铝合金熔铸加工技术原理
铝合金铸造技术篇要点

铝合金铸造技术篇要点铝合金铸造技术,这可是个相当有趣且实用的领域呢!咱先来说说铝合金铸造的基本原理。
简单来讲,就是把铝合金加热融化成液态,然后倒入模具里,等它冷却凝固,就变成了咱们想要的形状。
这过程听起来好像挺简单,但实际操作可大有讲究。
就拿我曾经参观过的一家铝合金铸造厂来说吧。
当时我走进车间,一股热浪扑面而来,巨大的熔炉里,铝合金正在欢快地翻滚着,呈现出一种亮闪闪的橙色。
工人们穿着厚厚的防护服,全神贯注地盯着熔炉的温度和铝液的状态。
模具的准备也是关键一环。
模具的设计得精准无误,尺寸、形状、结构,一个小差错都可能导致整个铸件的失败。
而且模具的材质也有讲究,得能经受住高温的考验,还得保证铸件容易脱模。
铸造过程中的温度控制那可是重中之重。
温度太高,铝合金容易氧化,产生杂质;温度太低,流动性不好,铸件容易出现缺陷。
有一次,我看到一个新手工人没控制好温度,结果出来的铸件表面坑坑洼洼的,这可让师傅们头疼了好一阵。
还有啊,铝合金的成分也会影响铸造的效果。
不同的合金元素添加比例,会让铝合金的性能大不相同。
比如说,加一些镁能增加强度,加一些硅能提高流动性。
另外,铸造后的处理也不能马虎。
铸件得经过打磨、抛光、热处理等一系列工序,才能达到最终的质量要求。
总之,铝合金铸造技术可真是个精细活,每个环节都得小心翼翼,就像一场精心编排的舞蹈,任何一个舞步出错都可能影响整个演出的效果。
希望通过我这一番不太专业但还算真诚的分享,能让您对铝合金铸造技术有个初步的了解。
这技术啊,还得靠不断地实践和摸索,才能真正掌握其中的奥秘!。
《铝合金熔铸加工技术原理》(四)
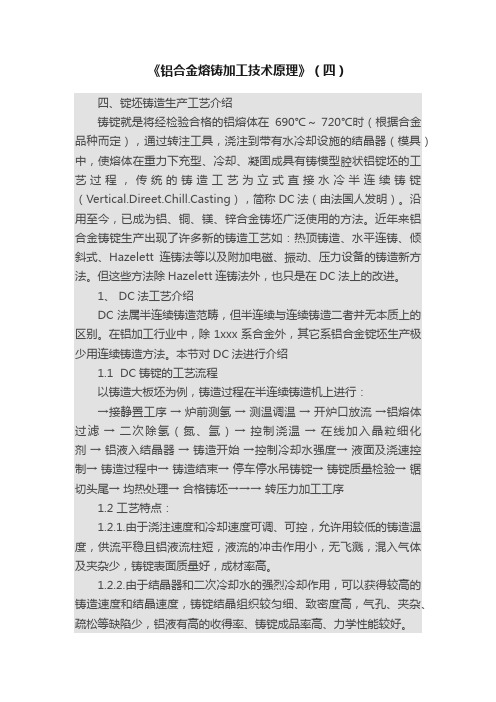
《铝合金熔铸加工技术原理》(四)四、锭坯铸造生产工艺介绍铸锭就是将经检验合格的铝熔体在690℃~ 720℃时(根据合金品种而定),通过转注工具,浇注到带有水冷却设施的结晶器(模具)中,使熔体在重力下充型、冷却、凝固成具有铸模型腔状铝锭坯的工艺过程,传统的铸造工艺为立式直接水冷半连续铸锭(Vertical.Direet.Chill.Casting),简称DC法(由法国人发明)。
沿用至今,已成为铝、铜、镁、锌合金铸坯广泛使用的方法。
近年来铝合金铸锭生产出现了许多新的铸造工艺如:热顶铸造、水平连铸、倾斜式、Hazelett连铸法等以及附加电磁、振动、压力设备的铸造新方法。
但这些方法除Hazelett连铸法外,也只是在DC法上的改进。
1、 DC法工艺介绍DC法属半连续铸造范畴,但半连续与连续铸造二者并无本质上的区别。
在铝加工行业中,除1xxx系合金外,其它系铝合金锭坯生产极少用连续铸造方法。
本节对DC法进行介绍1.1 DC铸锭的工艺流程以铸造大板坯为例,铸造过程在半连续铸造机上进行:→接静置工序→炉前测氢→测温调温→开炉口放流→铝熔体过滤→二次除氢(氮、氩)→控制浇温→在线加入晶粒细化剂→铝液入结晶器→铸造开始→控制冷却水强度→液面及浇速控制→铸造过程中→铸造结束→停车停水吊铸锭→铸锭质量检验→锯切头尾→均热处理→合格铸坯→→→转压力加工工序1.2 工艺特点:1.2.1.由于浇注速度和冷却速度可调、可控,允许用较低的铸造温度,供流平稳且铝液流柱短,液流的冲击作用小,无飞溅,混入气体及夹杂少,铸锭表面质量好,成材率高。
