板的强度和稳定性明显下降。
确定分层缺陷的形式对复合材料结构的完整性是十分层重要的。
1.3分层的微观结构
在微观尺度下,层间裂纹扩展后将在裂纹前缘形成损伤区域。
根据树脂的韧性和应力水平(I 型,II 型,III 型和混合型,如图 3 所示),损伤区域的尺寸和形状呈现不同的状态。
剪切载荷下裂纹尖端应力场的衰减较缓慢,因此 II 型和 III 型裂纹尖端的损伤区域比 I 型区域广。
此外,受树脂基体的影响,脆性与韧性树脂基体的损伤状态具有明显的区别。
在脆性树脂体系下,I 型裂纹尖端的损伤区域会发生微裂纹的合并和生长以及纤维—树脂间的脱胶现象,上述现象都会诱发裂纹前进,其中,脱胶行为的发生常伴随着纤维桥接和纤维断裂现象的发生。
而对于剪切模式的 II 型和 III 型分层,裂纹前缘处的微裂纹发生合并的现象,并与铺层角度呈 45°方向扩展,直至到达富树脂区域。
界面处微裂纹的合并在纤维间的树脂区域呈现锯齿状,如图 4所示。
而对于韧性材料体系,裂纹前缘的塑性变形推进裂纹扩展,呈现出韧性断裂并伴随层间脱层现象的发生 [7]。
图3 I 型、II 型和 III型裂纹拓展模式
图4 层间II 型分层的扩展模式:(a)裂纹尖端处微裂纹的形成;(b)微裂纹的生长及张开;(c)微裂纹的合并及剪切尖端的形成
2 准静态下分层行为预测方法
分层力学由前苏联的固体物理学家 Obreimoff (1894-1981)最先着手研究,1930 年,他在题名“The Splitting Strength of Mica”[8]的论文中详细讨论了层间断裂韧性并研究了在剪切力作用下云母试样的分层现象。
时至今日,分层的力学问题在吸引重多科研工作者兴趣的同时,已取得了突出的成果,分层行为的预测方法发展成为强度理论方法、断裂力学方法和损伤力学方法等三类。
2.1 强度理论方法
强度理论方法是研究分层问题的传统方法,是以结构或材料抵抗损伤发生的能力为基础,通过将材料内部的节点应力与界面强度的大小进行比较来判断界面是否发生分层。
该预测分层损伤的方法由 Whitney 等[9]首先提出;在进一步应用平均应力准则的基础上,Kim 等 [11]对受拉、压载荷作用下的层合板的分层产生时的临界载荷值进行了预测。
但是由于不连续铺层端部易出现应力奇异,应力准则方法高度依赖网格尺寸;且由于平均应力准则或点应力准则都引入了特征长度的概念,而特征长度并没有很强的理论基础,使该方法不能够准确地预测
分层扩展行为 [12]。
2.2 线弹性断裂力学方法
断裂力学方法通过计算裂纹尖端应力场与裂纹尖端张开位移来评价界面的损伤状态。
在忽略材料非线性的前提下,可以采用线弹性断裂力学方法(LEFM)有效地预测分层扩展状态,该方法的核心内容为裂纹尖端能量释放率的计算。
计算应变能释放率的常用方法包括虚裂纹扩展技术(VCCT)、J 积分、虚裂纹扩张和刚度微分方法等,通过比较应变能释放率分量的组合式与某临界值间的关系,可以对分层的状态进行预测。
2.3 损伤力学方法
损伤力学方法是通过引入微缺陷 / 微裂纹的面积等形式的损伤变量来预测界面处分层状态,相比断裂力学方法,该方法不仅可以预测已存在裂纹的扩展状态,更重要的是,可以预测新裂纹的产生。
以内聚力理论为基础,该方法考虑了复合材料基体与增强相间以化学反应的形式生成的一层界面物质层,以界面参数的形式,充分地反映了界面物质层的模量、强度和韧性等材料参数。
内聚力裂纹模型由 Dugdale [13]和 Barenblatt [14]首次提出:材料在屈服应力的作用下,会在裂纹前缘形成薄的塑性区域,在该区域范围内的裂纹表面有应力作用,此作用力为“内聚力”;而与之相对的裂纹表面不受任何应力作用的区域为断裂区(如图 5所示)。
图5 内聚力模型
虽然内聚力模型属于局部损伤模型[15],对网格具有依赖性,但由于其支持网格间的相互独立,因此可以方便地实现网格的充分细化,达到准确计算的目的。
采用内聚力模型方法可以同时预测分层的产生和扩展,可以同时完成损伤容
限和强度分析。
(注:可编辑下载,若有不当之处,请指正,谢谢!)。