1.2.2.由于结晶器和二次冷却水的强烈冷却作用,可以获得较高的铸造速度和结晶速度,铸锭结晶组织较匀细、致密度高,气孔、夹杂、疏松等缺陷少,铝液有高的收得率、铸锭成品率高、力学性能较好。
1.2.3.生产过程机械化程度高,工人劳动强度较小,生产率高。
1.2.4.工艺条件要求严格,技术性强,熟练掌握难度大。
铝合金熔铸加工技术原理
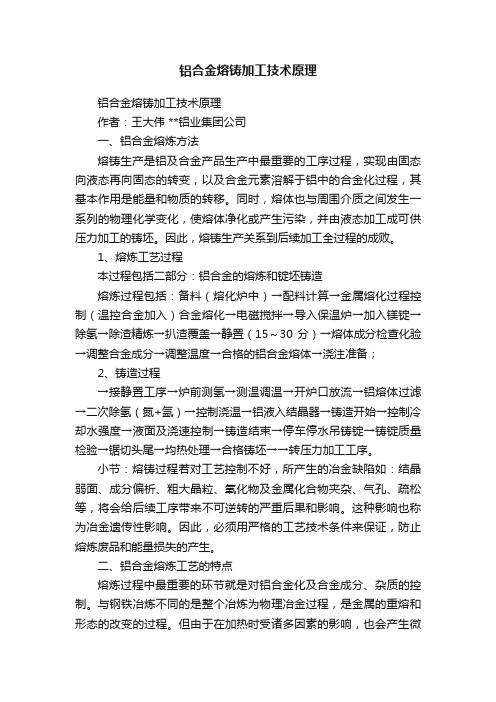
铝合金熔铸加工技术原理铝合金熔铸加工技术原理作者:王大伟 **铝业集团公司一、铝合金熔炼方法熔铸生产是铝及合金产品生产中最重要的工序过程,实现由固态向液态再向固态的转变,以及合金元素溶解于铝中的合金化过程,其基本作用是能量和物质的转移。
同时,熔体也与周围介质之间发生一系列的物理化学变化,使熔体净化或产生污染,并由液态加工成可供压力加工的铸坯。
因此,熔铸生产关系到后续加工全过程的成败。
1、熔炼工艺过程本过程包括二部分:铝合金的熔炼和锭坯铸造熔炼过程包括:备料(熔化炉中)→配料计算→金属熔化过程控制(温控合金加入)合金熔化→电磁搅拌→导入保温炉→加入镁锭→除氢→除渣精炼→扒渣覆盖→静置(15~30分)→熔体成分检查化验→调整合金成分→调整温度→合格的铝合金熔体→浇注准备;2、铸造过程→接静置工序→炉前测氢→测温调温→开炉口放流→铝熔体过滤→二次除氢(氮+氩)→控制浇温→铝液入结晶器→铸造开始→控制冷却水强度→液面及浇速控制→铸造结束→停车停水吊铸锭→铸锭质量检验→锯切头尾→均热处理→合格铸坯→→转压力加工工序。
小节:熔铸过程若对工艺控制不好,所产生的冶金缺陷如:结晶弱面、成分偏析、粗大晶粒、氧化物及金属化合物夹杂、气孔、疏松等,将会给后续工序带来不可逆转的严重后果和影响。
这种影响也称为冶金遗传性影响。
因此,必须用严格的工艺技术条件来保证,防止熔炼废品和能量损失的产生。
二、铝合金熔炼工艺的特点熔炼过程中最重要的环节就是对铝合金化及合金成分、杂质的控制。
与钢铁冶炼不同的是整个冶炼为物理冶金过程,是金属的重熔和形态的改变的过程。
但由于在加热时受诸多因素的影响,也会产生微小的化学变化。
熔炼生产工艺的基本任务就是要获得合金成分均匀、含气含渣(杂)少、合金成分达标的铝合金熔体。
确保下一步铸造工艺的顺畅实施,最终生产出组织性能、表面质量和尺寸都符合工艺要求的合格铸坯。
对一般合金;含氢量<0.13ml/100g、特殊合金;含氢量<0.1ml/100g。
铝合金熔炼与铸造 (2)

铝合金熔炼与铸造1.铝合金是一种重要的金属材料,具有优异的物理性能和机械性能,广泛应用于航天航空、汽车制造、建筑工程等领域。
铝合金熔炼与铸造是生产铝合金制品的关键步骤,本文将介绍铝合金熔炼与铸造的基本原理、常用工艺和注意事项。
2. 铝合金熔炼铝合金熔炼是将铝合金原料加热至熔点,并以一定方式进行熔炼的过程。
铝合金原料可以是铝锭、废铝或铝合金碎料,在熔炼过程中需要加入一定比例的熔剂和合金元素。
铝合金熔炼的目的是将原料熔化并混合均匀,以获得符合要求的铝合金液态材料。
2.1 熔炼设备铝合金熔炼通常使用电阻炉、感应炉或电弧炉等熔炼设备。
其中,电阻炉是最常用的熔炼设备之一。
电阻炉通过电流通过导体产生的电阻热进行熔炼,具有加热速度快、操作方便等优点。
感应炉则利用电磁感应的原理进行加热,加热效率高,适用于熔炼大批量的铝合金。
电弧炉则利用电弧的高温进行熔炼,适用于熔炼高温合金。
2.2 熔炼工艺铝合金熔炼的工艺通常包括预热、熔炼和保温三个阶段。
将熔炼设备预热至一定温度,然后将铝合金原料和熔剂放入炉中,并控制加热温度和时间,使原料熔化并混合均匀。
,保持一定温度,使铝合金保持液态状态,以备后续的铸造工艺使用。
2.3 熔炼注意事项在铝合金熔炼过程中需要注意以下几点:•安全操作:熔炼过程中需要戴上防护设备,避免接触高温液态金属和有害气体。
•熔化温度控制:严格控制熔化温度,过高的温度会导致铝合金组织不稳定,影响机械性能。
•熔炼时间控制:合适的熔炼时间可以保证原料充分熔化和混合均匀。
•熔剂和合金元素的添加:根据铝合金的要求添加适当比例的熔剂和合金元素,以调整铝合金的成分和性能。
3. 铸造过程铸造是将铝合金液态材料倒入铸型中,并经过凝固和冷却形成所需的铝合金制品的过程。
铸造过程可以分为压铸、重力铸造和砂型铸造等不同的铸造方法。
3.1 压铸压铸是一种通过高压将铝合金液态材料注入金属模具中,并经过快速凝固形成制品的铸造方法。
压铸具有生产效率高、制品精度高等优点,适用于生产复杂形状的铝合金制品。
铝合金熔炼与铸造技术

铝合金熔炼与铸造技术一、引言铝合金是一种重要的结构材料,具有轻质、高强度和良好的耐腐蚀性能,在航空航天、汽车制造、建筑工程等领域广泛应用。
铝合金的制备过程中,熔炼与铸造技术起到关键作用,本文将对铝合金熔炼与铸造技术进行详细探讨。
二、铝合金熔炼技术2.1 熔炼原料准备熔炼铝合金的原料主要包括铝、合金元素和辅助材料。
铝采用高纯度的铝锭,合金元素可以通过添加铝合金粉末或其他化合物来实现。
辅助材料包括熔剂、脱气剂等。
这些原料的准备对于保证铝合金的成分和质量非常重要。
2.2 熔炼设备和工艺熔炼铝合金的常用设备有电阻加热炉、感应加热炉和气体燃烧炉等。
其中,感应加热炉在铝合金熔炼中应用最广泛,具有加热速度快、能耗低和温度控制准确等优点。
熔炼工艺包括预热、熔化、调温和净化等步骤,其中净化技术对于铝合金的纯净度和性能起到重要作用。
2.3 熔炼过程控制与优化熔炼过程中,熔体温度、保温时间、搅拌方式等因素对铝合金的成分和组织结构有重要影响。
熔炼过程需要进行温度控制、气氛控制和搅拌控制等,以确保铝合金的成分均匀、杂质含量低。
三、铝合金铸造技术3.1 铸造方法铝合金的常用铸造方法包括压铸、重力铸造、低压铸造和砂型铸造等。
压铸是最常用的铸造方法,适用于生产复杂形状和尺寸精度要求高的铝合金件。
重力铸造适用于大型铝合金零部件的生产,低压铸造适用于长条状和壳状铝合金件的生产,砂型铸造适用于非常大型和特殊形状的铝合金件的生产。
3.2 铝合金铸造过程铝合金的铸造过程主要包括熔炼、准备模具、浇注、冷却和后处理等步骤。
熔炼过程中,需要根据具体合金配方和要求,控制熔体温度、浇注温度和浇注速度等参数。
准备模具是确保铸造件尺寸和表面质量的重要环节。
浇注过程需要保证熔体充分填充模腔,并避免气孔和缺陷的产生。
冷却过程中需控制冷却速率,以避免铝合金件出现应力和变形。
3.3 铝合金铸造工艺改进为了提高铝合金铸造件的质量和效率,可以采取一些工艺改进措施。
铝合金铸造工艺
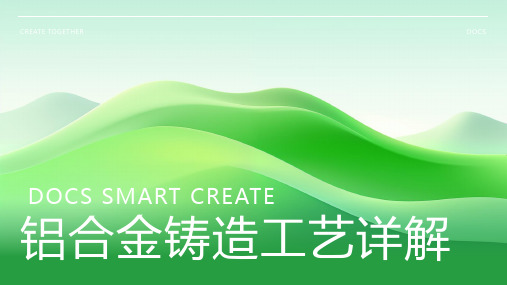
和应用
铝02合金铸造工艺的分类及
特点
重力铸造工艺及特点
重力铸造工艺是将熔融铝倒入模具中,依靠重力作 用使铝液充满模具并凝固成型的一种工艺
• 重力铸造工艺简单、投资成本低,适 用于中小型铸件的生产 • 重力铸造工艺对模具的要求较低,模 具使用寿命较长
学性能
• 挤压铸造工艺适用于对力学性能要求 较高的铸件生产,如汽车制造领域的零 部件 • 挤压铸造工艺对模具和挤压设备的要 求较高,投资成本较大
铝03合金铸造工艺的主要原
材料与辅助材料
铝合金铸造原料的选择及特点
铝合金铸造原料主要包括铝合金锭、合金元素、精炼剂等
• 铝合金锭是铝合金铸造的主要原料,根据不同的性能要求,可以选择不同的铝合 金牌号 • 合金元素用于调整铝合金的成分,改善其性能,如镁、硅、铜等 • 精炼剂用于改善铝合金熔炼过程中的气体含量和杂质含量,提高铸件的质量
铝合金铸造模具的设计需要考虑铸件的形状、尺寸、壁厚等因素
• 模具设计应满足铸件的成型要求,保证铸件的尺寸精度和表面质量 • 模具设计应考虑铸造过程中的温度、压力、时间等参数,确保铸件的质量
铝合金铸造工具的种类及用途
铝合金铸造工具主要包括铸造工具、测量工具、清理工具等
• 铸造工具用于成型铝合金铸件,如压铸工具、重力铸造工具、低压铸造工具等 • 测量工具用于检测铸件的尺寸、形状、质量等,如卡尺、千分尺、投影仪等 • 清理工具用于清理铸件表面的杂质、氧化皮等,如砂轮机、抛光机、喷砂机等
其他铝合金铸造工艺及特点
真空铸造工艺:在真空条件下进行铸造,可以降低 熔融铝中的气体含量,提高铸件的质量
• 真空铸造工艺适用于对气密性要求较 高的铸件生产,如航空航天领域的零部 件 • 真空铸造工艺对设备要求较高,投资 成本较大
铝合金及型材的生产原理熔炼

熔炼熔炼和铸造生产是铝及铝合金加工工艺中的组成部分,其主要目的是:配制合金;通过适当的工艺措施(如精练和过滤)提高金属净度;铸造成型。
它不仅提供符合加工要求的优质铸锭,而且铸锭质量在很大程度上影响压力加工过程和制品的质量,熔炼过程中的吸气和夹杂物会在铸锭中造成疏松、气孔、夹渣等冶金缺陷。
为此必须采取相应的净化处理措施予以防止和清除。
烘炉操作:新修、大修后的熔炼炉,其自然干燥时间在夏季不应小于半个月,在冬季不应小于一个月,中修后的炉子,其自然干燥时间不应小于一个星期。
烘炉的目的是:使炉体各部分内外层均匀缓慢地升温,避免炉衬受急冷急热而开裂。
同时,更充分地排除砌体中的水分,防止熔炼时金属吸气和氧化。
注:1.大修后,自然干燥时间少于半个月时,夏季应延长低温(200℃)烘炉时间24h,冬季延长36h。
2.停炉在5昼夜以内及5-10昼夜时,关上炉门用微火苗分别烘烤8h和12h后,将炉温升至900℃即可装炉。
3.停炉在10-15昼夜及小修后,先敞开炉门用木柴烘烤4h,再关上炉门用轻微火苗烘烤12h,然后将炉温升至900℃,即可装炉。
一、烧损合金在熔炼过程中由于氧化反应,挥发,以及与炉墙,精练剂等作用而造成的不可回收的金属损失称为烧损,总烧损率一般为2.5-5.0%之间。
二、熔炼温度过低的熔炼温度在生产实践中没有实际意义,在生产中既要防止熔体过热(使金属与炉气、炉衬等相互作用),又要缩短熔炼时间。
过热不仅容易大量吸收气体,而且易使在凝固后铸锭的晶粒组织粗大,增加铸锭裂纹的倾向性,影响合金性能。
半熔融的温度下,合金易吸气(铝液溶解的气体中80-90%是氢气)。
氢与铝不起化学反应,而是以原子状态存在于晶体点阵的间隙内,形成间隙式固溶体。
熔炼铝及铝合金时,应该选择微氧化性气氛:还原性气氛对铝合金并不是还原性的,CO 可使铝继续氧化,H 2及碳氢化合物还可与铝反应产生大量原子氢进入溶体;还原性气氛燃烧不完全,温度低;微氧化性气氛能使熔体表面生成一层氧化膜,使氧化过程变得非常缓慢。
第28次课-铸造铝合金熔炼原理讲解学习

铝铸件中气孔的形态及对铸件性能的影响
针孔:分布在整个铸件截面上,因铝液中的气体、夹杂含
量高、精炼效果差、铸件凝固速度低而引起。
点状针孔:呈圆点状轮廓清晰且互不相连,易和缩孔、缩松相区别。由 铸件凝固时析出的气泡所形成,多发生于结晶温度范围小、补缩能力良 好的铸件中。
为消除铝铸件中的气孔,应遵循“除杂为主,除气为辅”、 “除杂是除气的基础”的原则。
Al+O2=Al2O3(γ)---致密氧化膜 > 900 ℃ : Al2O3(γ)→ Al2O3(α)—疏松膜
γ-Al2O3 具有两面性:①和铝液接触的一面是致密的,可阻碍铝液的氧 化和吸气;②和炉气接触的那面却是粗糙、疏松的,其表面小孔吸附 着水汽和氢,搅动铝液时, γ-Al2O3将水汽和氢带入铝液,铝液氧化 生成夹杂物、吸入氢气。
氧化铝的形态、性能及对吸氢的影响(续)
η-Al2O3 、γ-Al2O3 在600-700 ℃范围内吸附水汽和氢的能力 最强,因此,铝液中的氢有两种形式:溶解氢和吸附在氧化 夹杂缝隙中的氢,前者约占90%以上,后者约占10%以下。 故铝液中的氧化夹杂越多,则含氢量也越高。
铝液中卷入Al2O3 夹杂,既增加了含氢量,吸附H2的Al2O3又 是温度下降时气泡形核的基底,容易在铸件中形成气孔。
网状针孔:呈密集相连成网状,伴有少数较大的孔洞。结晶温度范围宽 的合金,铸件缓慢凝固时析出的气体分布在晶界上及发达的枝晶间隙中, 此时结晶骨架已形成,补缩通道被堵,便在晶界上及枝晶间隙中形成网 状针孔。它会割裂合金基体,危害性比前者大。
混合型针孔:由点状针孔和网状针孔混杂在一起,常见于结构复杂、壁 厚不均匀的铸件中。
铝-水气反应(续)
在含硅、铜、锌等元素的铝合金,能较显著地阻缓铝 -水蒸气反应。含镁、钠等元素较多的铝合金,常使 铝-水气反应激烈进行。
- 1、下载文档前请自行甄别文档内容的完整性,平台不提供额外的编辑、内容补充、找答案等附加服务。
- 2、"仅部分预览"的文档,不可在线预览部分如存在完整性等问题,可反馈申请退款(可完整预览的文档不适用该条件!)。
- 3、如文档侵犯您的权益,请联系客服反馈,我们会尽快为您处理(人工客服工作时间:9:00-18:30)。
铝合金熔铸加工技术原理
作者:王大伟 **铝业集团公司
一、铝合金熔炼方法
熔铸生产是铝及合金产品生产中最重要的工序过程,实现由固态向液态再向固态的转变,以及合金元素溶解于铝中的合金化过程,其基本作用是能量和物质的转移。
同时,熔体也与周围介质之间发生一系列的物理化学变化,使熔体净化或产生污染,并由液态加工成可供压力加工的铸坯。
因此,熔铸生产关系到后续加工全过程的成败。
1、熔炼工艺过程
本过程包括二部分:铝合金的熔炼和锭坯铸造
熔炼过程包括:备料(熔化炉中)→配料计算→金属熔化过程控制(温控合金加入)合金熔化→电磁搅拌→导入保温炉→加入镁锭→除氢→除渣精炼→扒渣覆盖→静置(15~30分)→熔体成分检查化验→调整合金成分→调整温度→合格的铝合金熔体→浇注准备;
2、铸造过程
→接静置工序→炉前测氢→测温调温→开炉口放流→铝熔体过滤→二次除氢(氮+氩)→控制浇温→铝液入结晶器→铸造开始→控制冷却水强度→液面及浇速控制→铸造结束→停车停水吊铸锭→铸锭质量检验→锯切头尾→均热处理→合格铸坯→→转压力加工工序。
小节:熔铸过程若对工艺控制不好,所产生的冶金缺陷如:结晶弱面、成分偏析、粗大晶粒、氧化物及金属化合物夹杂、气孔、疏松等,将会给后续工序带来不可逆转的严重后果和影响。
这种影响也称为冶金遗传性影响。
因此,必须用严格的工艺技术条件来保证,防止熔炼废品和能量损失的产生。
二、铝合金熔炼工艺的特点
熔炼过程中最重要的环节就是对铝合金化及合金成分、杂质的控制。
与钢铁冶炼不同的是整个冶炼为物理冶金过程,是金属的重熔和形态的改变的过程。
但由于在加热时受诸多因素的影响,也会产生微小的化学变化。
熔炼生产工艺的基本任务就是要获得合金成分均匀、含气含渣(杂)少、合金成分达标的铝合金熔体。
确保下一步铸造工艺的顺畅实施,最终生产出组织性能、表面质量和尺寸都符合工艺要求的合格铸坯。
对一般合金;含氢量<0.13ml/100g、特殊合金;含氢量<0.1ml/100g。
适合的熔炼温度;熔炼时炉料的温度应<800℃。
熔体浇注的温度;在液相线以上50~110℃,一般为720℃。
下面就铝熔炼过程的特点进行介绍
1、铝合金熔炼能量消耗大
铝合金熔炼能量消耗多,难以达到理想热效率。
铝在熔炼时消耗热量多。
虽然铝的熔点低,但是熔化潜热大(394KJ/Kg),比热容大(固态1.139kJ、液态1.046kJ),黑度小,仅为铜、铁的25%,对热的反射强。
比其它金属熔化时消耗热量多。
铁、铜、铝热特性比较参看表(20)
在实际生产中每熔化1吨铝,在反射炉中需要天然气60~65标米/T。
电阻炉中需要电力700KWh、工频感应炉需要500~600KWh。
熔炼铝合金时对炉气的要求是,微氧化性或中性气氛。
炉子温升不能过快,连续生产时炉内最好留存15~20%铝液。
由于各种因素影响,在熔炼铝合金时,即使连续生产,每炉所消耗的能量也不尽相同,吨铝能耗约50~70×104千卡/t。
对熔铝炉而言,普通热传导炉有效传热只有28%、对流传热炉只有46.7%。
目前,最好的熔铝炉,据厂家介绍也只有55%
的热效率,难以达到理想热效率。
铁、铜、铝热特性比较表(20)
金属
密度
g/㎝3
比热容
KJ/(kg℃)
熔点
℃
熔化潜热
KJ/kg
加热到熔点所需热量KJ/kg
熔点﹢100℃热量KJ/kg
黑
度
铁
固相
液相
7.36 6.9
0.691 0.867
1536
272
1319
1470
0.8 铜
固相液相
8.62 8.36
0.481 0.544
1083
214
724
779
0.8 铝
固相液相
2.70 2.38
1.139 1.047
660
394
1122
1227
0.2
2、铝金属性质活泼、易氧化、烧损
铝对氧有很大的亲和力,氧化反应方程式:
4AI﹢3O2=2AI2O3
生成Al2O3膜浮在熔体表面,形成的Al2O3膜虽然有保护作用,但一旦被破坏,膜进入熔体,就很难除去。
因为,Al2O3在此条件下,不能被还原。
它的密度与熔体相近,悬浮在熔体中,不易清除,如溶在熔体中进入铸锭里,则会给下一步加工带来严重的影响,是造成产品报废的原因之一。
如产生铝箔针孔,Al2O3硬度很高,易损伤轧辊或模具表面。
在实际生产中采用陶瓷过滤板过滤的方法进行清除。
另外,Al2O3 杂质是炉中各种气体的载体,它的存在会使铝熔体大量吸氢。
同时,由于金属的氧化和蒸发造成了铝的烧损。
在火焰反射炉中熔炼铝合金烧损为1.0~3.0%、在电阻炉为0.5~1.0%、工频炉为0.3~0.8%。
铝合金的烧损除氧化外还和熔炼温度有关,在常压下,炉温越高,铝蒸气压越高,蒸发烧损越大。
例如:铝在660℃熔点时的蒸气压为1.2×10-3毫米汞柱、在1000℃时蒸气压为1.0×10-2毫米汞柱。
当加入的合金元素含有金属镁时,控制熔炼温度则显得更为重要。
因为镁的蒸气压更低,在1110℃时则达到760毫米汞柱(1个大气压)。
所以炉温过高时,不但造成铝还造成合金元素的损失,使合金成分不足而产生废品。
在铝合金熔炼时除个别情况外,炉温一般控制在800℃以下,防止铝熔体过热而产生不良影响。
因此,如何减少和防止铝及合金元素的氧化和蒸发也是铝合金熔炼加工过程中一个重要的控制环节。
3、易吸气(氢)、熔体易受污染
铝合金的吸气能力强。
由于是常压开放式熔炼,熔体含气量多少,受工厂自然环境影响较大。
在南方潮湿地区空气湿度大、熔体含氢量多。
含气量多少还与熔炼温度有关,与熔炼温度成正比。
尤其是当熔炼温度在800℃以上时吸气现象更为严重,在铝合金中主要进入熔体的气体是氢气。
这与铝的特性有关。
在铝中的气体90%是氢,因此说,铝合金的除气过程就是除氢过程。
铝在固、液态时氢的溶解度参看表(20),特别是在有水蒸汽或还原性气氛的炉气中,吸氢现象更为严重。
氢在铝合金铸锭中吸入的绝对量并不大,但是造成铸锭结晶时的气孔和疏松倾向严重。
因此,在熔铸操作中,减少吸气(氢)也是最重要的工艺环节。